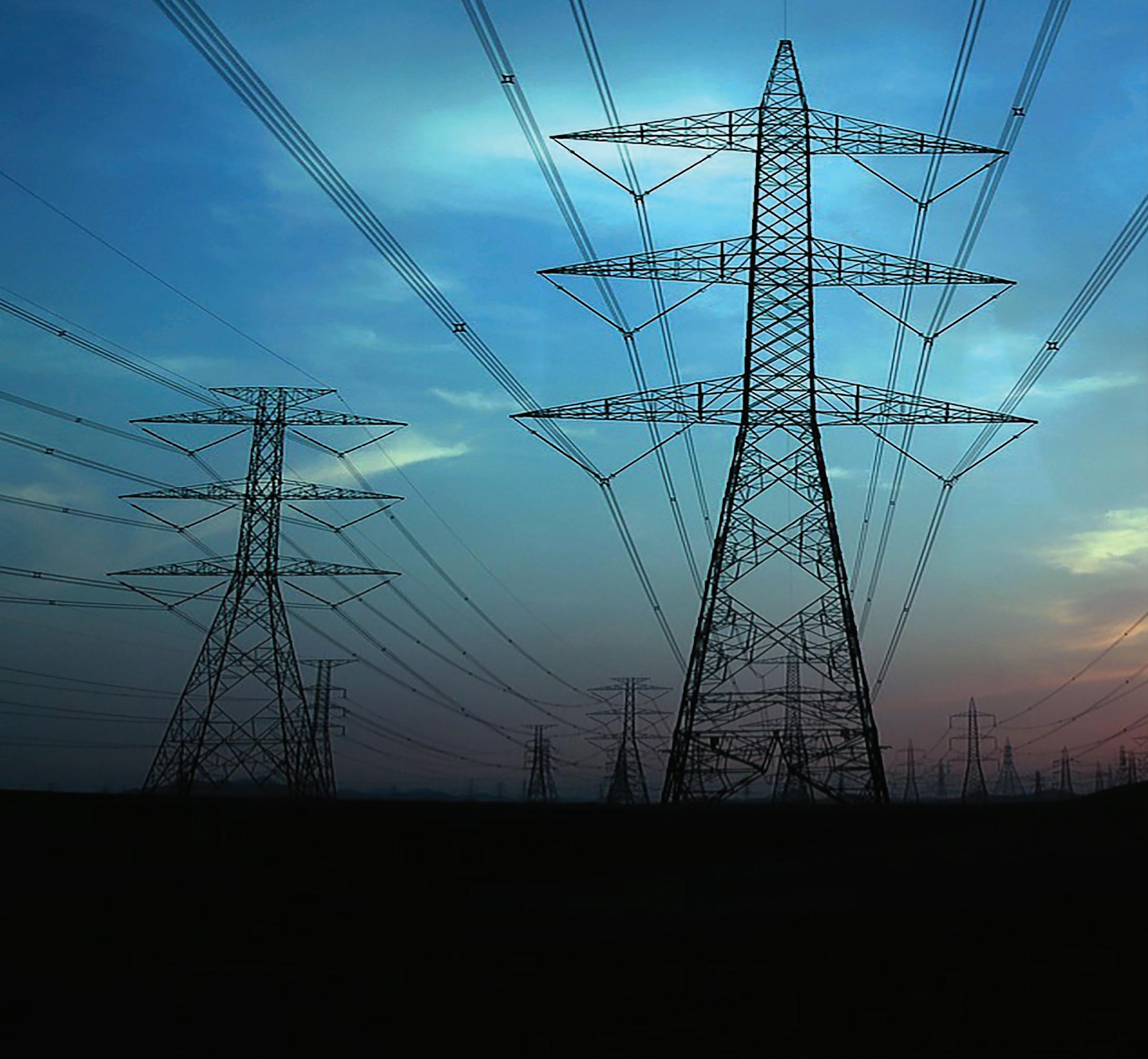
4 minute read
Beating Covid: How the worst pandemic in 100 years couldn’t stop NY utility’s first battery storage site
Beating Covid
How the worst pandemic in 100 years couldn’t stop NY utility’s first battery storage site
Advertisement
by Steven Williams
President Joe Biden pledged to reduce greenhouse gas emissions to half of 2005 levels by 2030. He also promised that the USA would have 100 percent carbon pollution-free electricity by 2035, citing clean generation and energy storage as the cornerstones. His plan accelerates New York State’s ambitious goal to achieve 70 percent renewable energy by 2030, and 100 percent by 2040.
For the New York electricity system to get there, energy storage facilities are key. COVID-19 put one pioneering utility-scale battery project in jeopardy as shutdowns loomed and the pandemic ravaged the Empire State. It almost didn’t happen but for the quick action of the contractor, developer, and state utility that managed to save the project and enable it to go live by the end of 2020. The project included building and commissioning a 3MW/12MWH energy storage facility on behalf of Con Edison Orange & Rockland Utilities, Inc.
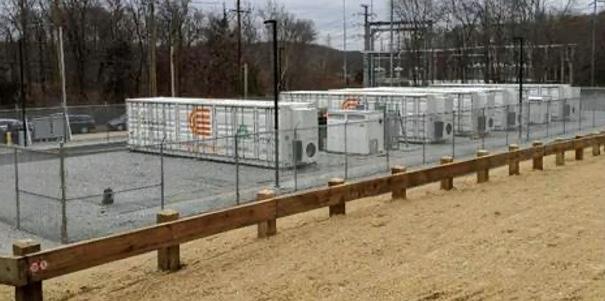
“This battery storage project is the first of its kind in our service area and represents a significant achievement to provide cleaner, more sustainable, local power while minimizing its costs to customers,” says utility CEO Robert Sanchez. “It opens the door to a brighter, cleaner, more sustainable energy future for them.”
Located in the upper Hudson River valley in Rockland County, about 30 miles from Manhattan, the $7.4 million battery storage project resembles five tractor-trailer-sized units, lined up side-by-side. The facility is designed to be a non-wires alternative facility that will ensure grid reliability, support cleaner renewable generation, and work towards meeting climate change prevention and mitigation goals.
The construction plan was highly sophisticated, and involved orchestrating numerous details including site staging, setting conduit systems and electrical equipment, installing containers, batteries, life safety and communications systems, interconnecting the facility to the utility, and then troubleshooting and testing it all. Getting a project this complex up and running is no easy feat under normal circumstances, let alone during a once-in-a-century pandemic.
“On top of COVID, we had numerous challenges from getting the building permit, to local fire code rules including a site fire hydrant, to financial hiccups, to testing and commissioning,” says Phil O’Connor, utilities manager for the contractor. “The key was solid planning, staying productive, communicating well and conducting regular reviews.”
As a unit, everyone on the job bought into the new COVID protocols for safety and efficiency. When there was an issue with concrete foundations, O’Connor and his team were able to draw upon the contractor’s in-house engineers to resolve it quickly and remain efficient for constructability.
During COVID, the fear of not getting paid also threatened to slow down the job. “Subcontractors need to be paid every other week if you want the job to progress,” says O’Connor. “We made allowances to ensure venders remained successful and they were able to conduct the specialized tasks we needed to get the battery storage system built and running quickly.”
O’Connor also hailed his field leader and technician Steve Bellows for his site leadership working closely with all the partners, subcontractors, vendors, the developer and the utility.
“We were able to overcome by keeping a positive mindset,” says Bellows. “We never gave up on the project and did whatever we needed to do to succeed.”
Bellows specifically credits his in-house site testing and commissioning team. He asserts that having those technical professionals at hand provided the owner, developer and contractor with peace of mind that ensured smoother progress and project handover at the conclusion.
“We were lucky on this project. Everyone understood the goals and the importance of this piece of infrastructure,” adds Bellows. “The partners worked in tandem to move the project along. For example, when construction noise issues arose, we quickly adapted our work schedules to ensure success.”
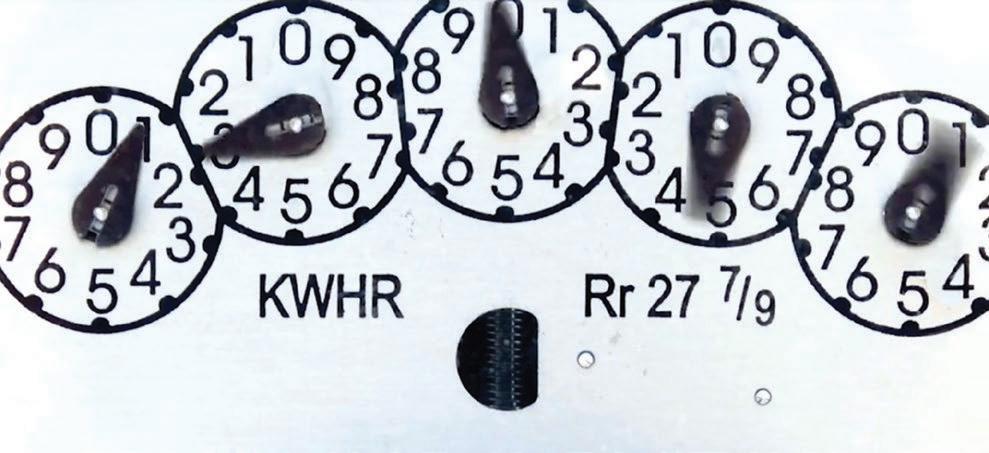
The project is projected to provide backup/battery support to about 600 residences and businesses for up to 12 hours. It also offers future revenue opportunities to sell surplus power back to the network. The battery storage project supports New York State’s initiative to install 3,000 MW of energy storage throughout the state by 2030.
What could have taken up to 18 months during COVID, the team was able to achieve in about six months or one third the time. The Rockland project proves that with the right team in place, clean energy and storage projects can come in ahead of schedule, which will make achieving clean energy and climate mitigation goals more realistic and likely to succeed.
Black & McDonald is a multi-trade construction services provider with more than 5,000 employees working out of 30+ offices across North America.