
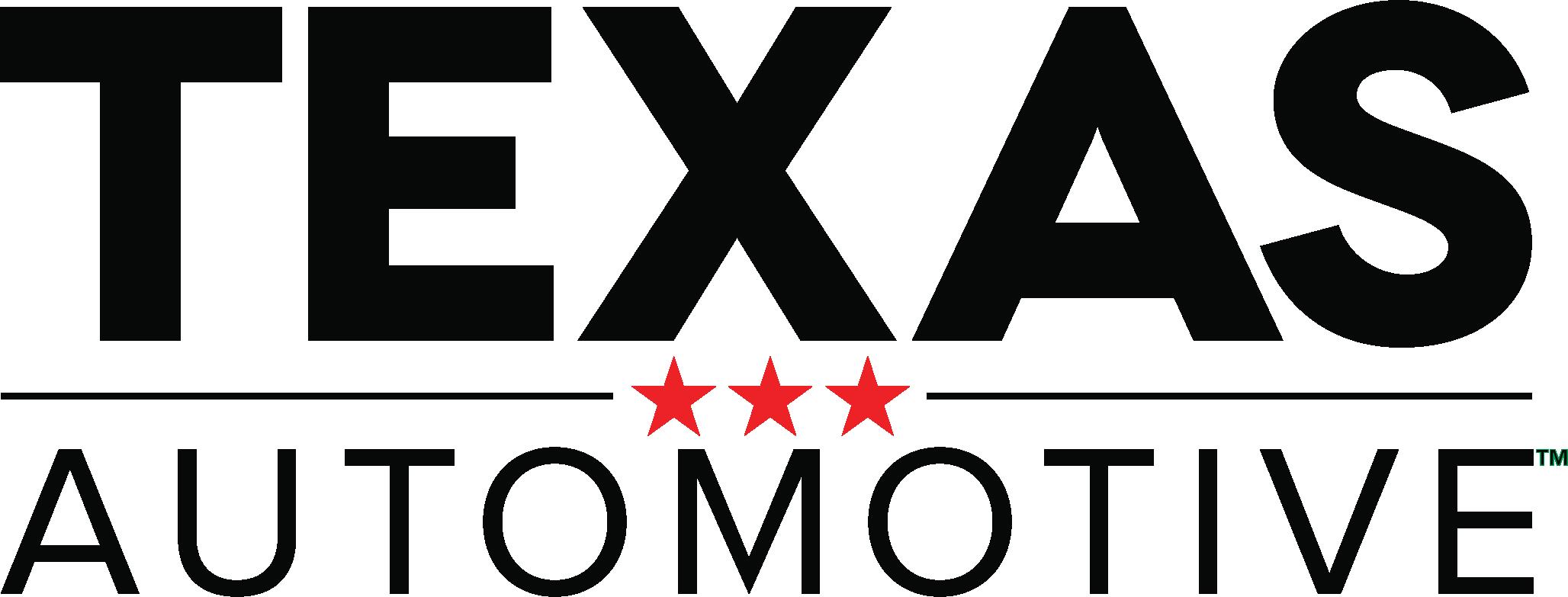

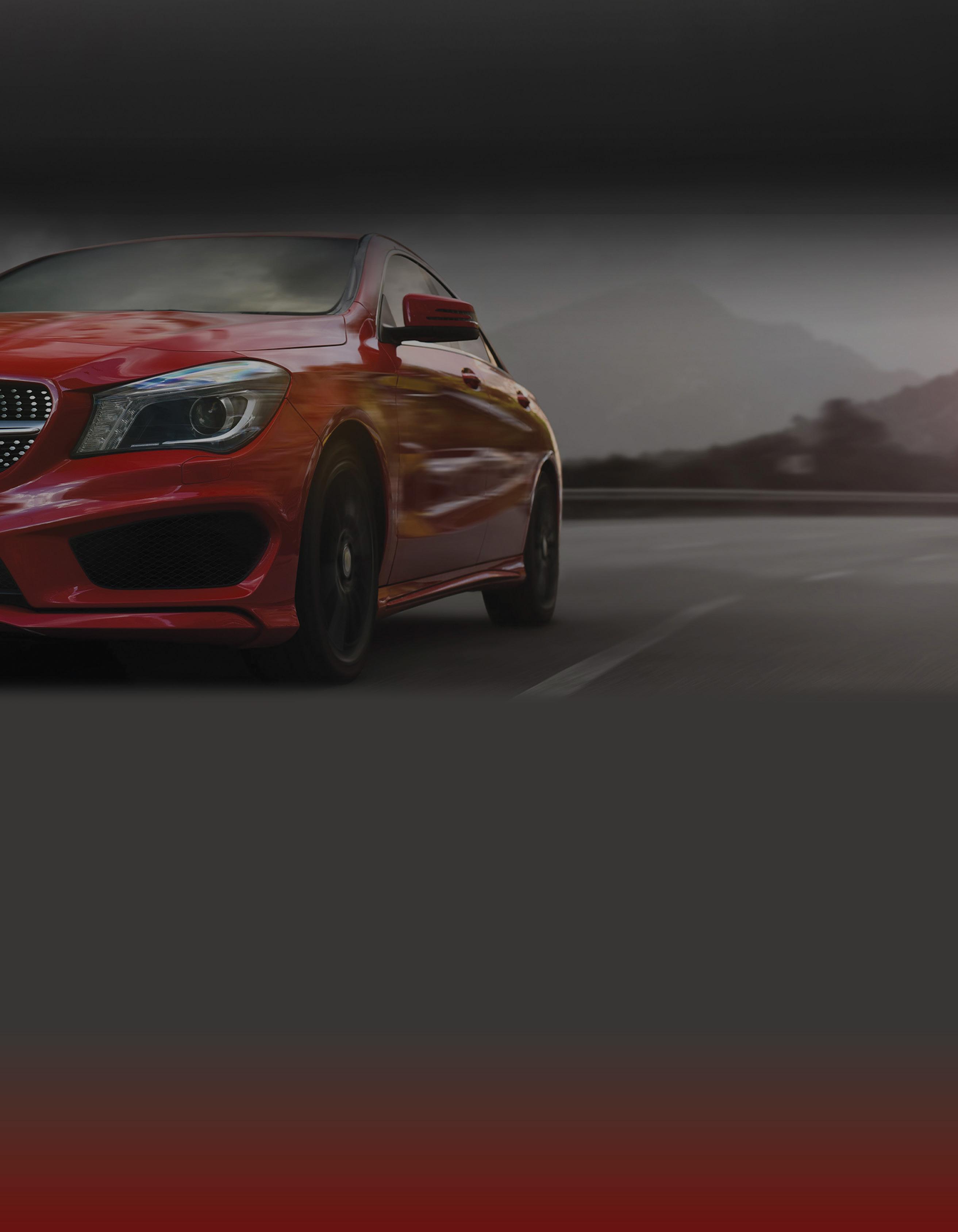
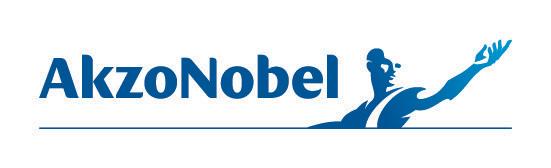
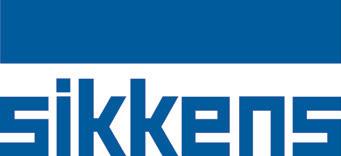
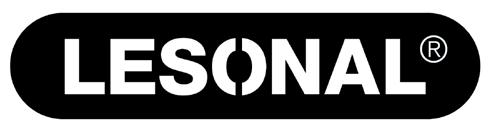

PRESIDENT’S MESSAGE by Burl Richards
A Sharing Place
EXECUTIVE DIRECTOR’S MESSAGE by Jill Tuggle
Elvis Is Back in the Building!
TEXAS AUTO BODY TRADE SHOW: SAVE THE DATE!
NATIONAL NEWS by Chasidy Rae Sisk DEG Reboot Enhances Security and Increases Efficiency
LOCAL FEATURE by Chasidy Rae Sisk
A Glimpse into Career and Technical Education with Texas Collision Instructors (Part 1)
ASK THE EXPERT by Robert McDorman
What is the Latest Update on the Appraisal Bill?
NATIONAL FEATURE by Chasidy Rae Sisk Operative Talent: On a Mission to Educate the Public about Collision Careers
President Burl Richards Burl's Collision Center burl@burlscollision.com (903) 657-8082
Chairman of the Board Corey Pigg S&W Expert Collision Repair coreyp@swcollision.com (936) 634-8361
Vice President Eric McKenzie Park Place Dealerships emckenzie@parkplace.com (214) 443-8250
Treasurer David Osburn Paint Works davidosburn@paintworkstyler.com (817) 648-5797
Executive Director Jill Tuggle jill@abat.us (817) 899-0554
Bobby Beason DeMontrond Collision Center bobby.beason@demontrond.com (936) 577-2747
Larry Cernosek Deer Park Paint & Body lcwrecker@comcast.net (281) 930-1539
Kevin Ellison Westway Ford kellison@vtaig.com (972) 584-9033
Brandon Gillespy Park Place BodyWerks bgillespy@parkplace.com 214-443-8250
Chad Kiffe Berli's Body & Fine Finishes chadk@berlisbody.com (512) 251-6136
Greg Luther Helfman Collision gluther@helfman.com (713) 574-5060
Darrell Smith McDaniel’s Quality Body Works Inc darrell-mcdaniels@sbcglobal.net (903) 753-5391
Robert McDorman Auto Claim Specialists rmcdorman@autoclaimspecialists.com (817) 756-5482
Chad Neal Innovative Collision Equipment Chadwneal@yahoo.com (817) 527-2143
Logan Payne Payne & Sons Paint & Body logan@paynescollision.com (214) 321-4362
Anthony Palomo West Texas Auto Color japalomo3@yahoo.com (806) 831-7765
Manuel Rubio Miracle Body & Paint manuelr@miraclebp.com (210) 843-9564
Albert Salinas South Houston Nissan asalinas@southhoustonnissan.com 833-856-7871
Mike Williams All Star Collision Center sales@allstarcollision.us (903) 589-3160
Published by: Thomas Greco Publishing, Inc. 244 Chestnut Street, Suite 202, Nutley, NJ 07110 Corporate: (973) 667-6922 / FAX: (973) 235-1963
PRESIDENT/PUBLISHER
Thomas Greco / thomas@grecopublishing.com
VICE PRESIDENT/SALES DIRECTOR Alicia Figurelli / alicia@grecopublishing.com
EDITORIAL/CREATIVE COORDINATOR
Alana Quartuccio / alana@grecopublishing.com
MANAGING EDITOR
Chasidy Rae Sisk / chasidy@grecopublishing.com
PRODUCTION COORDINATOR
Joe Greco / joe@grecopublishing.com
OFFICE MANAGER
Donna Greco / donna@grecopublishing.com
SPECIAL CONTRIBUTORS: Burl Richards / Jill Tuggle
Robert L. McDorman / Mike Anderson / Jacquelyn Bauman
@grecopublishing
www.grecopublishing.com
TEXAS AUTOMOTIVE is published monthly and is sent to ABAT members free of charge. Subscriptions are $24 per year. TEXAS AUTOMOTIVE is published by Thomas Greco Publishing Inc., 244 Chestnut St., Nutley, NJ 07110. The editorial contents of TEXAS AUTOMOTIVE are copyright © 2023 by Thomas Greco Publishing Inc. and may not be reproduced in any manner, either in whole or in part, without written permission from the publisher and/or editor. Articles in this publication do not necessarily reflect the opinions of Thomas Greco Publishing Inc. Stock Images courtesy of www. istockphoto.com
Y“You’re NOT the only one” – when ABAT first started, way back in 2014, we set out to help shops combat the ideology that had been instilled in us by the insurance carriers who constantly insisted that every shop charging fair rates for the work they performed was “the only one.” They brainwashed many shops to believe that we couldn’t charge for OEM procedures, that aftermarket parts were just as good as the originals and that we needed to fall in line and just accept the “prevailing rate.”
I’m happy to say that was all a bunch of hogwash, and shops all across the Lone Star State have embraced some truths of the business, starting with the fact that these are OUR businesses and WE are the ones who decide how they run.
We know there’s a huge difference in the safety component and aspect of a vehicle based on the type of parts used; OEM parts are designed to absorb energy in a certain way to ensure the occupants’ safety. Vehicles that are repaired using structural aftermarket parts simply aren’t as safe.
As a professional repair facility, our goal is to repair every vehicle to its pre-accident condition, and the only way to do that is by following the OEM recommended processes and procedures! You cannot properly repair today’s vehicles without following the manufacturer-specific guidelines. This is how we ensure that a customer’s vehicle will perform as it was intended if there’s another accident.
And we all know that the concept of “prevailing rate” is nothing but a hoax. A shop’s rates should reflect the cost of doing business in that particular market. Yet, insurers use the concept of prevailing rates to strongarm shops into accepting lower rates… or charging the customer the difference. And customers shouldn’t have to pay more than their deductible; the consumer already paid their insurance premium, which is meant to pay for restoring their vehicle after an accident. A consumer not getting what they paid for is under-indemnification, plain and simple.
Burl Richards ABAT PresidentKnowledge is power, and we are all learning more each day, strengthening our shops and one another. I saw powerful evidence of this recently when I received an email from a Dallas shop owner who had put necessary processes and procedures on their invoice only for Farmers Insurance to claim “you’re the only one.” Well, this ABAT member has really invested time and energy into learning our craft over the years, so they shared all their p-page research to show how clear coat time is capped at 2.5 hours, but when we have to paint inside the door jambs or paint the uniside, now that vehicle spends twice as long in the paint booth, and that additional time is a notincluded item. He did a great job detailing the information about this
continued on pg. 22
PPlans for the 2023 Texas Auto Body Trade Show are well underway, and we have BIG news for you…MIKE ANDERSON IS BACK! That’s right! Collision’s “Elvis” is back in the building, and he is just as excited as we are!
I ran into Mike several times in the past year at industry events, and each time, he made it a point to tell me how much he LOVES Texas. We obviously agree, and I also let him know how much we love him.
If you haven’t seen Mike Anderson speak, you are missing out! If you love his YouTube videos, you ain’t seen nothin’ yet – he is even more dynamic in person! He delivers both crucial repair information as well as customer and personnel relations tips that will change your whole viewpoint on business.
Beyond “the King,” we have some of the industry’s BEST speakers coming to you this year. We even have some new faces! Of course, you’ll see some old fan favorites like Danny Gredinberg (Database Enhancement Gateway), as well as ABAT’s own Burl Richards and Robert McDorman (Auto Claim Specialists). Back by popular demand is Texas and ABAT’s very own Logan Payne of the cutting edge and quite successful Dallas shop, Payne and Sons. Erin Solis with Certified Collision Group will deep dive into estimating
Another big name gracing our lineup this year is Aaron Schulenburg, executive director of the Society of Collision Repair Specialists (SCRS)! Aaron is an eloquent speaker who always leaves you with a lot to ponder. He will be talking about the jawdropping results of the blend study that SCRS conducted last year. He may even have some updates to share with us…
Jill Tuggle ABAT Executive DirectorAnd that’s not all, folks! We have so much more to share with you, but you’ll have to stay tuned to the coming issues of Texas Automotive! Registration opens this month, and you’ll want to get your spot early because some of these classes will sell out quickly!
Featuring education from national speakers, vendors, networking, live demos, celebrity appearances, a car show and ABAT’s BIG SHOTS Competition
Please plan to join us August 25-26, 2023 at The Irving Convention Center surrounded by the exciting Toyota Music Factory where dining, entertainment and hotels are just steps away!
Exhibitor registration open NOW & attendee registration will be opening soon. Stay tuned for updates by visiting abat.us/events/tradeshow
As anyone who works in an auto body shop can certainly attest, the operations identified by information providers (IPs), such as Audatex, CCC and Mitchell, are much more likely to be “estimates” of the time and requirements actually affiliated with certain procedures than the detailed repair plans written in today’s facilities. For 15 years, the Database Enhancement Gateway (DEG) has been helping the collision repair industry improve the quality, accuracy and standardization of their repair blueprints – with over 20,000 inquiries submitted through the end of last year.
Suffice it to say that the DEG is powerful, yet because it is funded and managed by the Society of Collision Repair Specialists (SCRS) and the Alliance of Automotive Service Providers (AASP), along with additional donors/sponsors, this resource is offered FREE to the industry, allowing users to provide feedback that is used to improve the quality of information in the IP databases… and if that wasn’t already an amazing feat, degweb.org saw a significant reboot earlier this year, designed to enhance security, increase user-friendliness and advance analytic capabilities.
“The entire website is completely refreshed with a new look and feel,” according to DEG Administrator Danny Gredinberg. “It has been mobile-optimized to encourage more users to utilize the free resource. Phoenix Solutions Group stepped up to the plate and not only built a new main website but also completely rebuilt the database from scratch, making it faster, easier to use and more visually appealing, all while maintaining the existing database and without losing any information.”
Nick Schoolcraft (Phoenix Solutions Group) shared highlights about the updated site. “Security has been enhanced, and the ability to input inquiries will be much faster and more user-friendly,” he promised. “Users will be able to dive deeper into each individual query, plus we increased the overall speed of the website, leveraged mobility so it will be usable on mobile devices and updated the structure of the database to improve the reporting feature.”
The primary goal of the redesign was security enhancement, ensuring the new website would provide the highest possible level of security while also improving the user experience. “We invested in enhanced security measures that don’t slow loading times or make the user experience cumbersome,” Schoolcraft explained. “By taking these extra precautions, we’ve been able to make sure visitors get the best possible experience while keeping their data secure. With the enhanced security measures in place and faster load times, visitors can feel good that DEG is doing its part to keep its data safe.”
“Phoenix Solutions Group’s top priority was ensuring the security of the data we receive cannot be accessed by anyone since that information can be sensitive,” Gredinberg added. “Each user that accesses the information only has a certain level of access, depending on their assigned permissions, for the specific information necessary to complete their review of the inquiry and database.”
Most users are familiar with the DEG from the perspective of submitting questions for clarification from the IPs, and often, those
inquiries result in changes to the databases. In fact, 60 percent of the inquiries submitted in 2022 resulted in a net change. “That’s the power of what the DEG does,” SCRS Board member Barry Dorn (Dorn’s Body & Paint; Mechanicsville, VA) noted. “It provides a way for us to collaboratively push the boulder up the hill together.”
While inquiries are still input through a webform, the process has been revamped to provide an updated look while also being updated to work seamlessly with all web browsers, whereas it worked best with Google Chrome prior to the reboot. Optimizing the site to make it more accessible on tablets and mobile devices was another top priority. “A fundamental component of the redesign was to make sure visitors had a seamless experience across all devices, from desktop and laptop computers to tablets and mobile phones,” according to Schoolcraft. “We wanted the site, as well as database inquiries, to be effortlessly consumed by visitors on any device.”
“We hope this will encourage additional use straight from the shop floor,” Gredinberg added. “You can quickly add attachments (photos, videos and various documents) right on the spot to streamline the inquiry process.”
Users can also expect improved search results and filtering options for vehicle-specific information when searching the database, allowing for streamlined workflows as well as advanced data and analytical capabilities.
“Visitors of the site will see improved search functionality as well as a much faster, responsive and intuitive experience,” Schoolcraft promised.
Lastly, the Estimators’ Toolbox portion of the website has been expanded to provide even more estimating tips, easy access to SCRS’ Quick Tips videos, OEM repair information, links to vehicle owners manuals and much more to help keep today’s collision repair professional informed with all the data they need right at their fingertips.
Learn more about the DEG or submit an inquiry at degweb.org. TXA
Collision repair shops face many challenges every single day, and some of today’s biggest include the ongoing workforce shortage and the need to contend with insurance adjusters who repeatedly insist that they “don’t pay for that.” approve shops’ repair plans because they dislike the way shops’ “estimates” are written have been attempting to steal repair planners from Texas
that those Pro-aggressive adjusters tried to poach my employee while reviewing cars in my shop with my employee. But really, this should come as no surprise to any of us.
Two shop owners have recently dealt with Progressive’s poaching attempts, and they want
Collision; Henderson) first brought the matter to light. “Two years ago, we hired a guy with no collision experience, and we’ve invested our time and energy into training him and turning him into the sort of repair planner that any shop would be proud to employ. Just as we started to reap the benefits of his newfound experience and knowledge, I learned that he had received an offer from Progressive. Well, I gave him a substantial raise to keep him, and although he earned it and it was coming anyway, it’s insane trying to reap the benefits of our shop’s years of
Increasing employee compensation is just one of the many factors contributing to rising costs for shops. “Our cost of doing business is accelerating more rapidly than ever before, and when a carrier creates this type of situation, that just exacerbates the problem,” Richards pointed
rejecting procedures and under-indemnifying consumers because they want to minimize their bottom lines even as they force shops’ costs up
David Norris, general manager of Scott’s situation that occurred in his shop last year. “An
more money (even though he was still not skilled or proficient in his position yet) because of an alleged offer made by Progressive. Ultimately, he didn’t leave the shop, but there was definitely a Progressive birdy in his ear, and while I cannot say with 100 percent certainty that it took place on my premises and timeclock, it seems likely
“We are dealing with a company that admittedly denies not-included operations,” Norris continued. “For example, labor time for prime, feather and block in both Mitchell and CCC state that the time is based on judgment and should be discussed. It also states that it is a necessary procedure to bring a repaired panel from 150 grit to a refinish-able surface or substrate. Yet, this operation and the materials needed to perform it are denied 100 percent of the time at my shop. I am told that Progressive is aware that the very estimating system they use states otherwise, but it is a company decision to not pay for a needed operation. Local Progressive adjusters tell me, ‘I am not allowed to pay for those operations.’ The list of Delay, Deny, Defend tactics from Progressive go on and on. Meanwhile, [Progressive CEO] Trisha Griffith raises rates on policyholders so she can collect her $15 million annual salary and keep shareholders happy with tremendous returns at the expense of claim suppression and policyholder under-indemnification. What a racket!”
Upon discovering the poaching attempts taking place, Richards reached out to Progressive’s managers, demanding they cease and desist with the “tortious interference” to his business. Although Progressive had previously hired four of Richards’ prior employees, he did not take it personally until he learned of their attempts to recruit his current repair planners during their duties at Burl’s Collision.
“I have information that you have reached out to one of my repair planners, and once they rejected your offer, you have now reached out to yet another one of my employees,” Richards wrote in an email. “I find it concerning that your employees come to my facility to write estimates and supplements, and now your company offers job opportunities to them even while they are on my clock. I also find it interesting that you refuse to pay our posted rates and many processes and procedures that are necessary to make proper repairs, yet I am put in the position to give my employees raises to keep them from joining your team, or I am faced with the expense of replacing and training new hires.
“You are contributing to my cost of doing business and are part of the reason I must continue to increase rates and other factors
that affect my profitability. You would think a company the size of Progressive could find and train their own estimators. I appreciate the fact that you find my employees valuable as they possess industry and OEM certifications and are trained to write proper repair plans based upon the manufacturer’s recommended processes and procedures. It’s a shame that the same company that under-indemnifies consumers and cuts our estimates/repair plans also wants to hire the same people that wrote them.”
The adjusters who attempted to poach Richards’ employees have been banned from his repair facilities, though he sarcastically offered a position to any Progressive adjuster interested in working for his shops: “Based on the industry knowledge and ability of your estimators to write OEM-recommended repair plans (excluding some of my previously trained employees), I would like to offer each of you a salary of $15,000 per year. Even monkeys are trained to do phenomenal feats, and I believe in time we could even train you to write proper repair estimates and repair plans that will restore vehicles to their pre-accident condition. Keep in mind that your salary could triple or quadruple in a short time if you can process proper estimating.”
Richards also confirmed that Progressive pays a bonus to any adjuster who is able to recruit a new employee. “One of your employees mentioned that they have referred other body shop employees to Progressive, but never from Burl’s,” he acknowledged in his email to the carrier. “I want to believe them, but I am very skeptical based upon what I am hearing from other shops that are now starting to wake up to the realization that Progressive is actively seeking to recruit qualified talent from our facilities.”
In response to Richards’ accusations, Progressive Claims Manager Doyle McCarty denied that the company has attempted to poach any
employees from Burl’s Collision. “Your email alleges, among other things, that we have ‘poached’ or are ‘poaching’ your employees to join our company. Additionally, you’ve demanded a cease and desist of the alleged activity. Although we respectfully deny any allegations that our employees engage in poaching, we will share your concerns with our staff interacting with you or your shop as part of the claims handling process.”
Richards insists on categorizing Progressive’s recruiting techniques “as poaching because it’s not being done off site from my business, and it is being done on my time as I am paying my employees. I consider this tortious interference to my business as Progressive is enriching themselves off my payroll and resources, and we’ve told their adjusters to come, write the estimate and then get out. There’s no reason to engage in small talk with my employees. Do your job and go.”
He also expressed the desire to “make other shops aware of these egregious business practices. Our industry has been dealing with a shortage of qualified talent for entirely too long, and when we have insurance companies coming on OUR property and trying to poach from our teams, that’s taking it to a whole new level. We want other shop owners to be aware so they can keep their eyes open and pay attention to those whispered conversations – are they talking about the repair, or are they making an offer to one of your valuable employees? We can’t afford to lose the well-trained help that we’ve spent years developing, and I doubt any of you can either.”
If your shop’s employees have been poached by Progressive or any other insurance carrier, Texas Automotive wants to hear about it! Let us know by emailing chasidy@grecopublishing.com TXA
Many of today’s collision repair professionals obtained their initial education through a local vocational program, but today, vo-tech is a thing of the past. As the industry has changed and adapted to advancing technology, programs have also adapted, rebranding to career and technical education facilities, which makes a lot of sense as these careers have become highly technical.
Yet, at the same time, it seems that fewer and fewer students are pursuing careers in the trades, including collision repair. Are students less interested in the field, or are shops failing to retain young talent? While some shops lament the lack of knowledge that recent graduates possess, few of them are involved with local programs to promote the need to teach the right skills. And without the industry’s involvement, there’s a real danger of many of these programs becoming obsolete – or even closing.
Do you know what’s really happening in today’s trade schools? Probably not, but the teachers dedicated to teaching tomorrow’s technicians sure do! Texas Automotive solicited feedback on these issues and more from four Lone Star collision instructors: Raven Hartkopf (Collin College; Allen), Keith Schieffer (Universal Technical Institute; Houston), Jannifer Stimmel (Texas State Technical College; Waco) and Jeff Wilson (Kingwood Park High School; Kingwood).
Texas Automotive: How long have you been a collision instructor, and how has vo-tech education changed over that time period, especially as it relates to the number of students enrolled in the program?
Raven Hartkopf: I have been a collision instructor for a year and a half. In the short time I’ve been teaching vo-tech, which we now call Career and Technical Education (CTE), we are seeing a shift of interest to ADAS and electric vehicles. We are also seeing more support for online educational materials from industry leaders such as Polyvance. Our program began in the middle of COVID during the fall of 2020, so our enrollment for that cohort was 10 students. Our second year open, the year I started teaching, saw 10 students in our single cohort. This past fall, we had 21 new students, and 12 more joined us this spring. This is the first time we were able to have a spring cohort, which shows the increased interest in our program. We saw a diverse pool of students with this academic year’s cohorts. Out of the 33 new students that joined us, seven are women! Twenty-five percent of our spring cohort are veterans.
Keith Schieffer: I have 51 years of experience in the collision industry, and I’ve been teaching for the past 34 years. At one point, there were about 900 students enrolled in collision technology studies at UTI, but over the last seven or eight years, it’s gone down to around 140. I don’t believe that’s the school’s fault, though. Today’s students understand far less about the auto repair industry
than they did 20 years ago, but that’s not necessarily their fault. I believe it’s more of a generational issue, resulting from the fact that the generation before them did not include them in general automotive knowledge or transfer those skills down the line.
Jannifer Stimmel: I started teaching three and a half years ago… and COVID happened just four months into my tenure, changing the amount and the mentality of the students we attract. Just like many jobs struggled to get people to come to work during the height of the pandemic, we had a hard time with students being afraid to come into the school. The semester before COVID, we had three first semester sections, each containing 14 to 17 students. That has changed quite a bit, and though it’s improving (we now have 24 in the first semester of the regular program and eight in co-op), we’re still not back to normal.
Jeff Wilson: I was born and raised in this industry. My father owned a body shop, so once I became certified in collision repair, I was basically free labor until I graduated school. From 1994 until 2006, I taught welding, and then in 2007, I started teaching collision and refinishing in the same district. We have a four-year course which starts with an introduction to the basics of automotive which allows the students to decide on a pathway: mechanics or collision. Collision students spend the second year on nonstructural collision and start their I-CAR certifications, and their third year is spent on refinishing, custom paint and blending. Seniors go on to participate in a work-based practicum via a paid or unpaid internship.
Prior to COVID, there was a great deal of interest in the program – after all, what 16-year-old kid doesn’t want to custom paint a car? I didn’t start having enrollment issues until COVID, when it was extremely hard to give students the hands-on experience they needed when everything got shut down, but it is getting better and better as time goes by. Location also matters. It’s harder for me to get students to sign up for collision classes (and even more difficult to convince them to consider a collision career) because most of my students’ parents expect them to go to college, not to graduate and enter the workforce. I’d guess that around 85 percent of the student body graduating from Kingwood Park ends up going to a post-secondary school of some kind to get a degree. I typically have three or four students (approximately two percent) that go into the industry after graduating from the program, but I’ve placed more students this year than in the past five-plus years. Right now, three of my 16-year-olds are working after school for a local momand-pop shop to get job experience. Unfortunately, we don’t have much luck placing students with dealerships and bigger companies because their insurers won’t allow them to hire students until they’re 18 years old.
TXA: What are your biggest challenges when it comes to attracting more people into the industry, and how is your school trying to increase awareness of the program to attract and retain students?
RH: The biggest challenge is the willingness of shops to be flexible with our students’ schedules. One student interviewed at several shops, and very few were willing to take someone on a part-time basis. If there’s a reason why students don’t end up in the industry while in school, it’s because people don’t want to work around their schedules. In some instances, students have been asked to quit school in order to work full-time, during their interview! It’s disheartening to see that happen because it shows that the shop is more interested in its bottom line and productivity than a potential employee’s aspirations. Frankly, it’s brash of an interviewer to ask someone to do that. Would other companies ask their candidates to quit school halfway through? Do we see that in other industries? Probably not, but those companies value education. More importantly, it’s a red flag for that student and any other student, because they talk amongst each other. Now before I get off my soapbox about this, I do want to clarify that not ALL shops are like this, but they do stand out when I consider challenges.
Another challenge is pay. Some students, especially non-traditional ones, have difficulty transitioning into an industry that may not pay them well to start. When people think of college students, they often think of 18-21 year olds, but the age range for my students spans over 30 years between my youngest and oldest. Some students have families, mortgages and car payments, all of which are skyrocketing.
The Collision Technology department is involved with several local high school auto body advisory committees, so we have a presence there. Any time we get asked to be at a career or college fair at any high school, we try to go. This year, we will be sending collision and refinishing teams to SkillsUSA, which is a first for our program. I’m excited about having students compete because many of our students have never been able to do so. In addition, those who compete at the secondary level have the chance to continue competing as college students. I’m hoping that will attract some students. As for retention, grants have helped pay for students’ tuition costs, but I think more could be done to help supply students with the right tools to join the industry.
KS: I believe that the number of qualified entry level students results from a lack of understanding and training of the school’s recruiters. The recruiters visit with interested parties and their parents to talk about automotive, diesel, aircraft and other options, but if they don’t know enough to talk intelligibly about collision, they can’t sell it. At UTI, they don’t understand collision and everything that’s involved in this field; they still view it as the dirty, dusty place of 25 years ago, filled with minimal technology and low pay. The former recruitment manager understood collision and did an exceptional job explaining the industry’s opportunities to his recruiters, but that was nearly two decades ago. The manager who took over for him didn’t understand the industry, so he didn’t promote it to his team. He recently retired, and I’m hopeful that his replacement will be receptive to learning about the advantages available in collision repair – job placement, salary, technology and benefits have all seen major improvements over the past 20 years, and our recruiters need to embrace this knowledge so they can sell the collision program when they’re talking to students and parents. Since they don’t know how to sell collision as a career path, they just don’t bother attempting it. Until there is a commitment to training recruiters to recruit for the collision industry, we will continue the path we are on.
JS: One of our biggest challenges is probably just the fact that most of this generation doesn’t actually know anything about this industry. Most young people aren’t necessarily working with their hands, but I also don’t know that we’re really reaching people like we could, though we’re trying to get out there and recruit as much as possible. We’re working to develop a social media outreach for our department, and our instructors are attending different events and visiting secondary schools to recruit. Actually, we’re trying to go anywhere to talk to kids and adults, including military bases and different work programs because we’ll take grownups too! Shops have always called, requesting help, but they’re getting a lot more desperate now. We want to help fill the workforce shortage, but we’re facing a ton of challenges ourselves.
JW: I attend and give presentations to the students of all of our feeder schools to help counselors be better prepared to direct students into my
Thank you for your response to my question about the mandatory appraisal bill at the Capitol. It is my understanding that there is a Senate Bill SB 554 sponsored by Senator Hughes and a House Bill sponsored by Representative Clardy. Can you give me and the readers an update on how these bills are progressing? Has there been a hearing on the bills?
Thank you for your question and response. On April 18, I testified along with others on SB 554 and HB 1437 at the Capitol. Both bills would require insurance carriers in Texas to have a mandatory Right to Appraisal in their personal auto policies. During the Senate bill hearing, lawmakers asked several good questions. During the House bill hearing, there were no questions. I have testified several times before the House Insurance Committee on the importance of the Right to Appraisal and the surrounding safety issues when this policy right is limited, reduced or removed.
Additionally, the Texas Department of Insurance (in their 2022 Biennial Report) and the Office of Public Insurance Council (in their report to the 88th Texas Legislature) have expressed their concerns on the insurer or insured’s Right to Appraisal in the case of loss disputes. I can only hope at this point that lawmakers have taken note and paid close attention to how important this issue is.
As I have stressed many times in this forum, it is important to know and understand that when a dispute arises between the insurer, the policyholder and the repair professional, the Right to Appraisal is the proper relief to see to it that the vehicle is returned safely and properly back to its pre-loss condition to the best of one’s human ability. The Fair Appraisal Bill SB 554 and HB 1437 requires insurers to include the Appraisal Clause in all auto policies, both for total loss and repair claims. This is very important because, as I have pointed out previously, there already is one auto policy in Texas that excludes appraisal rights for repair claims. The limiting or removal of the Right to Appraisal in motor vehicle auto policies would be the nail in the coffin for safe roadways for us all.
As I have repeatedly stated in my writings and testimony, it is my emphatic position that the Right to Appraisal is the guardrail for indemnification. Without this critical loss dispute resolution
process becoming mandatory in the insurance code, the insurance carriers and their defense team will be like beavers to running water to step up already ongoing efforts to reduce or remove this contractual economic relief for the insured.
The spirit of the Appraisal Clause is to resolve loss disputes fairly and to do so in a timely and cost-effective manner. The invoking of the Appraisal Clause removes inexperienced and biased carrier appraisers and claims handlers from the process, undermining their management’s many tricks to undervalue the loss settlement and under-indemnify the insured. Through the Appraisal Clause, loss disputes can be resolved relatively quickly, economically, equitably and amicably by unbiased, experienced, independent third-party appraisers as opposed to more costly and time-consuming methods, such as mediation, arbitration and litigation.
In today’s world regarding motor vehicle insurance policies, frequent changes in claim management and claim handling policies and non-standardized GAP Addendums, we have found it is always in the best interest of the insured or claimant to have their proposed insurance settlement reviewed by an expert before accepting. There is never an upfront fee for Auto Claim Specialists to review a motor vehicle claim or proposed settlement and give their professional opinion as to the fairness of the offer.
Please call me should you have any questions relating to the policy or covered loss. We have most insurance policies in our library. Always keep in mind a safe repair is a quality repair, and quality equates to value. I thank you for your question and look forward to any follow-up questions that may arise.
Sincerely,
Robert L. McDorman TXADo you believe that this industry needs to do a better job of educating today’s youth and the general public about the multitude of amazing job opportunities available in the collision industry? You’re not the only one! That’s why the Collision Repair Education Foundation (CREF), BASF and KTL Restorations (Danville, VA) teamed up on Operative Talent, a project focused on attracting future talent to the industry by educating the population as a whole on the ample opportunities, success stories and segments within the collision repair industry.
“We continually discuss the need for more technicians, estimators and other industry professionals, but instead of just thinking about it and talking about it, we’re going to put some actions behind it which will involve everybody in this industry,” shares Brandon Eckenrode, managing director of CREF.
The industry’s technician shortage is a multi-faceted problem, so Operative Talent will take a multipronged approach to solving the dilemma with the overall goal of addressing the industry’s aging workforce by highlighting collision repair as a viable career path. This approach includes engaging students through a vehicle rebuild, which will then be raffled off to raise funds to create public awareness campaigns promoting the industry. Ambitious, yes…but definitely doable with everyone’s help!
Since Operative Talent was first announced at the end of 2021, KTL Restorations has been rebuilding a 1969 Camaro, named “Talent,” but with over three dozen partners from across the country joining together to increase the reach of this impressive initiative, it’s important to realize that this initiative is about a lot more than simply raising funds through raffle ticket sales and generating industry involvement through sponsorship opportunities – Operative Talent also offers an unique opportunity for the next generation of collision repair enthusiasts to get some hands-on exposure to rebuilding a vehicle!
To encourage young people’s interest in this field, students between the ages of 16-23 are invited to participate in the rebuild by applying online. By participating in rebuilding the classic car and learning a little more about the different career paths available in this diverse industry during the process, students will
gain experience and exposure to the awesome opportunities the automotive industry offers…and hopefully uncover a passion that can turn into a fruitful and fulfilling career!
“Cars are cool, and working on them is a lot of fun,” shares Crystal Lawrance of KTL Restorations. “Unfortunately, today’s students don’t often have the chance to get hands-on exposure to this type of work because so many schools have closed their trade programs. We want to showcase the awesome opportunities this industry offers – whether you’re interested in pursuing an automotive career or just want to learn something new, Operative Talent offers a unique experience you’re not able to get anywhere else.”
“We’re passionate about the next generation, but few show enthusiasm for automotive careers because they know nothing about it. No one shows them what’s available…Kids are told they must obtain a four-year degree (and accrue college debt) to be successful, yet the trades offer great opportunities for good-paying jobs,” Lawrance adds. “It’s time to spotlight the many different jobs that exist and drive that knowledge to schools to help educate the future generation about industry careers and to help us find quality talent. If we don’t bridge that gap, there will be no one to repair vehicles or create custom cars in the future.”
“Talent” will ultimately be raffled off to raise funds to finance a national public service campaign showcasing collision career opportunities and generating awareness about the industry as well as a public-facing website to educate the public about the variety of career paths in the industry.
“Our industry has a bad reputation as this greasy, dirty place, but those days are long gone,” Lawrance insists. “It takes many different people with various talents to make up today’s automotive industry. Sure, body work and painting still happens in the back of the shop, but up front, we have estimators, accountants and a whole production team. Suppliers have many roles to fill; just look at BASF! They need chemists to create the beautiful colors we spray on these cars. And we even have positions for social media managers, industry journalists and more!
“We don’t do a great job of educating students or the general
public about all the options that are out there,” she continues. “Just because you don’t want to work in a shop, that doesn’t mean there’s not a place for you if you love cars. Automotive professionals don’t all fit in the same box these days…and that’s just the way we like it! So, we’re hoping to introduce students to some of the different ways they might fit in, whether they’re already planning to enter this field or maybe they just want to explore their options.”
The automotive and collision industries have spent years griping about the lack of qualified help entering the workforce, and it’s time to DO something about it!
“We need everyone’s support…from donated parts to raffle ticket sales, we need the entire industry to get behind this effort – to get behind these students, our industry’s future – and help make Operative Talent a success,” Eckenrode urges.
Those interested in educating the public about the multitude of opportunities available within the automotive industry can purchase raffle tickets now at bit.ly/Talent-raffle. And in addition to supporting trade school education, you’ll even get a chance to win the custom-built Camaro these kids will be working on at KTL!
The initiatives funded by the Operative Talent fundraiser will help showcase the industry and its career opportunities to the general public, which will benefit the entire industry. The success of the project relies on the entire industry getting involved and championing the endeavor.
“Operative Talent is amazing,” BASF’s Tina Nelles praises the project. “Attracting new talent is important to our company
and the entire collision repair industry. We’ve dedicated efforts to helping by offering internships, increasing scholarships and supporting schools, but the key piece that’s always neglected is outside perception of our industry…We need people talking about this industry in the right ways! By promoting collision repair careers through the website and the PSA campaign, we can ensure that students, as well as their parents, teachers and guidance counselors, understand the variety of opportunities that exist within this industry.”
“This is a full industry effort,” Eckenrode stresses. “And each of you can help determine the success of this operative by getting involved to make Operative Talent the best it can be – by raising funds and donating your time and efforts, we can showcase this industry and ensure it has a bright future!”
And Lawrance hopes that Operative Talent can continue highlighting the industry on a broader scale in the years to come. “We’re talking to different shops around the country, and so many people believe in this project…I hope to see it grow and expand to offer students opportunities in different markets. How many kids can we attract if we just welcome them into this industry in a fun way? How many share the same passion that we do but need help discovering it? This is just the beginning,” she promises.
To support the industry’s future by purchasing raffle tickets, participating in the rebuild as a student or by donating parts, visit OperativeTalent.com. TXA
continued from pg. 4
operation that estimating systems don’t include and even provided links to substantiate what he was saying.
Then, he didn’t keep that information to himself; he sent it to tons of other shop owners to help them get paid for that same procedure. I can personally tell y’all that I’ll be using that information at my shop…that email brought something to my attention that I didn’t know before, something that can help me in my daily operations. And that’s exactly what ABAT is all about: shops sharing information and communicating with one another to make all of us better and stronger.
So, keep sending those emails and sharing what you’ve learned with one another. Keep participating in the association because that’s where the value of membership comes from. Educating one another is a product of who we are as a group, and there’s no reason to be shy. We can all learn from each other, and that’s why ABAT was created in the first place. Let’s continue coming together to strengthen each other and our industry, to ensure that all shops in Texas are doing the right thing for our customers and keeping our roadways safe for all of us.
continued from pg. 17
program, but my course’s biggest challenge is location since I presently teach in an area where most students attend a four-year university after graduation. Last year, we had nine graduates; two of them are in the collision industry, and two attend a post-secondary trade school (such as UTI). Four went on to college, one works in another industry, and one is unknown. This year, I already know that two students are going to university because they received football scholarships. It’s hard to get students to pursue industry careers because they have other plans, even though they enjoy taking the course. Even success stories don’t always make it to the collision field. One of my students loved collision and planned to be an estimator, but while pursuing a post-secondary education, he got involved with Cummins and now works for them, making six figures to drive a truck.
The industry needs more fresh talent, and although there are many ways to attract more students to collision programs, instructors cannot do it alone; they need the industry’s involvement to demonstrate the need for these young technicians and to correct the general public’s perception of this field. Tune into Texas Automotive for Part 2 of this story in an upcoming edition to learn what YOU can do to make a difference in the future of vo-tech education! TXA
burl@burlscollision.com
If you’re not already an ABAT member, now’s the time! This industry is changing too fast for any individual to keep up with everything on their own. We’re stronger together, and we need you to both add to our collective knowledge and to learn what you don’t know you don’t know. Join now at abat.us/join-abat-new-member
Buying a paint booth is a huge investment, and there are many factors to carefully consider before selecting one Will the booth work well in a region where there’s a ton of humidity and with drastic changes in the weather? How long do you think the booth will last and will it require a lot of maintenance? Will your painters be comfortable using it ever y day and finally, will the company making the booth provide solid training and reliable customer ser vice?
To answer these questions before acquiring two Chronotech spray booths and a prep deck from USI ITALIA back in 2004, Collision Center Manager Kevin McIllveen at Russell & Smith Body Shop in Houston, TX spent six months studying the market He was looking for the best booths that matched his needs to use in a brand-new 36,000 sq ft facility that the company built from the ground up
Mcllveen, age 56, entered the industr y more than three decades ago as an estimator and has worked for Russell & Smith Body Shop since 1993 His goal with his new spray booths was to improve the efficiencies in his paint department and to accommodate his production, he said, while simultaneously saving time and energy if possible.
The vetting process was arduous but worth it in the end "We did our research so that we could make an educated decision," he said "I went to NACE two years in a row and talked to literally ever yone and asked a lot of questions We knew that this was going to be a ver y significant investment, so we took the time to perform our due diligence to cover all our bases. We invested in their prep stations as well, which was another good decision, because my guys can work so much faster and effectively with five different places where we can spray We put a curtain up in the prep booth that provides us two additional spaces that are heated and properly ventilated So, when we are really jammed, we can handle the workload and maintain our cycle time without interrupting or slowing down our production "
After using them for a ver y short time, Mcllveen could clearly see that his Chronotechs were more than capable as they quickly became a centerpiece in his new, high-end, modern shop
"We have four paint teams here, consisting of a painter and a painter’s helper and we consistently log approximately 600-700 paint hours weekly,” he said “We switched to waterborne paint when we opened this facility because we want to provide a healthier climate for our employees and the community as a whole ”
Why was Mcllveen able to improve his numbers by simply adding two USI booths? “In the end, it all comes down to their airflow because we never need blowers or additional air to cure these vehicles The fans in these Chronotechs are exceptional because they feature variable speeds, so we can switch depending on the parameters of each job Our painters are producing an impressive product day after day, so these booths are saving us both time and money We paint an average of 400 cars ever y month, so
we push these booths and they never let us down ”
Any issues that Russell & Smith Body Shop have encountered with their USI ITALIA booths have been rare and far between But Mcllveen feels good knowing that if called upon, the company will respond and find solutions promptly “If you do your scheduled maintenance and keep ever ything clean, these booths will last you 30 years and maybe even longer The issues that we have encountered with the Chronotechs have been minor and quickly solved, which is impressive when you think that we have been using these booths daily for the last 16 years I tell people that these booths will be here long after I’ve retired!”
After training provided by USI ITALIA, Mcllveen’s painters were able to start spraying after one day, he said "The Chronotechs are designed to work with waterborne paint, which makes it easier for our painters to do their work After a ver y short time, all of our guys were comfortable and the results were consistently exceptional ”
Mcllveen is also impressed by the Chronotech's sturdy construction and durability "Some booths are just a box, but these are wellbuilt," he said. “I know, because I've seen them all and there isn't anything like a USI ITALIA booth "
His career in collision repair industr y has been a great experience and products like his USI ITALIA spray booths and prep station are a part of that, he said “We haven’t had to furlough anybody here and that’s because we value our people and, in the end, our Chronotechs are part of the team ”
At Classic Chevrolet, we aim to offer an easy buying experience on wholesale priced Chevrolet performance parts. We are one of the largest sellers of powertrain parts in the U.S. and have been recognized by General Motors as #1 in total parts sales for the 6th consecutive year. With competitive price matching and free shipping on orders $250+, we want our customers to come back for our quality parts and service.