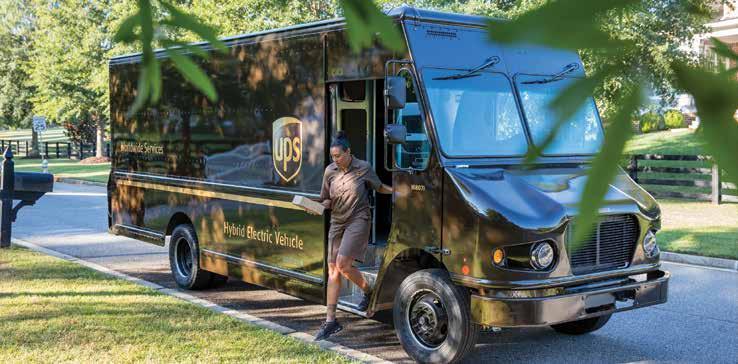
5 minute read
NRV Ride: UPS Truck
The Ubiquitous UPS Truck
I started out as a seasonal (temporary) hire in 1978, and now work in media relations at our corporate headquarters. Our last CEO began his career loading trucks while in college. So we mean it when we say we promote from within. – Dan McMackin
Advertisement
Text by Joanne M. Anderson Photos courtesy of UPS
Humble beginnings takes on new meaning when you learn that UPS (formerly United Parcel Service) was founded in Seattle in 1907 by two teenagers with a $100 loan. The numbers today are staggering:
2020 revenue - $84.6 billion Employees - 540,000 Countries/territories - 220 Packages delivered daily - 24 million or so (the world) Delivery vehicle fleet - 127,000 Jet aircraft - 550+ (owned, leased, chartered) Daily U.S. flights - 1,232 Daily global flights - 712
It is tricky to write about a UPS truck because they have so many. The firm has the largest private fleet of alternative fuel and advanced technology trucks in the world. Several still run on gasoline, others on compressed natural gas CNG. Some are electric hybrid, others are all electric, ethanol, propane, hydraulic hybrid and more which can power the engine which turns the wheels and carries the driver who hands you a package. Dan McMackin, UPS spokesperson, started his career with the company loading tractor trailers at night in high school. He worked his way through college as a part-time package handler, then a full-time driver, before holding several front line operations positions, including supervising drivers and working in the safety department. Eventually, he transferred to the Atlanta headquarters.
Driver Training
“There are more than 500 methods of package delivery,” McMackin explains. “Each driver learns how to sit, put on the seatbelt, and start the vehicle, all in one motion. Entering a truck is done with 3 points of contact at all times, which is two feet and one hand or one foot and both hands on a surface to avoid slipping or tripping. Exiting the vehicle is done in reverse, grabbing the handrail and facing the packages as you leave the truck space.” The company spends $200 million each year on safety alone.
Logistics
The large brown trucks and other UPS vehicles are not cruising
down streets randomly on any given day. The logistics of moving so many packages efficiently and carefully are vastly intricate. Superior, sophisticated algorithms have been developed to manage almost every facet of daily operation. “We have lots of experience doing what we do,” McMackin relates. “Engineering drives eliminating waste, reducing inefficiency, lessening our carbon footprint and maximizing consistency with optimum timing.” Time is money to any corporate entity, and delivery timing is the expectation of every customer. Consistency and safety are top priorities throughout the company, which spends $200 million each year on safety alone.
A very powerful math formula underpins the entire UPS network, according to McMackin. Packages are moving all the time on planes, ships, semis coming into huge distribution centers in Seattle on the West Coast and Atlanta on the East Coast along with several U.S. airports. Once here, an algorithm arranges the flow, which can be changed in seconds with the flip of a switch to adjust for variables, like weather conditions. “If there’s a snowstorm in the center of the country, for example,” he states, “within a matter of minutes or hours, delivery routes are changed, so the package is not delayed.”
Truck Interior
UPS has a vast array of excellent employment and career opportunities. “We foster careers with a culture that promotes from within, supports education, and provides excellent benefits--even to part-time staff.” [www.ups.com]
The front of the most common large brown UPS trucks seen around the New River Valley have a bare bones cab designed for optimum efficiency. The seat is bolted on an accordion-like metal riser to adjust the height. There is one cup holder, no frills and minimal distractions. A small, flat jump seat is hinged on the right for a second delivery person during holidays and busy times. The trucks are clean and have been loaded by group pre-loaders who work between 4 and 8 a.m. when the driver arrives for the day shift. Drivers have the same truck every day. Packages have been strategically placed for location and different service levels, i.e., some must be delivered by 8:30 a.m., others by 2 p.m. and more by the end of the day. The back of the truck has been organized so, ideally, there is not any hunt-and-peck activity trying to find any package at any stop. The driver’s handheld device has been programmed with all stops in the correct order for level of service, distance and directions.
Truck Check-up
Epic Road Trip
Drivers do not have routes, but delivery areas. Every driver is responsible for a pre-trip and post-trip checklist. More than two dozen items each morning include checking that a mechanic signed off on the vehicle the night before, hopefully eliminating the possibility of a breakdown on the day shift. “Drivers check that all signals, horns and lights work, emergency signal triangles are present, the gas cap is ‘leaded, threaded and sealed’, tires look good, nothing is loose under the truck and so on,” McMackin says. “Each evening, drivers will check many of the same things again, plus look for dents, scrapes, any damage, check pressure gauges, appropriate play in the steering wheel, lights work, lug nuts and rims look tight, front and rear of the vehicle is the same as it was in the morning and more.” One big goal at UPS for drivers, who may have driven a couple hundred miles and walked dozens of miles in short stints, is what they consider the most important stop of the day: When each driver is in his/her own driveway in the same shape as having left for work earlier that day. The other goal of the same value is that every customer received a package on time.
