
9 minute read
SILVICULTURE
from NZ Logger April 2021
by nzlogger
The long road to silviculture mechanisation
Story: Russell Dale and Mike Baker
WHILE MECHANISATION IN HARVESTING
has advanced in leaps and bounds over the past few decades, the same cannot be said for forest growing operations such as planting and pruning, which still rely significantly on manual methods.
However, the forest growing sector faces a number of challenges, including: • Forest owners are finding it difficult to attract people to work in labour-intensive tasks and the costs of these activities continue to rise. • Unless we can make forestry attractive to a new generation of workers this will get worse. • License to operate pressures will continue to increase where chemicals are used.
There is now the opportunity to explore whether advancements in technology can help overcome some of these challenges for forest growing operations. For example, through the implementation or further development of mechanisation, improved handtools or remote sensing, There is also the opportunity to learn from the advances made in other parts of the forest growing in value chain such as in harvesting operations.
The last time the New Zealand forest industry had a coordinated mechanised silviculture research programme was over 30 years ago, with the Silviculture Equipment Research Group.
This had some success in nursery mechanisation and mechanical land preparation. However, not much else has changed in our other forest growing operations, particularly when compared to other parts of the value chain.
Therefore, the time has now come for the forest industry, as a collective, to invest in the development of mechanisation and other technologies for forest growing operations.
A look at harvesting operations
In the 1950s all tree felling and log making was manual, with little focus on Health & Safety. Since then, mechanised harvesting has developed on flat ground, particularly over the last 25 years, but the same could not be said for steeper land.
For harvesting on steeper land, a focused effort to improve Health & Safety and
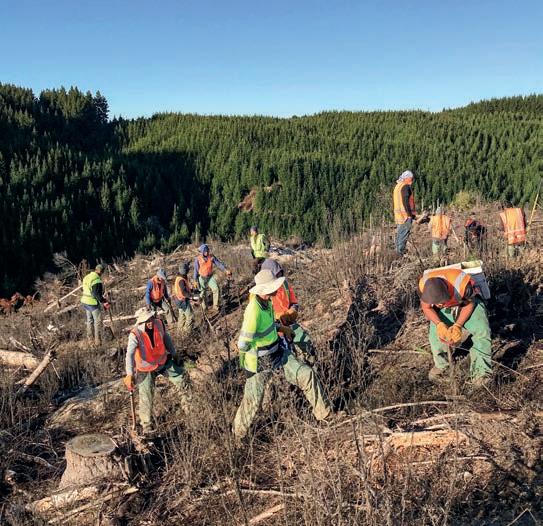
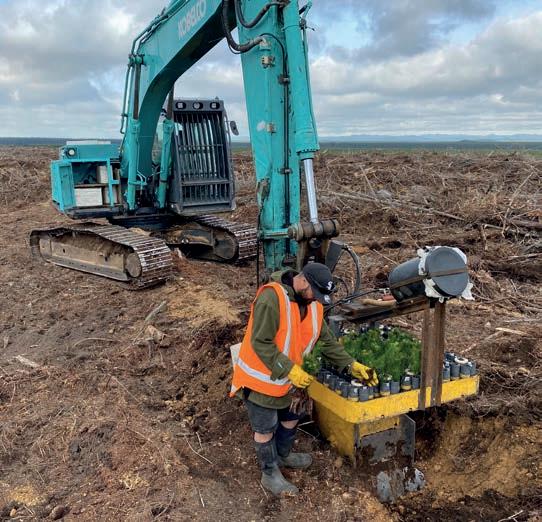
harvesting productivity has seen mechanised felling on steep country increased from 20% in 2008 to 70% in 2020. As grapple extraction and mechanised log making increased there has been a corresponding reduction in the rate of serious harm injuries and fatalities in harvesting. It was also successfully demonstrated that teleoperation of harvesting equipment is possible.
A new seven-year MPI Partnership programme, now in its second year, is looking at further mechanisation and automation opportunities beyond felling and extraction to reduce costs, eliminate repetitive manual tasks and improve data connectivity across the supply chain.
There have also been major changes in log transport from bullock wagons to the rigs of today. Trucks now showcase technology and driverless trucks are already a reality – no doubt we will soon see them entering our industry here in New Zealand, especially where private road networks exist.
Advances in remote sensing such as Lidar, radar and multispectral imagery and UAV/drone technology too, mean that we are increasingly less reliant on physical measurements from ground crews and it’s only a matter of time before all of our forest assessment will be by remote means.
A long time coming
Yet when we move to our forest growing operations such as nursery, establishment and silvicultural operations we have not made such advances.
In the early 1900s manual labour was the backbone of our forest nurseries. Today, while many of our nursery activities have been mechanised – bed cultivation, seed sowing, weed control, fertilising, irrigation – lining out of cuttings and the backbreaking work of lifting tree stocks, despite early attempts, are still dependent on manual labour.
In the 1920s, trees were planted with spades. Today little has changed. Planting spades are still used, with the difference being that the tree stocks are in plastic boxes rather than leather planting bags. Granted, land preparation and weed control have improved as has handling of tree stocks.
However changes are beginning to be considered, initially on relatively flat land, with the implementation of machine planting technology from Finland. The Top row: Changes in silviculture approaches are starting to make their mark. 2020 planting at Kaingaroa (Photo: Timberlands) and mechanised planting. Above and opposite page: Little has changed in pruning other than hi-viz. Below: There have been major changes in log transport from bullock wagons to the rigs of today.
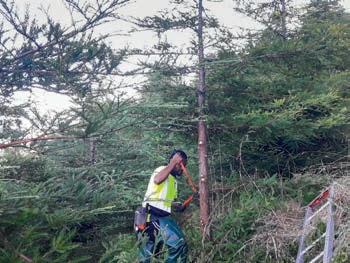



question remains if we can extend this, or other forms of technology, to steeper country and therefore the majority of our forest land.
Moving to pruning, again little has changed. Workers have hi-viz but 50 years on, low pruning is still being done with Porter pruners. Medium and high pruning has moved on from pole saws but the same ladders, Porter pruners and jack saws are still used.
Axe and poison thinning have given way to manual chainsaw thinning. However, other than improved chainsaws that are more powerful and easier on the body, the basic thinning to waste operations have not changed much in 50 years. Some thinning to waste on flat land is now mechanised, but as with planting, the real challenge is to extend this onto our more typical forestry sites.
In terms of herbicides, broadcast spraying is now more reliant on helicopters rather than fixed wing. While we have seen developments with technology in the helicopter – guidance systems and the like and nozzle technology to reduce drift – the basic broadcast spraying operation has not changed.
Does the future lie with swarms of smart drones, sensing the weed or pests of concern, and delivering targeted and precise applications of herbicide or pesticide?
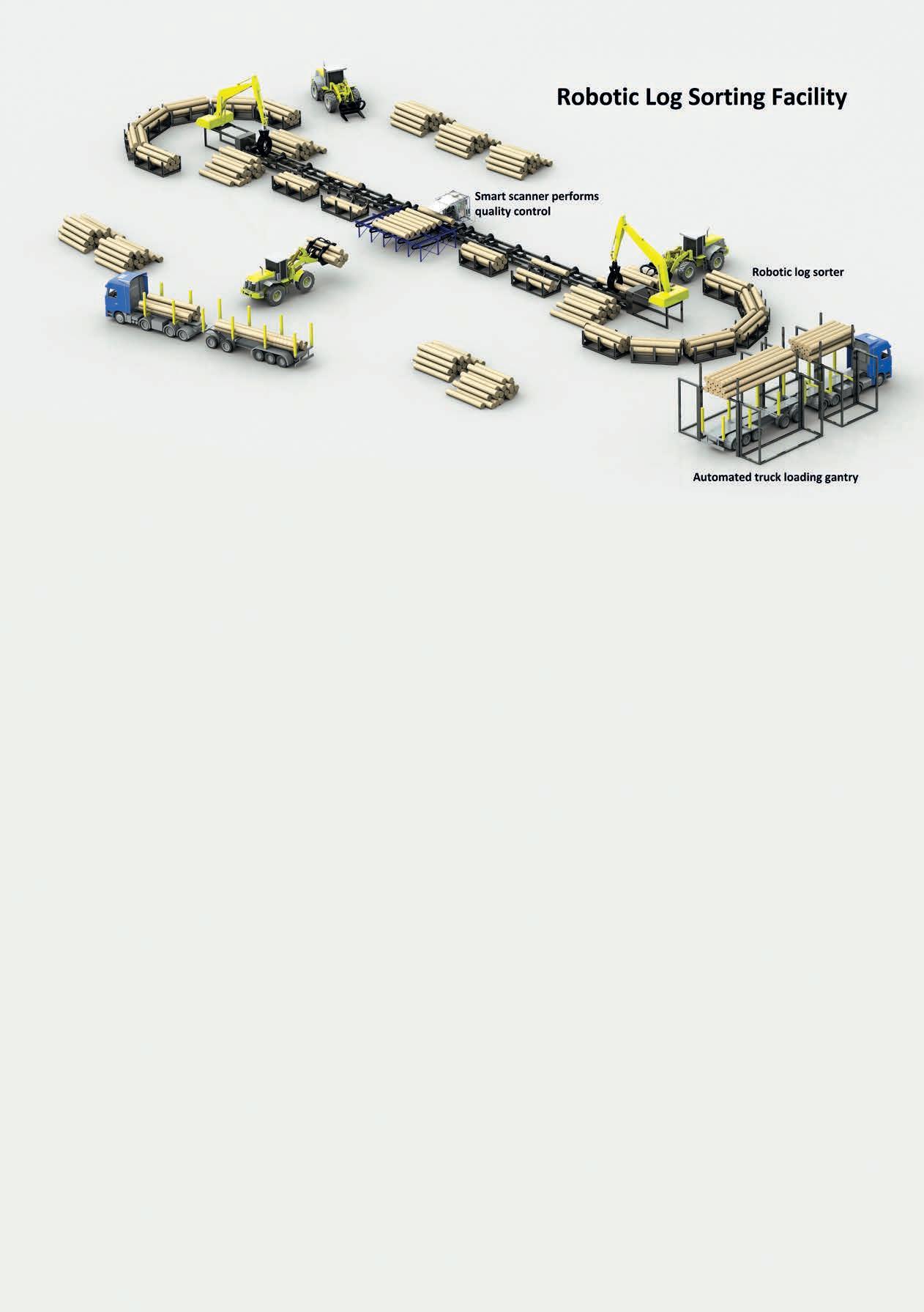
Where to from here
Whatever the future holds, it depends largely on funding and industry support. In New Zealand, funding for industry good activities in the forest growing Top: No boots on the ground, no hands on the log is fast becoming a reality. Above and below: Teleoperation of harvesting equipment is possible.


space is collected via a levy on harvested logs. Approximately two thirds of this is allocated to research and development. This funding – around $5.5 million in 2020 – also attracts leveraged funding from industry and government. Forest Growers Research (FGR) was established in 2008 to coordinate and manage industry investment in Research & Development. It manages research across the forest growing value chain, from biotechnology to harvesting and supply chain management, including some new special purpose wood product development.
With the more recent interest in mechanisation, an initial survey was carried out in 2018 of some of the larger forest growers in New Zealand to see whether there was interest in developing a research programme for mechanised silviculture. This led to a facilitated workshop being convened by Forest Growers Research in late 2019 with a group of industry personnel, with the aim to discuss industry interest in exploring further mechanisation opportunities in forest establishment and silviculture.
There was strong interest in the topic, and also support to develop the ideas into a new

Left: Planting spades are still used today. Opposite page: Other than improved chainsaws, basic thinning to waste operations have not changed much in 50 years.
programme of work targeting government co-funding.
The outcomes of this workshop provide the direction for the development of an industry research programme. Participants initially identified six key focus areas: • Nursery mechanisation and automation • Precision planting including mechanisation • Mechanised thinning to waste • Mechanised pruning • Precision forestry systems • Reducing herbicide use
Following the workshop, participants were asked to indicate their priority rankings and how much effort should be allocated to each area. The results were broken down between large forest owners (representing about 1 million ha) and small forest owners.
Precision planting including mechanisation was identified as the main focus area, followed by mechanised thinning to waste, precision forestry, mechanised pruning, reducing herbicide use and nursery mechanisation and automation (see table below).
Areas of focus (% effort) Projects % Effort
Precision Planting/Mechanisation (25%)
Mechanised planting 60
Precise tree locations 20
Optimal planting alignment 20
Mechanised Thinning to Waste (20%)
Automated tree selection 45
Improved hand tools 30 Mechanised felling 25 Smart forest inventory 50
Areas of focus (% effort) Projects % Effort
Optimal stockings by genetics 30 Worker proximity 20
Precision Forestry (20%)
Power assist hand tools 45
Mechanised Pruning (15%)
Reducing Herbicide Use (10%)
Nursery Mechanisationand Automation (10%)
Full mechanisation 45
Partial mechanisation 10
Precision guidance and application of herbicides 70 Remoteidentification of weeds 30
Mechanised lifting, trimming & grading 55 Precision weed control 25
Automated tree stock counts 20
Some of the projects identified and prioritised by participants include steep slope mechanisation, automated tree selection for silviculture based on remote sensing techniques, and incorporating power assist into hand tools.
Of course, full mechanisation of operations such as pruning will involve a lot of development and trial work and is not without risk, but it will be a game changer if successful.
Currently FGR is progressing with smaller, more focused workshops to further develop project plans in each focus area. These will form the basis of a business case to both industry and government funding bodies during 2021.
Over the years mechanised silviculture has been attempted in New Zealand, some methods successful for their time and conditions and others not. With labour availability and quality likely to be an ongoing factor for our industry, the time to invest in and adopt new methods has finally come.
If you are interested in participating in this work or would like to learn more please contact Bart Challis (bart.challis@nzfoa.org.nz). NZL

SAVE ON INFRASTRUCTURE! INCREASE PRODUCTIVITY! IMPROVE HEALTH AND SAFETY!

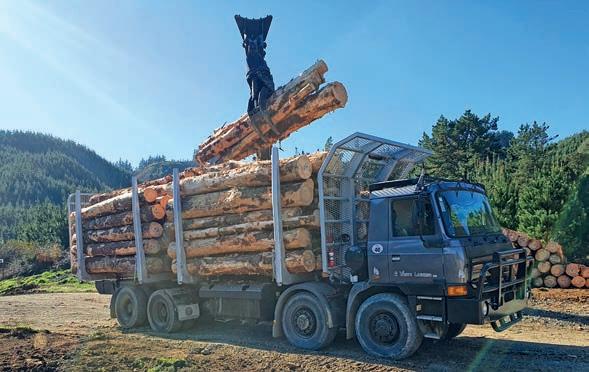
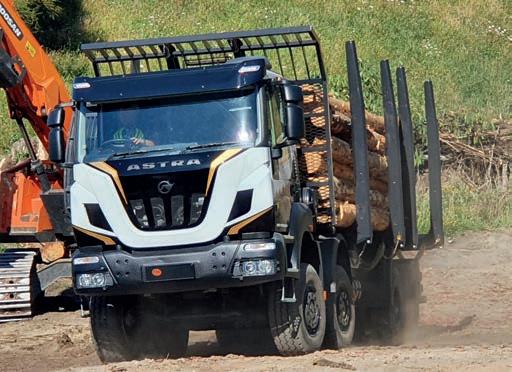
