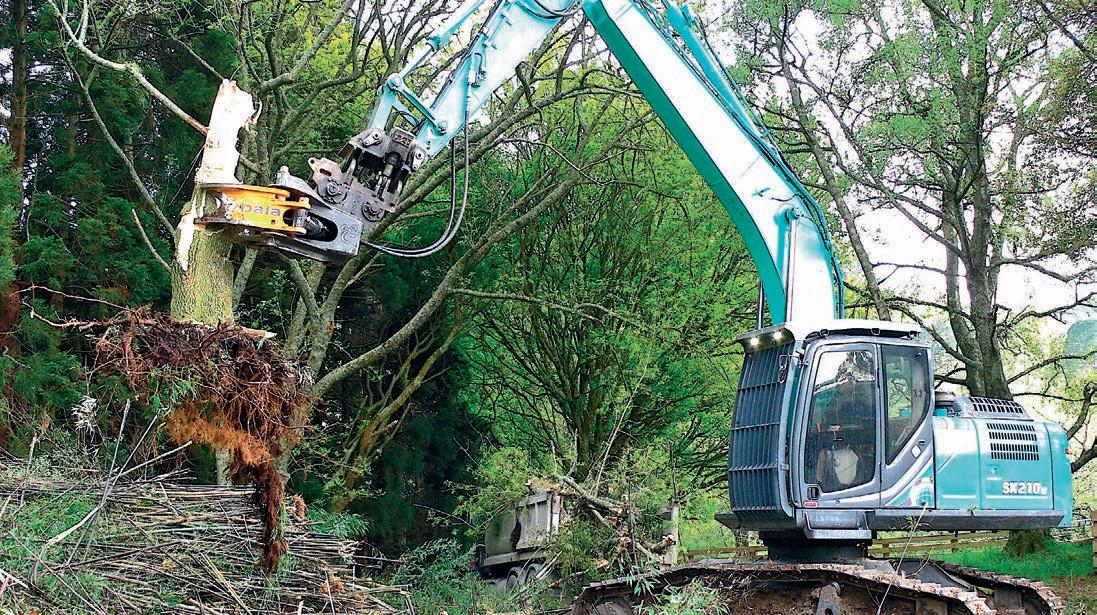
8 minute read
Three-in-one compact combo
by nzlogger
THE NAME HENRY FEAR IS SYNONYMOUS with innovation in New Zealand forestry circles. Whether it be as an early disruptor in silviculture with mechanical planters, introducing ‘smart spades’ which identify exactly where to plant a tree seedling, or hydrogel to extend the planting season, where there’s transformation you’ll find Henry in the thick of it. His latest project is no exception. The Kobelco ED 160, aka the Blade Runner, using an MDE Koala 400 tree shear attachment, is doing the job of three machines when we meet Henry in Kaingaroa Forest.
Henry of HA Fear contracting says, “Possibly the only three-in-one machine in New Zealand that can fall and bunch trees and bulldoze at the same time, the Blade Runner is a great example of a ‘one man, one machine’ operation and it removes the need for a whole lot of additional more expensive equipment.”
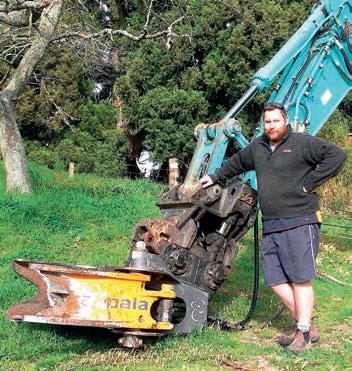
He explains: “There are three aspects to it. Because it’s an excavator top half, we can dig with it; we use the tree shear to cut the trees down and directionally fell them; and then the bulldozer blades sweep the skid sites and form them – all in one machine.”
For a small machine it’s clear it can do a lot. The 16-tonne excavator base with upgraded final drives and drive system give it the same pushing power as a D4 bulldozer with a six-way bulldozer blade, so this excavator/bulldozer combination is “really manoeuvrable, incredibly powerful and can push a large volume” says Henry.
This becomes clear as we watch operator, Anton Kereama, deftly take the Blade Runner through its paces. Instead of the processor coming through to cut the trees into logs; the forwarder taking them off to another skid site and the bulldozer doing the earthworks to form the skid site, the Blade Runner cuts the trees, stacks them off the edge of the skid and forms the skid site without any double handling.
“It’s good… quite a bit different. It’s the first machine I’ve driven with a blade and head sheer,” says Anton.
“It’s much more efficient,” adds Henry. “We can do a 40x30m skid site in about four-and-a-half hours for production thinning, which is pretty good going. It averages about one week a month doing that particular job and the rest of it is general earthworks and roading for Timberlands and the Kaingaroa Processing Plant (KPP) or on farms.”
High efficiency
Henry has come a long way, from starting in earthworks in 2010 to now thinning, cutting and removing stumps in a single operation. When work with a chipping contractor dried up, he approached Timberlands and put a machine into land preparation for spot cultivation. The rest, as they say, is history as he “slowly grew the business, one machine at a time”. Now there’s the Blade Runner, four 20-tonne excavators, two 30-tonne 6x6 articulated trucks, one D65 dozer, one transporter and a metal truck and trailer.
The idea for the Blade Runner came after initially building skid sites using a D65 bulldozer, working in conjunction with the logging crew who would cut the trees down, level the logs on the skid site, take them to a separate skid site and then allow for the bulldozer to form the skid, explains Henry.
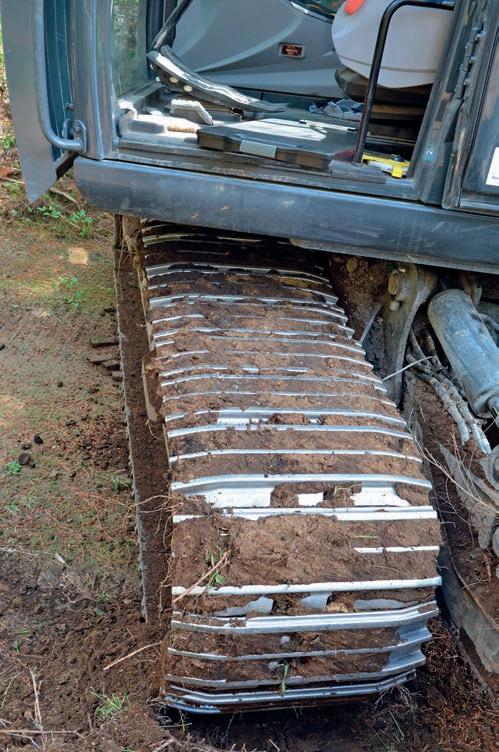
“We replaced one excavator with the 16-tonne Blade Runner after it tipped over, then it evolved when we matched that up with the tree shear and gave it a go doing the entire job with a single machine.”
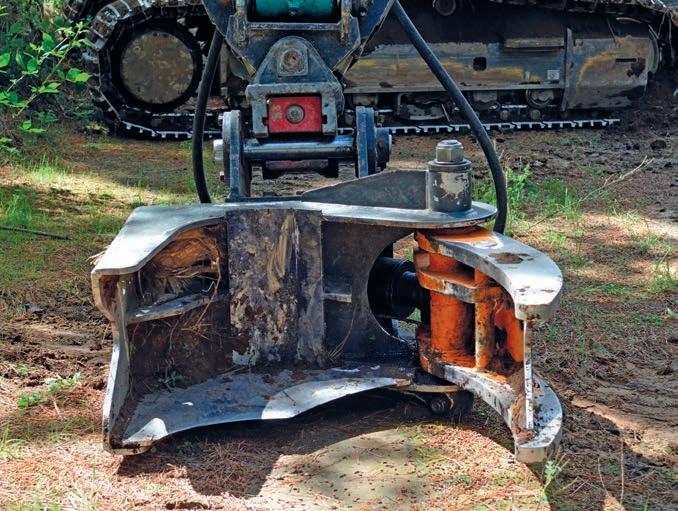
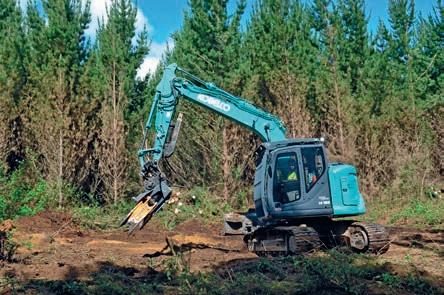

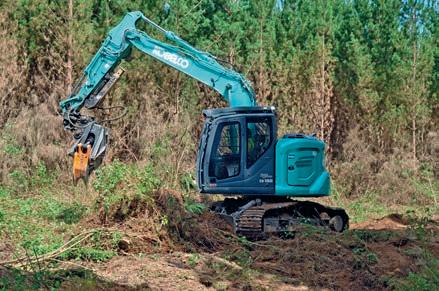
It’s clear the Blade Runner can handle the job with ease as we watch it prepare the Kaingaroa site for a production thinning crew, in one pass selectively falling the unpruned trees and stacking them while flattening the skid.
“The crew will cut down about a third of the trees that are there and ready the block for its final crop. We come into the block a few weeks early and form all the skid sites, so when the logging crew comes in there are efficiencies gained in having the site set and ready to go.”
Feature-full
The Blade Runner boasts a number of features that combine to achieve this efficiency. The excavator part of the machine is fitted with a coupler with a multidirectional tilting head. Then there’s the thumb for picking up material when it’s got the bucket attached. The excavator itself has an oversized, more powerful engine than the standard excavator, says Henry. The undercarriage sits on 20-tonne track gear with an extra-strong final drive and a six-way bulldozer blade lifts up and down, tilts and angles at the same time, able to fell trees sideways.
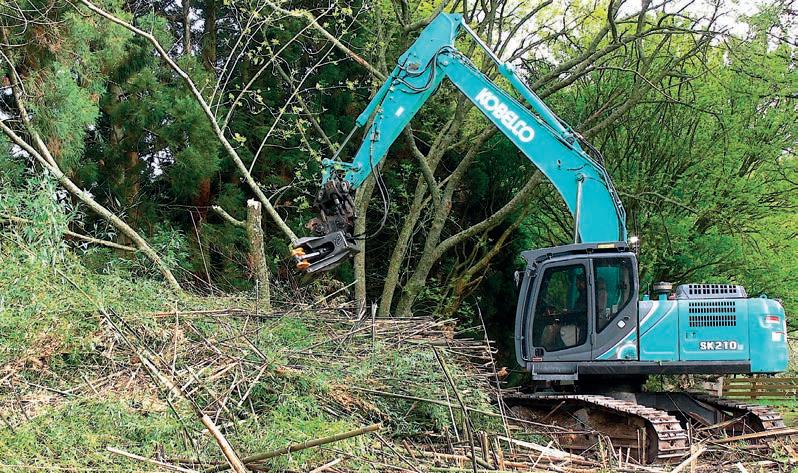
It’s the scissors on the front that get your attention though. Designed and manufactured in Northern Ireland, Boss Attachments’ MDE Koala 400 tree shear has a Hardox body and shear arm and replaceable Hardox blades
“It’s the most versatile attachment that I’ve ever operated and it provides us with the ideal balance between operational safety and performance. The Koala has been able to handle anything we put in front of it,” says Henry.
“The Koala also removes any need for a chainsaw attachment, which in turn removes the requirement to spend around $30K on bullet proof glass for our excavator,” he adds. “Plus it can cut right down to ground level, and the blade only needs sharpening at around two-monthly intervals.
“The operator can securely clamp on to the tree – prior to shearing – and then lift and place the sheared limb exactly where it needs to go. It’s an awesome tool for us and is proving to be a great investment.”
Koala has recently added larger 500 and 600 models to its range and these feature a single cylinder and a gas accumulator to deliver massive cutting for its 1.2 metre jaw. They are suitable for 18- to 50-tonne excavators, weigh 1060kg and 1500kg respectively, and have a 500mm or 600mm cutting dimension.

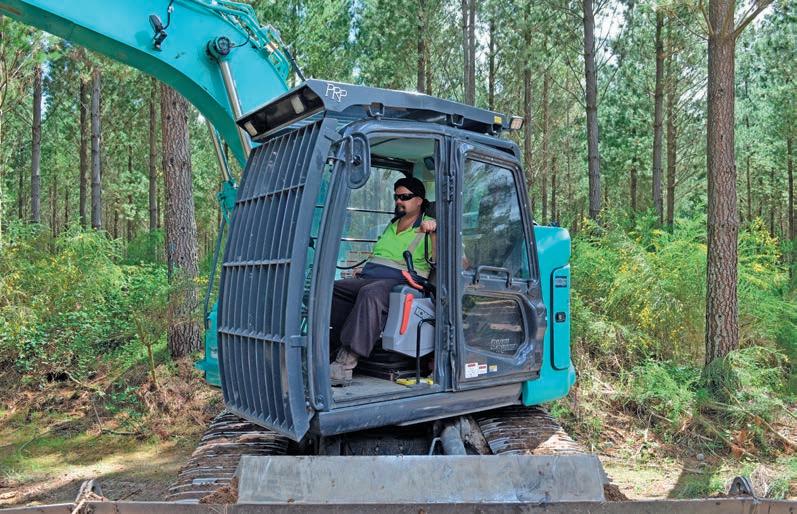
Seeing the compact Blade Runner manoeuvring between the trees, cutting them like toothpicks and cleaning up after itself, Henry tells me when it’s done here it will be “in the log yard cleaning up messes and doing roading work” and that it can potentially help with fighting fires thanks to its compact size too. Definitely one to watch! NZL totalenergies.co.nz @totalenergiesnz
Top: Removing limbs with ease.
Middle: Operator, Anton Kereama is enjoying the efficiency of the machine.
Bottom: Henry Fear and Anton Kereama say the added power and size of the blade means this little machine can push a large volume of material.
Reliable equipment is essential in New Zealand’s thriving yet challenging forestry industry.
High altitudes, rough terrain and extreme weather conditions put pressure on your people as well as your machinery. An environment where the right oil or lubricant is key to a safe, uninterrupted and profitable forestry business.
SINCE 2012 THE LOGGING INDUSTRY has gone through something of a revolution. As a result of mechanisation, the industry has been able to increase the volume harvested by about 50% (we harvested about 23 million m3 in 2012, and 35 million m3 in 2022) using 10% fewer logging workers (the NZ Forest Owners Association reports we had 8,300 ‘In Logging’ 10 years ago; more recently that was 7,900). That means the industry is more reliant on its harvesting machine operators than it has ever been.
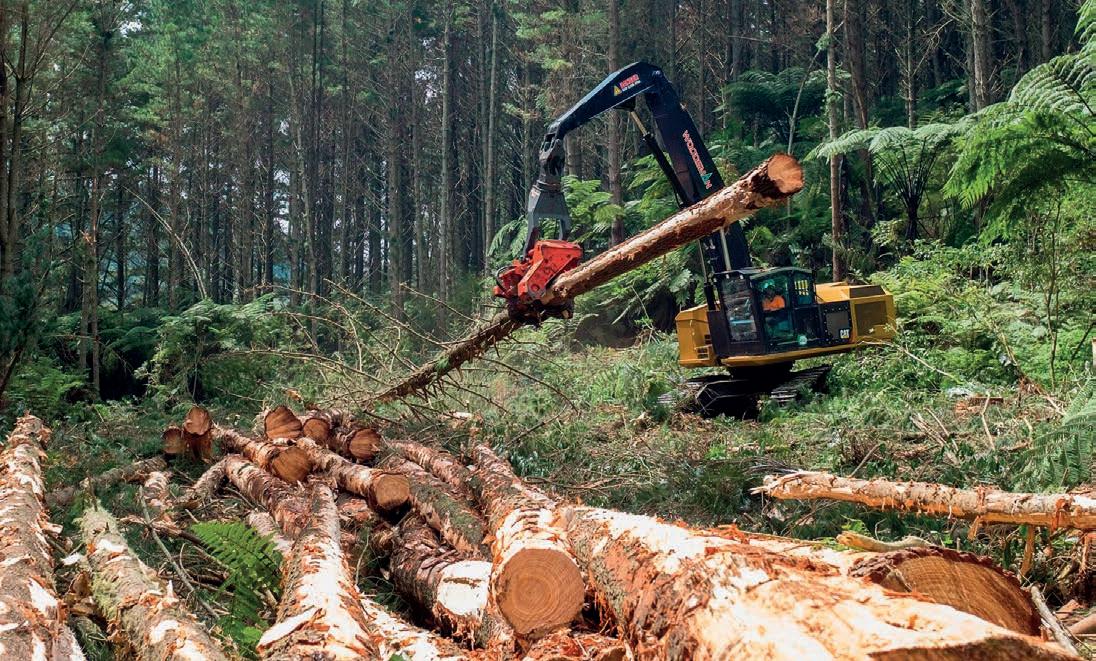
While moving forest workers into machines has significantly improved their physical safety, the greater concern now is mental health. Operating a high-value machine in a high-production environment can obviously be very stressful. The objective of this research (first covered in NZ Logger, June 2020) was to improve our understanding of what causes machine operators’ stress, but also what creates a healthy and happy work environment.
Who contributed to this research?
A total of 27 operators were interviewed for this project. Three operated the harvester, 5 the prime mover, 5 processed and 14 were mainly fleeting and loading. They were from 18 different contracting crews and worked for 14 different forest owners.
What did we find out?
You love the work for similar reasons: The physically demanding nature of the work – being outdoors and operating big machines that can shift a lot of wood quickly. The challenge – winning the battle against the elements (weather, terrain and wood) to make things happen.
What it allows you to do – providing a good life for your family.
Operating machinery is challenging and mentally demanding which can lead to both stress and wellbeing: Wellbeing: Many operators thrive on working hard to meet a challenge (like a production target). When you can control the factors that allow you to be successful it leads to ‘wellbeing’. When you are well, you have the energy to do everything you need to do and then recover day-to-day and week-toweek. You remain fit, do things you enjoy doing and are involved with family and community. You also have a strong sense of personal safety and financial success.
“Flow” is that state of mind that happens when you are so engaged in an activity that your sense of what is happening around you is lost. It is an effective antidote to both boredom and anxiety, and it requires a balance between the challenges being faced and the skills required to meet that challenge
Stress: Conversely, if the challenge is not reasonable, or the factors that allow you to be successful are outside of your control, this leads to stress. This can more readily lead to fatigue, unhealthy lifestyle choices (insufficient exercise, comfort eating, drinking and drugging), and conflict at work and home as energy levels are overwhelmed. For some of you it has resulted in your quitting the crew or leaving logging altogether.
What generates stress?
Anything that impacts the crew’s ability to achieve either their contractor’s targeted daily uplift (loads per day) or your ability to maintain throughput (tonnes per hour).
Anything that gets in the way of your ability to know what’s going on or influence what’s happening within the crew, particularly in the way it solves production problems. There are two obstacles to knowing what’s going on or having a say in a crew. They are:
• The formal hierarchy of crew boss, foreman and second in charge; and
• The informal hierarchy of experience and capability.
The more controlling the hierarchy is, the greater the potential for stress as a result of that hierarchy.
Anything that threatens the ability to provide for family. The two most significant risks are hazardous working conditions and insecure income due to market downturns.
What generates wellbeing?
Within the operator’s control:
• Adapting family life to cope with long working hours.
• Improving skills, both those useful for operating the machine and those that are useful for more personal reasons (e.g. financial skills, relationship skills).
Controlled by either the forest manager or the contractor or both:
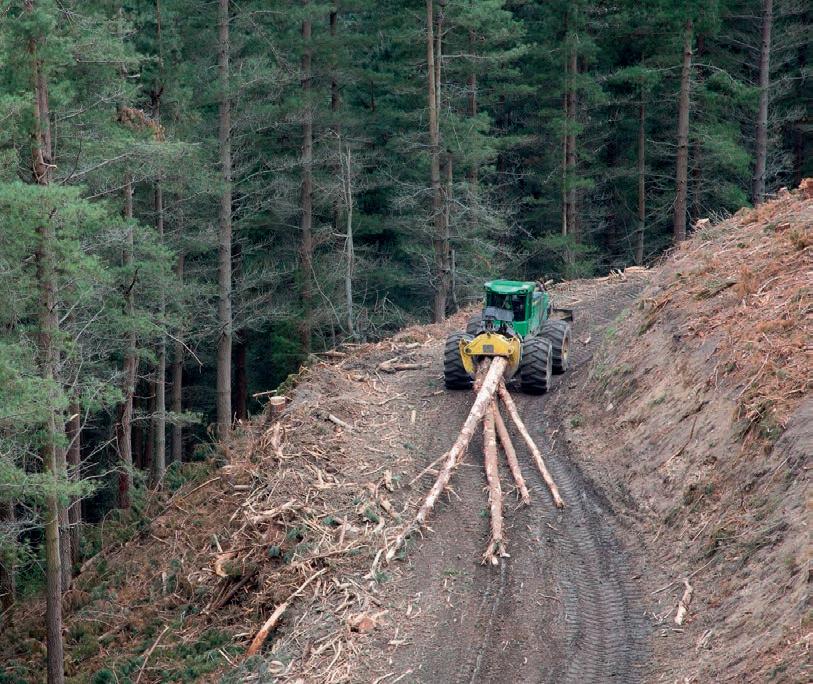
• A harvesting supply chain (roads, skids, logging machines, trucks and receiving point – port, sawmills) that can deliver and receive the required number of loads within healthy work hours on a one- or two-shift basis.

• Increasing certainty over income and safety.
• Being part of a family at work. That means being a tight-knit crew, knowing the target, being paid fairly and being included in decision-making.
How can we improve wellness amongst operators?
The harvesting supply chain needs to be designed by forest managers to deliver the required number of loads within healthy daily and weekly working hours. While most operators would jump at the chance to work eight to nine hours if income remained the same as that achieved over longer hours, it was noted that participants working in happier crews were working less than 10-11 hours per day including travel (less than 55 hours per week).
Highly productive logging crews that are well led and have a great crew culture also improve operator wellbeing. For the participants, that meant having the right gear for the job in the right amounts, having operators who could operate more than one machine and cover for each other, being transparent about production expectations, being paid well, and being included in decision-making processes especially where those decisions had an impact on their ability to do the job.
For a video presentation of these results visit: https://www.youtube.com/ watch?v=5Ki8B9A2TBo
For questions or feedback on whether what you see here is on target or not, contact Trevor Best at: trevor.best@pg.canterbury. ac.nz NZL