SERVICE TO THE FLEET
REMEMBERING USS THRESHER (SSN 593) 60 YEARS LATER
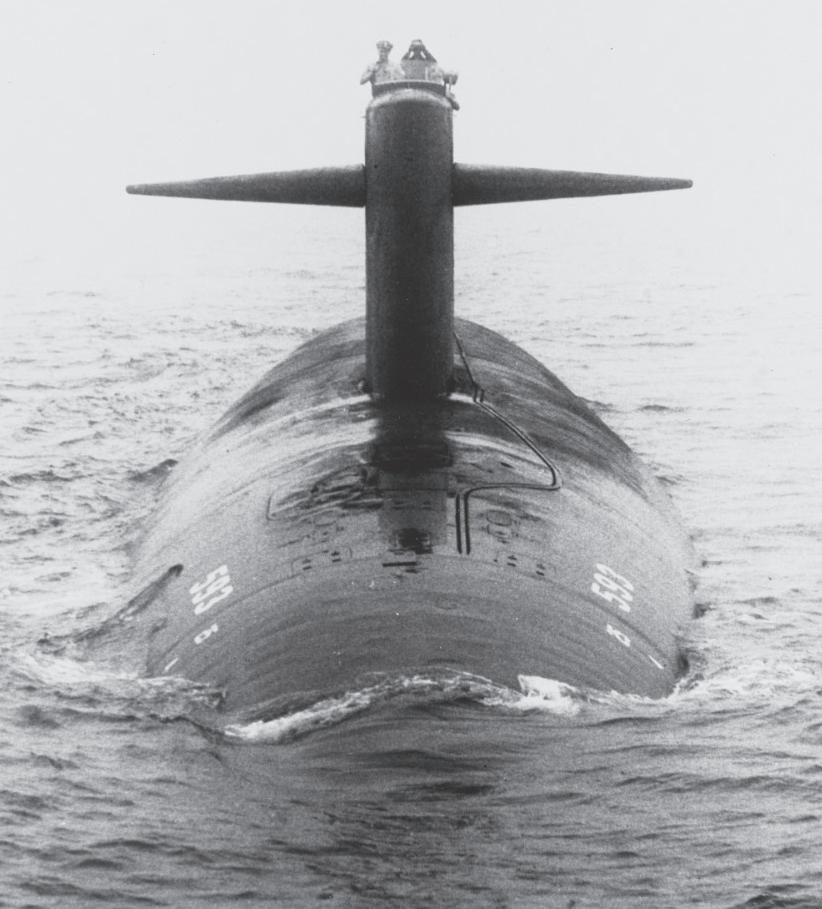
REMEMBERING USS THRESHER (SSN 593) 60 YEARS LATER
3 SHIPYARD TRIVIA
4 FROM THE COMMANDER: EVALUATION LEARNING: MOVING OUT WITH PERSPECTIVE AND PRECISION!
5 NORFOLK NAVAL SHIPYARD LEADERSHIP GEMBAS HELP RESOLVE ISSUES THROUGH WORKFORCE ENGAGEMENT
6 SHIPYARD INSIDER
8 NORFOLK NAVAL SHIPYARD REORGANIZES BLDG. 1505 INTO SUB HUB USING NAVAL SUSTAINMENT SYSTEM -SHIPYARDS
10 USS THRESHER: A LOSS. A LEGACY.
12 TAKE THE LEAD AND INSPIRE TO READ: NORFOLK NAVAL SHIPYARD VOLUNTEERS PARTICIPATE IN ANNUAL READ ACROSS AMERICA DAY 14 NNSY LGBTQ+ ERG RECOGNIZES EMPLOYEES MAKING A DIFFERENCE IN SHIPYARD'S CULTURE IN MONTHLY CONFERENCE ROOM NAMING CEREMONY
20 SHIPYARD SPOTLIGHT GRAPHIC BY COLE FRASER
21 EXPERT TRADESPERSONS GRAPHIC BY JUSTIN DEBRAUX
22 OUR YARD HISTORY: BUILDERS OF PIER 4
24 NNSY FAMILY DAYPREREGISTER BY APR. 21
26 MONTH OF THE MILITARY CHILD
27 CFRAM FRAUD SCHEME AWARENESS: ORGANIZATIONAL CONFLICT OF INTEREST
32 NATIONAL WELDING MONTH GRAPHIC BY COLE FRASER 12
SHIPYARD COMMANDER
Capt. Dianna Wolfson
EXECUTIVE OFFICER
Capt. Randy Reid
COMMAND MASTER CHIEF
CMDCM Stephanie Canteen
EXECUTIVE DIRECTOR (CODE 1100)
Brad Crosby
DEPUTY PUBLIC AFFAIRS OFFICER
Michael Brayshaw
SERVICE TO THE FLEET EDITOR/ PRODUCER
Kristi Britt
PUBLIC AFFAIRS STAFF
Susanne Greene, Troy Miller, Erica
Miranda, Marcus Robbins, Curtis Steward
VISUAL INFORMATION DIRECTOR
Jason Scarborough
VISUAL INFORMATION STAFF
Marisa Berkey, Danny DeAngelis, Justin
Debraux, Cole Fraser, Lorenzo Raines, Shelby West
EMAIL THE PUBLIC AFFAIRS OFFICE nnsy_pao@us.navy.mil
EMPLOYEE INFORMATION HOTLINE
(757) 396-9551
FRAUD, WASTE & ABUSE HOTLINE
(757) 396-7971
SERVICE TO THE FLEET is a Department of Defense publication and is authorized for members of the DoD. Contents of Service to the Fleet are not necessarily the official views of, or endorsed by, the U.S. Government, the DoD, or Norfolk Naval Shipyard. Service to the Fleet is published monthly. Submissions are due on the 10th of each month. The public affairs staff reserves the right to edit submissions for content and brevity.
LIKE US ON FACEBOOK www.facebook.com/NorfolkNavalShipyard1
FOLLOW US ON TWITTER www.twitter.com/NNSYNews
WATCH VIDEOS ON YOUTUBE www.youtube.com/NNSYBroadcast
FOLLOW US ON INSTAGRAM @norfolknavalshipyard
READ STTF ONLINE
www.issuu.com/nnsy
We exist to fix ships and we have been doing just that for 255 years at this location. There has always been a relationship between the private builder yards and Uncle Sam’s Navy yards as they support a ship from new construction into mission and then provide repairs and alterations over its lifetime.This early circa 1910s postcard of the battleship Virginia (BB 13) shows that it was built at Newport News and depicts its physical sizes as constructed.
The location shown in this image is at our Berth 2. Viewing from left to right you see ex-Building 41 as a bending slab, Building 9 serving as a Blacksmith Shop, the 1880 Trophy Park flagpole waving proudly, the dome of ex-Building 1 as the main entrance is still in place, Building 74 serving as general storage, the exwireless telegraph pole, Building 51 serving then as general storage and ex-Building 53 as a latrine.
So, if you have a naval ship to berth for repairs you always need up-to-date facilities to support same. This postcard is a visual testament to some bygone facilities that are no more as our mission changed over time to the present and earlier facilities needed to be replaced.
Hello, America’s Shipyard! Last month we held our annual Naval Reactors (NAVSEA 08) evaluation which is critical each year for NNSY’s authorization to conduct nuclear work. The evaluation scope is broad, and by design focuses primarily on areas needing improvement. The week culminated in an outbrief with Naval Reactors Four-Star, Admiral Caldwell, where he and his evaluation team offered some great perspective on specific findings and overall trends. The key takeaway was clear, Norfolk Naval Shipyard has made great progress in the past couple of years! And we are needed now, more than ever, to be at our very best delivering on our commitments.
The evaluation team noted project performance and leadership cohesion have greatly improved, and our Strategic Framework has a stronger foundation and is focused on the right areas. We have placed significant emphasis on our people and Building a Better Culture; creating a genuine and lasting environment where people want to come to work to do their very best and feel valued. Last year, evaluators commented they observed a “vector change up” from prior years meaning we were moving in the right direction. We are at an “inflection point,” which is a time of significant change in an organization. As our Senior Executive, Mr. Jeremy Largey said, it’s now about “turning good discussions into good actions.”
Good actions hinge on effective people development and empowerment. And now is the time to accelerate these actions! Now is the time to move out
with urgent and deliberate development (which is also an important aspect of our people feeling valued). To see the force multiplication, we have to unleash the power of our people and ensure they know it’s okay to fail. Our discussions with the NAVSEA 08 team reinforced that perspective. By the way, that is one of my favorite words: perspective – the capacity to view things in their true relative importance. It is the way people see the world. It comes from their personal point of view and is shaped by life experiences, values and even what they may be thinking that day. I believe that one can only truly embrace the root cause of an issue if they see another person’s perspective. It helps us to understand situations from other positions, experiences, and viewpoints.
During the evaluation, shipyard teammates shared they have ideas for improvement, but don’t feel empowered to voice or try them. We need each of you relentlessly driving for improvement. Your ideas and investment are needed to maintain the world’s strongest Navy. So if there are barriers to unleashing your ideas, as leaders it’s vital for us to get after those. Going into the evaluation, I spoke about “embracing the red,” addressing the areas head-on where we are not meeting our standards and goals. That involves candidly asking ourselves what is preventing us from excelling as individuals, teams, and leaders. We need to build our trust and relationships across working levels from one group to another so we can operate as ONE TEAM, being able to have the challenging conversations, growing and developing together with a clear sense of achieving our ONE MISSION.
As I consider our evaluation learning, there’s a part of our NNSY Command Philosophy that I keep coming back to: “we foster an engaged, productive and inclusive environment promoting workforce development and ensuring a sense of urgency and resolve at all levels of the workforce.” This workforce development must be a continual deliberate effort, from the first days of New Employee Orientation, to continuous training and development, to having a fully competent and committed
individual driving delivery on the deckplate. While every problem presents a learning opportunity to prevent it in the future, for sustained success we must be empowered to readily solve problems – which requires specificity. The goal is to develop actionable plans that are executed at the cognizant level with precision. That involves going to where the problem occurs, collaborating with all stakeholders, and moving beyond the problem’s symptoms to focus on fixing it—the Get Better.
In closing, in my last all hands I mentioned the audit was an opportunity. The NAVSEA 08 team shared similar thoughts at week’s end. Our overall takeaway should be positive and empowering. An inflection point is an exciting place to be at in our journey. We are getting better every day, and will be even better tomorrow. Because of our willingness to not only identify but embrace the red, we can develop solutions, and build a learning team continuously improving in the mission of relentlessly chasing best ever performance in serving our Nation’s warships. Thank you for all you do! It all matters for our shipyard, our Navy, our Nation.
You may have recently heard the word “Gemba” in shipyard communications. So what the heck is a Gemba? Gemba simply means observing work in action, often to provide senior leaders a better understanding of how things get accomplished and provide any help that may be needed.
Norfolk Naval Shipyard (NNSY) senior leaders have been increasing Gembas throughout the shipyard as part of an ongoing commitment to the workforce, ensuring standards are upheld and barriers are removed. Department heads, group superintendents, and project superintendents are all taking part in this significant effort across all work sites to include shipyard detachments.
“Gembas are important to understand how work is performed, any associated working conditions, and to understand if we can incorporate improvements right at the source,” said Shipyard Commander Captain Dianna Wolfson. “Gembas can also include observing working level meetings, and sometimes even having one-on-one conversations. Our Gembas are not just about finding problems; they can also be about recognizing excellence in action. That’s also a major part of why we Gemba.”
In taking Gemba engagements to the next level, participating leaders provide a follow-up written report on what was seen, what was learned, and what action was taken. This effort will help NNSY continue to self-identify, self-assess and self-correct as ONE TEAM, leveraging the Navy’s Get Real, Get Better behaviors.
“Direct observation and engagement matters,” said Wolfson. “Ultimately there is no substitute for eyes on target. I have always enjoyed my own Gembas—that’s often the best part of my week, to meet and engage with those who do the heavy lifting and are driving results for our Navy and Nation every day.”
Gembas may lead to something that a division head or project leader can go immediately resolve, such as a quick-fix in safety or cleanliness. Other Gembas may support morale and quality of work life, helping to identify facility issues with HVAC and restrooms.
In one specific example, NNSY’s Naval Sustainment System— Shipyards (NSS-SY) Champion Brittney Wright shared how Gembas have helped with the transformation of Building 1505 as a “sub hub” to improve work flow of the established work-execution cells for each tenant production shop. “Having senior leaders walk the space has not only brought attention to the need to improve our work space standards, the needed space and tooling to work efficiently, but has also driven accountability to the line organization owners to continue the progression of their transformation with urgency,” said Wright. “We also identified the work-execution cells could not be optimized without simultaneously improving the quality of life spaces—specifically improving the 1505 mezzanine break area and creating a break room/internet café to prevent eating and drinking in the same industrial work spaces.”
“We have been doing lots of Gembas on USS Toledo (SSN 769) and 1505, focusing on the mechanics and what we can do for them, and helping them get better every day,” added Joe Singer, Code 900F Facilities Manager.
“Actions speak louder than words, and Gembas will show how we’re listening to our employees today, and every day,” said Wolfson. “We recognize our projects, shops, departments, and satellite locations must all support each other and be invested in our mutual success. Because as ONE TEAM, we must look through the lens of our workforce and make sure we don’t give up the shift in meeting our ONE MISSION. Together, we got this!”
Congratulations to the latest graduates of Norfolk Naval Shipyard First Level Supervisor High Velocity (1LS HV) Training! These fourteen individuals received their certificate of completion and hard hats Mar. 8 during the 1LS HV Graduation Ceremony. (Photo by Shelby West, NNSY Photographer)
Most government employees are generally permitted to engage in political activities while they are off duty and not on government property or in a government vehicle. But, remember that there are two activities that government employees are not permitted to do at any time: (1) Running for, or holding, partisan political office and (2) soliciting, or accepting/receiving, political contributions. Remember the Navy employee in Hawaii who was prosecuted by the U.S. Office of Special Counsel (OSC) for violating that second rule. He was the chairman of a local political party and created social media pages to solicit political contributions for his party. He also sent several emails to solicit contributions for his party and its candidates. The employee retired when he was faced with disciplinary action. But, he still had to pay a civil fine and was debarred from future federal employment for three years as part of a settlement agreement. If you have any questions, please contact the Shipyard Office of Counsel (Code 107) at 757-396-8625.
The NNSY Waypoints Implementation Team hosts a Town Hall at 9 a.m. on MSTeams to provide the latest news and answer questions regarding Waypoints. To join NNSY Waypoints Town Hall, use the Team Code 70v8txt to join directly. In addition, those who enroll or close-out training for employees in your code or shop can also participate in one of two monthly workshops from the Waypoints Implemention Team. To register for a session, log into https://don.csod.com. On the Learner Home page, type in 00-DON Waypoints Scheduled Sessions/ Manage Rosters Role. The sessions will appear for you to request. Contact NNSYWaypointsHelp@us.navy.mil for any assistance regarding these announcements.
Have an idea for a story to feature in an upcoming Service to the Fleet?
Want to recognize one of your fellow shipyarders as the next Shipyard Spotlight? Want us to advertise an upcoming event? Email the NNSY Public Affairs Office today at NNSY_PAO@us.navy.mil.
Continuous Evaluation (CE) is part of the major overhaul of the security clearance process known as “Trusted Workforce” and is an integral part of the Continuous Vetting (CV) process. Traditional periodic reviews have been replaced with a CV model, which conducts automated record checks that pull data from criminal, terrorism, and financial databases, as well as public records, at any time during an individual’s period of eligibility. Investigations are only conducted if there is a “trigger” event. (Note: Some Special Access Programs will continue to conduct Periodic Reinvestigations.)
All individuals who are eligible to access classified information or hold a sensitive position are subject to CE. This includes federal civilian employees, contractors, and military personnel.
The information is acquired from automated records checks to include checks of commercial databases, U.S. Government databases, and other information lawfully available to security officials at any time during the period of eligibility. This is the same information that is reviewed during national security background investigations and follows the same privacy protections.
Those subject to CE authorize the U.S. Government to perform Continuous Evaluation checks by signing the Standard Form (SF) 86, or equivalent form, for release of information and submission to either an initial or periodic background investigation. Individuals will complete their SF 56 every five years to be re-enrolled in the CE Program - this also ensures that the most up to date release forms are signed and on file for all employees.
What’s the difference between being uncomfortable and being stressed? Is there actually a difference? Sometimes, being uncomfortable causes stress. So, let take a quick moment to define the two and focus on ways to overcome each challenge separately and together. Uncomfortable is “causing or feeling unease or awkwardness”. From last month, stress is defined as “any type of change that causes physical, emotional, or psychological strain.” We’re uncomfortable quite a bit in life but when we’re uncomfortable are we always stressed? If so, is the result of this stress good or bad? When being uncomfortable is coupled with stress what are some causes? Perhaps, I’m uncomfortable having this conversation about an employee being late because I haven’t been given the tools to help with this conversation so I’m stressed. Or, maybe you’re uncomfortable because you come into work and have to deal with improper behavior, so you’re stressed. The first example is an opportunity for you to grow as a supervisor. Perhaps you request to be enrolled in “Crucial Conversations” to get the tools to help you have the conversation. The second is an example of bad stress. While there is an opportunity for you to grow by speaking out against the behavior, this stress probably affects your ability to effectively work, feel safe, and feel community. This chronic stress is something that goes beyond being uncomfortable—it could begin to impact your psychological well-being. In both of these situations, as was stated last month, take time to breathe. After you calm yourself, take the next step in getting the help that is needed—for the first example request to be enrolled in the course and for the second report the improper behaviors. If they’ve already been reported, follow-up and elevate until resolution.
Norfolk Naval Shipyard is planning the 2023 Earth Day Celebration with participation from several local environmental support groups to help promote sustainability and stewardship of the environment. We would like everyone to participate on April 27, 2023 from 10 a.m. to 1 p.m. in front of NNSY’s Building 1500 where we will have vendors and hand out one free tree to attendees. Trees include Crape Myrtles, Red Maples, Eastern White Pines, Virginia Pines, and Yellow Poplars while supplies last!
In honor of the annual celebration of Flag Day, the Norfolk Naval Shipyard Veteran Employee Readiness Group (VET-ERG) is collecting old or worn U.S. flags to be donated to Sturtevant Funeral Home now until June 9th. As part of the Retire Your Flag Program, the flags will be draped over fallen veterans at the time of cremation. For more information or to schedule a donation, contact Nicholas Boyle at nicholas.e.boyle.civ@us.navy.mil. Learn more about the Retire Your Flag Program at https://www.sturtevantfuneralhome.com/retire-your-flag/retire-your-flag.
Norfolk Naval Shipyard (NNSY) aims to bring lasting change to the way we do business for our nation’s fleet – aiming to Get Real – Get Better to ensure our workforce is provided the tools they need to succeed. A recent transformation project, assisted by Naval Sustainment System – Shipyards (NSS-SY), has taken shape at the north end’s Building 1505 – redefining the area as the Sub Hub of the North End of the shipyard, ensuring productive workflow and establishing areas to best serve the employees of America’s Shipyard.
“The NSS-SY Champions Office has been supporting the USS Toledo (SSN 769) project team and has been working to rebaseline the schedule,” said NSS-SY Champion for NNSY Brittney Wright. “In order to meet these commitments, we needed to also look at how to rebaseline behaviors and identify what areas needed assistance to help ensure employees had what they needed to complete work. We noted that we needed to rebuild zone manager and general foremen relationships, identify and reduce work stoppages, and improve material control.”
The team took the lead in developing plans for improvement in a multi-phased project to redevelop Building 1505 to best support the projects of America’s Shipyard, working with Shop 38 as their starting point for identifying where they needed improvements and what could be done to support workflow overall.
“This effort truly has been decades in the making, with our
team having generations of tooling, knowledge and more built up into our sections,” said Shop 38 General Foremen Eric Chops Clarke. “As we continued to have new projects coming through, we found that more and more material was getting piled up, wasn’t being stored properly, and overall wasn’t where it should be to ensure our team was setup to do their best every day. We needed to take a deep dive on how we did business and where we could improve. With the support of leadership, we were able to get real within our space and outline exactly what we needed to do and how to get it done. In addition, we had additional support from shops and codes around the shipyard – so we embraced the mantra of ONE MISSION – ONE TEAM to create a space that was more efficient in the way we do business for our employees. It’s bringing positive change for all of us.”
“The organization is better overall within our spaces and doesn’t feel like we’re competing with our other teammates within the building for where we can store material or where we can conduct work,” said Outside Machinist Kevin Barrecki. “With the newest setup, everything feels more open and provides everyone a better workflow overall.”
With the Outside Machine Shop (Shop 38) as the flagship for this new initiative, more shops stepped up to the plate and completed workflow analysis and seeing where they can reestablish their spaces for work execution. The building itself transformed into a hub of work execution cells for each tenant
production shop, with reestablished material standards and improved work spaces to support their work flow. Material that supported work outside of the two-week window was removed from the work execution cells. Material envelopes were adjusted to support material needed for the jobs scheduled within the six-week window (SRV). In addition, the layout of the building was adjusted as needed to best support the shops and maximize workflow overall. Supervisory workspaces within these cells were also moved to other locations within the building to provide quiet areas to conduct administrative business.
Within Phase 1, the floor opened up into a functional workspace, built for efficiency and cleanliness for Code 920, and Shops 11, 17, 38, 51, 56, 56N, and 57N and NN. Project provided muster areas were developed in trailers to ensure the teams have the space needed to prep and plan for the start of shift without taking away from the space needed to conduct their daily workload.
Phase 2 has officially begun within Building 1505, the champions team taking on more of an oversight role for the transformation while shops within take on the role of functionality and sustainability. “We’re here for the team and ready to assist in breaking down any barriers that stand in their way,” said Wright. “It’s all about making a positive change and impact on the way we do business.”
USS Thresher (SSN 593) at sea on July 24, 1961.
On April 9, 1963, USS Thresher (SSN 593), the lead nuclearpowered attack submarine of her class, sailed from Kittery, Maine, to approximately 220 miles east of Massachusetts to conduct deep-diving tests. She carried 129 men, including her crew and several shipyard personnel.
After a rendezvous with Penguin-class submarine rescue ship USS Skylark (ASR 20), Thresher conducted trials throughout the day, before submerging overnight. The following morning, after reestablishing comms with Skylark, Thresher commenced deep-dive trials.
She dove slowly in a circular pattern beneath Skylark, maintaining communications, and stopping every 100 feet to check system integrity. But as Thresher approached her test depth, Skylark received an alarming, partial message. “…Minor difficulties. Have positive up-angle. Attempting to blow…” Another unclear communique was received which included a number. No further messages came through, and the Navy would eventually determine that Thresher and her crew were lost on April 10, 1963, once the ship descended below crush depth due to uncontrolled flooding, and imploded under the devastating pressures of the ocean.
Built to hunt and destroy hostile enemy subs, Thresher was the quietest and fastest submarine of her time. Equipped with the most advanced weapons and detection systems available, no one would have predicted that the boat could have possibly suffered such a fate. Being the first nuclear submarine lost at sea and the deadliest submarine incident in U.S. history, the submarine community, and indeed the entire nation, were devastated by the loss.
“When you lose a modern-day nuclear submarine and all the lives on board that ship, that’s going to greatly impact the submarine force,” said Rear Adm. Scott Pappano, program executive officer, Strategic Submarines (PEO SSBN). “That was very much an eye-opener for the submarine community; a devastating accident that forced us to really take a hard look at what we were doing and how we were designing, building and sustaining submarines going forward. The loss of the Thresher brought about a change in how we do submarine design, to minimize the possibility of this ever happening again.”
After thorough review of the loss of Thresher, the Navy established the Submarine Safety Program (SUBSAFE), to provide maximum reasonable assurance that submarine hulls will maintain watertight integrity, and that the boats can recover from unanticipated flooding. This rigorous quality control program oversees any and all systems that are exposed to seawater or would be critical to recovering the boat in the event of flooding.
SUBSAFE certification occurs throughout the areas of design, material, fabrication, and testing. Each step requires records collection, review, and approval. The records must also be stored for the entire life of the submarine. Material traceability
starts at original manufacturing and continues up to the point of installation and through final certification. This tracking is so thorough that it includes records of source materials (such as which quarry a metal was mined from) and material manipulation processes (such as smelting).
“The SUBSAFE program was established and fundamentally changed and improved our processes,” said Rear Adm. Jon Rucker, program executive officer, Attack Submarines (PEO SSN). “These processes - material, construction, maintenance, testing, certification, training, etc. - have been and remain vital to ensuring the safe continued operation of our submarines.”
Prior to the inception of SUBSAFE, from the onset of WWI up until 1963, the U.S. lost 16 submarines in non-combat related incidents. Since adapting SUBSAFE procedures the U.S. Navy has only lost one submarine, USS Scorpion (SSN 589). However, Scorpion was not SUBSAFE-certified and sank for unknown reasons in 1968.
“We maintain rigorous safety and technical proficiency in everything we apply to these boats,” Pappano added. “These are key tenets of the submarine program and make us who we are and define how we deal with our submarines and making sure that we can go be effective assets for the Navy and never repeat the loss of the Thresher.”
The SUBSAFE program, which falls under Naval Sea Systems Command (NAVSEA), has been so successful at preventing a repeat of the Thresher incident, that other agencies have looked to SUBSAFE’s example for guidance. Following the loss of the Space Shuttle Columbia, the Columbia Accident Investigation Board identified SUBSAFE as one of only three "successful safety programs and practices that could be models for NASA." Several subject-matter expert exchanges were held to help NASA identify ways their program could be improved to prevent future catastrophic casualties.
The loss of Thresher, and the lost lives of the 129 men on board, will forever remain a tragic moment in naval history, but that sacrifice led to the creation of a program dedicated to ensuring that the U.S. Navy never again experiences such a catastrophe.
“It is important to understand the details about this event including what happened, the root causes, the actions we took, and the program and processes we have in place today to ensure safe operation of our submarines,” Rucker stressed. “We must never forget what happened and we must maintain continued vigilance in our efforts to ensure the SUBSAFE program, as well as the other special emphasis programs, are maintained to the highest standards. It is a culture that takes continued effort and attention as we owe that to the personnel that operate our submarines every day.”
Norfolk Naval Shipyard (NNSY) partnered with Churchland Elementary School in Portsmouth, Virginia for the annual Read Across America Day March 2, an observance on the school day closest to the anniversary of Dr. Seuss' birthday.
This annual celebration is part of a year-long program focused on motivating children and teens to read. The program is led by the National Education Association (NEA), with its focus on building a nation of readers one story at a time. This year marked the fifth year NNSY has participated within the local community, and the first time returning to schools since 2019 due to the COVID-19 pandemic.
Churchland Elementary School Principal Dr. Jamill Jones said, “Read Across America celebrates diversity, inclusivity, the enjoyment and the pleasure of reading.”
“We believe that reading will encourage students to be successful in life and instill firm foundations for their future in everything that they do,” said Misty Conkel, Parent and Family Engagement Liaison for Churchland Elementary School. “Today is a great way to celebrate and bring the community together for the importance of reading.”
Among NNSY’s volunteers was Business and Strategic Planning Office (Code 1200) Management Analyst Janel Hofler who’s also a member of the shipyard’s Science, Technology, Engineering, Arts, and Mathematics (STEAM) Employee Resource Group (ERG). “I think it’s important to give back to
the community and help the kids develop and feel confident about themselves and their education,” she said. “Today’s event was a huge success. I think the kids were very engaged with us as an organization, came with a lot of enthusiasm and questions. I enjoyed working with my fourth grade class and it was a lot of fun.”
“Any time you can emphasize reading to the next generation, I think we should take the time to do that and have that impact on the community – especially as members of America’s Shipyard with the knowledge, skills, and abilities that we can use to help inspire the next generation,” said Supervisory Physical Science Technician and NNSY volunteer Eric Staten.
“Thank you so much for the support from NNSY – we really appreciate your partnership,” said Conkel. “My heart is community – I truly believe that we are better together and we all have something to offer. Having everyone come together for a common cause makes me so happy.”
“As Dr. Seuss once said, ‘The more that you read, the more things you will know. The more that you learn, the more places you'll go.’ Today was a step for these students’ futures, providing us all a moment to come together and celebrate the joys of reading and working together,” said Public Affairs Training Coordinator and STEAM-ERG Lead Erica Miranda. “We at NNSY are happy we could support this great cause today and look forward to continuing our outreach efforts
PHOTO BY DANNY DEANGELIS • NNSY PHOTOGRAPHERwithin our community. We aid the students as they learn and grow, inspiring them to follow their paths of choice. So as Dr. Seuss whimsically shared in Oh, The Places You’ll Go! ‘You’re off to great places! Today is your day! Your mountain is waiting, so…get on your way!’”
To learn more about the STEAM-ERG or to learn about future outreach opportunities, please email erica.s.miranda2.civ@ us.navy.mil. To learn more about Read Across America Day, visit https://www.nea.org/professional-excellence/studentengagement/read-across-america.
Norfolk Naval Shipyard’s (NNSY) Lesbian, Gay, Bisexual, Transgender, Queer + (LGBTQ+) Employee Resource Group took the lead in the Production Resource Department (Code 900) monthly Conference Room Naming Ceremony Mar. 9, identifying two individuals who’s work at the shipyard has advanced the efforts in building a better culture for all. Those recognized were LGBTQ+ Member and Former Chairperson Ronisha “Ro” Ford and Diversity, Equity, and Inclusion Accessibility Strategic Team (DEIAST) Member Lamont Ming.
“You are awesome individuals and I truly appreciate the amount of effort you all put in every single day,” said Operations Officer Capt. Lawrence Brandon. “I see you putting in the grind and working to help make change at America’s Shipyard. Your hard work doesn’t go unnoticed. It can be challenging to change the culture and environment for a 10,000-person workplace – but you don’t let that deter you from what you do. It’s true that we can’t directly change a person; however, we can do our part to create an environment where change is possible. That’s what building a better culture is all about.”
Production Resource Officer Capt. Frank Gasperetti added, “When it comes to building a better culture, it takes willingness and courage to step up to the plate and we see that especially in efforts you all are making to ensure our shipyard is a welcoming place for all to function as one team.”
Ford is a founding member of the LGBTQ+ ERG and was the Chairperson of the team until stepping down in late 2022. LGBTQ+ ERG Chairperson Janese Walker said, “Even after stepping down, Ro has continued to be an extremely active ERG member and mentor to our team. With her ever-presence and always willing to lend her support, she understands the value of maintaining a safe and inclusive space for LGBTQ+
employees and serves in any capacity to achieve that. Ro isn’t afraid to have those tough but necessary conversations required to promote inclusion in the workplace and is always willing to share her knowledge and experiences with others.”
Ford said, “This really makes me feel really special and seen to be recognized. I hope we can continue to work together to ensure diversity and inclusion are felt throughout America’s Shipyard.”
Ming, although not an official member of the LGBTQ+ ERG, has played a key role in their mission of creating a safe and equitable workplace for all. Walker said, “Lamont has dedicated several hours in between his formal role as an analyst to meet with stakeholders at all levels and advocate for LGBTQ+ inclusion and recognition as part of the ‘Build a Better Culture’ campaign. Lamont’s impeccable character and farreaching connections have helped build a bridge between our group and senior leadership in order to affect position change here at America’s Shipyard.”
Ming said, “I’m really blown away by this. We’re a family here at America’s Shipyard and it takes all of our commitment to make it the best it can be.”
This initiative began as an effort to recognize employees for their hard work and dedication to America’s Shipyard and building a better culture – with two employees being recognized each month with a plaque and one of the spaces in Bldg. 1500 bearing their name. As new months bring new recipients, each recognized individual will receive their official plaque and photograph. In addition, their photos and recognition will encircle the conference room to ensure their hard work and dedication is recognized for many years to come.
Bravo Zulu (BZ) to our Production Resources (Code 900) personnel supporting NNSY’s recent Production Training Facility ribbon-cutting! Shipyard Commander Capt. Dianna Wolfson recognized and thanked these teammates during the BZ100 ceremony March 1. Personnel from Codes 920, 950 and 970 helped prepare the building for the event, while 900F assisted with getting staging in place, and 990 fabricated ceremonial bunting. “All your efforts were not unnoticed and showed how much it’s the little things that matter,” Wolfson told the team. “Everything you did was so awesome, and really appreciated!”(Photo by Shelby West, NNSY Photographer.)
Bravo Zulu (BZ) to Shop 64 stage builders for supporting NNSY’s recent ribbon-cutting ceremony for the USS Harry S. Truman (CVN 75) living barge, APL-68. Shipyard Commander Capt. Dianna Wolfson recognized and thanked these teammates during the BZ100 ceremony March 1. “Thank you not only for supporting this major event, but what you do for us each and every day!” said Wolfson. (Photo by Shelby West, NNSY Photographer.)
Bravo Zulu (BZ) to our Shop 64 Boat Shop teammates, establishing themselves as subject matter experts in manufacturing blocks to fit cradles on surface craft for the new Rigid Hull Inflatable Boats implemented across the fleet. This particular task requires the Boat Shop’s specialized trade skills and craftsmanship now in demand for naval surface craft in Hampton Roads. Shipyard Commander Capt. Dianna Wolfson recognized and thanked these teammates during the BZ100 ceremony March 1. “Meeting our vision for the Navy also pertains to non-nuclear surface ships,” said Wolfson. “Our number of ships matters. We have to display prominence and being ‘fit to fight,’ so thank you for all you do!” (Photo by Shelby West, NNSY Photographer.)
Bravo Zulu (BZ) to our Code 740 team, a division of NNSY Lifting and Handling, for supporting USS New York (LPD-21) in executing an emergent weight test on a replenishment-at-sea sliding padeye, and coordinating with Mid-Atlantic Regional Maintenance Center (MARMC) on developing a valid weight test procedure for the first time on this vessel class. Code 740 members worked additional hours and through the weekend to support New York’s underway schedule. Shipyard Commander Capt. Dianna Wolfson recognized and thanked these teammates during the BZ100 ceremony March 1. “Saying ‘thank you’ is not only about this effort, but to tell you how much you mean to America’s Shipyard, today and every day,” said Wolfson. (Photo by Shelby West, NNSY Photographer.)
Bravo Zulu to our Lifting and Handling (Code 700) teammates who recently provided emergent crane support at the request of Navy Crane Center, requiring quick mobilization and on-site support with engineering and rigging to remove a damaged crane. Shipyard Commander Capt. Dianna Wolfson recognized and thanked these teammates during the BZ100 ceremony March 1. “Absolutely incredible work and call to action—any crane, anytime, anywhere!” said Wolfson. (Photo by Shelby West, NNSY Photographer.)
Bravo Zulu to our Shop 71 team for great work supporting an emergent shipyard availability, to include working through weekends and holidays. Work ranged from sail blasting, to cleaning, prepping and touching up nearly 30 tanks, the dome, recesses and underwater hull. Shipyard Commander Capt. Dianna Wolfson recognized and thanked these teammates during the BZ100 ceremony March 1. “This was a top priority for us at the shipyard. With maintenance like the tanks finishing ahead of schedule, we would not have been in the position we were in without Shop 71, so thank you!” said Wolfson. (Photo by Shelby West, NNSY Photographer.)
Bravo Zulu to our USS Toledo (SSN 769) welding team for their support on the boat’s Engineered Overhaul. “The artisans we have in our shop do extraordinary work, from hull cults to tank work,” said Jason Wills, Code 926 Group Superintendent. Shipyard Commander Capt. Dianna Wolfson recognized and thanked these teammates during the BZ100 ceremony March 1. (Photo by Shelby West, NNSY Photographer.)
Bravo Zulu to our production building monitors Kevin Campbell, Scott Peters and Jessica Younger, and facility support engineer Jason Legg! These teammates were recognized for their tenacity and commitment in resolving concerns to ensure clean, safe and functional facilities. Shipyard Commander Capt. Dianna Wolfson recognized and thanked these teammates during the BZ100 ceremony March 1. “What you do is a huge undertaking, and thank you so much for taking action to mitigate everything within your controls,” said Wolfson. (Photo by Shelby West, NNSY Photographer.)
Bravo Zulu to our USS John Warner (SSN 785) docking team supporting NNSY’s first Virginia-class Extended Drydocking Selected Restricted Availability! “This was a challenging evolution but due to the dedication and pride in your craft, we were able to safely land her on the blocks and kick off her first major depot maintenance period,” said NNSY Docking Officer LT Josh Hildebrand. Supporting departments and organizations for this ONE TEAM effort included Shops 06DD and 89, Codes 253, 740, 982, Port Ops, MARMC, the Warner project team and Ship’s Force. Shipyard Commander Capt. Dianna Wolfson recognized and thanked these teammates during the BZ100 ceremony March 1. “ONE MISSION, ONE TEAM is not a mantra, it’s a mindset, and it took great partnerships and teammates to make this docking flawless,” said Wolfson. (Photo by Shelby West, NNSY Photographer.)
An untold number of individuals labored day in and day out doing their jobs constructing Uncle Sam’s shipyard facilities for the United States Navy at America’s Shipyard here on the Southern Branch of the Elizabeth River. Their names were never recorded when photographed and are now lost to time. For sure these would have been local men, maybe even related to us who read these words today. Pictures do tell a story, so let us look back 104 years ago this month of April 2023 as Pier 4 was taking shape.
layout of the shipyard, you can see the original Machine Shop, Building 171 to the left and the extreme southern end of the Structural Shop, Building 163.
In the photo above taken looking west, you can see two large pile drivers and their associated cranes swinging concrete sheet pile into an upright position. Well, the next step would be to drive the pile and repeat many times on both sides of an almost 1,000-foot-long structure. It takes a lot of work to build the foundation for a wooden deck relieving platform and earth filled pier such as Pier 4 was. This very pier was later demolished just after the year 2010 to support an even larger new Pier 5A structure which also demolished the 1940s Pier 5 in order to lend wider wetslip spaces on either side to be able to dock two Ford class aircraft carriers at once yet that is for another story. Pier 4 stood proudly for about 90 years total providing service to the fleet. Also, while you are gaining your bearings, remember I just mentioned the first Pier 5 was constructed some 30 years later, located well to the left of the photo above where you see that pine tree on a swampy finger of land, that will become clearer by the final image that features the USS Arizona at Pier 4. For you all who know the
But back to the topic of this story because it is supposed to be about the men that built Pier 4. These two photos provide a rare close-up view of our workmen standing upon each of their pile driver rigs. What loud, tough and dirty work this must have been.
So fast forward to the month of October 1, 1920, as this is how Pier 4 appeared as Wet Slip 3 to its north and Wet Slip 4 to its south were almost complete of final dredging. Also note the old Belt Line Railroad track bridge in the distance has a center swing span, not the high lift of today that we normally see in the raised position.
And finally, a real American icon of a ship, the USS Arizona that received modernization at the Norfolk Navy Yard along with a drastic physical makeover from May 4, 1929, to becoming fully re-commissioned on March 1, 1931. The location of this final the below photo is of course, Pier 4.
These great facilities and piers did not just happen. It took the physical labor of many unknown souls giving an honest day’s hard work for Uncle Sam. The result of their physical efforts is evident both in photographs and the facilities we still use today. Pier 4 most likely outlived most of the men in these pictures but it is important to remember that their efforts supported our naval history and heritage at our shipyard because –"history matters."
The Department of Defense (DoD) celebrates military children during the month of April. There are more than 1.6 million American military children sharing many challenges and unique experiences as a result of their parents' service to the country.
While military members serve around the globe, their ready and resilient children are often with them experiencing new environments and opportunities. Military families move on average every two to three years, impacting military children through changing schools and support networks.
Each year, the DoD joins national, state and local government, schools, military serving organizations, companies and private citizens in celebrating military children and the sacrifices they make. A few children from Norfolk Naval Shipyard – New Gosport Youth Programs recently shared their perspectives on being a military child.
Christopher Cisneros
11 years old; 5th grade
Father: Aviation Boatswain Mate (Fuel)
Chief Rigo Cisnerosa USS Gerald R. Ford (CVN 78)
Mother: Mrs. Connie Cisneros
“My favorite part of being a military child is everytime my dad gets promoted, we get to go celebrate and have lots of fun.”
Iris Motter
10 years old; 4th Grade
Father: Aviation Structural Mechanic –
Hydraulics Paul Motter, Strike Fighter Squadron (VFA) 211
Mother: Lt. Tefany Motter, Naval Medical Center Portsmouth
“The best part of being a military child is being able to move around to meet new friends and to see new places. The worst part of being a military child is moving around and saying goodbye to friends and family members.”
Tye Joiner
13 years-old; 7th Grade
Father: Electronics Technician
Navigation Submarines First Class
Kyle Joiner, USS Monpelier (SSN 765)
Mother: Mrs. Candice Joiner
“The best part about being a military child is we get to see new places and experience new things. My family and I recently moved here from California where we had nice weather all the time. Here in Virginia we get to experience cold and wet weather.”
Peyton-Sanii Earnest
10 years old; 4th grade
Father: Chief Retail Specialist Donald Earnest, Navy Service Support Advanced Training Command, Naval Air Station Oceana, Dam Neck Annex
Mother: Hospital Corpsman Second Class Chloe Earnest, Naval Special Warfare Special Boat Team – 20
“I like being a military child because places show appreciation for what the military does for the country and give us discounts.”
Organizational Conflicts of Interest (OCI) means that because of other activities or relationships with other entities, the company/ organization/institution is unable to 1) render impartial assistance or advice to the Government, 2) cannot perform the federal contract work in an objective way, or 3) has an unfair competitive advantage compared to other entities. (FAR 2.101)
An OCI occurs when a contractor's performance on one contract might compromise its ability to work successfully on another contract or when one contract compromises its ability to compete for another contract fairly. Contractors are required to avoid, neutralize, or mitigate OCIs to prevent an unfair competitive advantage or conflicting roles that might impair their objectivity.
The three types of OCIs are:
• Unequal Access to Information: A situation where there is unequal access to information occurs when a contractor has access to non-public information that would give it a competitive advantage in a competition for a different government contract as part of its performance. Proprietary and non-public source selection information are considered non-public information.
• Impaired Objectivity: When under one government contract creates a situation where it benefits other government contracts, it creates an OCI due to impaired objectivity. Contractors that give subjective advice whereby its other business interests could be affected by their judgement or advice, it sets up a situation where its objectivity could be impaired.
• Biased Ground Rules: When a contractor has helped set the ground rules for procurement of another government contract and then submit a proposal for that contract, it's an OCI because of biased ground rules.
In May 2022, Cape Henry Associates (Cape Henry) agreed to pay $425,000 to resolve allegations that it violated the False Claims Act by failing to inform contracting officers of OCIs in connection with the award and performance of task orders on government contracts.
The Justice Department (DOJ) alleged that Cape Henry failed to disclose that one of it's officers had an ownership interest in KOVA Global, a Cape Henry subcontractor.
DOJ also alleged that Cape Henry failed to disclose information about an OCI arising from services performed by subcontractor Q.E.D. Systems Inc. (QED). Under a Navy SeaPort e-contract, Cape Henry submitted project-specific proposals to a Navy program management office that was responsible for determining project scope and funding. At the same time that Cape Henry submitted proposals to the Navy, Cape Henry was funding the labor of a QED employee through a subcontract. The QED Employee provided services to the Navy program office and made recommendations that could potentially affect Cape Henry's funding and treatment.
Unexplained or unusual favoritism of particular subcontractor; Inclusion of overly specific or unnecessary requirements when contractors assist with planning future procurements.
Check out the C-FRAM site on WebCentral under C100CE for more information. Need to report fraud? Contact the NNSY Hotline today at 757-396-7971 or NNSY_IG_HOTLINE@navy.mil.
Okay 72, so this is how you do! Congratulations to Shop 72 of NNSY’s Lifting and Handling Department (Code 700), winning the November 2022 Safety Flag and for the second month running! Shop 72 is committed to continual enforcement of safety and implementing improvements through in-person training, visual reminders and ongoing safety surveillances driving actions to protect the workforce. NNSY Production Resources Officer Capt. Frank Gasperetti met with the team Feb. 23 to present the flag and congratulate this achievement. A certificate of appreciation was presented to Kevin Jones for his efforts in contributing to a safer workplace. (Photos by Danny De Angelis, NNSY Photographer.)
Shipfitters? Safety hitters! Congratulations to Shop 11 of NNSY’s Structural Group (Code 920), winning the December 2022 Safety Flag! Closing out the year with no injuries and no lost workdays, this also marks Shop 11’s second safety flag of 2022 after taking the title in July. Shop 11 has demonstrated leading by example in creating a positive safety culture, ensuring employees are equipped with the right Personal Protective Equipment (PPE) and maintaining safety focus while performing challenging work evolutions to achieve first-time quality.
NNSY Business and Strategic Planning Officer Capt. Scott Tracey met with the team March 2 to present the flag and congratulate this achievement. Certificates of appreciation were presented to Lemar Ennis and Alicia Rodgers for their efforts in contributing to a safer workplace. (Photos by Shelby West, NNSY Photographer.)
EARN A COMPETITIVE SALARY WHILE YOU LEARN
GAIN YOUR TCC TRADE TECHNICIAN CAREER STUDIES CERTIFICATE
EMPLOYER PAYS FOR ALL YOUR TUITION AND BOOKS
The Norfolk Naval Shipyard Apprenticeship Program is now accepting applications until May 1, 2023. The program seeks to recruit enthusiastic individuals looking to start a rewarding career with the Federal Government. The four-year program offers selected candidates a chance to earn a competitive salary while they learn a trade, gaining their Technician Career Studies Certificate from Tidewater Community College (TCC) at the same time. Graduates also have the option to advance their education upon completion of the program by pursuing an Associate of Applied Science Maritime Technologies: Trades Technician Degree. Apprentices have the option to choose from various trades and become experts on their selected trade by taking TCC’s academic courses, NNSY’s trade theory training, and receiving on-the-job experience. For more information on NNSY’s Apprenticeship Program, visit https://help.tcc.edu/s/article/Norfolk-Naval-Shipyard-Apprentice-Program/.
OUR MISSION: We repair, modernize, and inactivate our Navy’s warships and training platforms.
OUR VISION: We strive to achieve our ultimate goal - deliver on time, every time, everywhere to protect America.
ONE TEAM: We are the NNSY Workforce! Together, we are ONE TEAM in the mission of relentlessly chasing best ever performance in our stewardship of our nation’s warships.
1. Complete an admission application for Tidewater Community College (TCC), either online or at the college.
2. Take the Virginia Placement Test (VPT). **Now Accepting Placement Test scores valid for two years with applications**
3. Set up an account and complete an application on www.indeed.com.
4. Applications are accepted now through May 1, 2023. Your application and college placement test must be completed and submitted via www.indeed.com before the deadline.
START YOUR CAREER TODAY AT AMERICA’S SHIPYARD!
www.facebook.com/
Here are scholarship opportunities for Norfolk Naval Shipyard (NNSY) employee dependents offered from organizations within America's Shipyard. Please note the deadline and point of contacts for each group and reach out to them if you have any additional questions.
Applications for the 2023 NNSY Naval Civilian Managers Association (NCMA) Scholarships are now being accepted until Apr. 17. Six scholarships will be awarded including a new scholarship for students enrolled in technical or trade schools. Applications and requirements are available on the NCMA WebCentral page: https://webcentral.nnsy.navy.mil/sites/associations/NCMA/SitePages/Home.aspx.
The NNSY Chapter of the National Association of Superintendents (NAS) is offering multiple scholarships for outstanding dependent students of shipyard military and civilian employees, worthy of $500 to those who apply. Applicants are evaluated based on their academic achievements, extracurricular, personal and service activities and a short personal narrative, with appropriate consideration given to special circumstances of need. Applications require sponsorship from a member of the NAS. A list of members can be found in the outlook distribution list titled Superintendent Association (NNSY_ Superintendent_Association@us.navy.mil). NAS Sponsors can provide a copy of the current year application.
The NAS will be competitively awarding ten scholarships this year: five to dependent students of NNSY employees at large and five to dependent students of NAS Members. However, depending on availability of funds, the number and/or value may increase. Selectees will be presented a NAS Scholarship Certificate and a check to be used for any legitimate educational expense of the student. Applications must be hand delivered to Brian Bennett or Faultine (Tina) Rodgers at 757-396-4390, faxed to 757-396-4080, or emailed to faultine.d.rodgers.civ@us.navy.mil electronically no later than April 21, 2023. Selected scholarship recipients will be notified no later than May 26, 2023.
Applications for the 2023 Federal Managers Association (FMA) Chapter 3 scholarships are now being accepted. Five scholarships are being awarded to dependents of FMA members in good standing, worth $500 each. Please reach out to shanna.l.krauss.civ@us.navy.mil to obtain an application - all applicants and supporting documentation must be turned in by July 1, 2023
It will be conducted as luck of the draw and names will be announced immediately after the drawing at the July regular meeting. Checks will be presented at the annual Crab Feast held in August.