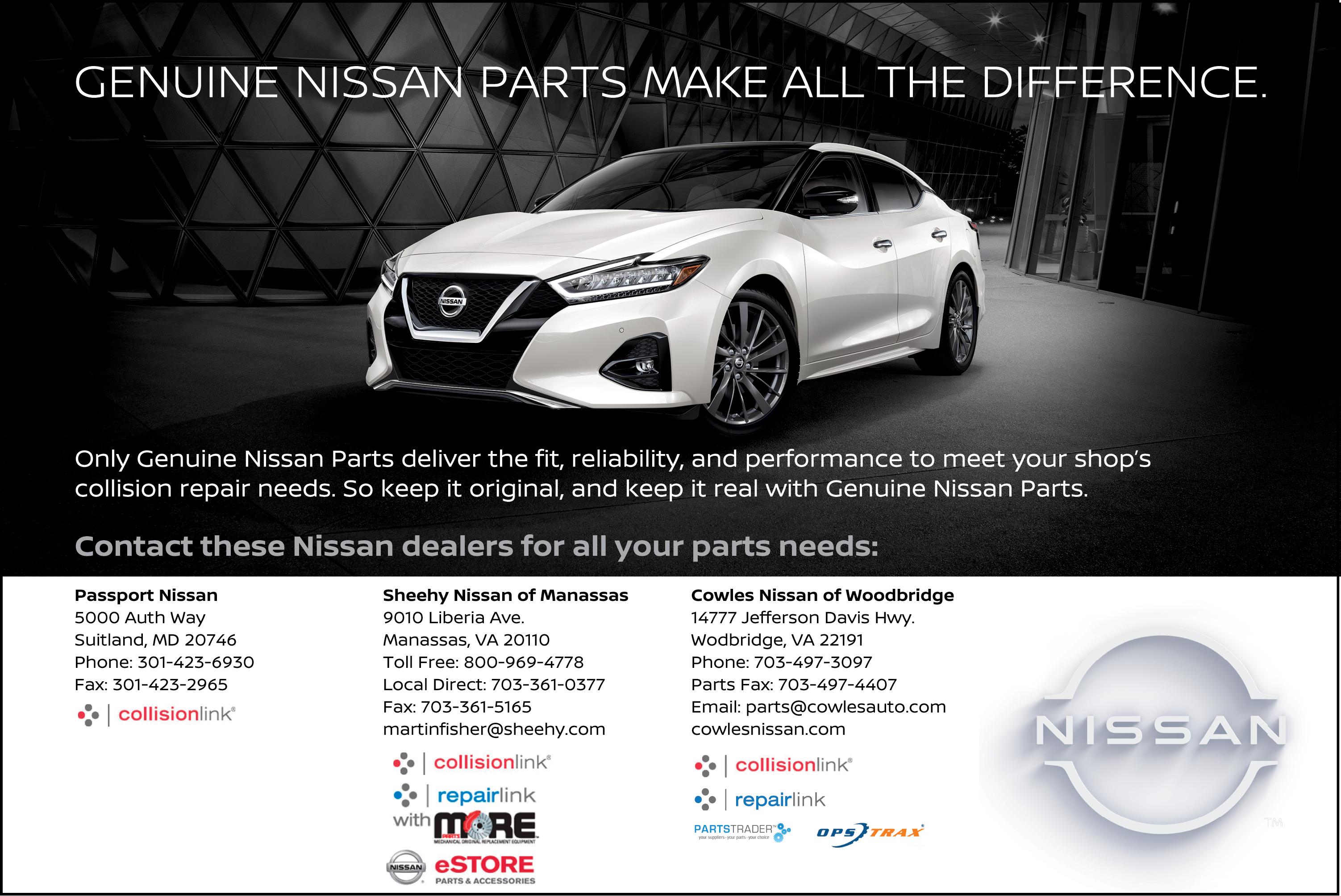
10 minute read
WMABA Member Application
JOIN TODAY!
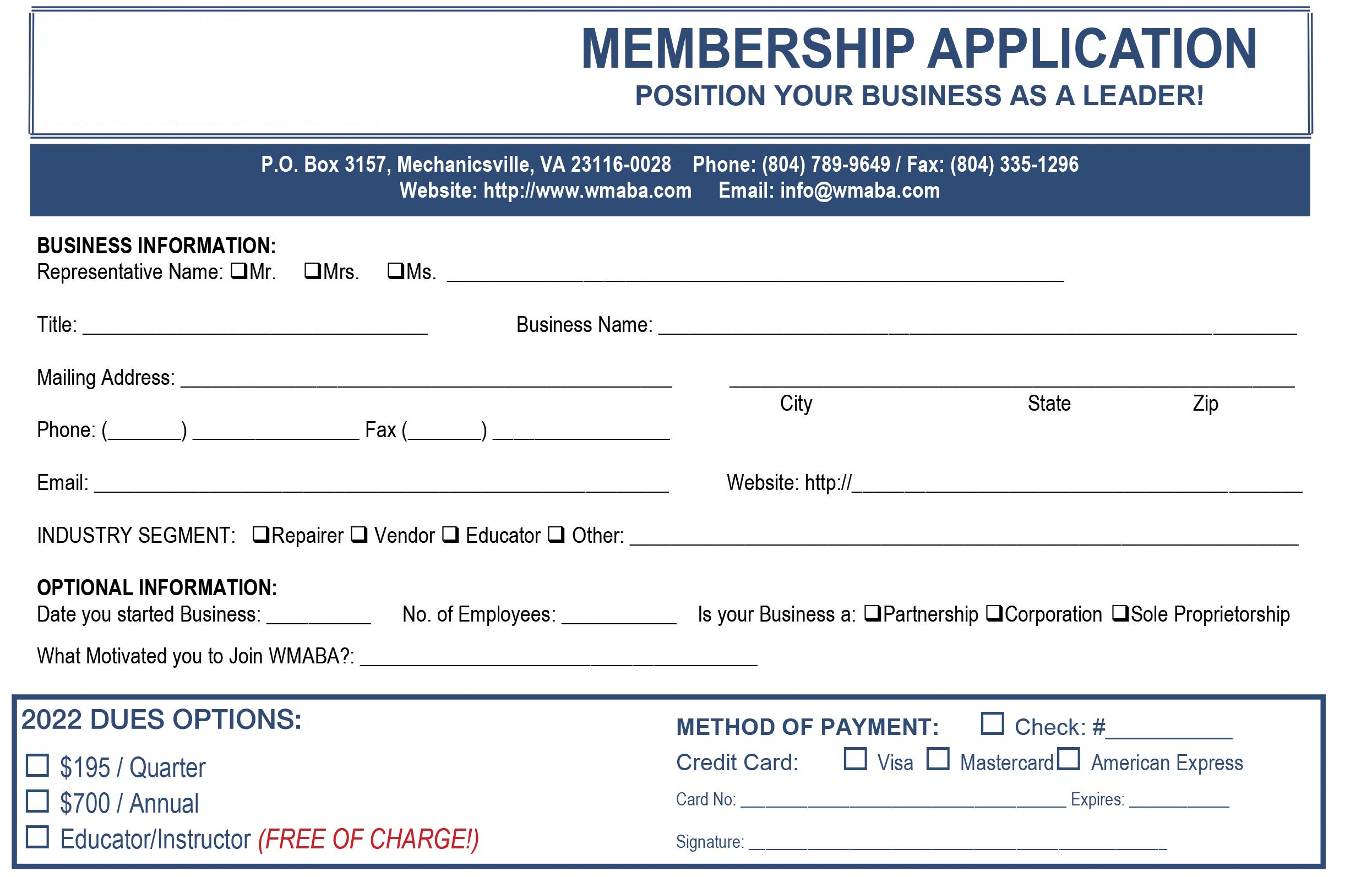
LOCAL NEWS
Invites Collision Repairers to Rate Insurance Companies in 2022 Survey
As part of its ongoing efforts to support the collision repair industry by providing consumer-driven resources, tools and information, WMABA has opened its 2022 Insurance Survey. The association urges members and non-members alike to share their feedback on insurance carriers by participating in the anonymous survey.
In addition to supplying collision repairers and insurers with insights into claims handling practices in the Mid-Atlantic region, the results of WMABA’s Insurance Survey will be available to consumers to help in the policy-buying process. The information compiled provides an excellent resource for educating consumers about insurance carriers and can be used by collision repair shops as a conversation starter with customers.
WMABA hopes the information collected on approximately two dozen carriers will also be beneficial to show more than just one person’s opinion, and rather a collective of voices, in an aggregate way. When approaching any regulatory body, this collection of opinions can be helpful in beginning useful dialogue
WMABA’s 2022 Insurance Survey covers a plethora of topics, including: Shop Relations - Claims Handling Customer Experience Insurer Knowledge Base Overall Fairness Insurer Payment for Proper Procedures Transparency
Collision shops will rate each insurer on a scale of 1 (worst) to 5 (best). This will be WMABA’s second Insurance Survey, following the survey’s debut in December 2018; results from the first iteration can be found in the May 2019 issue of Hammer & Dolly (available at grecopublishing.com), and results from the 2022 version will be available in a future issue.
This is one of the ways repairers can use their collective voice to stand up for their customers, their shops and the industry at-large. WMABA’s Insurance Survey offers a quick and easy way to share your thoughts and be part of positive progress. It’s rare an opportunity to be part of something that gives visibility in both an informative and declarative way; the survey may be for “informational purposes,” but that’s what makes it so great!
Help WMABA protect consumers and collision repairers by completing the survey at wmaba.com. H&D
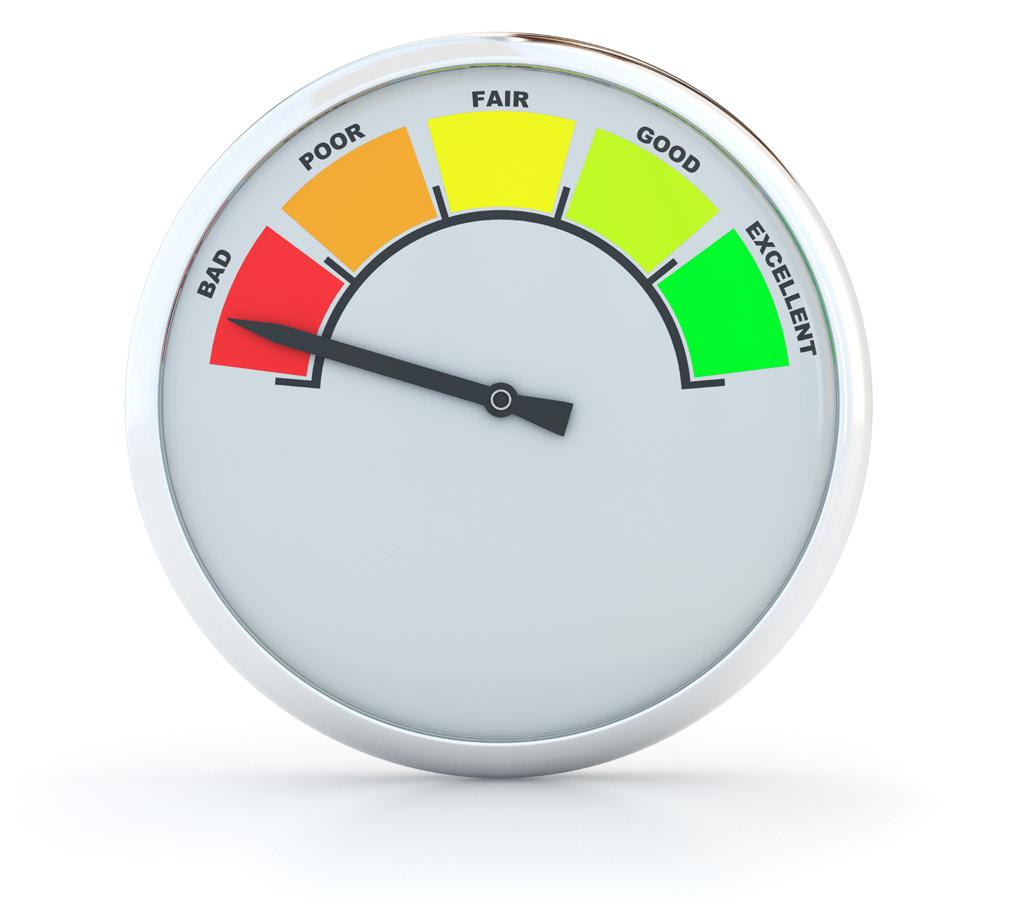
Executive Director’s Thoughts
We really encourage all repairers to give their feedback – and especially for those insurance companies they enjoy working with! It’s an opportunity to praise the companies who stand out
as excellent, fair, and customer-oriented. - Jordan Hendler
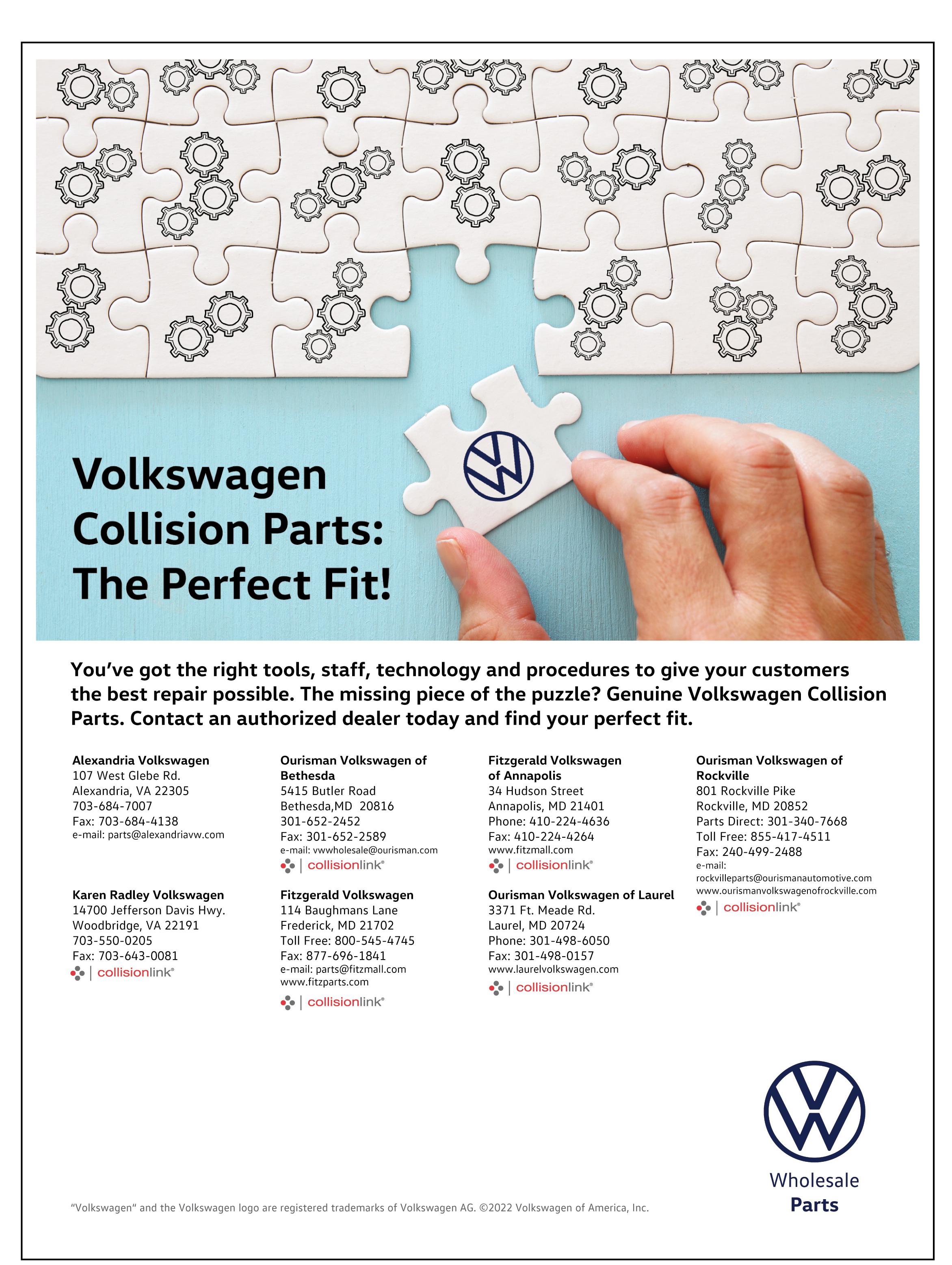
WMABA FEATURE
SAFETY & SPECIALIZATION:
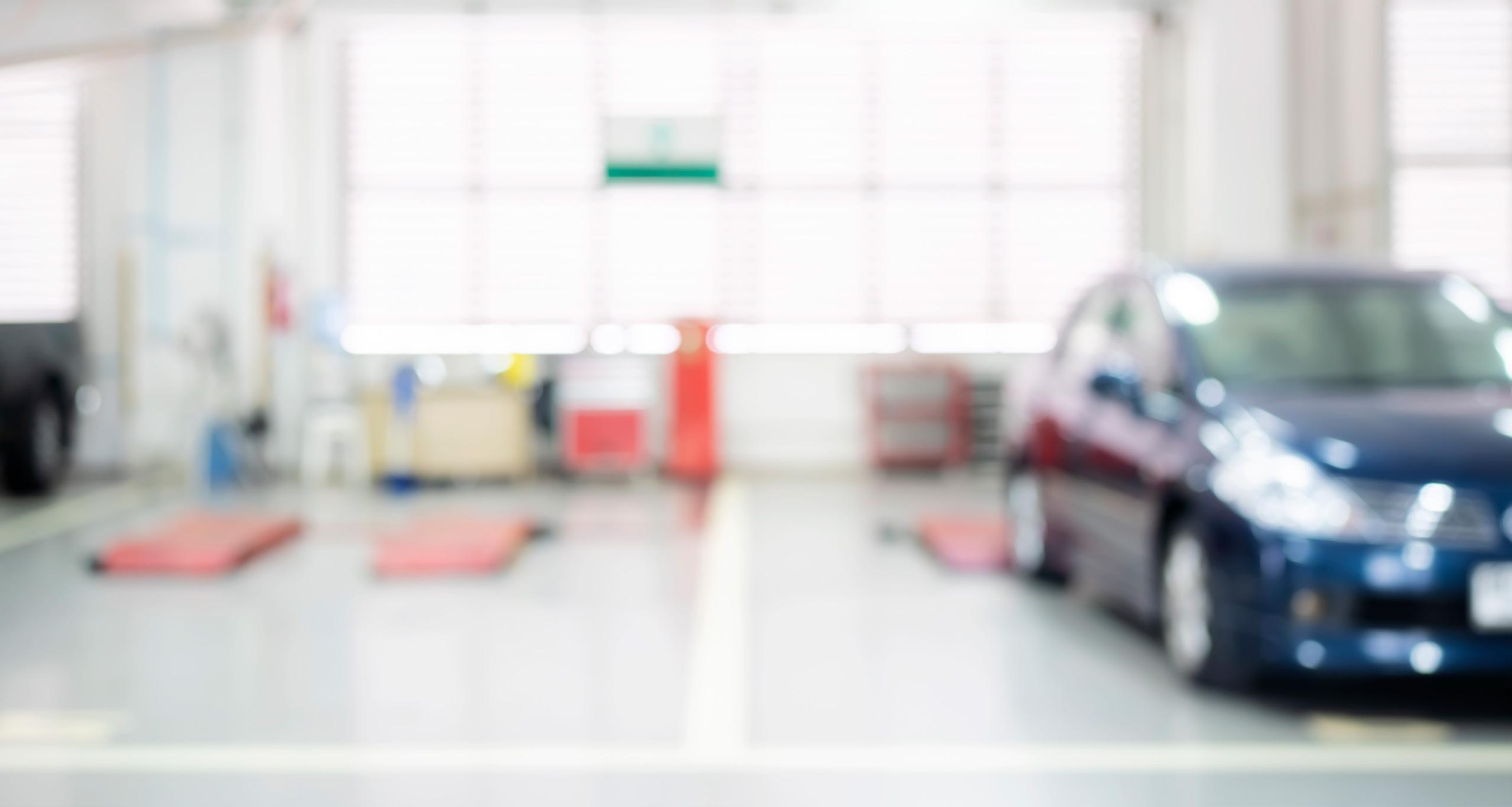
A TOOL & EQUIPMENT REALITY CHECK – PART 6
Clearing a diagnostic trouble code (DTC) seems like a simple enough process: Click the right button and the fault clears – but does this action actually correct the problem(s) with the vehicle? In a small percentage of situations, the answer is “yes” because that code was introduced during the repair process; however, the majority of DTCs result from something that happened during the collision, which means the conditions that caused the code to set must be analyzed and resolved to ensure the customer’s vehicle is properly restored to its pre-accident condition and is safe to drive.
“Scanning and calibrating a vehicle isn’t as simple as clearing a few codes; there’s a heck of a lot more to it than that,” says Barry Dorn (Dorn’s Paint & Body; Mechanicsville, VA).
Safety Concerns Associated with Incorrectly Cleared Codes
To explain why improperly clearing DTCs poses safety hazards, let’s explore a hypothetical scenario: A customer’s vehicle is dropped off at a collision shop with a pre-repair condition that set a code for the occupant sensor. Vehicle manufacturers design these sensors to identify the relative size of the passenger and determine the rate at which airbags are deployed, so a miscalculation could easily cause a tragedy.
“The airbag is designed to deploy at a certain speed if the occupant is a grown man, but by reading the weight in the seat, a child passenger will cause it to deploy at a slower rate,” explains Josh McFarlin, AirPro’s executive vice president of operations. “But for the sensor to know how fast to deploy the airbag, it must be calibrated so that it performs the way it was intended. When a fault exists and the repairer simply clears the code and sends that vehicle down the road without calibrating those occupant sensors, that airbag system is unlikely to operate correctly. And because it probably won’t trigger a light on the dash, the driver doesn’t realize there’s a problem – until it’s too late.”
“The check engine light is irrelevant for a professional repairer,” Dorn points out. “It’s not meant for us; it’s for the consumer, and using that to determine if the vehicle needs additional scans, calibrations and repairs is meaningless and dangerous.”
While initial scans aren’t that time-consuming, many fail to acknowledge that 85 to 90 percent of the time, a pre-scan fires DTCs which require additional operations, as well as additional time and effort to research, diagnose, validate and clear the codes.
“You can’t just clear the codes without doing the research,” McFarlin stresses. “Often, the technician just clears the code, and because the parameters prevent the fault from resetting for two key cycles, it resets after the vehicle is returned to the customer without the problem being resolved. Now, there could be a situation where their airbags don’t operate correctly. This is why it is so critical to take the time to research, diagnose and validate the cause of every fault that is present.”
“We Don’t Pay for That!”
Imagine your horror if a faulty occupant sensor on a vehicle you repaired caused an airbag to deploy at a rate meant for 6’5”, 250-pound man when a child occupied that seat. That’s a tragedy that no one wants to be responsible for, yet collision professionals neglect to perform the necessary calibrations on a large majority of vehicles. In fact, on average, only seven percent of the necessary calibrations are being performed on today’s vehicles, according to McFarlin.
“Although 93 percent of repaired vehicles aren’t correctly calibrated, they are returned to the roads, and they’re operating around us all the time.”
Fortunately, AirPro and similar companies offer diagnostic services performed by qualified technicians to help prevent this from happening. Unfortunately, few shops utilize these services because third-party bill payers are so fond of informing them, “We don’t pay for that.”
According to Dorn, carriers frequently write estimates limiting labor hours for pre- and post-scans to half-an-hour each, while in reality, this work takes a minimum of one hour. Depending on the DTCs set, a shop that accounts for all aspects of scanning,
research, diagnostics and calibrations could easily rack up eight labor hours or more.
“They want to generalize and normalize the process, leaving shops feeling as though they have to just deal with it because they don’t know any better. But it’s our customers who are in jeopardy when we accept that it’s ‘not included.’ That doesn’t matter. The important thing to pay attention to is what the OE requires. That’s how we achieve safe repairs.”
Dorn believes that insurers started writing for one hour of total pre- and post-scan time because the information providers (IPs) briefly tried to estimate the time it takes to perform this process.
“They measured how long it takes to drive the vehicle into the stall, hook it up to a scan tool and initiate the system, and they all came to the conclusion that it takes 0.3 hour. But what does that prove? Absolutely nothing! That’s why the IPs abandoned this approach, but the carriers have clung to it and keep trying to drive down the paid time to a half-hour for the pre-scan and a half-hour for the post-scan. About 60 percent of the vehicles we repair can be prescanned in about an hour and post-scanned in the same amount of time, but that doesn’t account for performing anything additional that those scans reveal.”
“It’s never as easy as hooking up the tool, getting the code and clearing the code,” McFarlin objects to the carriers’ method of paying for scans. “The bill payer looks at it that way, but there’s so many more nuances. We have to examine the data and the parameter IDs (PIDs) to perform active commands and bi-directional controls. Yet, we still hear carriers saying, ‘If no codes are present, we don’t want to pay for the scan.’ How does the shop know whether there are codes if they don’t scan the vehicle? So, they have to perform the labor to get the results, yet if the result is an all-clear, they aren’t entitled to get paid the labor they did to determine that. It’s illogical.”
Collision Repairer or Diagnostic Technician?
Most repairers want to do the right thing and would gladly eat the cost unpaid by the carrier if it meant protecting our hypothetical child. So, if we know that failure to perform required scans, calibrations and diagnostics leads to loss of life, as well as liability concerns for the shop, why aren’t collision repair shops doing a better job of scanning and diagnosing vehicles?
Well, that’s yet another major problem that arises with scanning and calibrations: Collision repair professionals are NOT diagnostic technicians! Each job requires a completely different skill set and level of training.
“Whether you’re using an OEM or aftermarket scan tool is immaterial; any tool is only as good as the person using it,” Dorn notes. “The tool’s effectiveness depends on the technician using it and their familiarity with the tool and the process. The most important tools in a shop’s toolbox are the technicians who work there, and on the collision side, we tend to hire repair planners, body techs, detailers and painters who aren’t proficient with using these tools. What we don’t do is hire diagnostic technicians.” McFarlin agrees:
“The key is the tech’s knowledge, and collision repairers generally don’t possess the knowledge related to scanning and diagnostics. A structural technician, non-structural technician or refinish technician isn’t going to be able to identify, diagnose and resolve those DTCs because that’s not what they’ve been trained to do. You need someone who knows their way around the vehicle’s electronics in order to get in there, chase down the issues, diagnose them and come up with a repair plan that actually resolves the problem. A collision repair professional is neither equipped nor trained to perform calibrations and diagnostics.”
A collision technician and a diagnostic technician may have some things in common, but they perform different functions. Dorn compared the difference to using two frame machines from different manufacturers.
“They’re similar in scope, but they produce unique results. Similarly, there are many variances in the duties of an average collision repair technician as compared to what a diagnostic technician does; the fact is that we just don’t have the same training or skills, not to mention the impracticality of an individual shop investing in all the tools and equipment needed to scan, diagnose and calibrate all vehicle makes and models.
“Sure, we can hook up a scan tool and generate a report, but that doesn’t mean we understand what we’re looking at,” Dorn adds. “We need to rely on someone with the ability to read and translate that report for us.”
Because diagnostics are such an important part of safely repairing today’s vehicles, Dorn relies on a third-party provider, utilizing their experienced diagnostic technicians who know how to remotely scan vehicles and can clearly indicate what needs to be done to ensure a proper repair for his customers.
“A diagnostic technician doesn’t merely look at the fault codes,” McFarlin clarifies. “Diagnosticians also look at live data because simply clearing the fault isn’t adequate; we need to actually validate that all the systems are operating correctly, and to do that, there are tons of decisions that need to be made. That’s difficult for a technician to do unless they’re well-versed in diagnostics, and because most collision technicians aren’t, customers are returned to the road in a vehicle that isn’t prepared to protect them – and it also doesn’t protect the repairer who is liable for the improper repair.”
“This is a comedy of errors,” Dorn observes. “But there’s nothing funny about it; when we make a mistake and neglect to properly diagnose and calibrate a vehicle, the situation is life-threatening.”
H&D Executive Director’s Thoughts
It’s clear; clearing codes is not a viable or safe answer to the diagnostic question. No more so than a standard minimal (or no) reimbursement. Every car is going to be different, as will its needs. Just like the special training needed to discern, diagnose, calibrate and send the safe vehicle back to the customer. It’s never been a
better time to understand the difference! - Jordan Hendler
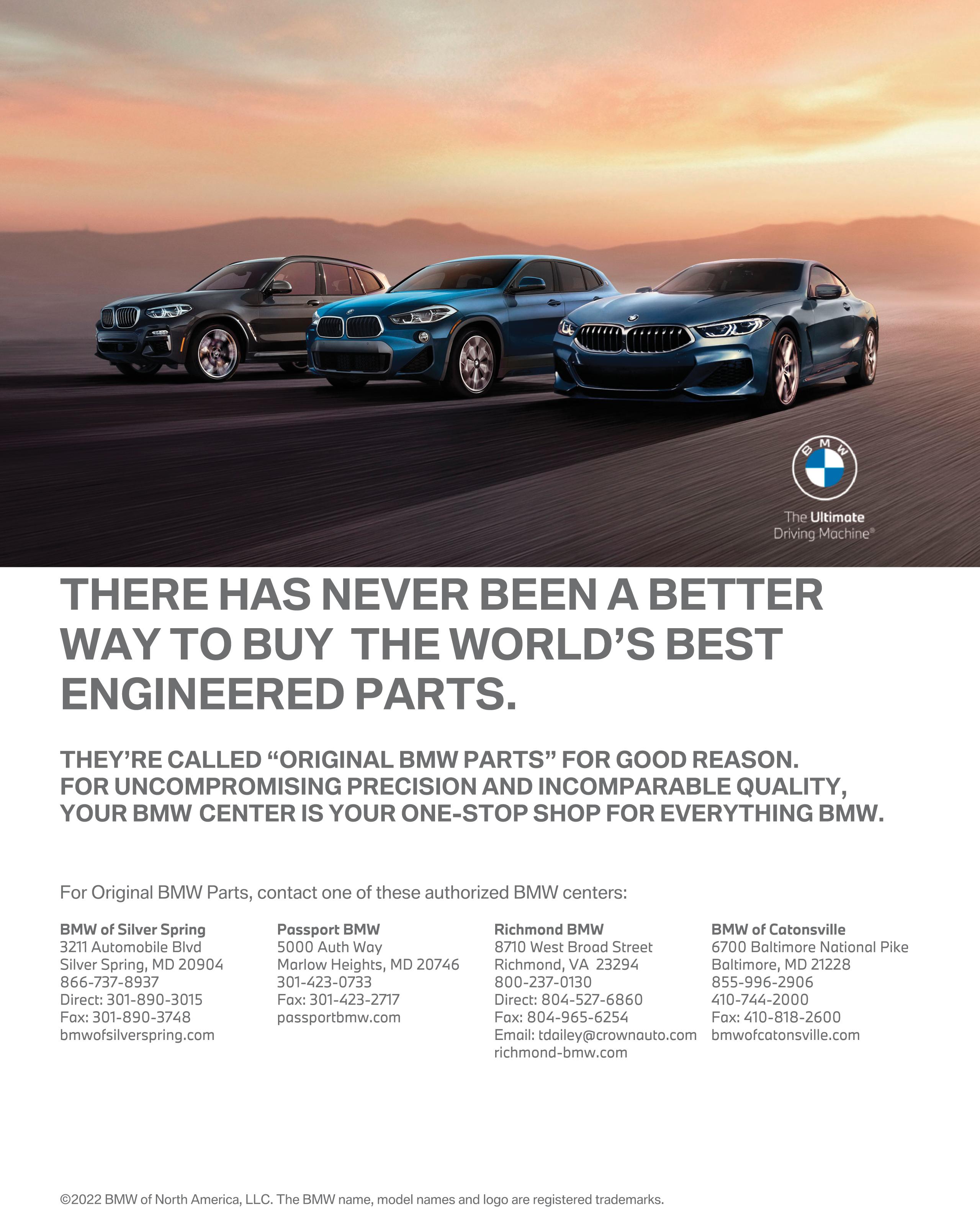