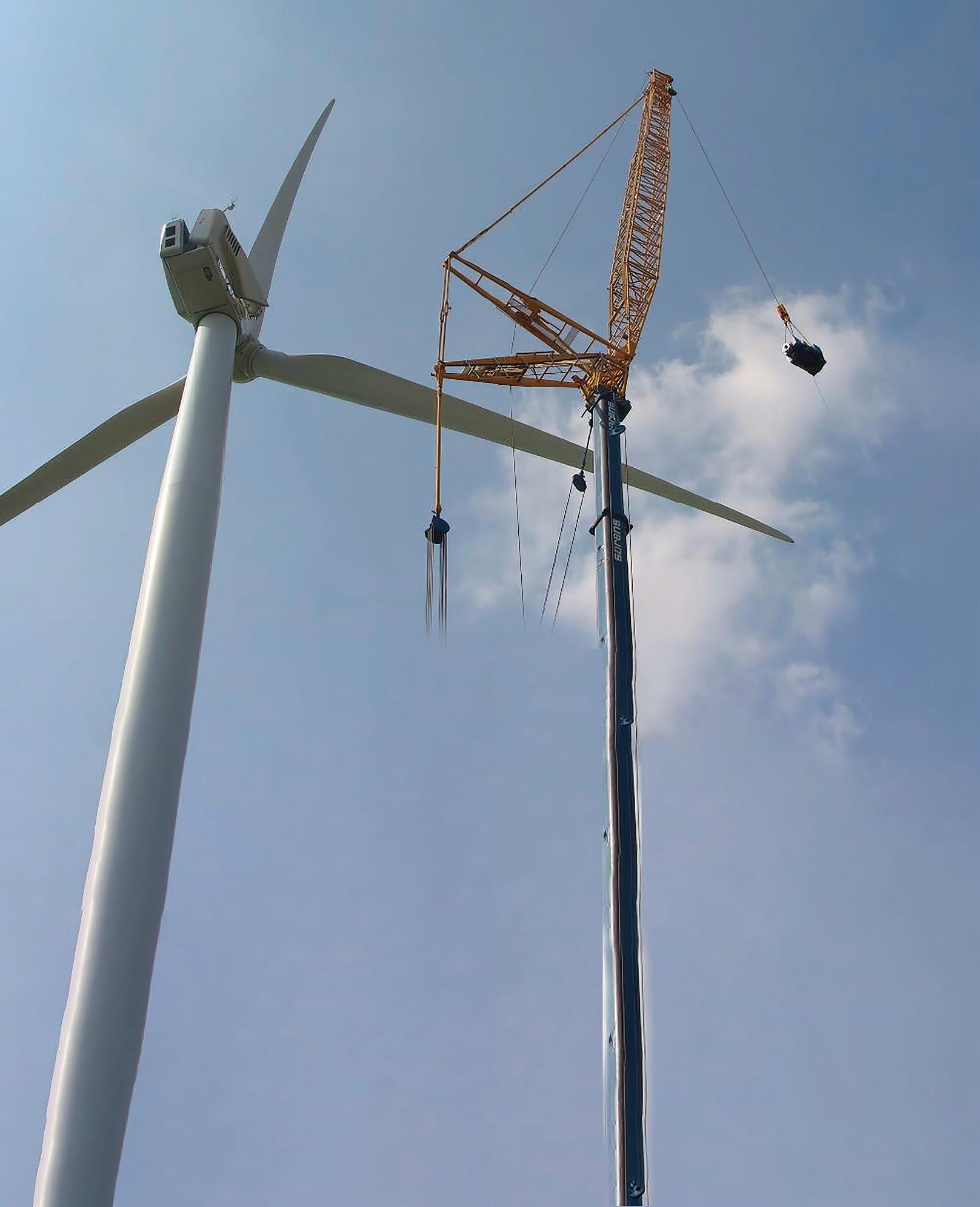
4 minute read
Advancing Wind Turbine Generator Maintenance: A case for up-tower solutions
Advancing Wind Turbine Generator Maintenance
A case for up-tower solutions
by Matteo Ghiotto
In the quest for sustainable energy, wind power has emerged as a key player, driving the transition towards clean energy across North America. However, ensuring the reliability and efficiency of wind turbines requires meticulous maintenance, especially concerning critical components like generators. Unlike traditional power plants, wind turbines face unique challenges in maintaining their generators due to the absence of scheduled turnarounds, and the logistical hurdles of sending equipment to a service shop. This article explores the significance of preventative maintenance inspection and overhauls for wind turbine generators, emphasizing the need for innovative up-tower solutions to minimize downtime and costs while maximizing turbine performance and longevity.
Generator maintenance in conventional power plants typically involves planned turnarounds or unplanned shutdowns, facilitating in-place or off-site overhauls. These procedures encompass essential tasks such as bearing replacement, cleaning, balancing, and testing, with more complex repairs occasionally necessitating component replacements or machining. However, the dynamic nature of wind energy presents distinct obstacles to this conventional approach. Wind turbines lack scheduled turnarounds, making it challenging to coordinate maintenance activities efficiently. Moreover, transporting a generator to a service shop entails considerable expenses, including crane usage and the provision of spare equipment, substantially inflating maintenance costs.
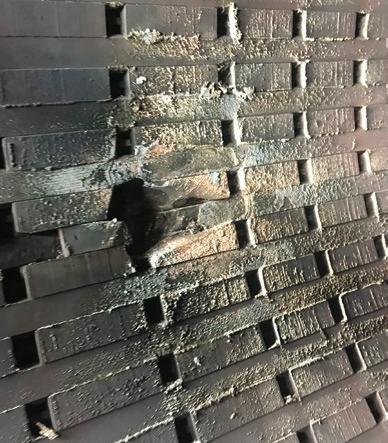
The evolving landscape of wind turbine manufacturing further complicates generator maintenance. Original Equipment Manufacturers (OEMs), in their pursuit of cost reduction and competitive advantage, often compromise component design, including generators. This compromise can lead to increased vulnerability to wear and tear, exacerbating maintenance challenges. Additionally, as OEMs push for taller and higher-capacity turbines to enhance energy output, the complexity and cost of generator swaps escalate significantly. Consequently, the traditional maintenance paradigm becomes increasingly impractical and cost-prohibitive, necessitating innovative solutions.
Generator service contractors specializing in preventative maintenance play a pivotal role in addressing these challenges. By leveraging expertise in up-tower repairs and unique solutions, these contractors extend turbine lifespan, mitigate the risk of catastrophic failures, and potentially qualify for repower credits. Up-tower maintenance involves conducting inspections, repairs, and overhauls directly on the turbine, eliminating the need for costly disassembly and transportation.
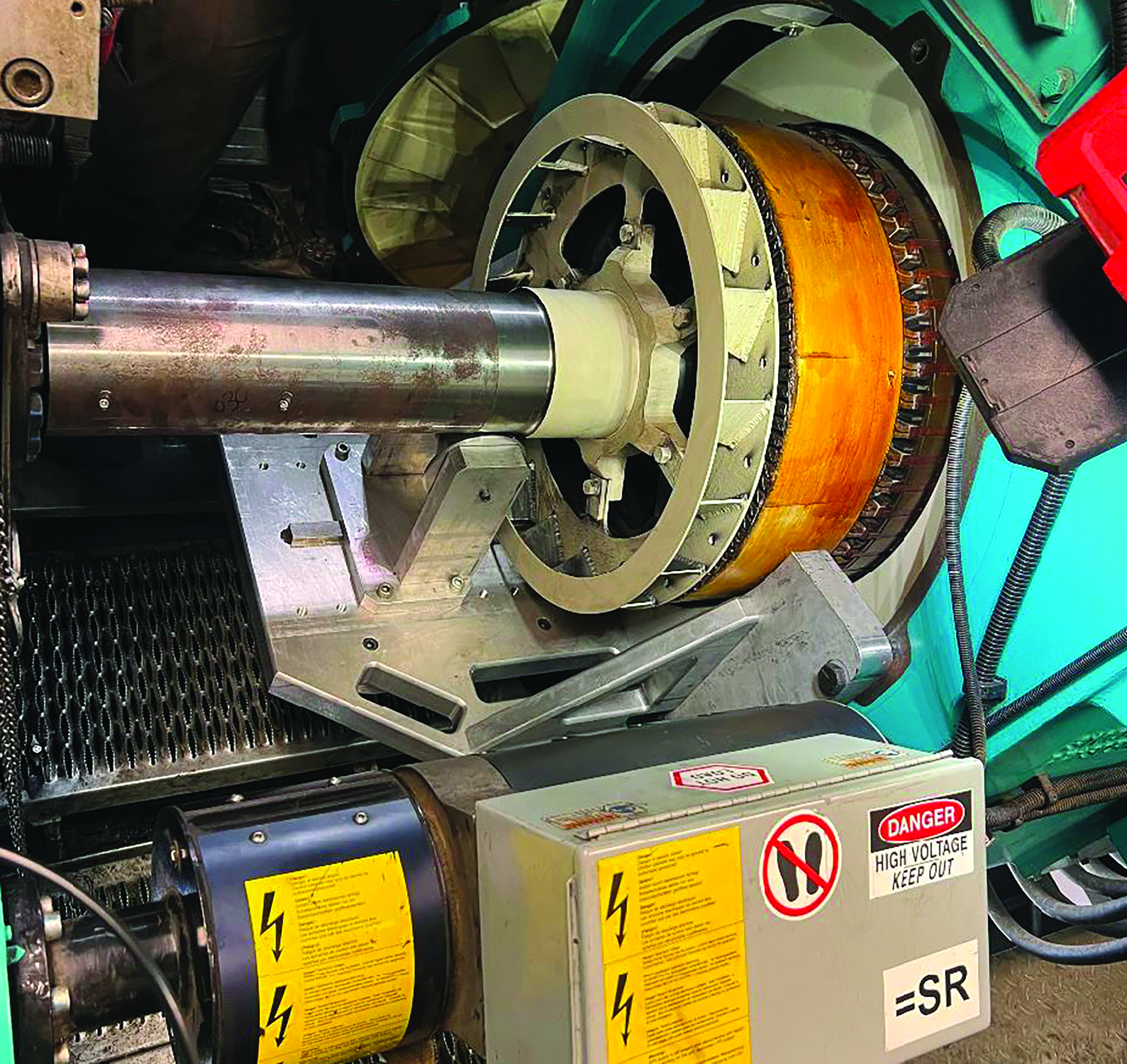
Up-tower maintenance techniques encompass a range of innovative approaches tailored to the specific needs of wind turbines. These include remote monitoring systems for early fault detection, modular repair kits for on-site component replacement, and advanced diagnostic tools for in-depth analysis of generator health. Furthermore, advancements in robotics and drone technology enable precise and efficient inspection and maintenance tasks, even in challenging or hazardous environments. Condition monitoring and inspections are invaluable for decision making, but they don’t solve maintenance challenges. Some contractors are developing unique tooling that allow for up-tower WYE ring replacement, rotor machining, dual plane balance, rotor re-banding, rotor removal for stator wedge repairs, and much more – all up-tower. By embracing these up-tower solutions, wind farm operators can streamline maintenance operations, minimize downtime, and optimize turbine performance.
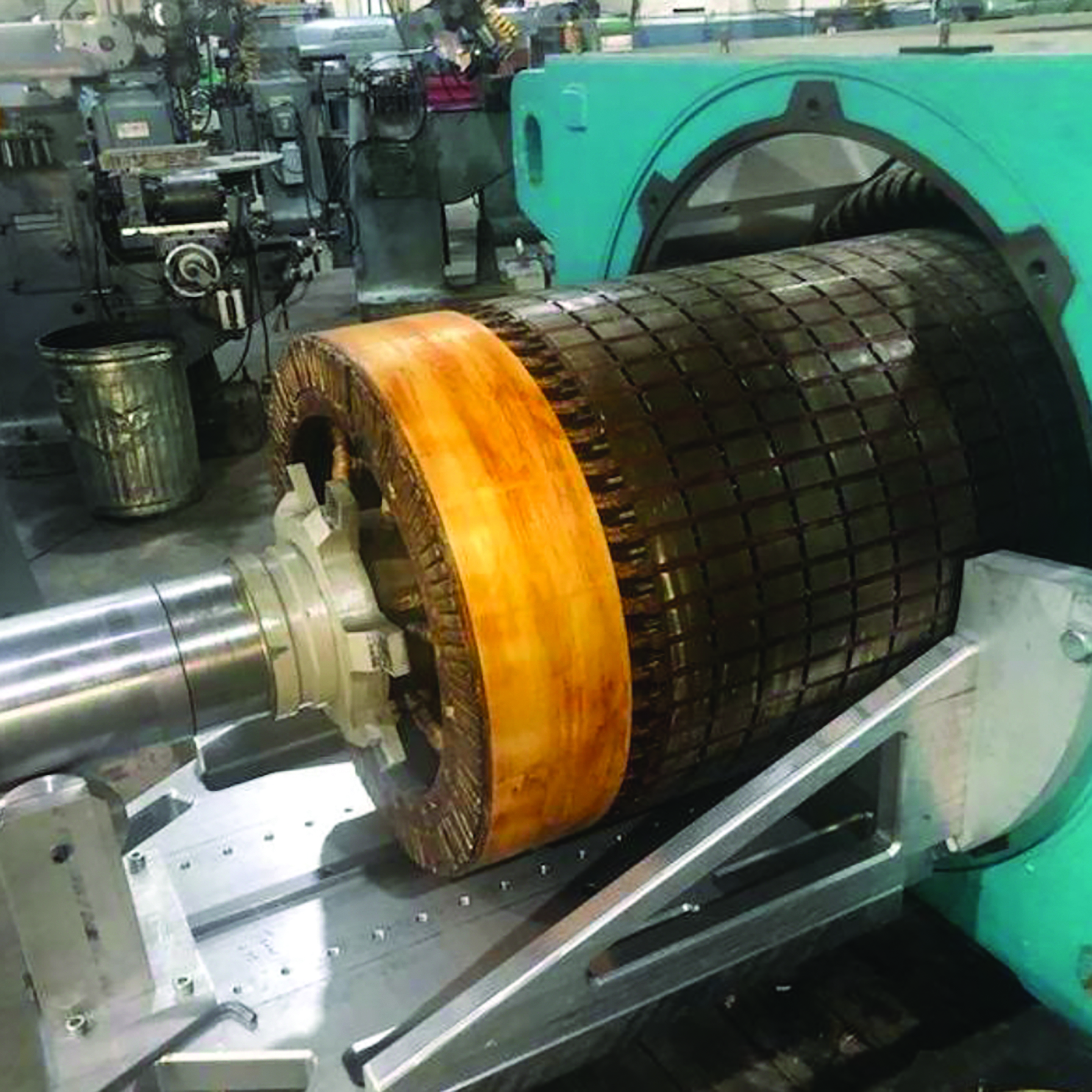
Emphasizing preventative maintenance is crucial for maximizing the return on investment in wind energy infrastructure. Regular inspections and overhauls not only extend the operational lifespan of generators, but also enhance overall turbine reliability and efficiency. By proactively addressing potential issues, operators can avoid costly downtime and emergency repairs, ensuring uninterrupted power generation and maximizing revenue. Moreover, preventative maintenance fosters a culture of safety, compliance, and sustainability, aligning with the broader objectives of the clean energy transition.
In the dynamic landscape of wind energy, effective generator maintenance is paramount to ensuring the reliability, efficiency, and longevity of turbines. Traditional approaches to maintenance, reliant on scheduled turnarounds and off-site overhauls, are increasingly impractical and cost prohibitive. Instead, the industry must embrace innovative up-tower solutions that enable efficient, cost-effective, and proactive maintenance directly on the turbine. By partnering with experienced generator service contractors and leveraging cutting-edge technologies, wind farm operators can optimize performance, minimize downtime, and drive the continued growth of clean energy across North America.
Matteo Ghiotto is US GM at Aurora Energy Services, a specialty service provider supporting the Renewable energy industry. Aurora has brought to market proprietary solutions to support its clients with better lifecycle cost and reliability for its critical components.
Aurora Energy Services /// www.auroraenergy.co