
10 minute read
NZ TIMBER
from NZ Logger October 22
by nzlogger
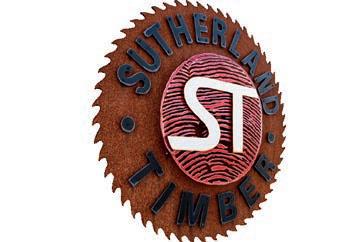
Story: Hayley Leibowitz

SEPARATED BY WORLD WAR 1, TWO
brothers (Jonnie and Norman Sutherland) nonetheless shared the same dream – to start producing lumber after the war. While one was sadly killed in action, the dream lived on and Sutherland & Co was born over a century ago in 1920 in the Happy Valley Tuatapere.
The mill, Sutherland Timber, moved a number of times, with a second mill set up in The Catlins until the family made the move to Cheviot to start the milling of pine timber. Finally in 1956 it was moved to its current site in Kaiapoi where it has developed in leaps and bounds over the years milling, drying and treating on site.
As the years passed, it was third generation, Jack and Ian Sutherland who took Sutherland Timber native production into the soft woods of Pinus radiata. Next came Murray (‘Muzz’) and Annie Sutherland who took the company to the next level, building up local and international relationships which are still vital to the company today. And it’s relationships that matter in this, the oldest sawmill in New Zealand that is still 100% family-owned and operated and has stayed in the same family since it was established, now in its 5th Generation.
Now Annie and Muzz’s children, two brothers and a younger sister, are now at the helm. There’s General Manager of the Sutherland Group, Jonathan (‘Jonnie’) Sutherland; David (‘Davie’) Sutherland running the ITM operations and Amy Sherwin coordinating the marketing for Sutherland Timber and the ITM stores.
Customer-centric
“Our Dad, Murray, has been able to take a step back now, although he is always our go-to man Above from left: Retired Mill Manager/Loader Operator, Rocky Scott, Murray (‘Muzz’) Sutherland, Jonnie Sutherland and Loader Operator, Mark Smith, pictured with Sutherland Timber's original Volvo and the new one on the right. Opposite top: The fillet/de fillet line with the sawmill and the chip bin and round table in the background.
Opposite bottom: From left: Davie Sutherland, Amy Sherwin, Muzz Sutherland, Annie Sutherland and Jonnie Sutherland

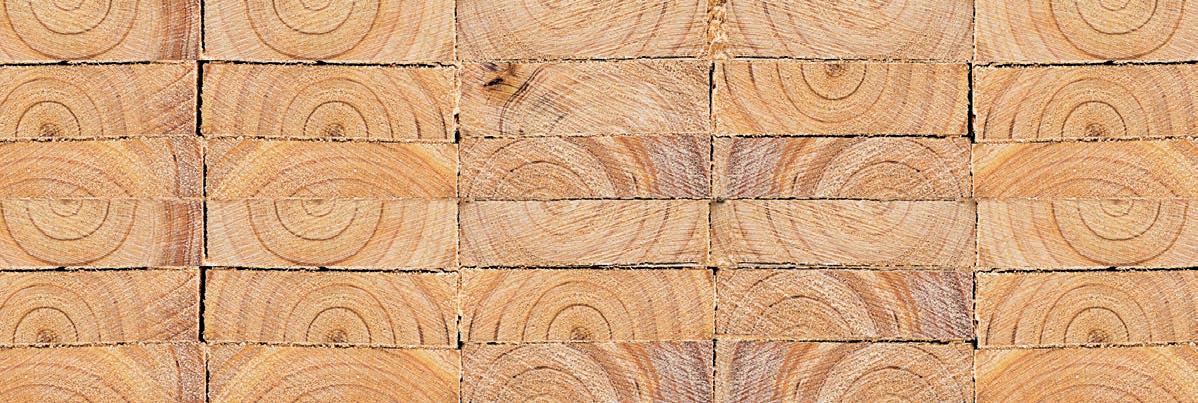
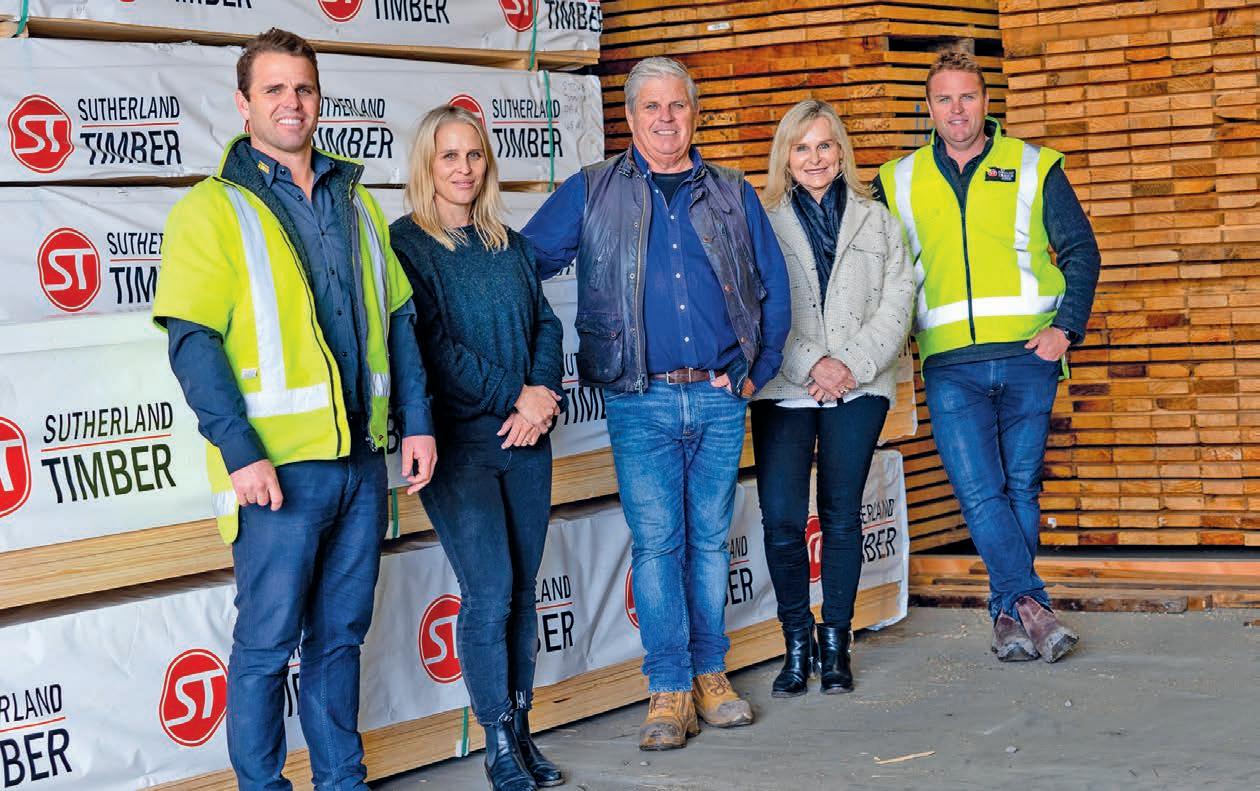
for anything! His knowledge and experience is something we all rely on,” says Jonnie. “Customer service is the biggest and most important part of our process, that’s why we have our own delivery trucks. This way we can deal with meeting customers’ needs and requirements quicker. Our father introduced building material supplier, Independent Timber Merchants (ITM), to our company to secure our supply lines, starting with the Kaiapoi store and more recently adding the Ashburton and Timaru stores to the group, which also includes our own frame and truss manufacturing plant. We now supply our stores as well as many other building merchants throughout New Zealand.”
Currently producing 120-150 cubic meters of timber per day, the mill cuts New Zealand radiata pine and Douglas fir to produce structural framing for the domestic building market, with an annual output of 25, 000 m3 . All logs are sourced locally throughout the South Island using local contractors.
Jonnie says while export has been a large part of the business in the past, shipping timber to Australia, Asia and America, Sutherland Timber now predominantly supplies the domestic market which has “been very strong”.
“Post-COVID, we still have export commitments that we fulfil when we can get containers and an available booking on a ship (getting the containers has been the main issue). We have a great team of staff who have all stepped up when we have had Above: The Sutherland Timber Head Rig showing the Southern Cross built Ilse Forge 60-inch band mill. Below: Wood chip bin at Sutherland Twimber. Bottom: Aerial view showing the sawmill site with the dry sheds in the foreground and sawmill and log yard in the distance.
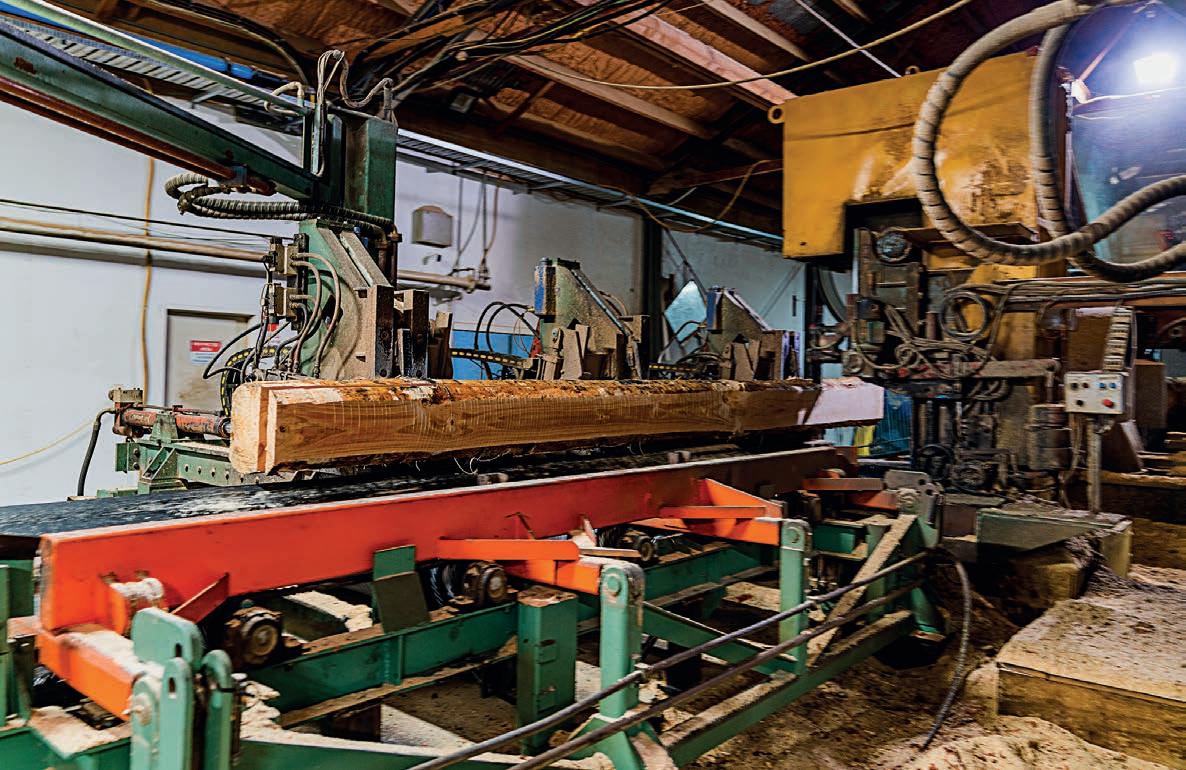

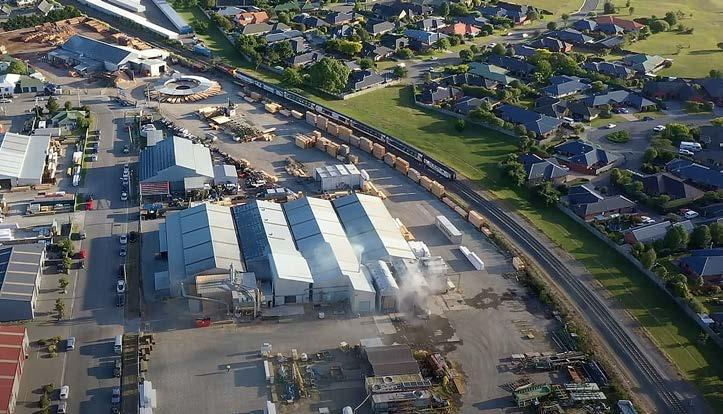

1 1 1
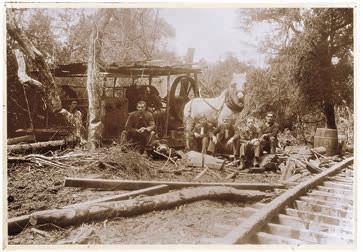
3
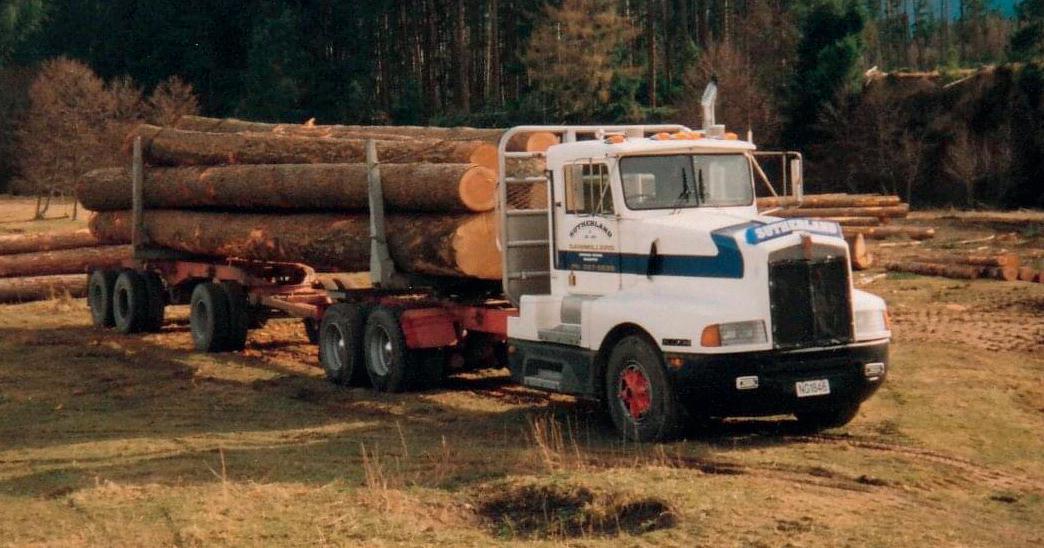
4

5
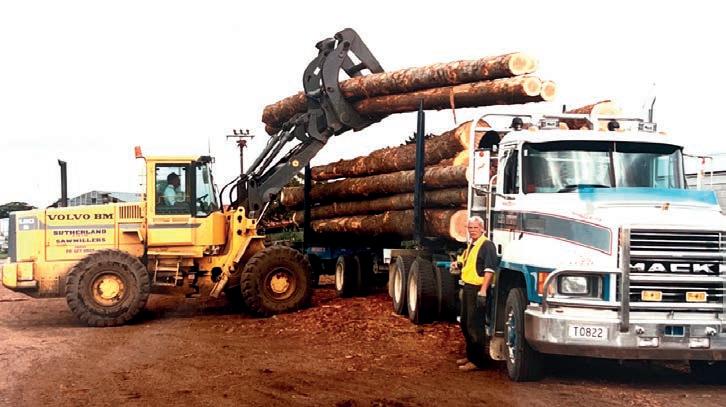
1: Sutherland & Co in Happy Valley, Tuatapere, showing the steam power log hauler that brought the logs in. It would be started with dry timber from the mill. This photo shows the harsh environment the men worked in. The rail line in the foreground was also vital for production. 2: Sutherland & Co in Happy Valley, Tuatapere, showing log extraction on the rail tractor from the bush to the mill. 3: The Kenworth T600 purchased by Muzz in 1992 and used to cart logs from Hanmer and Ashley back to the Kaiapoi Mill. It was sold and Jonnie has just repurchased it for restoration back into the fleet. 4 & 5: The original loader purchased by Muzz. Mill Manager/Operator, Rocky Scott, is driving the loader with Steve Murphy of Steve Murphy Limited pictured standing by the truck.
2
people off with COVID. Everyone helps out to cover each other,” adds Jonnie.
As to the process, “we run a pretty standard head rig carriage line to a slabber edger, gang saw and resaw through an overhead trimmer to a round table. We have three drying kilns on site as well as a CCA and boron treatment plant. Along with our trusty Weinig planer and Stenner resaw, we have an Iveco Stralis delivery truck which goes all over the south Island.”
Loading up
Jonnie is particularly proud of the latest addition to the mill, a new Volvo loader L90H purchased through TDX: “For many years It has been a goal of mine to replace the loader our dad purchased with a brand new one. As a nine-year-old boy having watched a new Volvo loader roll in the gate and now with that loader still working on site, it has proved it has been a quality piece of equipment and investment as it has stood the test of time over 30 years.
At the time, it was the first piece of machinery Muzz bought brand new for the company as well as being the first Volvo in forestry application in the South Island. Jonnie remembers learning to drive it at age nine as it was “something you could do back in those days”.
“Muzz approached three different companies with the view to supply us with a new machine rather than a second-hand one. The result being Mike McSkimming from Volvo who stepped up to the mark and convinced us that some of their new technology was the go-forward. This was backed up with Mike’s sound knowledge of his product.
“The L90B came complete with genuine Volvo Logging head, air-conditioning and advances in hydraulics. The purchase was also connected to the fact that servicing would be done locally through their agent. This local service simplified the decision, which proved its worth.”
The longevity of the machine was put down to the regular servicing and smooth, experienced operation by Retired Mill Manager/Loader Operator, Rocky Scott. It remained a front line machine until 2013 and was replaced with a second hand L90E which is still being used on site today.
With the need to source new equipment to keep up with the increased sawmill production, the decision was made to upgrade the log loader this year.
“It was a proud moment to watch the new loader roll in the gate with my dad and own sons present,” says Jonnie. “While some investigations were done on other brands, the history of Volvo on site proved too strong of a force which is why we went with them. We have always favoured the Volvo brand, due to its durability in our harsh conditions, having three working loaders on site today. This is a very special milestone for our company and family. We have had our previous loader operator, Rocky, work for us for 30 plus of those years and our new Loader Operator, Mark Smith, is ecstatic about the new purchase.”
With the original Volvo having a Volvo log Muzz and Jonnie Sutherland with loaders old and new.

head on it, after a short discussion with Matt Holloway from TDX, it was decided to equip the new L90H model number with genuine Volvo parts which included quick coupling, log head and bucket.
Another upgrade in the works is the restoration of the company’s Kenworth T600.


It was purchased by Muzz in 1992 and used to cart logs from Hanmer and Ashley back to the Kaiapoi Mill. It was sold and Jonnie has just repurchased it back into the fleet. It is currently being restored with great excitement for the family.

Future forward
Asked about the discontent in the industry and the closure of so many mills over the past few years, he says for some time now there has been a mismatch between the cost of production and market returns: “For a long time returns in sawmilling have been marginal with increased costs, and a struggle to compete with export log pricing and land value increase has led to a lot of people questioning the viability of their operations, with many of them answering that question through closure.”
The Sutherland mill, on the other hand, is thriving, adapting to change on both the practical and human fronts. Health and Safety is an integral part of the company and “something we prioritise”, says Jonnie. “Having lost a family member in the logging industry, health and safety is at the forefront of everyone’s minds.” Along with that vital focus, staff saving initiatives, weekly cooked lunches and breakfast available for staff daily, and an on-site vegetable garden are just some of the staff initiatives at the mill.
“There are so many great people who have worked for us over the years,” Jonnie adds. The company celebrated its Centenary by gathering their stories into a book, titled Mill Power. “Dad (Muzz) started working on the book a few years ago and then Amy
Above: Planer in feed system in the dry shed. Centre: The re-saw in action. Right: Janice Ormiston documenting packs for export.
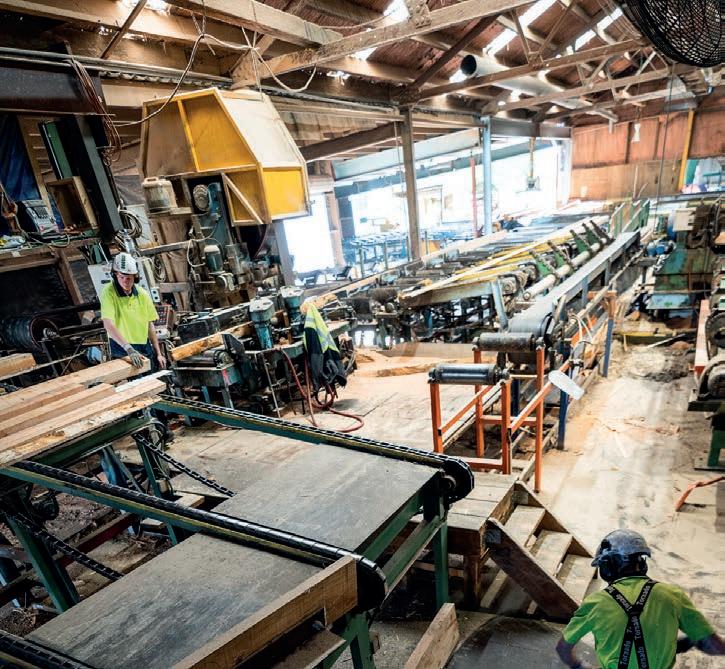
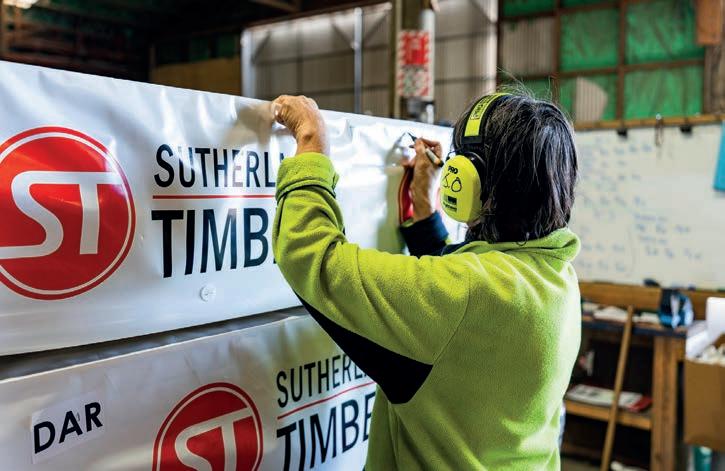
joined him to help finish the project. It was about preserving the history while we could – there weren’t too many people from the early days who could talk about the processes and how things really worked back then. It was about capturing those moments.
While celebrating the milestone 100th year of sawmilling last year was delayed a while thanks to COVID, they did manage to sneak the celebrations in between lockdowns, along with the publication for the book which has been described as:
“A beautiful production written in the voice of the fifth generation descendent detailing 100 years of Sutherland & Co business, historically detailing early sawmilling in Southland, the Catlins and Canterbury. A startling compilation of photography through the century of sawmillers and of milling innovation. An excellent and candid rendition of family business through six generations, of positioning family personnel, complex products and competitive markets.”
While the past is a matter of chronicling stories and experiences, Jonnie has this to say about the future: “The future of the industry looks exciting with the launch of the Industry Transformation Plan (ITP) through Te Uru Rakau – NZ forest service pushing the case for domestic production of an amazing, renewable and sustainable resource.
“No doubt robotics, automation and streamlined systems will see the need for a technology-based workforce, however there will still be the need for good-oldfashioned operators to help programme cut patterns and monitor recoveries.”
And the future for Sutherland Co? No doubt that lies in the sixth generation, Jonnie, Davie and Amy’s children (pictured above). NZL
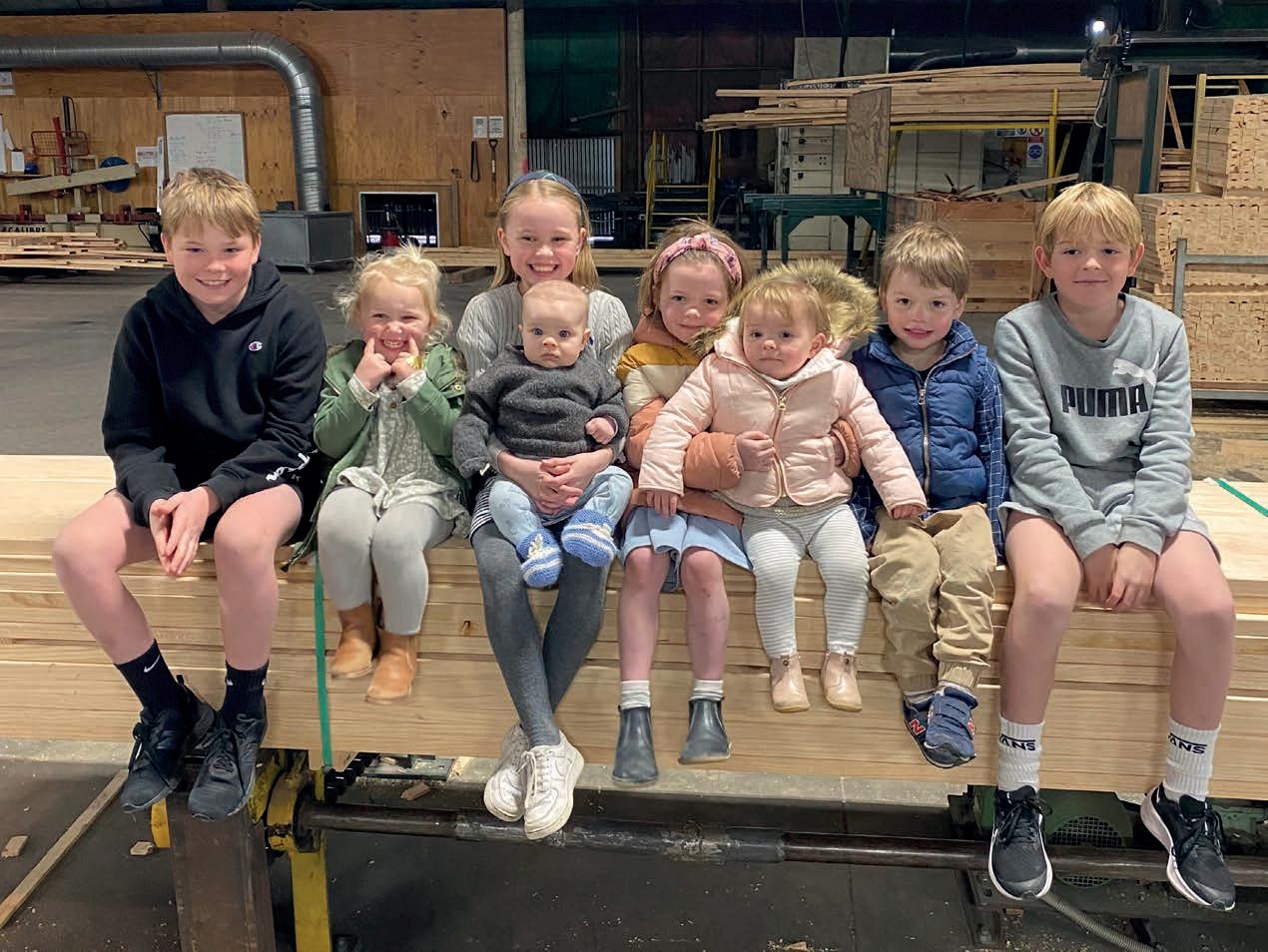
Above: “We see these wee people as the next generation to be looking after our forests, sawmilling and producing the best sustainable product for future generations to come,” says Amy Sherwin. Below left: Grant Brown loading packs to be exported. Below right: The Iveco Stralis delivery truck and trailer loaded with timber for delivery.

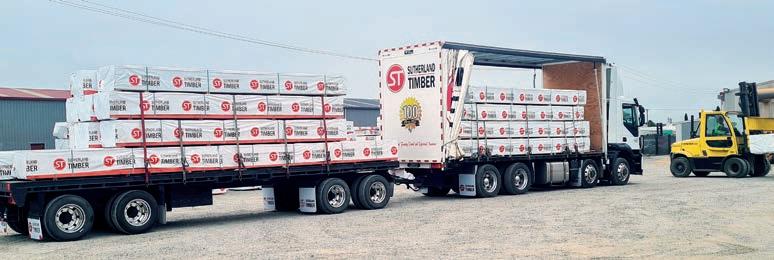