
13 minute read
LIQUID BIOFUELS
by nzlogger
a major source
UP TO 30% OF IMPORTED FOSSIL FUELS
could be processed in this country mostly from woody biomass derived from plantation forests according to research completed in 2018.
The principle feedstock is from exotic plantation forests, and other mostly vegetative sources. Researchers predicted savings of over $1 billion, which is currently attracting serious attention from government agencies and the forest sector.
The emphasis is partly based on climate change but interest is being spurred by escalating fuel prices, conflicts in the Middle East and Eastern Europe, supply problems of both fuels and gas, not to mention disruptions due to the worldwide pandemic and inflation.
New Zealand’s plantation forestry resources are renewable, sustainable and have a low carbon footprint through the cycle of establishment and management through to harvesting and processing. These forests sequester C02 during the growth period and some of it is retained in products such as sawn lumber, Cross-laminated Timber (CLT) and Medium Density Fibreboard (MDF). Mills often generate their own process and drying heat energy from residues created during log processing. By-products include wood biomass to replace coal for heat energy.
The time for bioenergy is ripe according to the current Bioenergy Association but it is dependent on Government policies and public and private investment to achieve the economies of scale to produce liquid fuels such as heavy fuel oils for shipping, diesel, petrol and even aviation fuel.
The technology for conversion of woody feedstock into a bio-crude and then into liquid biofuels has been undergoing small scale experiments over the past couple of decades.
An earlier Scion study into the economics of feedstock conversion found that in-forest sources of residues, including low grade and reject log, offcuts and slovens as well as large size branches, were the most costeffective. Other sources included oil-rich crops such as rapeseed and canola, cane crops, orchard and municipal gardens/ reserves as well as wood from demolition ending up in landfills, organic vegetation and cooking oils.
The Bioenergy Association's Brian Cox indicates future innovation to reach economies of scale cannot be left to the market. It will rely on support from government and its agencies to get started with some form of encouragement through regulations, legislation and innovative startup funding.
Biofuels was listed on the Government’s Emissions Reduction Plan in the May budget, mainly targeting solid energy to replace coal fed heating systems.
Quoting from the latest paper from the International Consultancy firm Indufor, Ernslaw One's Peter Weir notes that "under current settings" (limited trials) "conversions of biomass to liquid biofuels is uneconomic".
Referring to the Government's climate
Story and photos: Jim Childerstone
for liquid biofuels
budget, Grant Dodson, President of the NZ Forest Owner's Association (FOA), says the FOA welcomes this investment by Government and looks forward to its members partnering, where appropriate, on delivery of these initiatives. Among these was "development of systems to recover more forest residues for bioenergy" and enabling Crown investment. "The FOA actively promotes the significant contribution forestry makes towards climate change objectives. The Association continuous to facilitate the investment of levy funds into research including research into bioenergy. In addition, the association is a key partner in the Forest Industry Transformation Plan of which bio-energy initiatives form a part. Liquid bio-energy forms part of the wider package,” Grant explains. "Expertise has been developed at Scion through research funding and it is reasonable to expect that increasing numbers of liquid bio-energy products will eventuate," he adds. Above: Billet wood residue on the skid site – a potential chipping resource. Below: Offcuts, slovens and reject log suitable for biofuel processing.
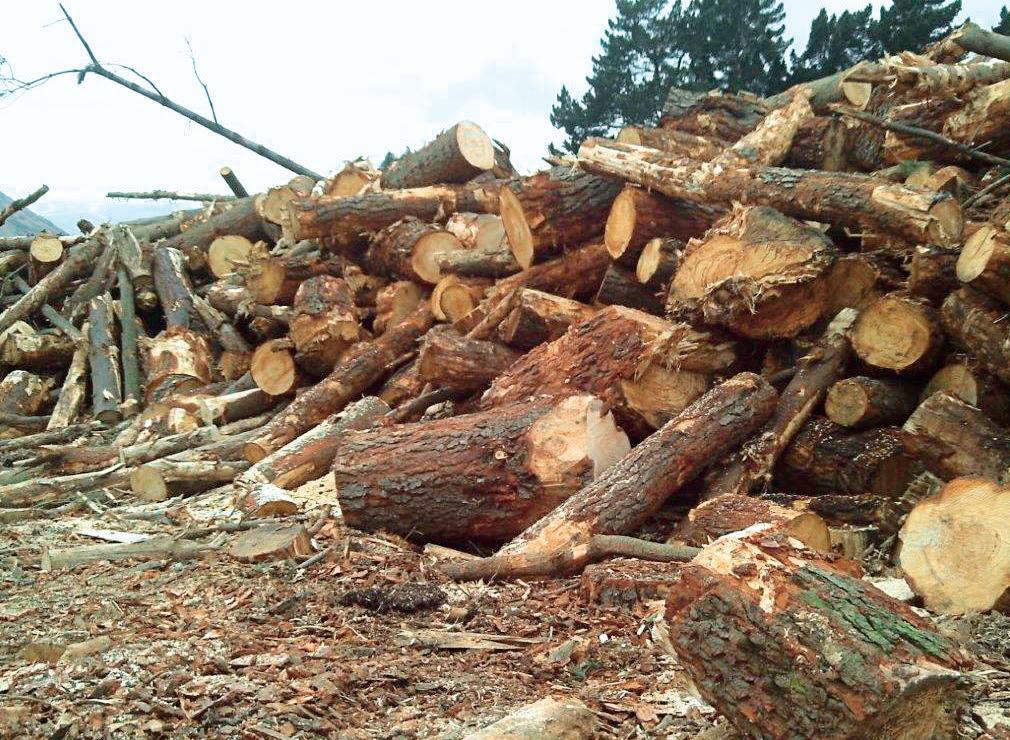
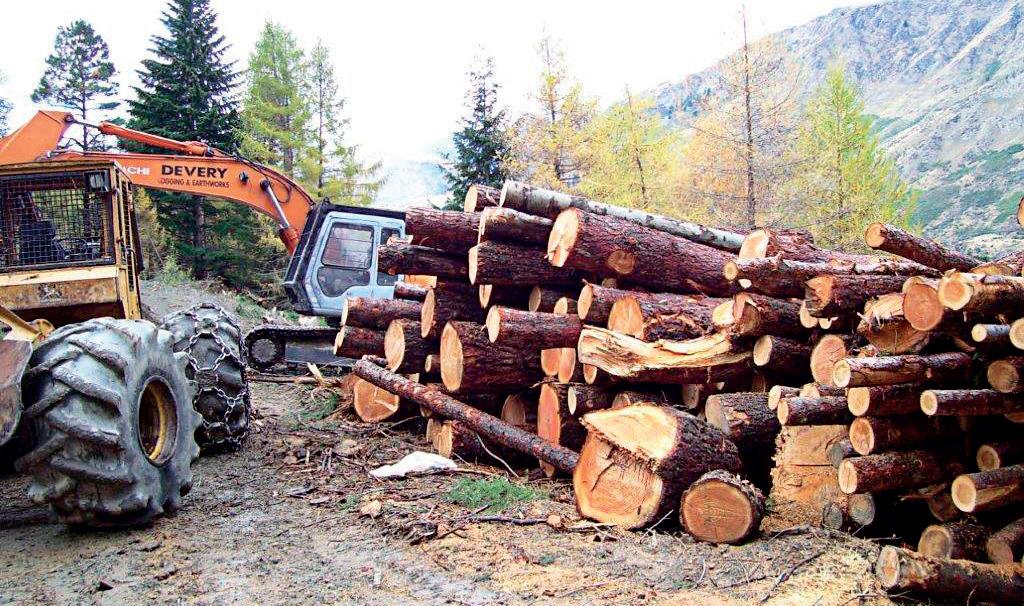
A RECENT BIOENERGY ASSOCIATION
Webinar noted that there is enough biomass, close to 11 million tonnes per year, to meet an initial assumed target of 150 petajoules (PJ) of energy to replace fossil fuels. This would reduce greenhouse gas emissions by 157m tonnes CO2 p/a by 2050, says a paper by Crown Researchers. And 70% of feedstock is derived from current plantation forests. In 2021 forests registered in the ETS sequestered 6.7m tonnes of CO2 and stored another approximately 417m tonnes.
Of the approximately 11.6 million green tonnes of material estimated to be available during the period 2026 to 2030, 4.4 million tonnes (38%) is K grade logs, 1.8 million tonnes (15%) is pulp logs (which are surplus to domestic demand), and 2.6 (22%) million tonnes is in-forest post-harvest residues and a range of forestry and primary production based residuals, including straw (0.5 million tonnes or 4%).
Wood processing residues are largely used for mills’ internal energy demand. Other sources include municipal wood waste, shelterbelt and orchard turnover as well as wood and bark residues generated at ports. To achieve full use of the potential energy depends on government policies and willingness of industries to get stuck into bioenergy projects. In the meantime these figures are mostly estimates of potential availability based on assumptions derived from a number of studies.
The volumes of residues and logs available are projected to drop over the next 25 years due to the current "wall of wood" coming on-stream from 2019-2021. However, with further government help, including the One Billion Trees Programme, the volumes are expected to ramp back up by 2050, in part due to increasing hectares of planting seen in 2021/22.
The forest by-product of residues, including rejects and low grade logs, would go through a standard chipping or shredding process. After screening, and in some cases drying. The woody biomass then goes into one of a variety of potential processes; for example gasification and Fischer-Tropsch, hydro-thermal liquefaction or fast pyrolysis and upgrading.
Further, a Bioenergy Association paper observes that ''the economics of extracting biochemicals from biomass to replace petroleum-derived chemicals and plastics etc. is fast emerging internationally, although New Zealand is behind in recognising the economic opportunities".
It notes the gap between current bioenergy use (50 petajoules) and the assumed immediate potential bioenergy demand (150 PJ) driven by process heat transition from coal. The emerging demand (and potential liquid biofuels sales obligation) for transport biofuels, and need to replace natural gas, can be met by better using existing biomass residues.
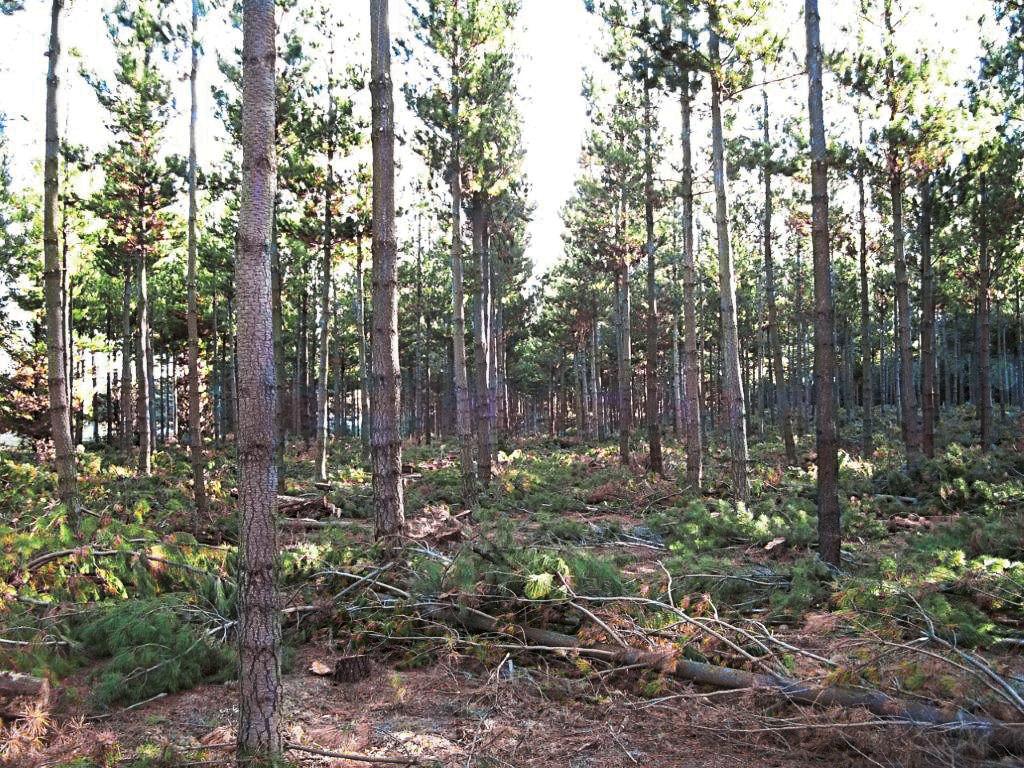
Above: Third lift thinning can be recovered for biofuels. Below: Reject logs and offcuts ready for chipping.
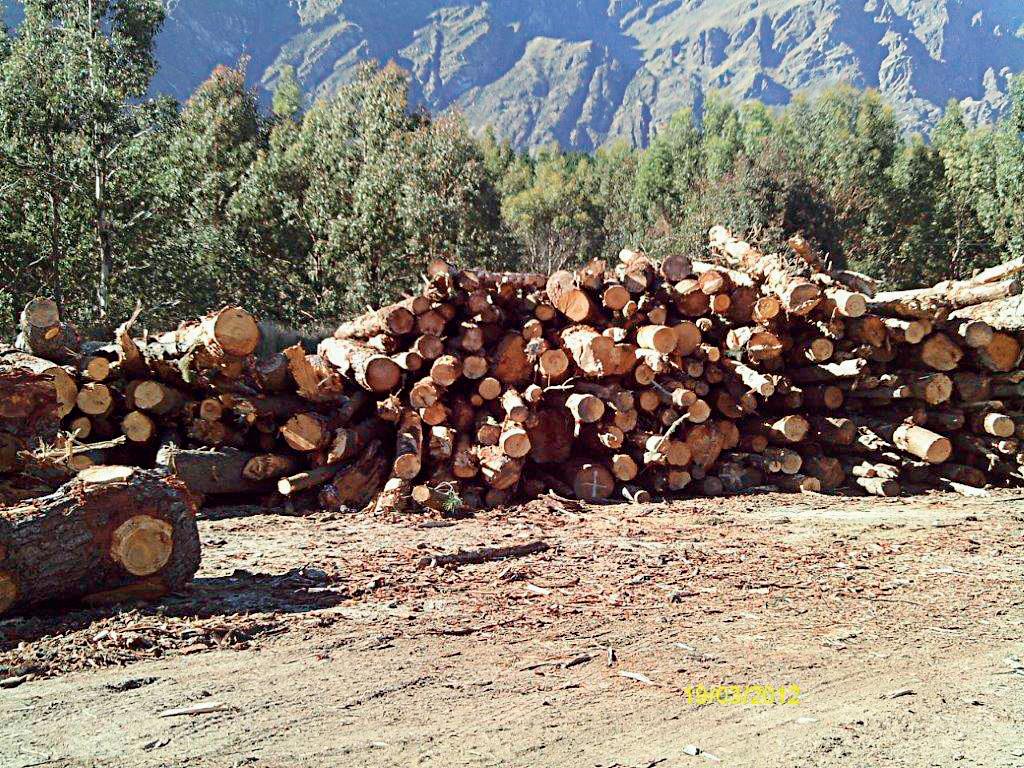
IMPROVING BIOMASS RECOVERY
RESPONSES FROM OWNERS AND
managers indicate they are upfront with what is required from in-forest biomass recovery, particularly with harvest operations.
The FOA's Grant Dodson says the economic recovery of wood suitable for wood energy use is increasing and is expected to increase exponentially in coming years as demand increases. "Individual members will have opportunities to explore opportunities during harvest as they seek to maximise recoveries from their forests. The mix of bioenergy end uses that each company supplies will depend on the regional demand profile," he says.
Speaking on behalf of Port Blakely, Timaru-based Andrew Cocking, stresses the importance of this developing technology.
Port Blakely "is actively recovering residue material (bin wood) from its logging operations. Logging crews recover this material like all other grades on a cutting instruction" since 2019, he explains. "This material and sometimes long-length chip logs are carted away from the landing and stored on older skid sites in the forest where it is dried for 9 to 12 months," he adds. It is then on-sold to energy companies who are invited to chip logs on site.
The chips go to the Washdyke Energy Centre owned by Alexander-based Pioneer Energy.
Andrew says the company provides fibre material in its forests to both Arundel-based Canterbury Woodchip Supplies and Pioneer Energy.
With steep country hauler operations, bin wood tended to be cast over the side of the skid, says Andrew. "This now can be recovered by specially adapted bin trucks developed by local trucking company Phillip Wareing out of Geraldine Forest." "They now have a double bin wood/ crane unit to meet our growing recovery programme across two more hauler crews," he says. "Working with energy producers directly and the customers is a good model. Port Blakely residue is helping to fuel the energy needs of the DB Brewery Plant in Timaru. We like (it that) our forests are helping to make beer," he jokes.
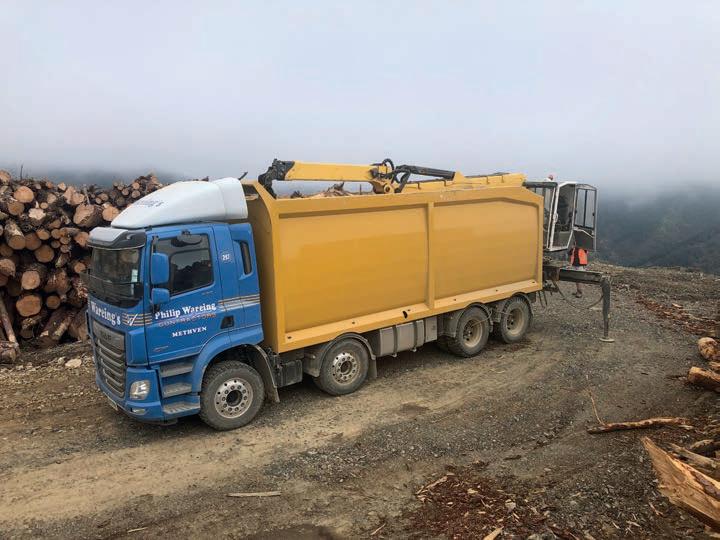
Wareing Transport's specially adapted bin truck with mounted crane to salvage billet wood off the skid site.
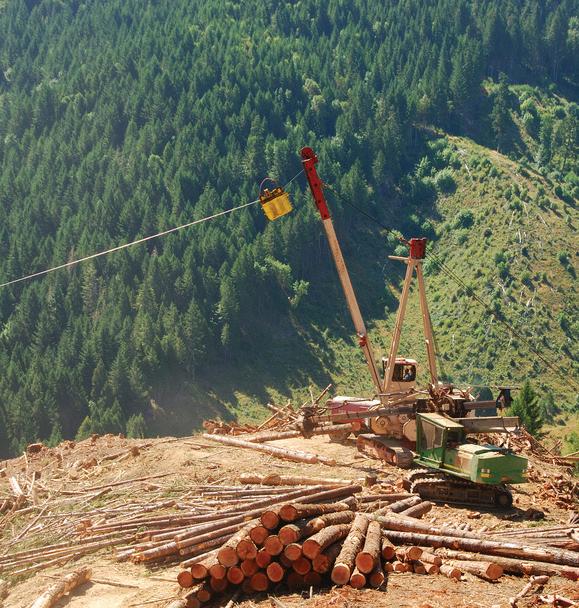
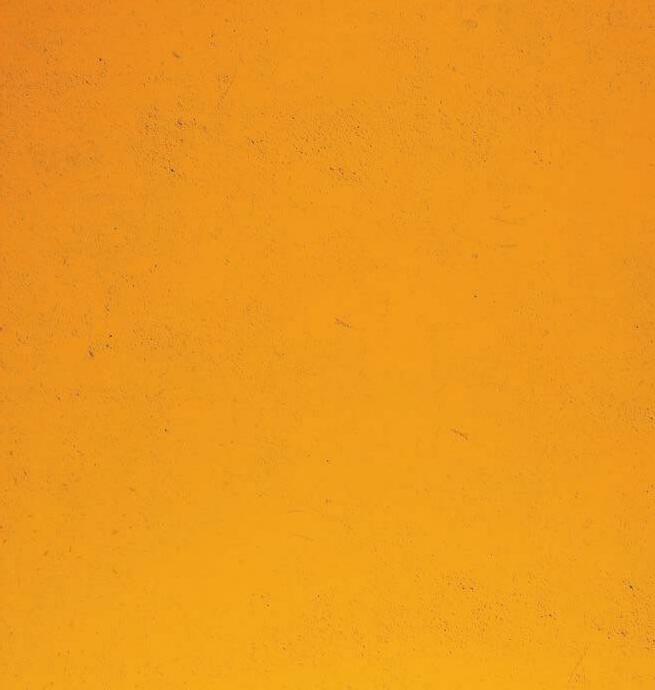
Dunedin City Forest's Kent Chalmers says there was merchantable volume, particularly billet wood, which had not been sold because it could not be shifted off site fast enough. "So our focus has been on building our customer base to keep this volume turning over. To this end we supply Daiken (MDF plant, Mataura), Pioneer Energy and Lumbr Ltd. "We have also started stockpiling volume in-forest. Our view is that central yards are the best bet, if I'm going to put a log on a truck I might as well cart it closer to the end user. "We are seeing demand is ramping up before yard infrastructure, so we are storing volume in the bush as there are no places to put it,” he explains. "We are still chasing the idea of getting as much volume loaded by the crew as we can. "My vision of how the market will develop is that we will continue to get as much off the site as possible when the crew is there, and that specs of what customers will take will get wider as demand increases."
Kent believes that as demand ramps up and crews get better at loading and sorting volumes, biofuel processors could be invited to collect residue off the site. These operations could then move into the cutover. This would then provide enough volume to make that viable. "Rising prices for this material will make it possible to reach further into the cutover as well," he says.
Wenita Forest Products CEO, David Cormack, told NZ Logger that Wenita has been watching recent developments in the forest residue space with interest, especially in terms of large industrial coalfired boilers in the Southern provinces. "Earlier this year we gave permission for a company to extract residues from a handful of our old skid sites," he says. "We did this on a trial basis to see how it worked out for them, as well as ourselves. The trial confirmed that only modest volumes remained on our skid sites, after our usual pulp logs, billets and firewood had been extracted and sold.
He advises that to increase volumes and reliability of supply, energy users will have to consider low-grade export logs into the mix, even KI Grade. "Even some of the major forest owners will struggle to meet the supplies of these energy users and we will have to consider how we can cooperate and combine our volumes," he says. "This is a new business opportunity for forest owners and those we contacted are interested to support and grow biofuel production."
Hamish Anderson of Independent Forest Service's One Forest says reject log and billet wood had been put aside mainly for Daiken's MDF Mataura plant in Southland, but recently had supplied Pioneer Energy from a Central Otago site.
Ernslaw One’s Peter Weir believes the economics of converting woody biomass from clean harvesting residues and chipping of whole logs to liquid transport fuels at scale are very different, as outlined in the new Indufor Report.
Peter explains that woody biomass left over after harvesting in combination with lower grade logs when chipped at scale are "probably a cheaper fuel source". It would conveniently allow industrial heat plant users to switch from coal to wood chip.
Back in 2008 the company partnered with the Energy Efficiency and Conservation authority (EECA) to develop a fast pyrolysis plant that produced bio-oil from chipped radiata which could then be used to co-fire a boiler, Peter says. This was "further refined to create a synthetic diesel substitute that could be used as a drop-in fuel for large old diesels such as KiwiRail locomotives or in ships such as bunker fuel oil ". He reiterates that "although we proved the technology, the economics of the time were against us" with the advent of cheaper shale oil and after the 2008-2012 GFC .
Peter was on the advisory board at Canterbury University's department of Chemical and Process Engineering which developed a wood gasifier which made a near optimal ratio of CO2 and hydrogen to feed into the well-proven Fischer-Tropsch process to produce synthetic sulphurfree diesel. NZL
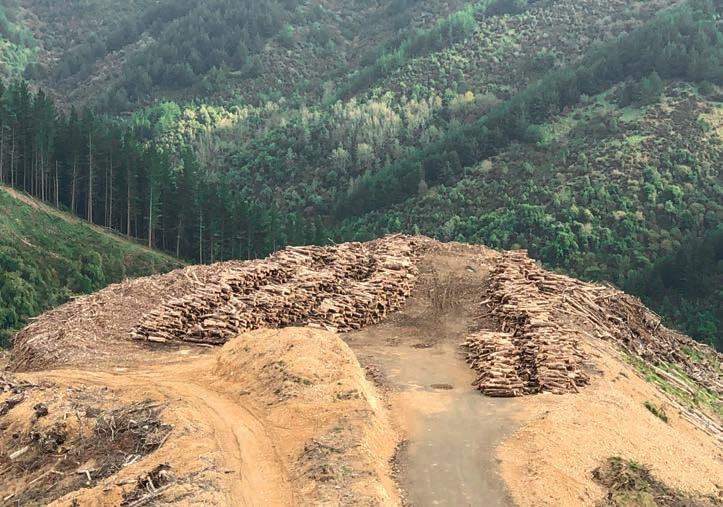
Drying reject log/billet wood stacked on the old Port Blakely skid site in Geraldine Forest.
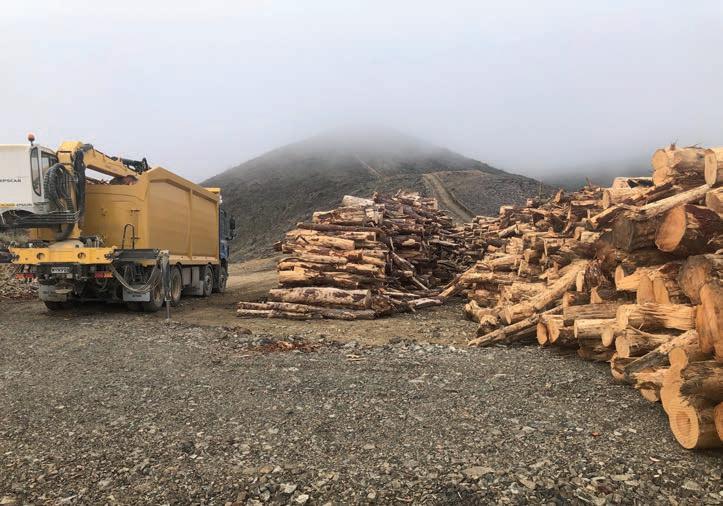
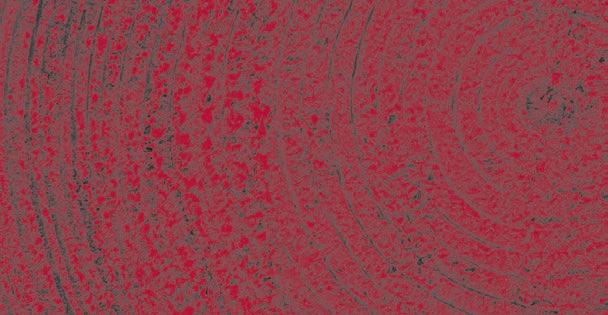
Nobody stands behind your felling head like we do. Nobody stands behind your felling head like we do. Nobody stands behind your
When you choose a Woodsman Pro Felling Head, you’re not just buying the best machine on the market, you’re joining the Woodsman Pro family. As family you’ll get looked after right from the start. Firstly we’ll make sure you get exactly the right head, and then we’ll make sure it’s set up just right. After that, no matter where, when or what happens to your felling head we’ll be there to sort it out for you. We can promise you that because the team that built your Woodsman Pro is right here in NZ, so when you need us we’re just a phone call away. When you choose a Woodsman Pro Felling Head, you’re not just buying the best machine on the market, you’re joining the Woodsman Pro family. As family you’ll get looked after right from the start. Firstly we’ll make sure you get exactly the right head, and then we’ll make sure it’s set up just right. After that, no matter where, when or what happens to your felling head we’ll be there to sort it out for you. We can promise you that because the team that built your Woodsman Pro is right here in NZ, so when you need us we’re just a phone call away. felling head like we do. When you choose a Woodsman Pro Felling Head, you’re not just buying the best machine on the market, you’re joining the Woodsman Pro family. As family you’ll get looked after right from the start. Firstly we’ll make sure you get exactly the right head, and then we’ll make sure it’s set up just right. After that, no matter where, when or what ENGINEERING SERVICES ROTORUA LTDEngineered kiwi happens to your felling head we’ll be there to sort it out for you. We can promise you that because the team that built ENGINEERING SERVICES ROTORUA LTDEngineered kiwi P. +64 7 348 1286 | E: INFO@ENSIGN.CO.NZforestry solutions since 1965. your Woodsman Pro is right here in NZ, so when you need us we’re just a phone call away. forestry solutions P. +64 7 348 1286 | E: INFO@ENSIGN.CO.NZWOODSMANPRO.CO.NZ since 1965. Engineered kiwi WOODSMANPRO.CO.NZ © Copyright 2022 Engineering Services Rotorua Ltd. All Rights Reserved. The Ensign & Woodsman Pro brands are registered trademarks of Engineering Services Rotorua Ltd. ENGINEERING SERVICES ROTORUA LTD forestry solutions © Copyright 2022 Engineering Services Rotorua Ltd. All Rights Reserved. P. +64 7 348 1286 | E: INFO@ENSIGN.CO.NZ since 1965. The Ensign & Woodsman Pro brands are registered trademarks of Engineering Services Rotorua Ltd.
WOODSMANPRO.CO.NZ
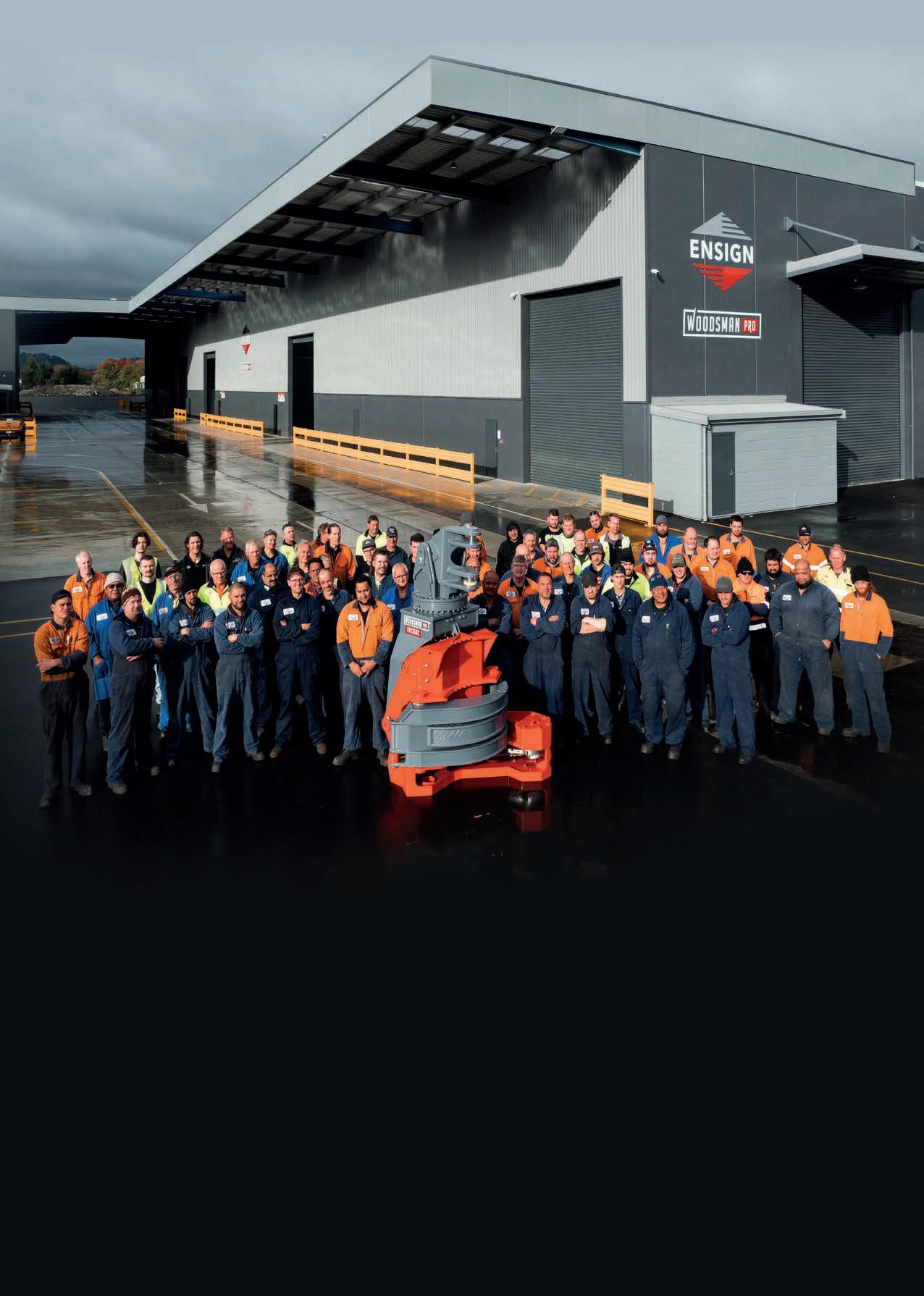