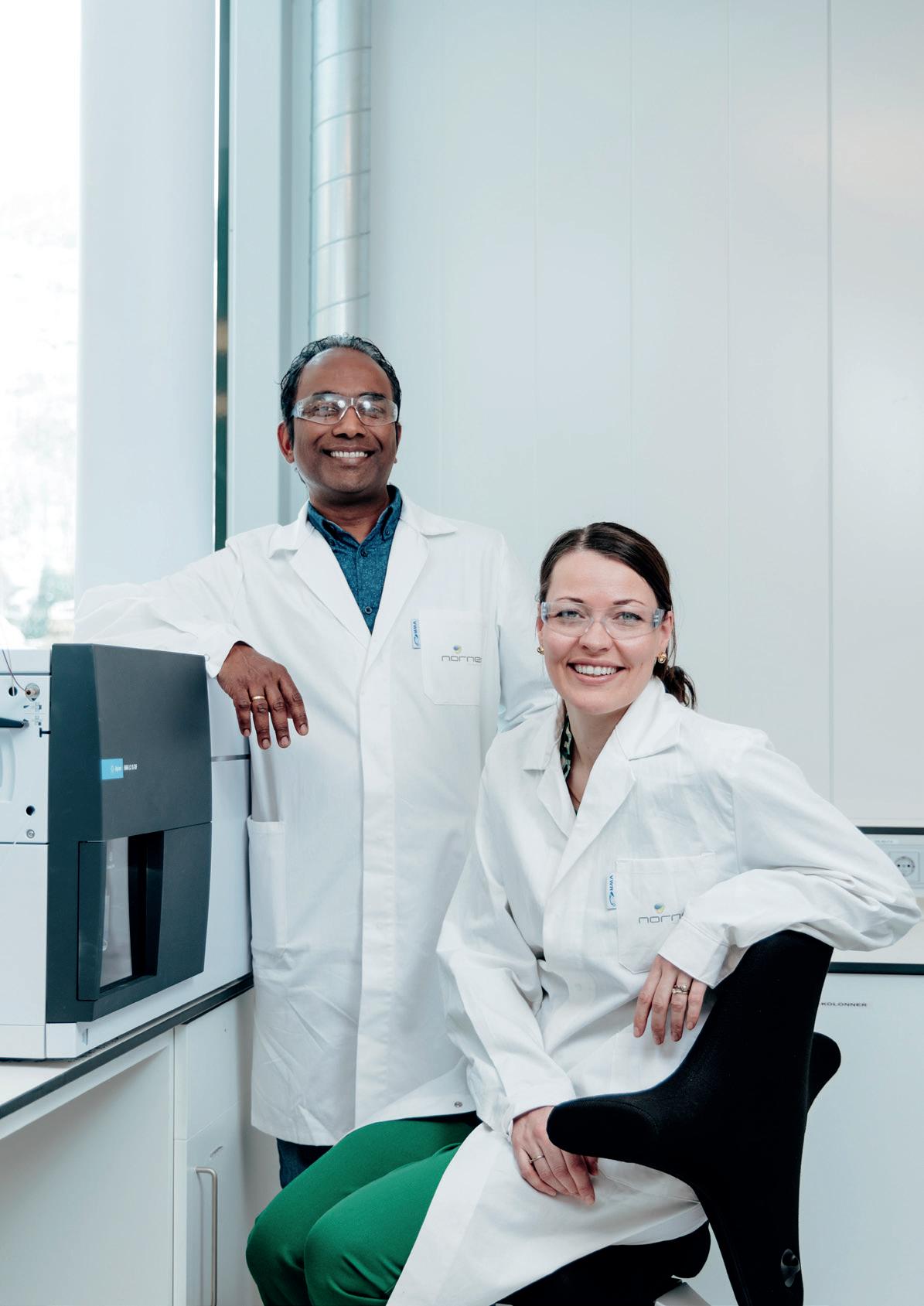
Norner supports the
Norner supports the
Our team is continuously growing, and we are very proud to welcome our new colleagues who will bring valuable expertise across the Norner organisation.
Norner is thrilled to introduce Peter Roberts as our new Customer Development Manager for the UK and Ireland. With over 35 years of experience in the polymer and packaging industries, Peter has worked for global organisations across various disciplines and markets, including technical, man ufacturing, and commercial roles.
Peter's journey has been marked by a passion for learning and experiencing different cultures, alongside a deep commitment to conservation and environmental stewardship. His person al ethos aligns seamlessly with Norner's mission of fostering sustainable solutions for the future. Peter is enthusiastic about becoming a part of the Norner team and is eager to leverage his capability, knowledge, and expertise to reach a wider audience. He aims to address existing and future challenges with sustainable solutions, building on the team's success achieved to date.
Dear reader
Norner is created on a vision – a vision to be the global market leader of industrial R&D services in Polymers by exploring opportunities and discovering sustainable solutions. In fact, we can also say that we are exploring, developing, and scaling up solutions for our customers or in partnership with customers.
It has been a long time since we have had such a troubled backdrop. The world and Europe are facing several challenges at the same time, like stagnating financial growth, rapid climate changes coming closer to everyone, social inequalities, a polarised political landscape, and dreadful wars in Europe and the Middle East. All at the same time. Creating uncertainty. In all this uncertainty, we chose to focus on the certainties:
The world population has hit 8 billion, counting to 10 billion by 2050. We will have an increased life expectancy and higher standard of living, and we will see more migration. We must take better care of our resources as well as the planet through higher resource efficiency, and we need new and sustainable sources of energy. And finally, advanced digitalisation and AI will permeate many parts of society. We are the first generation to feel the impact of the climate crisis, and we are the last generation where it is only a matter of will to do something about it.
We see these certainties and challenges as the best possible opportunities to invest most of our innovation focus.
For almost seven years now, I have enjoyed working with my highly competent colleagues and excellent customers worldwide as the CEO of Norner.
While many have talked loudly about sustainability and the circular economy over the last years without having the results to back it up, Norner continues to work systematically within all major fields of circularity of plastics.
We are working with customers in the whole value chain, many of whom are world-leading brand owners and polymer producers, to design their products for recycling. We are developing new recipes for customers so they can increase the fraction of recycled materials and maintain the good quality of their products.
We extended our important efforts in the circularity of plastics to advanced chemical recycling of plastics together with the company Pointbreak. Pointbreak offers novel technology that can handle mixed plastic waste and convert these into valuable oil products that can be further converted to monomers and polymers.
We are also making continuous developments in other fields of recycling, and this summer, we announced that we would partner up with Plast Nordic to develop and scale up a groundbreaking advanced process for chemical recycling of PET (polyester terephthalate) from e.g., packaging and textiles to monomers, and therefrom back to high-value PET products.
For Norner, 2024 will be another memorable year. At the beginning of 2022, we moved into our new Polymer Exploration Centre (PEC I), 4600 square meters with laboratories, a pilot hall, and offices. In 2023, we added another large centre, Polymer Exploration Centre II (PEC II), to our facilities. During 2024, PEC II has been rebuilt and customised for our new business growth areas. PEC I and PEC II are located in Porsgrunn near the railway station with excellent connections to Oslo, as well as near Sandefjord, Torp International Airport (TRP).
The world needs sustainable solutions, and the Norner team is stronger than ever, with state-of-the-art machinery and equipment to help our customers navigate towards new sustainable industrial solutions.
Enjoy the reading!
- Kjetil Larsen CEO, Norner
Name: Ronny Ervik
Title: Senior Consultant
From: Stathelle in Bamble, Norway
Lives in: Rugtvedt in Bamble
Ronny grew up in the small town of Stathelle in Bamble, Norway. Having lived in Bamble his entire life, his academic journey led him to HIT, where he earned a BSc in Chemical Engineering.
After graduating in 1995, he began his career at Borealis in February 1996, where he worked until the founding of Norner in 2007. In 2010, he left for other job opportunities but returned to Norner in 2021.
At Norner, Ronny is an integral part of the Business Development Group within consumable applications, with a balanced blend of project management and sales. Currently, Ronny is managing over ten smaller projects, maintaining close-knit relationships with his clients. He is responsible for activities related to rotational moulding and the coordination of RecyClass protocol testing.
Iselin is a skilled and talented engineer in the microscopy lab at Norner, based in Skien, where she was born and raised. She completed her apprenticeship in chemical processing at Statoil and Ineos, then she pursued a degree in gas and energy technology at the University of South-Eastern Norway (USN). Her career includes roles at Trelleborg Offshore (now Vipo), Kebony, and Vard Engineering. Since joining Norner in 2017, she has specialised in optical microscopy, SEM, failure analysis, FTIR, and wetting analysis. She is a LIMS superuser and a new member of the Norner board.
Iselin is passionate about advancing microscopy and recycled plastic, contributing to sustainable
solutions while learning from best people within the field.
She sees Norner's mission as helping clients in transitioning to circular plastic solutions, addressing the plastic waste issue, and transforming recycled plastic into a valuable resource. She hopes Norner remains a sought-after workplace with an excellent working environment.
When not working, Iselin enjoys reading, working out with friends, and sharing a glass of wine (balance is the key). She is currently studying strategic sustainability at USN.
Iselin exemplifies dedication, passion, and excellence. Her expertise and commitment to sustainability make her an asset to Norner and the engineering community.
His passion lies in rotational moulding and recycling. As the founding Chairman of Nordic ARM and a board member of ARMO, Ronny has made significant contributions to the industry. Over the past 25 years, he has delivered numerous presentations and looks forward to continuing his work for the next 25 years.
Ronny envisions Norner as the premier R&D partner for the plastics industry value chain. Beyond conducting tests and projects, Norner brings innovation, insight, and knowledge to their clients. The valuable information from Norner's labs and project managers is highly esteemed by customers, reinforcing the company's important role in the industry.
Beyond his professional commitments, Ronny's family and home/garden take up most of his spare time, and he enjoys sports like jogging and biking.
Name: Khrisna Kumar
Title: Senior Researcher
From: Kolar Gold Fields, India
Lives in: Porsgrunn
Krishna grew up in a small town called Kolar Gold Fields in India. He was uncertain about the path after high school until a neighbour suggested chemical engineering, calling it "an evergreen field with vast potential". Inspired by that, he pursued a BSc in Chemical Engineering, discovering his passion for the field through various internships.
Kirshna's career began at GEPlastics, focusing on BPA technology development. Later, at the SABIC Research Center in Bangalore, he led plastic pyrolysis research, built pilot facilities, and secured over 20 patents in chemical recycling.
Driven by his expertise in plastic recycling, Krishna joined Norner in 2022. Despite knowing little about Norway or Norner beforehand, the move proved life-changing. For the past two and a half years, he has worked on commissioning and operating a continuous
Gina Braathen grew up in Asker outside Oslo before moving to Trondheim where she earned an MSc in Chemical Engineering at NTNU. Natural science was a natural path for Gina, allowing her to combine her interests in chemistry, mathematics and programming and apply this knowledge to address global challenges. She found chemical engineering interesting because it provides insight into chemistry on all scales, from laboratory scale to industrial production.
Being in Norner since 2022, Gina is tasked with qualifying coating systems, a role that involves both testing and reporting. She conducts mechanical testing of polymers and provides lifetime estimations based on an accelerated ageing of materials and polymers. Moreover, she serves as an internal quality manager for ISO 17025 at the Coating lab, ensuring that the accuracy and reliability are maintained
Gina finds satisfaction in the combination of practical laboratory work and theoretical analyses. Her role offers professional insights into the ageing of various materials, including plastic coating, rubber, and metals. Working at Norner allows her to engage broadly across different fields and methodologies. She is also part of a major project aimed at increasing PCR in packaging, which is both challenging and rewarding.
Gina is committed to contributing to more sustainable material choices within the offshore industry and energy sector. At Norner, she appreciates the interdisciplinary knowledge used to find effective solutions in many sectors that are transitioning to more sustainable practices.
Outside of her professional life, Gina enjoys working out, singing in a choir, and spending a lot of time cooking vegetarian dishes.
pilot plant, tackling various challenging feedstocks and conditions, with the support of his mentors at Norner.
He thinks Norner has offered him immense opportunities to explore his field, providing critical insights through data analysis and project results that benefit both his research and the customers.
On a personal note, moving from India's warm climate (+25°C) to Norway's cold winters (-25°C was a major adjustment for Krishna, yet Norway's work-life balance has enriched his life, introducing him to new activities like ice bathing and walking on frozen lakes. This transition wouldn't have been possible without his wife and son's support. He thinks relocating has been rewarding both personally and professionally, proving that the grass is green everywhere with the right mindset.
Name: Gina Braathen
Title: Senior Engineer
From: Asker, Norway
Lives in: Porsgrunn
World Cleanup Day 2024 at Norner
Henning Baann henning.baann@norner.no
Norner has received DNV certification for both IMO Resolution IMO MSC.215(82) and IMO MSC.288(87) for coating testing in accordance with Class Programme DNV-CP-0622.
This is an essential quality standard for test laboratories internationally. With this approval, Norner is now an independent testing institute certified by the International Maritime Organisation (IMO) and the Performance Standards for Protective Coatings (PSPC) test standards.
for IMO and PSPC Standards
The relevant standards include IMO Resolution MSC.215 (82) for Seawater Ballast Tanks and IMO Resolution MSC.288 (87) for Cargo Oil Tanks. Approval from DNV and Lloyd's demonstrates that our lab excels in quality management and technical competence. We have also long held ISO/IEC 17025 accreditation for protective coating. These latest certifications from DNV will give our clients products a good credibility and higher competitiveness. We are now able to serve our clients with a full range of coating tests.
Norner is among few European institutes approved for specialised coating testing
According to DNV and Lloyd's list of approved institutes, Norner is one of the few approved institutes in Europe for this type of testing. We intend to strengthen our position in this area and already have plans for further expansion both in manning and equipment. A new state-of-the-art development and laboratory facility was opened in 2022. The coating lab is an essential part of this new building, and further expansion is secured through this investment.
Norner offers both 3rd party testing and pre-qualification testing of protective coating within different applications. Our wide range of methods covers cathodic disbonding, corrosion, immersion, UV testing, as well as climate exposure procedures, and various physical properties.
Ravindra Reddy Chowreddy ravindra.chowreddy@norner.no
The ENZYCLIC project combines biochemistry, chemistry, and social sciences to accelerate the development of new technologies for the recycling of plastics.
At the present rate of growth, plastic production is estimated to double within the next 20 years. A projected increase in future plastic use will result in a concomitant increase in post-consumer plastic waste and environmental concerns. Given these challenges, plastic recycling has
become increasingly important to mitigate the environmental impact of plastic waste.
The most common method of plastic recycling is mechanical recycling, in which the plastic waste is physically transformed into a reusable material or product. Mechanically recycled
plastics often represents a lower performance and are often blended with virgin plastic material to achieve acceptable performance. Chemical recycling is an alternative method that compliments mechanical recycling when the plastic wastes are difficult to recycle by mechanical means. In this case, the polymer is broken down into building blocks of hydrocarbons.
Chemical recycling of plastics is challenged by low recycling rates and undesired byproducts. To improve the plastic recycling rates, innovative, sustainable, and eco-friendly approaches are being explored in this project. One such approach is the biochemical recycling of plastics into monomers in the presence of microorganisms or enzymes. Such enzymatic recycling methods are being utilised to depolymerise polyethylene terephthalate (PET) into its constituent monomers. In the enzymatic recycling process, commercial enzymes like cutinases, lipases, and esterases are utilised to selectively hydrolyse the ester bonds.
The Enzyclic project, funded by the Norwegian Research Council, is a collaborative interdisciplinary project to develop enzyme-based technological solutions for the recycling of existing plastics and novel biodegradable plastics. The project is led by the Norwegian University of Life Sciences (NMBU). Besides Norner Research, Bellona, Aclima, and the Norwegian Packaging Association participate. The Faculty of Chemistry, Biotechnology, and Food Science at NMBU is a hub for interdisciplinary research, and it covers a wide range of scientific fields, from basic natural sciences to their applications in food, biotechnology, and environmental science. The Bellona Foundation is an independent non-profit organisation that is striving to identify and implement sustainable environmental solutions. Aclima is a textile producer with a target to find sustainable solutions to recycle synthetic fibres. The Norwegian Packaging Association is involved through the Circular Packaging Cluster with the goal of sharing knowledge about challenges and regulations of the packaging sector and having clear objectives of encouraging sustainable packaging. As a participant in the Enzyclic project, Norner has several major tasks:
• Developing novel aliphatic polyesters with superior properties that are amenable to enzymatic degradation.
• Exploring various technologies to modify conventional polymers to make them susceptible to enzymatic degradation.
• Supporting the project with various analytical methods to determine the plastics' physical, chemical, and thermal properties and the degradation products.
The Enzyclic project is an ambitious project where NMBU will identify enzymes for plastic degradation by adopting state-of-the-art (meta) genomics and proteomics techniques to explore the enzymatic machinery of plastic-degrading microorganisms and
insects. NMBU will also screen and re-design powerful oxidative enzymes that naturally target recalcitrant and crystalline surfaces of biopolymers to target conventional plastics.
Norner will produce novel polyesters in our lab pilots and modify conventional polyolefins to make them more susceptible to enzymatic degradation. In addition, Norner will develop methods for extraction, purification, and reuse of plastic degradation products. The ultimate target of the project is to depolymerise plastics into monomers through biotechnological routes and to regenerate new polymers from the monomers obtained from the degradation process.
• Norner Research has produced 13C isotope enriched polyolefins in research scale for traceability investigations in enzymatic degradation studies.
• Performed partial degradation of commercial polyolefins through thermal and UV degradation for enzymatic degradation experiments.
• Currently, a range of aliphatic polyesters are being produced for enzymatic recycling evaluations.
Albrecht Dix albrecht.dix@norner.no
Lars Henry Evensen lars.evensen@norner.no
Norner Advance® M represents a significant leap forward in Metallocene PE technology. By employing unsupported metallocene catalysts in solution form, this technology not only reduces environmental impact but also lowers production costs, making it a more sustainable and economically viable option for the industry.
In the second decade of the 21st century, the growth of metallocene polyethylene (PE) has been remarkable, driven by its superior properties and versatility. This period saw a notable shift in market dynamics, with metallocene resins experiencing high single-digit growth rates, outpacing traditional PE resins. In particular, Metallocene linear low-density polyethylene (mLLDPE) has gained significant traction, mainly in the flexible packaging sector, due to its ability to produce stronger, thinner films with enhanced performance characteristics. However, most of this growth was
fueled by gas-phase polymerisation plants, leading to a commoditisation of mLLDPE while leaving the product opportunities in MDPE and HDPE from slurry-type polymerisation processes unexplored.
Generally, the polyolefin industry prefers heterogeneous catalysts for polyethylene polymerisation processes. Ziegler-Natta catalysts, in particular, are effective in slurry-phase polymerisation, which is widely used for producing polyethylene, giving high productivity and reliable process
stability. Heterogenous metallocene catalysts, on the other hand, have proven to be costly due to manufacturing cost and low activity, thereby limiting access to advanced MDPE and HDPE products.
The Norner Advance® M PE technology addresses this issue by demonstrating high polymerisation activity, resulting in lower production costs and reduced catalyst consumption (Figure 1). The technology also ensures higher purity and lower catalyst residues in the final polymer, contributing to a cleaner and more sustainable production process.
One of the standout features of Norner Advance® M is its adaptability to slurry processes, such as Mitsui CX, Hostalen, MarTECH, and Innovene-S. The technology is particularly beneficial for multimodal PE production, which benefits polymer processability and product performance in film, roto blow moulding and pipe applications. Furthermore, the technology can be applied to a wide range of metallocene complexes and activators, allowing free choice for the implementation of license-free or proprietary solutions.
The technology has been validated in a continuous bimodal process on a mini-pilot scale, showcasing excellent operability and stable conditions. The validation process involved comparing the behaviour of unsupported metallocene catalysts with silica-supported catalysts, with the former demonstrating superior performance in terms of process stability and product quality. It was demonstrated that while achieving higher productivity, similar particle size and distribution are achieved in a 2-reactor process (Figure 2).
Norner Advance® M supports an advanced metallocene PE product portfolio, catering to various applications such as roto moulding and blown film. The technology has been tested and validated in these applications, with
the prototypes matching or surpassing commercial benchmarks. We are also confident that the high Mw capability of Norner Advance® M combined with excellent comonomer distribution will provide well-performing products for blow moulding and pressure pipes.
Norner Advance® M is a testament to Norner's commitment to innovation and sustainability. By leveraging unsupported metallocene catalysts, the technology offers significant benefits in terms of process operability, cost efficiency, and environmental impact. As the Metallocene PE market continues to grow, Norner Advance® M is well-positioned to lead the change towards a more sustainable future in polymer technology.
The technology has demonstrated a TRL 6, and Norner is now welcoming partners that are interested in evaluating the benefits of entering the market with high-value-added metallocene PE products by revamping their CSTR plants.
Norner Advance® M provides metallocene PE from slurry technologies with significant advantages, like:
• Substantially reduced catalyst costs
• A broader molecular weight window
• Enhanced purity
• Improved comonomer distribution compared to Ziegler-Natta catalysts
• A reduced carbon footprint
Lars Henry Evensen lars.evensen@norner.no
Jarmo Lindroos jarmo.lindroos@norner.no
You can unlock the market potential of innovative polyolefin production technologies like DOWLEX, SCLAIRTECH, and BORCEED with Norner's expertise and facilities.
Advantages of Solution Polymerisation Technologies
The polyolefin market, encompassing materials like polyethylene and polypropylene, is continually evolving with advancements in production technologies. Among these, the different solution polymerisation processes like DOWLEX, SCLAIRTECH, and BORCEED stand out for their superior performance and versatility.
DOWLEX technology, pioneered by Dow Chemical, offers enhanced mechanical properties and processability. DOWLEX-produced resins exhibit an exceptional range of densities and structures. This results in films with outstanding sealability, toughness, and puncture resistance, making them ideal for demanding packaging applications.
SCLAIRTECH Technology, developed by NOVA Chemicals, is renowned for its flexibility in producing a wide range of polyethylene products. This technology allows for the customisation of polymer properties to meet specific application needs, from high-density polyethylene (HDPE) to linear low-density polyethylene (LLDPE). SCLAIRTECH's ability to produce polymers with tailored molecular weight distributions ensures optimal performance characteristics such as strength, durability, and environmental stress crack resistance.
BORCEED technology, a proprietary process by Borealis, excels in the production of polyolefins with enhanced environmental profiles. This technology leverages advanced catalysts and polymerisation
techniques to produce materials with reduced carbon footprints. BORCEED polymers are particularly favored in applications requiring high recyclability and sustainability, aligning with the growing market demand for eco-friendly solutions.
The global polyolefin market is experiencing robust growth, driven by increasing demand from the packaging, automotive, construction, and consumer goods sectors. Products derived from the solution polymerisation technologies occupy a significant share of this expanding market. As these technologies continue to evolve, they are expected to capture an even larger portion of the market, driven by their superior performance and adaptability.
Norner, a leader in polymer research and development, has extensive experience in executing projects using advanced polyolefin production technologies. Utilising our bench-scale reactors, we have successfully replicated the demanding process conditions (high temperature and pressure) known to those of DOWLEX, SCLAIRTECH, and BORCEED technologies. Our team's understanding of these processes enables us to provide precise and reliable data that informs the scaling-up and optimisation of polymer production systems.
Our bench-scale reactors allow us to simulate various polymerisation conditions, offering clients insights into the behavior and performance of different catalysts and polymerisation techniques. This capability is crucial for developing new materials and optimising existing production processes. Our expertise spans across various polyolefin applications, ensuring that we can deliver R&D services without disclosing any proprietary information.
In the realm of solution polymerisation, Norner offers unparalleled value to its clients through a
combination of technical expertise, state-of-the-art facilities, and a commitment to innovation.
Norner's team comprises professionals with extensive knowledge in polyolefin chemistry and process engineering. Our experts bring experience in solution polymerisation, enabling us to tackle complex challenges and deliver tailored solutions that meet the specific needs of our clients.
Our advanced laboratories and bench-scale reactors are equipped with the latest technology, allowing us to conduct rigorous testing and analysis. These facilities enable us to replicate commercial production conditions, providing clients with accurate data and insights that drive informed decision-making.
At Norner, we understand that each project is unique. Our approach to solution polymerisation is highly customisable, ensuring that we deliver solutions that align with our client's specific requirements. Whether it's developing new polymer grades or optimising existing formulations, our innovative approach ensures optimal performance and efficiency.
We recognise the importance of sustainability in today's market. Norner is committed to promoting eco-friendly practices in polyolefin production. Our solution polymerisation services focus on developing materials that meet stringent environmental standards, helping clients achieve their sustainability goals while maintaining high performance.
Norner's extensive expertise in polyolefin production technologies, including solution polymerisation, positions us as a valuable partner for clients seeking to innovate and optimise their polymer production processes. Our state-of-the-art facilities, combined with our commitment to customisation and sustainability, enable us to deliver high-quality, tailored solutions that drive success in the competitive polyolefin market.
As we continue to advance our capabilities and explore new frontiers in polymer science, we remain dedicated to helping our clients achieve their goals and unlock the full potential of their products.
Ervik ronny.ervik@norner.no
Czulek tomasz.czulek@norner.no
Successful completion of PP film protocol testing and RecyClass approval has confirmed the new Capri-Sun 200ml pouch as fully recyclable.
Capri-Sun and sustainability
Capri-Sun's vision is to become "the most sustainable and best-tasting kids' drink in the world." In line with this goal, in 2023, the company decided to move all non-recyclable 200ml pouches to fully recyclable high-barrier mono-material pouches.
The challenge
In collaboration with packaging suppliers, the Capri-Sun R&D Packaging team developed a high-barrier mono-material structure intended to be compatible with the PP-flexible recycling stream. The goal was to achieve full recyclability, confirmed by RecyClass testing, with no compromises on compatibility with PP-colored flexible recycling. However, initial tests conducted at an external lab did not yield positive results. Determined to meet their high standards, CapriSun refined the film formulation and sought a more experienced partner in film extrusion and material testing.
This led them to engage with Norner for the next round of testing.
The approach
Norner, a recognised laboratory for RecyClass protocol testing of PP and PE-films and rigid packaging, was approached by Capri-Sun to support the testing of their novel fully recyclable PP-based pouch. Given the critical need for Capri-Sun products to maintain excellent protection against light and oxygen, the new packaging had to deliver a high barrier to both. Developing high-barrier packaging that remains fully compatible with recycling streams is always challenging. Therefore, Norner recommended that Capri-Sun began with an initial test focusing on the key parts of the RecyClass protocol (Pre-RecyClass test) related to the innovation film: pre-treatment (grinding, washing, floatation test, drying), extrusion to pellets (50 % control/50 % innovation), cast film production and testing.
This innovative approach enables Capri-Sun to gain a preliminary understanding of the material's performance in the recycling stream while saving both time and money. If the initial tests reveal poor material performance, Capri-Sun could redesign the film without committing resources to full protocol testing, which would not yield the desired approval.
The initial tests on Capri-Sun's high barrier 200 ml pouches showed excellent results, with both the mechanical and optical properties of the extruded cast film looking very promising. Based on these positive outcomes, Capri-Sun decided to proceed with the full PPfilm protocol testing and move forward with applying for RecyClass approval.
Photo of B.50 gels evaluation.
In March 2024, Capri-Sun shared the exciting news that the RecyClass PO Films Technical Committee had confirmed the "Capri-Sun PP-pouch" as fully compatible with PP-colored flexible recycling. Earlier this year, Capri-Sun products packaged in these recyclable PP flexible pouches were successfully launched in Europe.
Norner takes great pride in supporting our customers with our expertise and experience as they navigate their sustainability journey. If you need any support with the RecyClass testing, please do not hesitate to contact us!
Securing RecyClass approval has been a significant milestone for our development. Throughout our successful collaboration with Norner, our progress was validated, paving the way for a positive market introduction. This achievement underscores the importance of rigorous testing and documentation in bringing sustainable products to the market.
Jakub Pedzinski, Sr. Packaging Innovation Mgr. at Capri-Sun
As a RecyClass certification body and testing facility, Norner offers a comprehensive range of services, including:
• Design for Recycling Certification
• Recyclability Rate Certification for Norway
• Letter of compatibility
• Recyclability Evaluation for HDPE and PP-containers, as well as PP and PE-films
If you require any assistance with RecyClass testing, please feel free to reach out to us!
if labels, glues or inks are present
Jorunn Nilsen jorunn.nilsen@norner.no
Ole Jan Myhre ole.jan.myhre@norner.no
Packaging plays an important role in protecting products during transport and storage, ensuring hygiene and safety for the product to the consumer. Orkla aims to expand the use of recycled HDPE and has engaged Norner in a project to develop knowledge and strategies to ensure quality.
Orkla Home and Personal Care has long been engaged in the development and implementation of packaging solutions with better sustainability and environmental profiles. An important measure is to use recycled plastic in their packaging. A challenge with this is that recycled plastic often contains contaminants that can cause odour, weaker material, and unsafe substances that can leach into the product. Orkla has received project support from the Retail Environment Fund to establish relevant specifications for the use of recycled HDPE for Orkla's personal hygiene products, conduct tests to document the safe use of such, and approve relevant rHDPE
suppliers. This work will be done together with Norner Research AS.
The project will deliver solutions for how recycled HDPE (rHDPE), which meets the purity requirements for primary packaging of personal care and cosmetic products, can be used in such contact-sensitive packaging. rHDPE materials are often not good enough to meet the requirements of the cosmetics regulation (EC) No 1223/2009 - which allows the use of recycled materials - as long as safety is documented. CosPaTox (see fact box) has published its guidelines, and we will use these recommendations.
The project will, among other things:
• Gather information from industry and research to establish test and analysis methods
• Test and evaluate rHDPE materials from various recyclers
• Carry out screening analyses and target analyses of substances in the materials.
• Evaluate strategies for analysing the substances, e.g. directly on pellets or bottles.
• Evaluate strategies to minimise migration risk from cosmetic packaging through blends or multilayer packaging of rHDPE.
• Test whether the physical performance of bottles meets the technical specifications.
Norner Research's role in the project is to contribute with plastic and packaging competence, analyse substance composition, bottle testing and production of prototype bottles.
Norway and the EU's ambition is to increasingly recycle plastic packaging and recover this plastic so that it can be safely used in new packaging or other products. Progress has stagnated, and the authorities now want to further accelerate this. EU has a new regulation
underway known as the Packaging and Packaging Waste Regulation (PPWR). This will introduce new and stricter requirements for recyclability, the use of recycled material, packaging minimisation, and reuse of packaging. There will also be an eco-modulated fee on packaging to promote this.
Migration analysis shows that the rHDPE materials contain other substances than virgin HDPE. These substances fall into three categories:
• Odour components from previous content like soap or cosmetics.
• A small amount of food contact-approved additives in the materials and some derivates of these.
• Occasionally, some phthalate compounds are present.
The cosmetics industry has formed a consortium: CosPaTox (cosmetics, packaging, and toxicology). The goal is to understand and establish safety standards for high-quality recycled plastic materials (PCR) for cosmetics, personal care and household detergents. This resulted in a guideline for analysis and safety assessment. The recommended testing includes
• Migration testing on pellets or packaging with screening analysis of all substances
• Specific analyses for hazardous substances such as PAH, PAA, Bisphenol, Dioxins, and Heavy metals
Norner has established several of these new methods and is working to validate more. These methods will also be used in Orkla's project.
Ronny Ervik ronny.ervik@norner.no
Ole Jan Myhre olejan.myhre@norner.no
TOPAS Advanced Polymers has shown that their COC polymers, in combination with other polyolefins like HDPE and PP, bring significant benefits for packaging. Norner has carried out RecyClass testing to prove that such blends are recycleable.
TOPAS COC (Cyclic Olefin Copolymer) is a high-performance plastic known for its high purity and clarity. It is used in various industries, including packaging. Some of the key properties and applications are:
• Superior purity, making it well-suited for food packaging
• High stiffness and rigidity, making packaging more stable and enabling downgauging
• Heat Resistance, making it sterilisable
• Barrier Properties against moisture, alcohols, acids, and other substances, making it useful for product protection
• High gloss and clarity, enhancing the appearance of packaging
EU authorities have now published the Packaging and Packaging Waste Regulation (PPWR). This includes a requirement for fully recycleable packaging by 2023. Therefore, it was important for TOPAS to ensure the recyclability of such combinations. If a certain material composition has not been evaluated or tested, the producer can request testing according
to RecyClass-specific recyclability evaluation protocols. The outcome of the testing will determine whether the composition will be approved or not. If approved, it will be in the guidelines and the RecyClass Online Tool.
To enable the use of COC with HDPE or PP in packaging applications, TOPAS assigned therefore Norner to carry out RecyClass protocol testing to obtain RecyClass Technology Approvals for two cases:
• TOPAS COC in EBM containers with a two-layered bottle with COC 20 % / HDPE 80 %
• TOPAS COC in a blend of up to 20% in PP cast film. Both cases was proven recyclable, are fully accepted by RecyClass and included in the guidelines.
Norner is a recognised laboratory by RecyClass that carries out tests for flexible and rigid packaging of polyolefin. These protocol test projects with COC fit very well with the facilities at Norner. In our technology centre you will find a wide range of plastic processing lines, including 3-layer extrusion blow moulding and mono-cast film, which were used in these projects. In addition, we have lines for compounding, injection moulding, 7-layer cast film, thermoforming,
MDO for film orientation, mono-blown film, and 7-layer blown film.
This RecyClass approval was an important step in our plans to increase the potential of COC in packaging applications. Testing and documentation of materials to ensure recyclability are key factors for our development. TOPAS had a good collaboration with Norner and they delivered these assignments on time.
Dr. Dirk Heukelbach, Market Development at TOPAS Advanced Polymers GmbH.
RecyClass is a non-profit, cross-industry initiative advancing recyclability, bringing transparency to the origin of plastic waste, and establishing a harmonised approach toward recycled plastic calculation and traceability in Europe. The RecyClass methodology was developed in collaboration with value chain stakeholders, promoting the high standards that should improve the quality of waste in a way
that helps to "close the loop" on plastic packaging. This initiative aims to help the plastics value chain evaluate and improve the recyclability of their packaging through a systematic design for recycling approach.
Norner takes great pride in supporting our customers with our expertise and experience as they navigate their sustainability journey. If you need any support with the RecyClass testing, please do not hesitate to contact us!
Norner RecyClass Certification
Norner is a RecyClass Certification Body for recyclability evaluation We provide certification services for three certification levels:
• Design for Recycling Certification
• Recyclability Rate Certification (Nordic)
• Letter of compatibility
• Norner is a recognised laboratory for RecyClass protocol testing for PE film, PP film, HDPE rigid, and PP rigid packaging. Norner also carries out quick test procedures.
Irene Helland irene.helland@norner.no
The integrity and lifetime of piping systems are critical for numerous industries, from water supply to oil and gas. Slow crack growth is a significant factor affecting the lifespan of pipes, leading to potential failures and costly repairs.
Slow crack growth refers to the gradual propagation of a crack in a material under sustained stress over time. Slow crack growth occurs at a slow rate and is influenced by factors such as material properties, manufacturing
defects, environmental conditions, and the magnitude of applied stresses. In the context of pipes, slow crack growth is a significant concern, especially for those used in critical infrastructure such as water supply, gas distribution, and industrial processes.
In the field of materials science and engineering, the evaluation of slow crack growth in pipes is paramount to ensuring the longevity and reliability of critical infrastructure. The introduction of ISO18488 (Polyethylene (PE) materials for piping systems – Determination of Strain Hardening Modulus in relation to slow crack growth – Test method) and ISO18489 (Polyethylene (PE) materials for piping systems – Determination of resistance for slow crack growth under cyclic loading – Cracked Round Bar test
method) marked a significant advancement in this domain, providing standardisation methods that enhance the accuracy and consistency of slow crack growth assessments. Norner can perform both test methods.
This method involves analysing the stress-strain curves and the slope of the curve in the strain-hardening region obtained from tensile tests on compression molded samples.
The results correlate well with the more traditional slow crack growth tests, like the Full Notch Creep Test (FNCT), but it is much quicker to perform.
The cracked round bar (CRB) method focuses on the resistance of polyethylene materials to slow crack growth under cyclic loading. This standard is particularly relevant for long-term applications of thermoplastic materials, such as PE pipes and fittings, but also others.
This method is standardised under ISO 18489, which provides comprehensive guidelines for conducting CRB tests to ensure consistency and reliability in results. The CRB test involves subjecting a round bar specimen with a pre-existing notch to a cyclic load or displacement rate, allowing researchers to observe the initiation and propagation of cracks over time.
By employing cyclic loading, this method accurately replicates real-world conditions where materials undergo repeated stress cycles. This approach is essential for applications involving materials subjected to fluctuating loads over time, providing more realistic results compared to tests that primarily focus on resistance to sudden fracture or impact, such as the Charpy or single-edge notch bending tests.
Microscopy analysis is subsequently employed to examine the failure surface of the testing bar. This technique identifies crack initiation and propagation features, confirms the failure mode (brittle, ductile, etc.), and facilitates the accurate determination of stress.
This method is particularly valuable for assessing the long-term durability and performance of materials under stress, especially when reliability is of the essence.
This test method can also be used to determine the impact of environmental factors, such as temperature, to understand how these factors affect material performance.
The cracked round bar test method is utilised across a diverse range of applications, including pipes, tanks, containers, sheathing, and floating elements. This method is essential in various sectors such as marine, mining, energy, and construction, where material durability is essential.
Jorunn Nilsen jorunn.nilsen@norner.no
Tomasz Czulek tomasz.czulek@norner.no
Norner has been developing test methods to identify contaminants in black recycled materials from the aquaculture industry and evaluate their impact on recyclate performance.
SirkAQ project
The SirkAQ project aims to develop solutions for one of the largest waste streams in the fish farming industry: plastic materials from end-of-life fish farms. The transition from a linear to a circular economy in aquaculture products will become a reality, with recycled materials being reused in new products. One of the key challenges in using recyclate for new products is ensuring its quality.
The challenge
Materials commonly used in the aquaculture industry are polyolefins (PE and PP), which are often black in color. Over their service life and during disposal, these materials become contaminated with various organic and inorganic pollutants. During the recycling process, not all contaminants can be easily removed, and some remain in the recycled materials. Due to the black colour of the recyclates,
those contaminants cannot be easily seen and identified during the quality assurance process. These contaminants may negatively impact the material performance and the quality of new products, potentially leading to unexpected material failures. Norner identified this during tensile tests of recycled materials, where failures were caused by particles in the tensile bars.
Norner was given the challenge to develop a method that allows to qualify and quantify contaminants in black materials.
Norner has extensive experience in material testing and method development. For black materials, standard visual inspection methods were ineffective. As a result, Norner designed a series of experiments using various techniques to develop a suitable solution.
One of the methods evaluated was based on the ISO 18553 standard, where samples are microtome-cut from a hot-pressed plate at six different positions and assessed according to the grading table. However, the grading table in Annex A of ISO 18553 was originally designed for smaller particles, such as pigment agglomerates. To evaluate recyclates, an upscaling of this scale is required. This method can be easily combined with identification techniques like FTIR microscopy, SEM-EDS, and LM hot stage to better understand contaminant types and potential sources.
contaminants from a larger volume of material and enables the identification of inorganic contaminants using the SEM-EDS technique.
To better understand the content of inorganic contaminants of various sizes, Norner developed a method using multiple filtration loops. In each loop, a different filter size was installed. The experiment was conducted using a Nordson filter, where the same recycled material was continuously passed through filters of different mesh sizes. Starting with recycled material pellets, the process involved extrusion, filtration, and the production of new pellets. The test began with a large mesh filter, followed by progressively smaller mesh sizes through five loops. Ash content was measured from samples taken after each loop, allowing the quantification of inorganic contaminants of different sizes per 100 g of
Measuring the visible contaminations in feedpipe material by microscopy.
In another tested method, the material was extruded through a 120-micron filter, which was then removed from the extruder and washed in xylene. The number and size of particles were measured in the next step. This method allows for the accumulation of
recycled material. This approach helps establish specifications for inorganic contaminants in PCR.
We also explored simpler methods, such as film blowing and gel counting, which could serve as effective quality control techniques.
Blown film with marked five samples of 100 cm² for a gel and specks count.
Norner believes that no single method fits all purposes. Therefore, different test methods must be applied depending on the objective. Norner is currently developing a comprehensive toolbox of methods to assess feedstock quality, support material specification development, and ensure ongoing quality control during recyclate production.
If you would like to learn more about our testing methods or discuss the most suitable approach for your needs and products, please feel free to reach out to us!
Karina Asheim karina.asheim@norner.no
Naveen Singh naveen.singh@norner.no
Norner plays a crucial role in the Norwegian battery value chain, offering a comprehensive range of services across all stages of battery production. With decades of experience in polymer processing, Norner optimises process parameters and ensures the quality of battery components, from raw materials to end-of-life. Our service portfolio for the battery value chain is summarised in Figure 1.
Each stage of battery manufacturing impacts the final performance. For instance, the assembly process can affect the safety and efficiency of separator films, while variations in raw material properties influence slurry rheology and electrode quality.
Factors like particle size, shape, and mixing processes influence the rheological properties of electrode slurry. Proper slurry rheology is vital for achieving high-quality electrodes, ensuring homogeneity, and preventing defects. Norner utilises state-ofthe-art equipment to optimise slurry properties, enhancing product quality.
Norner's expertise in polymer films covers material selection, processing, and characterisation. Our pilot-scale facilities enable the production of separator films using both dry and wet processes, allowing clients to refine their manufacturing methods. We also offer extensive testing to evaluate these films' mechanical and thermal properties.
Characterisation
Characterising electrode materials and manufacturing processes is essential for high-performance batteries. Norner's capabilities include analysing material properties and optimising conditions to enhance battery performance, focusing on composition and structural integrity.
Polymers in battery waste complicate recycling and hinder precious metal recovery. Contaminated plastics reduce yields and are difficult to process. Norner's expertise in polymer processing and material analysis supports the development of advanced recycling methods.
Norner provides various testing services for battery components, including separator films, electrode materials, and electrolyte solvents. Our analyses enable manufacturers to meet high safety and performance standards, ensuring reliable, long-lasting components that support the entire battery life cycle.
Norner's pilot-scale production capabilities for separator films bridge laboratory research and full-scale manufacturing. This approach allows
manufacturers to identify potential issues early, optimise processes, and save time and resources.
Safety and performance are paramount in battery development. Norner's analyses help identify risks and areas for improvement, leading to more robust designs and increased reliability.
Norner's deep understanding of materials and processes fosters innovation in battery technology. Our expertise drives industry advancements as demand for high-performance batteries grows in sectors like electric vehicles and renewable energy storage. Our focus on optimising production processes also promotes sustainability by reducing waste and extending the life of battery components.
In summary, Norner's extensive capabilities throughout the battery value chain - from raw material analysis to process improvement - are vital for advancing the development and manufacturing of high-quality batteries. Our expertise in polymer recycling further enhances battery recycling yields. By leveraging our knowledge and advanced testing, Norner ensures that battery components meet the highest safety, performance, and sustainability standards, contributing to innovative and sustainable energy solutions for the future.
Siw Bodil Fredriksen siw.fredriksen@norner.no
Katrin Nord-Varhaug katrin.nord-varhaug@norner.no
The growing demand for renewable energy has a significant downside: it will result in a substantial increase in waste generation in the coming years, especially regarding end-of-life photovoltaic (EOL-PV) waste. Together with partners from 9 countries, Norner participates in the large EU Horizon Project QUASAR, which aims to enable a circular economy for the solar PV industry.
This aligns with Norner's strategy, which emphasises a focus on polymer materials in the energy sector. Our approach is centred on advancing technologies for renewable energy sources, with a strong commitment to sustainable and recyclable solutions.
In 2023, solar power made up three-quarters of the new renewable energy capacity globally, and increasing solar production is essential for cutting emissions. Millions of solar panels have been installed in the last two decades, and since they typically last between 25 and 30 years, many will soon be ready for retirement and will head for landfills or incineration, where they may endanger ecosystems with hazardous materials. It is expected that the amount of PV waste could
reach 50 million tons by 2040.
However, waste from end-of-life solar panels presents opportunities to recover valuable materials that would reduce the dependency on primary raw materials and can be used to produce new solar panels and create jobs through recycling.
Materials used in a typical solar panel Did you know that about 10 wt% of a typical solar panel is made of plastic? A photovoltaic panel typically consists of several key layers, and the plastic parts have an important function (Figure 1). In the middle of the panel, silicon solar cells convert sunlight into electricity. The silicon solar cells are encapsulated in a thin plastic layer, typically made of Ethylene
Vinyl Acetate (EVA). This transparent encapsulant protects the cells from environmental damage, ensures efficient light transmission, and provides electrical insulation.
The encapsulated solar cells are sandwiched between protective layers of glass on the front and a durable back sheet material, often made of polymer, on the rear. The glass layer is designed to allow maximum light penetration while protecting the cells from environmental damage. The complex structure of solar panels, which combines various materials, is making disassembly difficult. This complexity is challenging for effective recycling processes, as different materials require different treatment methods.
QUASAR's ambition is to offer Europe the unique opportunity to move towards competitive PV production and a fully circular economy.
QUASAR aims to enhance the circularity, reusability, and recyclability of solar panels and has very ambitious recycling targets for all the key materials, including polymers (Figure 3).
and ethylene glycol. Subsequently, these monomers will be repolymerised to demonstrate that virgin-quality PET may be produced from the chemically recycled monomers.
The recycled PET – from mechanical and/or chemical recycling – will eventually be converted into multilayer films to demonstrate fit for
Project duration: Sept 2023-Nov 2027
Participants: 19 partners from Norway, Lithuania, Ireland, Germany, Belgium, France, Spain, USA and South-Africa
Financing: European Union's HORIZON - sustainable, secure and competitive energy supply Grant agreement no. 101122298
For more information: quasar-project.eu
Norner's role in QUASAR
Norner is responsible for developing recycling pathways for multilayer backsheet structures, in particular, related to PET recycling.
Norner will receive solar panel waste PET fractions from QUASAR partners. Norner has a proven track record related to the mechanical recycling of PET bottles. Norner's Mechanical Recycling Pilot has the necessary testing and characterisation facilities to determine the composition types and number of impurities. Based on the assessed quality of the PET waste, upgrading methods will be selected e.g. to obtain the required IV for PET film grade.
The received PET waste will also be subject to depolymerisation using a suitable small-scale setup in Norner's Catalysis and Polymerisation Pilot. Such depolymerisation results in the PET building blocks, terephthalic acid
application in the new PV backsheet. The findings shall enable QUASAR to demonstrate that the PET present in the backsheet – that is recovered for recycling – will have viable mechanical and/or chemical recycling routes for applications in the new backsheet.
Siri Stabel-Olsen siri.stabel.olsen@norner.no
Tanja Radusin tanja.radusin@norner.no
Circular solutions for plastic medical packaging have until recently been out of scope, given that PCR material from such packaging can be biologically and chemically contaminated.
Medical packaging include pharmaceutical packaging and packaging for In Vitro Diagnostic devices. These are designed to keep the integrity of the product and safety for the users, making recycling challenging. However, designs for recycling and decontamination processes are now being developed to overcome these hurdles. Large volumes of valuable PCR material streams will become available to the market once industrial processes are available. It remains to
be seen if medical packaging closed loop is a viable path. However, the market need for high-quality PCR materials for all products and packaging will increase in the years to come. The most important now is to continue development to avoid the current situation where medical packaging ends up in incineration or landfill.
Recycling medical packaging presents several unique challenges, and here are the main ones:
1. Contamination Concerns
Medical packaging often comes into contact with biological materials, making contamination a significant concern. This can complicate the recycling process as materials need to be thoroughly cleaned and sterilised before they can be recycled.
2. Complex Material Composition
Medical packaging frequently uses multi-layered materials to ensure sterility and protection. These layers can include plastics, metals, paper and other materials that are difficult to separate during the recycling process.
3. Regulatory Requirements
Strict regulations govern medical packaging to ensure patient safety and product efficacy. These regulations can limit the use of recycled materials in new medical packaging, thereby reducing the demand for recycled content for medical packaging.
4. Lack of Recycling Infrastructure
Many healthcare facilities lack the infrastructure to properly sort and collect recyclable materials. Limited space and resources within hospitals can make it challenging to implement effective recycling programs.
5. Public Perception and Safety
There is often a public perception that recycled medical materials may not be safe or hygienic. This can hinder the acceptance and use of recycled materials in new medical packaging as well as in non-medical packaging.
6. Economic Viability
The cost of recycling medical packaging can be high due to the need for specialised processes to handle contamination and complex materials. This can make it less economically viable compared to producing new packaging.
Despite these challenges, there are ongoing efforts to improve the recyclability of medical packaging. For example, the Healthcare Plastics Recycling Council (HPRC) and their industrial members are working on developing advanced recycling technologies and improving recycling infrastructure within healthcare settings. The main message is that all healthcare plastic should be safely and effectively recycled to become a valuable resource for the future.
Primary medical packaging will be excluded from the first deadline requirements for recycled content in the new proposed packaging and packaging waste regulation (PPWR). Still, it must be recyclable (in line with the required Design for Recycling (DfR) requirements defined in the regulation). These rules will become obligatory in the future, and thereof, it is important to understand how medical packaging can fit into existing DfR guidelines. Design of medical packaging must take into consideration both the upcoming PPWR as well as the regulations for packaging of Pharmaceuticals or Medical Devices.
What does this mean for medical packaging? It means that all packaging will be redesigned if necessary to be aligned with new DfR guidelines. In this process, the requirements of the packaged goods will still be a number one priority, but sustainable and circular solutions for packaging will have to be considered. Today, companies can already introduce themselves with existing tools published by RecyClass
and CEFLEX, as well as some guidelines focused specifically on medical packaging. For the manufacturers of medical packaging, it is beneficial to evaluate their products in line with RecyClass to detect possible incompatibilities with recycling that can be resolved and redesigned, providing a competitive advantage on the market.
Today, this process is defined in RecyClass methodology and can be a good starting point. The certification itself provides a pillar of trust towards both businesses and customers as a recognised quality indicator.
Norner has been a trusted development partner to companies in the whole plastic packaging value chain for many years. Recently, collaborations in the medical plastic packaging value chain have also been initiated.
Ole Jan Myhre olejan.myhre@norner.no
For more than 20 years, Norner has been involved in developing MDOPE films. This is more relevant than ever before, with its role in enabling mono-material PE flexible packaging.
Machine Direction Orientation
Polyethylene (MDOPE) films offer several significant benefits such as:
• Improved stiffness, strength, and durability of PE films, making them suitable for various packaging applications.
• The higher stiffness and strength enable further reduction of film thickness in packaging, reducing the environmental impact.
• Superior optical properties, including higher gloss and transparency, enhance the visual appeal of the packaging.
• When used in mono-material PE films, HDPE-based MDO films offer a unique recyclable solution.
• MDO films have better barrier properties against moisture, oxygen, and other gases.
These benefits make MDO-PE films a versatile and eco-friendly choice for various packaging applications ranging
food, cosmetics and healthcare as well as industrial packaging.
When the MDO process is applied to LLDPE films, highly filled with Calcium Carbonate, breathable films can be produced, which find their applications in both hygienic applications and building membranes.
The properties of an MDOPE film are highly dependent on the PE grade used due to the variety of PE technologies.
Figure: Property balance of various LLDPE types (D=920 kg/m³). All films produced as 150 µm blown film, MDO Stretch Ratio (SR) = 1:6, final film =
Through several projects we have tested different categories of PE and PP film grades. These have been processed as mono or coex films, stretched with different parameters, and the resulting films have been tested. This gives Norner a unique experience of the performance and application of MDO films.
A key result of these projects is how some polymers gain large improvements in properties while others do not. The figure illustrates the huge difference in performance of various LLDPE material types. These different types give a very different balance of dart drop impact and Elmendorf tear resistance. This and similar insights make Norner a preferred partner for MDO trials and development assignments.
MDO is suitable for a wide range of applications like food pouches, consumer packaging, magazine wrappings, laminated films, liquid packaging, labels, shrinkable films, packaging of compressible goods and industrial bags.
In one R&D project, Norner demonstrated the replacement of 40µm BOPP films with a 20µm MDOPE film, resulting in 50% downgauging of packaging films for vegetables. Compared to the BOPP film, the 20µm MDO PE film had better overall strength and performance.
During the last 6-7 years, a strong motivation for investing in MDO technology has been the increasing market demand for mono-material and recyclable laminates where MDOPE/ PE films replace OPET/PE and other similar multi-material laminates.
The multi-material laminates, which combine PE, PET, PA, and/ or PP, bring a variety of benefits, like barrier properties, stiffness for standup pouches, easy-to-seal in converting, and FFS lines, to mention a few. All of these benefits are not straightforward to reproduce with MDOPE/PE laminates, but several developments are making the situation better, such as:
• Using HDPE materials with high melting temperature of the MDOPE in the outer printing film of the laminate.
• Application of coatings like AlOx or metallisation to improve the gas barrier of MDO film.
• Incorporation of EVOH in the inner sealing film of the laminate.
• The introduction of seven or nine-layer technology in combination with MDO also enables the incorporation of EVOH in the printing film.
Norner is involved in research and innovation projects where such technological variations are explored. Our pilot facilities include
• Seven-layer blown film line by Collin
• Seven-layer cast film line by Collin
• MDO line by Hosokawa Alpine
• Mechanical testing of film
• Barrier measurements
• Polymer compositional analysis
• Microscopy investigation of multilayer films
Want to explore more? Let us cooperate!
Plastics are increasingly being collected for recycling, which is good news for the environment. We need to ensure that such resources are not wasted. Discarded plastic is regarded as waste no matter if the source is infrastructure, automotive or household packaging.
When plastic is being recycled, the products are shredded and washed before they are melted and reprocessed into pellets fit for a new production cycle. The melt undergoes filtration to remove foreign particles. It seems easy to do, but it is rather challenging to remove solid contaminations.
Sometimes, it is critical to understand what kind of impurities are in the recycled material, and there are several possible strategies to analyse this.
This is an example of utilising compression moulding of pellets into a thin film. In this way, we can easily observe the solid contaminants.
Norner uses various investigations by microscopy to analyse and assess what kind of material is in these particles. Some examples are minerals, sand, wood, sawdust, pigment agglomerates, foreign polymer, cross-linked polymer, natural fibres like cellulose, and artificial fibres like PET.
Write to post@norner.no if you need analytical support.
Norner AS Dokkvegen 20, NO-3920 Porsgrunn, Norway post@norner.no
Follow us /NornerAS /thepolymerexplorers /norner-as