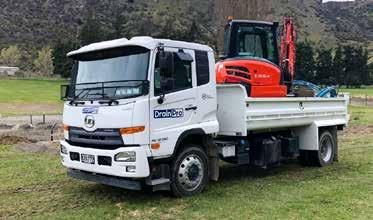
5 minute read
Suppliers, contractors & the 3Cs
SUPPLIERS, CONTRACTORS AND THE 3CS
Consult, cooperate and coordinate—follow these three Cs for effective health and safety management of contractors and suppliers.
They’re contractors—health and safety is their responsibility!!
An all too familiar approach from businesses in years gone by. Now it’s all about sharing the load; you are all playing in the same sandpit.
Overlapping duties was a term introduced into the Health and Safety at Work Act 2015. The question nowadays is, “Who is responsible for health and safety?” The alltoo familiar answer is, “Everyone of course.” But how do we apply that in reality, when dealing with contractors and suppliers?
Businesses must consult, cooperate and coordinate (commonly known as the 3Cs of health and safety) activities with all other businesses they share overlapping duties with. Successful approaches to this occur when PCBUs: plan ahead and think through every stage of a project, considering how the work could affect other businesses and the public make sure risks that need managing have been clearly identified, and consult with other PCBUs working with them to gain agreement on who will manage each risk and how they will do that clearly define roles, responsibilities and actions, and explain these so everyone knows what to expect.
Four-step process to 3Cs
A simple four-step process will help you with the 3Cs of contracting and health and safety. 1. Know your supply chain – While most think of their physical works contractors, AUTHOR: GREG DEARSLY, FIRST 4 SAFETY
there are also the other suppliers you might engage in your business—such as designers, architects, engineers, importers, manufacturers and commissioners. They have health and safety obligations and, as the head contractor, you have a duty to satisfy yourself that all your suppliers have taken account of their responsibilities. 2. Define the type of relationship you have with each one of these suppliers – It could be different for all of them. Consider where the work is done, whose tools, plant, equipment or substances are being used, who is the person in control of the workplace. Consider who has the ability to influence and control operational risks. Is it you as the head contractor or your supplier? 3. Define responsibilities, accountabilities, who you need to consult with and who you need to inform on a RACI matrix –
Identify those important aspects of health and safety and then determine where they fit for each relationship type on the RACI (Responsible, Accountable, Consulted,
Informed) matrix. You might include actions such as the management of incidents, training of workers, provision of advice and PPE issues. 4. Formalise key information in a contract with your suppliers – Keep it simple. Maybe insert new clauses into contracts or legal agreements when it comes time for renewal. Have a separate clause for each relationship type. If you separate how you manage your suppliers, based on their risk profile, that might only mean three extra clauses for high, medium or low risk exposures.
The most important thing to do is to engage directly with your suppliers and explain why you are making these changes. It provides clarity about what you expect and what the contractor or supplier can deliver. Day-to-day management
Of course, there is another layer to this, and that is how you manage contractors and suppliers day to day. Consider the following steps.
Scope the work – Make sure that YOU have a clear understanding of the work you want a contractor or supplier to perform.
Pre-qualify the contractor – Make sure your potential contractors and suppliers have the systems to effectively manage health and safety.
Select contractors and negotiate terms – Provide information to potential contractors on the health and safety matters of the particular contract. This applies in both tendered and nontendered contracts, although they may be delivered in different ways.
Award the contract – For larger projects, develop a job-specific health and safety plan. For smaller jobs, or ongoing work, maintain agreed standards, systems and processes. These can be modified to suit the circumstances of the individual contract.
Monitor the contractor’s performance –
Monitor or check performance throughout the duration of the contract. Respond
to information and keep the contractor informed of the results of monitoring. Are they meeting the agreed standards? Post contract review – Review overall performance to determine the success or otherwise of the contract.
Taking a structured approach to the management of contractors and suppliers means there is clarity about the work to be done, who has responsibility for key tasks associated with health and safety, and performance criteria contractors will be measured against.
Businesses must consult, cooperate and coordinate with all contractors and suppliers who share overlapping duties.
Client
HOW DO I CONNECT THIS TOGETHER?
Create a list or a map of your contractors or suppliers Satisfy yourself that your contractors are committed to consultation, coordination and cooperation on matters of health and safety Understand who has the ability to influence and control operational risks, and define responsibilities and accountabilities Monitor your contractors’ performance—are they working safely, following your rules and their own procedures? Review your contractors’ performance at the end of the project.
Sub-contractor Overlapping duties
Contractor
About the author: Greg Dearsly owns First 4 Safety Ltd, a generalist health and safety consultancy. He has been involved in the provision of occupational safety and health advice and assistance for 20 years. Greg holds a Masters in Advanced Leadership Practices, a Graduate Diploma in Occupational Safety and Health, and the National Certificate in Adult Education. His work has involved supporting industries in their H&S development. He encourages organisations and their senior people to show good H&S leadership, conduct effective risk management and ensure their workforces are able to contribute. Greg is a Professional member of the NZ Institute of Safety Management (NZISM) and was NZISM President from 2016-2020. He represents NZISM as President Elect on the Board of Directors of the International Network of Health and Safety Practitioner Organisations (INSHPO) and will be INSHPO President in 2022.
First 4 Safety offers Master Plumbers members tailored health and safety support and advice at competitive rates. Order through the Master Plumbers member website (Health & Safety).
FRANCHISES AVAILABLE
DrainPro has franchise opportunities available around the country. Whether you are an existing company struggling or a tradesman looking to go out on your own, we have the experience, systems and industry contacts to help you develop a successful business. We are members of the Franchise Association of New Zealand (FANZ), and can give you all the assistance you need in deciding if a franchise is the right thing for you. Contact Nathan to register your interest nathan@drainpro.co.nz