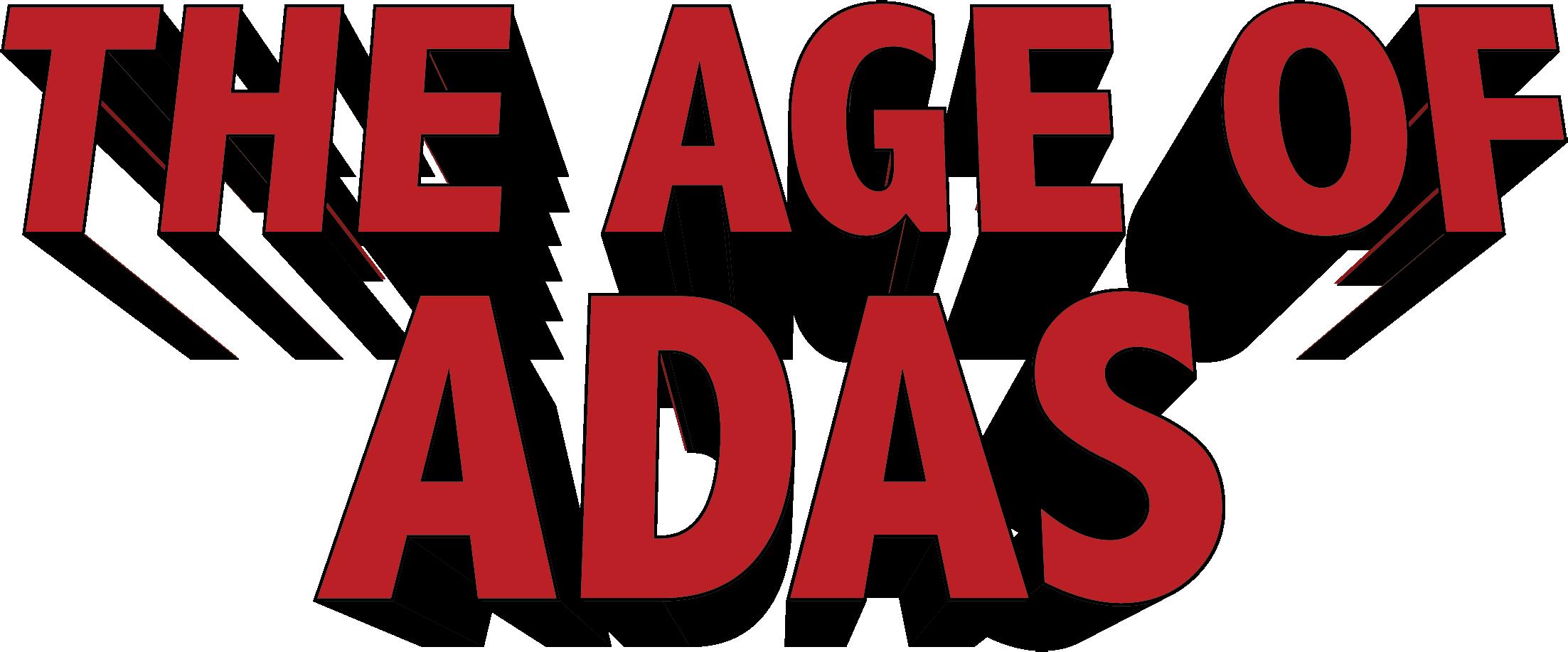
7 minute read
COVER STORY
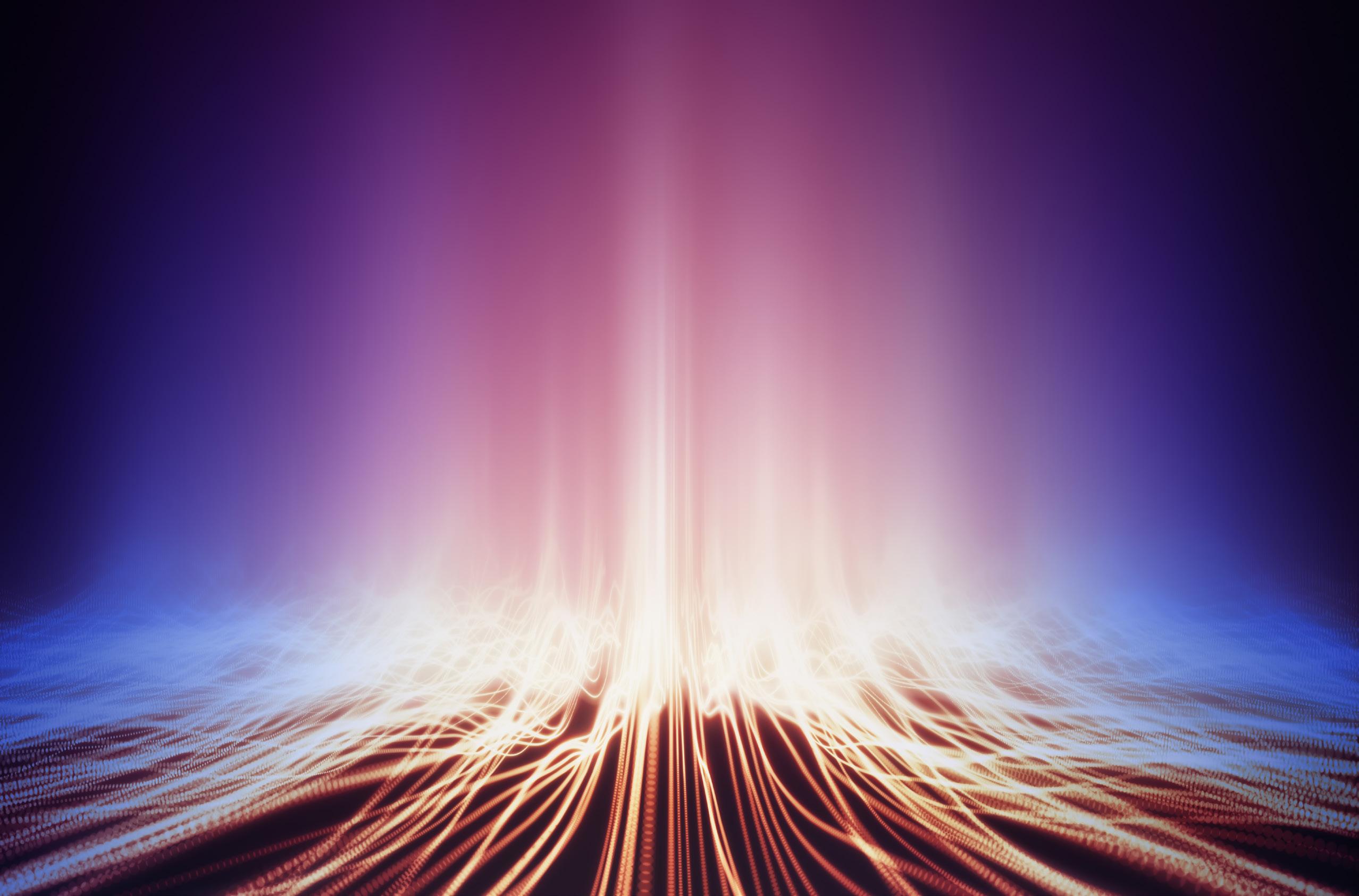
Realities, Recommendations and Roadblocks
There’s never a dull moment in this industry.
Ten years ago, nobody could have predicted the technical, training and procedural demands now hitting the collision repair and auto service industries. These days, performing professional work isn’t just a matter of fixing the damage you can see; it has to do with extensively researching OEM information and identifying hidden issues through the use of specialized tools. This is the era of ADAS, scanning, diagnostics and calibrations – a time that has led many within the AASP-MN community to drastically restructure the way they work on vehicles.
It’s been roughly a decade since automakers began strongly encouraging (and, in many cases, outright requiring) pre- and post-repair scanning procedures. Shannon’s Auto Body in Brainerd hit the ground running early in the trend by incorporating scanning back in 2012. About five years later, the I-CAR Gold facility took things a step further by moving exclusively to OEM software to complete these tasks.
“We had a few different scan tools, and it got to the point where one scan tool wouldn’t pick it up but another one would,” owner Shannon Christian recalls. “When we went to OEM software, it scanned everything.”
In 2015, the shop’s capabilities expanded through the addition of a dedicated mechanical service department. This has enabled the shop to speed up the process while still adhering to manufacturer standards. In Christian’s mind, the reason to invest the time and resources necessary to do OEM-level scans and ADAS-related work was simple.
“We don’t want to put somebody back in an unsafe car.”
When AASP-MN member Chad Bijou opened Waconia 1 Collision & Auto in Waconia in July 2020, he made sure that he had a game plan to address modern vehicles. Currently, the hybrid collision/mechanical I-CAR Gold facility performs 75 percent of its ADAS work under its own roof and meets the requirements of four OEM certifications through accessing and utilizing OEM information and procedures.
“All the guys [here] have been scanning cars since [the OEMs] first started requiring it. Everyone who’s here had worked for me in the past, and they were pretty familiar with my style of management.”
To help things move in the right direction, he keeps his main mechanic involved in auto body repairs.
“The technicians will do the pre-[repair] scans when writing the estimates, but my mechanic will do the post[repair] scans, because he’s more in tune with what was done to the car and what needs to be looked at and whether or not there’s a calibration that’s required.”
Over at I-CAR Gold shop Ed’s Collision in Maple Grove, General Manager Shawn Hartner utilizes the services of Prior Lake-based AASP-MN member The
Flasher_Scope & Scan Diagnostics LLC to have proper calibrations performed on customers’ vehicles as per OEM requirements/recommendations and hit the benchmarks set by his eight automaker certifications.
“It’s a tremendous asset. Usually, I can get them out here within a half hour to 45 minutes to do that scan or recalibration, and I can get that car out that day. At the dealership, you’d have to call and make an appointment, and then [the vehicle] sits there for a couple of days.”
Body shops aren’t the only ones embracing evolving technologies. Although the need to perform ADASrelated procedures is still a rarity at his facility, AASP-MN President Tom Archambault of BLVD Autoworks in St. Anthony does encounter it in cases where a bumper needs to be removed (to address a leaking radiator, for example) or a sideview mirror with sensors needs to be replaced. Like Ed’s Collision, Archambault’s facility uses The Flasher to complete these operations, as the current frequency of such work doesn’t demand in-house specialization.
“We will adapt; we will get there as time goes on. But right now, it [makes sense] to us to outsource servicing those systems.”
In business for eight years, The Flasher owner Matt Batulis and his team of technicians provide ADAS relief to approximately 160 shops each week. Although his service began as a mostly mechanical-facing endeavor, he has seen considerable growth in the collision side of his business in the past four years. These days, 70 percent of his work comes from body shops – an indication that these businesses are looking for streamlined solutions to fulfilling OEM repair requirements/recommendations.
“We only use factory scan tools. We use factory service information and the factory targets.”
Perhaps most significantly, The Flasher has assisted mechanical and collision shops in better ensuring that vehicles are returned to customers in the condition the manufacturer intended. This is a welcome service at a time even the most forward-thinking shops struggle to find the qualified and properly trained help needed to meet various automaker technical guidelines.
“People don’t spend the time or they don’t know how to look up the service information. When they’re writing estimates, a lot of times they don’t know what they’re looking for.”
Of course, nobody in the automotive repair/service field shows up for work every morning expecting to work for free. As vehicle technologies continue to escalate, third-party payers have been notoriously reluctant to both acknowledge the necessity of certain procedures (including research and inspections) and actually provide adequate compensation for them.
“The biggest feedback that we’re getting is, ‘Why are we paying you to do something that nobody else is doing? It’s not needed,’” Christian shares. “We try to explain to them that this is required. We’re looking up procedures on every vehicle that comes to the shop. We explain that to the adjusters and tell them, ‘These are the inspections that are required, and we’re actually doing them. This is what it is.’ We are getting paid on the majority of them, but there are still a few insurance companies that refuse to pay for inspections and research on stuff and say that it’s ‘not standard and customary in the marketplace.’”
“Our estimators spend a lot of time documenting and making notes on why we’re doing what we’re doing based on OEM procedures,” Ed’s Collision owner Mike Cox adds. “A lot of times, the third-party payer does not want to pay for certain operations – even though they’re OEM-required – just because they don’t think them necessary. It’s up to us to document why we’re doing what we are to get paid.”
While mechanical work is typically free from insurer control in terms of pay, Archambault notes that there are instances where warranty providers fail to fully cover ADAS operations on his side of the fence.
“We are almost solely customer pay. We do work with warranty companies as necessary; we have no problem doing that. But even in an instance like an extended warranty, we have no problem telling the customer, ‘This is what was covered; this is your responsibility.’”
Although it’s fair to suggest that outside parties need to step up and do the right thing, the same can be said for more than a few shops that still refuse to embrace the changes occurring around them. In blunt terms, plenty of shops are still not taking the time to pull OEM repair procedures, let alone do proper scanning and calibrations and give ADAS the professional attention it deserves. Cox is one shop owner whose mind boggles at this reality.
“Some things are so basic. If you’re going to remove a battery from a car, it matters which cable you take out first – the negative or the positive. That could be different depending on the model and make of the car. If it wipes out the computer, you’ll have to buy a new one because you hooked up the battery cables wrong. That’s basic, but who knows what other things are out there unless you go look them up ahead of time?”
Hearing Cox’s words, this writer was reminded of a recent conversation with a shop owner (thankfully not in Minnesota) who scoffed at the idea of having his techs pull OEM information for every repair.
“My guys have been working on these types of cars for years. They already know what they’re doing.”
Frankly, these words nearly knocked me off my chair – and illustrated how much work still needs to be done to get the entire industry on board with what it means to perform a true repair these days. Christian has a clear response to any owner out there who’s tempted to feel the same way that particular owner does.
“I’d ask if their business is for sale, because they should not be doing auto body anymore.”