
12 minute read
Fighting the fatbergs
Grease management systems have developed significantly over the last decade to deal with food, oil and grease from a growing food industry, as Dux explains.
Business is not ‘as usual’ for plumbing and food service professionals when it comes to combatting the large amounts of fat, oil and grease generated by a growing food industry. Guarding against sewer blockages, expensive clean outs and damage to sewer lines is an increasing focus of local councils.
To meet growing demand, grease management systems have been developing significantly over the last decade, with more advanced features to increase their level of performance. The wide choice can make life difficult for professionals evaluating, selecting and installing. Choosing the wrong system can have a negative impact, but times are changing and grease management is advancing; from simple capture and contain systems, to systems that capture, separate and even convert.
GREASE INTERCEPTION
How we talk about grease management systems is changing. The term ‘grease trap’, which is still widely in use, is making way for more specific terms. ‘Trap’ suggests the presence of a water seal, whilst ‘grease interceptor’ more appropriately describes the modern unit. Generically the application of a grease interceptor, regardless of type, is defined as follows: “A plumbing appurtenance or appliance that is installed in a sanitary drainage system to intercept non-petroleum fats, oil, and grease (FOG) from a wastewater discharge.”
Specific characteristics define the three types of interceptor: 1. Hydromechanical Grease
Interceptor (HGI) These units are sized by flow rate (litres per minute) and qualified separation/ retention efficiency. They control the flow to entrain air into the effluent, with baffles and/or barriers promoting hydromechanical separation. Most HGIs can be installed inside or outside the facility they serve and either above or below the grade. 2. Gravity Grease
Interceptor (GGI) Characterised by volume, generally GGIs have a minimum 30-minute retention time, more than two compartments, over 100 litres total volume as per the NZBC, and gravity separation. They are generally installed outside the building below the grade. 3. Grease Removal Device (GRD) GRDs come in a variety of forms with various methods for removing fats, oil and grease either through heat, enzymes or bacteria/ enzyme combination.
ENGINEERED FOR EASY
Endura Grease Traps Dux Industries distribute the Endura range, which has been ‘engineered for easy’ with: lightweight self-supporting bodies (empty they weigh only 106-128kg) load rated trafficable or pedestrian lids optional risers for deeper installations.
Extensive development has resulted in an internationally recognised range of hydromechanical grease interceptors that are easy to install, less susceptible to corrosion, designed for optimal maintenance and hold up to 75% grease within total volume. www.dux.co.nz/productcategory/greasemanagement/grease-traps/
Think downstream—act upstream Increasing population is a given and will generate more demand on food outlets, increasing the load on our wastewater systems. Another source will be domestic wastewater and, in a growing number of developed countries, residential grease interceptors are mandatory. Grease management systems are expected to continue to evolve to meet these changes, even in New Zealand.
“We had ongoing issues across the Matakana Village site with fats, oils and grease solidifying downstream before the main sump area, which meant significant monthly maintenance costs to pump out,” says Laser Plumbing Warkworth Operations Manager Tony Franich. “As there are multiple food outlets and restaurants, we needed a superior solution to deal with their fats, oils and grease, given these are busy food service areas. We decided on a combination of the Dux Stainless Steel Grease Converters and Endura® XL Grease Trap from Dux Industries for our Matakana Farmers Market site.
“The Stainless Steel Grease Convertors were conveniently installed under the bench areas of both Matakana Kitchen and Honest Chocolat, and a floor installation in The Matakana Deli, importantly using the Dux Actamatic Liquid to prevent the previous solidification issue. The lightweight Endura® XL 75 Grease Trap was installed for Matakana Bacon Company within their existing carparking area, as it is a trafficable grease trap. Being only 106kg it was easy to get onsite, and installation was a piece of cake.”
“When deciding on the type of grease management system, important considerations are: the availability of a suitable installation location appropriate sizing to ensure performance ease and cost of installation simple maintenance long term efficiency and durability. This safeguards the private and public sewer networks, prevents costly blockages and reduces council and owner costs.”
GORDON GEORGE
Trade Waste Manager, Hutt City Council
Dux Grease Converters Dux Grease Converters capture and permanently transform fat, oil and grease (FOGs) from the wastewater of commercial kitchens, cafés, bakeries and restaurants to water-soluble, environmentally acceptable (effluent) levels. The system includes converter, pump and bacterial liquid. Dux Grease Convertors come in a range of sizes to suit the patronage capacity of restaurants big and small. www.dux.co.nz/product-category/grease-management/grease-converter-systems/ For more information contact dux@dux.co.nz
Get insured today and save.
Exclusive corporate rates for Master Plumbers members.
The best quality life, medical, income protection, mortgage cover and more.
ACTIVE SURFACE heating & cooling An innovative Austrian surface heating and cooling system has been introduced to New Zealand, as Kiwi plumbers discovered during a recent nationwide trade show.
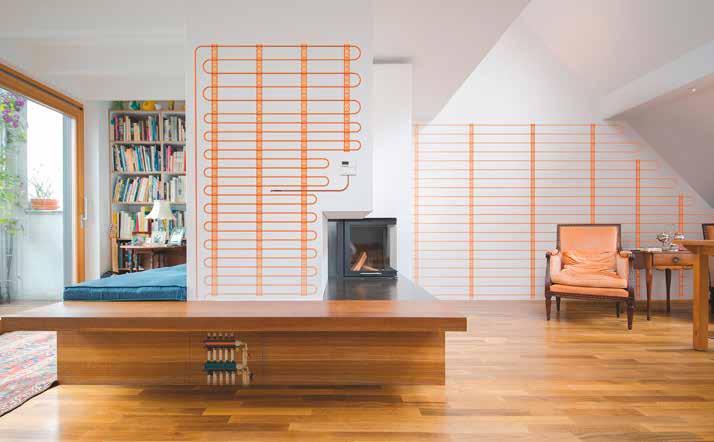
N
ew Zealand homes are typically heated in one or two rooms only—or not at all. Space heating and cooling is often an afterthought, with forced air heat pumps installed on the wall or floor once construction is complete. That, coupled with a recent trend to build large houses with floor-to-ceiling glass windows and doors, means that even top-end homes can be cold in winter and too hot in summer.
How it works Earlier this year, Alexander Watzek of Austrian company Variotherm travelled around the country with their New Zealand partner, Central Heating New Zealand, talking to plumbers and other construction industry professionals about the company’s modular surface heating and cooling product for new builds and refurbishments, which he believes is the future in comfort and sustainability in both commercial and residential situations, particularly as cooling becomes more prevalent in people’s homes. He refers to this approach as ‘active surfaces’.
In essence, 18mm thick modular gypsum fibre panels with preinstalled pipe coils are installed on the wall or ceilings. The pipes in the panels are connected to the central manifold. The panels can be installed with the plastered interior finishing or, more typically for New Zealand, as a drywall system.
For commercial situations, ceiling grid modules are available with the option of perforated acoustic panels, enabling the panel to fulfil four functions: ceiling panel, heating, cooling, and acoustic diffuser.
With this water-based wall or ceiling heating and cooling, the entire surface heats up or cools down quickly and evenly to provide the most comfortable ambient temperature possible without needing high flow temperatures for heating or very cold temperatures for cooling. This translates to very high efficiency and comfort.
“We have reached a point with the changing climate where we need to accept that heating and cooling running temperatures must
A rendering of Variotherm active surface heating and cooling in a domestic setting.
Variotherm ceiling grid modules are available with the option of perforated acoustic panels for commercial heating, cooling and acoustic diffusion.
be reduced to save energy—and this will probably become law in Europe,” says Alexander. “We need to open our eyes and minds to this new normality.”
Variotherm is a low-temperature system due to the fact that the pipes are laid over a large area. For the heating aspect, the water generally needs to be heated to
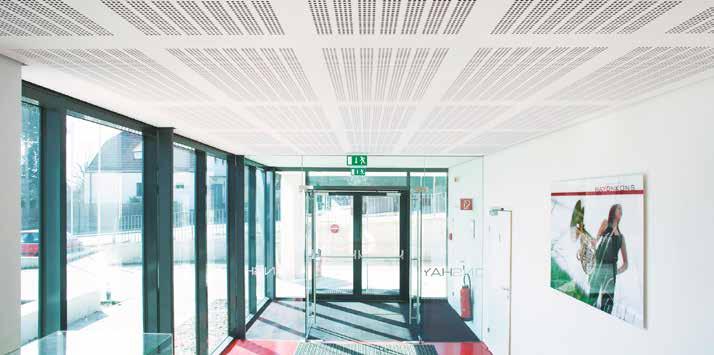
between 26°C and 38°C compared with a conventional radiator flow temperature of up to 60°C. Being radiant heat, the room air temperature can also be reduced by up to 2°C compared with convection heating while still feeling totally comfortable.
For cooling, the room will feel comfortable at around 26°C as opposed to around 23°C for an air conditioner, saving the homeowner up to 30 percent on energy costs.
Biomass, electric air-to-water and ground source heat pump systems are popular heat sources for Variotherm products in Austria, says Alexander, but diesel, gas and solid fuel boilers are equally viable alternatives.
COST VS COMFORT
Any kind of hydronic central heating—underfloor, radiator or wall panels—comes at a higher cost than, say, a single wallhung air heat pump but, says Central Heating New Zealand director Lyall Smith, it’s all a matter of what priority you put on comfort. “It’s a feeling the rest of the world are familiar with that Kiwis are beginning to understand,” he says.
Central Heating New Zealand has seen 20 percent annual growth in the hydronic central heating market during its 18 years in business, but there’s still some way to go in educating end users, as well as architects, builders, consulting engineers, merchants and the plumbers installing these products, he says.
Central Heating New Zealand has a training academy at its Christchurch office, running courses covering heat loss calculation, system design and individual product application.
30
28
14 16 18 20 22 24 26 R oom surfaces t empe r atu r e °C
12
10 12
Just about still cosy
Cosy
Zone of Comfort diagram showing that not just the air, but also the surfaces in the room need to be warm to provide good comfort.
Inhospitable
14 16 18 20 22 24 Room air temperature °C
26 28
Rinnai offers a design service, with installers receiving a plan of this kind with the duct kit.

Quiet, quick to heat up and unobtrusive, gas-fired ducted central heating provides homeowners with a comfortable ambient temperature throughout the home, says Rinnai’s Brian Rowan.
DUCTED CENTRAL HEATING
T
o understand how space heating works, you need to understand basic physics, says Brian Rowan. Most of us know that warm air rises—and that’s because the heavier cold air pushes it up. If you want to be warm in a room, you’ve got to get the warm air down and keep it there.
Air flow Forced air systems that blow heated air down (think high wall heat pumps), suck the warm air from the top of the appliance and blow it down to the floor. The issue with this is that moving air has the chill factor—it takes heat away from your body and cools it down— which means the appliance has to work harder and run longer to reach a comfortable temperature in the room than other heating methods. “Even at 45°C, fast moving air can feel cool,” says Brian.
In addition to this, the temperature of the air leaving the heat pump depends on the outside air temperature and moisture.

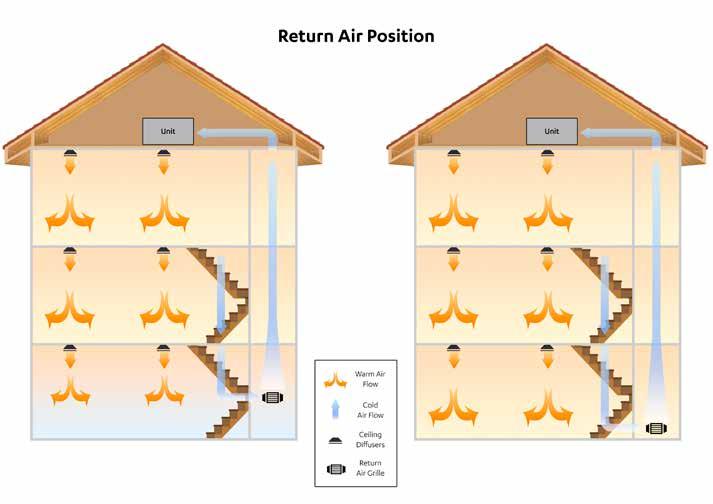
The air intake must be at floor level to maximise the effectiveness of the system.
“This is not the case with gas-fired ducted central heating, where you have control of fuel source and air flow to generate heat,” he says. “If a room is sitting at 10-20°C, it doesn’t take much air flow to change its temperature quickly to a comfortable 20°C by setting the heat source at 65°C.”
Installer advice • Rinnai offers a design service for its
Rinnai gas ducted central heating system, which includes aspects such as sizing the heater and recommending where to put the air intake. • Installers need to provide a property plan to scale, with practical details such as floor material, height of stud and access to roof space or subfloor. • The Rinnai Tradesmart website has installation and service manuals along with training videos. • Rinnai also has a technical helpline and offers installer training on how to run ducting for maximum performance.
Air collection The other key difference from forced air systems is the air collection method. With ducted central heating, the use of flexible ducts means the system can be designed to collect air from the lowest, and therefore the coldest, point in the house—in a two-storey home, this is generally the ground-floor hallway. “The system essentially sucks the cold air out of a home, rather than blowing warm air around the home,” explains Brian.
To do this, interconnecting spaces are needed, such as a subfloor or roof. Ducting is generally too large to go between floors. “In a 300sq m house, there is 750-1100 cubic metres of air to heat, so the ducts need to be quite large to do this quietly. You start with a big duct of around 300-450dia at the heater, and a large grille in the hallway, then install smaller ducting down to 150dia around the building.”
The final outlet will be in a room furthest away from the air intake as possible, so the warm air can be drawn back to the intake and recirculated. heating in that the heat is almost instant—the householder doesn’t need to heat the home for long periods while they are not in it. The system is programmable and can be designed to split into zones if needed—for example, if a retired couple only uses one end of the house when the grandchildren come to stay.
“A lot of Kiwi homes use spot heating with, say, a wood fire in the living room and a heat pump in the dining room or bedroom,” says Brian. “This is actually wasteful of energy because our bodies feel even a 1°C-2°C temperature difference, so going from a room that’s 20°C to one that’s 18°C will be noticeably colder—and going from one that’s 24°C to 10°C will feel like Siberia. As a result, we tend to run the appliance for longer to achieve a higher temperature to warm ourselves up. By contrast, whole house heating set at 20°C will feel warm.”
About the author: A plumber and gasfitter by training, Brian Rowan has worked in the central heating industry for over 50 years, working on his first hydronic central heating system in the UK in 1966. For almost 25 years, he has been involved with Brivis gas-fired ducted central heating, which is now owned by Rinnai.