
5 minute read
Big and Bigger: The opportunities and challenges of large-format solar modules
Big and Bigger
The opportunities and challenges of large-format solar modules
Advertisement
by Aaron Hall, Daryl Hart, and Joe Thorpe
The past few years have seen an amazing amount of solar module innovation. One of the biggest trends is literally about bigness—the emergence of the large-format, high-power module. With peak power ratings already well over 500 watts (and pushing toward 600 watts and beyond), these mega-modules are made possible by another photovoltaic technology trend: the transition beyond 72-cell modules featuring 156-/166-mm cells, to larger modules using cleverly manipulated 182- and 210-mm slices of silicon. Manufacturers have implemented cell-splitting, shingling and tiling, multi-busbar architectures, and dense cell-to-cell interconnect schemes (as well as bifacial technology) to drive up the power output in these supersized modules. Although the larger modules are just starting to be shipped at volume, market research firms predict they will dominate the utility-scale solar market within a few years.
Large-format modules present both opportunities and challenges for developers, engineering, procurement and construction (EPC) companies, and operations and maintenance (O&M) providers. This article will examine some of the issues around the new big modules from the perspective of all three business sectors.
Anything New Means There’s a Learning Curve
The new, larger form factor and higher wattage of these modules will mean that everyone - designers, developers, owners, and financiers - will need to ensure all the implications have been considered. One key issue is compatibility; for example, optimizers may have voltage limitations. It will also be crucial to determine whether the larger modules are pushing amps in a way that requires upsizing wires, combiner boxes, and other balance of systems components. In addition, there’s the question of possible warranty implications; specifically, whether using large-format modules will have any impact on the warranties of other components in the project, such as mounting systems that may not have been wind-load tested or certified for the larger modules.
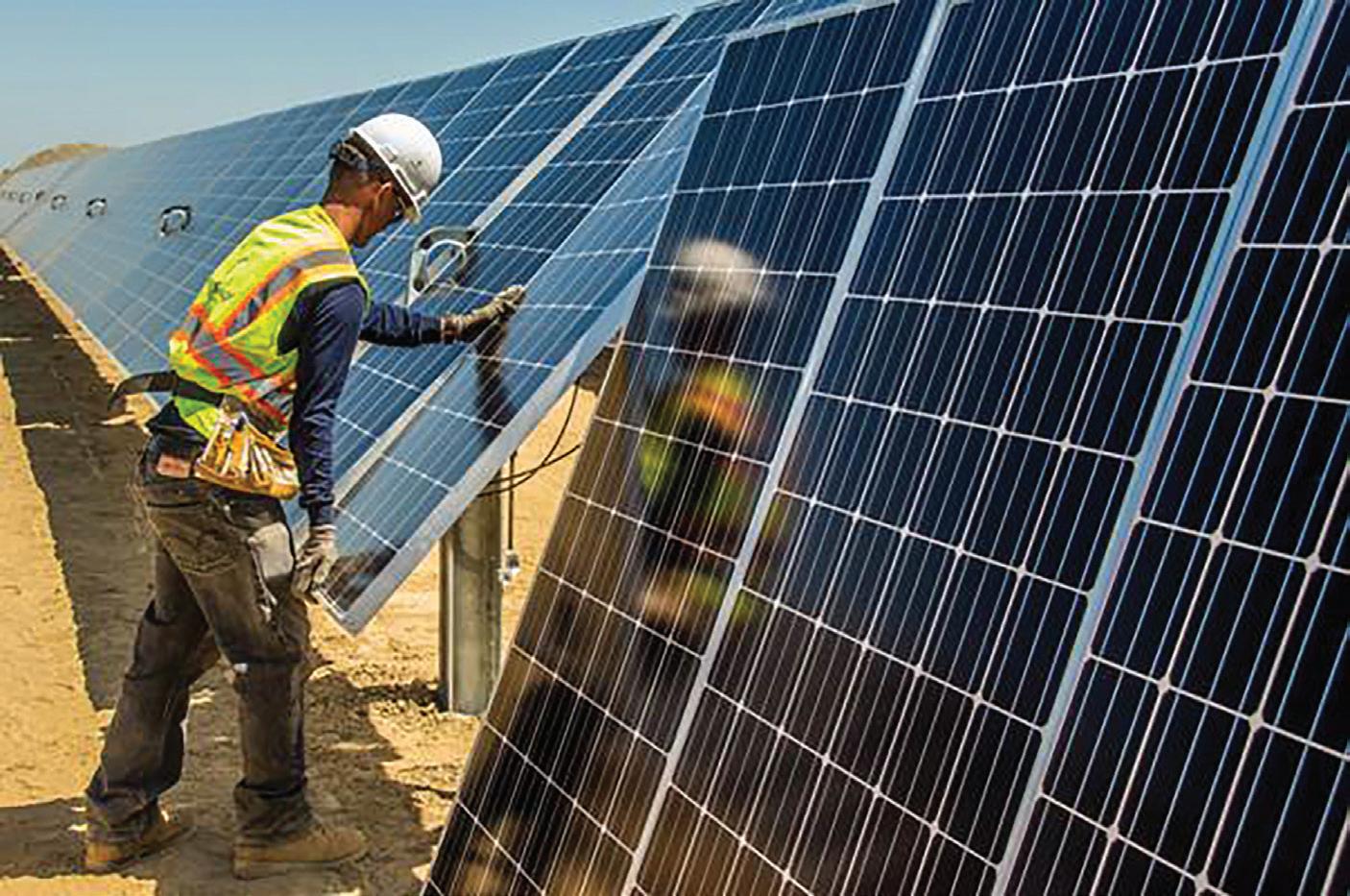
More Power Means Lower Costs
The main advantage of these large-format modules is straightforward: the higher power output per module allows a reduction in the required balance of system (BOS) and electrical BOS components and, most importantly, lower installation costs - to the tune of several cents per watt. Simply put, it means fewer modules to ship (and, in the case of 182-mm modules, more watts per shipping container), fewer modules to mount on fewer trackers or fixed-tilt racks (and more watts per tracker row), and fewer strings to connect to achieve the same installed capacity of the power plant. Plus, fewer systems to operate and maintain once the plant is up and running. The result? Decreased capital expenditures, lower levelized cost of electricity, and higher net present value, all of which has developers and asset owners excited.

From a developer-owner’s perspective, there is additional risk any time a new technology is introduced, whether it’s in terms of financial bankability, higher insurance premiums, or simply the durability and performance of the module. While Tier 1 manufacturers have (mostly) good track records when it comes to quality and reliability, it’s early days in terms of real-world power generation numbers from the mega-modules, let alone degradation, failure rates, or other field performance data. Given the larger surface area of the modules, there could be concerns with cell microcracking or susceptibility to extreme weather events such as damaging winds, hail, or snow loads.
Site Design Advantages and Tradeoffs
Large-format modules offer a tantalizing opportunity for developers, giving their landowner partners and EPCs more flexibly to utilize and benefit from the project site acreage. A space-constrained site could include additional megawatts of capacity; for many markets and scenarios, this is a worthwhile tradeoff with a corresponding specific yield reduction. This flexibility could also provide transmission system injection benefits when using a solar-plus-energy storage system equipped with large-format modules.
Site designers will need to factor in the increased module size in how they lay out the tracker rows, increasing the spacing between the mounting structures to keep the same ground-cover ratio (GCR), if that is their goal. Large-format modules do allow for a boost to the system’s DC kilowatts by increasing the GCR, while maintaining reasonable construction and O&M access (typically about 10 feet between rows).
One cannot assume that large-format modules can just be swapped in on trackers, since the tracker rows might become too long for the available north-south dimensions of the site. The varied voltage and amperage schemes of different mega-modules will require close attention to the electrical elements of the system design—a midstream change in module procurement choice could trigger a DC wiring redesign. Larger tracker structures may also translate into the need for bigger, deeper (and costlier) foundations and more robust, smarter systems that can handle the added dynamic wind-load potential. Be prepared to account for permitting issues if the height of the modules on a fully rotated tracker exceeds a typical 15-foot maximum height zoning requirement.
Less Complex O&M
From an O&M perspective, megamodules will mean less plant complexity, fewer parts to inspect, maintain and manage, and more efficient plant operations. Since labor makes up the biggest chunk of O&M costs, savings could be significant over the lifetime of the plant.
Given the large variety of module sizes and electrical characteristics coming to the market and the lack of standardization so far, the larger modules do present some O&M challenges. For example, how easy will it be to get proper replacement modules—under warranty or otherwise—in the future? The issue of inadequate supplies of spare modules already dogs many existing solar plants, and could become even more acute when the mega-module era ramps up in earnest. Taller tracker arrays may also require some additions to the onsite O&M toolkit—and hard costs in the contract—as boom-lifts will be needed to service the big modules.
Large-format modules offer a pathway to significant savings on the development, construction, and operations of utility solar power plants. It’s a safe bet that their rapid adoption into new project designs will help accelerate the clean energy transition.

Aaron Hall

Daryl Hart

Joe Thorpe
Aaron Hall is president, Daryl Hart is vice president of utility-scale project development, and Joe Thorpe is senior vice president of O&M operations at Borrego, a nationwide developer, EPC and O&M provider for large-scale renewable energy projects throughout the United States.