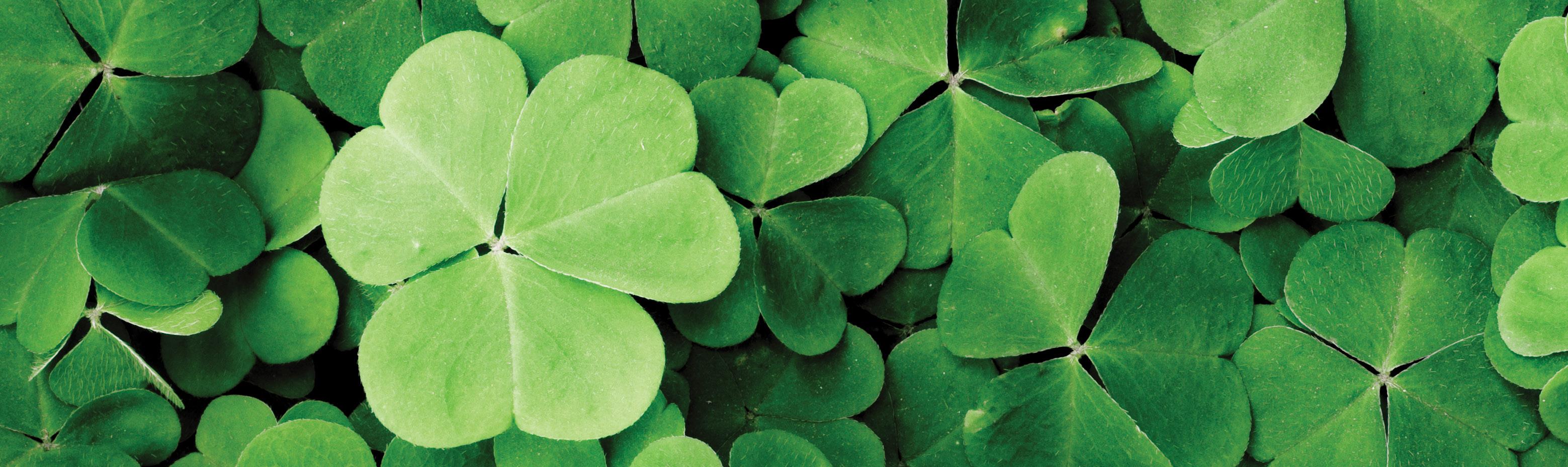
5 minute read
COMPLETE HEALTH, ENVIRONMENTAL & SAFETY SERVICES C.H.E.S.S
Don't Trust to Luck
by Janet L. Keyes, CIH and Carol A. Keyes, CSP
A review of OSHA’s fatality and catastrophe records for the automotive industry shows some consistent patterns.
Employee is killed by falling vehicle and lift.
Employee’s finger is amputated by fan belt.
Bad luck, you say? That implies that it was unavoidable. We’d argue it was the absence of good luck. The employee who lost a finger to a fan belt probably wasn’t doing anything new. He/she got lucky the other times. This time, his/her luck failed. When the same hazard is present time and time again, we should figure out how to prevent it instead of hoping luck holds.
In December 2019, in Houston, TX, an employee was working under a vehicle on jack stands. A customer backed their car into the raised vehicle, knocking it off the stands. The employee was crushed and killed. The falling vehicle pinned another employee against a wall, injuring his hip and leg.
We are safety geeks, so I’ll point to a failure of energy control for both the fan belt amputation and the fallen car. Lifting a vehicle, whether on jacks or with a vehicle lift, subjects it to gravity. The jack or lift relies on hydraulics to circumvent gravity. The car’s motor kept the fan belt spinning around. If we only had controlled that energy, the finger would remain attached, and the technician wouldn’t have been killed.
Everyone who has been trained on working with hybrid or electric cars has learned about controlling hazardous energy. They’ve learned to turn the car off, remove the key and, wearing electrical insulating gloves, disable the battery pack. Then they wait to let the capacitors discharge.
You should apply that same idea of hazardous energy control to all repair operations. Changing a grinding wheel? Unplug it, so you don’t hit the start button by mistake. Need to work under a car? Hydraulics can fail, so use jack stands or a vehicle lift equipped with safety latches. Of course, you still need to make sure the car is correctly balanced on the lift. Hazardous energy control procedures aren’t fail-safe.
What if you’re replacing the ballast in a light fixture? That’s the type of simple electrical repair that a lot of unqualified people do. It killed a Virginia man in June 2019 – “he was replacing a ballast in a fluorescent light fixture when he was electrocuted.” Turning off the light isn’t enough because someone else can easily flip it back on. What should have been done: turn off the light at the breaker and then lock it out, pocketing the key to the lock so no one else can turn it on.
When we think about lockout/tagout or control of hazardous energy, it’s electricity that most often comes to mind. But the moving fan belt has kinetic energy. The raised car has gravity. The energy in a pneumatic tool is from air pressure. Energy can be mechanical, electrical, hydraulic, pneumatic, chemical, or even thermal. In some cases, it can be controlled simply by turning the equipment or machine off (and making sure it cannot be turned back on). Sometimes, blocking or bleeding is the right approach. If you’re working on a pressurized system, bleeding off the pressure is energy control. If you’re working under a car, blocking the wheels is energy control.
You aren’t likely to service your vehicle lifts or spray booths. Tire changers, compressors and alignment racks usually need to be fixed by qualified service technicians. That means you don’t need to worry about hazardous energy from them, right?
Almost right. If equipment fails, mark it out of service. If someone could be injured when using it, put a lock on it (on the disconnect, on the breaker or, if it unplugs, over the plug itself). Attach a tag that explains why the lock is there (“damaged – out of service” is fine). And then make sure employees know they mustn’t use it.
When the technician is servicing that equipment, that repair person is responsible for the energy control procedure. But your employees need to be trained to watch for energy control devices and leave them alone. If a “do not start” tag or a lock is on a piece of equipment, that equipment must not be used. Think the technicians forgot to remove warning tags? Call them back in. Only the person who put the lock or tag in place should remove it. They refuse to return? Carefully check the equipment to make sure it is safe to use. Send them a note (email is okay) telling them you cut the lock. And don’t use that vendor again.
OSHA has numerous reports of employees injured or killed when energy control procedures weren’t followed:
• An employee was preparing to add cloth and a bar to a Mitter machine at a car wash while the machine was in operation. The employee’s jacket caught on the cam of the electric motor and he was pulled into the machine, crushing and killing him. If only he had turned

off and locked out the machine… • An employee was servicing the transmission of an automobile raised up on portable ramps. The automobile rolled off the ramps, with the automobile’s engine compressing the chest of the employee. The employee suffered asphyxiation secondary to external chest wall compression from an automobile engine and was killed. If only he had blocked the wheels…

Don’t be an “if only.”
Turn your safety stalemate into a checkmate with CHESS, INC
CHESS is your solution for OSHA& MPCAcompliance! Working with the automotive repair industry for over 25 years.
Are you aware you need...
An AWAIR program by July 2020*
Annual Right to Know / Hazard Communication Training A COVID-19 Prevention Plan by July 2020**
*By July 2020, automotive repair facilities must have A Workplace Accident and Injury Reduction (AWAIR) program **Essential businesses must have a written COVID-19 Prevention Plan
We Can Help
Contact us today for help with your shop’s safety, health and environmental needs. (651) 481-9787 chess@chess-safety.com www.chess-safety.com
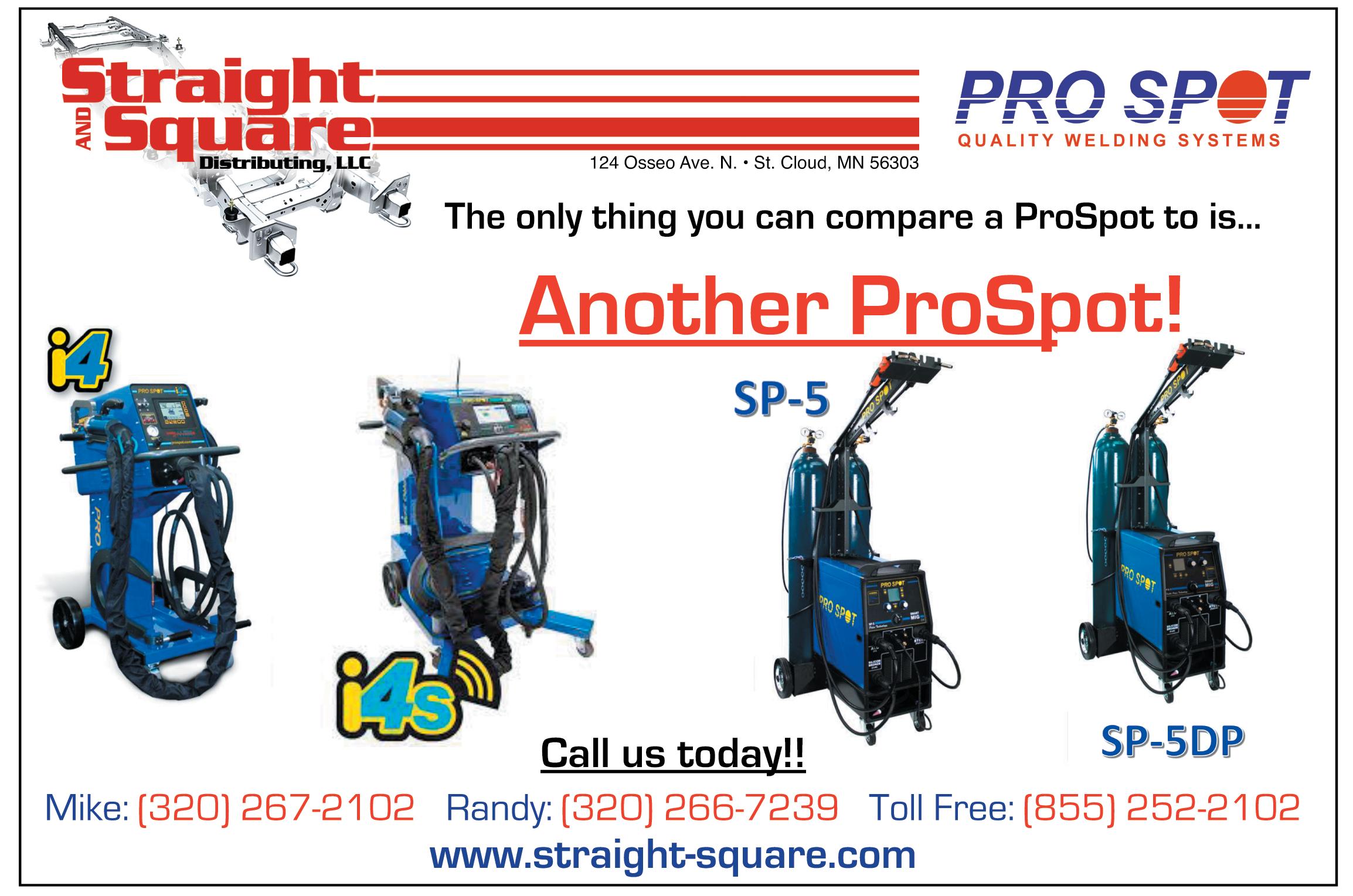