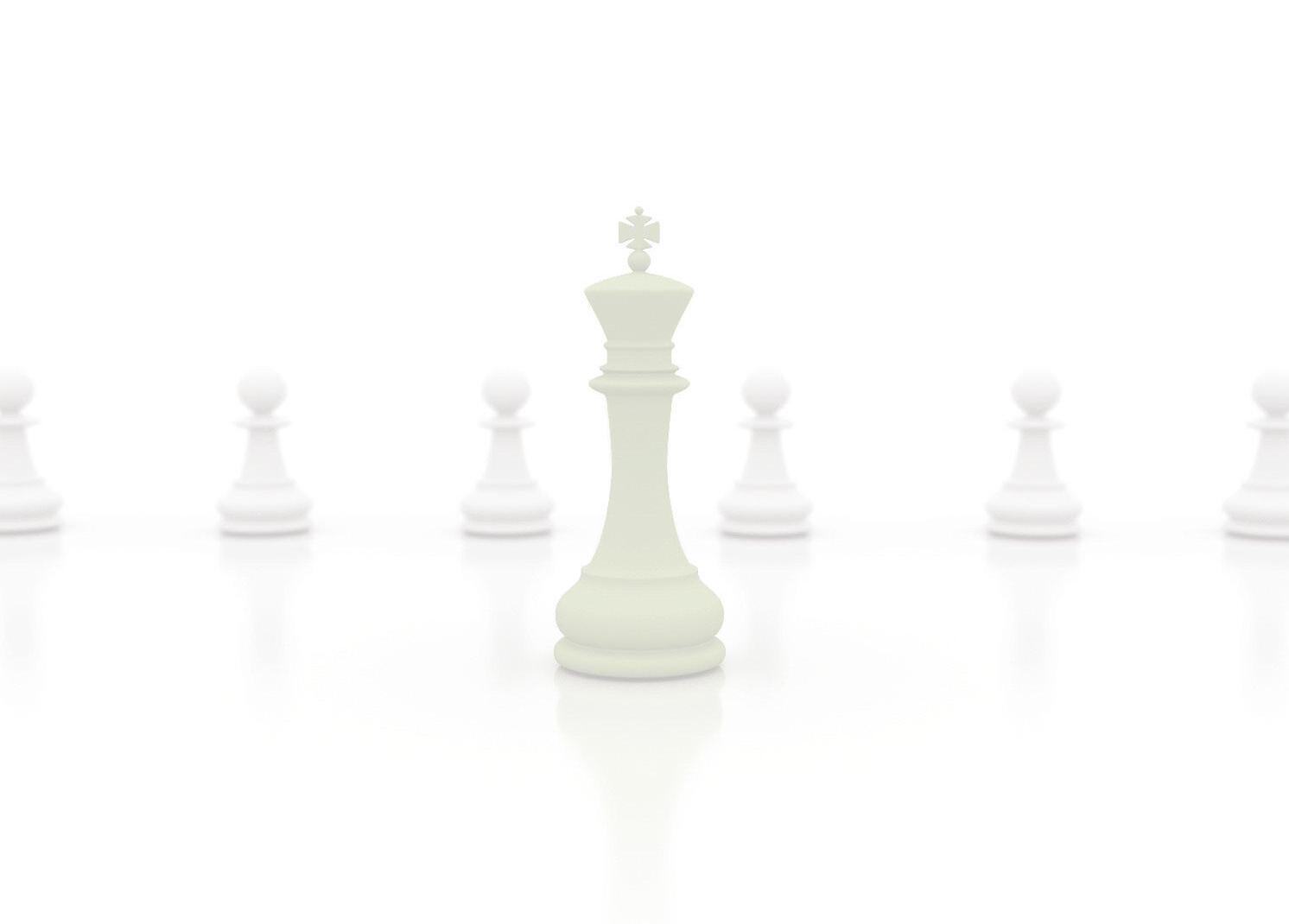
3 minute read
Report! Record!
By Carol A. Keyes, CSP and Janet L. Keyes, CIH
Has any employee ever gotten a scratch? Something in an eye? Stubbed a toe? Received a paper cut? Would you report that to your insurance company? I doubt it, but if it happened at work, you should.
Imagine the worst: The scratch and paper cut become infected with flesh-eating bacteria; the stubbed toe is broken and just won’t heal. Gunk in the eye leads to a weekend emergency room visit. These no-bigdeal injuries are now days of lost work time, many dollars of medical expenses. And because your workers’ comp carrier never heard of these injuries until they blew up, the insurer questions if they really are work-related – and if they are, why you didn’t report them right away. That could saddle the employee with a big medical bill, a lot of ill will, and maybe even a visit to an attorney. The insurance company could end up paying a fine for late reporting, a cost that will certainly be passed on to you.
Most of the time, that scratch and stubbed toe and paper cut and eye heals quickly. Most of the time, those minor injuries stay minor. If you report them to workers’ comp, your insurer will open a file and then close it, with no costs incurred and no penalty given to you.
So, why should you go through the effort of reporting these minor injuries? We gave you one reason: In case they turn into something major. If the employee ends up in the emergency room over the weekend, both you and the employee are covered.
Keeping track of those minor injuries helps you identify patterns. If you have one employee with something in the eye, you might attribute it to clumsiness or working under a very rusty car. But what if five employees report something in their eye? It might be time to look at what’s causing that. Maybe you need to rethink your policies on safety glasses in the body shop.
You might be tempted to just pay out of pocket for that weekend emergency room visit. But that isn’t allowed under the workers’ comp law. You could end up paying more in premiums, paying penalties and even have your insurance canceled. And if something goes wrong – if the stubbed toe becomes infected and requires hospitalization – you could be on the hook for high medical costs, too. Protect yourself and your employees by submitting injuries to your workers’ comp carrier.
What do you do with all these minor injury reports? Track them and review them. Look for trends.
You can track them on an OSHA 300 log or another spreadsheet. Record the facts: Who was involved, what happened (stubbed toe on vehicle hoist), when, what task was being done, what was the injury. It is easy to forget what happened five months ago, but now you can look at your spreadsheet for any common issues or concerns.
Now that you’ve identified a problem trend, how can you correct it?
Talk with your employees in your next safety committee meeting. What safety committee, you ask? The one that you now must have. A new law in Minnesota requires it for every company that falls under the AWAIR (A Workplace Accident and Injury Reduction program) standard. Formerly, all companies with 25 or more employees needed a safety committee. There are some exemptions for lower-hazard companies with fewer than 10 employees. All automotive repair facilities (collision and mechanical repair) are required to have AWAIR programs – so start forming your safety committee.
So, how do you start a safety committee? What should it do?
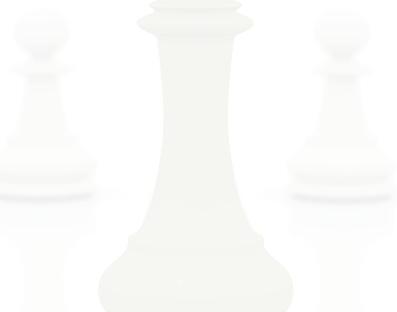
Do you meet with your employees for production or other staff meetings? Once a month or every other month, add time to discuss safety issues. Have a set agenda, ask for input and take notes. Voilá – you have a safety committee. If you’re a large shop, it may make sense to have a handful of employees (some from each area) make up your safety committee. But small shops can have committees of the whole.
This could be your agenda:
• Any recent injury or near-miss. How can you prevent recurrences? (For example, safety glasses, replacing damaged ladders, wearing gloves…);
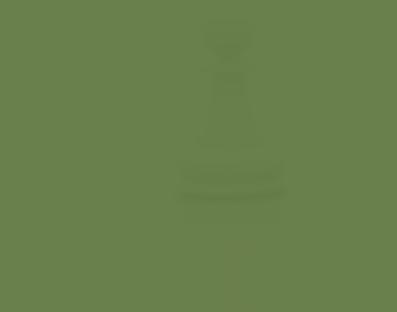
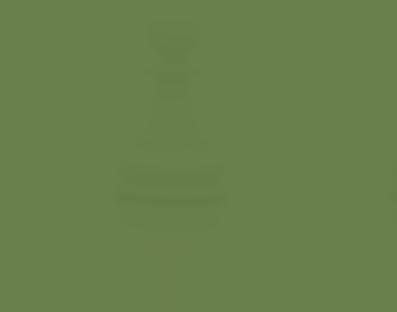
• Issues seen when you walked through your facility – blocked fire extinguishers, expired or used eye wash station, electrical panels blocked, etc.;
• Discuss a recent safety article from AASP-MN News, such as safe storage of tires or welding hazards; and
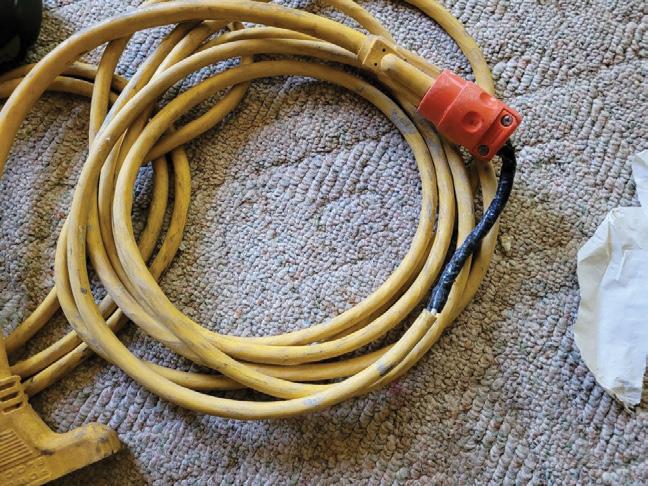
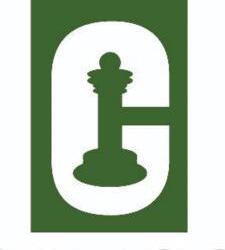
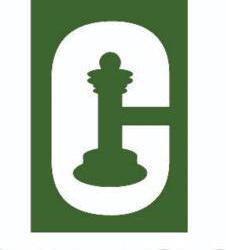
• Safety concerns from employees.
Take notes of what was discussed, who attended, and any decisions made. Post them on your employee bulletin board.
Linking the AWAIR standard to safety committees is new. As we write this, MNOSHA has not yet updated its website with information about it, but that shouldn’t stop you. A safety committee is easy enough to implement, and it can lead to a safer workplace – and a safer workplace is a more productive workplace. Safety pays. For more information, contact Carol Keyes at carkey@chess-safety.com or (651) 481-9787.
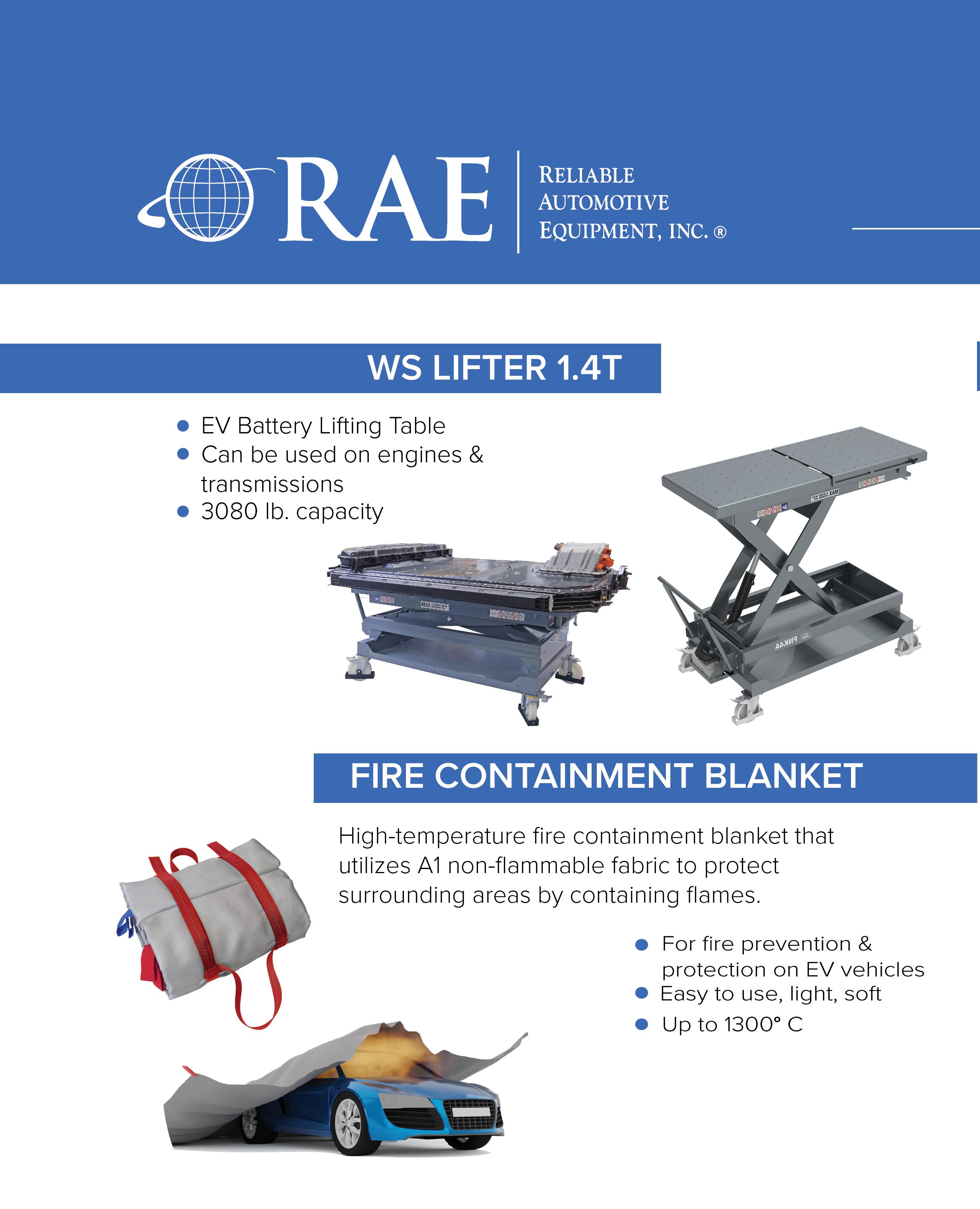
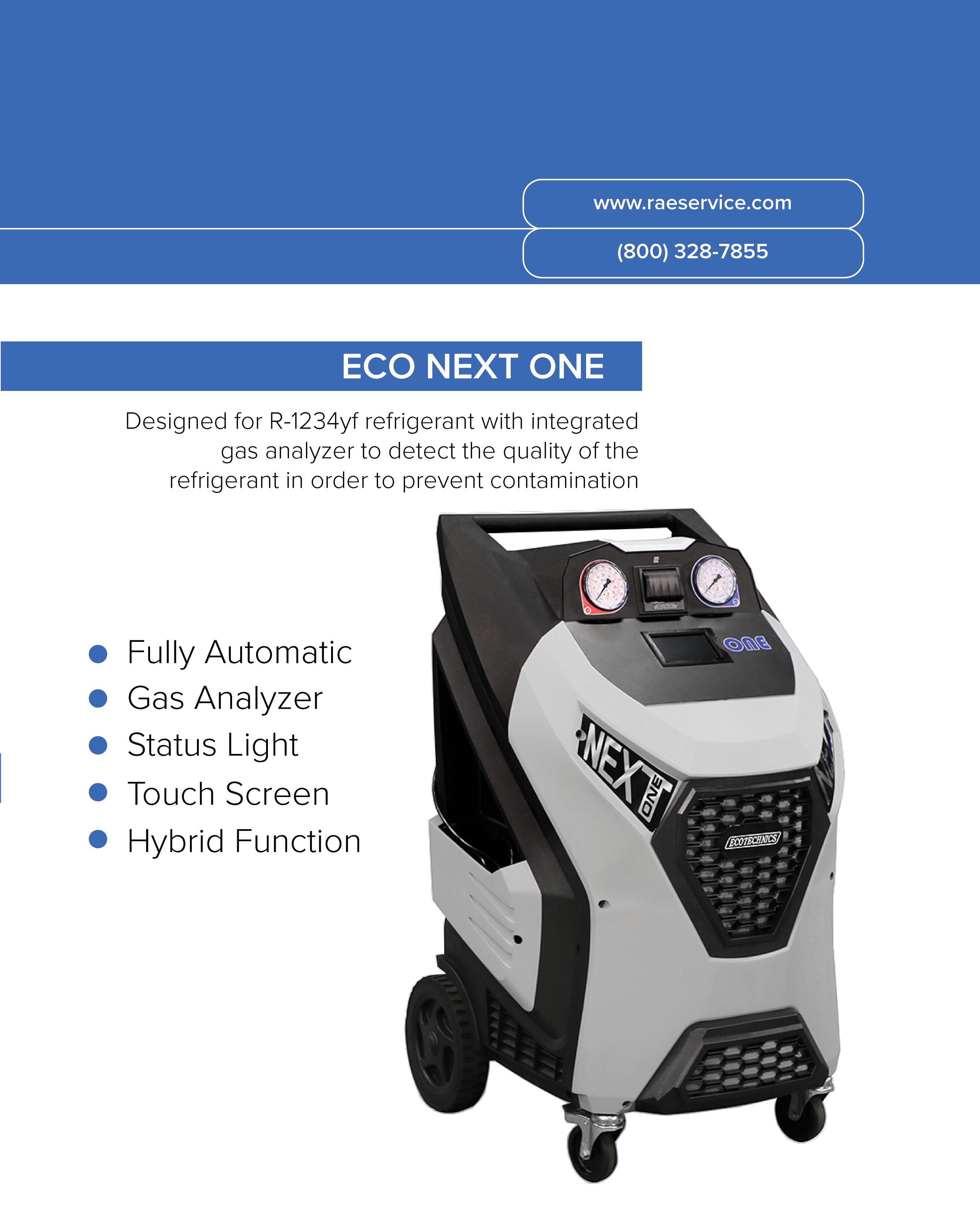