
6 minute read
Case study
from Connections - Summer 2015
by NICEIC
MUSEUM LIGHTING
Live wire
Light at the museum
> The Oxford Museum of Natural History is housed in a Grade 1 listed building
The Oxford University Museum of Natural History recently reopened aft er a £4 million upgrade that has seen the restoration of the iconic Victorian glass roof and the installation of a stunning new architectural lighting scheme
By Andrew Brister

Oxford, the city of dreaming spires, boasts a plethora of architectural gems. Many of the city’s most stunning buildings form part of Oxford University – the oldest university in the English-speaking world – and among them is the Oxford University Museum of Natural History, the Grade I listed neo-Gothic building, designed by the Irish architects Thomas Newenham Deane and Benjamin Woodward and built in 1860. Among its most famous features are the Oxfordshire dinosaurs, the Dodo, and the swifts that have been nesting in the ventilation flues in the tower of the museum for many years.
The iconic building has recently benefited from a major refurbishment and development programme that has cast the museum’s main court in a new light, both through the cleaning and replacement of some 8,600 glass tiles, but also thanks to a new state-of-the-art lighting scheme that was installed at the same time.
The major work to the roof structure was originally to include minor works to increase light levels on the two main stairwells, but Oxford University’s Estates Services’ deputy electrical engineer Robert Gregg managed to secure funding to introduce a lighting scheme into the main court areas.
“He wanted to develop something unique in the history of the building,” says Richard Francis, partner at Monard Electrical, the Oxford-based and NICEIC-registered firm that won the tender for the design-and-build contract. “The lighting project moved from small maintenance works to a substantial re-lighting project across the museum.” The end result comprises a combination of Zumtobel, Bega and Limburg luminaires, all carefully chosen and positioned to create a superb eff ect, while minimising visual intrusion.
Creative solutions
The main challenge for Monard Electrical was how to install the lighting in a way that was sympathetic to the listed interior. The museum consists of a large square court with a glass roof, supported by cast iron pillars that divide the court into three aisles. Cloistered arcades run around the ground and first floors of the building, with each column made from a diff erent British stone. The stonework and iron pillars are ornamented with natural forms such as leaves and branches.
“We couldn’t drill into the pillars because of the listed status, so we came up with the idea of using magnets to attach the fittings and the
If you’ve been involved in an interesting and innovative project let us know. Email nick.martindale@redactive.co.uk
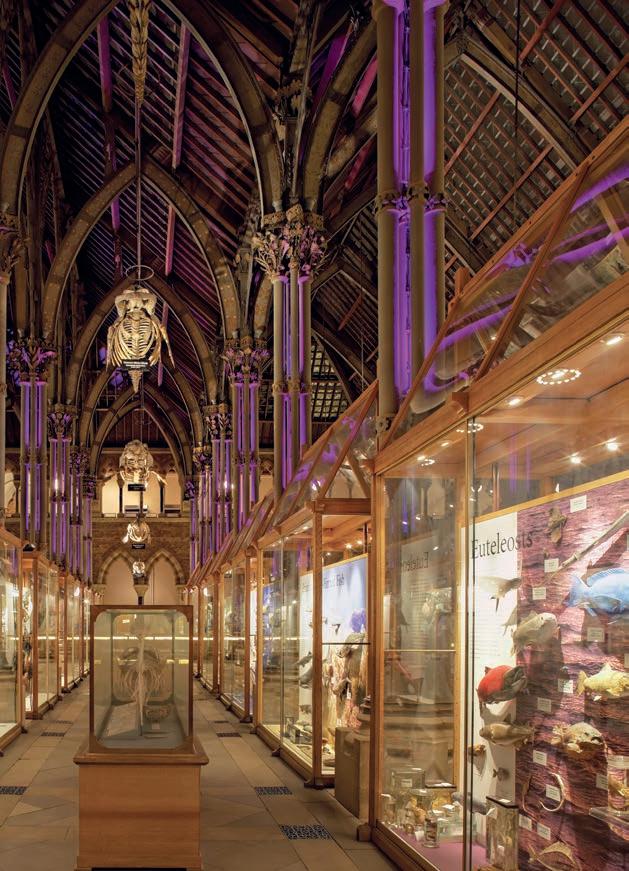
cabling,” says Francis. “Drawing on our experience of working on other projects with Oxford’s Ashmolean Museum, we suggested making bespoke magnet mounts that fit the contours of the ironwork and have the strength to support the luminaires for decades.”
While the Ashmolean had used magnetic mounts in exhibition cases, Francis believes this is the first time that such an approach has been used to support lighting. Using museum-grade acrylic, the mount structures were cut out using state-of-the-art design software and a laser cutter.
The size of the aperture for the magnet was critical, being cut to tenths of a millimetre, with allowance made for the thickness so that the magnet would just fit. Too tight and the acrylic might split; too loose and the magnet could potentially fall out. In time, the magnet will literally be embedded into the acrylic as it deforms around the magnet.
“The mounts were combined with aerospace-industry-grade magnets, which were required to give us the strength and compact size we needed to achieve a safe fixing with a minimalistic look,” says Francis. “We checked that the high strength of the magnets did not aff ect the luminaires by sending test sample data to the manufacturers, which was used to confirm the control gear and LED light engine were not aff ected in any way by the magnetic field.”
80,056:
The number of magnets used to support fi ttings and cabling
A series of seven magnet mount types were designed and developed by Monard, the museum’s project team and the Ashmolean Museum’s mount maker. Over 2,500 magnet mounts were created, using more than 8,000 magnets and 48,000 overall components. At least five variations of each mount type were tested and modified to ensure a final bespoke solution for each luminaire and cable fixing. “The key success factor for this part of the project is that, even with all these components, the magnet mounting system is more or less invisible to the museum visitors and can also be taken out to leave no damage to the building structure,” says Francis.
The team also had to contend with high degrees of heat at a high level, caused by the glass roof. Temperatures can climb to more than 50°C, so the magnetic mounts were heat-tested on a purpose-built rig mounted inside an oven. They were put through their paces to ensure they could withstand temperatures up to at least 70°C, over a long period of time, as well as the eff ects of daily changes in temperature.
Restricted access
Every luminaire and its control gear had to be carefully positioned to allow for maintenance access for future replacements and testing. All control gear is mounted no higher than 12m due to restrictions on the size of the access platform that could be used, as the widest door into the building is only 1m wide.
“Lights and control gear are often in awkward places – this is standard in most buildings of this size – but not many buildings have to navigate dinosaurs,” says Francis. “We went to great lengths to install the control gear in the roof voids and in the clusters of the columns to achieve this, which meant redesigning the cable routes several times, as no more than two cables could be run on each side of the ironwork.”
All luminaires are dimmable and networked to a Zumtobel lighting control system, with an integrated central battery for emergency, designed in combination with Oxford-based M&E consultancy CBG Consultants. Day-to-day operation is fully automated with daylight control by a roof-mounted Skyscanner device that monitors the available amount and direction of daylight. For events, museum staff have wireless access to a choice of lighting scenes via an iPad.
Monard also recently relit the museum’s lecture theatre to an all-LED scheme, which is linked to the control system installed in the first phase. “I’m really passionate about the building and it’s fantastic to be able to have played a part in making such an amazing diff erence to the space,” says Francis.
The attention to detail has not gone unnoticed, including by the client. “For the first time the museum is benefiting from a well-designed lighting scheme that has attracted critical acclaim from external conservation bodies,” says Gregg. “The results are a testament to the commitment, passion and pride in the project of the whole team.”