
19 minute read
CIC: INDUSTRY ISSUES INSPIRE INNOVATION
NATIONAL FEATURE
CIC: INDUSTRY ISSUES INSPIRE INNOVATION
Life in a body shop presents a series of challenges each day, which may feel overwhelming at times, but when the greatest need presents itself, industry leaders differentiate themselves by offering forward-thinking solutions – and that’s a trend that continues to pervade the Collision Industry Conference (CIC) meetings each quarter!
While the most recent CIC meeting, held in conjunction with the 2022 SEMA Show, drew an unprecedented amount of attention and attendance related to the Parts & Materials Committee’s SCRS Blend Study Research, the final presentation of the day was far from being the only notable information shared as collision repair professionals learned tips on recruitment and retention, discovered the truth about telematics and received insights on periodic vehicle safety inspections.
Personnel issues have been one of the largest complaints among shop owners for quite a number of years, and CIC’s Talent Pool & Education Committee sought to ask “How Can You Help Yourself” when it comes to recruiting, training and retention as Committee Chair Bud Center (I-CAR) moderated a panel of experts, which included Jim Guthrie (Car Crafters), Mario Dimovski (Gerber), Brandon Eckenrode (Collision Repair Education Foundation/ CREF) and Dara Goroff (I-CAR).
“Explain what’s wonderful about working in this field, about the depth and breadth of this field. Make sure the marketing materials you’re using to attract talent are visible to the audience you want to attract,” Goroff offered suggestions for recruitment, stressing the need to consider “the mindset of recent high school graduates [and other young people]. Where are they getting their content and media? Not from traditional channels. They’re looking at social media; they look to influencers. So, we have to capture the hearts of those influencers who can help us tell the story of why this industry is so wonderful. We need to tell that story together.”
Eckenrode agreed that there’s a large need to focus on the youth, specifically by investing in local high school and college collision programs to ensure those programs are attractive and showcase a welcoming environment. CREF has also begun collaborating with school counselors to help them “embrace technical education so they
CIC’s Talent Pool & Education Committee discussed recruiting, training and retention as panelists explained how shops can help themselves solve the workforce shortage. Pictured from L-R: Bud Center (I-CAR), Jim Guthrie (Car Crafters), Mario Dimovski (Gerber), Brandon Eckenrode (CREF) and Dara Goroff (I-CAR).
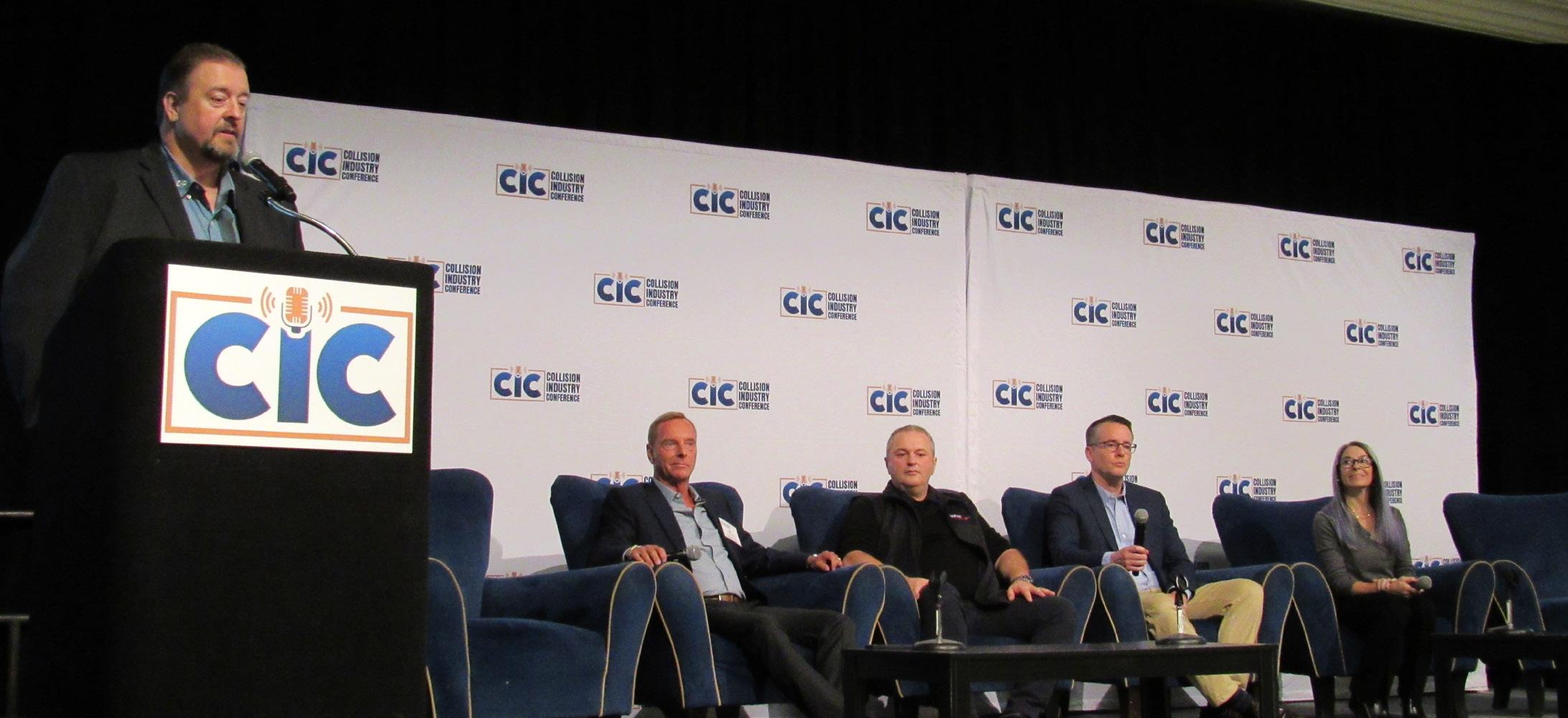
can educate their students on this industry and create resources so they can showcase this field as a viable option with a multitude of different opportunities. That way, we’re their first option, instead of getting the leftovers that didn’t know where else to go.”
Parents present another obstacle, and changing their mindset is imperative as well.
“It’s on us to showcase our industry in a more professional manner,” Goroff stressed. “And when we paint that picture of what today’s technician looks like, we need to show how clean the space has to be when repairing an electric vehicle (EV) and the importance of making sure the work we’re doing is truly quality work so we can get the vehicle back on the road safely. We have to show that vehicles are nothing like they were 40 years ago…and this industry isn’t what it was 40 years ago. Thinking of us as a trade is a mistake because this is truly a highly skilled, technical field these days.”
Once new employees are hired, a shop owner’s job isn’t done – additional training and feedback is necessary to keep young people motivated and engaged in their chosen career path. This means setting expectations and connecting them with a mentor who will patiently guide them on the right path.
“You have to invest in talent to develop talent,” Dimovski expressed. “There’s nothing worse than just throwing them into it because everyone is too busy. Sooner or later, they’re going to leave. Invest in training them, but also invest in the right tools and technology because that’s what interests these kids; we have to show them where the industry is heading if we want to keep them engaged in their journey.”
Less obvious factors, such as demonstrating a career path and showing appreciation, play a vital role in retention, according to Guthrie.
“You have to make them feel appreciated and provide a good environment with heating and air conditioning. They want to work in a clean shop, and it has to be a shop that trains, where they can see their future and maybe even different career paths. Yes, you

CIC’s Emerging Technologies Committee panelists discuss the skills collision repairers need now and in the future. Pictured from L-R: Tim Morgan (Spanesi Americas), Kelly Roberts (BETAG North America), Kevin West (Nylund’s Collision Center), Kye Yeung (European Motor Car Works) and Jason “Buck” Zeise (LaMettry’s Collision).
Future Disruptions Committee Co-Chair Jake Rodenroth explores “The Real Truth About Telematics Today.”
need good benefits, but pay is not always the number one reason why somebody will leave. The key to retention is really showing your appreciation and helping them grow in their roles and beyond.”
So, exactly how are technicians’ roles – and the skills needed for collision repair – evolving today and in the future? CIC’s Emerging Technologies Committee tackled this ever-changing topic by exploring the short set of typical skills identified in collision repair job listings…compared to the vast and various requirements for alternate types of technicians as the committee differentiated between structural, non-structural, refinish, mechanical, electrical/diagnostics and production management technicians.
“It takes a team of specialists to properly repair a vehicle now,” Kye Yeung (European Motor Car Works) emphasized.
Panelist Kevin West (Nylund’s Collision Center) recommended looking “for someone who understands and knows their limitations. A technician cannot do this job from start to finish anymore. There are different roles, and you have to know and understand your limitations.”
An ideal technician “comes in and sees the opportunity and potential…and is willing to do the work to understand and keep leveling up their skills,” Kelly Roberts (BETAG North America) agreed, noting that advancing technology creates “an opportunity to create a culture [with employees who are] curious and concerned about safety because there are no longer any trivial or innocuous parts on today’s vehicles. Every aspect of the repair poses potential risks that can significantly compromise safety systems.” CIC Future Disruptions Committee Chair Frank Terlep joined Jake Rodenroth (Lucid Motors) and James Spears (Tractable) as they took on the role of MythBusters and uncovered “The Real Truth About Telematics Today.”
The trio explained how data is collected and the primary ways that telematics is currently being used, yet “We’re far away from an end to end process,” Terlep acknowledged, continued on pg. 24

continued from pg. 23
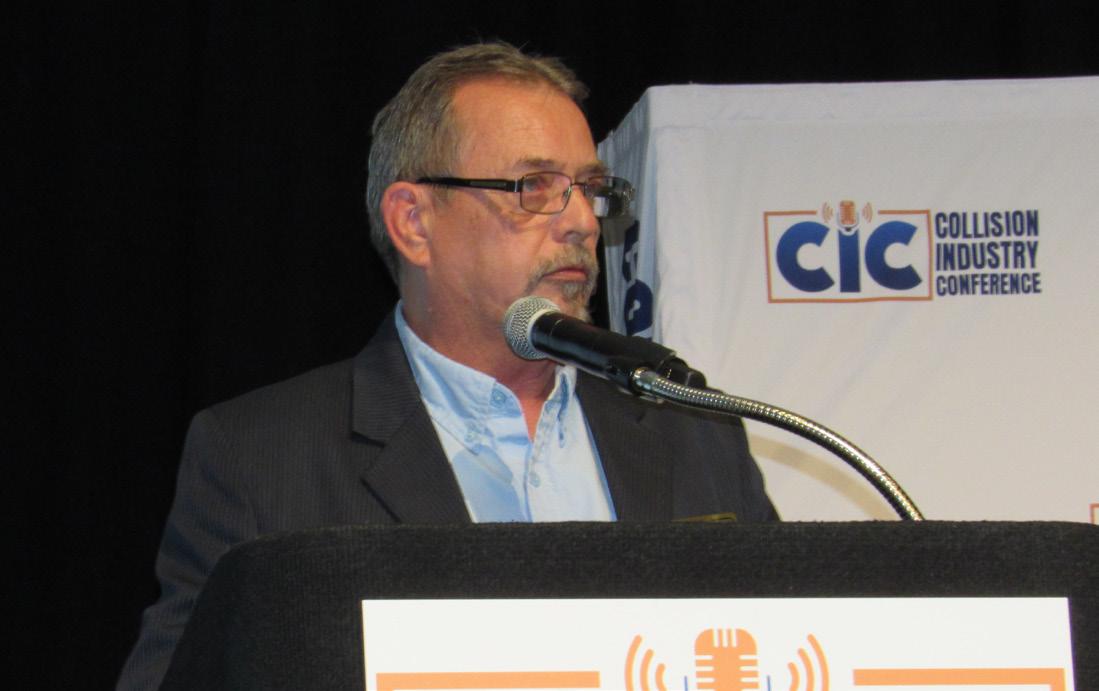
CIC’s Emerging Technologies Committee Co-Chair Chuck Olsen moderates a panel on evolving technician roles.
and Spears acquiesced, “We still need a human in the loop,” admitting there’s still a lot of heavy lifting to be done. “It’s important to get it right with AI [artificial intelligence] to avoid degrading our trust with the customer. There’s plenty of work left to do, but we’re definitely getting things started on the right path.”
“We’re only going to see more of it, driven by customers who want to see cool features, safety and white glove service,” Rodenroth predicted. “Shops are repairing high tech vehicles, and they have high tech customers who are aware of the features that come with it, so study up…Product knowledge is everything.”
Terlep alluded to the fact that data is “the new gold,” but the Data Access, Privacy and Security Committee really dove into the importance of “Understanding the Impacts of Data in the Collision Industry.”
Ashley Denison (Caliber Collision) was “wildly surprised at how free flowing data was when I first came into the industry” and stressed that when it comes to data security, the auto body world “still has a long way to go,” urging shops to consider “how are we protecting our customers? As an industry and as shop owners, what do we need to do? It’s about knowing the process and making sure you know where your customer data is at all times and having the ability to retrieve that data upon request.”
Denise Koukal (LaMettry’s Collision) shared an anecdote about data leaving the business without permission and the issues it caused with that customer. “If you have a happy customer, they’re going to tell one person; if you have an unhappy customer, they’re going to tell 15. Unhappy customers are not good for referral business,” she warned before she and other panelists offered suggestions for mitigating these risks.
Risk abounds in every area of the industry, as the Governmental Committee pointed out while discussing the opportunities, benefits and obstacles related to Periodic Vehicle Safety Inspections. Committee Chair Bob Redding, Co-Chair Janet Chaney and panelists Chuck Olsen (AirPro Diagnostics), Mark Olson (VECO Experts), Bill Dell (OPUS Inspections) and Scott Benavidez (Mr. B’s Paint & Body Shop) debated whether state or federal legislation should regulate the need
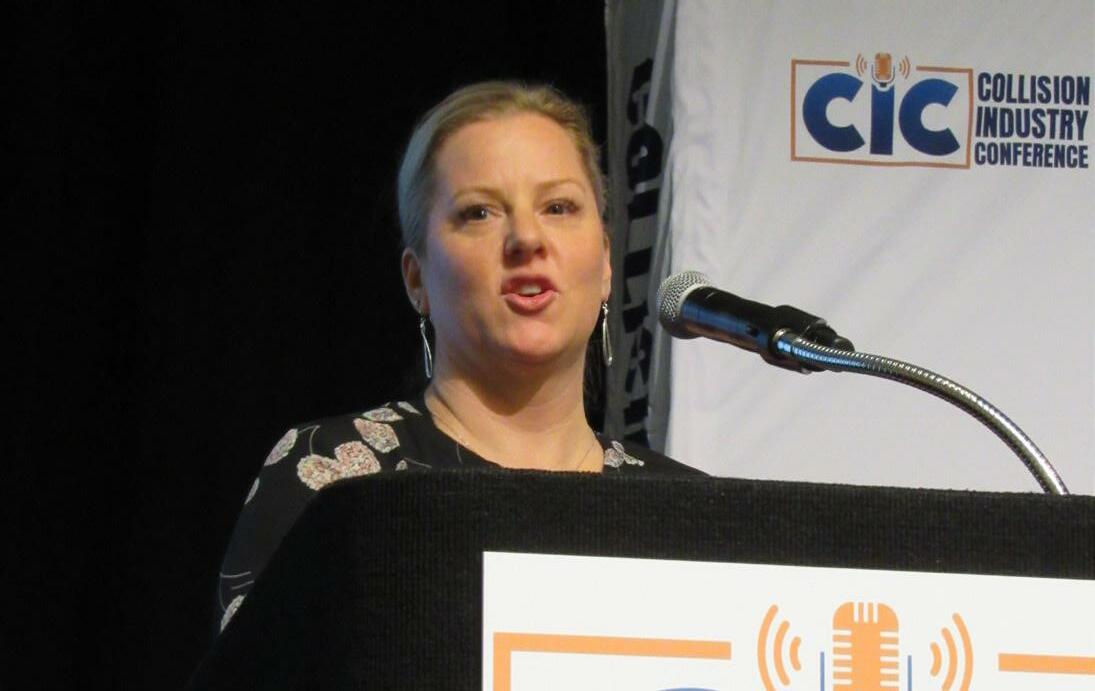
WMABA Executive Director and CIC Administrator Jordan Hendler announces CIC’s new slogan is “Connect. Influence. Collaborate.”
for periodic safety inspections.
On an upbeat note, Redding indicated that he has seen a lot of positive progress when it comes to legislation within the past couple years. Although the US government is not yet ready to make a federal mandate today, he feels certain that “once a major state takes the lead, others will follow. It’s coming, and it’s going to be good for the industry.” Connect. Influence. Collaborate. That’s the message behind all of CIC’s meetings and individual presentations, so it was no surprise when WMABA Executive Director and CIC Administrator Jordan Hendler announced the winner of CIC’s slogan contest was Cindy Schnier Granse who received $500 for her efforts, which she graciously donated back to CIC. CIC’s next meeting is scheduled for January 19, 2023 in Palm Springs, CA. Registration information, as well as presentations from previous meetings, can be found at ciclink.com. H&D
Executive Director’s Thoughts
This issue will be on your desk when the next meeting happens for CIC, but trust me, you’ll want to make your plans and buckle up for CIC coming to the Omni in Richmond, Virginia April 13-14 along with board meetings from the Society of Collision Repair Specialists, and followed immediately by the Southeast Collision Conference. We have not had national meetings so close in so long; literally your own backyard. These meetings are where every issue you face on the daily is addressed by the industry’s leading representatives. It will be an actual shame if
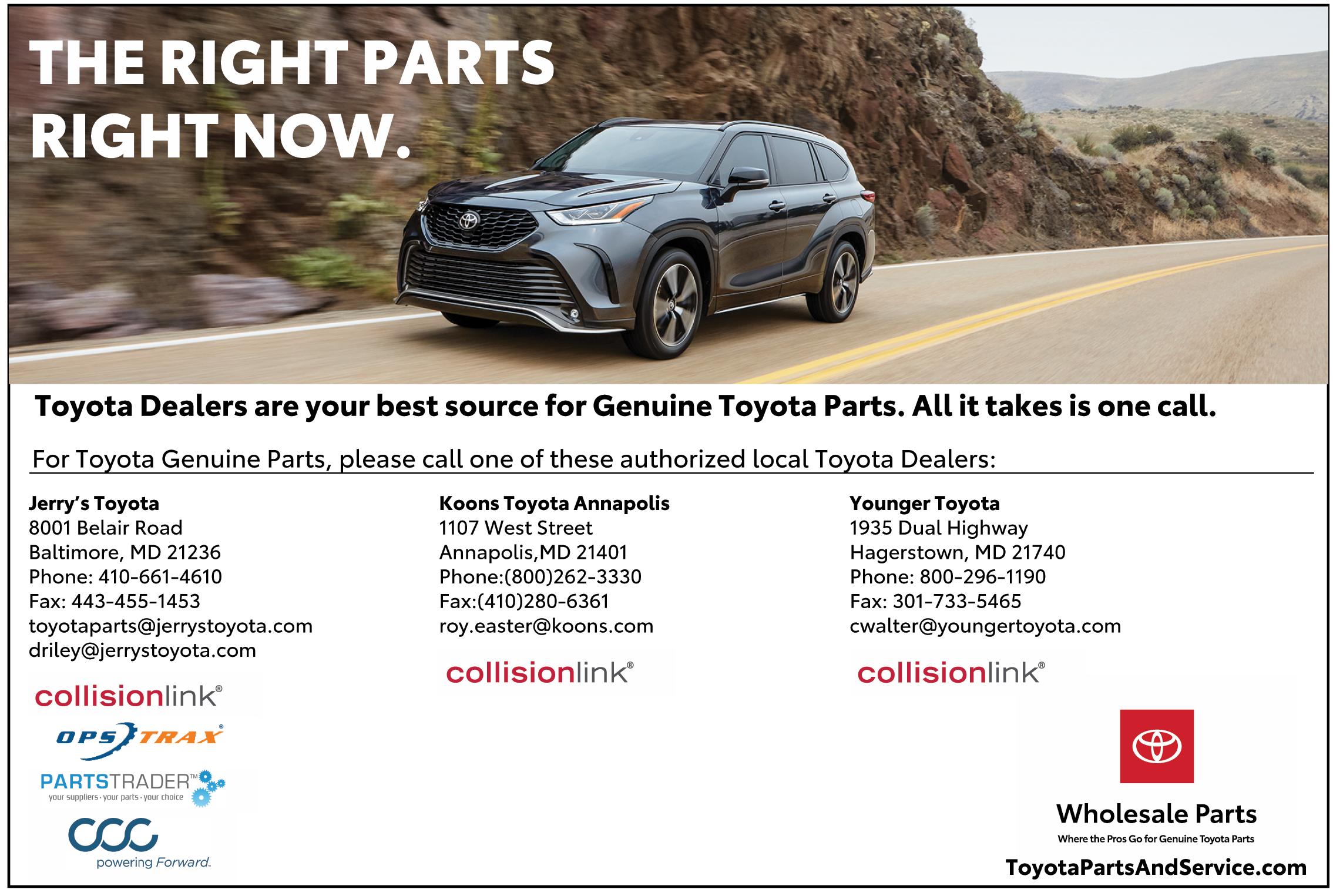

MARKET RATE DATA IS GOLD: WMABA’S LABOR RATE SURVEY RETURNS
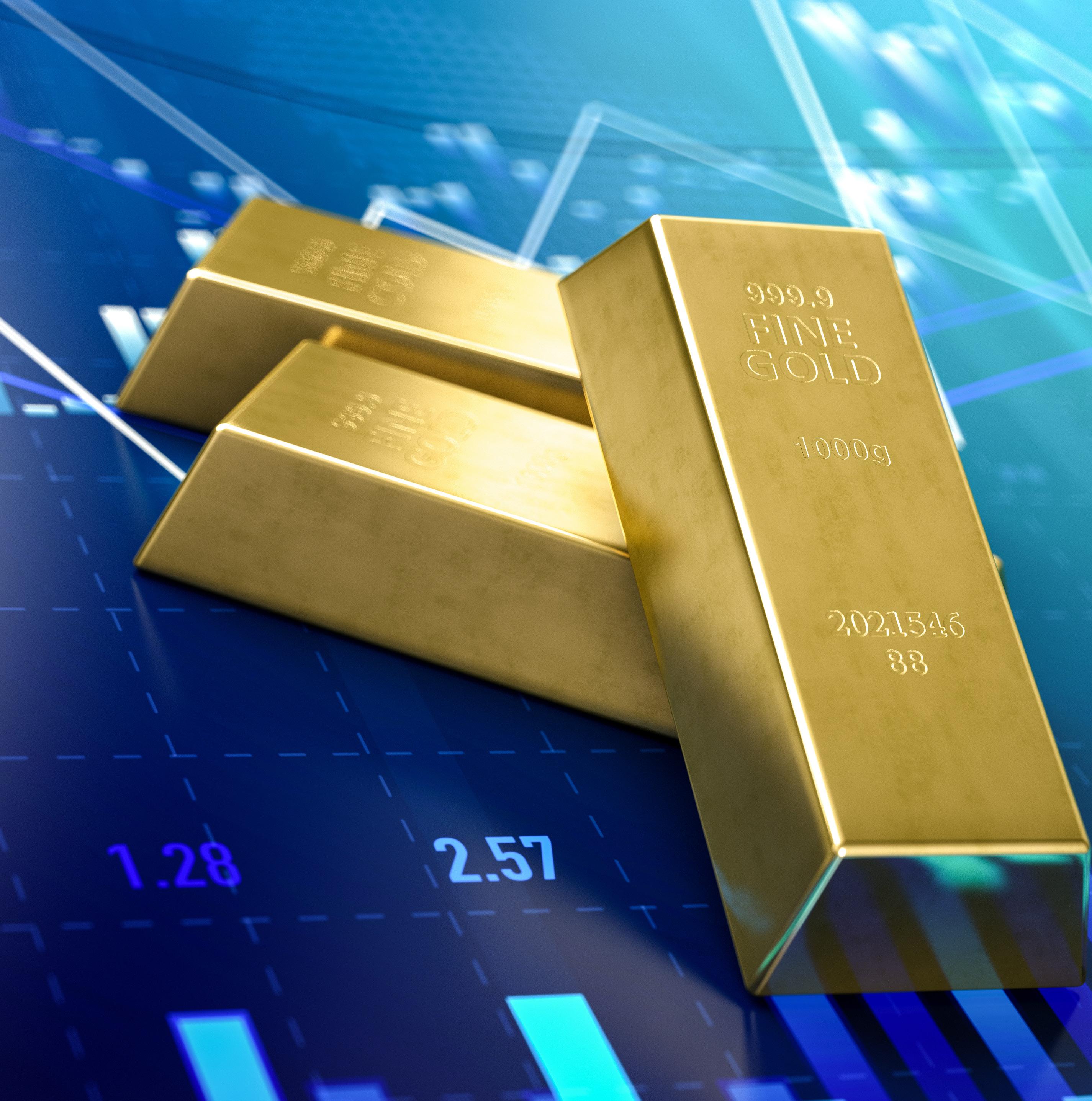
Are you sick of fighting to receive fair and reasonable compensation for the work performed in your shop…only to be told “you’re the only one” time and time again? It’s frustrating and demoralizing when a third-party payer consistently insists that no other shops in your market charge for certain processes and procedures or simply that you’re charging too much.
It’s time to advocate for your shop – and your industry – by participating in the eighth iteration of WMABA’s Labor Rate Survey to provide insights into actual market data by sharing your true retail door rates and answering questions related to the procedures. The 2022-2023 Labor Rate Survey (available online at wmaba. com/labor-rate-survey) asks WMABA-area shops to provide their posted/retail rates for several operations. As always, all Survey results remain completely anonymous; no participating shops will be identified by name.
WMABA believes that shops should charge a fair price for the important and necessary work they perform in safely repairing today’s complex vehicles. This can be different than the amount insurance
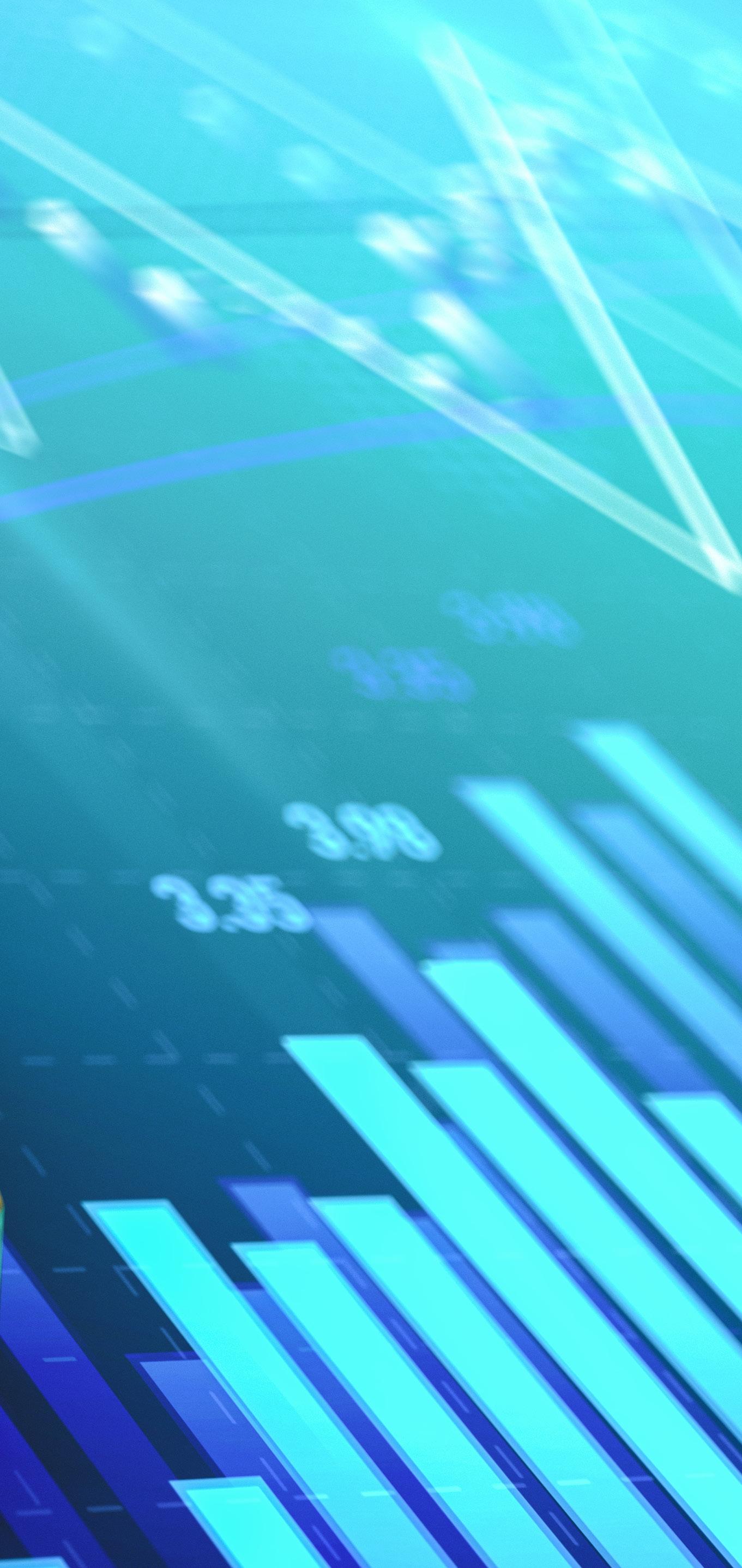
companies try to dictate. The practice of estimating at the business’ identified retail price is necessary in maintaining a healthy, competitive marketplace. “Third-party payers’ systems determine ‘market rate’ based on a variety of information, including discounted DRP rates added by insurers, which skews the overall average in a downward trend that negatively impacts the market,” laments WMABA Executive Director Jordan Hendler. “The Survey only takes five minutes to complete and allows us to collect our own data which we report back to our members, plus we can use that real-world information to discuss the issues with regulatory and legislative entities to help better support collision repairers in WMABA markets.
“We hope to use the compiled survey results to educate within our membership, our regional contacts and our government agencies that oversee market conduct. There’s no question about it…we are always fighting an uphill battle, but with the support of these facts and figures, WMABA is better equipped to defend this amazing industry. We have to keep moving forward, and we need your help to do it!”
Shops taking the Survey are asked to provide their door rates for body labor, frame/structural work, paint/refinish, paint materials, aluminum structural work (if applicable), mechanical work and daily inside/outside storage.
“WMABA’s Labor Rate Survey requests shops’ retail door rate, representing their posted or customer pay rates, not a skewed wholesale or concessionary amount found in information providers’ systems,” Hendler explains. “Those rates do not accurately and fairly represent market rates, which often include price reductions granted to insurers in exchange for high volume through DRP contracts. We encourage DRP shops to participate, but ALL shops should complete the Survey by providing their walk-in rate so we can report realistic regional rates that are truly indicative of the majority of shops in that area…This information is not available any other way.”
WMABA encourages Survey participants to share certain procedures they believe are required during the repair process and whether these procedures are currently performed and charged for at their shops, such as: “mark-up” or “admin” on sublet (towing, upholstery, mechanical, etc.); “clips and fasteners” needed in the repair process; “color sand and buff;” Feather, Fill, Block and Prime on welded panels; “check and test seat belts” being used in the accident; “prep raw plastic” when recommended by paint suppliers; and “weld-thru primer” and/or “cavity wax” when needed. The Survey also consists of nearly three dozen critical industry-related “yes or no” questions, including the following: Do you believe insurers rate you on the use of alternative parts to OEM, such as used or aftermarket? Do inadequate or poorly written estimates by insurance company representatives delay the repair process and cost your shop time and money while you rectify mistakes? Do appraiser(s) tell you, “We can’t pay for that because it is against insurance company policy,” even though you know it is a fair, reasonable and necessary item? Is it your experience that a good portion of insurance company representatives write “low-ball” estimates that omit obvious visible damage? Do you use the degweb.org website to submit inquiries of missing or inaccurate labor, parts, material or other flaws in the estimating system guides? Do you believe insurer reimbursement rates are fair enough to support adequate profit for continuing education, certifications and new equipment?

You’ve got the right tools, staff, technology and procedures to give your customers the best repair possible. The missing piece of the puzzle? Genuine Volkswagen Collision Parts. Contact an authorized dealer today and find your perfect fit.
Alexandria Volkswagen
107 West Glebe Rd. Alexandria, VA 22305 703-684-7007 Fax: 703-684-4138
e-mail: parts@alexandriavw.com
Karen Radley Volkswagen
14700 Jefferson Davis Hwy. Woodbridge, VA 22191 703-550-0205 Fax: 703-643-0081
Ourisman Volkswagen of Bethesda
5415 Butler Road Bethesda,MD 20816 301-652-2452 Fax: 301-652-2589
e-mail: vwwholesale@ourisman.com
Fitzgerald Volkswagen
114 Baughmans Lane Frederick, MD 21702 Toll Free: 800-545-4745 Fax: 877-696-1841
e-mail: parts@fitzmall.com www.fitzparts.com
Fitzgerald Volkswagen of Annapolis
34 Hudson Street Annapolis, MD 21401 Phone: 410-224-4636 Fax: 410-224-4264
www.fitzmall.com
Ourisman Volkswagen of Laurel
3371 Ft. Meade Rd. Laurel, MD 20724 Phone: 301-498-6050 Fax: 301-498-0157
www.laurelvolkswagen.com
Ourisman Volkswagen of Rockville
801 Rockville Pike Rockville, MD 20852 Parts Direct: 301-340-7668 Toll Free: 855-417-4511 Fax: 240-499-2488
e-mail: rockvilleparts@ourismanautomotive.com www.ourismanvolkswagenofrockville.com
“Volkswagen“ and the Volkswagen logo are registered trademarks of Volkswagen AG. ©2023 Volkswagen of America, Inc. Wholesale
Parts
continued from pg. 27
Survey respondents can include the number of estimators, office personnel and technicians at their facilities, as well as total square footage, preferred paint and materials cost accounting system (if one is in use) and their gross annual sales. As in years past, the Survey also asks participants to provide information on employer/ employee relations by answering questions on the perks they offer, including personal leave, paid vacations, paid sick time, health/dental/ vision/life insurance, long-term disability and 401(k) retirement plans.
“The questions asked provide a complete snapshot of the issues shops experience on a daily basis, and investing a few minutes into completing the Survey could easily benefit your shop for years to come,” Hendler encourages.
The 2022-2023 WMABA Labor Rate survey can be taken online at wmaba.com/labor-ratesurvey. The results of the Survey will be featured in an upcoming issue of Hammer & Dolly. If you have questions or require additional information, please contact Jordan Hendler at (804) 789-9649 or jordanhendler@wmaba.com. H&D
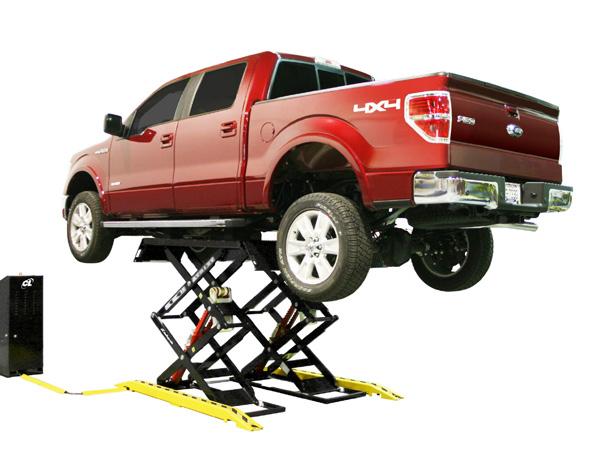


Providing Top-of-the-line Automotive Equipment
PRO SPOT i4s AUTO WELDER
How Can Our Team Help?
View Our Work at chesautoequip.com
Facility Layout & Design Project Management Equip. & Specs. Training Equipment Installation
CELETTE X-TRAC LIFTING AND PULLING PLATFORM CHALLENGER DX77 SURFACE MOUNTED DOUBLE-SCISSOR LIFT
HUNTER ALIGNMENT SYSTEMS WITH ADAS CAPABILITIES
chesautoequip.com • 800.604.9653
Conquest your Mitsubishi parts needs!
Mitsubishi now offers Genuine OEM parts through our new “Opt-OE” parts program at discounted prices. See Mitsubishi’s Ultra-Conquest parts and prices in the Optional OEM Suppliers category of popular collision estimating systems.
Ultra-Conquest Collision Parts Program Highlights:

• Discounted prices on quality new and unblemished OEM parts • Automated price and part selection in collision estimating systems • High parts availability • Delivery to most major U.S. cities within 24 hours • Available through all participating Northeastern area Mitsubishi dealers • Includes the majority of key collision components for select popular models • We can meet or beat aftermarket prices!
To find out more about Ultra-Conquest pricing contact your local Mitsubishi dealer.
For Genuine Mitsubishi parts, contact these authorized Mitsubishi Dealers.
Fitzgerald Mitsubishi
1930 West Street Annapolis, MD 21401 Direct: 410-224-4636 Fax: 410-224-4264 E-mail: adamsf@fitzmall.com
Younger Mitsubishi
1945 Dual Highway Hagerstown, MD 21740 Direct: 800-296-1190 Fax: 301-733-5465 www.youngermitsubishi.com
Jerry’s Mitsubishi
1906 E. Joppa Road Baltimore, MD 21234 Toll Free: 844-817-9406 Local: 443-219-2728 Fax: 443-403-1419 mitsubishiparts@jerrymitsubishi.com www.jerrysmitsubishi.com
Buy Genuine Mitsubishi Parts and get the perfect fit at the perfect price. 10% off on all parts orders when you mention this ad.
KEEP IT GENUINE
INSIST ON GENUINE GM PARTS
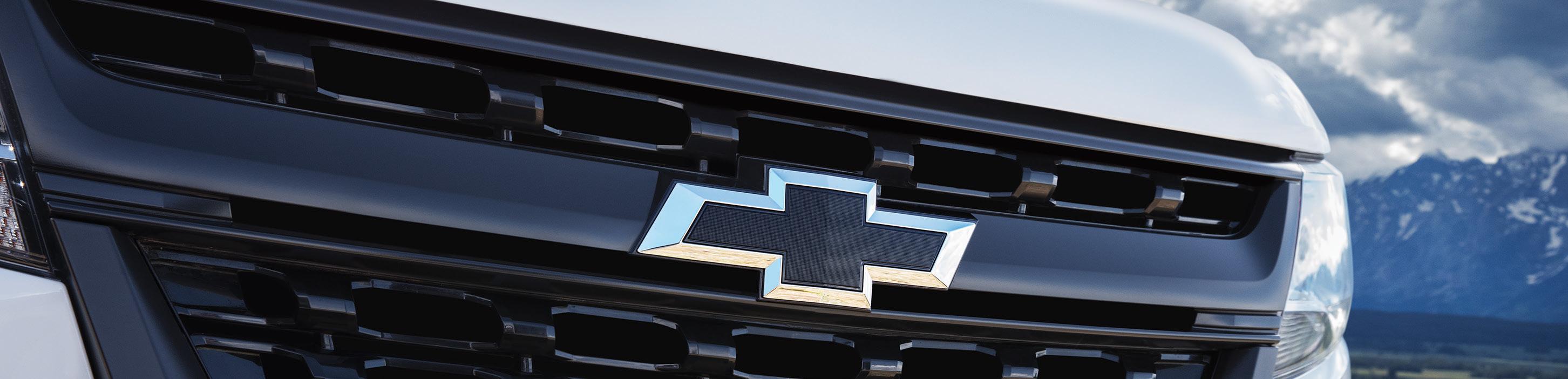
Using Genuine GM Parts for collision repairs is better for your customers, and better for your business. Contact the following dealers for all your Genuine GM Parts needs:
JERRY’S CHEVROLET
1940 E. Joppa Road Baltimore, MD 21234 Toll Free: 844-817-9405 Local: 443-219-3339 Fax: 443-403-0803 chevyparts@jerryschevrolet.com www.jerryschevrolet.com
OURISMAN CHEVROLET OF ROCKVILLE
807 Rockville Pike Rockville, MD 20852 Toll Free: 800-345-4640 Direct: 301-424-5332 Fax: 301-294-6381 www.rockvillechevrolet.com
OURISMAN CHEVROLET
4400 Branch Avenue Temple Hills, MD 20748 Phone: 301-899-6990 Fax: 301-899-9375 www.ourismanchevrolet.com
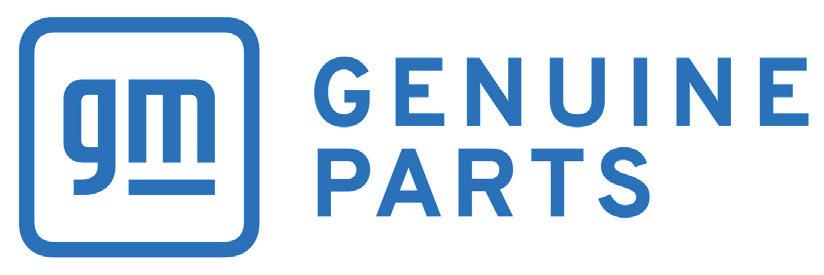
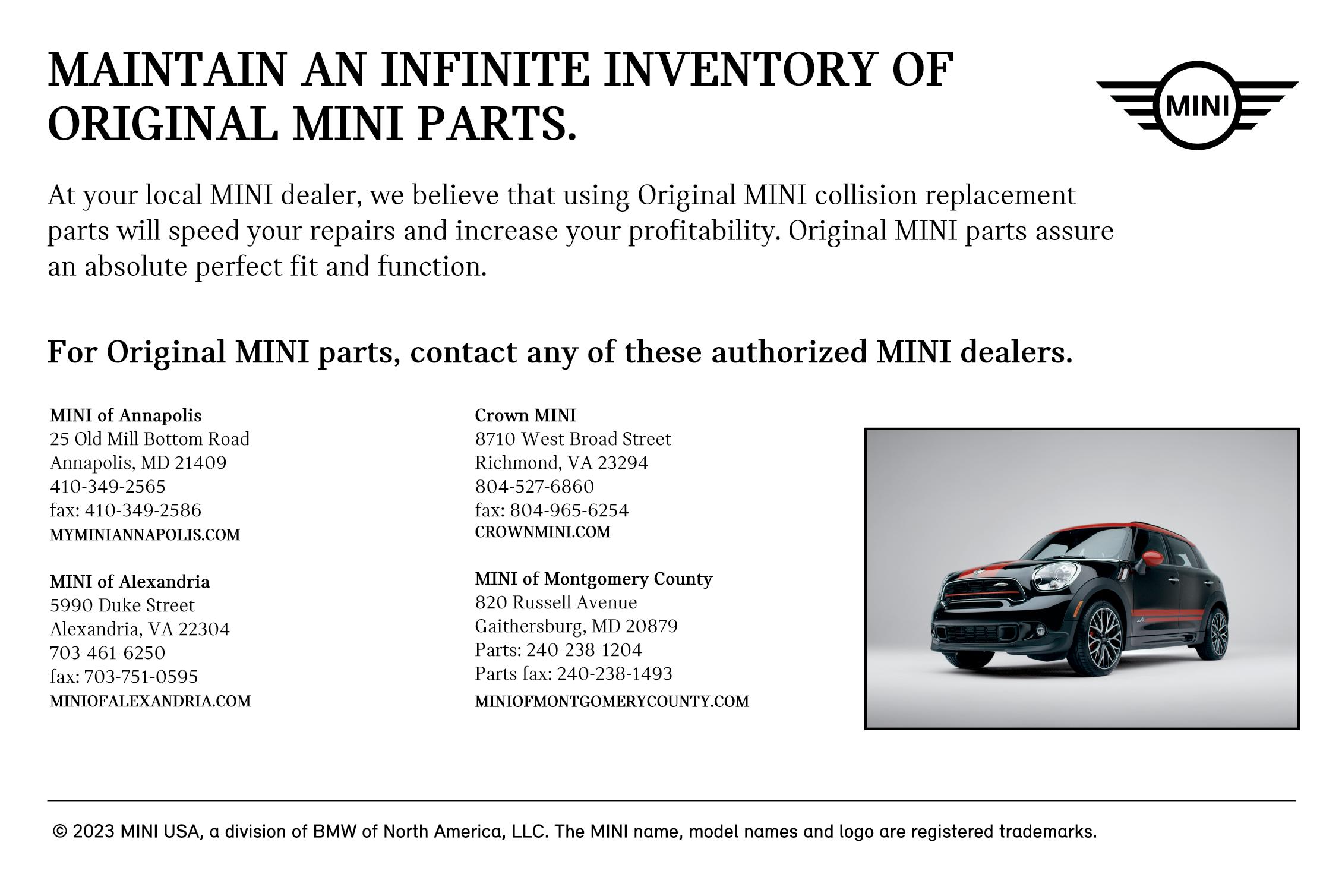
OFFICERS
PRESIDENT: Steven Krieps srkrieps@live.com 304-755-1146
SECRETARY: Phil Rice phil@ricewoods.com 540-846-6617
PAST PRESIDENT: Torchy Chandler torchy.chandler@gmail.com 410-309-2242
Bill Hawkins hawkinswilliamjr@gmail.com 510-915-2283 Barry Dorn bdorn@dornsbodyandpaint.com 804-746-3928
John Shoemaker john.a.shoemaker@basf.com 248-763-4375
VICE PRESIDENT: Rodney Bolton rbolton@aacps.org 443-386-0066
TREASURER: Kris Burton kris@Rosslynautobody.com 703-820-1800
BOARD OF DIRECTORS
Position Your Business as a Leader!
Just like equipment and training, WMABA membership is not only a commitment to excellence, but also a valuable investment.
WMABA is recognized both regionally and nationally as the key forum for the exchange of ideas concerning the D.C., MD, VA and WV collision repair industry. It is the venue to discuss, learn about and impact evolving standards and policies in the technical, administrative and legislative fronts of our industry. Shops and industry supporters can best develop themselves and their employees by actively engaging in the association and its activities.
Automotive collision repair facilities in Maryland, Virginia, West Virginia and Washington, D.C. who are willing to adopt WMABA’s Standards of Membership and offer a guarantee to their consumers are encouraged to engage their business as an active member of the association. For over 40 years, the WMABA membership of professional collision repair businesses and affiliates have committed to operating at a higher standard on behalf of their industry and their consumers. Over the years, WMABA has proudly represented the collision repair industry at hearings on Capitol Hill, in Annapolis, MD, and Richmond, VA as well as almost every national collision repair event. While WMABA has a rich history of dedicated men and women serving the local collision repair community, WMABA also boasts numerous past and current accomplished Board members who represent our membership at the national level.
WMABA offers current and dynamic discussion forums on topics facing collision repairers, technical information and educational seminars, opportunities to network and discuss pressing topics with leaders of the collision repair industry, an arbitration program that works with consumers to help resolve issues they might have, apprenticeship programs, legislative representation and the ability to receive and contribute to one of the nation’s leading collision repair magazines, Hammer & Dolly.
EXECUTIVE DIRECTOR: Jordan Hendler
jordanhendler@wmaba.com 804-789-9649