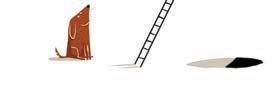
3 minute read
Live wire
RISK ASSESSMENT
Live wire
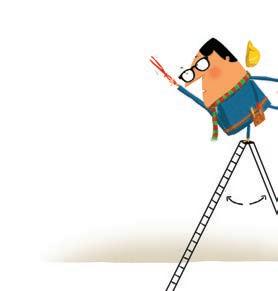
Covering all angles Electrical
contractors need to ensure they assess and control any risks that are associated with jobs, to keep staff , customers and the public safe, says Paul Reeve
E lectrical contractors should always understand the hazards and risks associated with any job they do, or supervise, and how any significant risks will be controlled.
This is particularly true for electrical safety, but it’s also true for other health and safety issues. In fact, in the commercial sector, falls from height and manual handling injuries are far more common than electrical accidents, and asbestos is an even bigger, industry-defining, health issue.
The Health and Safety Executive (HSE) says risk assessments need to be ‘suitable and suff icient’, and it’s the risk assessment that informs other key documents such as construction phase plans and method statements. In the public and commercial sectors, clients and pre-qualification schemes are very keen to see if the contractor can deal with risk assessments.
Two basic types of risk assessment are ‘quantified’ – giving a number that indicates the level of risk – and ‘qualitative’ – a general statement identifying something as ‘low’ or ‘medium’ risk. Either type can be based on the following seven steps.
Understand the risks The starting point for any risk assessment is to understand what the task/job involves. In short, what are the activities involved in this job? Next, consider any relevant hazards (the potential causes of significant harm) and who could be harmed, and how.
When you have considered the hazards, decide which ones are the most significant, and could lead to serious harm. You can then base your risk assessment mainly on addressing these hazards.
Implement control measures If eliminating a hazard is not an option, you’ll need suitable risk controls to reduce the risk to an acceptable level. So, consider what control measures you’ll need to control the risk of harm. This might include safety measures such as safe isolation, permits to work, safety barriers, site instructions or protective equipment.
You may well have general approaches to reducing the risk from any significant hazards that are associated with what you usually do. Note these risk controls first.
Identify any further issues There may also be additional, job-specific, health and safety issues. Again, note these. They might range from using a new apprentice to more specific hazards, such as work on mobile elevating work platforms or in a refrigeration room. Note what further risk controls you will use. Clarify responsibility Add who has supervisory responsibility for ensuring your control measures are, first, available when needed and, second, used and understood by operatives/sub-contractors. Your control measures will need to be applied properly at the workplace, if your risk assessment is to be eff ective.
Assess the risk The risk assessment then requires you to consider what risk remains, and to who, once all your control measures are in place (this is called the ‘residual risk’). To assess this, consider the following two factors (remember, this is with all your control measures in place): 1) How harmful could an accident or exposure be? 2) How likely is it to happen? (severity x how likely = risk of harm)
The remaining risk from this activity – the residual risk – is the output of your risk assessment. Now, decide if the remaining risk is suff iciently low. If it’s not, then you need to re-visit what you are doing to control risks from this activity.
Paul Reeve is director of business services at the Electrical Contractors’ Association To help contractors quickly and eff ectively assess risks, the ECA has developed e-RAMS, available free to ECA members. For more information see www.eca.co.uk