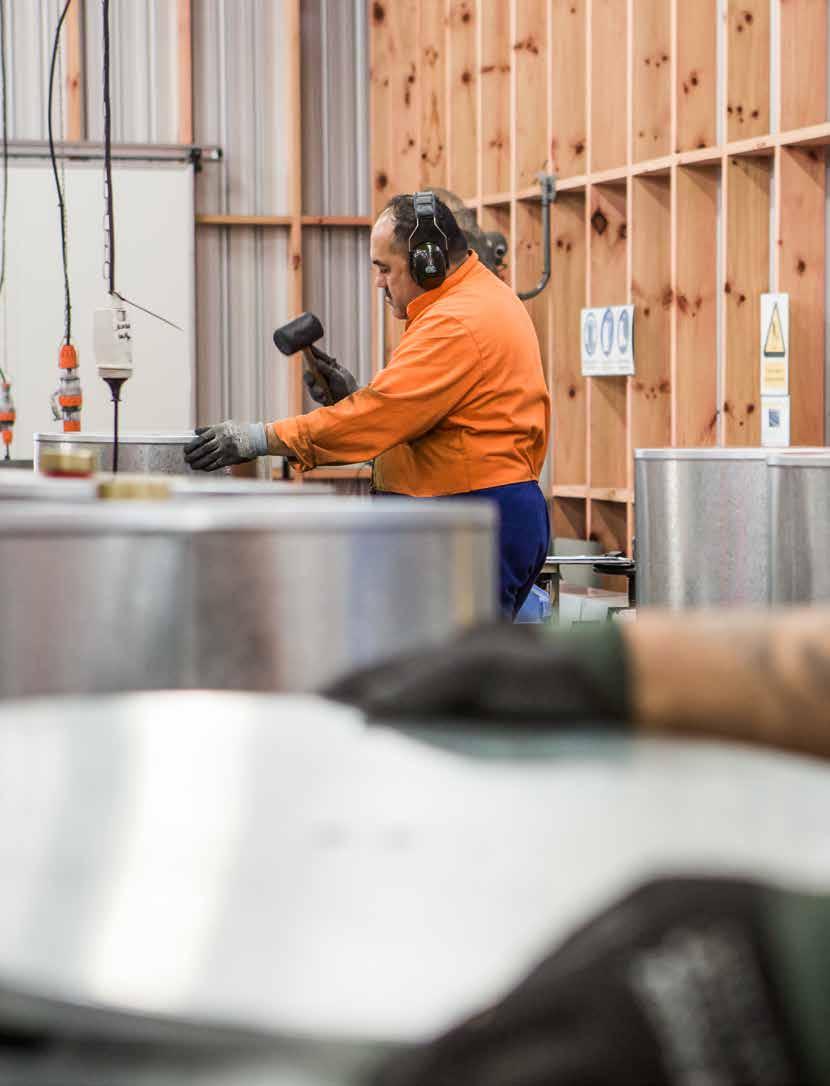
12 minute read
Made in New Zealand
At a time of construction supply restraints, with Gib as rare as gold dust, the plumbing industry is fortunate to have a wide choice of readily available products from New Zealand manufacturers. NZ Plumber looks at some of what’s being made on our doorstep.
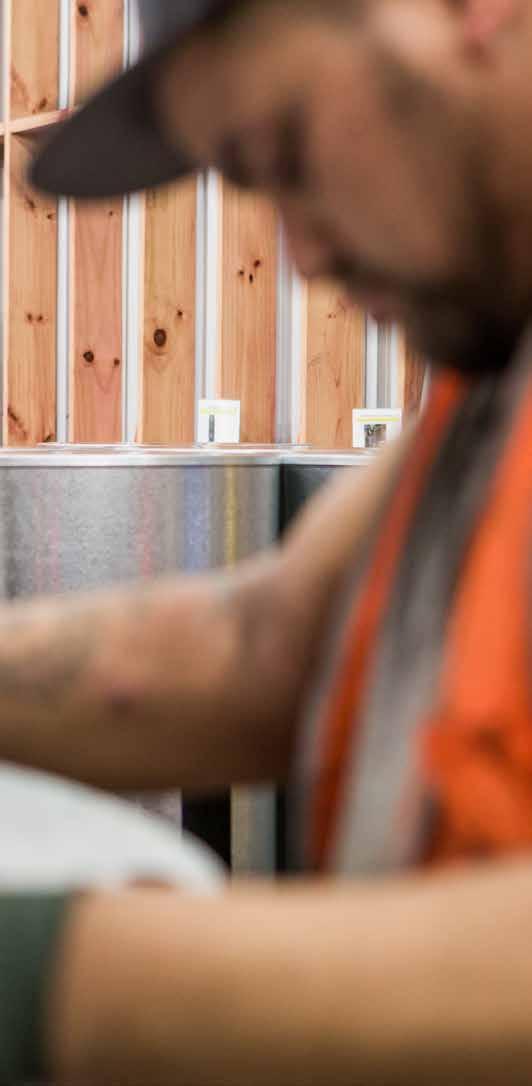
RINNAI
Rinnai New Zealand manufacture their gas fireplace collection and hot water cylinder range at their headquarters in Māngere, Auckland. They also make the Boil&Brew hot water dispensers and build commercial hot water systems. The company has been manufacturing gas heaters in New Zealand for almost 50 years, since they first started in 1975, with gas fire manufacture beginning in 1997. “Cylinder manufacture has been on site since 2012, but we are carrying on the HJ Cooper tradition of New Zealand manufactured products for the plumbing industry, which goes back to 1904,” say Rinnai.
All R&D for manufacturing is carried out here in New Zealand. “We source many components from local suppliers but also source components and technologies from specialist suppliers all over the world. In particular, we are able to draw on the technical expertise of our parent company in Japan for our control systems.”
Rinnai say they have been significantly affected by supply constraints and shipping delays but are managing by increasing lead times and buffer stocks—and, in some cases, relying on air freight for critical overseas items.
“Where possible, we are working with suppliers based in Australia and New Zealand to keep lead times to a minimum,” they say. “We are also working with our suppliers to understand their constraints and provide a longer-term view of our demand forecasts. This allows them in turn to better plan for our requirements.”
Rinnai recognise and acknowledge the challenging landscape plumbers have faced in recent times. “As a supplier to industry, we want to do more to support this critical sector and the plumbers and businesses that represent it. As part of our response, we now have a dedicated Trade Partnership team. This is a clear commitment by Rinnai to support the growth and sustainability of plumbers across the country.”
A recent sustainability initiative from Rinnai has been removing the polystyrene packing from their latest gas fire release, the Novo. This is something they are looking to continue for any new products manufactured in New Zealand.
MARLEY
The vast majority of Marley’s plumbing range is made here in NZ. This includes Optim® DWV pipe and fittings, Stormline® stormwater pipe and fittings, Marley rainwater systems, polyethylene pipe systems and more. They supplement this range with products from sister companies within Aliaxis, such as the DBlue acoustic plumbing system and the Akasison Siphonic drainage system.
Marley’s products are manufactured in the North and South Islands at their Auckland and Ashburton facilities, using raw materials such as resin and additives generally sourced from overseas.
“Like all suppliers and manufacturers, we have been affected by ongoing global supply chain challenges and equally the local Covid impact on the health of our people,” says Marley. “However, when we saw this starting in 2020, we quadrupled our safety stock of key materials and over the last two years have put significant resource into managing our supply chain. Making our products locally has allowed us to respond faster to market demand.”
Marley says possibly its biggest focus to support plumbers has been on stock availability. “We take our position in the plumbing industry very seriously and have invested significant time and resources over the past two years to ensure continuity of supply to the best of our ability. Our New Zealand manufacturing operation team usually operates 24/5 but for the last two years have been working every second weekend to help meet demand.”
Globally, parent company Aliaxis has a target to reduce its carbon footprint by 75%—an ambitious target which Marley plans to achieve locally in NZ through recycling, waste minimisation, reduction of energy use and innovation.
“More recently our focus has been on collecting, crushing and reusing PVC and PE offcuts or products at the end of their life, so they don’t end up in landfill. So far in 2022, we have recycled and reused almost 300,000kg of PVC and PE through this programme. As part of this, one of the key initiatives has been to make it easier for plumbers to recycle by setting up collection bins both on job sites and at merchants.”
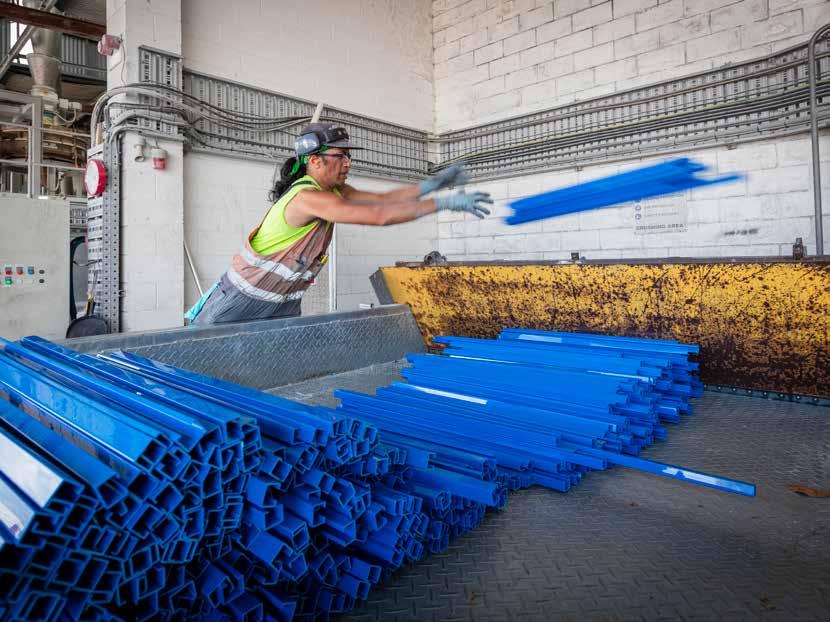
HYDROFLOW

Since 2016, Hydroflow has distributed Anka LDPE fittings, spray guns and nozzles manufactured and assembled by Apex Valves at its factory in Avondale, Auckland. “There have been no supply restraints for the Anka range, and we’ve been able to supply to the market as usual,” says Hydroflow. “It’s a bonus to be able to say that in the trying times we’ve all been facing in the industry.”
The Anka product range is made from glass fibre reinforced nylon, is non-corrodible and approved for use with drinking water. It is also fully recyclable.
Hydroflow’s technical team, territory managers and customer services have been grouped into three regional teams to ensure there is a dedicated local team member with the necessary knowledge and expertise to assist the merchant or customer.
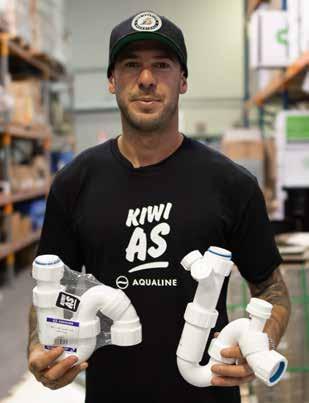
AQUALINE
Aqualine Traps are manufactured in Christchurch, using a combination of local product and popup waste componentry supplied from overseas. Aqualine say they have not experienced any supply restraint issues since 2020.
APD
APD manufactures urban stormwater systems made from recyclable polyethylene for all retention and detention situations. They also produce chemical handling tanks and bunds from recyclable polyethylene—heavily specified in water treatment plants.
Based in Wiri, South Auckland, APD have been providing solutions in plastics for over 35 years. Products are approximately 95% New Zealand made, using APD’s rotomoulding and fabrication expertise to create the range from imported PE resin.
Working closely with their PE resin and sheet suppliers, APD have been able to ensure they always have enough materials to supply customers. They also work very closely with plumbing and drainlaying contractors to meet their needs.
“Customer feedback has been integral in the design features of our recently launched urban stormwater products: StormPit, StormSlim and StormSlab,” says APD. “It was great to be recognised at the New Zealand Plumbing Awards for our contribution to product development in the industry through winning 2022 Product of the Year for our StormSlab tanks.”
APD’s PE waste is sent for recycling and they say they are always looking at ways to reuse the recycled pellets in their products.
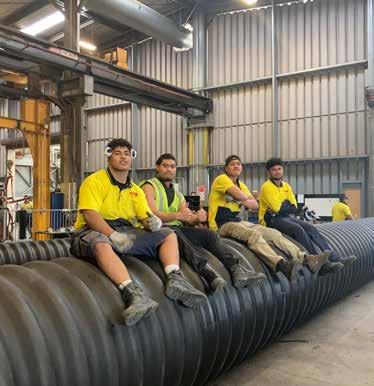
ALLPROOF
From their Auckland facility, Allproof manufactures drainage and passive fire protection products. These include PVC fittings, plastic and stainless-steel floor wastes, stainless steel shower channels, trays and wall niches, recycled polypropylene channel drainage and drainage pits, cast bronze roof drains, downpipes, rainwater heads, scuppers, and intumescent fire collars.
Allproof was established by Ian Jackson in 1987 and production has always been in Auckland as the company has grown, with the current facility at Beach Haven on the North Shore. A large portion of products are fully manufactured in-house in their injection moulding, stainless fabrication and product assembly departments.
Supply chain restraints have made it more challenging and expensive to secure raw materials, largely due to freight reliability and cost increases. This led Allproof to acquire additional warehousing and increase their production and stock volumes.
During this time, they have continued to assist the trade industry with technical support at site visits and at industry events. “Allproof looks to provide any additional support to plumbers as required. This is part of our standard sales operations regardless of any national or global health or economic challenges,” they say.
The company recently finalised the installation of 449 solar panels on the roof of their main facility, providing nearly half of the building’s energy needs and saving 50 tonnes of CO2 from entering the atmosphere every year. “In addition to this, we manufacture our domestic channel, commercial channel, drainage pits, cast-in fire collars and various other componentry from 100% recycled plastic.”
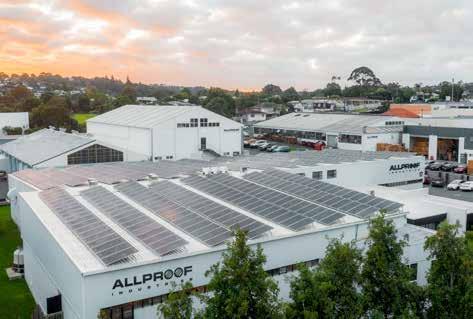
APEX VALVES
Apex Valves manufacture a range of plumbing valves, rural valves for water tanks and troughs, pipe fittings and hose nozzles. Plastic componentry is manufactured on site at their Auckland facility in Rosebank Road, with brass components imported from various overseas locations, and assembly of finished goods completed by their staff at Rosebank Road.
Some of the imported brass componentry comes in fully finished and ready for assembly, while others are machined on site. Other components, such as springs and washers, are sourced from a variety of local and overseas suppliers.
Apex Valves say their supply chain has been affected since early 2020, when the pandemic was starting to take hold. “Raw materials supply and freight delays have meant forecasting and ordering of materials is more critical than ever to ensure Through its product ranges made from 100% recycled plastic, Allproof prevents over 12 tonnes of plastic from going to landfill every month—the equivalent of more than 383,500 takeaway containers.

operations and customer requirements are not impacted,” they say. “As a result, we have increased stock of imported components to insulate ourselves from uncertainty of the current environment.”
With the demand for plumbing services currently exceeding the number of plumbers in New Zealand, Apex Valves released their CP 20 Fast Fit in 2021. The product is designed to increase the speed and efficiency of installation and was developed based on feedback from plumbers. This then led to the development of a new ‘T’ Ball Valve and pre-installing the non-return valve in the cold water expansion valve to create the CP 20FF.
Apex Valves has plans for some new environmentally friendly initiatives, which are under wraps until they launch. They also hope to remove single use plastics from their packaging by the end of 2022.
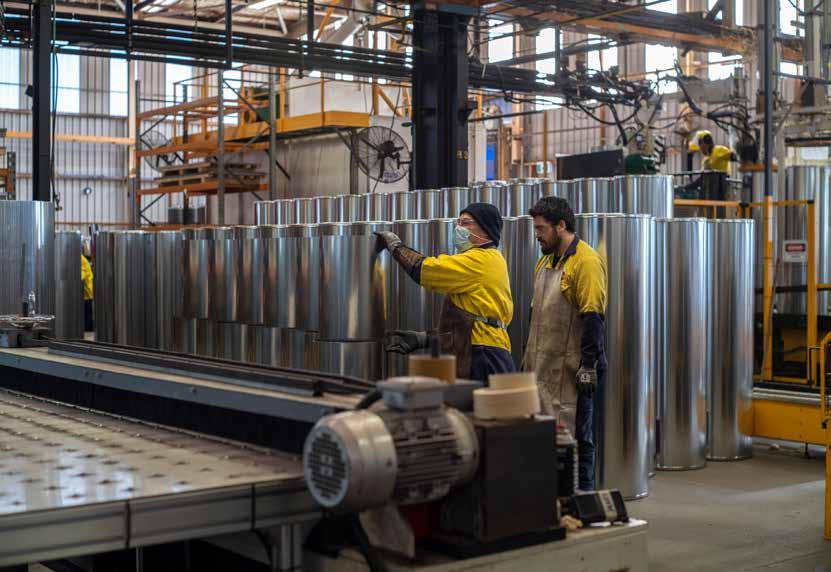
RHEEM NZ
Over 75% of what Rheem sell into the New Zealand market is made at one of their two plants in Auckland and Christchurch. If you include products being assembled in New Zealand, that figure is over 80%. More than 100 staff are employed across both plants.
Most of Rheem’s residential storage water heaters and boiling water appliances are made in New Zealand, with their commercial range coming from their sister company, Rheem Australia. Their gas continuous flow water heaters are manufactured at their parent company, Paloma, in Japan.
“Because we manufacture and operate locally, our products are designed to best suit our market and local conditions,” says the company. “We have our own enamelling plant and furnace (unique in NZ), which enables us to locally manufacture our own vitreous enamel tanks.”
Rheem is a global company, established in 1925. The global team’s support came to the fore during the Covid-related global supply chain crisis, enabling the New Zealand division to lean heavily on global resources to keep them stocked with raw materials, components and the like, so they could maintain their continuity of supply in challenging market conditions.
The operations team kicked into high gear at the first lockdown, and with several new challenges facing them (correct PPE gear, frequent Covid testing, distancing), were still able to produce enough to meet demand. This has been the case for the last few years as they have adjusted to the different lockdown levels.
Rheem is a member of Buy NZ Made and many of their products carry the Buy NZ Made logo. Buy NZ Made has a strict set of criteria, with materials and/or components used in Rheem’s finished product having to be 100% created in NZ from material 100% grown, extracted and produced in New Zealand.
“We do source some components from overseas, but this is usually because we’ve been unable to find a local manufacturer who either makes the component or is unable to meet our exacting quality standards,” they say.
Although Rheem NZ was initially affected by supply restraints as Covid restrictions hit manufacturing sites around the world—with freight suddenly going from a maximum lead time of two months to six—their supply chain team reacted quickly by increasing their inventory holding for raw materials/components and adjusting orders to the longer lead times.
Their biggest challenge, however, is trying to find more staff to adequately plan for and manage the increased industry demand. “Staff shortages are a pain point that many businesses in New Zealand are facing and was a hot topic at the recent NZ Plumbing Conference,” they say.
In 2020, Rheem globally put some hefty sustainability goals in place for all the Rheem teams around the world to achieve by 2025. These are best described in three main areas:
Launching a line of heating, cooling and water heating products with a 50% reduction in greenhouse gas footprint
Reducing greenhouse gas emissions by 50% and achieving zero waste to landfill in
Rheem’s global manufacturing operations
Training plumbers, contractors and key influencers on sustainable products or sustainable installation and recycling best practices.
BUTELINE
NZ owned and operated, Buteline have been manufacturing Buteline polybutene-1 pipe and polymer fittings from their factory in East Tamaki, Auckland, since 1980— adding Pexline pipe and fittings to their range in 2019 and Gasline in 2022. Pexline polymer fittings and Gasline pipe end plugs are also manufactured at the Auckland factory, with most of the brass fittings assembled on site.
Managing Director Llewellyn Picton says all products are designed and tested in New Zealand, with raw materials sourced both from New Zealand and overseas. “In the past few years, plumbers have given us lots of ideas for new fittings. We assess the feasibility of the market and the fittings before manufacturing them and bringing them to the market.”
Global supply chain restraints did cause some issues, but Buteline say they never let plumbers feel the heat of it. “We have mitigated these issues by investing in a second manufacturing and stock storage site near the Buteline headquarters and increasing our product and raw material stock levels,” says Llewellyn.
They also kept their factory operational with shift staff to supply the market with product and employed more staff to assist with any restrictions and with their growing product range.
Buteline’s aim is to recycle, re-use and regrind materials used in the production process—and some of their packaging boxes are recyclable. “We aim to make this a high priority as packaging materials evolve with more readily available sustainable options,” says Llewellyn.
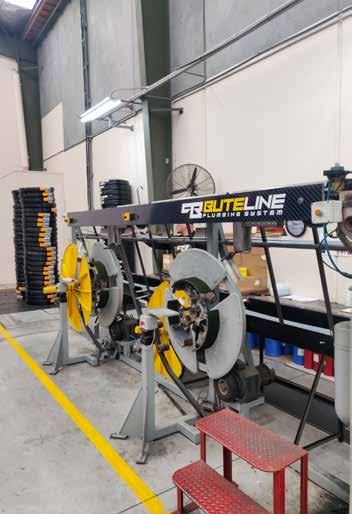
AMBIHEAT ™
HEAT PUMP WATER HEATER
We strive to innovate best-in-class products to lead our industry in environmental improvements
A Greater Degree of Good™ represents our global commitment to sustainability.
COP OF 4.5
Quiet operation (47dB) High Energy Efficiency
Smart LED Controller Display Microchannel Technology