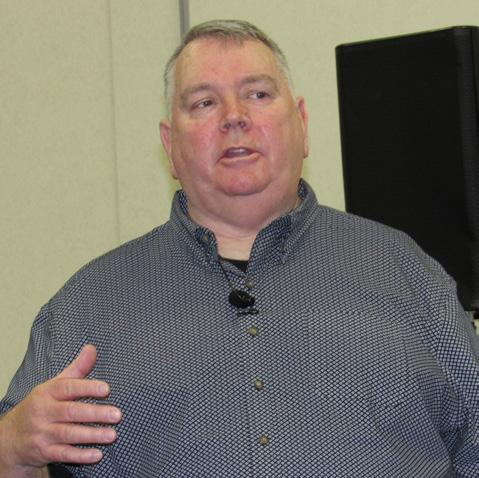
1 minute read
What’s an OEM Certification Auditor Looking For?
Repairers often dread an OEM certification audit, but understanding the auditor’s objectives and the Repair Quality Assessment (RQA) process can actually help shops better manage their businesses and the quality of their repairs every day. Rick Miller (Wadsworth International) and Dennis Smoyer (Subaru) explained the process “From an Auditors’ Perspective, where Repairers are Hitting and Missing the Objectives.”
Auditors are assessing everything about a facility to identify how it will impact the customer’s experience, from the standards compliance to administrative systems and operations, tools and equipment. The RQA is built around technology and vehicle safety, according to Miller, who identified the OEM’s desired result as a “positive customer experience from a stress-purchase scenario, ensuring a safe and quality repair.”
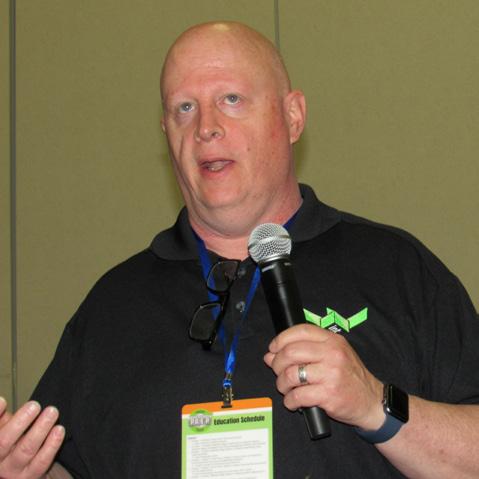
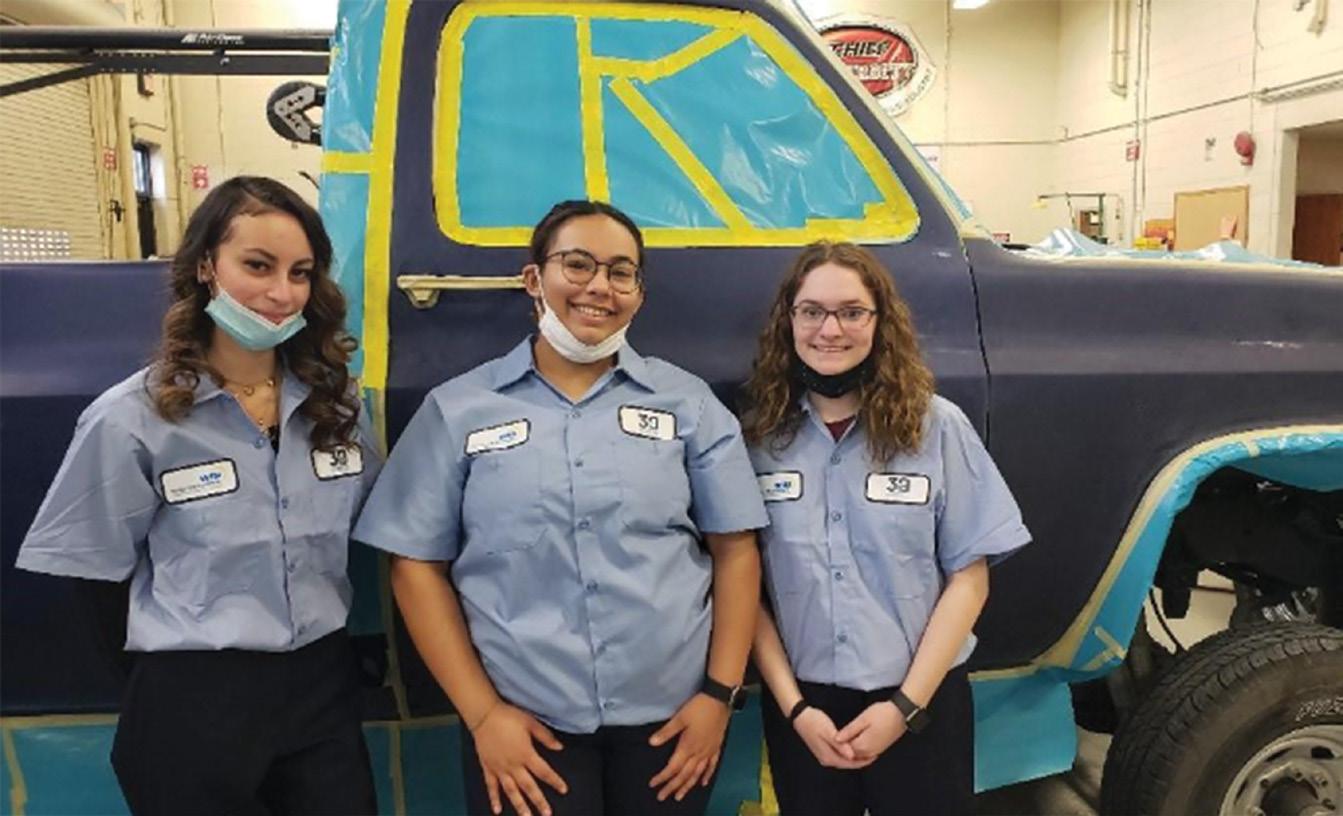
Correct documentation, especially pulling repair procedures on each vehicle, is a vital component in audits, but Smoyer stressed, “While having the procedures in your file is one thing, following them is absolutely critical. If you’re on an OEM network, you’ve got to follow procedures…no ifs, ands or buts.”
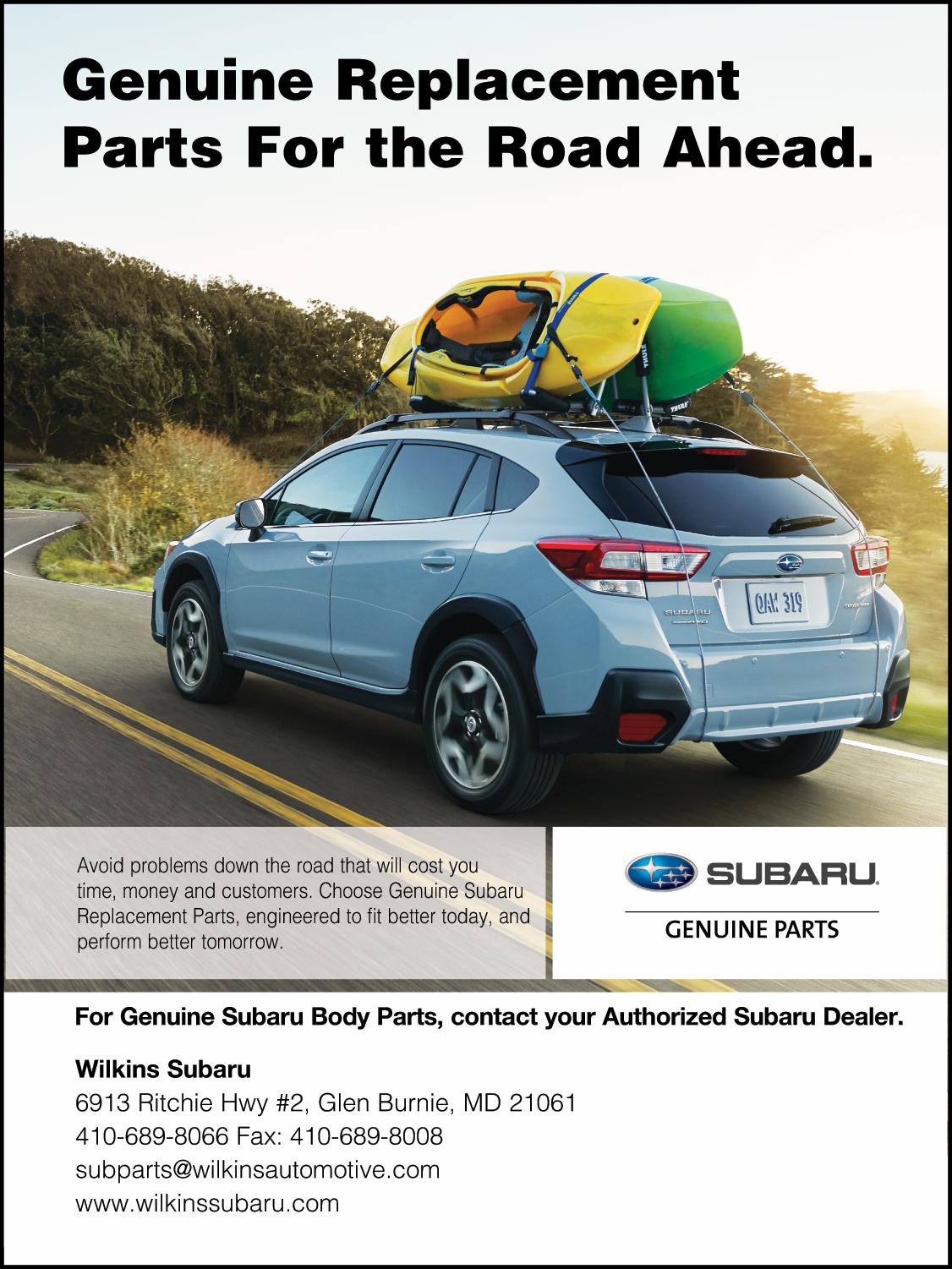
Auditors also evaluate weld quality, often finding “terrifying welds that will never hold up in a subsequent accident,” Miller lamented. “An auditor’s job is to tell you what you’re not doing correctly.
“The customer should not be your quality control. If they are, it’s way too late in the process,” he added, emphasizing the importance of shops performing their own in-process QC throughout the repair. “You need to do a RQA on your own business every day!”
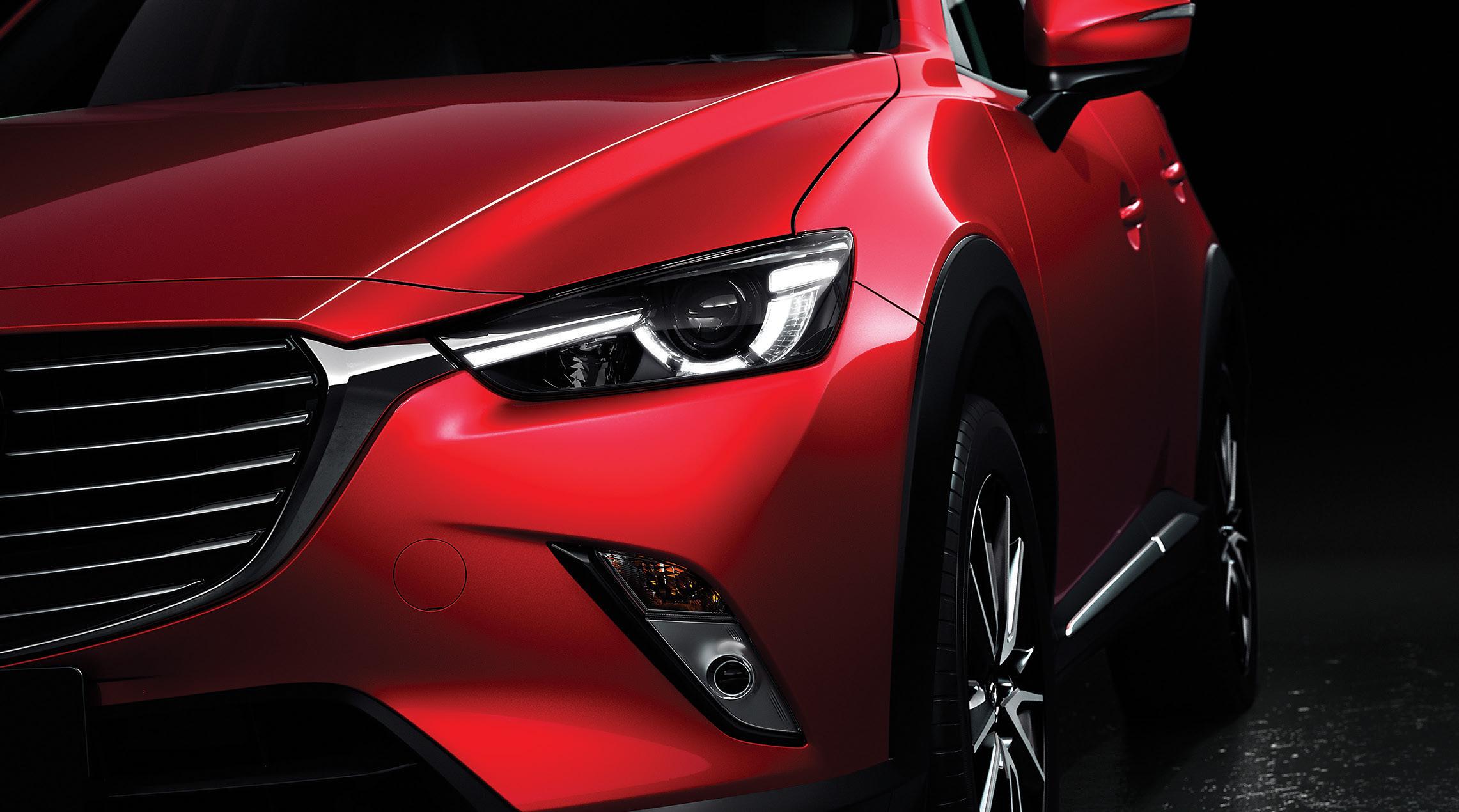
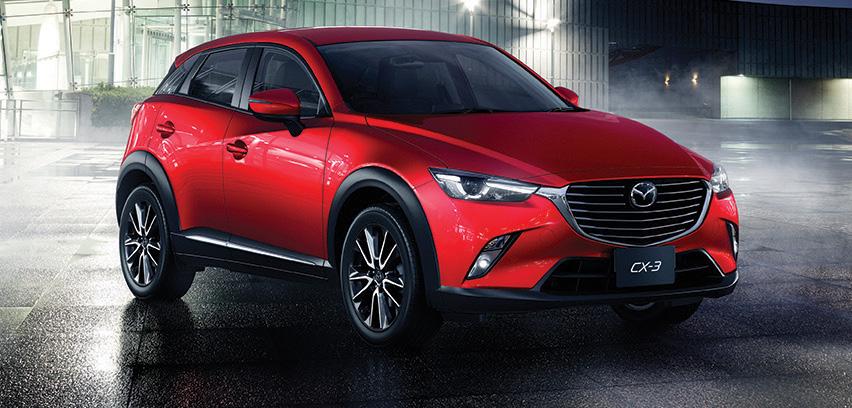