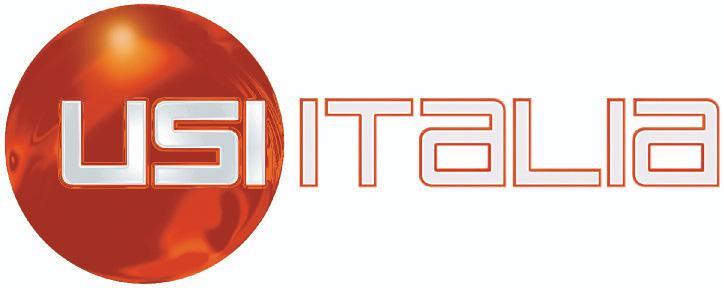
10 minute read
USI
Russell & Smith Logging Big Paint Hours with USI Booths & Prep Station

Buying a paint booth is a huge investment, and there are many factors to carefully consider before selecting one. Will the booth work well in a region where there’s a ton of humidity and with drastic changes in the weather? How long do you think the booth will last and will it require a lot of maintenance? Will your painters be comfortable using it every day and finally, will the company making the booth provide solid training and reliable customer service?
To answer these questions before acquiring two Chronotech spray booths and a prep deck from USI ITALIA back in 2004, Collision Center Manager Kevin McIllveen at Russell & Smith Body Shop in Houston, TX spent six months studying the market. He was looking for the best booths that matched his needs to use in a brand-new 36,000 sq. ft. facility that the company built from the ground up.
Mcllveen, age 56, entered the industry more than three decades ago as an estimator and has worked for Russell & Smith Body Shop since 1993. His goal with his new spray booths was to improve the efficiencies in his paint department and to accommodate his production, he said, while simultaneously saving time and energy if possible.
The vetting process was arduous but worth it in the end. "We did our research so that we could make an educated decision, " he said. "I went to NACE two years in a row and talked to literally everyone and asked a lot of questions. We knew that this was going to be a very significant investment, so we took the time to perform our due diligence to cover all our bases. We invested in their prep stations as well, which was another good decision, because my guys can work so much faster and effectively with five different places where we can spray. We put a curtain up in the prep booth that provides us two additional spaces that are heated and properly ventilated. So, when we are really jammed, we can handle the workload and maintain our cycle time without interrupting or slowing down our production. "
After using them for a very short time, Mcllveen could clearly see that his Chronotechs were more than capable as they quickly became a centerpiece in his new, high-end, modern shop. "We have four paint teams here, consisting of a painter and a painter’s helper and we consistently log approximately 600-700 paint hours weekly, ” he said. “We switched to waterborne paint when we opened this facility because we want to provide a healthier climate for our employees and the community as a whole. ”
Why was Mcllveen able to improve his numbers by simply adding two USI booths? “In the end, it all comes down to their airflow because we never need blowers or additional air to cure these vehicles. The fans in these Chronotechs are exceptional because they feature variable speeds, so we can switch depending on the parameters of each job. Our painters are producing an impressive product day after day, so these booths are saving us both time and money. We paint an average of 400 cars every month, so we push these booths and they never let us down. ”
Any issues that Russell & Smith Body Shop have encountered with their USI ITALIA booths have been rare and far between. But Mcllveen feels good knowing that if called upon, the company will respond and find solutions promptly. “If you do your scheduled maintenance and keep everything clean, these booths will last you 30 years and maybe even longer. The issues that we have encountered with the Chronotechs have been minor and quickly solved, which is impressive when you think that we have been using these booths daily for the last 16 years. I tell people that these booths will be here long after I’ve retired!” After training provided by USI ITALIA, Mcllveen’s painters were able to start spraying after one day, he said. "The Chronotechs are designed to work with waterborne paint, which makes it easier for our painters to do their work. After a very short time, all of our guys were comfortable and the results were consistently exceptional. ” Mcllveen is also impressed by the Chronotech's sturdy construction and durability. "Some booths are just a box, but these are wellbuilt, " he said. “I know, because I've seen them all and there isn't anything like a USI ITALIA booth. "
His career in collision repair industry has been a great experience and products like his USI ITALIA spray booths and prep station are a part of that, he said. “We haven’t had to furlough anybody here and that’s because we value our people and, in the end, our Chronotechs are part of the team. ”
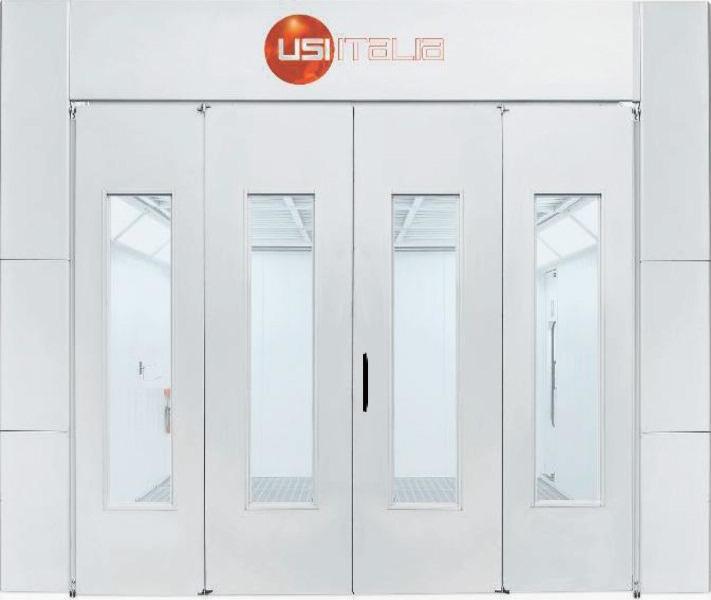
Back to Business: Consumer Forms
Jill Tuggle
ABAT Executive Director
AAs I sit and write this message, I think to myself, “I can’t believe this year is almost over” - and I’m sure it goes without saying that we are all hopeful that next year will be different, that all our hopes for 2021 will come to be in 2022. But maybe that’s a message opener for next month.
For now, the party is over, and it’s back to business. The “party” being the 2021 Texas Auto Body Trade Show, of course. And the planning and execution of such a big event has the tendency to put all of our usual business on hold for a couple months.
Remember those consumer forms? It’s time to get back in the saddle and send them in again. The 87th legislative session is over for HB 1131, but much of the real work comes during the interim. Our consumer safety bills have made continued progress each session, and we must keep up the momentum. We are almost halfway to our goal of 1,000 forms submitted.
I have heard so many times that we stand no chance fighting against the insurance and LKQ lobby, but that couldn’t be more untrue! What is true is that if we neglect to put in the work, then they will surely devour us. I have written about this before, but it deserves repeating: NOTHING is more powerful than an outcry from the consumer.
If you are not familiar with the form, it is a simple checklist to be completed by your customers if they face the common challenges brought on by the insurance companies in the repair process. In the case that they are not fully indemnified, suffer unnecessary delays or if their total loss was undervalued or abandoned, that’s when you would utilize this form. Additionally, it is a great opportunity to have the conversations that must often be had when a customer drops their vehicle off: “Your insurance company may not be willing to reimburse
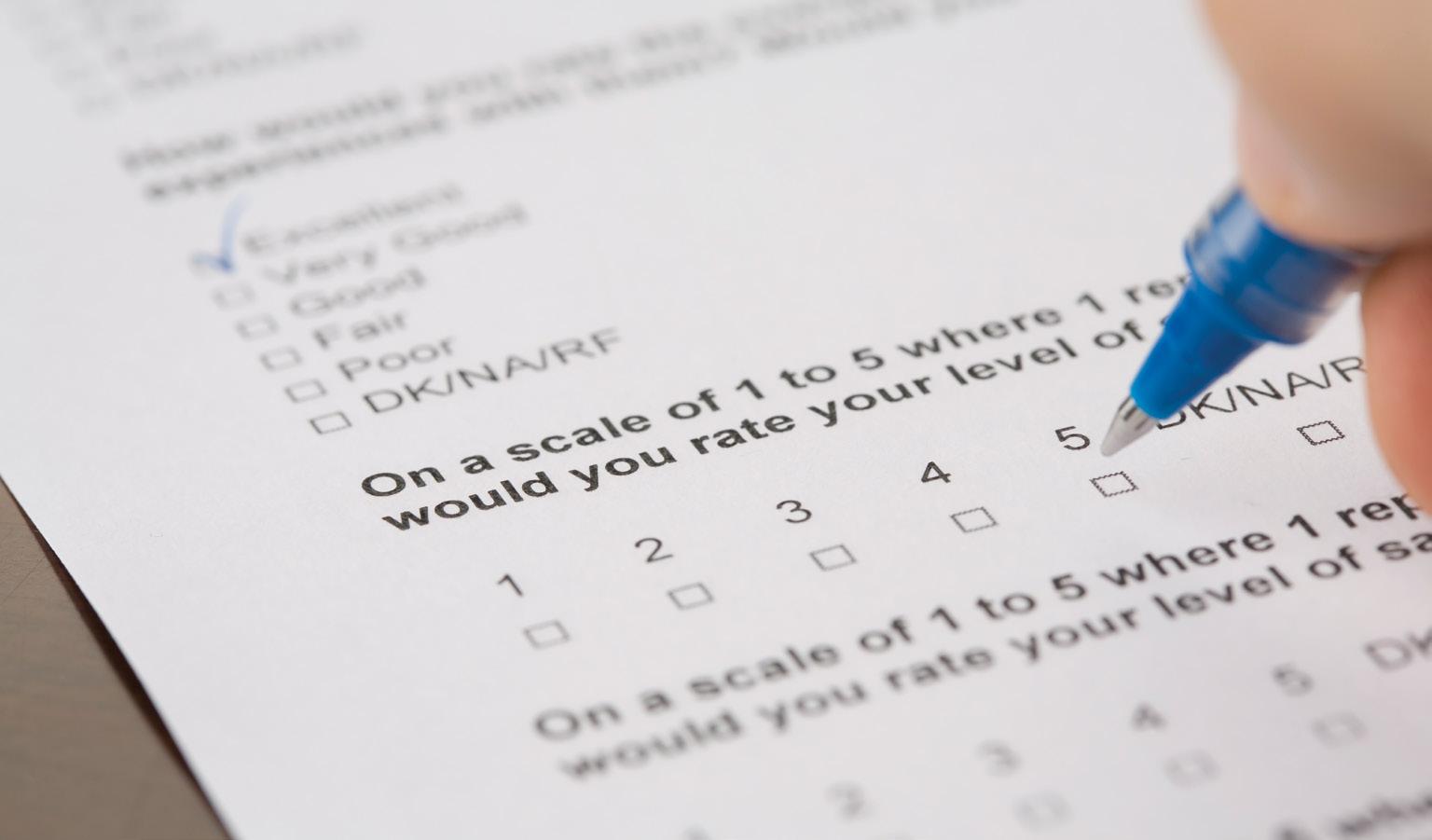
you for all necessary parts or procedures to safely and properly repair your car, and you may have to come out of pocket to return your vehicle to its preloss condition.” These forms are filled out at the end of the repair and sent to me so I can file the form and send it to your local legislators to make them aware of the daily struggles you face while trying to put Texas drivers back in safe cars.
The importance of each one of you getting involved in this initiative cannot be stressed enough - we must cover
ALL 150 districts in the Texas House
of Representatives. From those of you in El Paso to Beaumont, Dalhart to Padre - and EVERYONE in between - we need you! Just 10 forms could make the difference in getting this legislation passed and changing your business forever. Can you imagine the day you are collecting for all manufacturerrequired procedures? Getting paid your posted Labor Rate? Not hearing “We don’t pay for that” on a daily basis? It’s just a few forms away from becoming reality, but we need to be ready before the next session, which will begin in just 15 short months.
Please contact us to get a copy of our most recent form and be a part of making some big changes in Texas!

Excited for This New Adventure!
Chasidy Rae Sisk
Editor
II’m ecstatic to greet y’all as the new managing editor of Texas Automotive!
For those of you who don’t yet know me, I first started writing about collision repair in 2010 and quickly found this industry to be filled with some of the warmest, most caring individuals I’ve ever encountered. Despite my complete lack of knowledge about anything related to cars (beyond how to make them stop and go), the folks I’ve met have always been willing to share their insights and help me understand what’s what – beginning with my first interview when I timidly asked a shop manager, “What’s a DRP?”
Over the years, I’ve learned a lot, yet I realize that I still know next to nothing when it comes to the complexity of modern vehicles. When friends express their awe that little ol’ me writes about cars, I never hesitate to explain:
“I just know a lot of really smart people.”
Although I’ve only been working at Thomas Greco Publishing for a couple months, I’m fortunate enough to have met some really great people, starting with Burl Richards in 2014 when ABAT was founded.
Over the years, I’ve received invaluable information and feedback from others, such as Jill Tuggle, John Kopriva, Larry Cernosek, Chad Kiffe, Eric McKenzie and so many others. The list of awesome collision repair professionals is bigger in Texas too! Thank you all for graciously tolerating my incessant requests for information…and for being prepared to be bombarded with even more questions in the future.
I look forward to expanding that list of industry professionals in my Texas network – and hopefully those I call friends – as I get the opportunity to meet more ABAT members and industry leaders. I appreciate your knowledge, talent and hard work more than I can articulate.
One of my favorite things about this industry, besides the people, is how multi-faceted and diverse it truly is and continues to become as technology advances. Hear me out; while I know those advances are a pain in your you-know-what, it provides limitless possibilities to explore unique ideas, discover innovative processes and garner new experiences.
Because to me, new thoughts and experiences make life so much sweeter. In the short time since I joined the team at Thomas Greco Publishing, I’ve already enjoyed several new adventures: Driving a golf cart (the same day that I stepped onto my first golf course), walking around a trade show with co-workers and visiting new places. By the time this edition is mailed, I’ll be in Las Vegas, attending the 2021 SEMA Show, which will be my first rendezvous with that renowned event, as well as my first opportunity to meet many of you in person after years of talking only by phone or email.
I’m honored that Tom Greco hired me and grateful for the faith that he, Alicia, Joel, Alana, Donna and Joe (the whole TGP team) have placed in me. I know that I have some BIG shoes to fill – and although my feet are undoubtedly smaller than Joel’s, I look forward to the challenge.
I’m also proud to have such an awesome opportunity to continue writing for this wonderful industry and the amazing professionals that comprise it. Each of you does your best every single day to ensure the cars you repair are safe because you care about the people behind the wheel. Likewise, I care about the people reading this magazine and will strive to bring you the most useful information possible to help you continue keeping our roads, our families and our neighbors safer.
At the end of the day, Texas Automotive is YOUR magazine, so please never hesitate to reach out to me with topic suggestions to help ensure that we’re providing the information you actually want to know.
Thank you to everyone who has embraced and welcomed me as I embark upon this new adventure. I look forward to continuing to provide you with the high-quality content that you expect from this magazine. I’m so excited to see what the future holds for all of us, and I hope you are, too! TXA