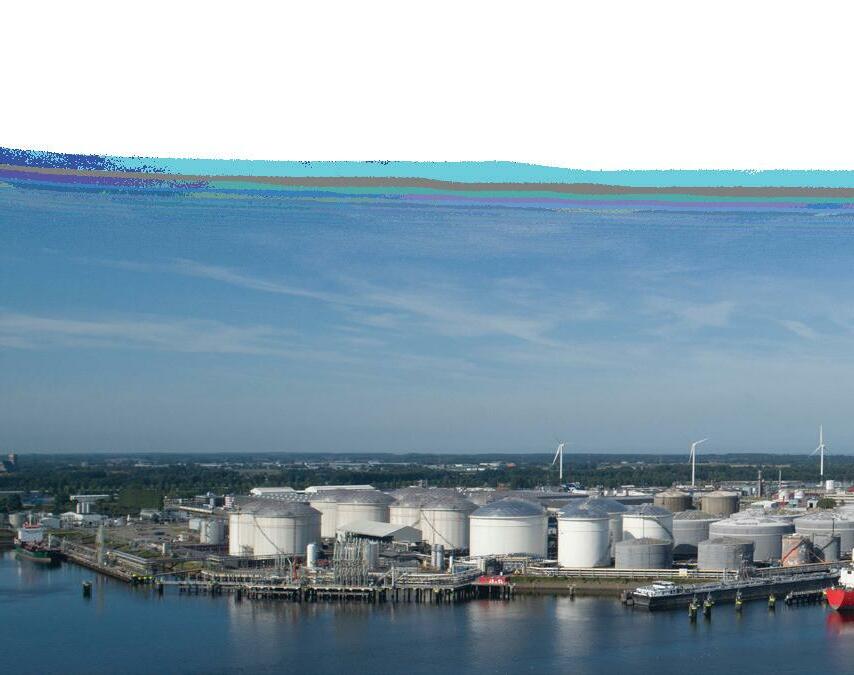
4 minute read
Risk Management & Safety Course
from NISTM Program Guide 2022 - 24th Annual International Aboveground Storage Tank Conference & TradeShow
StorSafe – Terminal Risk Management & Safety Course
NISTM CO-LOCATED EVENT April 11, 2022 | 8:00am – 5:00pm
This eight-hour risk management course is designed specifically for midstream facility owner-operators. Candidates could include area managers, facility managers, as well as facility operators as well as any other stakeholder that wants a better understanding of hazard assessment and risk management at a typical midstream facility.
The course content is prepared in a series of modules with a quiz at the end of most modules to ensure comprehension. Course will begin with a discussion of the concepts of risk and understanding that the setting of a level of risk tolerance is often organization specific. We will review key definitions and the typical hazards in a petroleum facility. Greatest risks occur during product transfers as there is risk of overfill as well as the potential for releases when transferring for out-of-service inspections.
We will discuss in detail confined space entry including the responsibilities of the entry supervisor as well as the different types of confined spaces and application of hierarchy of controls to confined space work. There will be a section on emergency planning and rescue associated with facility maintenance and repairs and a discussion of the controversial issues related to use of certain often optional personal protection equipment. The course will conclude with an understanding of DOT PHMSA as it relates to operator qualification compliance, drug, and alcohol testing, as well as a review of strapping requirements and return-to-service. There will be an opportunity after each module to ask questions and there will be a question and answer at the end for any related topics of interest to the candidates.
SPEAKERS
Earl Crochet, PE
• Principal of Crochet Midstream Consulting LLC & Executive VP of Perceptive Sensors Technologies • 32 years of Owner-Operator Experience with Plantation Pipe Line and Kinder Morgan since 1988 • Various Roles in Engineering, Measurement, Quality, Operations, Maintenance, Asset Integrity, Project Management, EH&S, Business Development, Management • BS in Mechanical Engineering from LSU –1986
David Cushman, CSP
• General Manager, West Virginia Paint LLC since 2001 • Midstream contractor installing protective coatings with same organization since 1980 • BS Economics, Univ. of Pennsylvania, 1980 • AAS Mechanical Engineering Technology, 1988 • MS Occupational Safety, SSEM, Eastern Kentucky Univ. 2010 • Certified Safety Professional CSP-38923 • OSHA Outreach Instructor, Construction 10 and 30 hour, #12-000196378 • Chair - API 2015, 2026, 2207
MODULES
1 | Introduction Safety share, introduction of presenters, and introduction of modules and learning objectives of each
2 | The Goldilocks Story
(or is it the Three Bears Story?)
There are lots of lessons to be garnered from this 19th century tale. By looking at Goldilocks and her antics with the three bears we can understand how level of risk acceptance is not absolute, but relative, and this will help understand when processes and procedures are required, recommended, or merely suggested.
3 | Definitions Some highlighted definitions are essential to understanding hazards in the facility and often misunderstandings can lead to errors.
4 | Hazards in the Plant This module is a thorough examination of potential hazards found in a terminal, many of which that are often overlooked, along with a mitigation strategy applying the hierarchy of controls.
5 | Product Transfer The risks are highest when product is transferred. This module looks at the requirements of the latest edition of API 2350 for overfill protection as well as mitigating hazards when transferring product by vac truck and when tanks are being opened and cleaned.
6 | Confined Space Entry 6A | Atmospheric Monitoring 6B | Floating Roof Safety 6C | Tank Cleaning 6D | Inspection and Repairs Many aspects of confined space entry are often misunderstood. OSHA programs follow the hierarchy of controls, which underlies all good safety practices. By understanding how the hierarchy of controls should be applied to confined space entry, there is a better understanding of the differences between permit required and non-permit required confined space as well as use of alternate procedures under the OSHA standard. We examine the different aspects in thorough detail. 7 | Emergency Planning and Confined Space
Rescue
Expect the unexpected! The better that you can plan or anticipate emergencies and their consequences, the better prepared you are to deal with them when they occur.
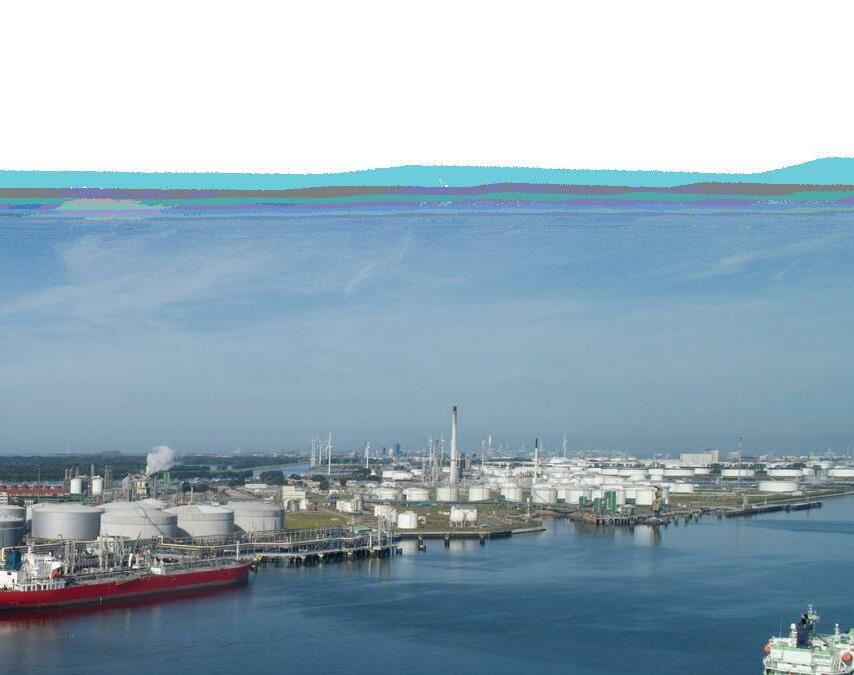
8 | PPE Discussion This discussion centers on personal protective equipment and other equipment that is commonly used in the facilities, but not universally treated with the same risk acceptance level. This includes cell phones, gloves, and fire retardant clothing as well as other commonly used items. We will explore the “gray” areas of safety equipment selection that vary from facility to facility.
9 | PHMSA, OQ, Drug Program Compliance and
Return-to-Service
PHMSA and DOT affects many facilities, even if the entire facility is not subject to DOT. The failure to follow these regulatory requirements may subject the facility to citations. As with many regulations, there is not always a defined path forward and this module discusses the OQ rule as it applies to different tasks as well as the drug testing requirements in detail. It includes a review of strapping and strapping schedules as well as risk mitigation when performing a return to service.
10 | Quiz Review and Open Q & A We will do a review of the quiz answers to make sure everyone understands the material. Next, we will have a chance for anyone in the class to ask about any related topic that might need further explanation or was not included in the core course material.