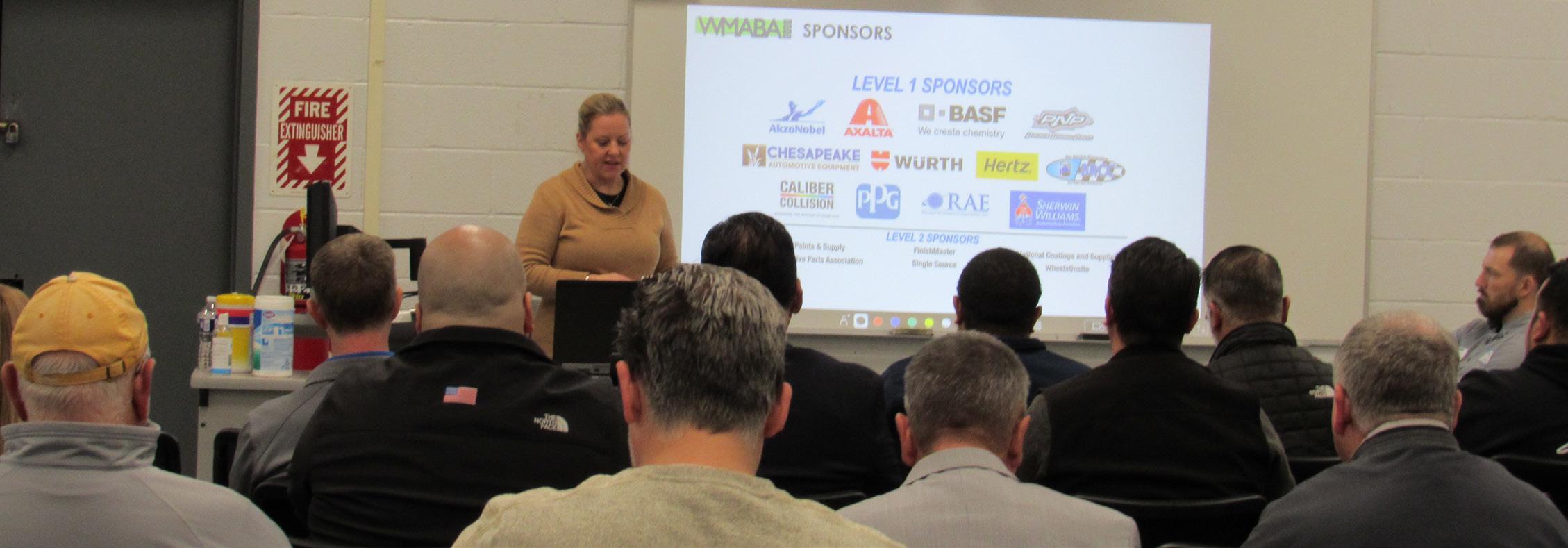
2 minute read
COVER STORY
Green light: repair planning.
BY CHASIDY RAE SISK
Michael Bradshaw (K&M Collision; Hickory, NC) believes it’s time to stop estimating.
“Many shops want to write estimates for every customer, but it’s time-consuming and often a waste of time because a large subset of customers are just looking for the cheapest estimate,” he stressed to the room full of collision repair professionals, gathered at Northern Virginia Community College (NVCC) in Alexandria, VA for WMABA’s Annual Membership Dinner. “We don’t write estimates in our shop because they’re inaccurate; we cannot determine what the vehicle needs until we disassemble the vehicle and conduct repair research.
“If our estimate goes up dramatically after we tear down the vehicle, the customer is upset…We put ourselves in a bad position from the start by not explaining what’s needed to get an accurate cost,” he explained. “So, we sell our customers on the process of being thorough and getting it right the first time instead of merely taking a guess.”
Instead, Bradshaw believes that shops should be writing repair plans, which are more accurate and efficient. As a result, they cause fewer delays and less administrative burden by reducing the number of supplements needed. Writing an accurate repair plan begins with accessing reliable sources, such as OEM information, Motor’s Guide to Estimating, the Database Enhancement Gateway (DEG), the Blueprint Optimization Tool, the Society of Collision Repair Specialists (SCRS) website, Refinish Manufacturer Tech Info, Collisionadvice.com and I-CAR’s Repairability Technical Support.
Using an actual repair plan on a Honda Pilot quarter panel from K&M Collision, Bradshaw reviewed the many steps that shops take when blueprinting a vehicle yet often neglect to include on estimates. Simply preparing for the repair blueprint includes numerous tasks, such as pre-washing, which Honda specifically recommends since it’s “impossible to properly inspect a dirty vehicle for damage.” He also stressed the importance of documentation, advising that his shop’s average workflow includes around 200 photos. During the pre-scan, shops should document the ADAS components on the vehicle and identify which calibrations are likely to be needed.
In addition to the mechanical/electrical and refinish operations, as well as the ADAS calibrations that might be included on a quarter panel replacement, Bradshaw also reviewed the structural operations that should be considered, observing, “If it’s attached using welding, weld-bonding or rivet-bonding, it’s structural. Period.”
“The repair blueprint essentially needs to tell the story of what you’re going to be doing to the vehicle,” Bradshaw emphasized. “It takes a little more time to be detailed, but you’re never going to collect what you’re worth if you’re putting everything on one line. When you break it out and show exactly what you’re doing, how many more labor hours could you legitimately pick up?”
Ultimately, Bradshaw revealed his blueprinting totals on the example he used, which included 35.6 hours of body labor, 33.4 hours of paint labor, 13.6 hours of mechanical labor, three hours of frame labor, one hour of diagnostic labor and 45 hours of structural labor. Once parts, materials and taxes were added, the total bill totalled $21,421.96 to put a quarter panel on the car.
“This is a good example because on the hundreds of estimates I see, I mostly see body and paint labor; but there are 12 labor types within CCC,” WMABA Board member John Shoemaker (BASF) pointed out. “You don’t see any frame or structural, yet your techs have done the same repair Michael just illustrated. They’re performing these repairs, so why aren’t you charging for it?”
Acknowledging that K&M struggled to get properly compensated for some line items at first, Bradshaw discussed the shop’s decision to take legal action and support customers in pursuing the Appraisal Clause in multiple cases.
“A lot of people believe they can’t do this, but if you could see where we were just 10 years ago…It’s about grinding and being consistent with your staff and how you do things in your business. If you can lead by example, others in your organization can buy in. Develop a plan and stick to it. Implementing QC processes to correctly prepare your repair plan can make a world of difference.”