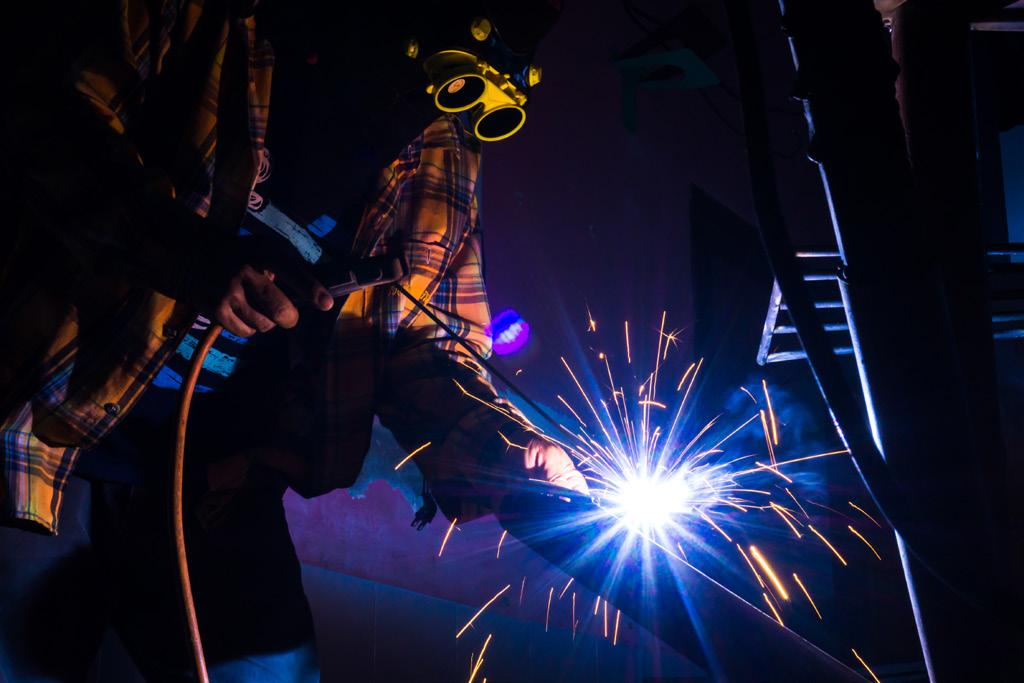
5 minute read
Complete Health, Environmental & Safety Services (C.H.E.S.S.)
Hazards in a Flash: WELDING
By Janet L. Keyes, CIH
We predict that more than half of them will say yes. And we can predict their answers when you ask them what caught fire. Rags. Parts of cars, such as foam insulation and carpeting. Their clothing. Themselves.
Another question to ask your technicians: “Have you ever had welder’s flash?” Don’t be surprised if nearly all of them say yes. Ask them how it happened. Sometimes, it’s because someone else was welding near them. Sometimes, it’s from the radiation reflecting off a nearby wall. Sometimes, the battery on their autodarkening welding helmet gave out. And sometimes, inexcusably, they decided to weld without eye protection.
What is welder’s flash? It’s photokeratitis – a burn on the lens of the eye caused by the intense ultraviolet radiation from welding (too much sun, particularly when reflected off snow or water, can cause it, too. In that case, it’s called snowblindness). It usually isn’t felt immediately. Instead, symptoms often show up at night, hours after the exposure occurred. Welders report it feeling like ground glass or burning sand in their eyes.
Fires cost you money. Employees who need to take time off work because their eyes hurt aren’t productive. Don’t underestimate the hazards of welding.
Welding hazards aren’t limited to fires and welder’s flash. Electrical shock can occur, especially if cables and connectors are damaged. The ultraviolet radiation can cause skin burns, just like a sunburn. The heat can cause thermal burns. Breathing in the fumes can damage lungs and increase the risk of lung cancer. If the metal is galvanized (zinc-coated), getting a big noseful of the fume can lead to metal fume fever. Several hours after breathing in the zinc fumes, the welder will start feeling like he’s come down with the flu – achy, feverish, chilled. That usually requires a day or two off work to recover.
It’s all very well and good to say how hazardous welding can be. What can you do about that? Stop welding? That isn’t realistic. Instead, think about ways to reduce the risk.
Don’t let welding burn down your shop. The Minnesota Fire Code requires that welding either be done in areas authorized for that purpose or that a hot work permit be filled out each time anyone welds (and
the permit just means you take the steps to make an area safe for welding). What makes an area safe for welding? Flying sparks or slags won’t hit anything that burns easily. Floors are kept clean. Walls and partitions won’t burn. There’s no welding or torch use on containers that hold flammable liquids or gases unless those have been thoroughly cleaned or purged. You have a fire extinguisher at hand, with people trained on how to use it.
The body shop or mechanics’ shop can be a designated area for welding. But you need to keep things that easily ignite out of the area. Keep aerosol cans and body filler on tool chests, not on the floor. Limit how much of those are out in the shop. Make sure rags are picked up and put into closed metal containers. Check that the extinguisher is close to hand.
If you’re welding on a car, try to fire-proof it. Can you remove any interior components, such as foam-padded seats? If you can’t remove them, use welding blankets or welding and spark deflection paper to cover it up. That adds to the cost and time, but you’ll make it up by not having to replace the vehicle.
Of course, don’t allow any welding in painting and priming areas.
Make sure welders dress appropriately for the job. As the employer, you are responsible for providing the required personal protective equipment. Even for quick welding jobs, that means welding helmets and leather gloves. Leather jackets keep sparks from burning clothes and skin. Is a respirator needed?
Those in the area need to be protected from the flash. The best option is to set up welding screens. The screens block the ultraviolet radiation and sparks. If that isn’t feasible, at least require everyone in the shop to wear polycarbonate safety glasses; teach them to look away from welding; and train welders to alert others in the area when they’re about to weld. If they’re helping someone who’s welding, they need the same level of protection, including a welding helmet, as the welder.
Don’t allow technicians to burn off coatings. Grinding them off is much safer. Only bare metal should be welded. Solvent residues and coatings can create toxic fumes.
How can we ensure welders don’t breathe too much of the fume? Welding helmets block some. Having good general ventilation in the shop provides some protection. But if anyone does a lot of welding, wearing a respirator with N95 or P100 filters is a good idea. And you must include that person in your respiratory protection
program – getting medical approval for respirator use, training them on correct care and use each year, and fit testing.
Welding is hazardous. We can’t eliminate the hazards, but we can mitigate them. If your technicians need to weld, remind them of what they need to do to weld safely. Better to take five minutes now, instead of rebuilding the burned-down shop later.
For more information, contact Carol Keyes at (651) 481-977 or carkey@chess-safety.com.