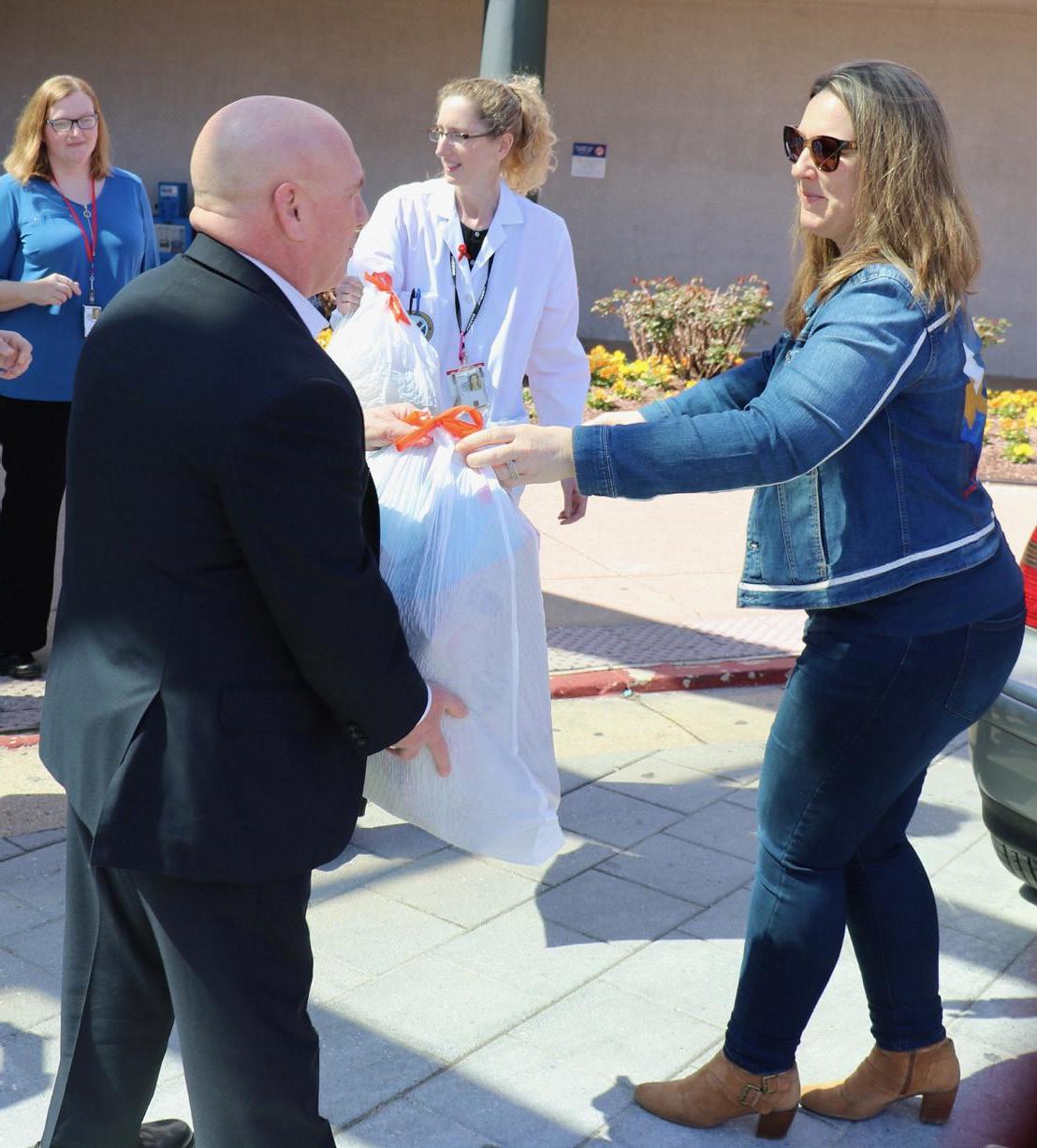
4 minute read
Nimble, Distributed Production and Delivery, aka, Team PPE Transport
Nimble, Distributed Production and Delivery, aka, Team PPE Transport
by Thant Aung
Advertisement
It was late March when I saw a Facebook post about Nova Labs’ PPE Challenge. Earlier that week, I had been reading news of medical staff not having enough PPE, so I thought it amazing that Nova Labs would be making a direct impact. I figured I’d help by making a PayPal donation as I didn’t have a 3D printer, and by the time I’d be able to get one and have it adjusted, Apple and other companies might already be making local deliveries of the much-needed PPE.
I started to wonder if I could help in some other way in the meantime? I had been working from home for a week at this point, and my family had been watching the news all day worrying about what would happen. My phone’s newsfeed was full of COVID-19 posts. I wished there was something I could do rather than staying home so I sent a message asking if I could help. I’ve learned this is a common story of how all of us have come together for the PPE Challenge. In under four weeks, our team of part-makers grew seven-fold, we took on five times the number of projects, and we’re still growing. How do we move all these parts and supplies around when we’re not allowed to get together in a single location?
In the first week, I was transporting the face shield parts from the makers to the assemblers. The tracking sheet was small enough that I didn’t have to scroll through it. Peter von Elling, Margie Foster, and I were tracking individual transports to meet the requests. The destinations were only for two primary assemblers. It was simple. As the PPE effort was taking off, more and more part makers came on board and there were individuals without 3D printers who wanted to contribute. The administrative burden was growing and it no longer made sense for us to track every single transport.
We needed to scale up our transport system and have a more structured process in place. With a new volunteer, Tiffany Winsor, Peter, Margie, and I moved to the next logical step of having drop off hubs. Luckily, more volunteers were offering to drive at the same time. Tiffany compiled a list of folks who were willing to share their locations as hubs and I started putting all the addresses on Google Maps to see where everyone was and our current transport model was born. I didn’t have any prior experience with distribution, but fortunately I recently read Marc Randolph’s “That Will Never Work,” Netflix’s early story of their DVD-by-mail business, and I borrowed some ideas. I cannot deny that my younger days of playing a ton of Starcraft might also be contributing to move armies and to gather resources around a map.
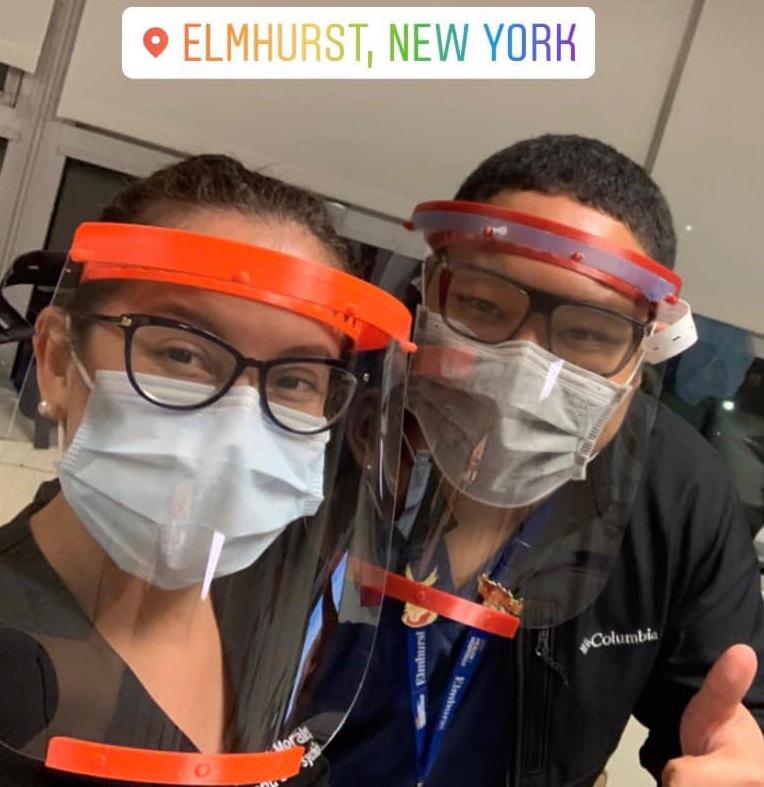
Our initial number of part makers started at ten and has grown to about eighty today. There are now ten drivers instead of two. We’ve expanded to make CPAP adapters, mask straps, Mala masks, fabric masks, intubation tent brackets on top of the face shields in less than four weeks. The final destinations now change from project to project. It is getting complex, but our tracking sheets play an enormous role in organizing these efforts. We moved from makers individually communicating via Slack when the parts were ready to them updating the tracking sheets on their own.
We progressed from having to pick up at individual locations to makers dropping off parts at their closest hubs 10-15 minutes away from them. The hubs also offer bins outside for a safe, nocontact drop off and pick up. The drivers closest to the hubs are assigned to transport parts from hub to hub. On some occasions, the drivers will pick up from individual locations if the makers are unable to drive and if the parts need to move urgently. We would need an army of drivers if the part makers were not willing to drop parts off at the hubs. This transport system isn’t possible without the makers constantly updating the tracking sheets and delivering parts. Kudos to them!
If you have a chance to look at the map of the hubs, you will find Pho Bytes in Fairfax is one of the hubs. It’s an amazing location because I’ve gotten into a habit of getting Pho with meatballs when I’m picking up parts at Pho Bytes. Not to mention they are giving 20% off if you mention Nova Labs, and they have great quality food. The owners, Nhan Nguyen and his brother-in-law, are printing 3D parts, and Nhah’s wife, Thuy Nguyen, is sewing fabric masks. They are also donating food from Pho Bytes to hospitals to lift up the spirits of our nurses and doctors on the front lines.

You can donate on GoFundMe - https://www.gofundme.com/f/pho-bytes-provides-food-for-our-front-lines-heroes
If you want to contribute to their ongoing efforts. I’m thankful to Pho Bytes and everyone else who has come together to organize and volunteer in this PPE Challenge. I’ve gotten myself a 3D printer and started contributing. I have been able to network with almost all the makers around the DMV and I have gotten help with 3D printing. There’s no ego here. People are willing to jump in to do anything that’s required and make things happen. There’s nothing like a shared purpose of meaning to help us get through these trying times.
If I may borrow Margie’s words, you should pat yourselves on the back if you’re organizing, volunteering, or contributing to this PPE effort in any way. You are awesome!