
4 minute read
Have a tools policy?
There’s good reason why businesses should have a tradesperson tools policy, as Sam Tyson explains.
Awhile back, one of our tradespeople came to me saying his power drill had broken and to fix it was going to be $1,000, but to replace it would be $1,400, so I should replace it rather than get it fixed.
I said, “Hang on a minute… Me replace it? It’s your tool; why should I replace it?”
He said, “Because it broke while I was using it on a job, and I won’t be able to work without it.”
At the time, we had no clear tradesperson tools policy and it became a standoff situation. I did not feel I should have to pay when the tradesperson was receiving a tool allowance. He felt, because it broke at work and it had worn out because of all the use it got at work, I was responsible for replacing it or at least getting it fixed.
In our industry it is common practice for tradespeople to provide all or some of their tools of trade. Ideally, these tools should be sufficient to carry out the function of their trade. Good practice would be to have a list in their agreement outlining exactly what tools the employee is required to provide.
If the tradesperson is providing tools, my responsibility as the employer is to pay the tradesperson a tool allowance in return. The amount is negotiated in the employment agreement and is dependent on what level of tools they are providing—all or some.
It is the tradesperson’s responsibility to maintain and keep the tools they provide in a good, safe condition—replacing or fixing unsafe or broken tools as soon as possible. As I found out, it is really important you have the responsibilities of both the employer and the employee outlined in a tradesperson tool policy, so there is no argument.
As an employer, I also need to ensure the tools the tradesperson provides are safe to use and comply with current safety standards. If a safety incident were to occur due to an unsafe tool, as a PCBU (Person Conducting a Business or Undertaking), I would ultimately be responsible, even though the tool was owned by the employee.
We have a guy who comes in every six months to test and tag all company- and employee-owned power tools and equipment, but as a safeguard you also need to be regularly inspecting the other tools and equipment employees provide, and making
sure the employee is trained in the correct use and the right tool for the job as well.
If a tool does need replacing or upgrading, you could offer your tradesperson a tool account, where they can purchase a tool through one of your suppliers or trade merchants. You pay the supplier, and then bill your employee passing on the cost, giving them the option of paying it off in weekly instalments.
Your tools policy needs to outline at what point they need to seek approval to purchase. Ours is set at $200 and considers what unpaid tool account invoices they have outstanding at the time. Then there is the total amount you are prepared to go to and how much they must pay each week—they need to be able to afford to pay you back in a reasonable timeframe without hardship.
Plus, there is always the risk that if, for whatever reason, they leave, they might not be able to pay you the balance owing on exit.
In your tradesperson tools policy, you should include how you stand on replacing tool consumables. What we have written in ours is, we will replace tool consumables that are used in the course of work, such as drill bits and blades, as long as we consider the level of replacement to be reasonable.
If, in our opinion, the replacement of such tool consumables is or becomes excessive, we will discuss with the tradesperson what is considered reasonable and agree.
You may need to include who pays for insurance. Our insurance covers the tradesperson’s tools located in our company vehicle, should the vehicle or equipment from the vehicle be stolen, or should a vehicle accident occur and the tradesperson’s tools are damaged. It depends on the value of the tool, but what if their power drill was accidentally damaged on a work site, or at home on the weekend? Whose insurance kicks in: their personal insurance or yours?
The great thing about policies is everyone knows where they stand should a situation arise. In my situation, if I had had a tool policy in place, it would have avoided feelings of inequity creeping in. Policies make it fair and ensure every employee is treated the same.
Sam Tyson is working with Master Plumbers HR Manager Lisa Duston to develop a generic Tradesperson Tools Policy, exclusive for members of Master Plumbers. Members will be advised when this is available for use.
About the author: Sam Tyson has been Managing Director of Climate & Plumbing since 2010. She is an active member in the industry and, with a background in strategic business development, shares the knowledge and experience gained from her award-winning business to help others obtain better results in their businesses. Sam is a Director on the national Master Plumbers Board.
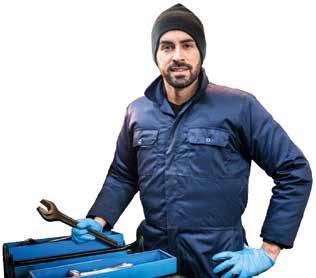