
10 minute read
NZ Plumber December 2023-January 2024
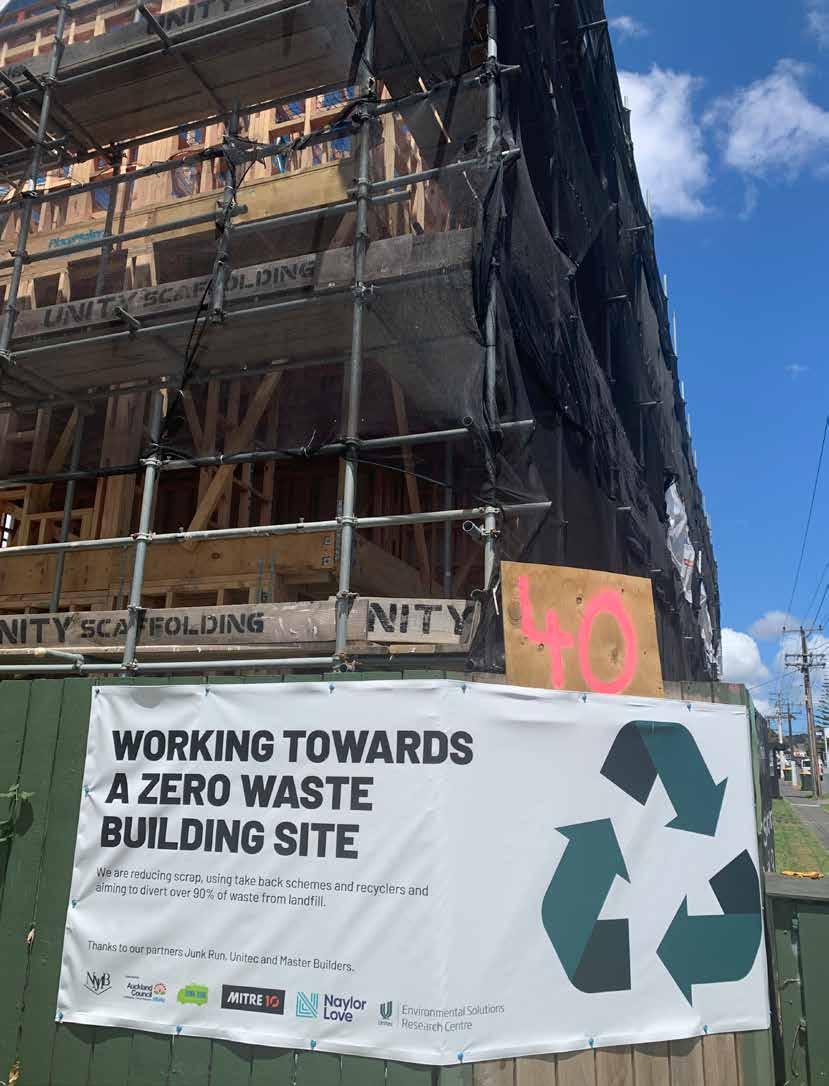
WAGING WAR ON PLASTIC WASTE
AUTHOR: MATTHEW LOWE PHOTOGRAPHS: ENVIRONMENTAL SOLUTIONS RESEARCH CENTRE
A drive to identify alternative options for plastic use in the building industry and to divert plastic waste from landfill is being spearheaded by Environmental Solutions Research Centre (ESRC), based at Unitec in Auckland.
Co-founded by Professor Dr Terri-Ann Berry in 2019, the centre has audited a number of new-build construction sites to help inform the development of practical solutions to reduce plastic use and encourage reuse or recycling.
She suggests if 230,000 new homes were built in Auckland, it would currently generate enough plastic waste to fill 16 Olympic-size swimming pools.
“We have been working with six different contractors in the Auckland region and put in waste separation stations to collect every item of plastic,” explains Terri-Ann. “We look at all waste products, but plastic has been the main focus when it comes to looking for replacements where it’s viable and sensible.
“Sometimes the plastics used are unnecessary and, where it’s plastic that isn’t suitable for reuse or recycling, we have suggested replacing it with a different type.
“Transportation is still the biggest pain for removing plastic waste, but we hope that
by getting more people on board and better attitudes on construction sites there will be the volume to combine transport logistics.”
She notes that generally pipe offcuts and packaging create the most plastic waste from residential and commercial sites.
The amount of leftover plumbing packaging at the end of the project was substantial, with the 14 showers across the eight homes generating 42 leftover boxes, 42 plastic bags and 168 pieces of polystyrene.
The toilets came packed in a further 42 boxes, 56 pieces of polystyrene and 28 plastic bags, while mirror cabinets, vanities, kitchen taps, heated towel rails, hot water cylinders and super tub boxes added to the pile of rubbish.
In terms of overall waste, 22.4 tonnes of material was collected and audited from the project, of which 18.4 tonnes was recycled or repurposed.
Changing mindsets
Project site audit
Nigel Benton, a property developer and vice-president of Auckland Master Builders, recently completed a build of eight terraced townhouses in New Lynn, Auckland, and worked with ESRC to recycle 70 per cent of the project’s plastic waste.
An audit of the site revealed it generated 270kg of soft plastic waste, 201kg of polystyrene and 156kg of pipe. Of those totals, 214.5kg of the soft plastic and all of the polystyrene and pipe was recycled.
Nigel says he has been in the building trade for 44 years and could see the large volumes of rubbish going to landfill, with packaging and plumbing offcuts at the fitout stage among the main sources of waste.
“We need to change people’s mindset and get out of that bin culture, which in the past we’ve been so used to without a thought of where the waste ends up,” he adds.
“As a group, we’re here to help builders, manufacturers and other people who want to get into this to come up with solutions. Companies that start early with this type of recycling and waste management work will be the leaders as we go forward.”
He encourages plumbers and drainlayers, along with other tradespeople, not to dump waste into builders’ bins but to return it to their merchants and ensure it gets reused or recycled from there.
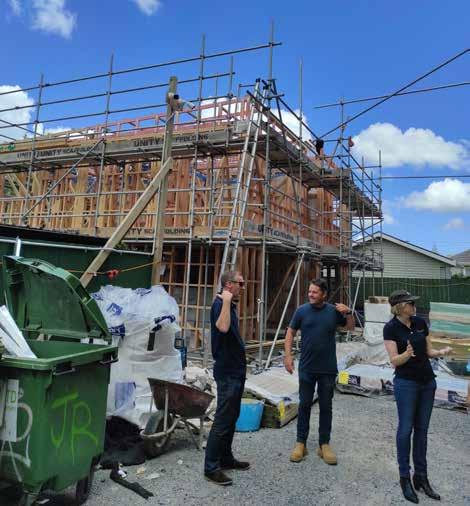
Terri-Ann adds: “My message to plumbers would be to go back to your supplier and see if it can remove some of the packaging if you don’t need it, and when you do come onsite take your waste back with you and ask the supplier what they do with it.
“Alternatively, if there’s active waste separation on-site then learn to use it because it makes so much difference.”
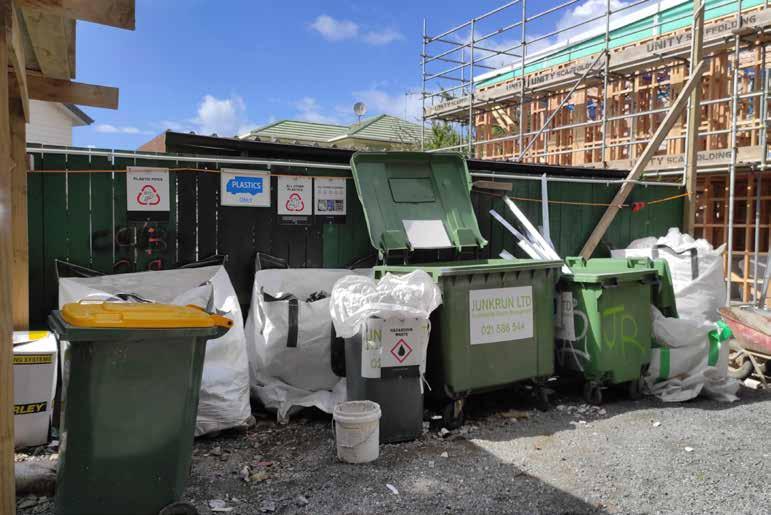
Have a waste champion
ESRC is trying to change the ‘skip mentality’ and make that shift as easy as possible through signage, education and encouraging businesses to appoint waste champions.
MARLEY MAKING A DIFFERENCE
Marley NZ recycled 625,000kg of plastic construction waste last year, with much of it going back into the manufacturing of new products. This year, it has set a goal of lifting that figure to 1,300,000kg.
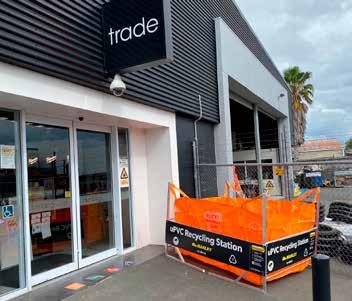
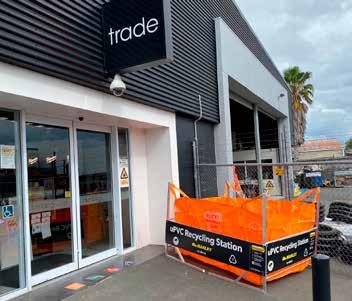
The company, which is part of the Aliaxis group, accepts returns of used waste pipes, spouting, ducting and other plastic construction waste and offcuts, including PVC fencing offcuts.
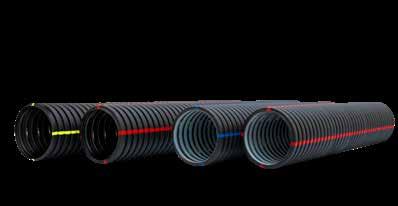
A key to the success of its project to reduce PVC and HDPE plastic waste is its partnership with Waste Management New Zealand, which collects, sorts and collates the product before sending it to Marley.
The first waste drop-off points were in Auckland before the scheme expanded into Christchurch and Wellington through direct merchants. There are now more than 25 PE and PVC recycling drop-off locations across the country.
Dwayne Carroll, Marley’s recycling project lead, says the amount of waste it reuses has significantly cut how much goes to landfill, as well as the amount of plastic resin that needs to be imported to make products.
“The collected plastic will be used at Aliaxis New Zealand’s sites to manufacture our next generation of PVC and HDPE piping systems used in building, infrastructure and agriculture projects across New Zealand, closing the loop and reducing our overall plastic resin importation,” he explains. “We are proud to be at the forefront of the drive to recycle
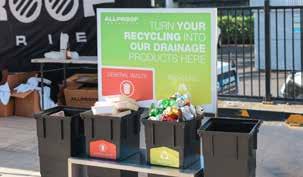
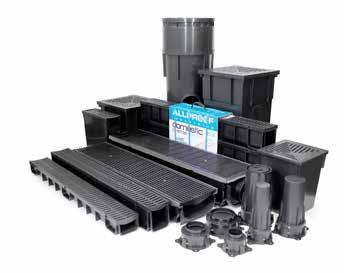
ALLPROOF CUTTING CARBON
Allproof Industries has set a goal of cutting its carbon footprint by embracing solar power, reducing emissions from its vehicle fleet and recycling more of the waste from its manufacturing plant.
Adam Jackson, General Manager, adds that the company also uses locally sourced recycled plastics, where appropriate, for a number of its products.
“These are sourced from post-consumer and postindustrial feed sources and extend the lifecycle of these plastics and provide a viable alternative to virgin materials for certain product categories,” he says.
Solar panels have been installed at its manufacturing site in Auckland with the up to 1,200kWh of energy generated per day put back into powering the plant.
Other green measures include collecting and storing rainwater, and generating nitrogen gas at the plant for manufacturing, with the latter eliminating the need for gas bottles to be transported to and from the premises.
“We also seek to reduce onsite waste at our manufacturing facility through the recycling of soft plastics, consumer packaging, timber and metal,” he says.
“We consider product packaging and waste when designing new products and seek to use products that can be recycled or have less environmental impact. We utilise biodegradable pallet wrap and packaging tape as part of this effort.”
Allproof’s vehicle fleet has also switched to a mix of electric vehicles and hybrid models to further reduce its emissions.
WATER KEY TO RECYCLING
The director of Baxter and Neilson Plumbers in Invercargill has been working with the charity Recycle South since April 2022 to transform an old freezing works in nearby Makarewa into a hive of recycling activity.
Bale wrap and silage covers are among the main plastics accepted by the facility, and they go through water blasting, heat treatment and wash cycles.
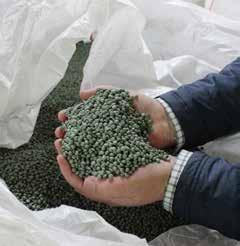
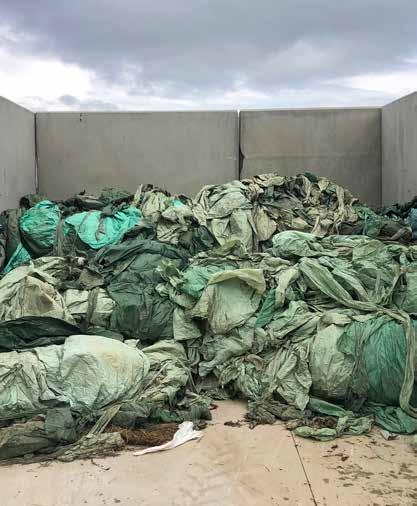
While Nathan has done the lion’s share of the plumbing work, he has had up to three of his colleagues on-site with him at certain times.
“One of the biggest obstacles for us was storage of wastewater, and the filter system needed to remove bits of plastic so the water could be recycled back into the system,” he explains. “We had to work out what to do to capture all the waste plastic by filtering the water, and then pumping that water back so it can be reused.
“It’s been a rewarding project and definitely been a learning curve for getting your head around operating numerous pumps at a big commercial site.”
Besides working on the two recycling lines at the plant, with plans to double it to
four, Nathan also installed toilets, drains and connected potable water supplies at the site.
Hamish McMurdo, general manager of Recycle South, says he visited 17 different factories overseas to find the right technology to bring to New Zealand and admits the most complicated part has been the plumbing.

“It turns out this process uses a significant amount of water and we needed to find a way we could recycle the water because that’s the sensible thing to do,” he says.
“In association with Nathan and our engineers, we’re building a settling process where we can recirculate the water, it then settles out, gets refiltered and we reuse that water.”
Hamish says the recycling operation means waste traditionally buried or burnt is now turned into plastic resin, which is exported to countries that can make it into bale wrap again. “Initially, I thought the pure resin would be used for drainage pipes but the quality we can produce is good enough it can be put back into wrap, so it’s created a circular economy.”
Among its ideas is the on-site separation of waste products — for example, having different bins for pipes, polystyrene, polypropylene, soft plastics, and all other plastics.
“I would like every single builder out there to have waste separation on site and to maybe start making money out of their waste,” adds Terri-Ann. “That’s bold and it may not occur for the next 10 years, but we want to make it easy and enable everybody to do it, so it becomes part of the culture.”
Nigel notes some plastics can’t be recycled and he is keen to see those designed out of use.
Plastic reduction initiatives
Other initiatives to cut plastic use at construction sites include Mitre 10 no longer automatically providing timber or panels wrapped in plastic. In its first year no wrap was used on 97% of such supplies.
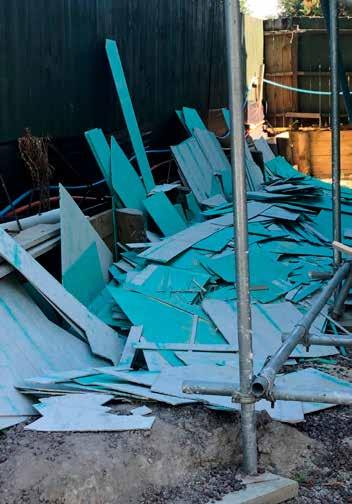
Carters has followed suit with a similar scheme, while Naylor Love has boosted its green credentials by covering its timber packs with reusable tarpaulins instead of plastic.
Meanwhile, the Ministry of Business, Innovation and Employment says the building and construction sector has a key part to play in helping New Zealand meet net zero carbon emissions by 2050.
The sector currently accounts for about 20% of the country’s carbon emissions through the energy and materials used in buildings.
Officials hope over the coming decades the embodied carbon emissions of buildings will significantly reduce through improved designs, being more efficient with construction products and materials, and reducing the carbon associated with those items.