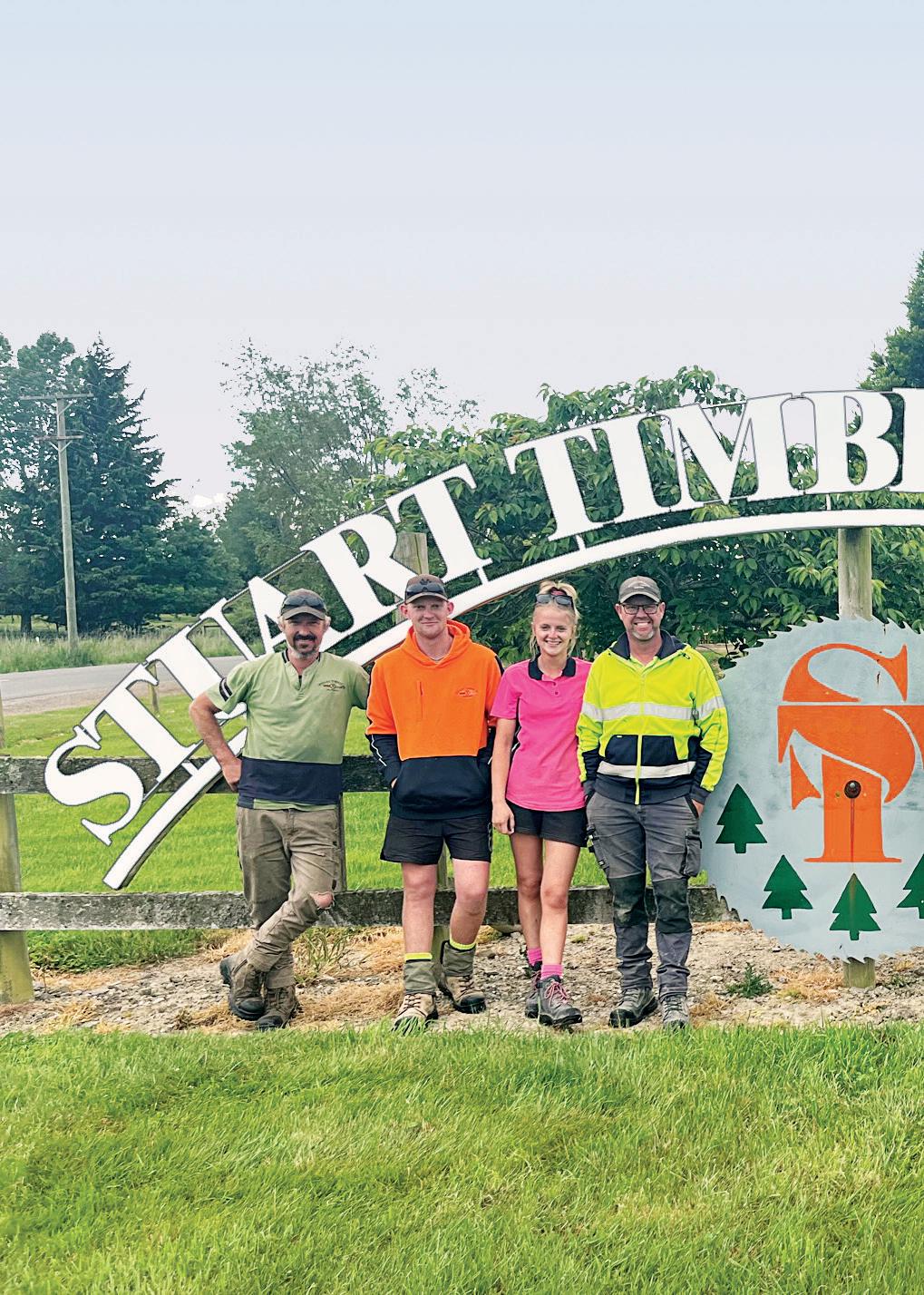
15 minute read
NZ TIMBER
by nzlogger
SURVIVING TWO DECADES OF MILL CLOSURES
Story: Jim Childerstone
SURVIVING TWO DECADES OF

ASMALL SURVIVING TIMBER MILL
near the rural West Otago township of Tapanui has battled on regardless of changing times, with some updated innovations.
Stuart’s Timber Company now supplies a wide range of products throughout the Southern provinces.
From the Queenstown Lakes District, Central Otago to Dunedin and Invercargill, wholesale building supply firms, farming communities and builders vie for the mill’s products.
These range from landscaping to structural framing, dressed timber, weatherboarding, garden, horticulture, and post and pole supplies.
The family business is headed by second generation, Roger Stuart, who believes the business is moving from small to more midsized.
Roger explains, “The company has almost done the full cycle, from manufacturing outdoor furniture to finger jointing, and laminating in the late 1980s and 90s. However, the Stuart family enterprise is now back to the basics of timber production.”
The past two decades have seen many local based saw mills winding up operations. Part of the reason was the demand for export logs making it marginal for local mills to compete, and a lot to do with modernised economy of scale manufacturing.
Also, the effects of globalisation, manufacturing of wood products by low wage economies such as China, India and South Korea put paid to local processing.
On top of that, the volume of wood harvested in this country exceeded demand of the Nation’s building industry at the time.
Nearby Ernslaw One’s Blue Mountain Lumber closed down about 15 years ago, as well as a couple of regional mills in Northern Southland
Stuart’s Timber Company is currently cashing in on the recent regional building boom, particularly in Central Otago, Wanaka and Queenstown.
Moving with the times
Roger, Managing Director, admits to tough times since the company’s launch back in 1980 by his father Campbell Stuart and his three brothers.
“It was a matter of modernising the plant where possible, and when funding was available,” Roger explains.
Gone was the old 60-inch breakdown saw and 44-inch breast bench, and in with the electronically mechanised band saw in 2005. One of the original twin flitch re-cutting breast benches will be replaced with more modern and efficient equipment. Cant hooks for positioning logs on the bench, are now implements of a past epoch.
Operating the head rig, mill hand, Max McCormack, says it does take a bit of concentration focusing on the operating machinery for any length of time.
“It’s a somewhat sedentary job so we move about the sawmill doing other tasks to remain active,” he told NZ Logger.
Management makes certain all employees are trained to handle the variety of mill jobs.
“We now have 38 permanent employees,
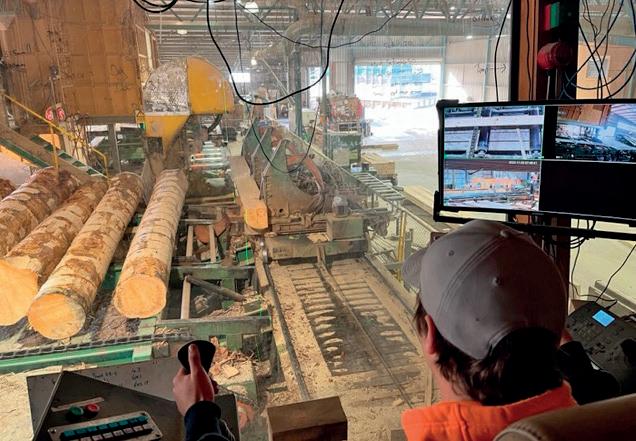
of which seven are whanau and have become skilled in their jobs,” Roger says.
When it comes to job creation, the Tapanui district indicates how forestry and related industries benefit rural areas.
In effect this involves 25 families living around the township with the rest residing in nearby Gore.
“In some cases there are two or more working at the sawmill from the same families,” says Roger.
Logs are supplied from local woodlot owners and corporate foresters
The family must have taken something of a gamble to erect a 1500 m3 work shed on the six hectare site back in 2001, which now houses the main mill processing operations.
This was originally built for furniture manufacture, then finger jointing and lamination. But then in 2006 it was used as the main sawmill building, Roger explains.
However, it is diversification, offering a wide range of timber products and strong relationships with timber retailers that has put the mill in a strong position.
“The company has built up good relationships with most of the log suppliers in the Southern region over the years, buying 90% S grade and 10% pruned logs plus roundwood for the post and pole operation.
“Stuart Timber has taken the opportunity to upgrade our operation, purchasing
equipment no longer required by other mills in the region,” Roger explains.
“A larger treatment cylinder was purchased from Craig Pine and a pressure steaming cylinder was purchased from the Lumsden treatment plant when it closed down.”
The newest family member, Emma Stuart (nephew Andy Stuart’s daughter), is learning about the treatment and steaming operation when we visit.
Set up in the shed the four-side planer mill consists of a Weinig, primarily for gauging and larger runs. “Also a SCM Superset for profiling weatherboards, is ideal for smaller runs of both weatherboard and customer profiles,” says Roger.
A more recent innovation is the installation of an optimizer docking saw sorting out
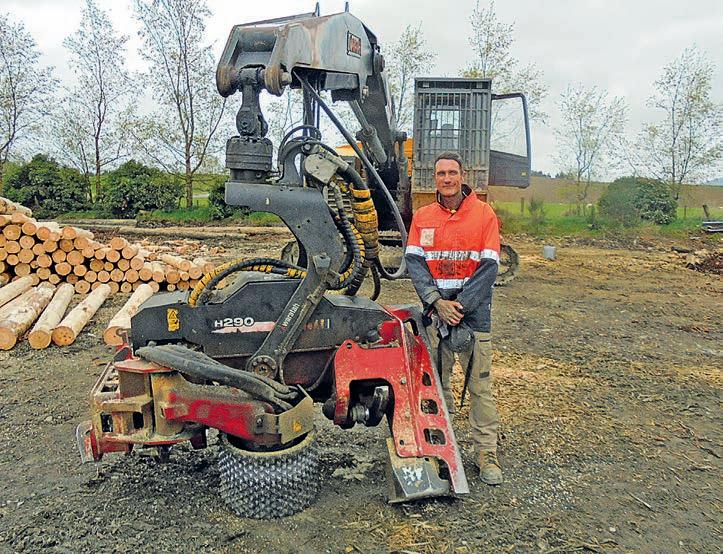
Above: Chris McCullum beside his Waratah post cutter. Below: The log carriage in operation.
fence and pallet timber to length, operated by Roger’s wife Catherine.
“For environmentally-friendly treatment, we are now using MicroPro, ideal for raised garden beds and anything that requires dressing after treatment. This, alongside traditional CCA and Boron treating,” he says.
Changes afoot
The family has been using coal to fire its kilns, but is now in the process of looking at a boiler conversion to use some of the off-cut wood, sawdust and shavings to fire what will most likely be a new boiler installation. “This will not be a cheap exercise,” says Roger.
He says they are still investigating the most efficient and cost-effective system, possibly something around the two- to threemegawatt mark.
Coal is starting to get expensive as well as with Co2 emissions tax under the ETS and having to get rid of the ash to landfills costs money.
Many Southland/Otago mills, businesses and institutions have now converted for chip use, with some help from local and national entities such as the Energy Efficiency and Conservation Authority (EECA).
The company has an on-site chipper and post peeler. Chip is sold to Mataura’s Daiken MDF plant, but could be more convenient to heat the plant.
Stuart’s mill sells most of its products to the big box retailers in Central Otago, Dunedin, Invercargill and locally, and pole timber from the yard to merchants involved with barn and implement shed construction. Asked to comment on the company’s future development and the Government’s recent incentives for value-added wood Top: Max McCormack operating the head rig. Above: Scott Mackenzie and Turipa Mahaki operating the breast bench. Below: Sawdust and chip pad.

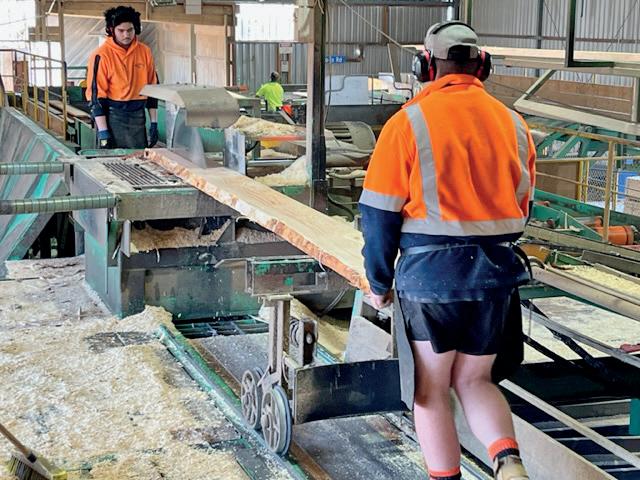
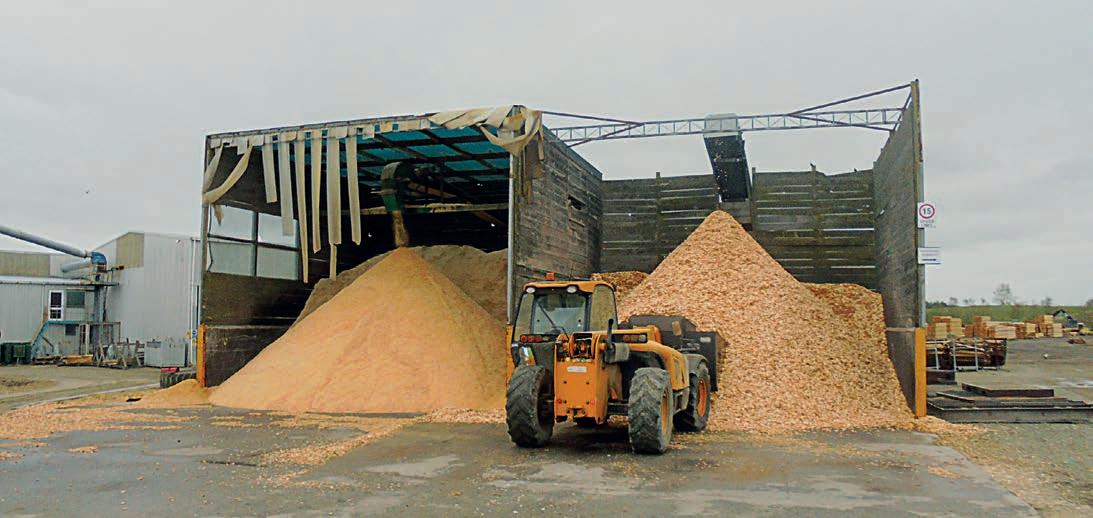
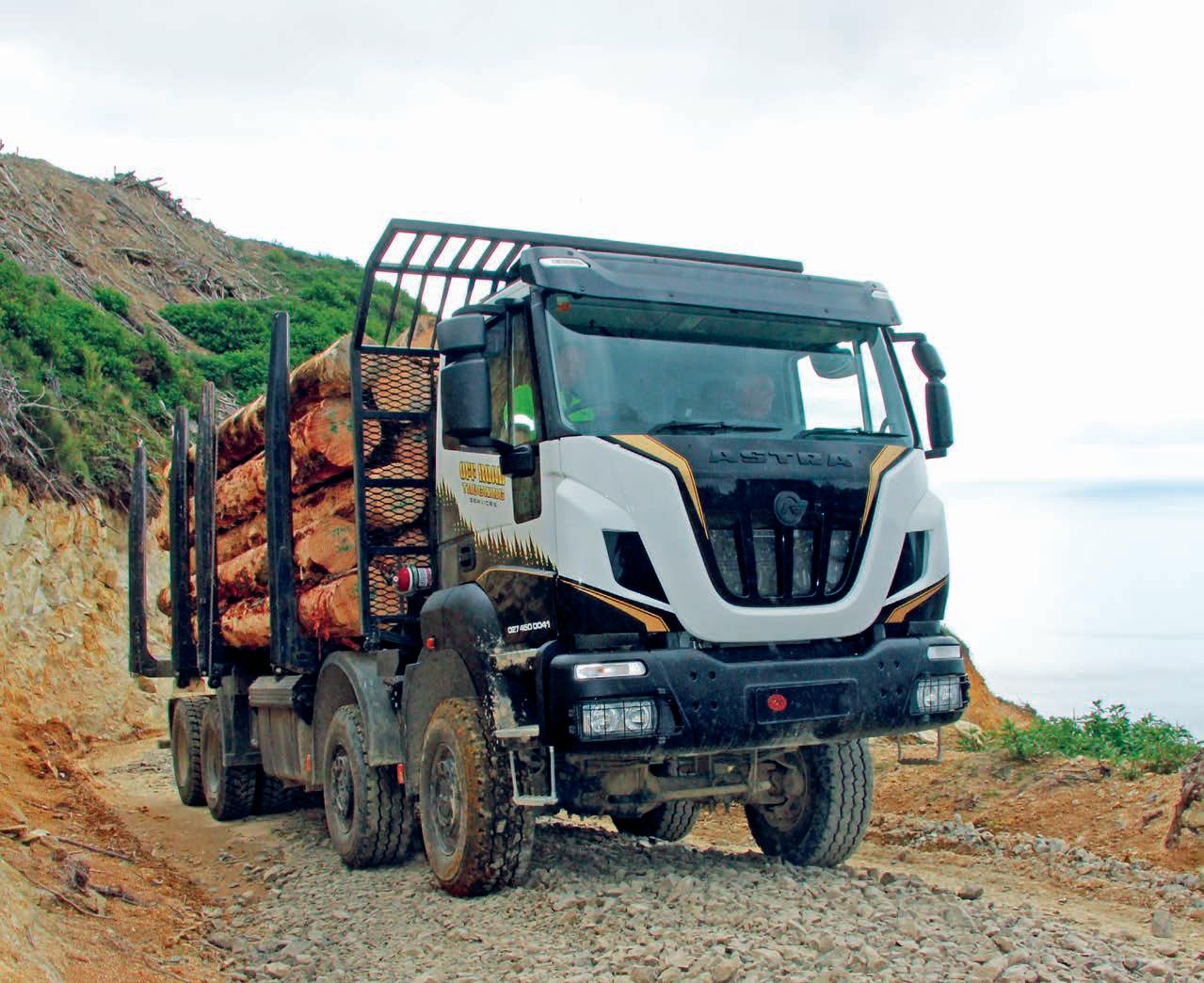
NO LIMITS. NO BOUNDARIES.
20232023

processing, Roger observes that engineered wood products are gaining momentum, but the company does not currently have any plans to go down the engineered wood line again.
Forest industry stakeholders point out that the new Forest Industries Transformation Act proposal is short on specifics on how it will assist on-shore added-value products. “When we get a more detailed picture of how they intend to go about this, and what sort of investment or incentives are available, we will take a serious look at it,” Roger says.
Currently the company needs to invest in its new heating system.
On the recent controversy of livestock farmers being asked by Government to pay towards greenhouse gas emissions, which is dragging forestry into the controversy, Roger says the whole thing was “just ridiculous”, particularly antagonism developing between farmers and foresters with the advent of permanent carbon farming forests. But he admits to not being too familiar with this issue.
New Zealand Forestry Owners Association President, Grant Dodson, says he understands that up to now the issue of mill closures centres around the fact that “New Zealand has a very small domestic market”.
“To date the production of sufficient structural timber for domestic construction can effectively be fulfilled by one or two bigger mills,” says Grant.
“Red Stag and Carter Holt Harvey have invested to expand production to fill this gap. In doing so, they have increased scale and reduced costs, and this competition has forced many small players to close.
“A number of smaller mills have, however, done reasonably well at a lower production scale, particularly filling niche markets and supplying smaller customers that the big players don’t service.
“Mills unable to find sufficient sales in the domestic market have been exporting. This is a difficult market, and people like Marty Verry, who owns Red Stag, often talk about export destination countries having various tariffs and other trade barriers that make it hard for unsubsidised New Zealand mills to compete.” NZL
Top: Emma Stuart sorts out dried posts for treatment. Middle: Planing in process. Right: Mike Stevenson loading the kiln trolly.
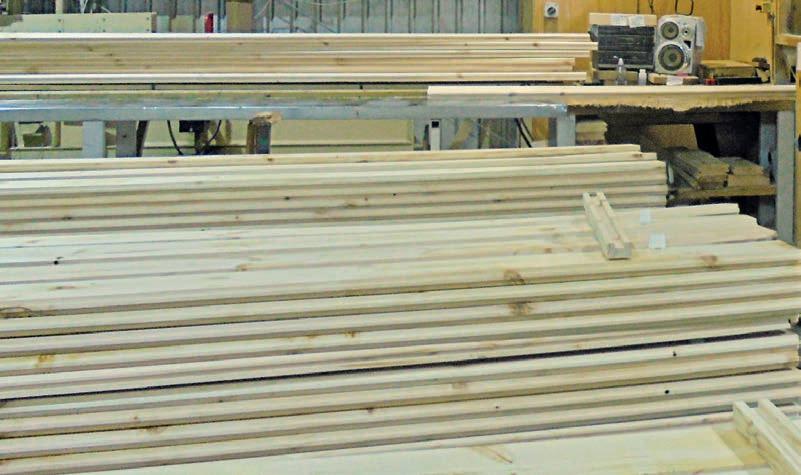
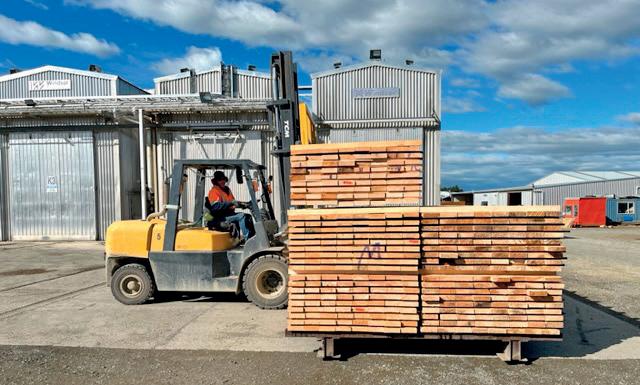

Projected development of duplexes at Jack’s Point, Queenstown.
VALUE-ADDED TIMBER:
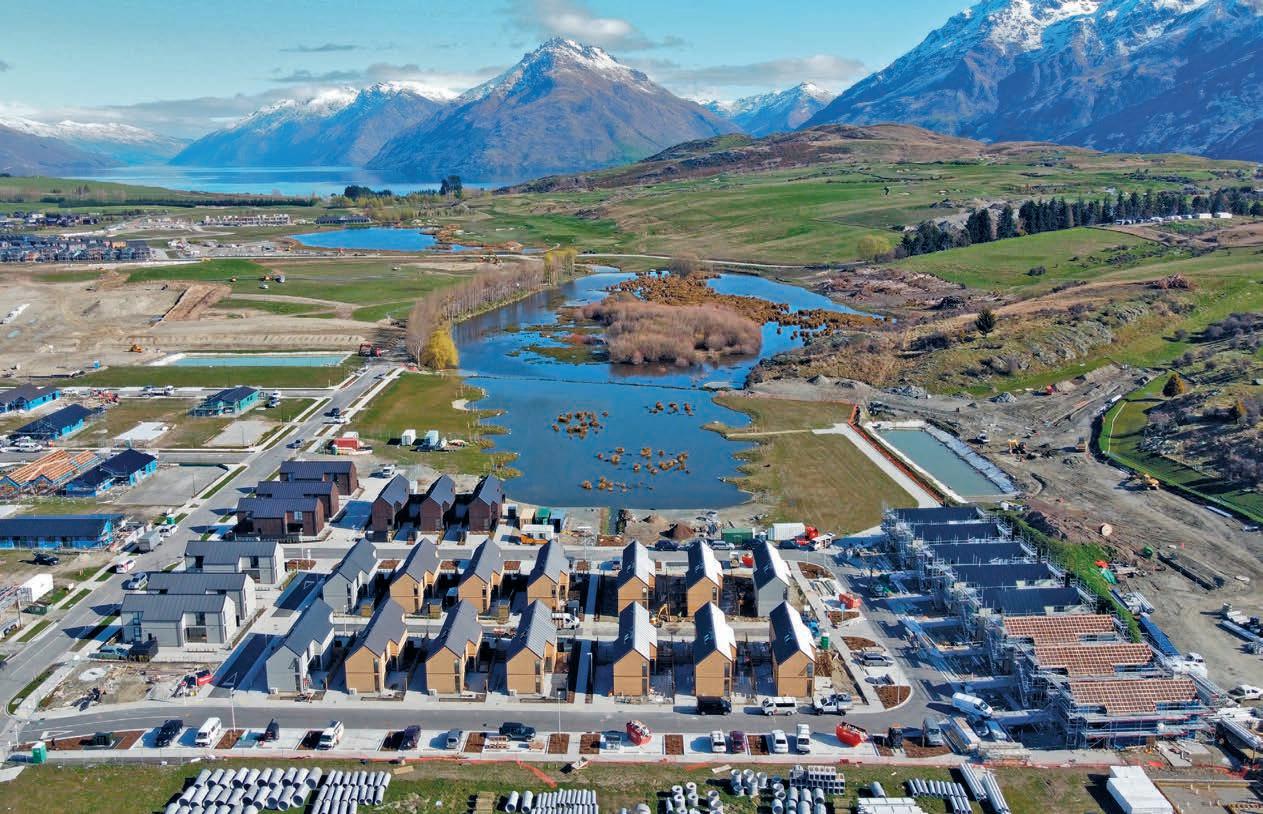
HOW IT’S DONE Story: Jim Childerstone
FORESTRY MINISTER, STUART NASH, recently saw how the Forest Industries Transformation Act could be applied to foster value-added timber products
At a visit to a newly-built Cromwell timber manufacturing plant he witnessed an all-timber housing operation in action.
Swiss backed, Hector Egger New Zealand, built a substantial factory premises in Cromwell’s industrial area over a year ago.
It aims to produce up to 100 buildings per year, from standalone housing to multilevel units such as apartments, motels and hotels.
To achieve this, the factory runs two seven man shifts per day in the electronically mechanised plant.
Current builds range from $500,000 to $7 million, much of it for Central Otago and Lakes District clients.
The bulk of the timber used is engineered laminated veneer lumber (LVL) and crosslaminated timber (CLT) sourced from Nelson Pine Products and glulam from Levin-based Techlam’s plant, explains Hector Egger Managing Director, Stephan Mausli.
“Building components are delivered on site, fully lined, insulated, fitted with conduits and flush boxes, window and door openings, pre-cut to 1 mm tolerances and external walls, lined with breathable and water proof membrane,” he says.
The company builds a 3D model of the initial design process detailing every aspect of the project. It includes every piece of timber, every staple and every screw in the model so the connections can be resolved prefabrication,” Stephan explains.
Hector Egger New Zealand is a 50-50 joint venture with Swiss-based Hector Egger Holzbau AG and local investors, including Tristan Franklin (Director) and Stephan.
“All our timber comes from sustainably managed New Zealand forests,” he says. “Mostly manufactured in this country, with the added benefit of carbon retention in finished products. Thus our buildings help mitigate greenhouse gases.”
Viewing the factory floor from the office balcony Stephan points out the various components of residences being built for a project being developed by Queenstown architects.
This includes up to 20 meter engineered timber beams spanning the roof ridge lines. The rest of the timbered exterior cladding and flooring was mostly cut from 12 meter lengths off engineered wood.
The only metal sighted is the aluminium window frames. A suggestion that this is available through Christchurch-based Health Based Buildings, cut from native hardwood, native red beech, is worth
The factory floor.
looking at and could be an option, says Stephan.
The Queenstown initiative by property developers Black Robin is being funded through Capital Markets.
It is believed to be the first development ever financed through New Zealand’s Stock Exchange for growth businesses, according to Chief Executive Colin Magee.
The first home has already pre-sold for $2.75 million at Jack’s Point south of the township.
Other home units for the southern provinces would range from $500,000 upwards, says Stephan.
He explains that Hector Egger Holzbau AG is a leading European manufacturer with 20 years’ experience in off-site prefabrication of timber buildings and structures.
The Cromwell factory layout is a copy of its largest Swiss factory, using Swiss imported machinery, says Stephan.
He considers himself a New Zealander after moving here nearly 20 years ago as a qualified structural engineer in Switzerland. NZL

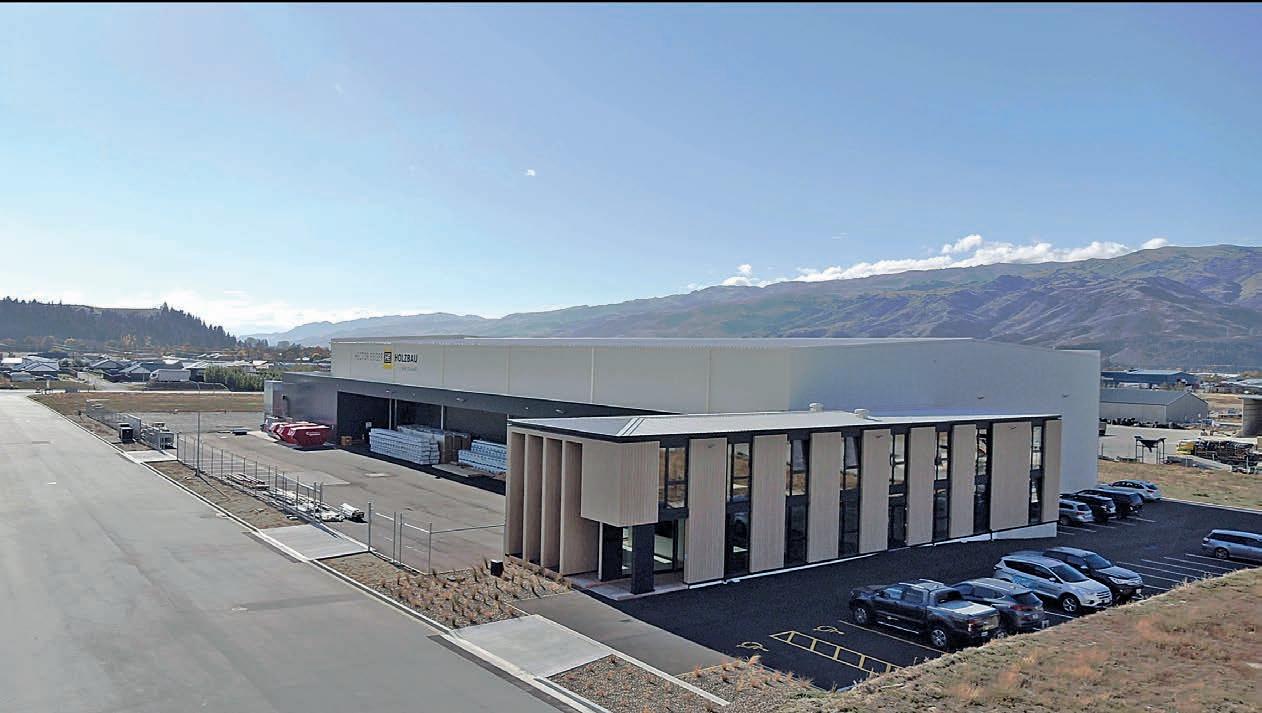
GOVERNMENT INCENTIVES FOR VALUE-ADDED TIMBER?
Story: Jim Childerstone
THE INCREASE IN LOG EXPORTS SINCE
the millennium and general closure of local timber mills and wood processors has prompted action by both Government and the forestry industry to initiate more onshore processing of this country’s forestry resources.
In an email addressed to NZ Logger, the Hon Stuart Nash, Minister of Forestry, listed several steps under the Forestry and Wood Processing Industries Transformation Plan (ITP) on actions to transform the industry.
These include:
“Boosting productivity and supporting New Zealand’s drive to a low emissions future. This includes the allocated $57m through the current 2022 Budget to stimulate investment in the domestic production of value-added wood products. But the Government would want input from all forestry stakeholders. It awaits suggestions of investment proposals, but it would be subject to Cabinet approval” – hopefully before the end of the year.
The plan is to transform the entire supply chain in over a generation, the Minister writes. • Increase woody biomass supply: The
Government will plant 10,000 ha of forest, including alternative species to meet growing demand for biomass. • Government investment to grow wood processing capacity: Ensuring the sector has the right assets to produce high value and low carbon products. • Improve financial incentives: Exploring the appropriate mix of financial incentives to stimulate investment in advanced wood processing and wood based bio-product technologies. This includes accelerated depreciation and investment grants. • Supporting the development of regional manufacturing clusters: The government will partner with the sector to explore, assess, and deliver processing manufacturing clusters.
So far some positive and some mixed responses to the original worded proposals has been received from stakeholders.
Forest Owners Association President, Grant Dodson, writes: “Despite the traditional sawmilling sector there is much opportunity in remanufacturing and engineered wood products. This is part of the focus of the new ‘Forests, Our Low Carbon Future’ campaign, and the recently released Industry Transformation Plan (ITP).
“We can expect considerable demand for timber internationally, particularly engineered wood products for medium rise construction in a modern climate friendly world, he says: “Significant investment in scale and technology is typically required to be competitive in these specialised areas. Other key areas of opportunity are in bio materials, biochemical and bioenergy”.
Referring to the closure of medium-sized, overseas-owned Blue Mountain Lumber in 2008, Ernslaw One Regional Manager, Phil De la Mare, explains it had been loss-making for a number of years “where a New Zealand owner would have closed it earlier”.
Asked if the company would have continued with the mill had the current initiatives been available at the time, he replies: “We unsuccessfully tried to build a new mill in the Coromandel in the 2000s. We lost in the Environment Court, so if the MPI initiative kicks the Resource Management Act to touch for greenfield sawmills, then the answer could be Yes, but the playing field has moved on in everything else.”
Commenting on the future of engineered timber Phil says, “Engineered timber for high rise buildings will only happen at scale when owners, government ministries, councils, universities, engineers, architects, specifiers, quantity surveyors and the village priest are all aligned. Steel and concrete manufacturers have always been very strong at lobbying... at the expense of timber. We have a lot of lobbying and educating to do.”
David Cormack, CEO of Wenita Forest Products says Wenita is broadly supportive of the plan saying the sector can do this by: • providing low emissions construction materials and fuels, • increasing domestic processing of lower grade logs, • increasing export earnings from highvalue products made from wood, • replacing emissions-intensive building products with engineered wood products, • increasing the resilience and productivity of our plantation forests.
David urges ongoing government support and partnership as essential for this plan to be successful.
He says some of the ways government can support the plan are to coordinate and bring together the different parts of the sector - forest owners, processors, forest advisors etc. “to work together on the plan”.
Also, “lead by example and show the way with the wood-first policy for government construction projects, and demonstrate new building products and construction techniques.”
David suggests supporting increased domestic processing with tax relief, simpler consenting processes and recognition plus rewards for the carbon locked-up in processed wood products. That is, carbon credits for wood products.
On the question of wood-based biomass for heat energy and electric power generation, Otago-based Pioneer Energy is expanding its operation to Milton and the Central North Island. It already has chipping operations in Naseby, Dunedin, Timaru and Pukaki, where it is trialling wilding conifers as a resource.
Pioneer’s Richard Ireland, at this stage, believes it is not efficient and too costly. “It only makes sense where fuel is available and cheap, and/or existing electrical infrastructure is not capable,” he says.
However Scion Research notes it’s a matter of economy of scale where excess steam is used to run generators. It cites Red Stag sawmill near Rotorua which has three boilers with a capacity of around 55MW thermal and two steam turbine generators ranging from 1 to 3.4 MW electric and 1 to 2.9MW electric maximum.
It reports a large cogeneration plant at Kinleith Mill, Tokorua producing steam and power for the pulp mill where the boiler can run on wood or gas, or both. The boiler is around 130MW thermal and steam turbine generator is around 39MW.
The Pan Pac pulp and sawmill site at Whirinaki runs a cogen (co-generation) plant producing 14MW electricity from a thermal 45MW boiler.
Experiments with wood-based liquid fuels and chemical extraction are ongoing with research bodies. Port Blakely, for example, is in the process of researching extraction of essential oils by utilising the thinnings of one of its plantations. NZL