
13 minute read
The Next Big Challenge: Preparing for the Electric Vehicle Wave
The Next Big Challenge:
Preparing for the Electric Vehicle Wave
This industry is never short of moving targets in terms of automotive technologies, but the rise of electric vehicles (EV) is one item that needs to be on top of every collision repair facility’s list of things to know about now.
If you think EVs are simply an exotic and specialized segment of the automotive market that will not impact the work you perform, it’s time to take a closer look at where automakers plan to be in just a few short years. For example, General Motors recently made headlines by announcing plans to stop making gasoline and diesel-powered vehicles by 2035. GM drove home its commitment to EVs in a statement posted on its consumer-facing website (gm.com/electric-vehicles.html):
GM is on its way to an all-electric future, with a commitment to 30 new global electric vehicles by 2025. We are aggressively going after every aspect of what it takes to put everyone in an EV, because we need millions of EVs on the road to make a meaningful impact toward building a zero-emissions future. GM is positioned to design, engineer and produce EVs for every style and price point, and we are rapidly building a competitive advantage in batteries, software, vehicle integration, manufacturing and customer experience.
Of course, motions by GM and other car manufacturers to board the EV train with greater frequency mean that experienced technicians are needed to properly repair and service such vehicles – and the learning curve will be massive. As just one example of the change about to hit shop floors, EVs generally have fewer than 20 moving parts versus the more than 2,000 found in traditional combustible-engine vehicles.
For some OEMs, the seeds for EV training are largely being planted at the dealership level for the time being. As of this writing, Audi is one OE that is focusing on getting its dealers up to speed on EVs first before branching out to other facilities.
“If you look at the tool packages that are required, the investment is fast approaching $100,000 just for hardware – and then there is that pesky tech training issue,” Mark Allen, collision and equipment manager for Audi of America, explained in a recent conversation with New England Automotive Report. “These are highly specialized skills with a danger quotient applied.”
For its part, I-CAR has been actively working to stay ahead of the EV trend and provide training to the industry at-large. The following is a small sampling of the I-CAR EV-related courses currently available, with some developed and launched within the last handful of months:
Hybrid Vehicle Identification & Damage Analysis
This course explains the different types and parts of hybrid and electric vehicles. Hybrid vehicle identification and important safety procedures when inspecting electrified vehicles, including steps to disable a hybrid system and an overview of the cooling systems for a high-voltage battery, are also covered.
Introduction to Electric Vehicles
This course introduces the different types of EVs on the road today and identifies the unique parts of an EV and the purpose of those parts. Video is also included to highlight the steps for operating an EV for the first time.
Understanding High Voltage Safety
This is a course that explains the elements of electricity and the relationship between voltage, current and resistance with highvoltage systems. This course describes the effects of electricity on the body and lists the required PPE when working around high voltage.
Electric Vehicle (EV) Initial Inspection & Handling
This course discusses initial inspection and safety considerations for EVs upon arrival at a repair facility. Precautions and considerations for high-voltage batteries and systems and vehicle staging/handling of damaged vehicles are also covered.
Electric Vehicle (EV) Damage Analysis
This course reviews necessary safety precautions when working with EVs. It provides detail on an EV’s high-voltage components, safety precautions and relevant non-high-voltage parts.
Jeff Peevy, I-CAR’s vice president of technical products, programs and services, pledges that the organization will be there for technicians and owners every step of the way as they work to quickly adapt to working on this new breed of automobile.
“Today, the big thing seems to be battery-powered electric vehicles, but that’s just the next thing – there’s stuff lining up behind that. I-CAR is not unlike a collision repair shop; we have a lot to invest in and a lot to learn. We needed to set ourselves up so that we culturally could take our ability to expedite new technology, research it, learn, work with the car manufacturers and convert that into training quicker and quicker – and just be more efficient and effective at it.”
Although shops have plenty to contend with in the here and now, electric vehicles are poised to greatly impact – and perhaps overwhelm – any facility that is not staying on top of the trend and the resources currently available to prepare for the near future. Look for ongoing news and information on this topic in future issues of New England Automotive Report.
PROTECTING CONSUMERS AND THE COLLISION INDUSTRY
MASSACHUSETTS
Hours: M-F: 7am-6pm Sat: 7am-1pm
NEW ENGLAND’S NEWEST MOPAR DEALER
777 Washington Street • Newton, MA02160

Call Us For All Your MOPAR Needs or visit us on the web: www.mcgoverncjdrofnewton.com
For First Time Customers, Call me: Mando Bogosian, Wholesale Manager
Hours: M-F: 7am-6pm Sat: 7am-1pm TOLL FREE: 800-741-7563 DIRECT: 617-454-2990 FAX: 617-467-0006
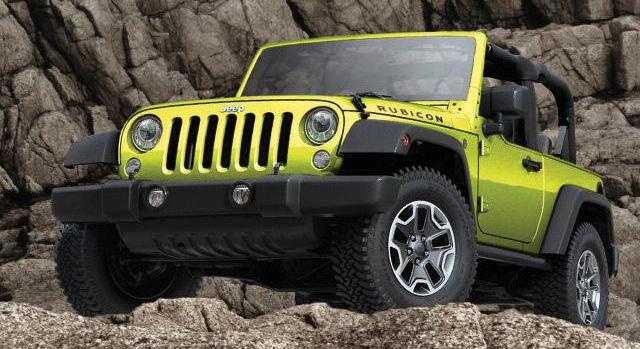
Call us and get the right MOPAR parts the FIRST TIME!

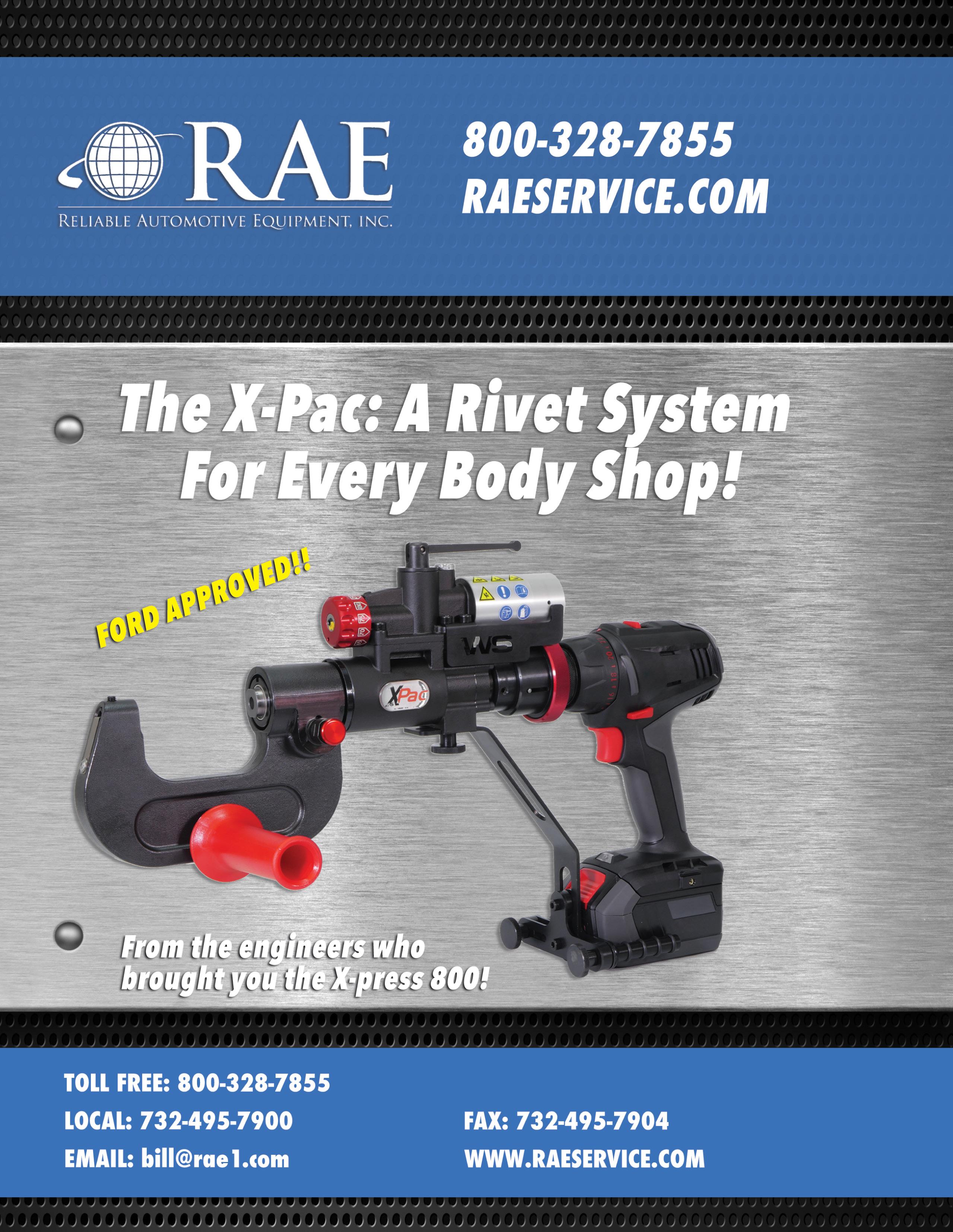
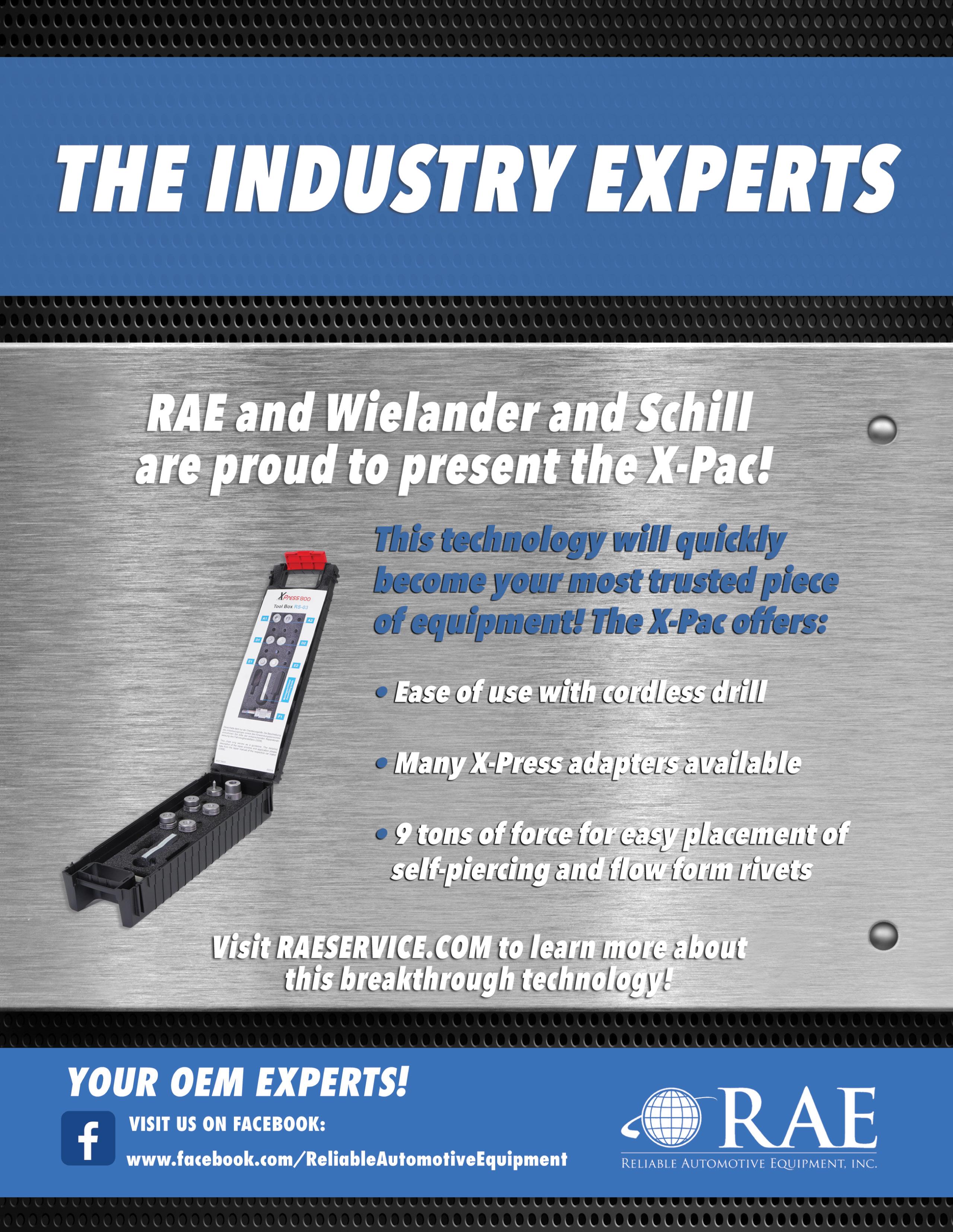
[AASP/MA] FEATURE by Alana Bonillo
The Road Ahead:
AASP/MA Members Work toward Post-Pandemic Normalcy
To say the last 18 months have been a challenge would be an understatement. But as the collision repairers of the Commonwealth have proven time and time again, it takes a lot to keep this industry down. Now that the COVID-19 threat has begun to subside and things are finally beginning to resemble regular life, AASP/ MA and its member shops are brushing themselves off and picking up in order to emerge stronger than ever.
Thankfully, the association never missed a beat during the entire crisis. AASP/MA worked daily to provide members with vital resources about PPE protection and PPP loans and continued to bring shops together by way of monthly virtual educational seminars and training meetings.
With busier times on the horizon for shops as the summer months come into play, the association is now working to help make the transition for its members as smooth as possible.
“We will continue as we did throughout the COVID-19 time to provide the assistance to our members, their customers and the industry,” AASP/MA Executive Director Evangelos “Lucky” Papageorg comments.
Looking back over this past year plus, he believes there were some positives among the hardships in the way member shops continued to come together in a web-based format.
“Through meetings and seminars via the Zoom platform, we stayed in touch with our membership so that they knew they were not alone in the battle to survive. We will continue to service their needs in whatever way they need.
“In some instances, the further apart we were forced to stay, the closer together we became,” he adds. “Being forced to communicate through electronic methods in many instances was a time-saving benefit.”
Unfortunately, the contactless methods that insurers adapted created downsides in the way shops were forced to negotiate. Papageorg says there were far too many instances of insurers taking advantage of the situation. However, he does see an unexpected benefit in that shop owners had to improve their methods of documentation and pay more attention to what they were getting back from insurance companies. On the downside, this also created more administrative tasks for shops with no increase in reimbursement.
Thankfully, things are looking up for collision repair businesses, as many are reporting an increase in the amount of vehicles they see coming in. Of course, compared to this time last year, it’s easily like comparing night and day. The better news is that it appears as though business is beginning to resemble what it was like before the pandemic started.
Rick Roberts of Midway Collision Center confirms business is looking up at his Norton-based shop.
“Things are starting to pick up and get busier. We are on the road to getting back to where things were.”
AASP/MA Zone 3 Board member Andrew Potter (North Amherst Motors, Inc.; North Amherst) is witnessing business coming back but is experiencing understaffing in light of the pandemic. As a result, he has been forced to be more handson than he has been in the past.
“We’re picking up momentum, but we are still staffed thinner [than before].” Things are on the upswing at Auto Body Builders, Inc. in Middleton, where AASP/MA Zone 4 Board member Paul Tuscano is seeing his schedule increase. Additionally, he has begun to venture into other possible avenues beyond the traditional auto body realm, including work on heavy equipment, trucks or other larger vehicles.
“Even though there are more cars out there, we have noticed a slight decrease every year as cars are getting more advanced and are equipped to avoid accidents.”
As COVID-19 cases continue to decline and more of the population becomes vaccinated, AASP/MA looks forward to once again hosting in-person events and hopes to conduct its first face-to-face event in October. Papageorg also plans to attend AASP/NJ's NORTHEAST® Automotive Services Show in Secaucus, NJ this September 10-12.
“Once we are able to resume faceto-face interaction, visit shops and hold meetings where attendees actually see others around them, AASP/MA will once again gain the momentum we were experiencing in local chapter meetings and an increase in membership. There is a lot to be said for seeing a colleague in the room with you versus their face in a little block on your computer screen. The in-person interaction is more conducive to conversation and the exchange of ideas while nurturing true camaraderie. We are an ‘Alliance’ that is truly strengthened when we are together.”
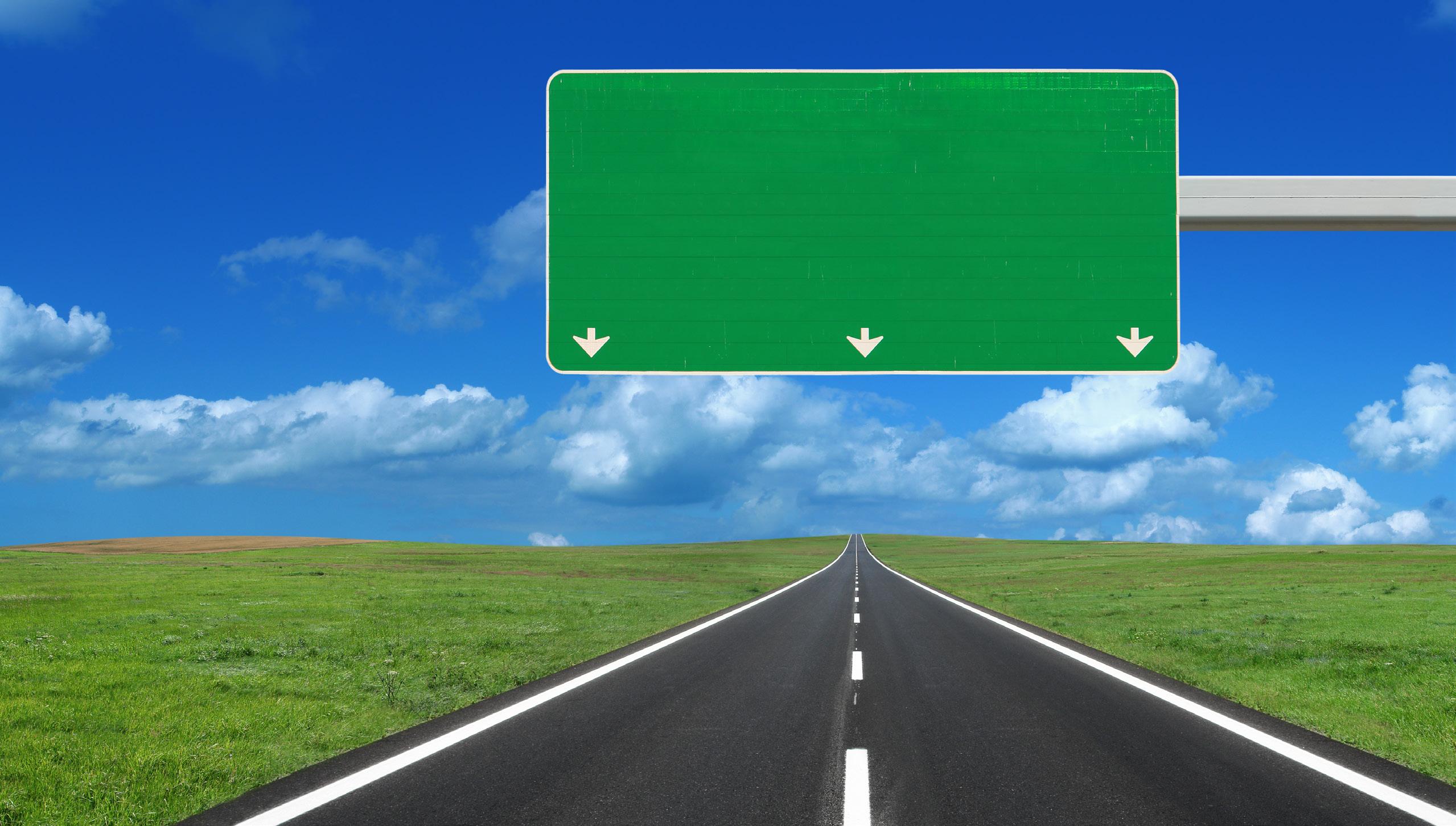
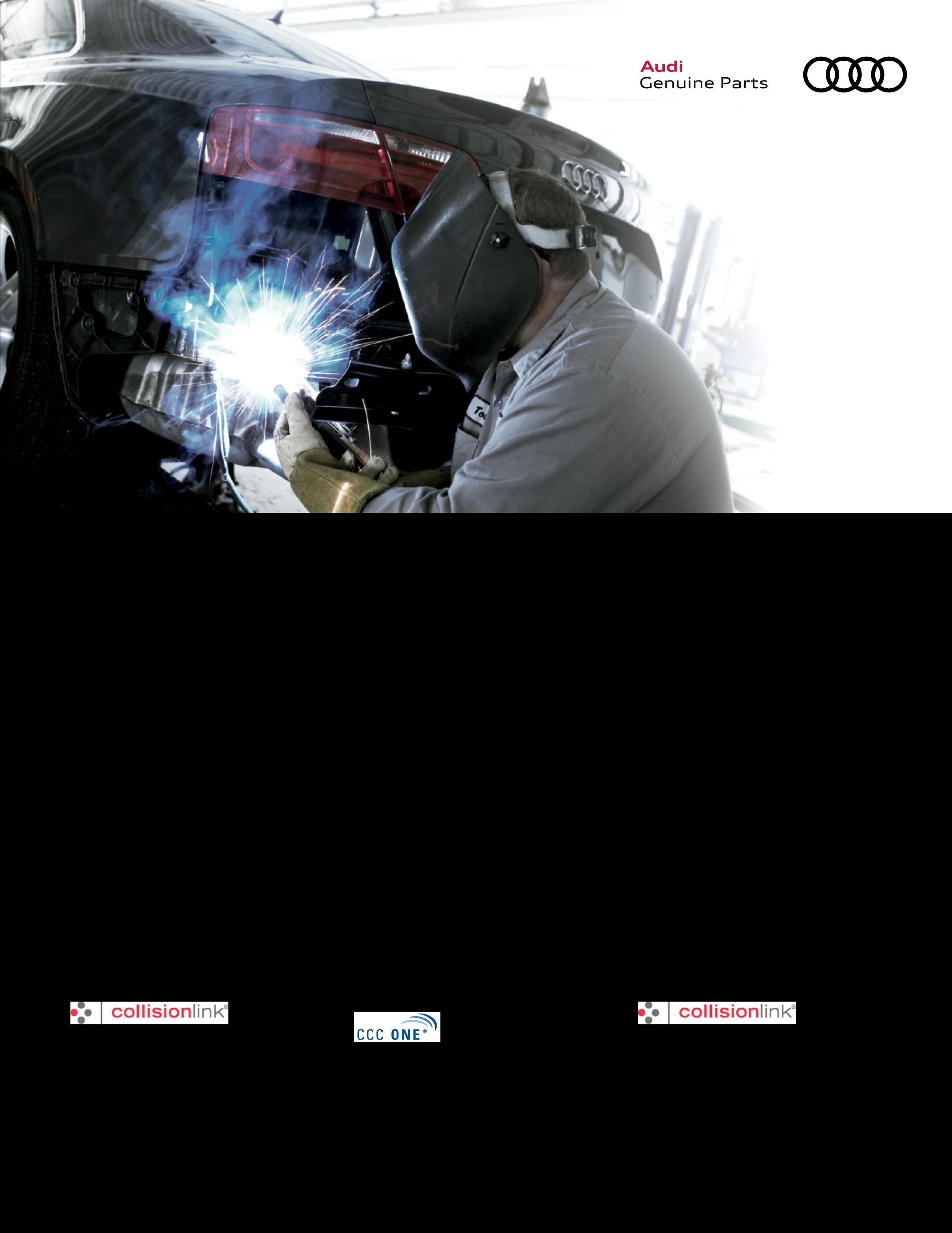


WHOLESALE PARTS
800.992.6220
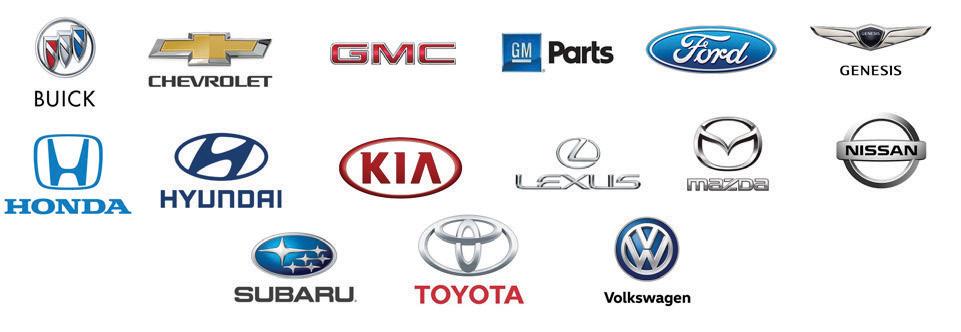
WHOLESALE PARTS 800.992.6220
GM PARTS .................Press 2
FORD .........................Press 5
HONDA .....................Press 3
HYUNDAI ..................Press 7
KIA ............................Press *
LEXUS ........................Press #
MAZDA .....................Press 6
NISSAN ......................Press 4
SUBARU ....................Press 8
TOYOTA .....................Press 1
VOLKSWAGEN ...........Press 9
O ne Call, One Truck and 11 franchises delivered to your Collision Center!
◊ Team of 11 parts professionals to assist you with your wholesale parts needs ◊ 30 Trucks on the road daily serving MA, CT and RI ◊ Two deliveries per day in most markets ◊ Web Based dispatching tools with real ti me ETAs ◊ Three Field Sales Professionals to assist you ◊ $6.1 Million in Inventory to support our Wholesale Customers’ needs
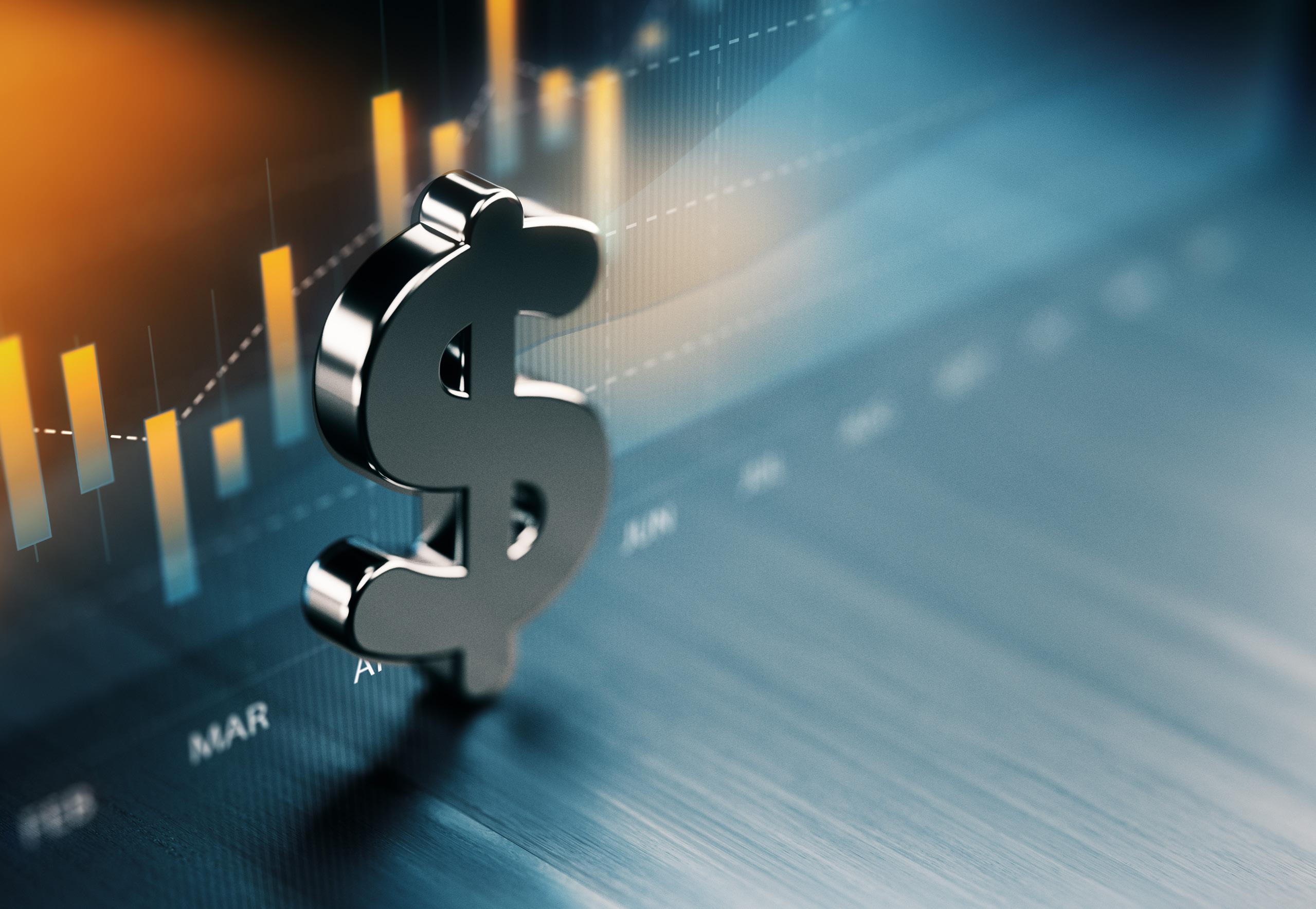
A Better Path to Profitability:
AASP/MA Helps Lead the Way
There isn’t a single business in collision repair that doesn’t want to make more money, but sometimes a shop neglects to realize that the key to improving its bottom line is already in its hands.
This was the critical takeaway from AASP/MA’s most recent General Virtual Membership Meeting, which featured “Estimating Solutions for Profit,” a guest presentation by Lee Rush of Silver-level Vendor Affinity Program (VAP) sponsor Sherwin-Williams Automotive Finishes. The hourlong discussion provided attendees with insights into how to incrementally improve profitability through greater estimate accuracy, eliminate in-shop inconsistencies and – perhaps most significantly – potentially beat insurers at their own game.
A large portion of Rush’s presentation detailed what he called the “five-to-10 percent strategy” of increasing profits through consistent processes and procedures. By addressing “leakage” such as not-included items and small material compensation that is consistently missed on estimates, a facility could develop ways to add five-to-10 percent increases to each repair, gradually adding up to considerable additional revenue over time.
Most important of all, shops that utilize this “five-to-10 percent” philosophy could succeed in counteracting similar methods already employed by the insurance industry.
“It’s the same strategy that’s being used in reverse against the shops. The insurance companies have rarely come to our industry and hit us hard with massive reductions in compensation. It’s usually small, incremental and tolerable decreases […] The reality is, for 20-something years, they’ve been eroding the compensation that we get to restore vehicles.
“We’ve got to flip the script and begin incrementally and cumulatively improving the consistency of our compensation,” he added.
Rush recommended a host of resources that could benefit shops in developing a strategic plan for improved estimatics and profit, including the Society of Collision Repair Specialists’ (SCRS) Guide to Complete Repair Planning, oem1stop.com, the I-CAR Repairability Technical Support Portal and the quarterly “Who Pays for What?” surveys conducted by Collision Advice and CRASH Network. Although OEM websites are obvious resources for recommended/required repair procedures, he cautioned that end-users must access them on a regular basis to receive the most accurate and up-to-date information.
Not surprisingly, he noted that a “five-to-10 percent” strategy would only thrive if a shop puts in the work to establish a system of checks and balances to identify and address missed profit opportunities. “The opportunity for us lies within consistency. I’m sorry, but if you’re depending upon your memory, then you’re going to have some oversights. You’re going to miss those small, incremental, compensable operations or materials – and you’ve got leakage.”
Additionally, he emphasized the importance of inshop standardization as one tool to achieve higher profits, encouraging attendees to create scenarios where “every station – whether it’s a laptop or a PC in the front – is standardized to ensure consistent analysis and easy access to all the data in your estimating systems.”
Above all, Rush stressed that the collision industry needs to focus greater attention on providing consistent training to employees. He noted that while shops typically train their front-end staff every three to five years, insurers do the same for their adjusters and appraisers every 45 to 60 days.
AASP/MA members are strongly urged to view the entire “Estimating Solutions for Profit” video presentation, which features discussion points and information beyond what is featured in this article. The entire presentation is available in the Members Only section of aaspma.org.
HELPFUL LINKS: OEM1STOP: oem1stop.com SCRS’ Guide to Complete Repair Planning:
bit.ly/SCRSguide
crashnetwork.com/collisionadvice
I-CAR Repairability Technical Support Portal:
rts.i-car.com
Sherwin-Williams Automotive Business Development Training courses: ecoleanuniversity.com
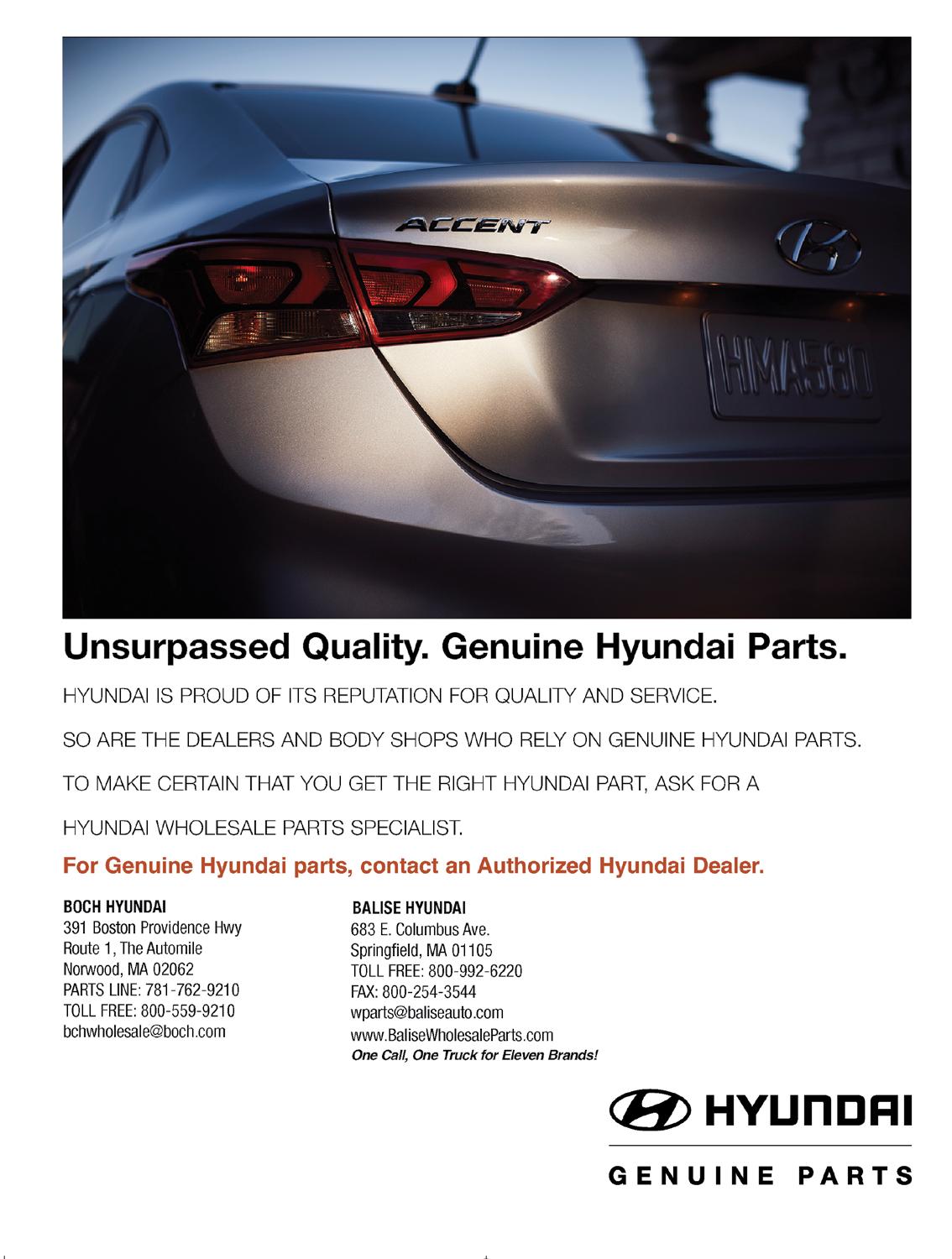
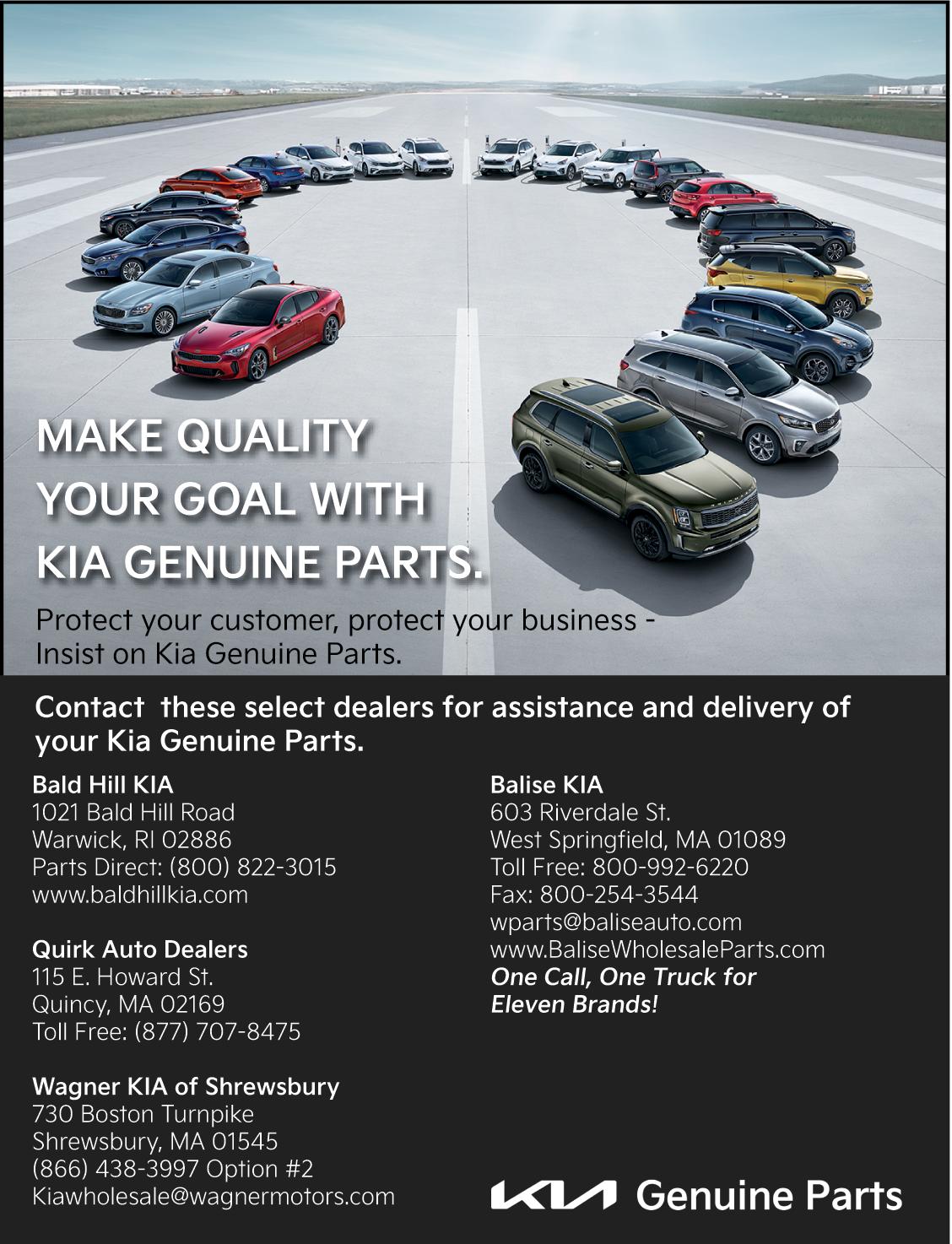
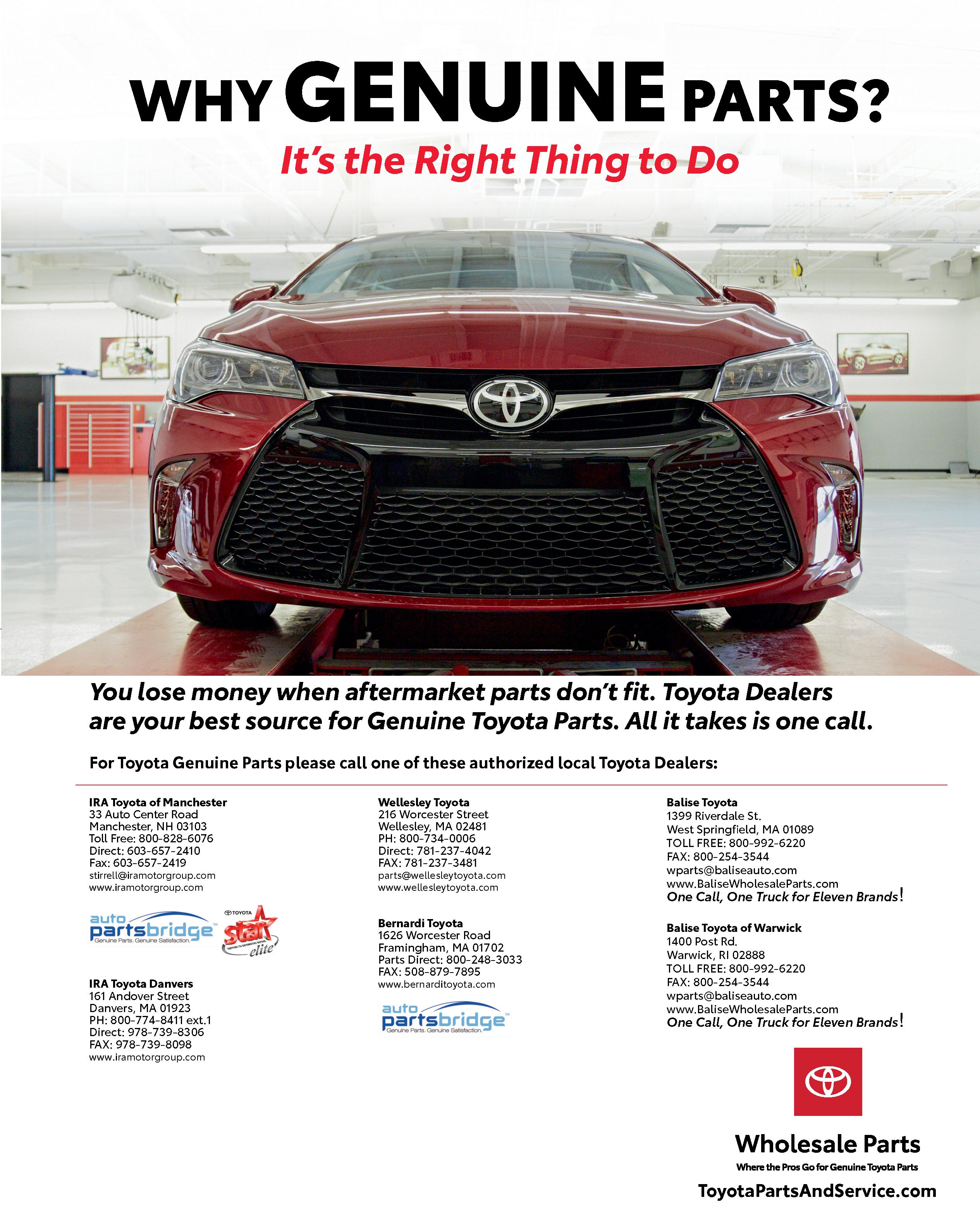