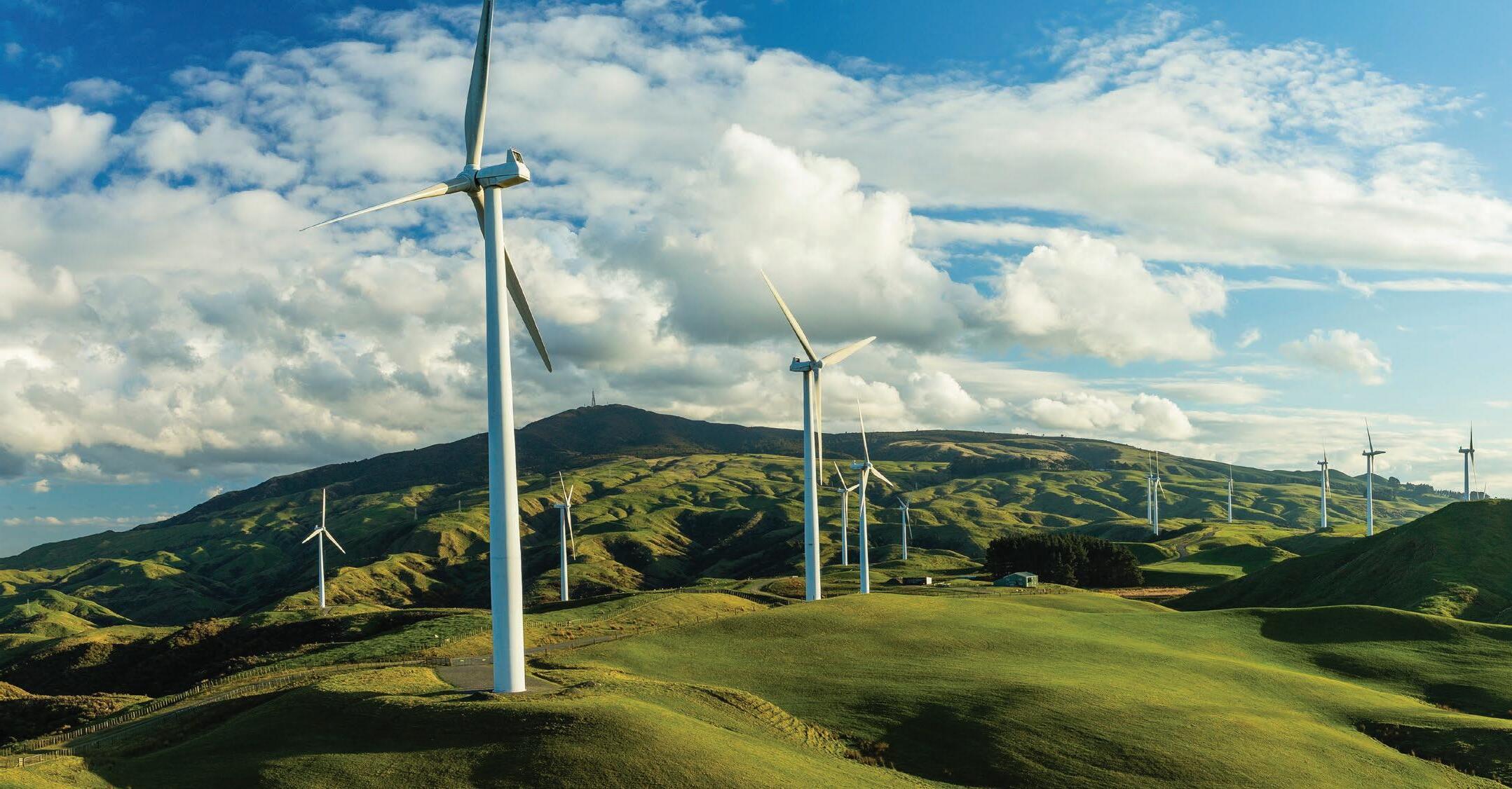
6 minute read
Transforming Condition Monitoring: Focusing on the structural health of wind turbine towers and foundations
Transforming Condition Monitoring
Focusing on the structural health of wind turbine towers and foundations
by Frank Fladerer
Traditionally, Condition Monitoring Systems for wind turbines concentrated primarily on the drivetrain. Thanks to a rapid increase in the number of wind turbines, monitoring the condition of the rotor blades also became a requirement. Today, the focus is increasingly on monitoring the tower and foundation by means of Structural Health Monitoring (SHM).
Structural Health Monitoring (SHM) is the collection and analysis of monitoring-related data from sensors located on the turbine tower and foundations. SHM data can often be used to extend the service life of a wind turbine. The term refers to the monitoring of the condition of a turbine's tower and foundations.
Wind turbines (WTGs) must produce clean energy for 20 years or longer, often operating under extremely challenging conditions. They must be reliable and, above all, safe. Unlike the USA, onshore wind turbines in Europe are installed in increasingly densely populated areas, even close to built-up areas or roads. If they collapse or parts fall off, human life could be endangered, not to mention the financial loss incurred.
Rotor blade lengths greater than 100 m, total heights greater than 250 m, rated capacities of 12 MW and higher – and the end is not in sight: Wind turbines have been increasing in size by roughly ten percent every two years, with the near-constant introduction of new materials and designs.
The risks associated with WTG construction are well known: A rotor blade can break or the tower can collapse. On the other hand, structural loads and the associated dangers are increasing due to the growing dimensions of wind turbines, and the impact of a potential collapse becomes much more severe.

SHM for lifetime extension
Once the type test's service life ends, turbine operators must choose between dismantling or building a new turbine with higher output (keyword: repowering) at select locations.
Following the standard 20-year service life, the question will arise: what is the current state of the structure? Is it possible to continue operations for another five, or even ten years? If the answer is yes, this massively improves ROI. An extended period of operation also helps bridge the "expansion gap"; the missing capacity required by energy transition targets. But to safely extend the operating period, the plant operator requires reliable data detailing (for example, actual loads on the WTG during operation compared with the original design loads).
In contrast to Europe, there are no universal legal regulations for the lifetime extension (LTE) of wind turbines in the USA. Instead, local law applies in the individual regions. However, the technical process remains basically the same.
Achieving a lifetime extension permit involves an expert report compiled by authorized experts. This happens in two stages. First, recurring inspections during operation serve as the practical part. Second, specialists investigate factors influencing the installation's resilience, examining planning presumptions against real-world results, checking feasibility of lifetime extension while addressing risk factors, tailoring maintenance plans, and eventually recommending approvals to officials granting permits. This is where Structural Health Monitoring (SHM) comes in.

SHM retrofits for added value
Modern wind turbines are equipped with systems that monitor drivetrain vibration and, increasingly, rotor blade. This is an established method for avoiding catastrophic failure of rotating components, and does not differ dramatically from the methods applied to Structural Health Monitoring.
The installation of CMS and SHM sensors during turbine construction captures the entire load history. While retrofitting sensors after construction has its limitations, operators still see major benefits from collecting this data, instead of relying solely on SCADA data and theoretical wind models.
SHM systems record actual measured load data, rather than the site-specific loads, which can only be estimated based on SCADA data. When it comes to Lifetime Extension (LTE), actual load data enables load calculation experts to determine the remaining service life more accurately than in the past as it uses more dynamic assumptions.
When it comes to the technology behind CMS and SHM, we often differentiate between hardware and software. CMS hardware detects and records turbine vibration data and converts it into analog or digital signals that can be processed by the control system. Acceleration sensors and strain gauges are traditionally implemented, with newer approaches utilizing sensors that are not subject to mechanical deformation to improve their long-term stability.
But analyzing the collected data requires specialized software. Condition monitoring experts are continuously working on dedicated algorithms and software solutions specifically for this purpose. Today, artificial intelligence plays an everincreasing role in enabling condition monitoring teams to process the growing volumes of CMS data.

Increased safety at a lower cost
Structural Health Monitoring provides information for the evaluation of structural integrity. It also helps reduce fatigue by forewarning operators about unfavorable operating situations that exert stress on the structure – the type of stress that would cause resonance within the actual natural frequency of the tower’s structure. Thus, SHM not only improves the safety of a wind turbine, it reduces maintenance costs. With reliable data concerning the precise state of a wind turbine, SHM can also facilitate lifetime extension of the WTG beyond the planned operating lifetime, putting money into the pockets of wind park owners and operators.
Frank Fladerer is a journalist with long-standing experience at daily newspapers and technical magazines. He works in corporate communications at Bachmann Electronic GmbH, which provides automation, grid measurement and protection, visualization, and condition monitoring of plants and machines. Headquartered in the Austrian town of Feldkirch with 19 locations worldwide, Bachmann is an internationally-aligned and strong-growth enterprise with intelligent, scalable technology based on over 50 years of experience in the field of integrated engineering.