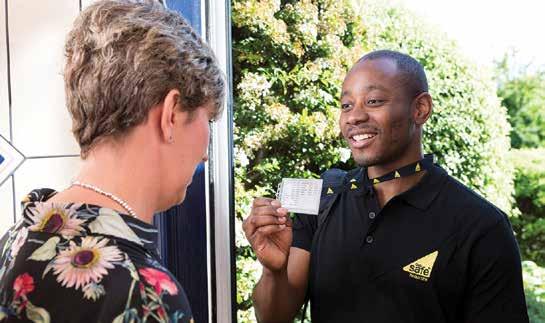
9 minute read
Unsafe Situations
The tale of a hidden horror
Are you sitting comfortably? Then we’ll begin. This is a story about an everyday job in an everyday gas engineer’s everyday life. And how they may have just saved their customer’s life. By Jon Palmer, Gas Safe Register Technical Support Officer.
Advertisement
It’s Monday morning and I’ve picked up my first job sent from the office. I’ve arrived at a small semi-detached house in a quiet close on the outskirts of town. The house seems well maintained and, as I walk up the path through the front garden, it feels like the gnomes are watching me.
The customer directs me through the small but tidy passageway to her kitchen. “The boiler’s in that cupboard,” she says, pointing to a larder unit in the corner. “It was fitted last year by a local chap. He was ever so nice, but he’s not turned up twice now to do the service, so I had to call someone else in. It needs to be done for the warranty, you see.”
I assure her it’s no problem as I put my toolbox down, and I open the larder door to take my first, cursory glance at the installation. At first sight, the installation seems to be OK. The pipes are straight, evenly spaced and clipped. There’s a magnetic filter fitted to the return pipe. And the condense has been run into 1½” waste pipe, which is then
taken out through the wall.
It’s then that I notice that the chimney/flue pipe doesn’t run straight out through the wall behind the boiler, but turns right, running above the other wall units in the kitchen and out through the back wall.
I hadn’t noticed this at first because the space has been covered with boxing – obviously to hide the chimney/flue, I think. “Did the boiler installer do that boxing?” I ask. “Oh yes, he said he’d hide that ugly old pipe for me,” the woman replies. “He said he’d make it easy to pop off though.”
While she makes me a nice cup of tea, I go out to my van to grab my stepladders, returning just in time to see a selection of biscuits laid out on a plate next to my steaming cuppa. I set up my steps, climb the first few rungs and take a look at the boxing.
It’s then that I notice a puddle of water on top of the wall unit. Feeling apprehensive, I grab a little handle that has been attached to the boxing and pull off the panel covering the chimney/flue.
Inside, I find a horror show. While the rest of the installation looks good, the chimney/flue most certainly is not. Only one clip has been fitted, installed to hold the first section in place. But there are no clips on the next three sections and, worst of all, two of those sections have come apart, spewing products of combustion into the property. There’s water all over the top of the units.
“Have you noticed water dripping down from up here?” I ask the customer, concerned as to if and how long she may have been being exposed to carbon monoxide.
“Sometimes,” she answers. “If the heating has been on a while, I seem to get water on my tiles at the back. I thought maybe it was condensation.”
I step down from the ladder and say: “I’m ever so sorry to tell you this, but your boiler is very dangerous, and I’ve got to turn it off immediately. Your chimney/flue pipe has separated, and the water you see at the back is actually water from the chimney/ flue. Have you been feeling unwell at all lately? Headaches? Any flu-type symptoms?”
“Well, I do get headaches sometimes if I’ve been in here cooking for the family,” she tells me, looking worried. “But I just thought it was because of the heat.”
“OK, that may be the reason, but I want you to get yourself to the doctor and get checked for CO poisoning. Do that now. Unfortunately, I’m going to have to cut off your boiler. Let me just check the Unsafe Situations book I have. I need to check whether this is RIDDOR reportable. You phone your doctor, and I’ll set about making you safe.”
As the customer goes off to phone her surgery, I grab my tablet and call up the GIUSP (IGEM/G/11 Gas Industry Unsafe Situations Procedure). I open the document and look down the sections till I get to the chimney/flue section. There it is, 6.2:
6.2 Leakage of products of combustion from room-sealed chimney system eg, evidence of products of combustion; leakage from the chimney/flue system; appliance or condensate air break. ID Where the affected property is one of a number of similar properties in a block or complex, include the approximate number of properties in the development in the summary of the report.
Also classify as ID signs of distress to material enclosing a concealed chimney/flue system with no evidence of subsequent corrective remedial work.
The tale of a hidden horror
And there, at the top of the page it explains about RIDDOR.
When considering whether an unsafe situation is RIDDOR reportable the following criteria need to be met: 1. The situation is as a result of the design, construction, manner of installation, modification or incorrect servicing of the fitting (often referred to as poor workmanship/design),
AND 2. It is dangerous to such an extent it is likely to, or has caused: death, unconsciousness, taking to hospital of a person. Note: See Section 8.6 for all other reporting routes.
Is the situation the result of the manner of installation of the fitting? Yes it is. It hasn’t been supported properly.
Is it dangerous to the extent that it is likely to cause death or unconsciousness? I’d say so.
Therefore, this situation is RIDDOR reportable as well as Immediately Dangerous. So, I follow the GIUSP and go to section 8 on RIDDOR reporting. Following the advice in this, I can see that this is a reportable under RIDDOR 11(2). That means I must do it online, within 14 days from today.
I locate the gas meter and isolate the gas, after first doing a tightness test to check that there are no further surprises in store. After that, I cut and cap the gas pipe below the boiler, stick a ‘Danger: Do Not Use’ sticker on it, and fill out a warning notice, exactly as I’m told to in section 6 of the GIUSP.
As I do this, I explain what I’m doing and why I’m doing it to my now very worried customer. After all, I can only do this with her permission. I’d hate to have to phone the gas transporter if she refused. I retest the pipework and turn the gas back on, so that at least she can use her cooker, and I notice there’s a gas fire in the front room for heating too. This, she assures me, is serviced every year by the local fire centre that installed it.
OK, that’s her safe: now I think I’ll do the RIDDOR report and get it out of the way. So, I get my tablet back out and take another look at section 8 of the GIUSP. There’s a link right there for the form I need to complete. So, I follow the link to the RIDDOR form. I fill in the form and submit it, happy that the poor workmanship of the fitter will be properly investigated.
While I don’t wish ill on any other engineer – after all, mistakes happen and I don’t believe anyone would do such a thing purposely – this type of incident must be reported to the relevant authority. If this doesn’t happen, the installer may not know that what they did could have had fatal consequences. Hopefully, they’ll think twice about cutting corners again.
As I wish my customer well, genuinely hoping that she is going to be OK, I feel good about myself, secure in the knowledge that today, I may just have saved a life. As I leave, the sun starts to shine. Is it my imagination or are those gnomes smiling? ■
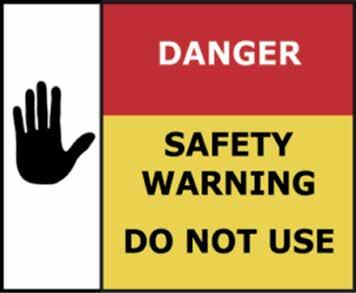
Unsafe Situations Procedure: what’s new?
Gas Safe Register’s recent Open Channel live discussion was all about the updates to the Gas Industry Unsafe Situations Procedure. The procedure, which was revised in January 2021, has evolved based on feedback from gas engineers themselves, as well as the wider industry, said Dave Bendle, chair of the Unsafe Situations Committee.
The document’s aim is to create a robust way for gas engineers to make a risk assessment on their particular situation. It has evolved as the situations that gas engineers and Gas Safe Register inspectors find have changed over time, and the revised procedure brings further clarity on key areas. These include RIDDOR reporting, the tables that provide examples of the situations that engineers might find, an updated flowchart to help gas engineers choose the correct classification, and information about how to report unsafe workmanship that is not reportable under RIDDOR.
The Open Channel panel explained that the update helps to clarify the requirements of what and how to report under RIDDOR. They said that considering the potential outcome of the installation or appliance in front of them should help to guide gas engineers as to whether they should report under RIDDOR or whether they should report unsafe workmanship to Gas Safe Register to be investigated and dealt with.
Rob Denman, Gas Safe Register’s head of Technical, said: “To report unsafe gas work to Gas Safe Register, you can now log into your online account and notify this, and Gas Safe Register will follow up.”
There’s a new section that deals with reporting the theft of gas, providing information on who to inform, even if the situation is not unsafe.
The updates to the procedure have been shaped by the experiences of working gas engineers and from organisations in the industry, including Gas Safe Register. Rob Denman highlighted that some of the updates have come as the direct result of calls that registered engineers have made to the Register’s Technical Helpline, and from information gathered through inspections, investigations and complaints, and from RIDDOR.
IGEM’s Ian McCluskey said: “IGEM wanted to draw out clarity on RIDDOR and on what is required of a visual inspection.”
The updates will have an impact on training and assessment too. Trevor Smallpeice, representing the Standards Consultation Forum, said it’s essential that training and ACS reflect what’s in the procedure. This highlights the importance of the panel that puts together the updated procedure receiving information from as wide a range of industry organisations and engineers as possible.
You can download the updated Unsafe Situations Procedure from IGEM and from your Gas Safe Register online account. A new app will be available soon too.
You can see this discussion and previous Open Channel live events by joining the Open Channel from Gas Safe Register group on Facebook.
The Open Channel Panel on Unsafe Situations was:
Scott Darroch, Head of Strategic Communications & Engagement, Gas Safe Register Rob Denman, Head of Technical, Gas Safe Register Ian McCluskey, Head of Technical and Policy, IGEM Dave Bendle, Chair, Unsafe Situations Committee Trevor Smallpeice, Standards Consultation Forum