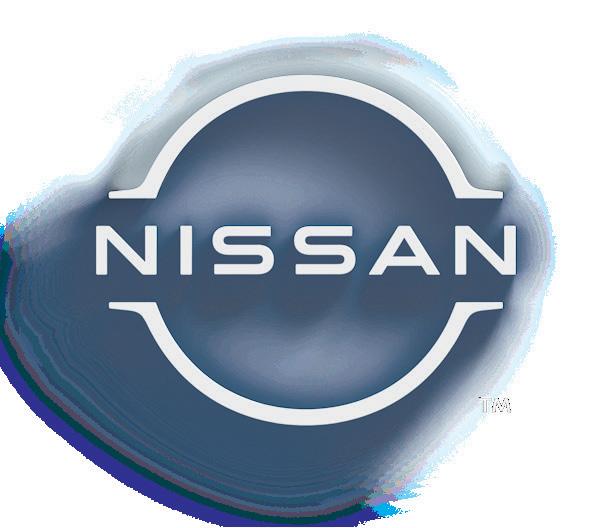
3 minute read
NATIONAL FEATURE
continued from pg. 23
“Attracting young people into our trade only solves half the problem because we’re pushing them into an industry that often is not a good fit for them culturally,” he pointed out, noting that experts predict that over 70 percent of the workforce will be Millennials and Gen Z by 2025. He suggested that “the perceived shortage is often the result of using highly skilled technicians to perform low-skilled work, so we have to ask if we are utilizing our A-techs wisely and how that is contributing to our so-called talent shortage.”
Although older generations often complain about the younger generations’ work ethic, Luehr suggested, “They know how to work hard; they just don’t want to work hard for you. I don’t believe we have a shortage of talent, but I do think we have a shortage of great places for them to work. This is a global issue that can only be solved locally, and it begins with each of us taking personal responsibility for the attractiveness of our businesses.”
Encouraging attendees to build a business that “defies the status quo,” Luehr explored five elements that shops can use to determine “if your business is attractive…or if it’s repulsive.” Those elements include meaningful work, acknowledgement, measurement, teamwork and goal guidance. “That’s how outlier businesses do it, and they get the best employees.”
The best employees often start as students, though, and the Talent Pool Committee invited Todd Grothe to discuss how the Newgate School’s unique business model is producing entry-level technicians. Founded nearly 40 years ago, the post-secondary non-profit technical school provides tuition-free automotive training and career placement for young adults.
“People donate cars, which the students repair, and then we sell the cars at auction,” Grothe explained how the school is funded. “This allows us to teach whoever we want; we’re completely autonomous.”
The school trains 10-15 students at a time, but rather than having official start and end dates for the school year, they accept students at any time, teaching them until they’re ready to graduate, which typically takes around nine months. The first two weeks are spent training them on detailing to gauge their interest in the field before moving students into either the mechanical or auto body program where they focus on repeating basic jobs until they start to develop the right habits.
“Some get really far really quick. We’ve had students that seem like they were born to do this,” Grothe said. “Others struggle the whole way through, but that doesn’t mean they won’t become great technicians too; everyone has different learning styles, and they all deserve a chance. Every so often, we’ll have a student, and it just never fully clicks with them, but they’re hard-working, so we’ll focus on training them on tasks they can excel at like becoming a solid detailer.”
By repairing and selling cars at auction, all students graduate without debt, and the Newgate School even equips them with an entry-level toolbox to begin their careers before helping them find local employment.
“I can certainly brag about having 100 percent placement,” Grothe boasted. “Part of that is because we really are a great school with a great program, but the other part is situational due to the industry’s needs.”
Since the school teaches basic skills, they’ve been able to get by with their current equipment, but “we’re certainly 10-15 years behind as far as where cars are now since we get donated vehicles,” Grothe acknowledged. “It hasn’t been an issue yet, but we’ll definitely need to invest in updated tools and equipment as the donated cars evolve.”
Demonstrating the importance of investing in collision students, Ron Reichen and Society of Collision Repair Specialists (SCRS) Board member Toby Chess took the stage for a presentation by the March Taylor Memorial Fund which was designed to give “the next generation of collision repair techs a step upward through tool scholarships and mentorship.” Tools awarded to the Center for Educational Technology and Excellence (Salem, Oregon) were accepted by instructor Alex Crays, accompanied by three students who spoke about their experiences at the school and expressed gratitude for the opportunities their education will provide. For more information about the March Taylor Memorial Fund, visit marchtaylorfund.org
Talent Pool Committee Co-Chair Petra Schroeder indicated that rather than reinventing something that has already been invented, it may benefit the industry to look for opportunities to collaborate. “We’ve been talking about this topic for a while. We all experience trouble with not having enough workers, but there’s a lot of energy at many levels to attract, advance and retain technicians. Various marketing efforts showcase how much technology is present in today’s cars and what’s necessary for a safe and proper repair, but I can guarantee that not many people outside our industry know these things.
“The tremendous changes in our industry over the last decade have gone largely unnoticed by the general public, and I believe it’s critical to combine forces, collaborate and share ideas, concepts and resources in the interest of collision repair professionals nationwide, to drive awareness and highlight the appeal of the exciting and rewarding career opportunities within our industry,” she expressed, suggesting the industry work together to hire someone like Mike Rowe of Dirty Jobs or Jay Leno to “assist in getting our message out to schools, students, instructors, administrators, parents, families and to the general public.”
CIC’s next meeting is scheduled for April 12-13, 2023 in Richmond, VA. Registration information, as well as presentations from previous meetings, can be found at ciclink.com H&D
Parts and the perfect fit at the perfect price. 10% off on all parts orders when you mention this ad.
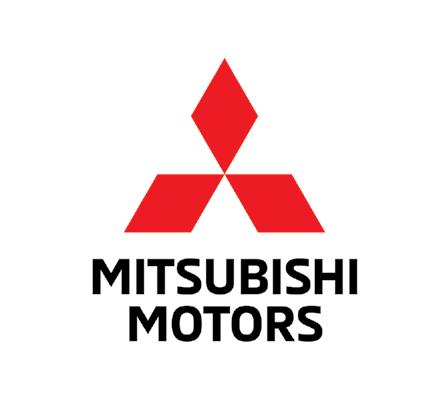

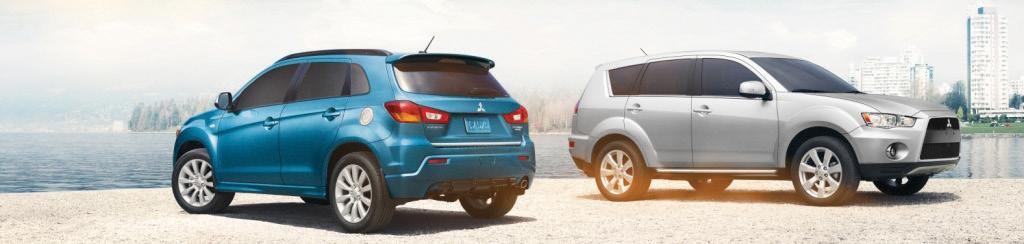
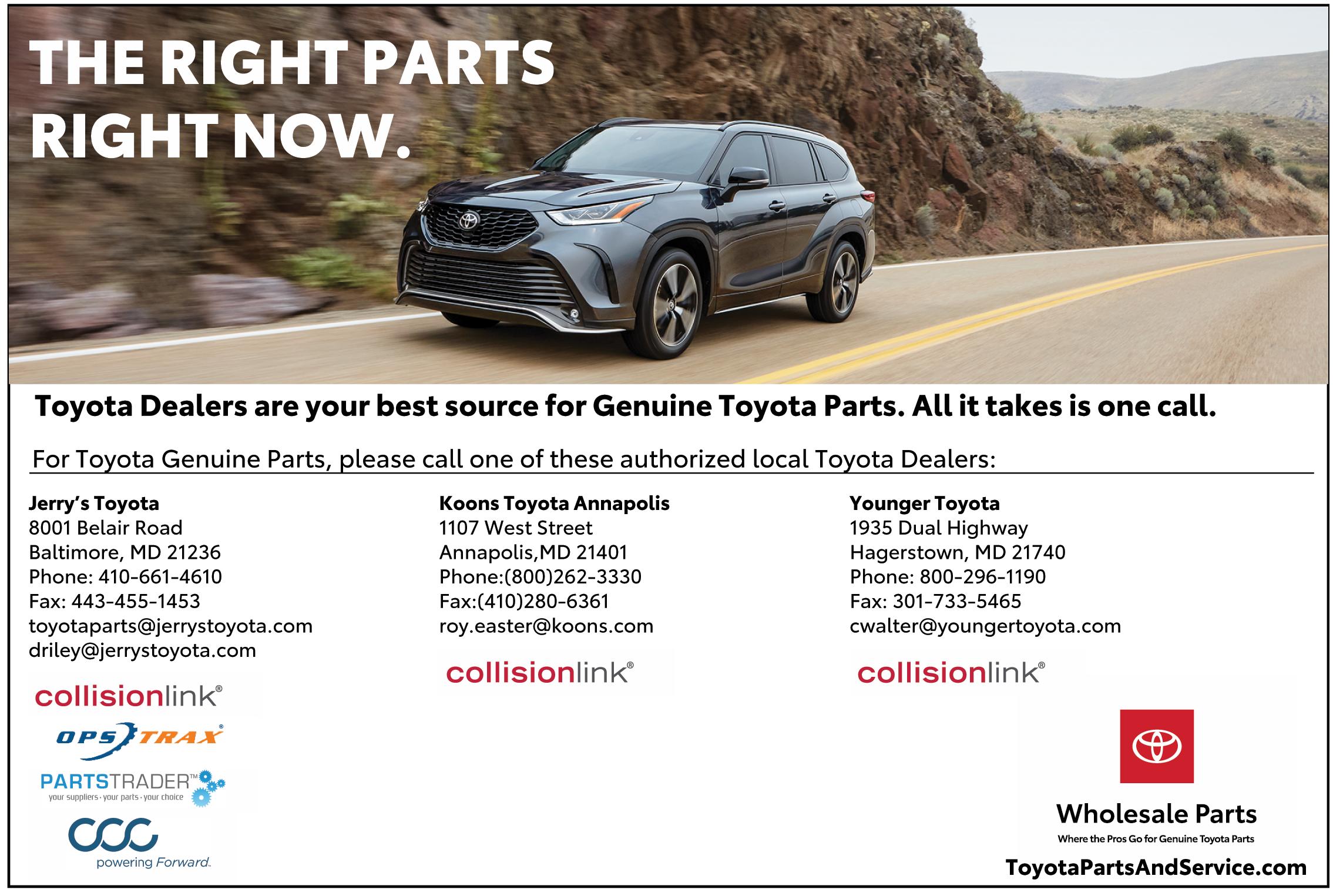
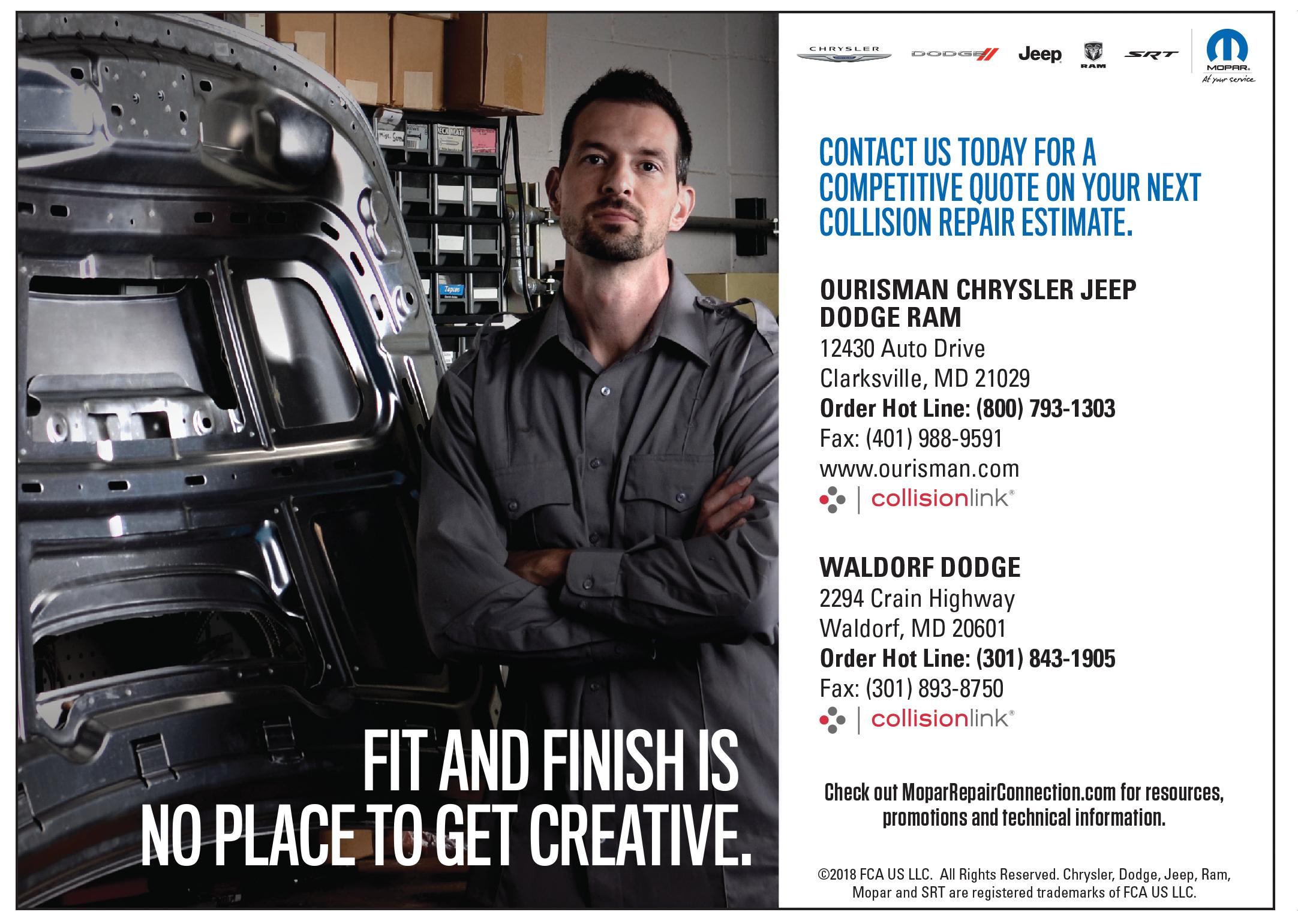