
43 minute read
COLLISION CHAIRMAN’S MESSAGE
Will Funds from the Infrastructure Investment and Jobs Act Benefit the Automotive Industry?
by DENNIS CATALDO, JR.
The 1.2 trillion dollar “H.R. 3684 — 117th Congress: Infrastructure Investment and Jobs Act” currently sits on our fearless leader’s desk, waiting for him to sign it into law (if he could just remember to ask his handler for a pen). Did you know if you could spend at a rate of $40/second, it would take 792.5 years to spend one trillion dollars? That seems like an awful lot of money to me, so I decided to take another look at several parts of what has now become a 1,039-page bill to see how it pertains to the automotive sector - our industry of automotive repair. SEC. 13008. WILDLIFE-VEHICLE COLLISION RESEARCH will allocate funds to research enhancing vehicles’ ability to detect wildlife and prevent vehicle collisions. SEC. 24109. REVIEW OF MOVE OVER OR SLOW DOWN LAW PUBLIC AWARENESS would fund attempts to increase driver awareness to ensure they know that they should move over for police, emergency vehicles and tow trucks operating on the side of the road.
SEC. 24112. SAFE STREETS AND ROADS FOR ALL GRANT PROGRAM would fund research to increase the effectiveness of pedestrian detection of motor vehicles.
SEC. 24202. RECALL COMPLETION is intended to allow the Federal Government to get a better handle on vehicle recalls. They want to know the overall number of vehicles recalled by manufacturers as well as the amount of completed recalls performed by those manufacturers. This section also shows a desire to increase awareness of vehicle recalls by requiring vehicle manufacturers to notify manufacturers, distributors, owners, purchasers or dealers of defective parts or materials.
SEC. 24203. RECALL ENGAGEMENT would grant a study into the reasons why vehicle owners do not have repairs performed for vehicles subject to open recalls. It would also examine whether engagement by third parties, including state and local governments, insurance companies or other entities, could increase the rate at which vehicle owners have repairs performed for vehicles subject to open recalls.
SEC. 24214. HOOD AND BUMPER STANDARDS requires hood and bumper standard upgrades to better protect pedestrians and bicyclists during a collision with a motor vehicle. SEC. 25006. ELECTRIC VEHICLE WORKING GROUP would create a government-backed study group with the intention of increasing the number of electric vehicles (EVs) sold in the marketplace, figuring out where the infrastructure would need improvement and how to deal with current raw material shortages for battery components. A good amount of the bill is dedicated to both improving the infrastructure of the electric grid across the country as well as increasing our capacity to create new “hi-tech” or “advanced” battery systems within the United States plus increase our abilities to recycle current battery systems for reuse or raw material components. SEC. 70953. REQUIREMENT OF LONG TERM CONTRACTS FOR DOMESTICALLY MANUFACTURED PERSONAL PROTECTIVE EQUIPMENT addresses something that we all dealt with firsthand last year: The lack of access to PPE. This section would mandate USproduced PPE in American facilities to safeguard public health and national security. A trillion dollars (or one million millions) is an incomprehensible figure. To put it into perspective, a trillion seconds equals 31,710 years! Such an enormous amount of money could certainly do a lot of good for our industry - and for society in general - but after reading through H.R. 3684, I have to wonder: Are we spending it in the right ways?
NJA
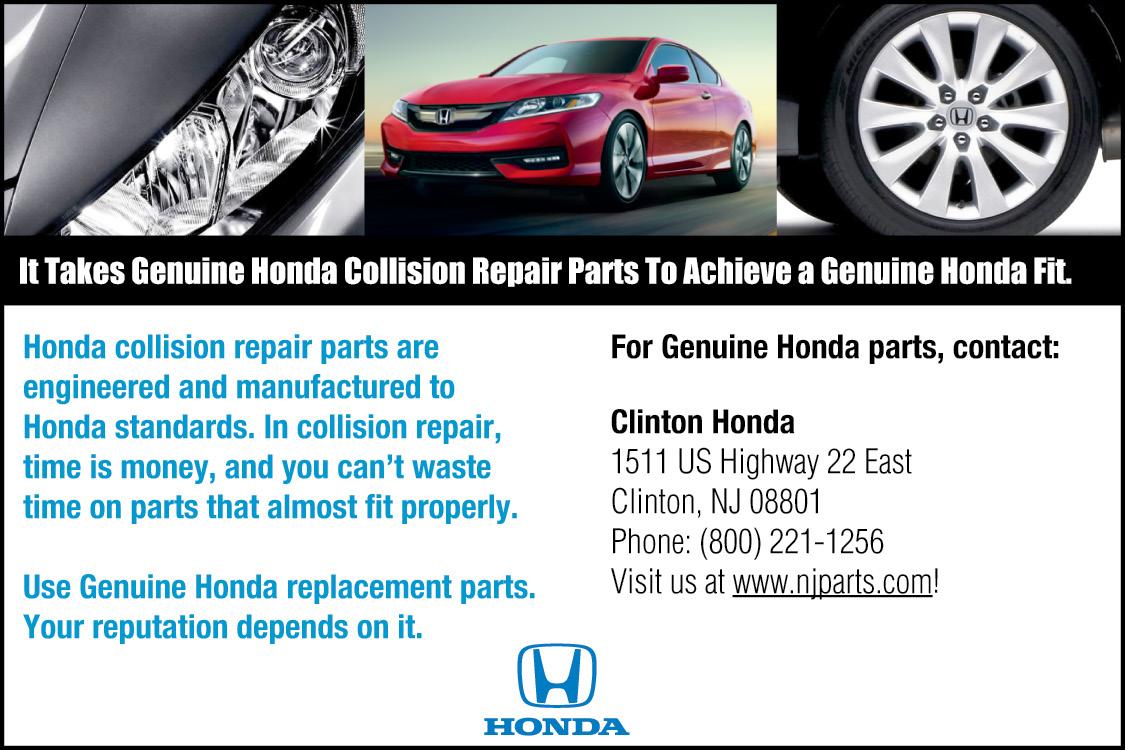
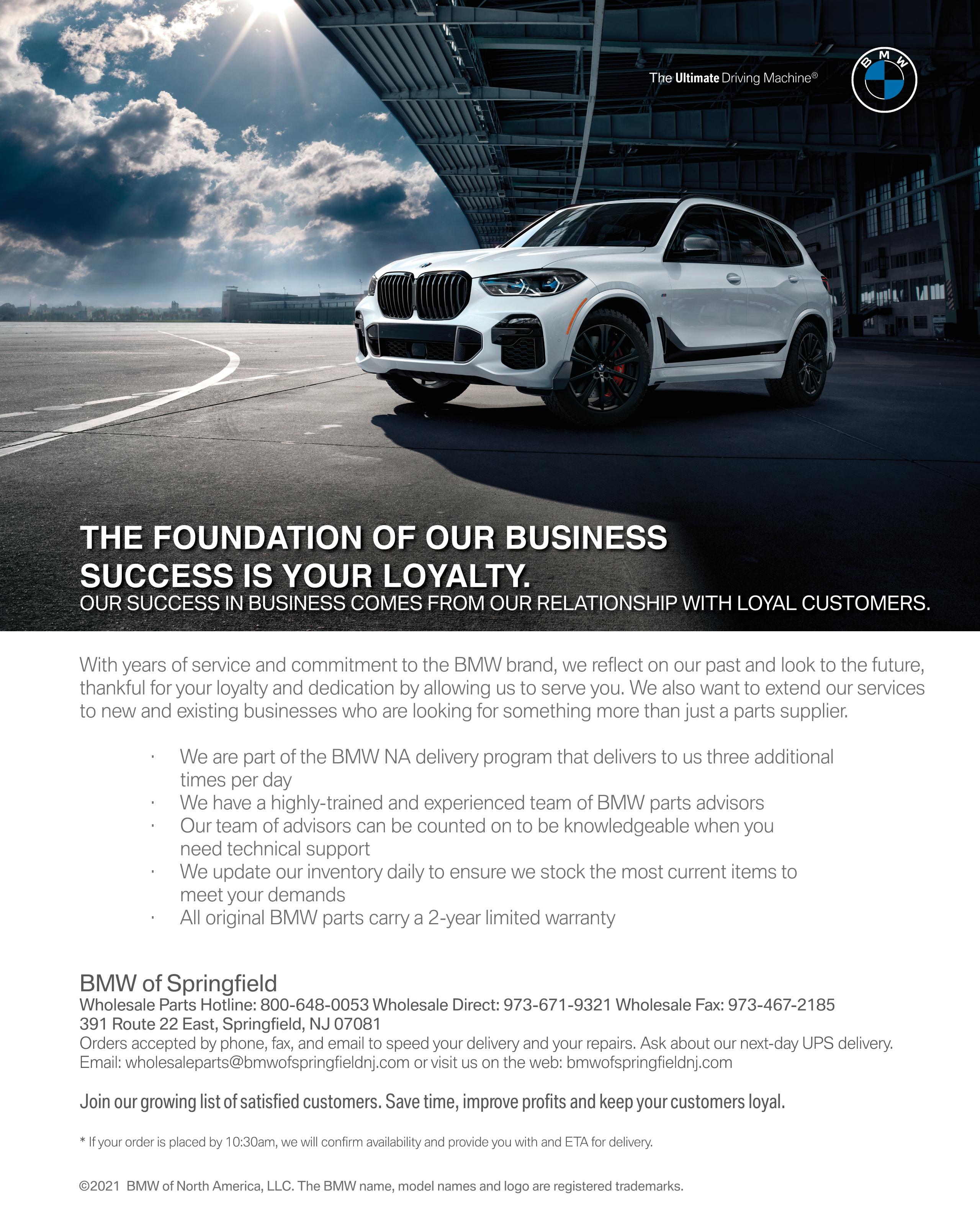
Election, Awards and Education: AASP/NJ Reconnects at Annual Meeting
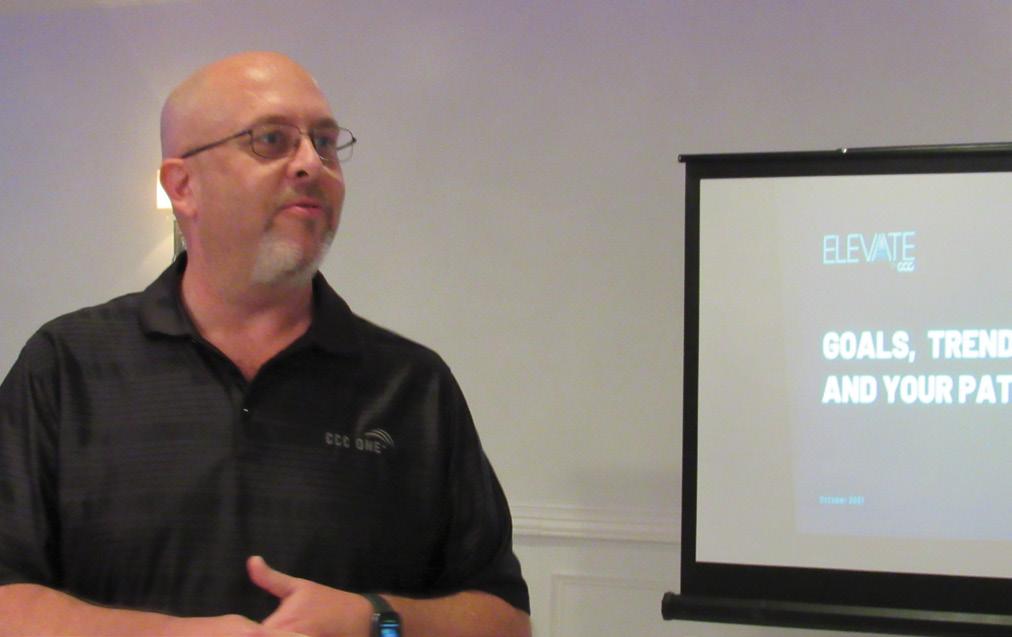
The Alliance of Automotive Service Providers of New Jersey (AASP/NJ) held its Annual Meeting on October 20 at Gran Centurions in Clark, NJ, featuring its Board of Directors election, a special awards ceremony where longtime members were honored and a vital education session delivered by Neal Bobzin and Craig Stevens of CCC.
Re-elected Executive Board members include Jerry McNee (Ultimate Collision; Edison) as president, Dennis Cataldo, Jr. (D&M Auto Body; Old Bridge) as collision chairman and Keith Krehel (Krehel Automotive Repair, Inc.; Clifton) as mechanical chairman, in addition to Treasurer Tom Elder (Compact Kars, Inc.; Clarksburg) and Secretary Tom Greco (Thomas Greco Publishing; Nutley). Board member Dave Laganella (Peters Body & Fender; Oakland) will return for another term, and the Board welcomed a new member: Ken Miller (821 Collision; North Haledon).
During the special awards ceremony, Tom Elder and Luci Robson presented the Russ Robson Scholarship Award to Gavin Danitz (Compact Kars; Clarksburg). “I’ve been around cars basically my entire life, and I’ve always had a passion for it,” Danitz said. “I love the working environment, I love working on cars, and I love solving problems. I want to continue to better myself, and I’m very honored to have the opportunity to win this award.”
The Stan Wilson/New Jersey Automotive Body Shop of the Year Award went to Dennis Cataldo, Jr. of D&M Auto Body in Old Bridge. “The only way we’re going to move forward [as an industry] is if we start working together,” Cataldo encouraged as he accepted his award. “A lot of people throw the word ‘competitor’ around, but I don’t think that we’re really competitors; we have no reason to be in competition with one another. When we’re all working toward moving in the same direction, I think we can really go somewhere.”
Alicia Figurelli, senior vice president of Thomas Greco Publishing, became the second woman to be inducted into the AASP/NJ Hall of Fame. “There is no person that I’ve interacted with in this association who has dedicated their life any more intently than Alicia,” AASP/NJ Immediate Past Neal Bobzin President Jeff McDowell (Leslie’s Auto Body; Fords) stated as he presented the award. “When I was president, she was my go-to person – she made all the
22 | New Jersey Automotive | December 2021 Craig Stevens
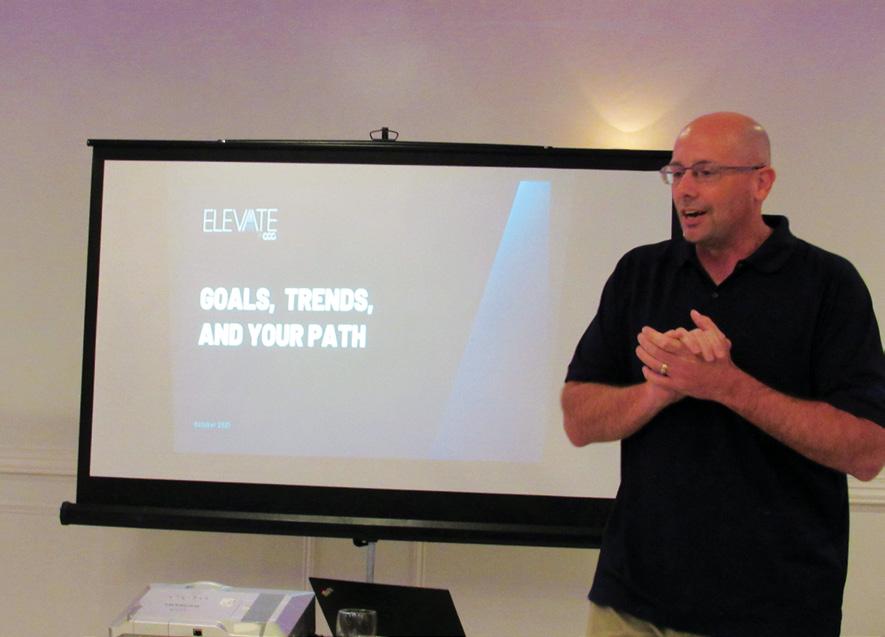
wheels turn. And she still does. Alicia is the energy behind the association.” “I’m humbled to be included in the company of such an elite group of professionals, many of whom I’m also proud to call my friends,” Figurelli said. “It’s an amazing honor.”
AASP/NJ Past President Eddie Day (Collision Restoration; Fairfield) presented the Lee Vetland Lifetime Achievement Award to Tom Elder. “This man has worked tirelessly for the association and has never missed a single meeting,” Day said about Elder. “He puts it all in every day. He’s led numerous committees, and he’s lifted the automotive industry up the best he could for the condition we’re in. He was a groundbreaking shop owner.” “I’m happy to be here serving the industry, and I would like to stay as long as I can do it,” Elder stated. “I’m thrilled and totally surprised to receive this award.” After the awards ceremony, Nicole Lewicki of the Amato Insurance Agency (a division of World Insurance) shared a brief update on the AASP/NJ Health Insurance plan. Keynote speakers Bobzin and Stevens then took the floor to discuss how ELEVATE by CCC helps shops set goals, monitor trends and make decisions to improve their businesses. “When I ask a new client, ‘What’s your goal?’, they don’t tell me ‘to survive,’” Bobzin said. “The goal isn’t to remain flat - they’re looking to grow, or they’re looking to become more attractive for sale. Those higher level goals need to be broken down into the details, and then your employees need to understand the relationship between these particular goals and their responsibilities within the department.”
In terms of industry trends, Bobzin honed in on decreasing sales opportunities, vendor delays, staff shortages, CSI decreases and ramping up for a return to normalcy. Exploring the most beneficial ways to market to modern customers, Stevens astutely asked, “You guys deserve the same attention that any other industry gets, so why shouldn’t you have the same tools that any other industry gets?”
When discussing vendor delays, Stevens suggested, “The more robust your network of suppliers, the better, and the
more you can expand it, the more visibility you’ll have into your market.”
Bobzin broached the importance of supporting local votech schools as he discussed the ongoing staff shortage, but he also pointed out the importance of developing internal talent: “Invest in your people!”
The most important factors in improving CSI include understanding your customer base and keeping them informed, according to Bobzin. “Simple changes can positively influence CSI,” he said encouragingly. “It’s important to find out what’s important to your customer,” Stevens added. “Ask your customer what they like best about their car, and then spend an extra minute making sure that works properly for them when they pick their car up.”
The topic of returning to normalcy included the need to dig deeper into cycle time analysis and finding the balance in triage. “It’s amazing what you all do every day,” Stevens said as the presentation came to an end. “I respect that, and I think that, as an industry, you deserve that respect. You’re putting people back in their cars and putting them on the road - that’s a pretty big deal. And we’d love to help you leverage the use of the tools in the products you’re already using.”
As the meeting concluded, McNee encouraged attendees to take a more active role in the association and in the industry: “The only way to effect change is to get involved. If we don’t put any effort in, if we don’t at least try, what do we expect? Our industry needs to participate - something has to change!”
NJA

MAINTAIN AN INFINITE INVENTORY OF ORIGINAL MINI PARTS.
At your local MINI dealer, we believe that using Original MINI collision replacement parts will speed your repairs and increase your profitability. Original MINI parts assure an absolute perfect fit and function.
For Original MINI parts, contact any of these authorized MINI dealers.
MINI of Mt. Laurel
1311 Rt. 73 Mt. Laurel, NJ 08054 856-778-3000 Fax: 856-813-4622 MINIOFMTLAUREL.COM FACEBOOK.COM/MINIOFMTLAUREL
MINI of Manhattan
793 11th Avenue at 55th Street New York, NY 10019 212-246-7375 Fax: 212-315-9560 MININYC.COM FACEBOOK.COM/MINIOFMANHATTAN
© 2020 MINI USA, a division of BMW of North America, LLC. The MINI name, model names and logo are registered trademarks.
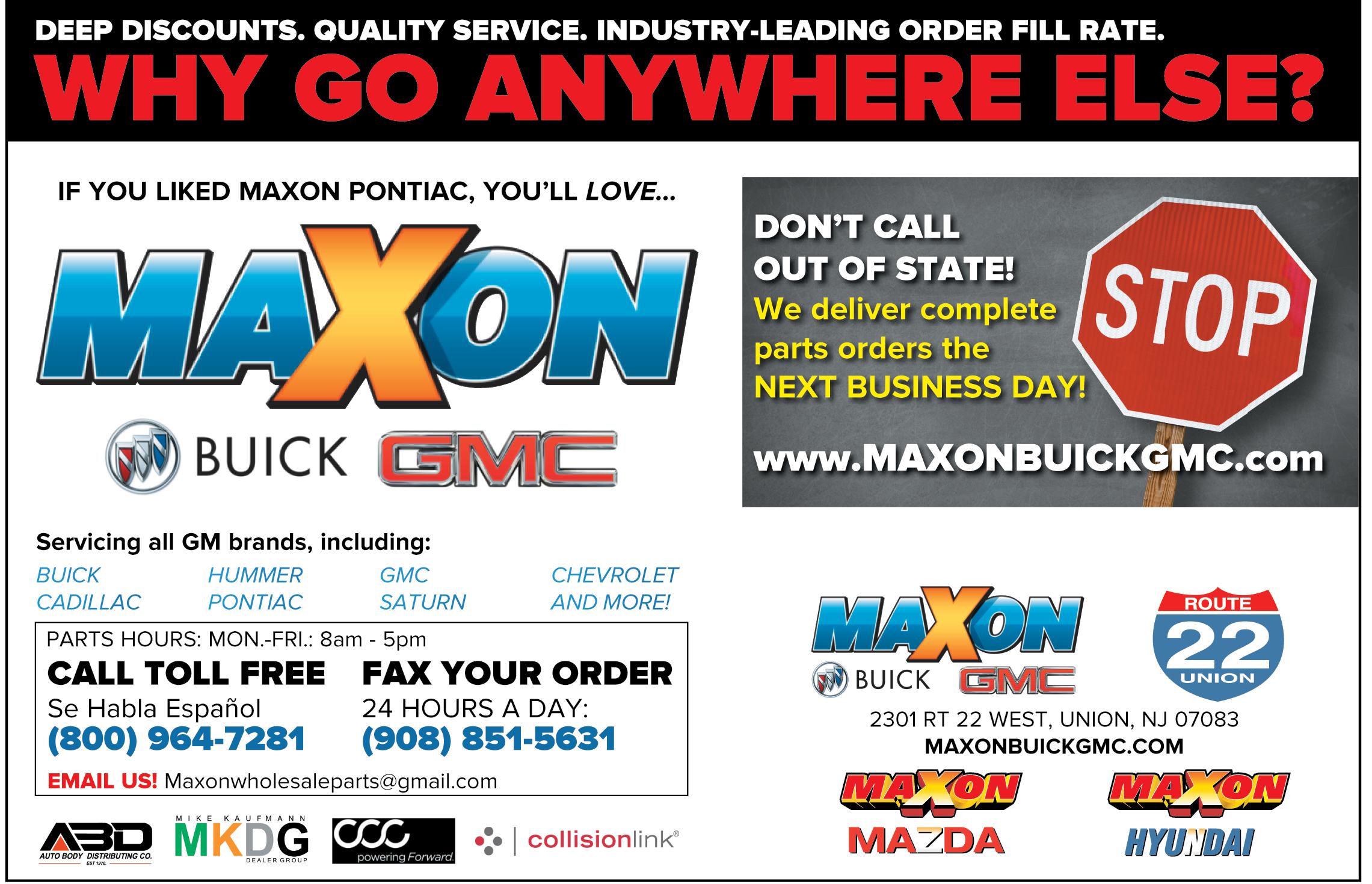
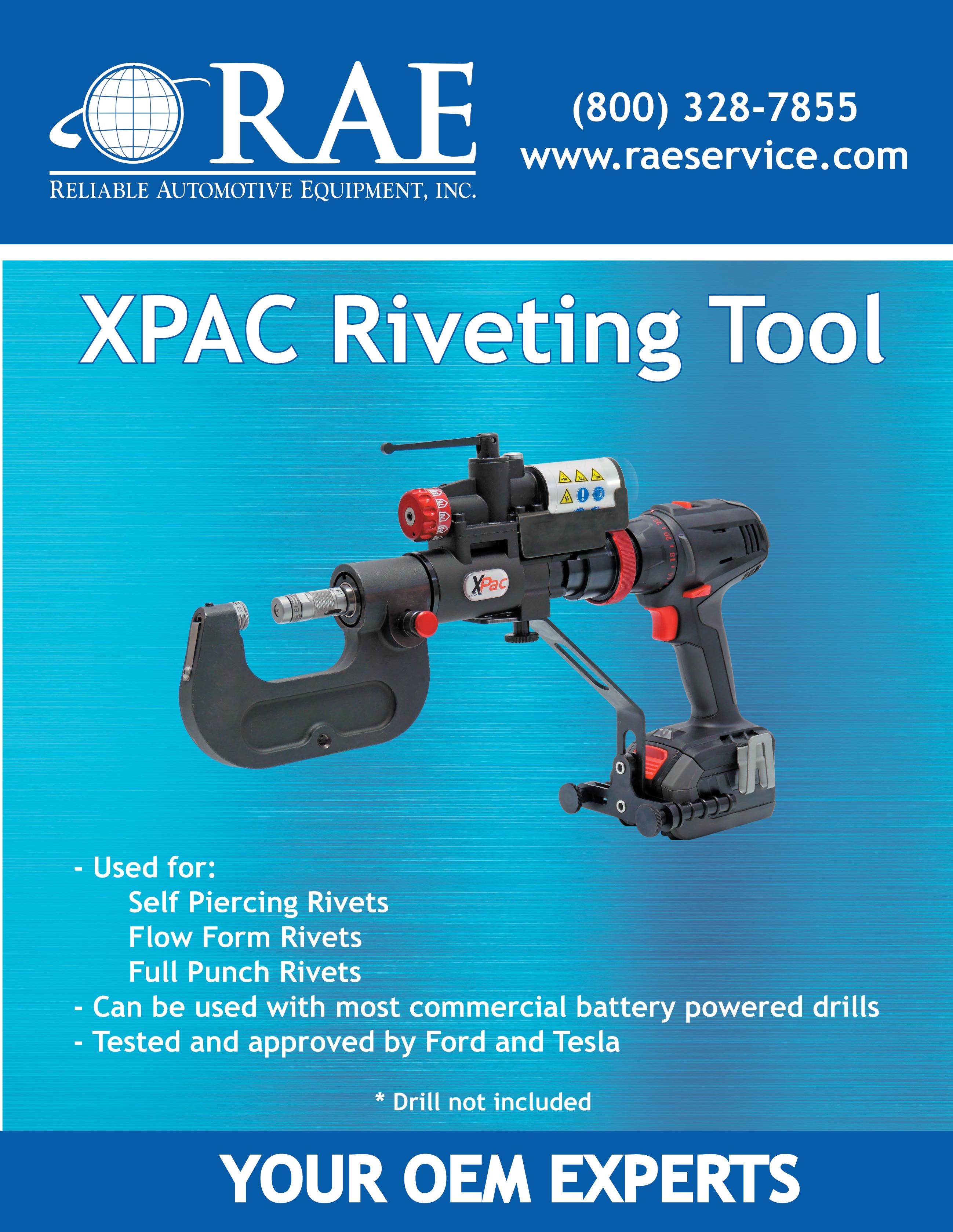
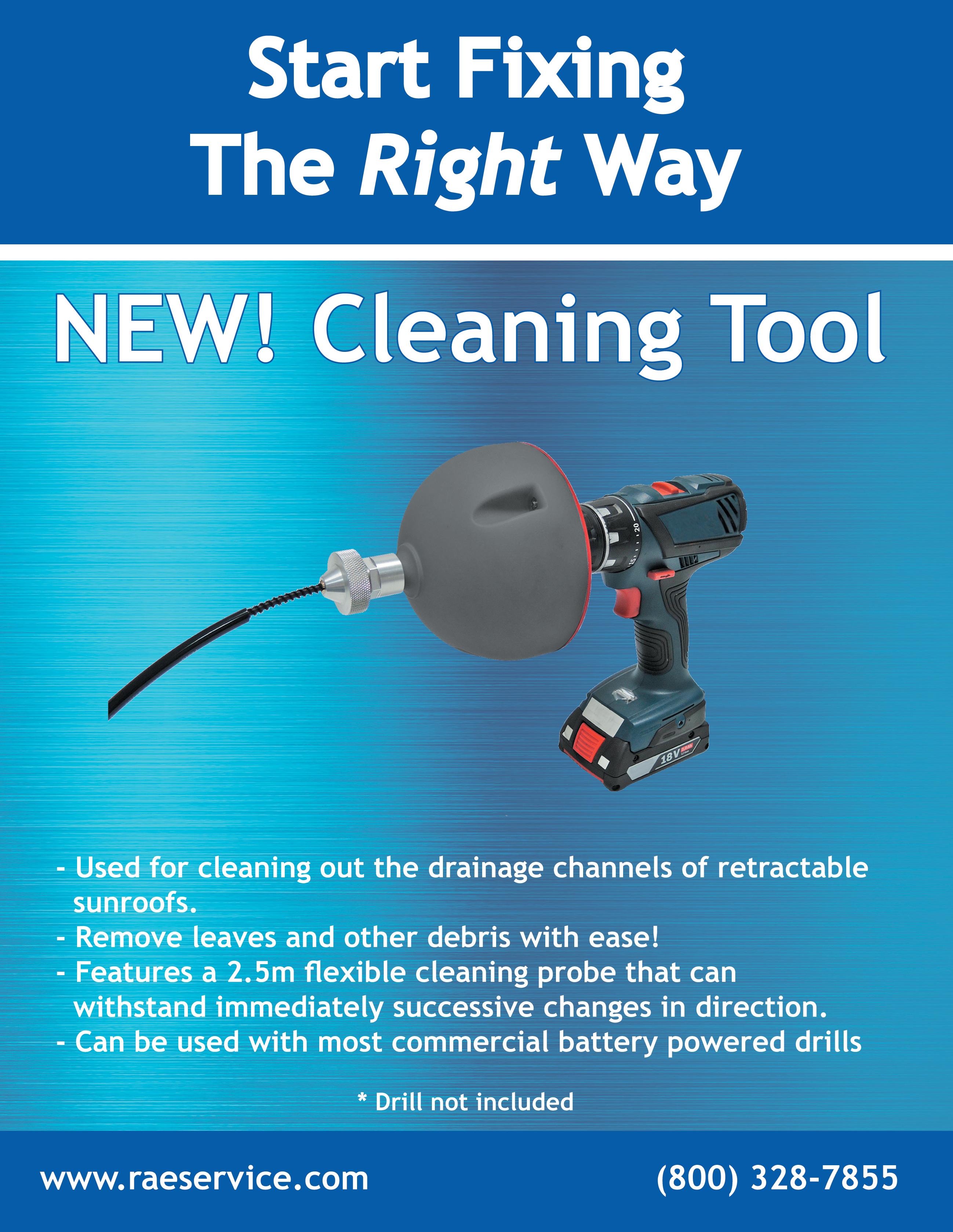
AASP/NJ Questions Insurer Delays, Objects to Photo Estimating at National Board Meeting
During the Alliance of Automotive Service Providers’ (AASP) National Board virtual meeting on November 8, state affiliate representatives were joined by other industry experts to discuss a multitude of issues impacting member shops and the automotive and collision repair industries as ? a whole. Affiliate leaders also provided updates on what’s happening in their specific market areas. AASP/NJ Executive Director Charles Bryant questioned whether other affiliates are experiencing the same inspection and supplement delays being seen in his area. “Everything is behind – often by weeks or even months! And everybody seems to be trying to go to photo estimates instead of personal inspections, which is an additional administrative burden on shops.” After confirming that other states are seeing similar trends, Bryant shared that, under New Jersey’s Unfair Claims Practices regulation, an insurance company choosing to inspect a vehicle must do so within seven working days, commence negotiations and make a good faith offer of settlement. Recently, the DOI agreed that if the insurer does not inspect the vehicle within that time frame, they waive their right to the inspection. “One of our members just took a stance on this. After 29 days waiting for a supplement inspection, the shop fixed the car based on the repair authorization signed by the vehicle owner and presented a bill, rather than an estimate,” Bryant explained. “Within an hour, the insurer sent a supplement, but the shop rejected it. The next day, they sent an appraiser to the shop to negotiate, but the shop owner informed him that he was too late. At the end of the day, the insurance company paid the shortage of $3,500. “We’re now in the process of creating a form to inform insurers that, if they don’t follow the regulations and inspect the vehicle within the time allotted, they will have waived their opportunity and right to challenge the repairs.”
AASP’s National Board also addressed additional business during the meeting, beginning with an update from Pat Kane of United Fire Group (UFG). Although 2020 and 2021 have not been profitable for the insurance industry due to high catastrophe losses and commercial auto claims, Kane assured Board members that “UFG’s commitment to AASP is unwavering. Insuring automotive repair businesses is one of our top priorities, and this is going to be a bigger focus for us moving forward.” Danny Gredinberg, administrator of the Database Enhancement Gateway (DEG), announced that the DEG has received nearly 18,000 inquiries. “That’s a huge number right there, and it’s a testament to why the DEG is so important to the industry. It demonstrates the kind of impact we can make when it comes to helping the industry.” “The OEMs have even recognized the DEG as a valuable resource and given us access to their information free of charge because they realize that validating the inquiry with the OEM repair information is the only way we’re going to achieve a positive outcome,” he continued. “At the end of the day, we all just want accurate databases - nothing more, nothing less.” AASP National Board President Tom Elder proposed that the organization provide a recommendation for Condition Now, a program that attempts to moderate the negative impact CARFAX reports have on customers’ vehicles. “If a CARFAX report is pulled after an accident, it does not take into consideration whether you wrote an estimate and repaired the vehicle, but now, there’s a way to abate that by inspecting the car and attaching your shop’s report to the CARFAX to show that the vehicle was repaired by a certified collision facility and is now in better condition than that negative CARFAX report indicates.” With a Condition Now report, Elder acknowledged, “The car will likely be valued at a number somewhere between the diminished and full values, but this is something we didn’t have before. Being able to show who repaired the vehicle and the quality of the workmanship demonstrates what transpired and can help our customers.” Lastly, Joe Amato, Jr. from the Amato Insurance Agency (a division of World Insurance) shared details on the possibility of expanding their New Jersey Health Insurance plan nationally to make it available to all AASP members. For more information on AASP National, visit autoserviceproviders.com. November edition of New Jersey Automotive available at grecopublishing.com. For more information on AASP National, visit autoserviceproviders.com.
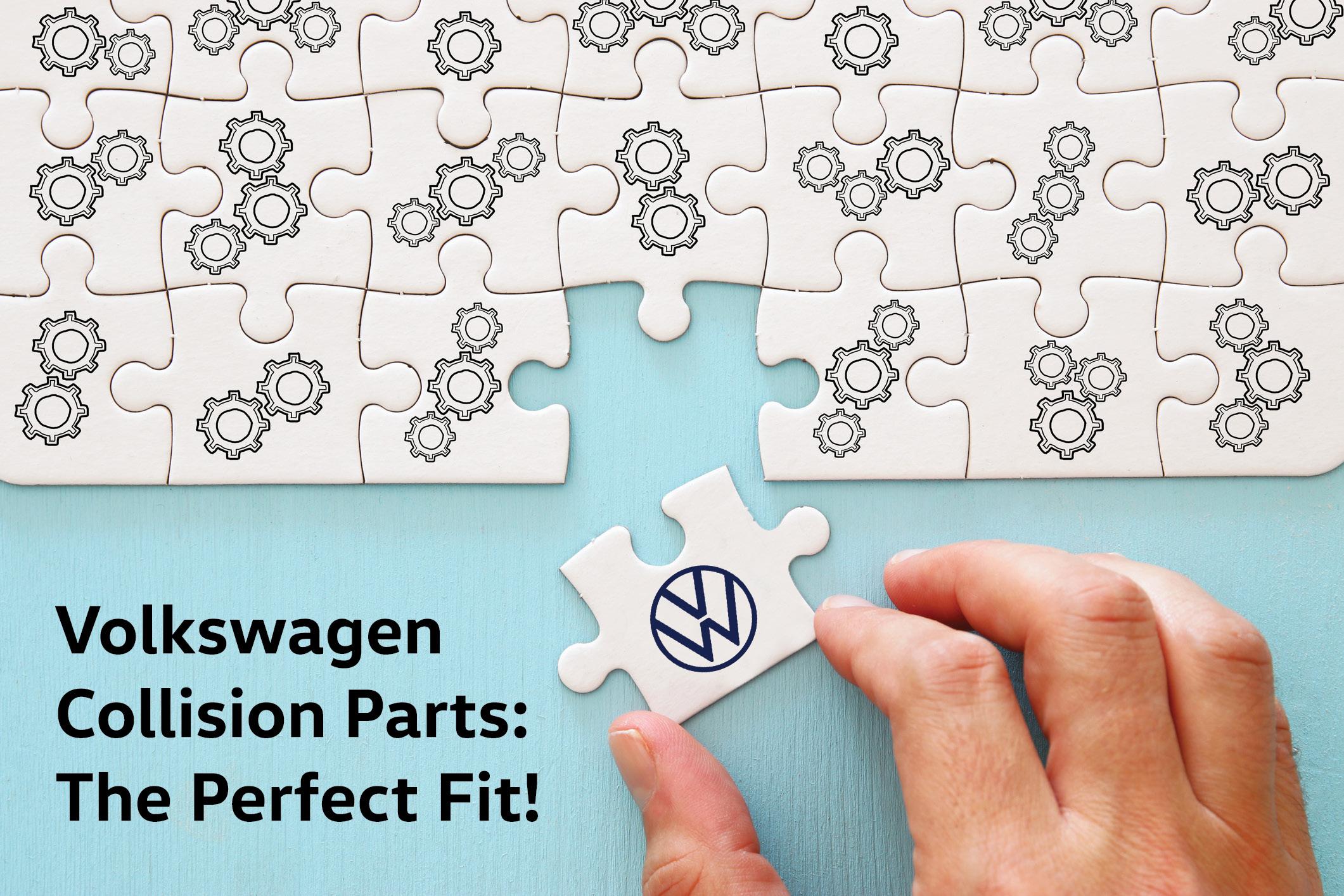
You’ve got the right tools, staff, technology and procedures to give your customers the best repair possible. The missing piece of the puzzle? Genuine Volkswagen Collision Parts. Contact an authorized dealer today and find your perfect fit.
Flemington Volkswagen
213 Route 202/31 Flemington, NJ 08822 TOLL FREE: 877-657-2787 FAX: 908-782-1795 email: rmuir@flemington.com www.NJPARTS.com
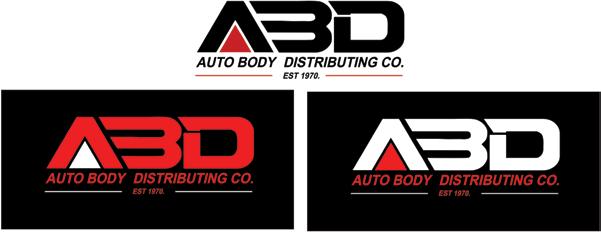
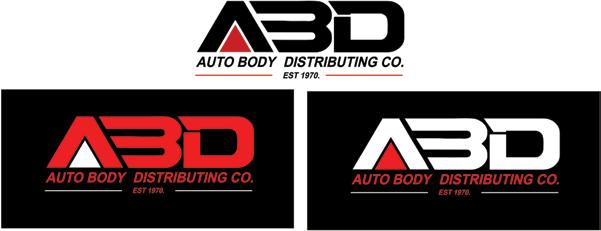
Paul Miller VW of Bernardsville
118 Morristown ROAd Bernardsville, NJ 07924 Toll Free: 877-318-6557 Local: 908-766-1600 Fax: 908-766-6171
Douglas Motors
491 MORRIS AVE. SUMMIT, NJ 07901 PHONE: 908-277-1100 FAX: 908-273-6196 TOLL FREE: 800-672-1172 www.douglasvw.com email: douglasparts@douglasautonet.com
Trend Motors
221 Route 46 West Rockaway, NJ 07866 888-267-2821 fax: 973-625-4985 www.trendmotors.com email: dreinacher@trendmotors.com
Crestmont Volkswagen
730 ROUTE 23 NORTH POMPTON PLAINS, NJ 07444 TOLL FREE: 800-839-6444 fax: 973-839-8146 www.crestmontvw.com email: vwparts@crestmont23.com
Wholesale Parts

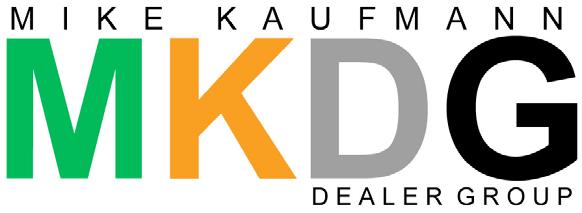

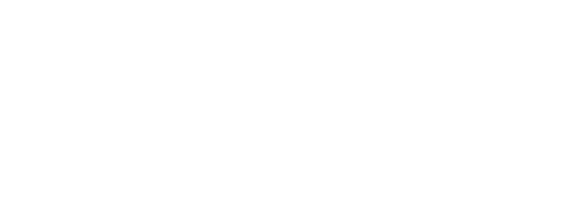
Where Are We Now?
New Jersey Automotive’s 2021 Survey Results
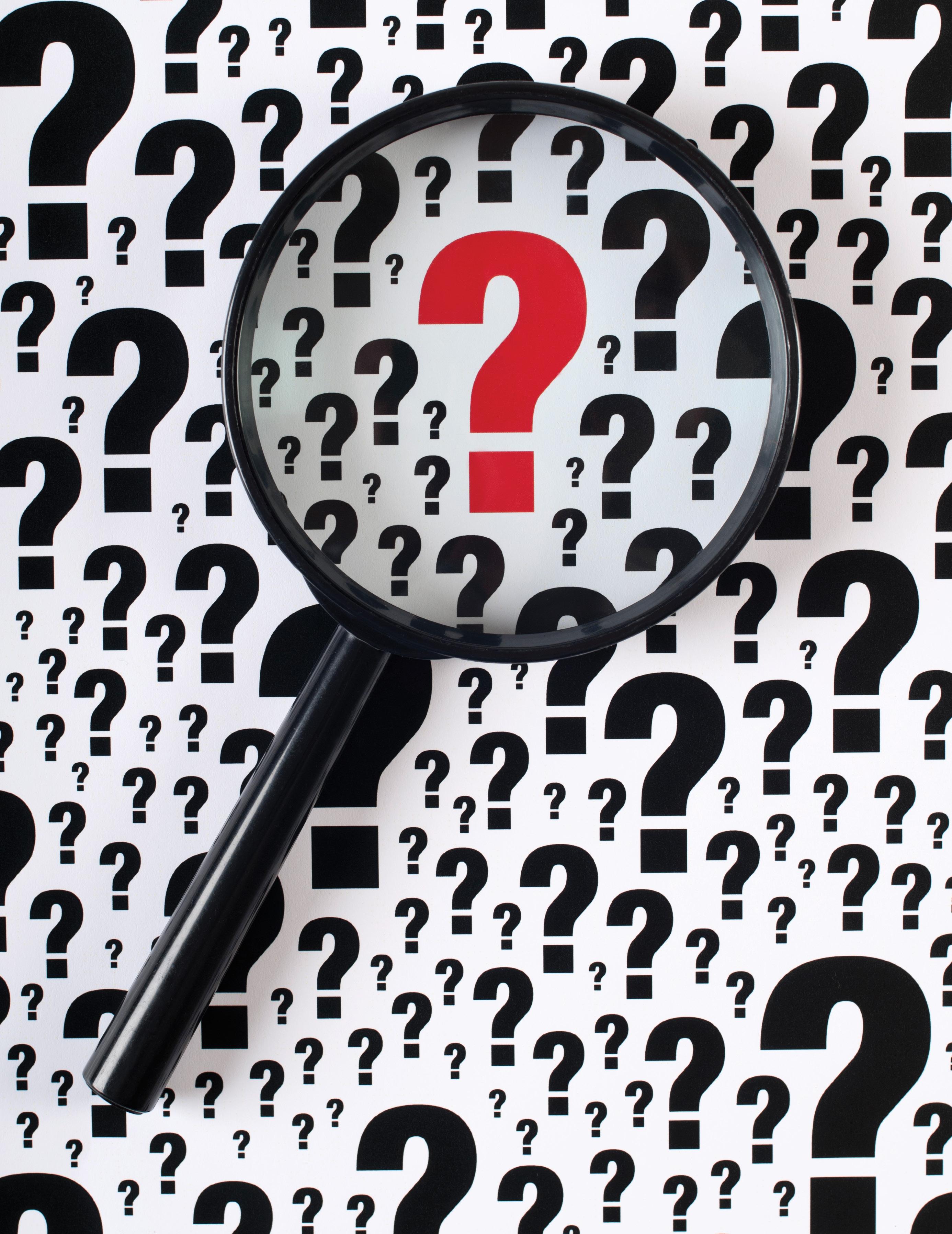
If you had asked many people what the next year and a half would look like back in March 2020, very few would have any idea what we would be facing today. While the collision and mechanical repair industry has never been an easy one, new challenges have certainly arisen affecting shop owners all around the Garden State. So how are your peers around New Jersey handling the current state of the world? Are they having as much trouble getting parts? How are they dealing with difficult insurers? What are their Labor Rates? All of this and more can be found in the following pages with the results of the New Jersey Automotive 2021 Industry Survey. We would like to thank all of the shops who participated in this survey and hope that you find the following information enlightening.
How long have you been in business?
1-5 years: 5% 6-10 years: 8%
More than 10 years: 87%
What best describes your primary business?
Collision Repair: 76%
Mechanical Repair: 5% Collision & Mechanical Repair: 19%
Where is your business located?
Northern Jersey: 56%
Central Jersey: 38% Southern Jersey: 6%
Collision Shops: Are you a DRP?
Yes: 64% No: 36%
If you selected “Yes” to being a DRP, how many programs are you on?
1-5: 70%
6-10: 30% More than 10: 0%
How many employees do you have, including yourself? How many employees have you hired in the last year?
None: 43%
1: 19% 2-4: 27% 5 or more: 11%
You see it all over the internet these days. Small businesses all around the country are putting up signs that say, “No one wants to work anymore.” Since the automotive repair industry has been feeling the pain of hiring new employees for quite some time now, it’s no wonder that many shops are feeling exactly the same way. Compared to the results we received from our survey in 2020, 30
percent more shops experienced a year with no new hires, and 22 percent fewer shops hired more than two employees this year. Even though our previous survey indicated that hiring numbers were on the rise, it seems the industry has now leveled out.
1-5: 41%
6-10: 30%
11-20: 16% More than 20: 13%
What is the age of your oldest employee?
30-40: 3% 41-50: 3%
Over 50: 94%
What is the age of your youngest employee?
18-25: 49% 26-35: 21% Over 35: 30%
Last year, our survey results indicated that for 18 percent of shops in New Jersey, their youngest employee was over the age of 35. That number has nearly doubled in 2021. It’s no secret that one of the major concerns in this industry is that many qualified technicians are aging out, while bringing in new blood proves to be a consistent struggle. In 2020, we found that for 82 percent of shops, their oldest employee was over 50 years old. Just one year later, the vast majority of survey respondents are now noting that this is the case.
Where do you look to hire new employees?
It’s the ever-persistent conflict of this industry – doing things the tried-andtrue, “old school” way versus relying on technology. Out of our survey respondents, there was an even split of 46 percent
each for those who use word of mouth to find new techs versus those who use
the Internet – whether it be Indeed, Facebook, Craigslist or Zip Recruiter. One Northern NJ shop, who hired more than five new employees this year, joked that he looks at “Indeed, Craigslist, emergency rooms, city morgue…anywhere bodies are available.” Although he was joking, this shop owner isn’t alone in his desperation to find new technicians to bring into their businesses. Eleven percent of respondents noted that they look for new technicians “everywhere.” Very few survey respondents indicated that they used the industryspecific resources available to them, such as the Labor Pool (five percent) or sourcing from Vocational or trade schools (eight percent).
How has your ability to attract and retain employees changed over the past year?
The world is in a crazy state right now, and it has impacted everything around us. Although 29 percent of survey respondents have had no difficulty either hiring or retaining employees, the majority of our
readers are scrambling to find ways to keep their technicians onboard and bring
in new hires. Nearly 30 percent of shop owners who participated in our survey either had to increase their pay rates or offer more benefits to employees just to stay afloat.
“Maintaining benefits has cost more, but providing them is more important,” one shop owner from North Jersey explained. “We increased our starting offer and now pay 100 percent health insurance.”
However, for many of our readers, even paying more out of pocket hasn’t been enough to bring new bodies into their shops for employment.
“Today’s youths do not have interest in working in a hands-on job,” noted a Central Jersey shop owner. “The current labor pool is very limited, and the quality is very low.”
“They’re making more money not working right now,” agreed a South Jersey survey respondent. “There aren’t any new technicians to attract.”
Less than $25,000: 6% $25,000-$45,000: 39% $35,001-$45,000: 31% $45,001-$55,000: 15% $55,001-$65,000: 9%
Less than $50,000: 5%
$50,001-$70,000: 36%
$70,001-$80,000: 5% $80,001-$100,000: 24% More than $100,000: 30%
What do you think is the most pressing issue facing shops today?
Working in the automotive repair industry is not for the faint of heart. As any shop owner knows, there are a slew of everyday battles and complexities you need to navigate in order to be successful, from steering to subpar Labor Rates to ever-evolving repairs, and so much more. While many of these struggles have been persistent fixtures of the industry for longer than most of us remember, a new issue is starting to affect Garden State shop owners more and more each day – parts delays. Although this question received many of the usual responses, with 73 percent of survey respondents
indicating that their most pressing issue was dealing with insurers not paying
properly for repairs and 64 percent explaining that hiring new technicians was their biggest blight, a whopping 18 percent of shop owners now state that the delays they’re experiencing on receiving parts is what’s affecting them most.
“We have these operational bottlenecks going on that we’ve never experienced before,” explained a North Jersey shop owner. “In addition to it taking forever to receive parts these days, we’re also getting hit with delays from the insurance company’s lack of organization and handling claims in a timely manner.”
“We’ve got a lot going on right now,” a neighboring North Jersey shop commiserated. “Between dicey availability on parts and rates from insurance companies not going up to match with inflation, we’re having trouble staying afloat.”
For another shop from Central Jersey, technology and keeping up with the cost of complex repairs is what’s affecting him the most.
“There are currently extremely complex vehicles requiring special training, tools and facilities to perform proper/safe repairs,” he shared. “And then on top of it all, there’s increasing pressure from insurers to reduce costs. I don’t understand how you’re supposed to run a business like that.”
Are you currently certified/ recognized by an OEM to perform collision repairs?
Yes: 27%
No, but I’m working towards it: 32%
No, and I do not plan to become certified/recognized: 41%
Since 2020, there has been a 46 percent increase in those not planning on becoming certified at all. We also saw a 27 percent decrease on those currently working towards certification, with no significant change on how many shops are actively certified, demonstrating that some New Jersey shop owners have changed their minds about the value of becoming an OEM certified shop.
If you answered that you ARE certified / recognized by one or more OEMs, please list them below.
Over 20 different manufacturers were mentioned by repairers who took our survey. The top certification programs that
Most pressing issue is dealing with insurers not paying properly for repairs.
Last year, New Jersey shop owners rated their current state of business at an average of 6.5. Luckily, that number has only decreased slightly over the past 365 days. On average, our survey respondents indicated that they would rate their current state of business at a 6.1, with 50
percent rating their state of business at a
seven or higher.
In the past year, did your sales increase, decrease or stay the same?
Increase: 59%
Decrease: 27% Stayed the same: 14%
As COVID restrictions eased up and remote workers started to move back into offices, more people returned to the road. While last year, 77 percent of survey respondents noted that their sales had decreased, it seems shops are starting to receive more business, with 73 percent of shops seeing their sales stay the same – or even increase.
readers are participating in were Nissan/
Infiniti, Hyundai/Kia, Subaru and
Honda/Acura. One survey respondent even had 19 different certifications!
How do you feel OEM certification programs will impact your business?
My business will be affected in a POSITIVE way: 50%
My business will be affected in a NEGATIVE way: 9% My business will not be affected: 41%
Although our survey is currently showing a decrease in shops seeking out certification, those involved with various certification programs across the state are preaching the importance of participation.
“We leverage our OEM certifications as a means to add credibility to our business and establish us as experts in the eyes of our customers,” explained one survey respondent from North Jersey.
“Certifications will become the future of our industry,” another shop from Central Jersey agreed. “It may not affect you right away, but in the years to come, they’re going to be important.”
How has steering affected your business?
If you’ve been a part of this industry for any length of time, you are no stranger to the stress that steering can put on a business. Although 27 percent of survey takers believed that steering isn’t a problem currently affecting them, the majority of
shop owners across the state feel the pain
of this issue on a daily basis.
“I don’t even know the number of potential customers that have been steered away from my shop,” a Central Jersey repairer noted. “When we do actually get a car in the door, it’s preventing us from charging properly for the work we do. Most DRPs are basically giving the work away, and the MSOs can afford to take it at a lower level.”
“So far, it looks like the steering of the future seems to be unnecessary delays on the carrier’s end, and then to point blame at the shop,” one shop owner from North
FIT AND FINISH IS NO PLACE TO GET CREATIVE.
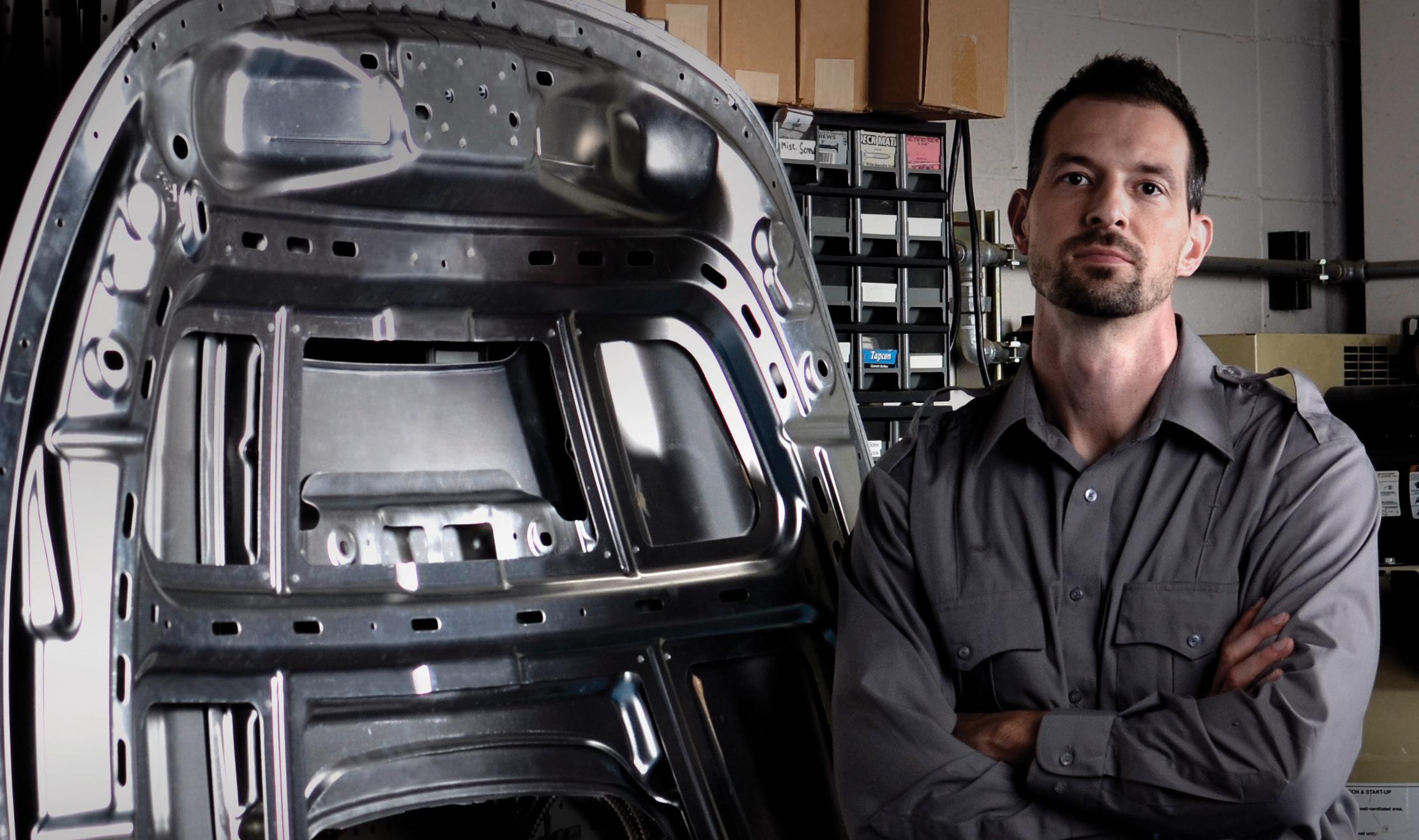
CONTACT US TODAY FOR A COMPETITIVE QUOTE ON YOUR NEXT COLLISION REPAIR ESTIMATE.
CENTRAL AVENUE CHRYSLER JEEP
1839 Central Park Avenue Yonkers, NY 10710
Order Hot Line: (800) 967-5298
Fax: (914) 361-1508 www.centralave.com
COLLISION LINK, REPAIR LINK AND PARTS TRADER
DOVER DODGE
158 S. Salem St. Dover, NJ 07801
Order Hot Line: (888) 676-6727
Fax: (973) 366-0757
EASTCHESTER CHRYSLER JEEP DODGE
4007 Boston Road Bronx, NY 10466
Order Hot Line: (914) 597-7018
Fax: (718) 881-3014
WE COMPETE WITH AFTERMARKET PRICES! FREE DELIVERY!
FRANKLIN SUSSEX AUTO MALL
315 Route 23 Sussex, NJ 07461
Order Hot Line: (888) 528-2200
NIELSEN DODGE CHRYSLER JEEP RAM
175 Route 10 East Hanover, NJ 07936
Order Hot Line: (877) 890-9545
Check out MoparRepairConnection.com for resources, promotions and technical information.
Big. Gray. Available Today.
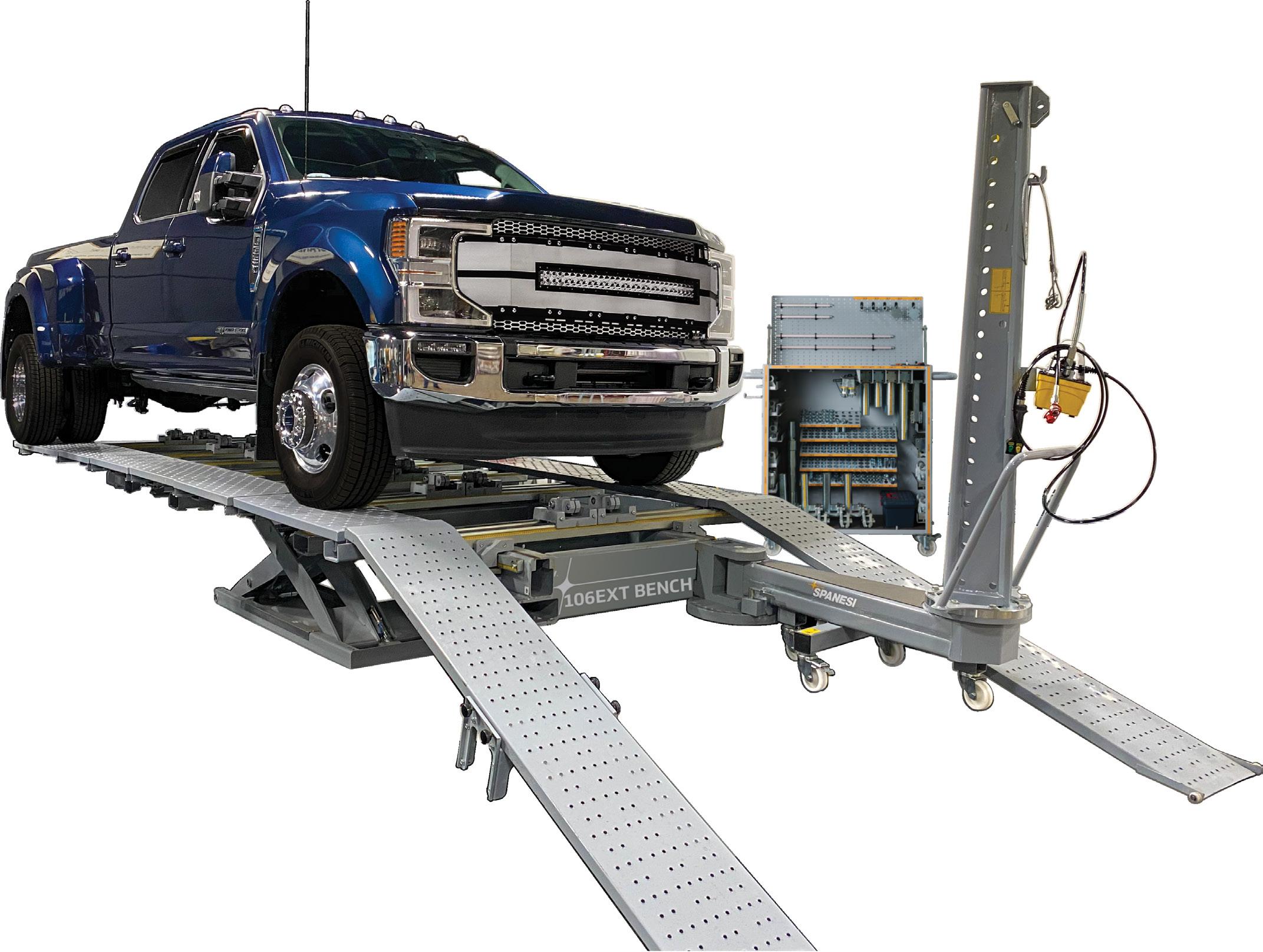
The Spanesi® 106 EXT Structural
Straightening Bench is designed for larger and longer vehicles. The 106 EXT easily accommodates large work vans, light and medium duty trucks, and full-size SUVs.
The 106 EXT is included in OEM certification programs around the globe. Contact Spanesi Americas for a current and complete list of programs.
Spanesi Americas, Inc.
123 Ambassador Dr. STE 107 Naperville, IL 60540
106 EXT
Structural Straightening Bench
106 EXT Structural Workstation Includes:
7 Crossbars 14 Mounting Locations Bench With Rack Gears Lift With Control Box Loading Trolley Positioning And Ascending Ramps Pulling Column Universal Jig System Loading Capacity 5,000kg (11,000lbs) Length 6m (19.7’) Width (Up To) 2.1m (7’) Pulling Force 10 Tons
224-SPANESI (224-772-6374)
www.spanesi-americas.com
facebook.com/spanesiamericas
Jersey shared. “I haven’t been able to get in touch with [one insurance company] for more than two weeks for a simple supplement, yet [the insurer] is telling the customer that we ‘just need to follow the instructions on the estimate,’ which has me calling CCC customer service for the instructions process…and on and on and on it goes. We’ve seen about a 20 percent decrease in sales.”
Although steering has been mostly negative for New Jersey repairers, for some shops who decide to “play the game,” steering has actually worked to their benefit.
“Steering doesn’t really affect us since we’re a DRP for six of the top eight insurers in the state,” one survey respondent bragged. “It certainly helps us with business to be a direct repair shop.”
Do you feel the increase in photo estimating since the COVID-19 pandemic has HELPED the repair process?
Yes: 27% No: 73%
When our survey last ran at the beginning of the pandemic, 67 percent of respondents indicated that the increase of photo estimating had helped their repair process. It seems that many of these shop owners have now changed their tune.
“Virtual estimating is a doubleedged sword,” explained a North Jersey shop owner. “It can help cycle time, but it eliminates accountability from the carrier. Now, if you send pictures, you’re forfeiting an in-person negotiation and leaving a file that will require much more back-andforth.”
“Right now, we’re stuck between a rock and hard place in terms of proper repairs and our cycle time,” shared a survey taker from Central Jersey. “You can either use photo estimating and get a cruddy estimate, or you can wait two to five weeks for an in-person inspection. I think insurance companies are using it as a crutch to take longer to settle claims.”
“We’re doing the insurance company’s work for free,” another shop from South Jersey agreed. “With photo estimating, you get piss-poor estimates written, followed up with piss-poor supplements that are grossly underwritten. It’s an easy out for them to disconnect from face-to-face interaction.”
When a repair requires calibrations, what is the average number of calibrations you perform per vehicle?
Most survey respondents indicated that they run a minimum of two calibrations per vehicle. One Northern NJ shop noted that they run calibrations on about one-third of vehicles, while 14 percent of survey respondents stated that they run 100 percent of the calibrations, or as many as the OEM requires.
Do you experience difficulty in getting properly compensated for calibrations and scans?
Yes: 73% No: 27%
Where do you typically go for information on ADAS repairs and procedures?
OEM: 45% AllData: 32% Sublet: 18% Other: 5%
In your experience, which insurer do you find the most difficult to deal with, and why?
For the fifth year in a row of our NJA survey, Garden State shop owners
overwhelmingly agreed on the top three
worst insurers to deal with: State Farm, Allstate and Progressive.
“State Farm doesn’t negotiate,” pointed out one South Jersey repairer. “They don’t reimburse customers for safety inspections, and they don’t care. They act like they are above the law; there’s no accountability in their policy. They just suck!”
“Allstate and State Farm refuse to pay – no negotiation. Just a take-it-or-leave-it approach,” agreed another shop owner from North Jersey. “They just tell you to collect from the owner.”
“In my opinion, there are four insurers that receive a failing grade – Allstate, State Farm, Progressive and Geico; however, State Farm is the worst at this point,” a North Jersey repairer shared. “Between their failure to recognize and reimburse for required procedures to their complete disregard of their contractual obligations to their lack of caring and empathy for their insureds, they are by far the worst.”
What is your current Labor Rate?
$50-$60: 68%
$61-70: 23% $71-$80: 5% More than $80: 4%
What do you think your Labor Rate should be?
Less than $60: 4%
$60-$80: 43%
$81-$100: 28% More than $100: 25%
How do you promote your business to current and potential customers?
Word of mouth: 55%
Social media/website/ Google/Yelp: 50% Local advertising/Cable/Radio: 27% None: 10%
How do you feel social media and digital platforms like Yelp have impacted your business?
When you used to hear about stars, the first thought that would come to your mind would probably either be Hollywood or the night sky. These days, everything has a star attached to it, rating businesses on a scale of one to five, and these once-celestial bodies now dictate much of our customers’ lives. From choosing a restaurant to rating your Uber driver, everything is determined by those little stars – and automotive repair shops are no different. So, how have online reviews affected New Jersey repairers?
“It has greatly impacted us in both good and bad ways, but it’s not going away anytime soon,” indicated a shop owner from North Jersey. “That’s why we’re always trying to impress and deliver the best customer service at all times.”
While delivering on customer service expectations is something all shop owners should strive for, regardless of reviews, many Garden State repairers know that, in this day and age, even that isn’t always enough to get a stellar rating.
“Anyone can leave a negative review, even if they’re not a customer of your shop,” explained a Central Jersey shop owner. “When that happens, we have zero recourse to correct.”
“Yelp is a scam filled with selfgenerated fake ‘leads,’” a south Jersey repairer shared. “It’s designed to make you spend more money on advertising. It’s too expensive for the rate of return.”
Approximately how much do you spend on parts annually?
$1-$100,000 per year: 9%
$101,000-$500,000 per year: 59%
$500,001-$1 million per year: 18% Over $1 million per year: 14%
What is the most important factor in determining who you purchase parts and supplies from?
Service: 64%
Price/Discounts: 54% Inventory: 18% Other: 23%
Where do you look first when purchasing parts and services for your shop?
New Jersey Automotive: 28%
Word of Mouth: 38%
Online: 14% Other: 23% Certification programs ABD Dealer reps
How has the COVID-19 pandemic affected your relationship with insurers?
It has been nearly two years since the start of the COVID-19 pandemic, and yet the stress and intricacies of navigating owning a business during this time have not subsided. One unexpected side effect of this pandemic was the way it impacted the already-tense relationship many shops have with insurers. Even though 41 percent of survey respondents saw no change in the way they work with insurers, more than half of our readers are experiencing new frustrations in these previously difficult dynamics.
“It seems to have strained any relationships we previously had,” said one North Jersey survey taker. “It feels like the insurers sat around figuring out how to deny components of claims for two years and are now beta testing all of these techniques.”
In addition to denying integral parts of the repair process, many shop owners are noticing how the pandemic has caused insurers to affect their cycle time.
“Insurers are using it as a crutch to slow down the repair process,” explained a Central Jersey shop owner. “It has delayed every aspect of my business. If you’re a DRP shop, you’re fine. But non-DRPs take three to four weeks to process an estimate and then another three to four more to process a supplement.”
Has COVID contributed to supply chain delays at your business?
Unsurprisingly, 100 percent of our survey respondents noted that supply chain delays affect their businesses, with one South Jersey shop owner explaining that Honda parts took over two months to come in, and another shop from North Jersey noted that they’re seeing 25 percent of their parts are on backorder.
Have you found difficulty in refilling positions due to the COVID-19 pandemic?
Yes: 65% No: 35%
The COVID-19 pandemic changed almost everything about how we see the world and how we conduct our businesses. While hiring new technicians in the automotive repair industry hasn’t been a walk in the park for quite some time, it has clearly hit new lows in the past year and a half, with 65 percent of survey respondents specifying that it has impacted their ability to fill positions at their local shops.
“We just can’t find help,” one shop owner from Central Jersey lamented. “Fifty percent of the interviews we hire don’t even show for the job. Some have come, worked for the day and then never came back. No one wants to work.”
“I wouldn’t blame our difficulty in hiring on the pandemic, to be honest,” one North Jersey shop owner shared. “There was a time I would say the extra government payouts made it hard to hire, but truthfully, it hasn’t been easy for as long as I can remember.”
While a significant number of shops had to replace techs this year, some got lucky in avoiding the hiring fiasco simply by keeping their employee numbers flat.
“We kept full staff on during the pandemic,” explained a fortunate shop owner from the Central Jersey area. “We didn’t need to refill any positions.”
What aspect of the COVID-19 pandemic has impacted your business the most?
Shut downs, stay at home orders, vaccine mandates, everything about life as we know it has shifted since March 2020, and repair shops around the state have felt the impact of this pandemic tenfold.
“No one is driving anywhere,” says one shop owner from North Jersey. “My sales are currently down 30 percent. I’m hoping they pick up as things open back up again and people start going back to the office. The loss of income and business on top of the fact that parts are harder to get has made things really difficult.”
“Everything is delayed,” shared a South Jersey repairer. “Insurer delays, parts delays: They’re all making the length of repair time impossibly long.”
Thirty-two percent of survey respondents mentioned parts delays as one of their biggest impact areas, while 27 percent noted that the effects of the labor shortages were what they’re feeling the most.
“There’s a lack of help because the government is paying people to stay home,” explained a Central Jersey shop owner. “They’re getting free handouts; I can’t hold it against them.”
One thing is certain: shop owners around the state are waiting with bated breath for this pandemic to subside so that business as usual can resume.
Have you and/or your employees undergone any training in the past year?
Yes: 68% No: 32%
Do you feel that MSOs (Caliber, ABRA, Crash Champions, etc.) are:
A threat: 41%
Irrelevant: 45%
An opportunity: 14%
With technology changing more rapidly than ever before, where do you see this industry 10 years from now?
Everything around us is rapidly going digital, from virtual reality to augmented reality and so much more. The world we see today has changed drastically from the one we were in even five years ago. The advent of this kind of technology has impacted New Jersey repairers as well, and although no one can see into the future, our survey respondents had some insights into what they think the industry will look like in the next decade.
“The cost to keep up is going to cause some shops to go under or be left behind,” one South Jersey shop owner predicted. “Only the strong and educated shops will survive the next 10 years. There’s
definitely going to be a significant
reduction in the total number of shops.”
“We’re going to need to be certified to work on vehicles in the future,” a North Jersey repairer explained. “I just don’t know how we’re going to be able to do it at these rates we’re forced to charge. Our rates need to be drastically raised.”
“I think we’re going to have more tech to deal with and less to physically repair,” opined a Central Jersey survey respondent. “It’s going to be more plug-and-play and less skilled or hands-on, with more computer-skilled laborers.”
Closing
Although this is a scary time for the world and for our industry at large, we hope it was helpful to read that you are not alone. Hopefully, the information provided assists you in finding new strategies to navigate the issues you’re facing and make more informed decisions for your business. While this can be an isolating time, let this article serve as a reminder that we as an industry are all in this together.
NJA
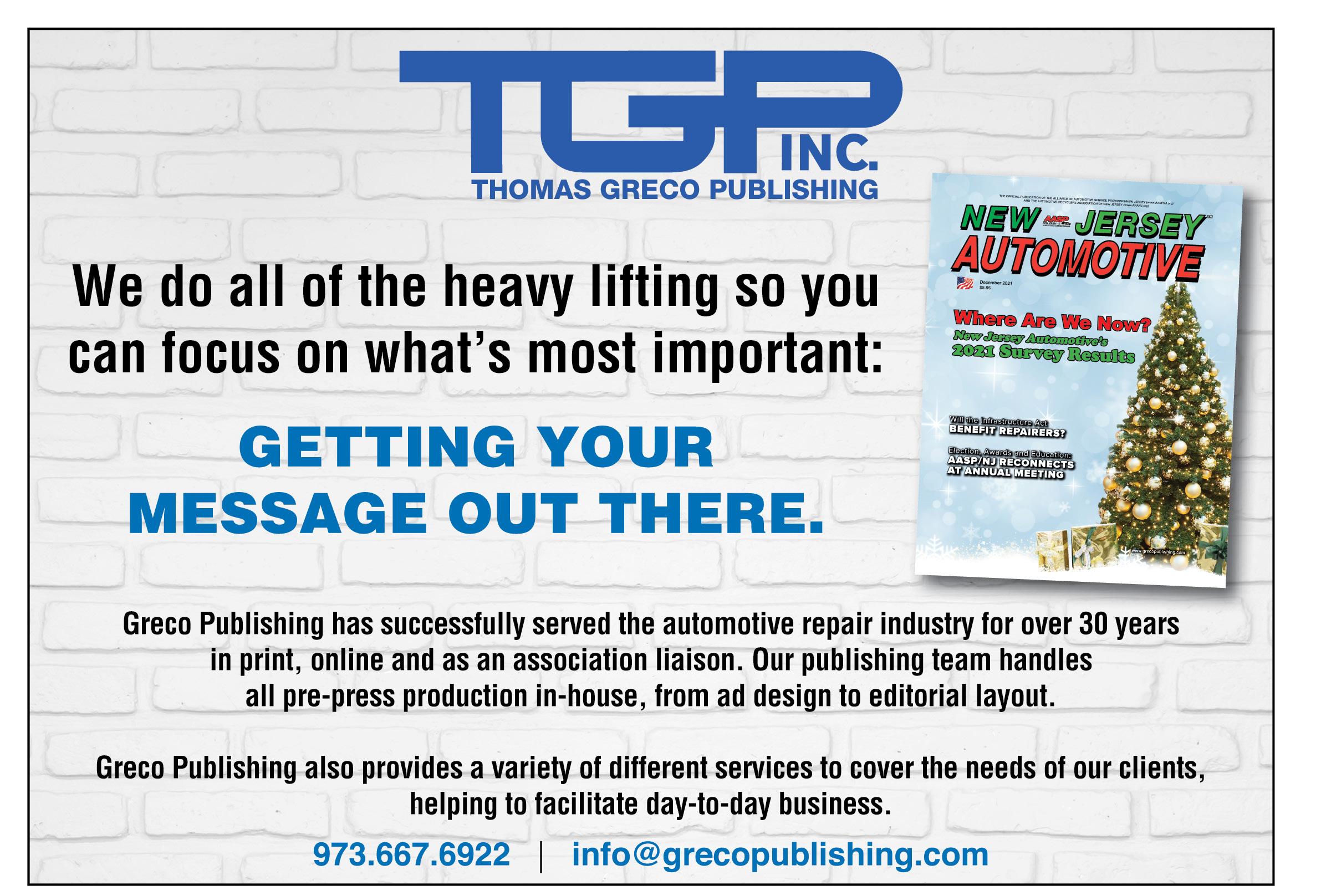
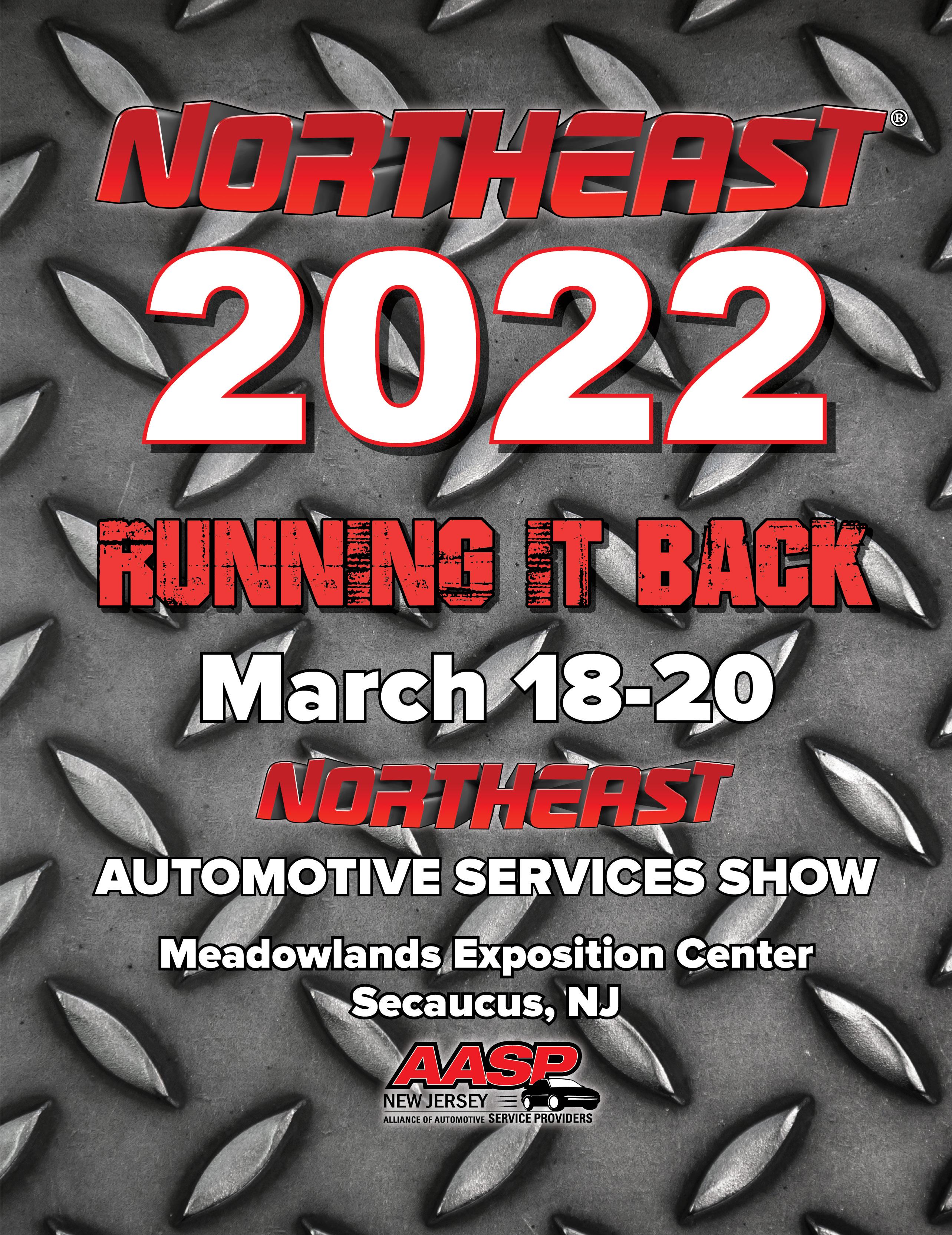
continued from pg. 10
was having déjà vu. My dad and older brother used to do the same exact thing to me when I was a little kid. But I wasn’t that bad, as a little kid. In fact, until my sister Diane got her driver’s license, I actually ate what my mom put on the table. And that included some Italian food.
Monday night was pasta night in the Greco household. My mom would make spaghetti and meatballs and her homemade sauce (gravy?). And she would “make” my favorite: frozen Celentano raviolis. Everyone else would eat the spaghetti. Me? I gobbled up those 12 round mounds of dough and ricotta cheese with just a dot of sauce (gravy?). Of course, it was the sauce that made it. My mom was a great cook. I loved her sauce.
I hadn’t had ravioli since my mom passed away in 1988. My sister Gloria attempted to get me to try hers one time, but the sauce (gravy?) wasn’t the same, despite her ranting.
So, there I was, trapped at an Italian restaurant. I NJA0420_CSNE.qxp_Layout 1 3/30/20 10:50 AM Page 1certainly didn’t want to insult these guys – especially since they were packing heat. But I was starving, and the bread “ Eventually I actually hit the target instead of wasn’t gonna do it. My only option on the menu was ravioli. the wall behind it. ” When it arrived piping hot a few minutes later, I took my first bite...Holy shit! It was amazing! It tasted EXACTLY like my mom’s sauce (gravy?)! Eddie almost fell off his chair, while Bobby and Kenny took their fingers off their triggers. I finished the whole meal in about three minutes and ordered a second plate. A few weeks later, I was a registered handgun owner and a weekly customer at Stephanie’s. Maybe during the next crisis, I’ll start eating London Broil again. Merry Christmas everyone! NJA
LYNNES
AUTO GROUP WHOLESALE DEPARTMENT
Genuine Service & Parts
SERVICE, SELECTION AND VALUE SINCE 1953
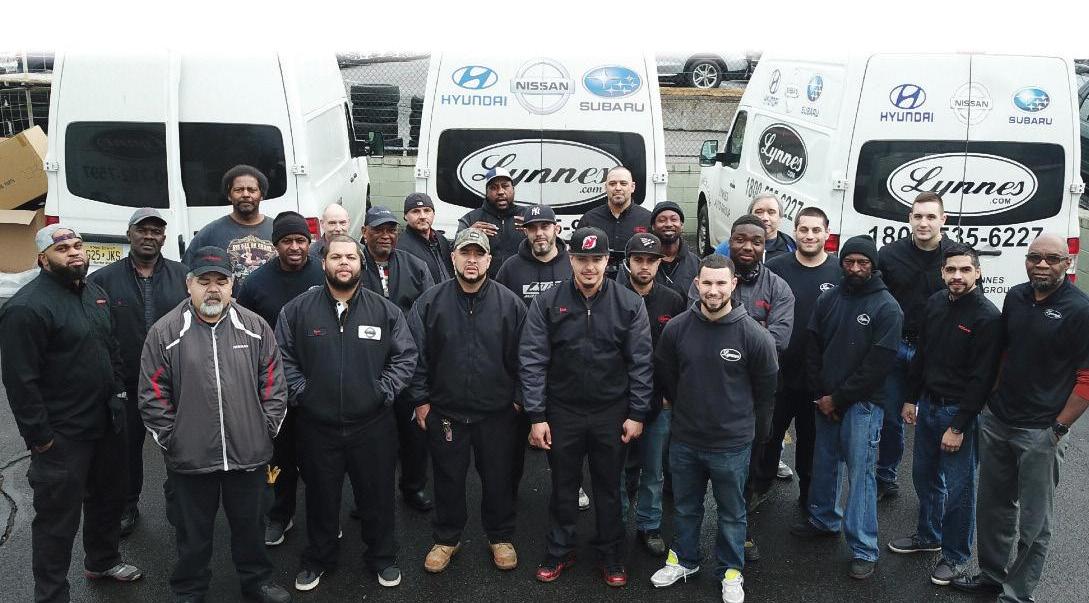
Delivering to the New Jersey/New York area.
Genuine Nissan parts are built to the same standards as Nissan vehicles. It’s no wonder they’re the driving force behind the most exhilarating vehicle on the road.
7 experienced countermen and 12 drivers ready to serve

Parts: 800-782-7597
E-mail: John@lynnes.com www.lynnesnissan.com Hours: M-F 7:30am - 6pm, Sat 7:30am - 2pm 5 Alva Street | Bloomfield, NJ 07003 is a distributor of high quality collision supplies sold at cost effective pricing.
Check out our website and find many great products!
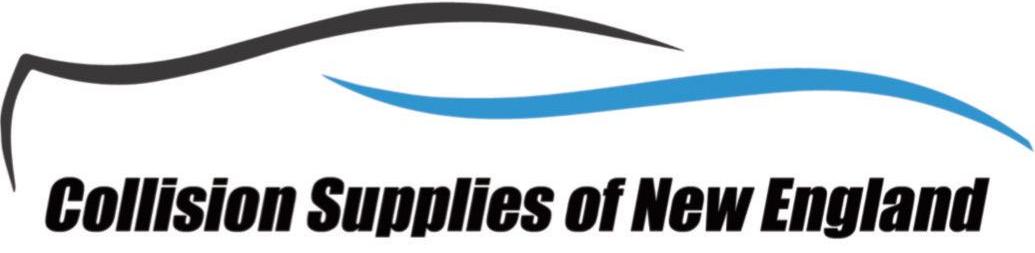
• Clear Coat Set Ups • Seam Sealers • Primer • UV Products • Putties and Fillers
• IWATA Spray Guns • Masking Tape • Colad Cup Systems • Colad Paint Suits • Spray On Bedliner Product Sign up for our newsletter! Subscribers are notified of new specials each month. We carry a complete line-up of ICR Sprint, Colad and Sunmight Abrasive products.
First Time Customers receive 10% off when placing their first online order of $50 or more! Use coupon code 10-Off when ordering online.
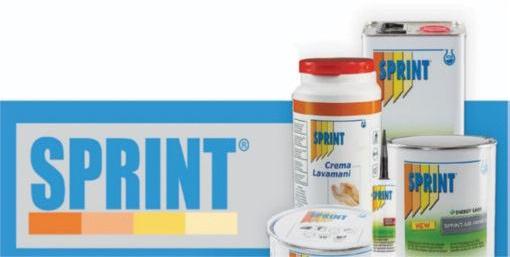
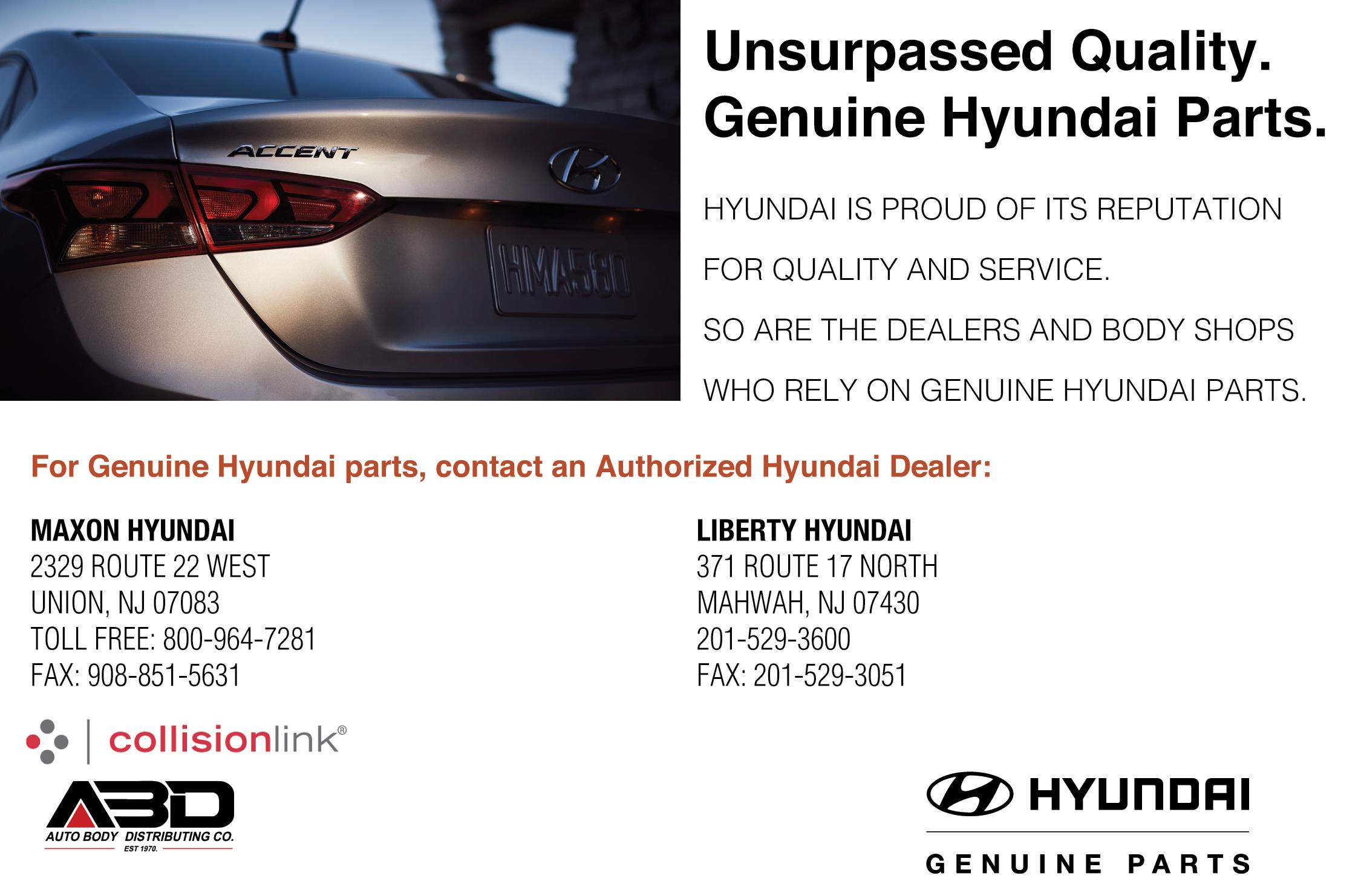
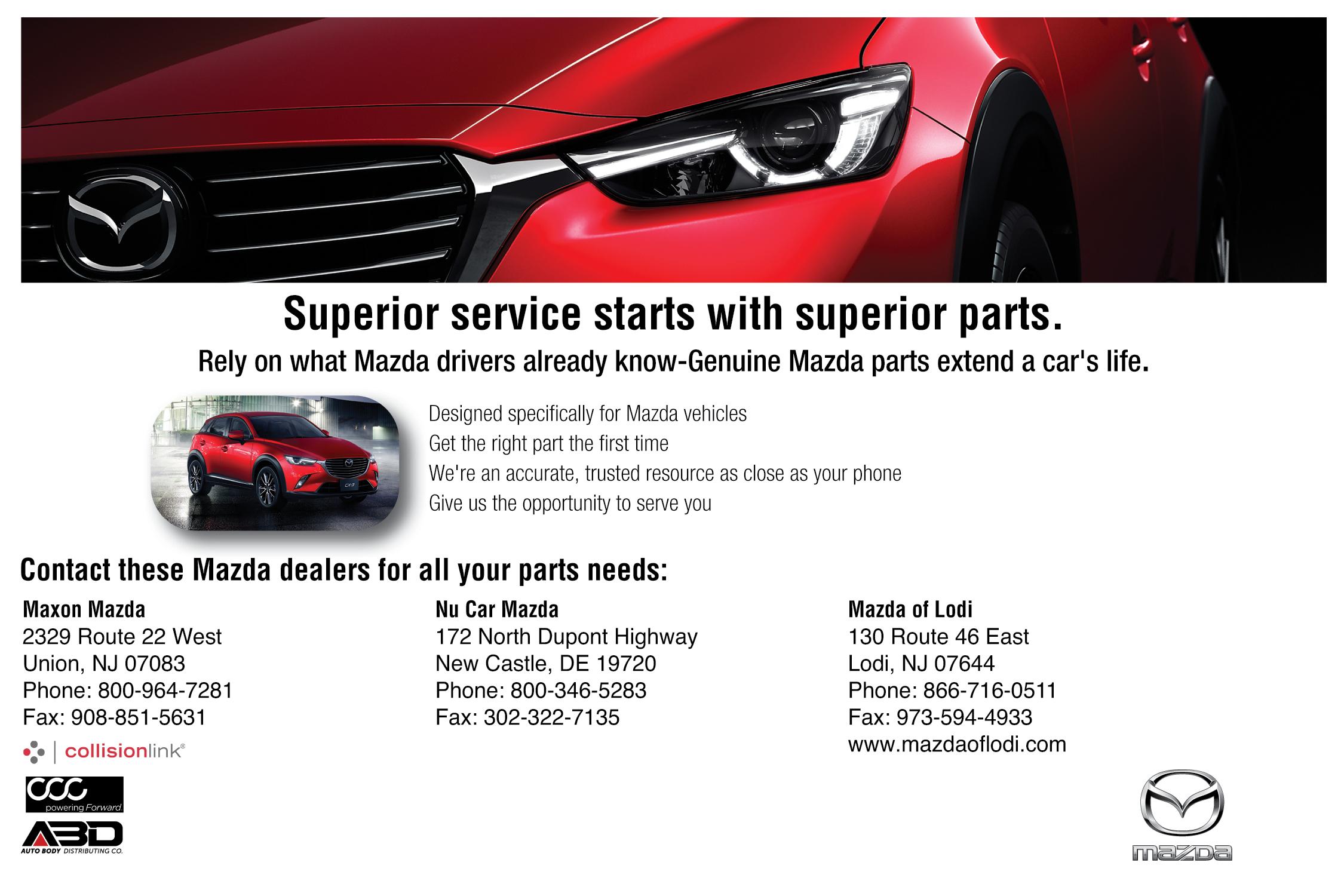
EMPIRE AUTO PARTS
Spend more time running your business and less time worrying about your parts. www.empireap.com
Lamps Bumper Covers Radiators Hoods & Fenders
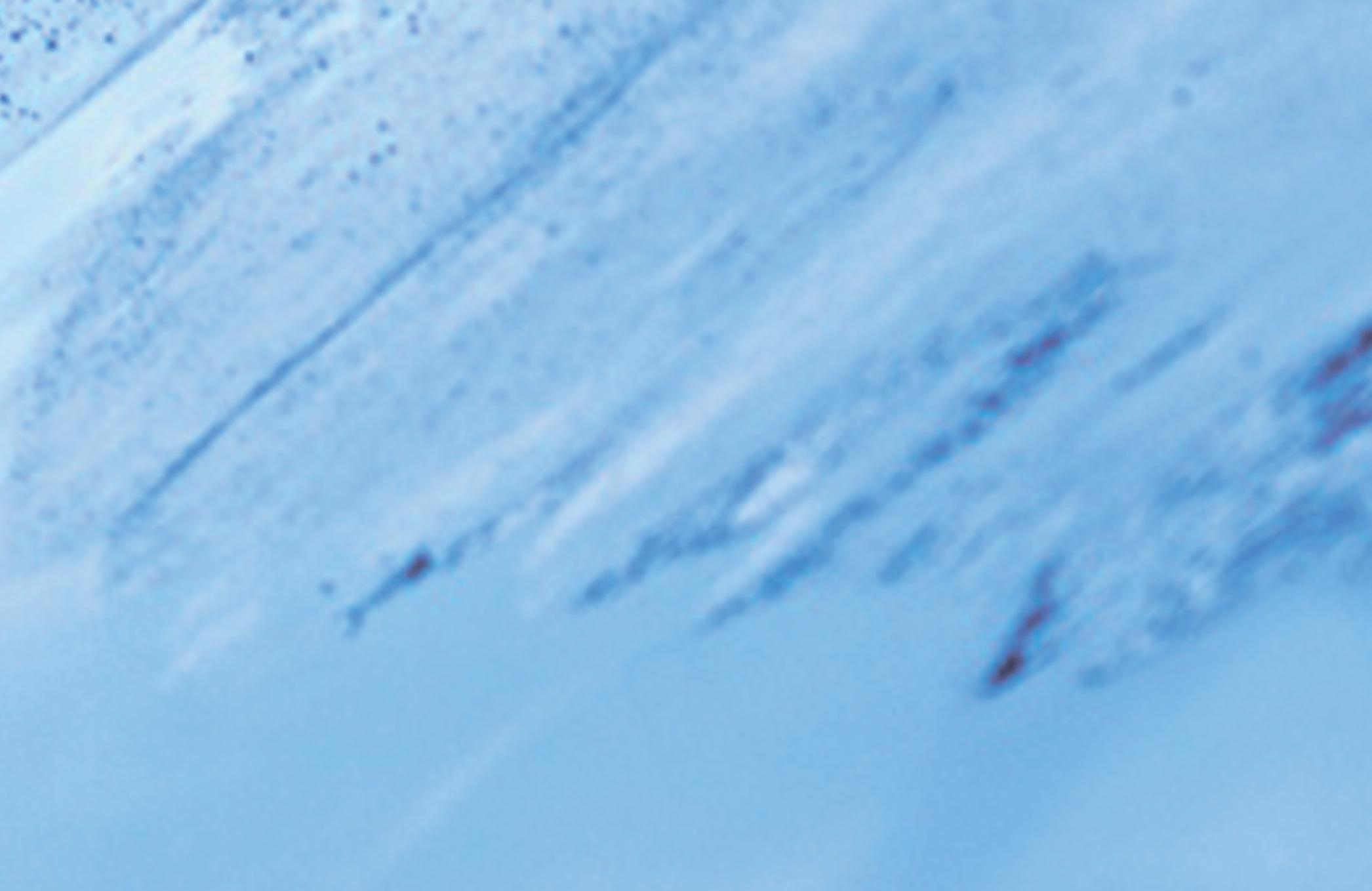
Door Mirrors Steel Bumpers
Cooling Fans
NJ DISTRIBUTION CENTER
Grilles & Bezels
800.624.4561
Serving CT, DE, MA, NJ, NY, PA, VT
Parts Accuracy Friendly Sales Team Quality Assurance Fast, Free Delivery
Pro Spot Announces VW Group Approval

Adding to its prestigious list of OEM approvals, Pro Spot International proudly announces the Volkswagen Group has approved their SP-5.3 MIG welder, VAS 821 007, for the North American market. “It has been a rigorous process to get to this point, and I am pleased to receive the recognition of such an industry giant as the VW group for our company and product approval,” Pro Spot President Ron Olsson states.
Introduced three years ago, Pro Spot’s SP 5.3 multi-process, double pulse MIG welder was tested and approved for aluminum, steel and MIG brazing (CUSI). Easy and quick to use, the SP-5.3 uniquely features three built-in torches, attached to a wire spool which prevents the need for changing liners and wires when swapping materials. Clicking the desired torch trigger automatically sets the welder control and gas.
Contact Pro Spot for more information at (877) 776-7768 or at ProSpot.com.
Women’s Industry Network Accepting Nominations for 2022 Most Influential Women
Do you know an influential woman in the collision repair industry? You probably know a few!
Nominations are now open for the Women’s Industry Network’s (WIN) 2022 Most Influential Women (MIW) awards. Women working in any segment of the collision repair industry across the US and Canada can be nominated for the MIW award; nominees are not required to be WIN members to be eligible.
Nominations will be accepted through Friday, January 14, 2022. Winners will be celebrated during WIN’s 2022 Annual Conference, scheduled for May 2-4, 2022. Established in 1999, the MIW award recognizes women whose leadership, vision and commitment to excellence have enriched the collision repair industry. Over 100 impressive women have been recognized to-date for their contributions. Make sure that amazing woman in your shop or other collision business gets the recognition she deserves by nominating her today!
More information and a nomination form can be found online at bit.ly/2022MIWnominees.
continued from pg. 12
because she has scruples. The powers-that-be dictate what it takes to fix a car, how to fix it and where to buy parts. But we shops let them do it! Who’s the expert in fixing cars: Them or us? We are! An increasing number of shops have begun to realize that we cannot continue running our businesses the way we did in the past and are pushing back against these unfair practices, but there are still shops who haven’t got a single clue about what they’re doing, so they’re always willing to do the job for less money if the insurer feeds it to them.
Lately, I’ve noticed a lot of appraisers are falling back on their morals and quitting the insurance industry. They know the insurance companies aren’t doing right by their customers, and they simply cannot partake in such a broken system anymore, so they’re jumping ship. Some find employment at body shops; others leave the industry altogether. After the threats and the coercions, they simply decide to walk away because they’ve had enough! When are we going to say, “Enough is enough” and demand that insurers properly indemnify our mutual customers?
NJA
Our wholesale parts team is here to make sure you find the exact Genuine Subaru Parts you need for every repair.
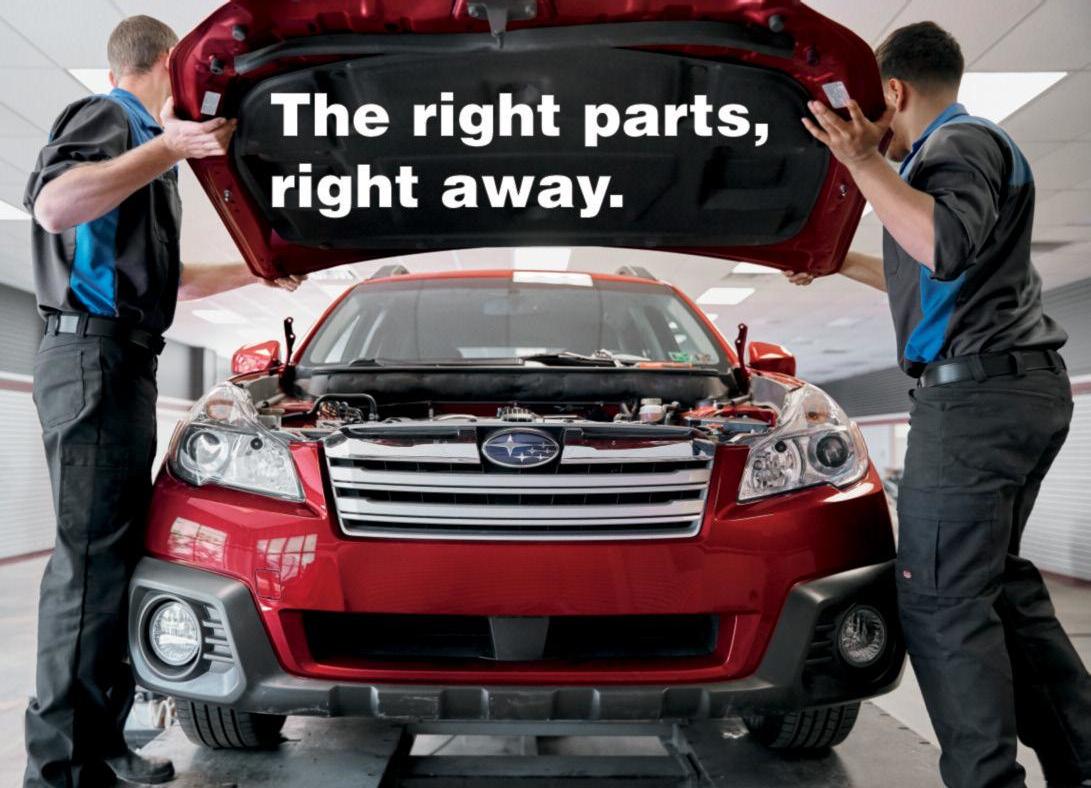
• Competitive prices • Fast, accurate deliveries • Genuine Subaru Parts that drive your business
Paul Miller Subaru 3469 Route 46 Parsippany, NJ 07054 Phone: 973-658-5714 Fax: 973-402-9591 mdaltilio@paulmiller.com www.paulmillersubaru.com/parts
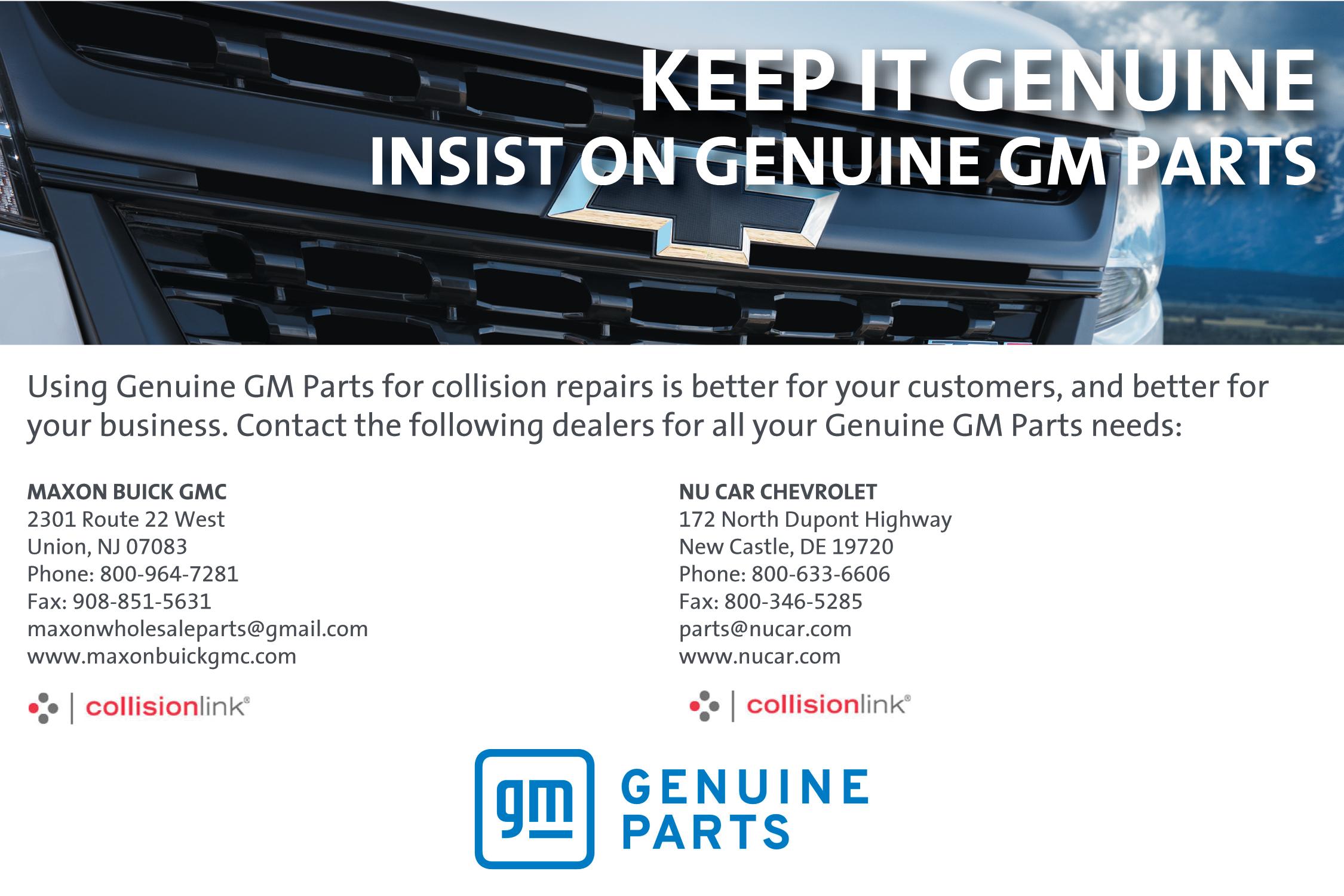
ARANJ Board of Directors
David Yeager - EL & M Auto (800) 624-2266 / elandmauto@aol.com
Ed Silipena - American II Autos (609) 965-0987 / esilipena@yahoo.com
Norm Vachon - Port Murray Auto (908) 689-3152 / portmurrayauto@yahoo.com
Dillon Rinkens - East Brunswick Auto (732) 254-6501 / ebautonj@comcast.net ARANJ Officers
President - Rodney Krawczyk Ace Auto Wreckers (732) 254-9816 / aceautonj@comcast.net
1st Vice President - Daryl Carman Lentini Auto Salvage (908) 782-4440 / darryl@las-parts.coms
2nd Vice President - Mike Ronayne Tilghmans Auto Parts (609) 723-7469 / tilghmans@snip.net
Past President - Bob Dirkes Dirkes Used Auto Parts (609) 625-1718 / dirkesauto@gmail.com
ARANJ
The Automotive Recyclers Association of New Jersey
Wharton Insurance Briefs
Providing a strong employee benefit program is still an important part of attracting and retaining valuable employees. Even more crucial is the ability to provide a good employee benefit package at an affordable cost. Years ago, the employee benefits market evolved from indemnity-style plans to managed care plans, commonly referred to as HMOs. As the years went by and prices increased, many employers added deductibles and increased copayments to help offset the continuing premium increases. High Deductible Health Plans (HDHP), also known as consumer-driven healthcare plans, mimic the indemnity-style plans and are designed to encourage employees to become better consumers of healthcare. Consumer-driven healthcare plans utilize high deductibles to decrease costs which can be offset with employee-owned or employer-funded bank accounts, also known as Health Savings Accounts (HSA) and Health Reimbursement Accounts (HRA). These options have become very popular with both small companies and larger corporations as it meets the needs of employees and the budget of employers. Professional Employer Organizations (PEOs) and designing an employee contribution through payroll deductions are two other ways employers have initiated cost reductions. If you would like more information about reducing insurance premiums or have an interest in learning more about the options, please contact me.
Mario DeFilippis, AAI Vice President (800) 221-0003, ext. 1320 (908) 513-8588 mdefilippis@whartoninsurance.com
NJA

Diagnostically speaking, there is no substitute.
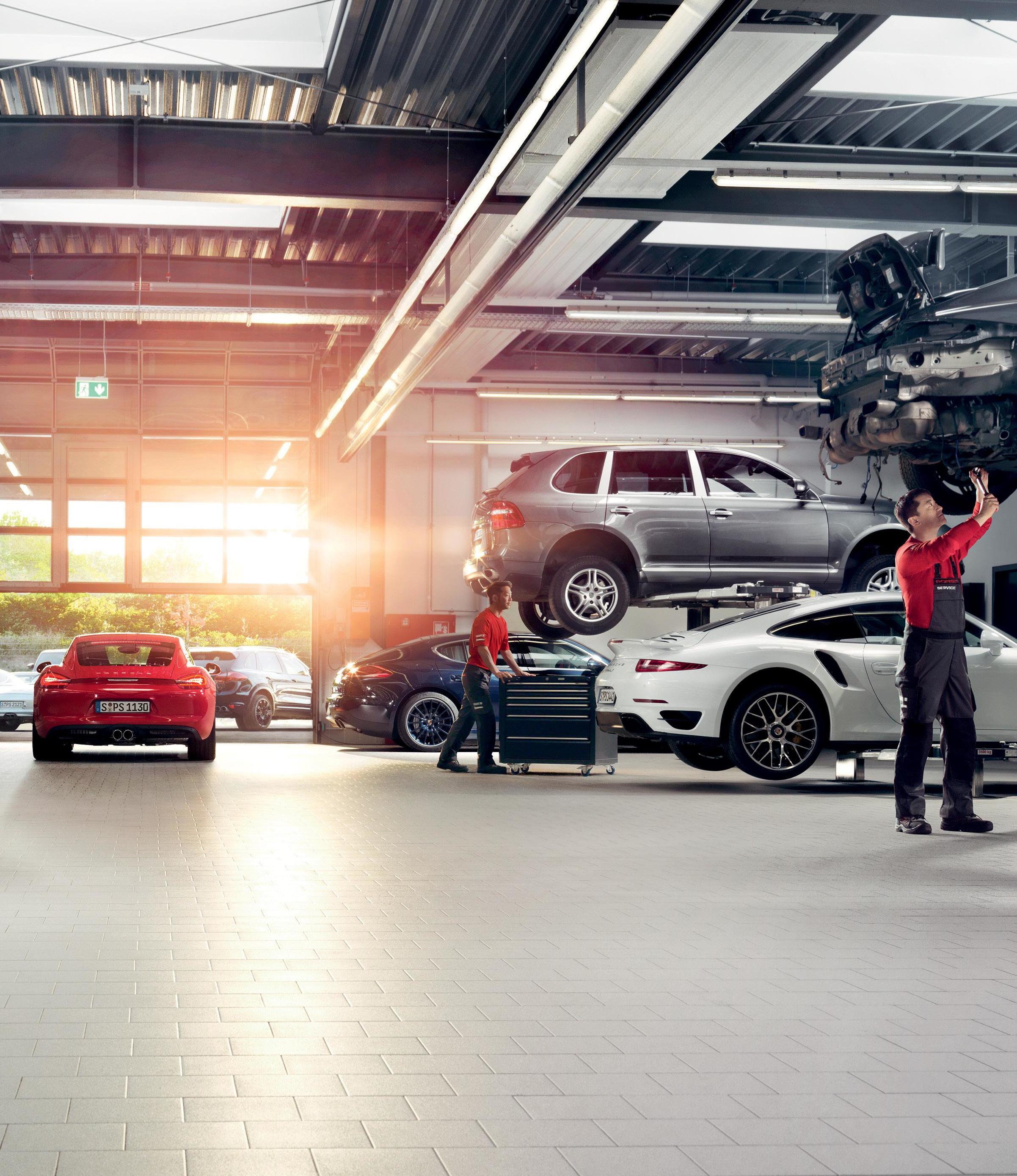
Porsche technology. Porsche Genuine Service & Parts.
Contact one of these authorized dealers.
Town Porsche
105 Grand Avenue Englewood, NJ 201-227-6505 Fax 201-227-6553 town-motorcar.porschedealer.com
Flemington Porsche
213 Route 202/31 Flemington, NJ 800-216-5124 Fax 908-782-9397 flemingtonporsche.com
Porsche Princeton
3333 Route 1 Lawrenceville, NJ 609-945-1500 Fax 609-945-1501 princetonporsche.com
Paul Miller Porsche
3419 Route 46 East Parsippany, NJ 973-227-3000 Fax 973-575-8396 paulmillerporsche.com
Porsche Monmouth
280 Route 36 East West Long Branch, NJ 732-935-7600 Fax 732-935-7602 porschemonmouth.com
Manhattan Motorcars
711 11th Avenue New York, NY 877-661-1586 Fax 646-473-0798 manhattanmotorcarsporsche.com
© 2021 Porsche Cars North America Inc. Porsche recommends seat belt usage and observance of traffic laws at all times.