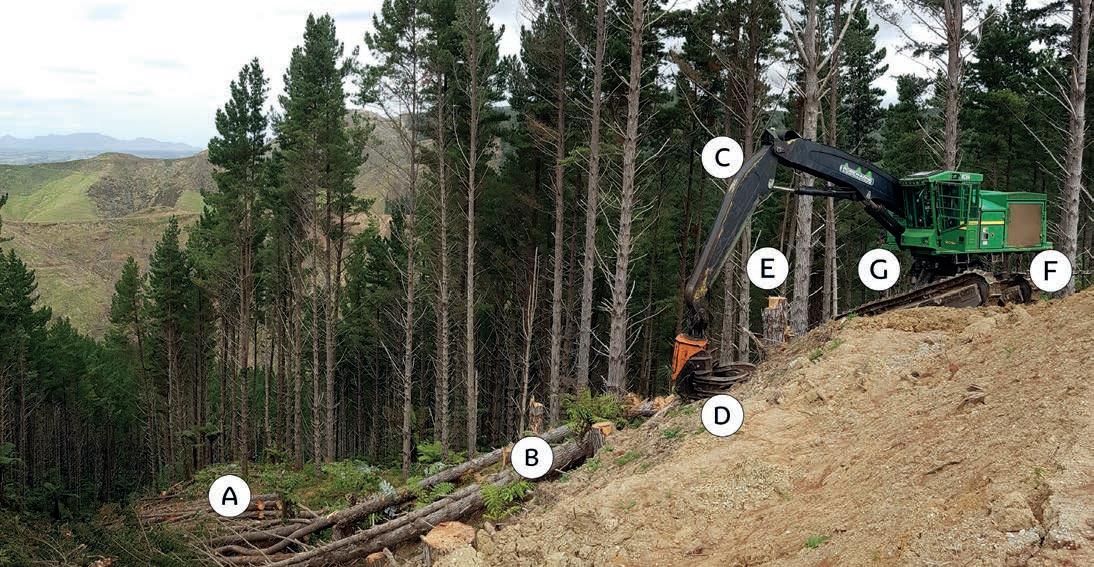
7 minute read
WINCH-ASSIST HARVESTING
by nzlogger
Maximising the benefits of mechanisation
Story: John Lowe, Acting National Safety Director of the Forest Industry Safety Council (FISC) and Safetree.
THE NEW ZEALAND FORESTRY
industry has seen a huge shift from manual to mechanised harvesting in the past few years, greatly reducing risks to manual fallers and breakers-out.
However, mechanised harvesting creates its own critical risks, particularly if machines and the people who operate them are working on steep and more difficult terrain.
With winch-assisted technology now widely used around New Zealand, the forestry industry identified the need for a NZ Winch-Assisted Harvesting Best Practice Guide. This guide, published in July 2022, sets a benchmark for winch-assisted harvesting on steep slopes.
Winch-assist is a ground-based harvesting system that uses wire rope(s) attached to a machine to operate in a broader range of conditions, often on steeper slopes. It is often called cable-assist or tethered harvesting.
Winch-assist is specifically designed to extend the operating range of machines on steep slopes. It allows harvesting machinery to operate on steeper slopes where previously no machine could have worked. It can also be used to support cable logging operations through mechanised directional felling for extraction, bunching and shovelling.
A common New Zealand use of winchassist is steep slope felling or shovelling with a tracked excavator. However, a range of other machines can be successfully winch-assisted including skidders and forwarders.
A big driver for winch-assisted harvesting systems has been to improve felling safety.
Machines protect workers from many of the risks associated with manual felling. WorkSafe’s position on new technology is that companies should adopt it when it better manages risk. The move to winchassist has been an important safety step to protect workers through new technology.
Companies using winch-assisted harvesting also report that, with correct management, it can benefit productivity, the environment, operational flexibility, and forest owner returns.
However, like any technology it brings its own set of risks. An analysis of data from the Incident Reporting and Information System (IRIS) shows recent winch-assisted incidents are split between three key areas: • Anchor set-up and anchor components:
This includes winch components, controllers and site factors, and anchor lead angle incidents. • Rigging-related incidents: This includes ropes, chains, connectors and unintentional factors like binding and redirects.
Winch-assist incidents
Source: IRIS data Anchor Rigging Assisted machine
How steep is too steep? Many factors other than slope affect machine operations e.g. soil conditions, operator skills, the machine and roughness of the slope. Operators say productivity drops on slopes greater than 42 degrees.
Slope (degrees) Slope (%) Consideration
17° 30%
This is considered a limit for when a wheeled ground-based machine can start to slide under poor conditions.
22° 40%
This is considered a limit for a tracked ground-based machine. It can start to slide under poor conditions. 28° 50% Most purpose-built forestry machines, with good operators in good conditions, can work up to this limit. Beyond this slope it is wise to consider using winch-assist. 35° 70% This is considered the absolute upper limit for ground-based machines without winch-assist. Only under very favourable soil strength condition, with a purpose-built steep slope harvesting machine and a very experienced operator, and then only traversing directly up or down the slope. 42° 90% A realistic upper limit for all winch-assist operations. 45° 100% Considered the absolute upper limit for any winch-assist operation. If any part of the rigging fails, a machine roll-over would be dificult to avoid.
• Assisted machine (most commonly a harvesting machine): This covers harvester stability, trees falling onto the machine, other felling issues and cab and operator specific incidents like slips, trips and falls.
The Guide provides information to help forest owners/managers, contractors and workers manage risks in these, and other, areas.
The Guide was developed with input from forestry companies, contractors, workers, machine makers, academics and other industry experts. It was funded with support from ACC and WorkSafe.
It is free and is available to download on the Safetree website (https://safetree.nz/ resources/winch-assisted-harvesting-bpg/) . The Guide will be routinely updated as winchassisted harvesting technology develops.
Below are some top tips from the Guide on safe winch-assisted harvesting.
Maintaining stability and traction
A loss of traction is the main cause of a loss of stability. Loss of traction can lead to machine rollover.
Factors that reduce traction include: • Terrain – boulders, rock, thin soils and gullies • Wet locations – aspects that get less drying, or poorly drained soils • Steep slopes especially over 35% (20 degrees), and long steeper slopes • Machine design and capability
In addition to the table opposite and photograph above, other things to watch out for include: • Common natural hazards like stumps, holes, rocks, drop-offs, windthrow and thick scrub. • Larger woody debris and slash mats that can reduce traction through slipping. • Also check that ropes and connectors are secure and not damaged.
Tips on preventing loss of traction:
A: Only turn around on a steep slope when there’s a flat and wide bench. B: Cut and move away woody debris that could affect traction and stability. C: Keep boom stationary when moving, otherwise weight and traction on each track changes. D: Keep the saw head or grapple close to the ground to provide quick stability support. E: When going over steep terrain, lower boom and head and use for stability. F: Before moving into the harvest area, pre-tension ropes to support the machine. Check lead angles are okay. G: Keep tracks parallel to the slope so the grousers or tyres provide resistance to sliding.


Safe machine anchoring
A well-positioned machine anchor in excellent working condition is key to safe and productive winch-assisted operations.
Most anchoring failures are a combination of factors – poor machine positioning or cable angles, and high loading.
Remember, machine anchors do move. Put the blade or bucket behind a stump. Check the anchor is holding each set-up. Do a straight pull test.
Don’t move the anchor and steep slope harvesting machine at the same time. One machine needs to be stationary and stable during line shifts.
In addition to the set up and guidance photographs to right and below, also, check the anchor machine regularly. • Always follow the Original Equipment
Manufacturer’s guidance on inspection and servicing. This will include: • Mechanical parts that move, like boom, blade, winch, tracks, pulleys and end connectors. • Control systems like electronics, hydraulics, aerials, tension monitors and alarms. • Structural components like chassis and cab. • Check anchor alarm is set for machine movement of about 0.5m.
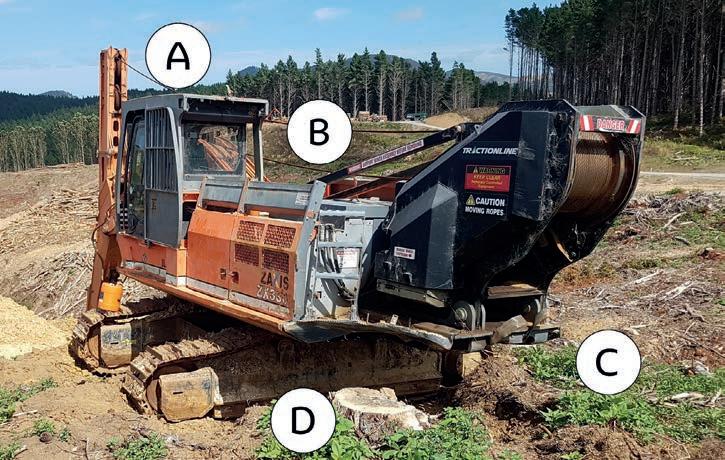
Safe set-up:
A: Install a tension monitor that relays to the steep slope harvesting machine operator. B: Use camera(s) to show the
steep slope harvesting machine operator cable spooling. C: Use an anchor movement alarm. D: Position safely and securely e.g. avoid soft road or landing edges.
Additional guidance for excavator anchors:
A: Dig bucket into firm soil so it won’t pull out. B: Bucket can be normal way or reversed. C: Lead angle within manufacturer’s limits. D: Low cable exit points to prevent overturning. E: Boom and stick angle between 90-110 degrees.
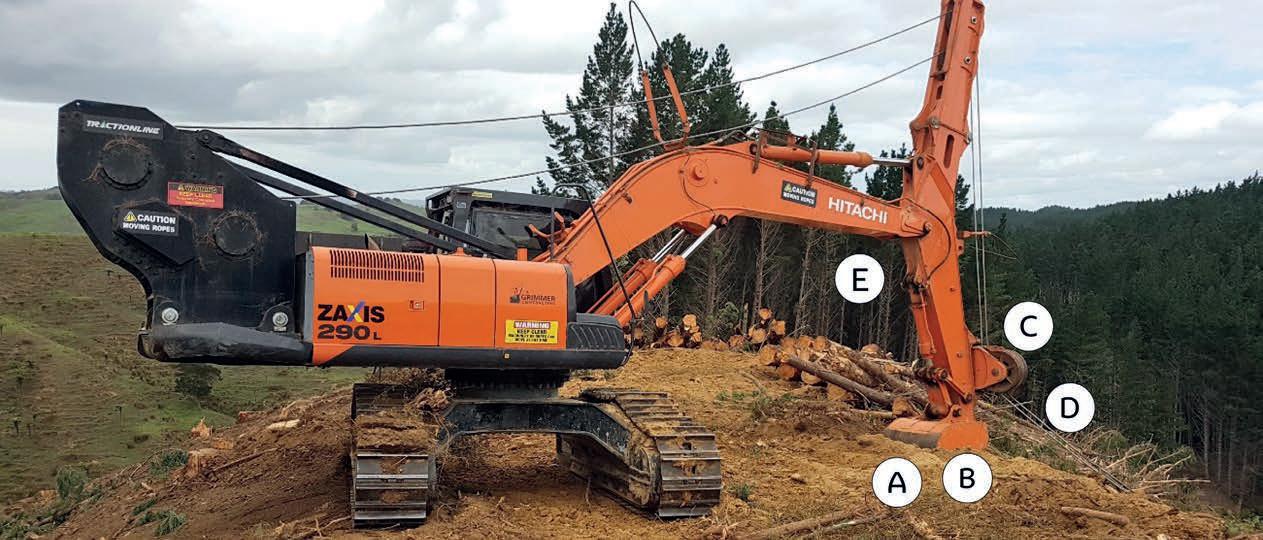
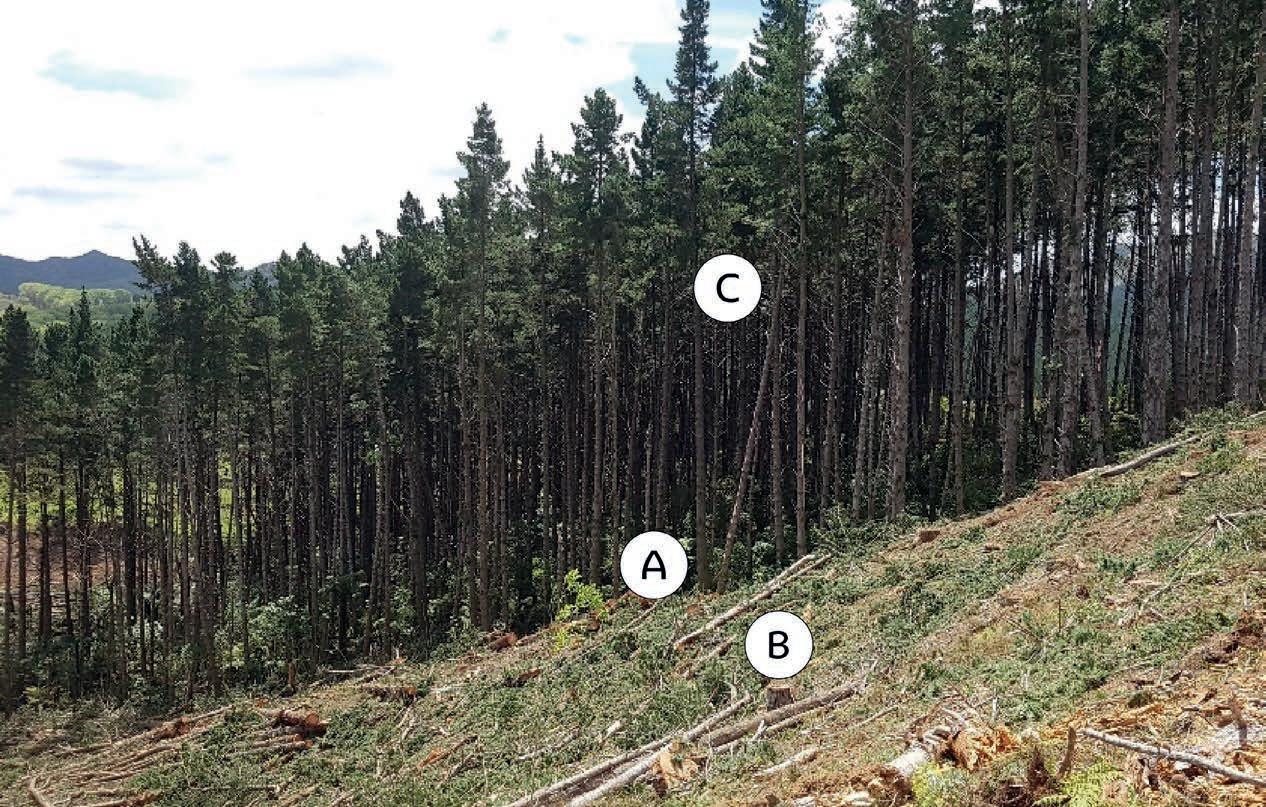
Where hand-falling follows mechanisation
Sometimes it’s not possible to mechanically fall the whole block. Here are some steps to make it safer for the hand fallers working with mechanised crews:
Have the hand fallers work first if possible.
Even when you think you can get all the wood, fell as if you might not.
Always make boundaries as safe as possible for the hand fallers.
Also: • Redirect (rub) trees must be felled by the winch-assist machine. • Remove risks identified by hand fallers. • Eliminate other hazards that could be between standing and felled trees. • Inform the hand fallers of boundary hazards. A: Keep hand fallers escape routes open on the boundary. B: Fall away from the boundary. No branches or tops in the hand-falling area. C: Leave a clean boundary canopy, with minimal broken branches. These are hard to see because they are still green.

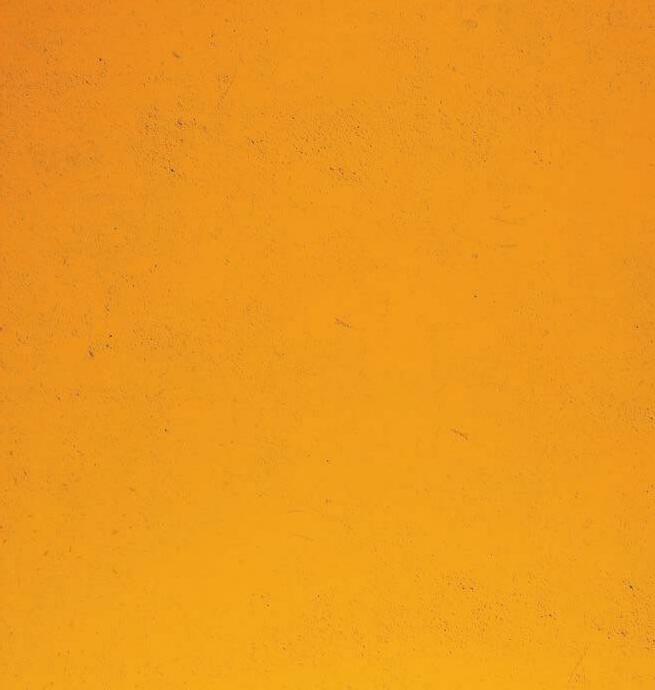
10 Tips from experienced operators
As part of creating this guide we asked experienced machine operators what advice they’d give to others:
1. Check your gear and trust it – anchor, electronics, rigging and machine! 2. Plan and have a Plan B. Be adaptive to changing situations. 3. There are places you don’t winch-assist. Don’t be forced to go there. 4. Stay focussed. Take regular breaks and stop operating if you’ve lost concentration. 5. Take your time. Don’t let production pressure affect your decisions. 6. Ensure you can see the ground, and look up as well as down. 7. Work within your limits. Make sure you can always get out of where you’ve gone. 8. Look how the winch rope(s) lay. That’s where they take you back up the slope. 9. Know when to stop and leave the remainder for hand felling, even if it is just a few trees. 10. Always keep things clean for the hand fallers, just in case they need to finish things off. NZL
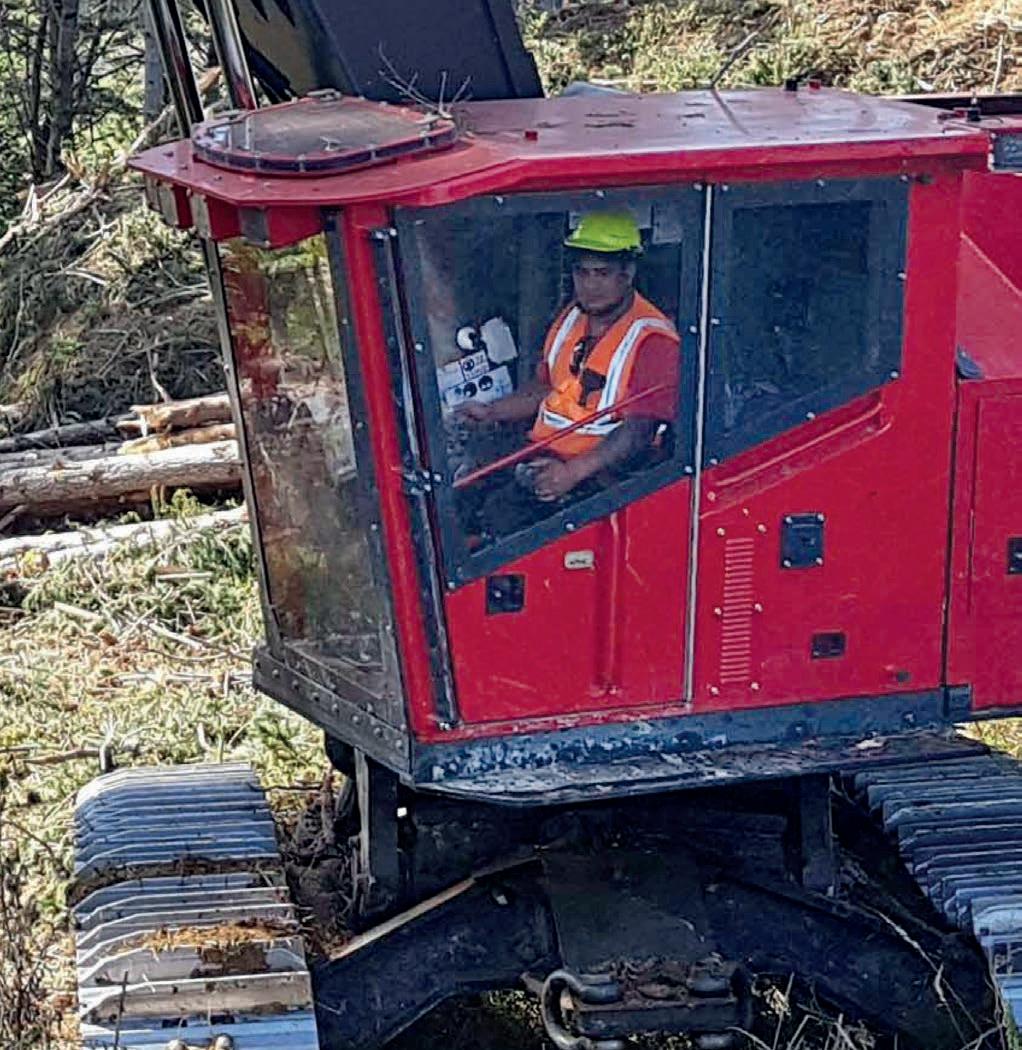
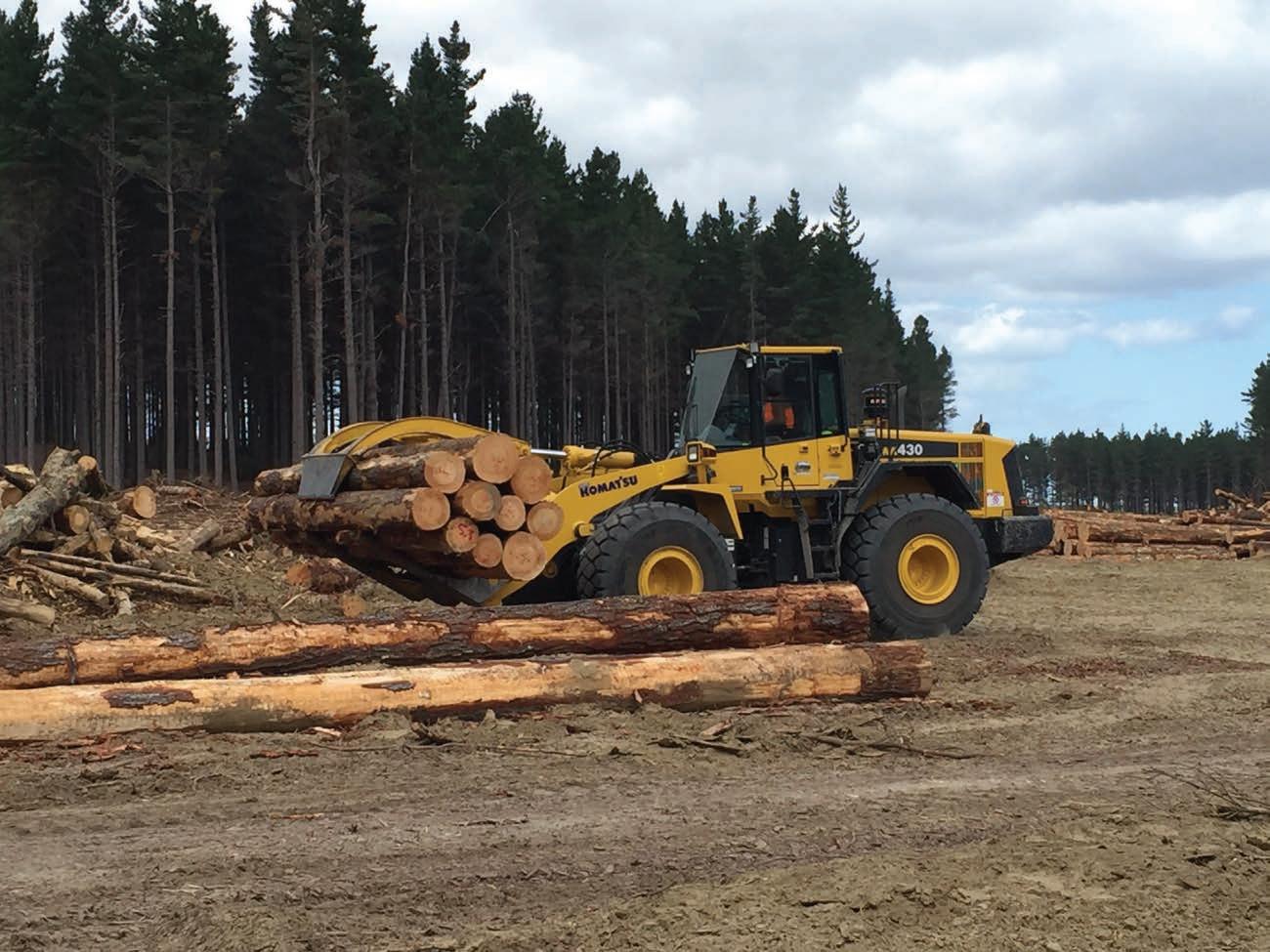