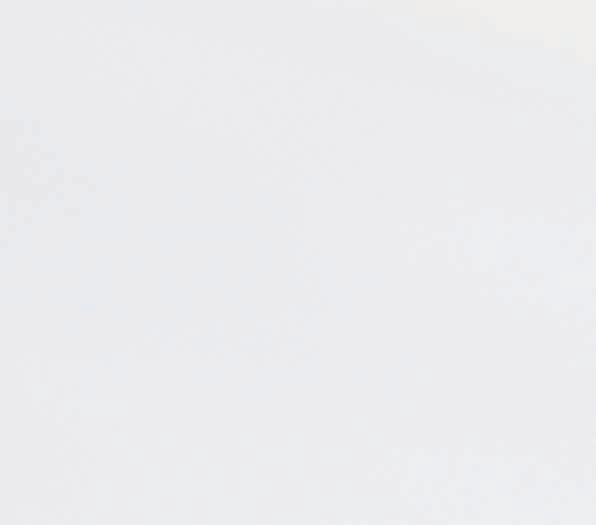
8 minute read
HIDDEN DANGERS
from Connections - Spring 2011
by NICEIC
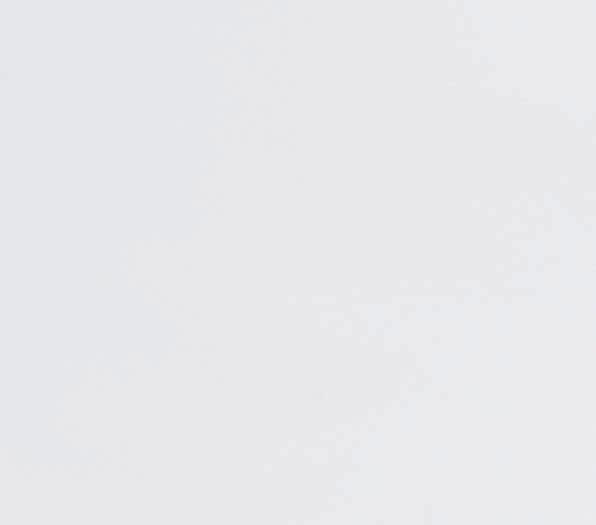
Electrical contractors could be unwittingly jeopardising their reputation and putting lives at risk by using unsafe cable. New initiatives aim to raise awareness of this threat
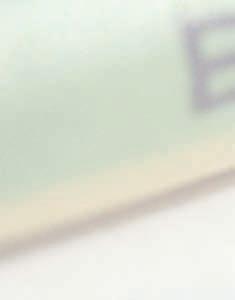
By Rob Shepherd
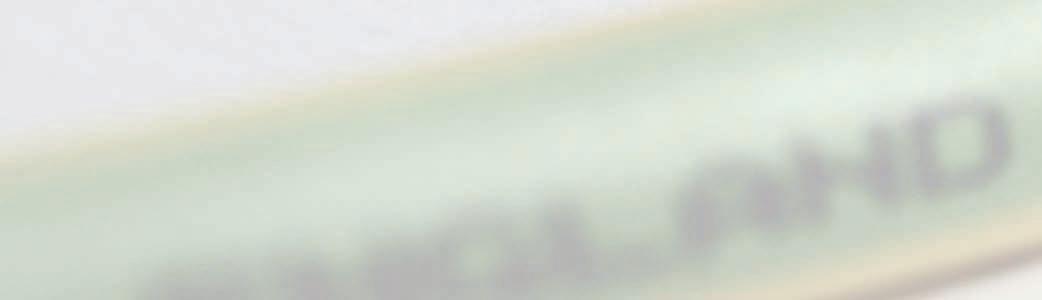

Electrical cable is the lifeblood of any building, but sometimes it is taken for granted. The UK electrical cables and systems market is worth about £2 billion, but the British Cables Association (BCA) estimates that 20 per cent of cable products are non-approved, unsafe or counterfeit.
There are a number of reasons for the growth in counterfeit cables, the main one being the escalating price of copper. At the end of 2010, copper prices hit an all-time high, well above the key $9,000 (£5,645) a tonne level. Unless you happen to be the owner of a copper mine, the problem is set to get even worse, with analysts and traders suggesting that prices could reach $12,000 (£7,526) a tonne on the back of the growing shortage.
As a result, a number of unscrupulous producers have cut corners and used less copper than required for the manufacturing process. Some have cut back the diameter of the copper wire too much, which reduces the current rating and increases the resistivity of the cable. This can result in overheating, which can lead to fire or reduce the level of safety against electric shock.
There have also been instances where materials other than pure copper, such as steel wire, copper-clad aluminium or badly recycled copper, have been used in cable manufacture.
For nearly 40 years the British Approvals Service for Cables (BASEC) has promoted independent cable testing and approval, and has been at the forefront in highlighting this important issue.
“The electrical contracting sector is very price-driven, but this must not be at the expense of safety and quality,” says Jeremy Hodge, chief executive of BASEC. “Cutting down on copper is one way that suppliers can cheat their customers, and to help stamp this out BASEC is conducting more unannounced spot checks on manufacturers and wholesalers. Efforts to expose these traders and manufacturers have been effective and more intelligence has been obtained about poor practices.”
But it’s not just down to the supply chain to be vigilant; contractors also have a significant role to play in managing this issue. “The potential risk to the public is a real problem and contractors have a responsibility not to compound the issue any further by ensuring on each and every job delivered that the specification is correct and it is followed through to installation,” says Michael Simms, president of the BCA.

Taking action
Last year saw the launch of the Approved Cables Initiative (ACI), which aims to educate contractors about the dangers of purchasing and installing non-compliant cables. It has received widespread support from industry trade bodies, including NICEIC, BASEC and BCA, and has pledged to name and shame suspect importers, manufacturers and distributors.
It is also lobbying government to enforce legislation, ensuring that only cables that fully comply with British, European or international standards and carry a third-party certification can be manufactured, distributed or installed in the UK.
Identifying a non-compliant or counterfeit cable is not always easy. While some cables carry no markings at all, the majority are fraudulently marked, showing standards and approvals for which they have no claim. They are clearly intended to mislead the distributor, wholesaler and contractor and it is often difficult to

> MAKING A MARK
LEAVING NOTHING TO CHANCE

Electrical cable should have the following markings to demonstrate that it is authentic and meets acceptable quality standards: • A manufacturer’s name and mark; • A British Standard (BS) number to signify that the manufacturer has confirmed conformity to this standard; • A BASEC marking if the cable has been tested by BASEC; • Harmonised cable and designation markings that denote the cable is harmonised; • A conductor size mark denoting the cross-sectional area of the copper conductor; • A letter attributable to its year of manufacture; • The cable’s country of origin; • A mark signifying that the core colours are in line with the rest of Europe. Source: Draka



BASEC


tell that a cable is not manufactured to the appropriate standard merely by looking at it.
The ACI is urging the supply chain to routinely check cable markings and reels, looking for a recognised manufacturer’s identification, so if there is a problem it will help trace the cable back through the supply chain. Companies that sell, supply or install unsafe cable are contravening health and safety regulations, could void their insurances and may also face serious criminal allegations, which can result in a custodial sentence.
Jim Duffy, chief executive of AEI Cables, believes it is important to emphasise the importance of traceability. “Contractors need to ensure that the cable specified has been correctly sourced and installed, and independently tested,” he says. “Wholesalers need to be clear that the products they are selling are fit for purpose and tested, while end-users should also work with the contractor to make sure that what is installed is working correctly and passes all relevant tests.”

Making progress

A recent example of the problems of non-compliant cable entering the market comes from the Turkish manufacturer Atlas Kablo, which was suspended by BASEC last summer.
Identified as underspecified and therefore unsafe, this manufacturer’s cable was the subject of a product recall and the cable is now in the process of being destroyed. However, despite this finding, some distributors are continuing to sell it.
Nicholas Wakefield, quality assurance manager at Eland Cables, suggests that, if in doubt, contractors should ask questions. “They should not be afraid to ask their supplier for relevant test certification and certificates of conformance to relevant specification should they have any concerns about the cables they are purchasing,” he says.
Firms that install fire detection and emergency lighting systems have to be especially vigilant that the cable they install can withstand the damage caused by a fire.
Eddie Bean, technical manager at Norfolk-based T&P Fire, believes that, when it comes to cable, if a deal looks too good to be true, it normally is.
“We are well aware of there being non-compliant cable on the market and would encourage any contractors to buy only from established and trusted sources,” he says. “In my experience there is no such thing as cheap, quality cable and anything that SOURCING COMPLIANT CABLE

NICEIC Approved Contractor WH Good, based in Rossendale, Lancashire, believes electrical contractors should be at the forefront of the battle against counterfeiters.
“The problem of non-compliant cable is very real and we have made sure that all of our staff are aware of the issue,” says managing director Phil Sumner. “Our supply chain management process means that we only ever buy cable from trusted wholesalers.”
Being able to identify that a cable has been through the correct tests and is marked accordingly is an important factor in ensuring that any non-compliant cable is identified straightaway, he adds.
“All of our team are asked to check a cable’s markings prior to installation,” says Sumner. “We know that anything that has a BASEC mark will have been through a rigorous third-party testing procedure and will perform as expected. However, we leave nothing to chance and our staff also perform tests at the end of the installation to make sure the cable performs as expected.”
claims to be is either counterfeit or stolen. I also think that most contractors are aware of this.”
BASEC’s Hodge urges contractors to become familiar with design codes such as BS5839, BS5266 and BS8519 to help determine the necessary grade of cable to use. “The key consideration is the length of time the electrical system must effectively operate after a fire starts while maintaining necessary levels of safety and protection,” he says. “Also, make sure the cable used carries a suitable approval marking.”
Contractors need to be well informed to reduce the chances of being fooled into paying good money for an inferior product. “As a time-served electrician myself I continue to be amazed at how little time is spent on learning about the different types of cables during formal training,” says Wakefield.
“Education is essential to ensuring that electricians understand the key parameters and materials that go into cable design,” he adds. “This knowledge would help promote the use of quality cables and the selection of the correct one for each installation.”
> Rob Shepherd is a freelance journalist specialising in the electrical industry
> FACTS OF THE MATTER
• 20 per cent of cable products in the UK supply chain are thought to be non-approved, unsafe or counterfeit; • 15 deaths have resulted from faulty electric cable in England over the past five years; • 1,200 non-fatal major accidents have been attributed to faulty electrical wires and cables over the past five years; • 27 per cent of all electrical fires are attributable to faulty wire and cables; • In 2007, 4,093 fires across England were attributable to faulty wires and cables in homes and businesses. Source: Department of Communities and Local Government
