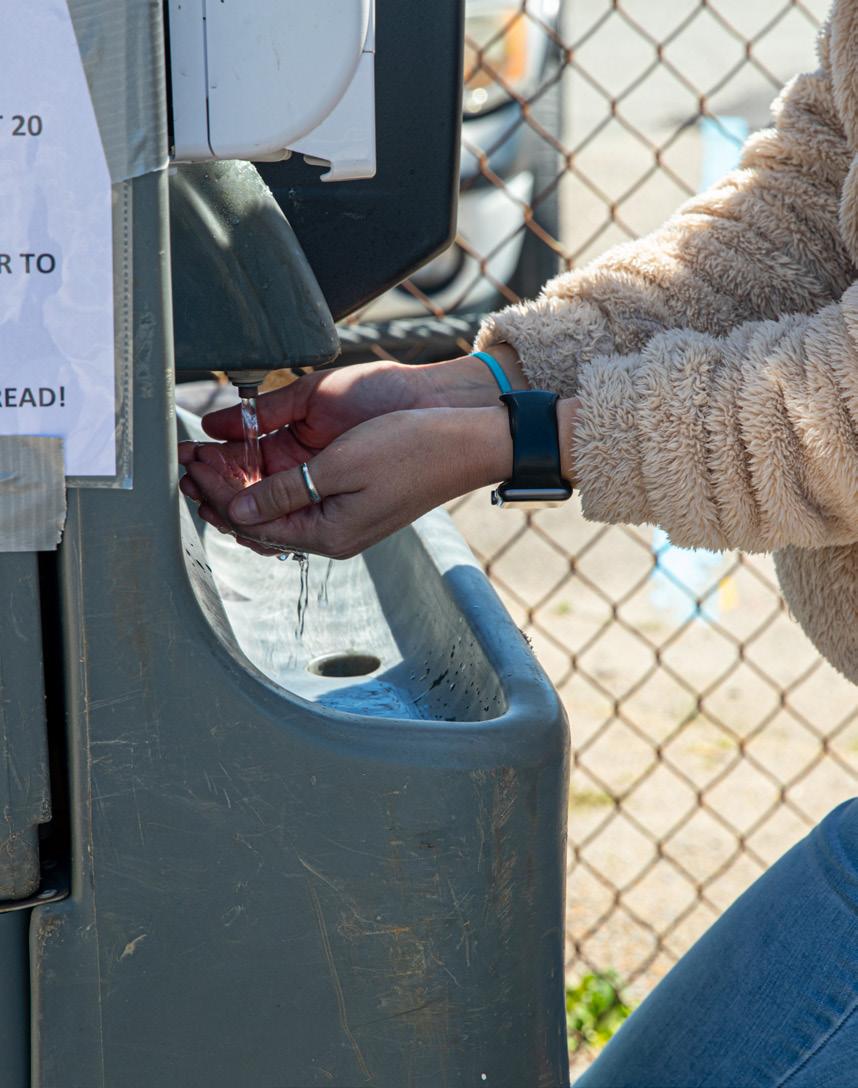
6 minute read
NATIONAL SAFETY MONTH
NATIONAL SAFETY MONTH: HOW AMERICA'S SHIPYARD HAS PROTECTED THE WORKFORCE DURING COVID-19
STORY BY MICHAEL BRAYSHAW • LEAD PUBLIC AFFAIRS SPECIALIST I PHOTOS BY DANNY DEANGELIS • NNSY PHOTOGRAPHER
Advertisement
Observing National Safety Month at Norfolk Naval Shipyard (NNSY) is usually devoted to highlighting important efforts like electrical safety and fall protection. This June, the health and safety issue of greatest workforce concern is minimizing the spread of coronavirus 2019 (COVID-19).
Since COVID-19 impacts began at NNSY in March, shipyard leadership across all departments worked to swiftly brainstorm innovative ways to both conduct work and attain—or in many cases, make--vital supplies and equipment. New processes like enhanced screening at the shipyard gates and physical distancing during work evolutions, along with equipment like handwashing stations and face masks, have all helped NNSY minimize the spread while maximizing the mission.
In one of the most visible and immediately beneficial measures, NNSY began enhanced screening procedures April 22 for installation entry, with personnel taking temperatures and asking questions to ensure employees are not exhibiting any symptoms or at increased risk for having COVID-19. NNSY was the first installation in the region and first of the four public shipyards to conduct temperature checks at its gates. Improvements were already made to the process within a matter of days, both for employees and to assist supervisors in the event personnel are denied access. In addition to NNSY implementing a daily self-screening website created by its Nuclear Corporate Training Initiatives Division (Code 2360), the Duty Office began providing employees real-time gate traffic updates on their phones via AtHoc. The Turn Around Hotline was implemented May 1 for shipyard supervisors to call if they have questions when one of their employees is denied access to NNSY due to a screening problem.
Per guidance from the Centers of Disease Control and Prevention, handwashing is more effective than using hand sanitizer for preventing COVID-19, which prompted the shipyard attaining and installing handwashing stations in early April. Operated via foot pump, these stations were placed in 18 locations around the shipyard including all major docks and servicing piers. Technicians service the stations several times per week to ensure they are fully supplied and operational. Shipyard personnel were also provided additional time at lunch to practice thorough handwashing and hygiene.
When faced with the challenge of ordering cleaning supplies and sanitizer early in the response, NNSY’s Supply Department coordinated with NNSY’s Safety, Health and Environmental Department (Code 106), Defense Logistics Agency (DLA) and Mid-Atlantic Regional Materials Test Laboratory (Code 134) in assembling cleaning kits and making sanitizer from scratch using the World Health Organization (WHO) recipe. To increase accessibility, the Supply Department also established refilling stations for hand sanitizers and disinfectant sprays in convenient locations throughout the shipyard. These supplies are used on a frequent basis thanks in part to NNSY designating several cleaning times throughout the workday.
Further bolstering workforce safety and health, employees were issued multiple facemasks in April to change out and launder as needed. A coordinated effort between NNSY’s Sail Loft, Insulation Shop and teleworking employees produced more than 40,000 of these cloth face masks to distribute across the workforce. Personnel are required to wear them if physical distancing is not maintained while on the installation. In addition, personnel are required to wear them in several areas, including onboard submarines and at the NNSY Branch Medical Clinic.
While members across all levels of the workforce have learned much in recent weeks about preventing spread and what actions to take in certain situations, questions still come up. On this front, the shipyard’s Code 106 has been assisting supervisors with the COVID-19 desk guide, providing helpful guidance on engineering and administrative controls in addition to safe work practices and information on how to obtain face mask and cleaning supplies. Code 106 has also been conducting ongoing safety surveillances across the shipyard to identify workspaces and common areas where personnel are not practicing effective physical distancing or wearing the appropriate face mask.
“Per our C.O.R.E. Ownership value, we are each responsible for our attitude, behavior, decisions and all their positive and negative consequences,” said Shipyard Commander Captain Kai Torkelson. “That very much applies to our COVID-19 response where we are each responsible for making smart decisions to protect ourselves and our co-workers. And as important as our larger efforts like enhanced screening are, preventing spread is also on each of us as individuals by wearing face masks, thorough handwashing, not touching our faces, frequently cleaning surfaces, and maintaining sufficient distancing. These practices take a daily commitment on our part, and we must keep up our dedication to minimizing the spread in America’s Shipyard.”
He added, “Your safety, security, health and well-being are my top priority. During this challenging time, shipyard leadership is continuing to do everything in its power to ensure a safe work environment, protecting the safety and health of our coworkers, ship’s force, all those within Norfolk Naval Shipyard.”
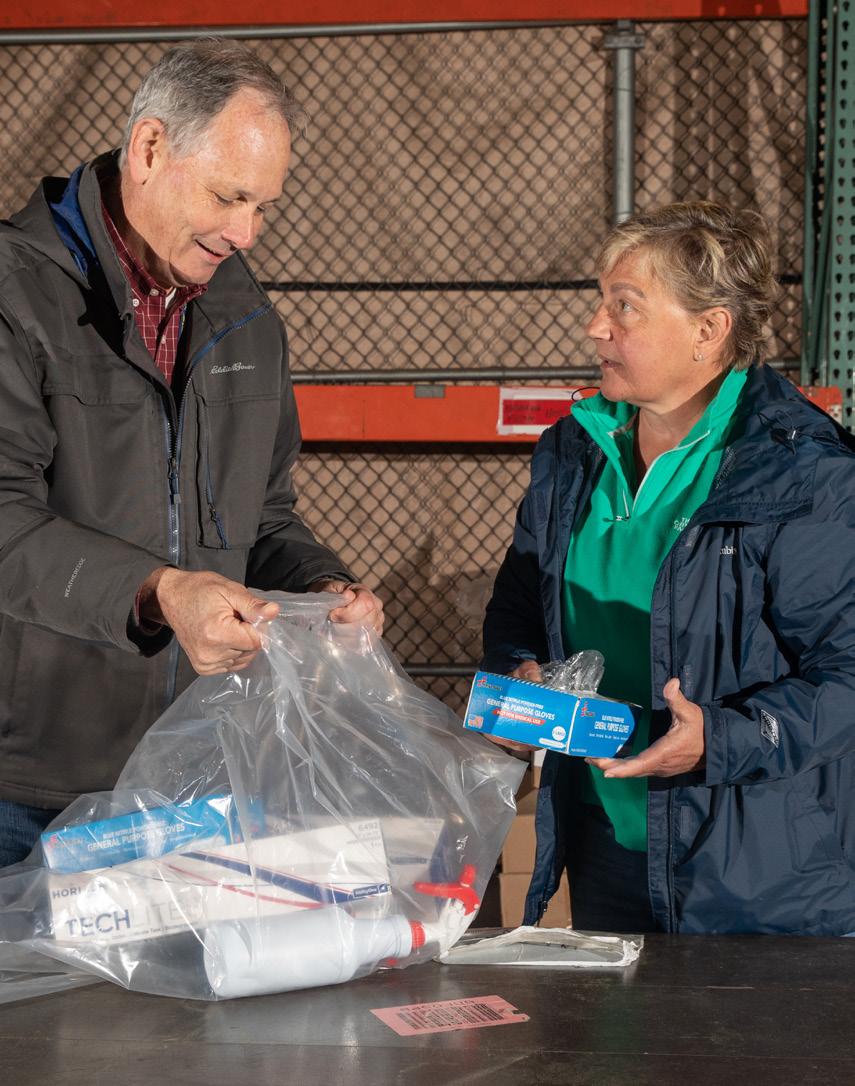

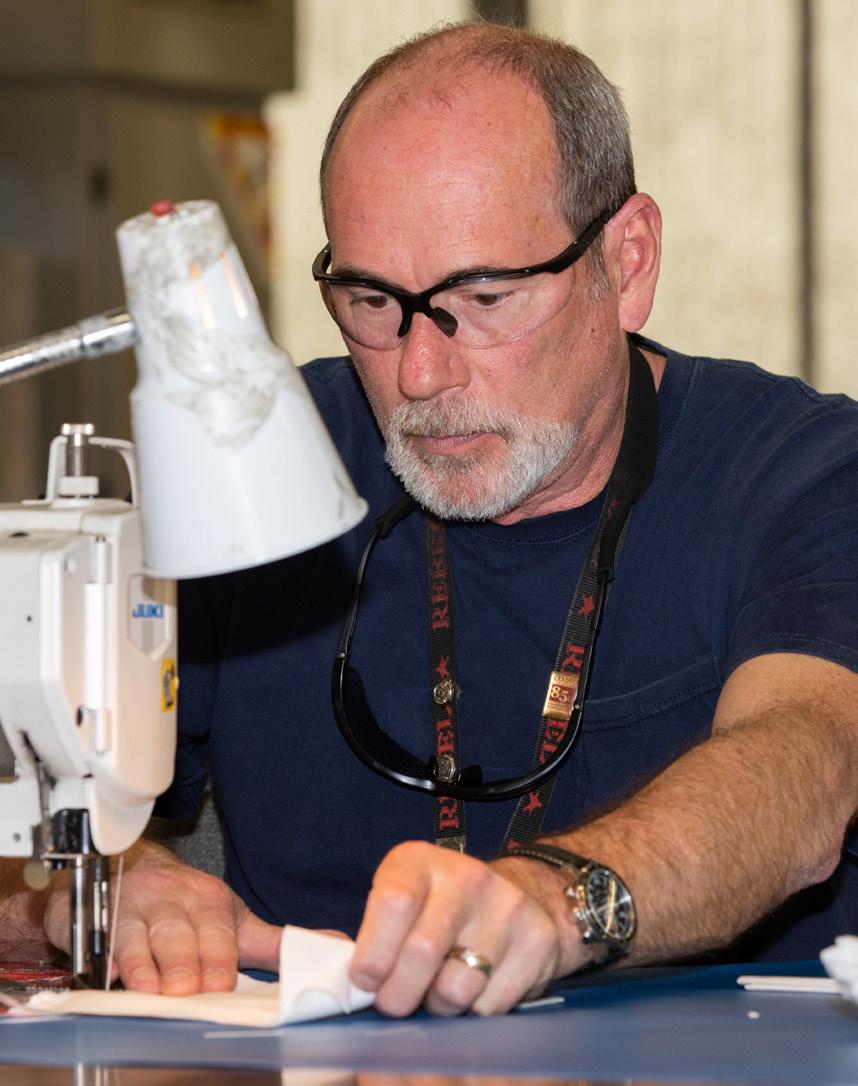
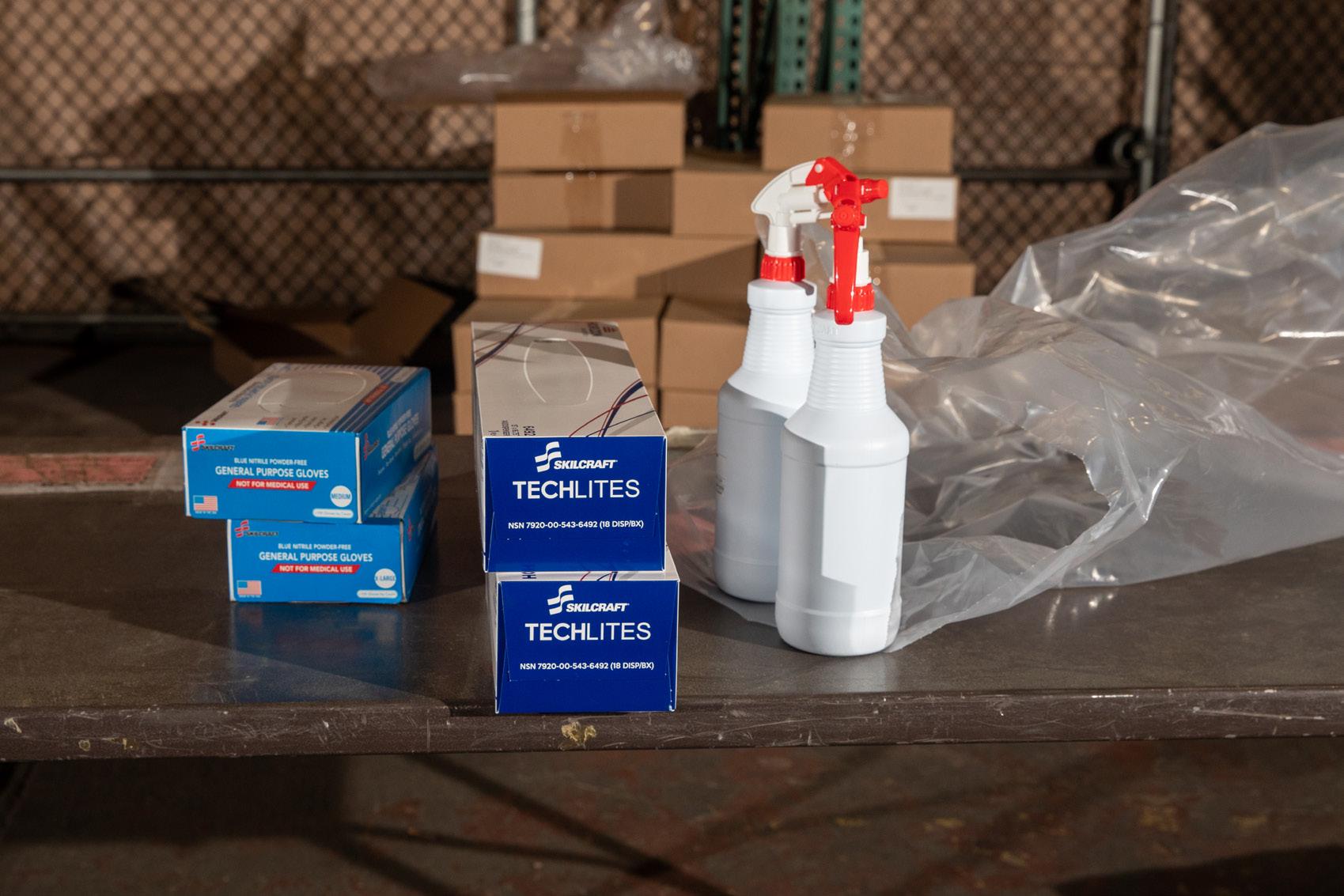
From its infancy as a construction site for our World War II carriers to currently hosting the USS George H.W. Bush (CVN 77), over eight decades of service the Navy’s sole carrier dry dock on the East Coast has proven its value to the Fleet time and again. Related to that anniversary, on June 3 we will mark 75 years since the USS Lake Champlain (CV-39) was commissioned. As the second of three carriers built in America’s Shipyard during World War II, Lake Champlain wasn’t used in battle during World War II, but it was utilized in several other interesting ways during its 20-plus years of service. You can read about this fascinating history in the article on page 20.
I wanted to update everyone on the progress being made on NNSY’s Production Training Facility. It’s been almost a year since we held the official groundbreaking for this facility that will consolidate our shipyard training in a convenient, modernized facility befitting our high-performing teams at America’s Shipyard. I was just on site recently and saw some of the great progress being made. Now that foundational work is complete, we’re starting to see the building take shape, with the first structures such as the stair and elevator towers rising out of the ground. We’ve got 25 trucks worth of steel beams and girders being delivered in the next few weeks, with installation beginning late this month. This multistory, multifaceted facility is one of our biggest initiatives yet as part of NAVSEA’s Shipyard Infrastructure Optimization Plan (SIOP), and it’s exciting to see America’s Shipyard being rebuilt for its next 250 years of service.
Summer officially begins this month, and we have a busy one on deck while working to complete USS Wyoming (SSBN 742), undocking USS George H.W. Bush (CVN 77) and USS San Francisco (SSN 711), and completing our portion of the S8G overhaul at NPTU Ballston Spa, New York, all while starting work on USS Harry S Truman (CVN 75). Thank you for all you continue to do as we collectively minimize the spread and maximize the mission. Committed to our C.O.R.E.!
Co's Comments Continued
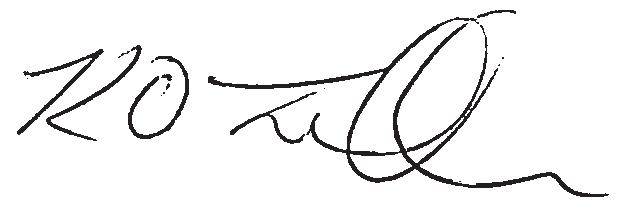