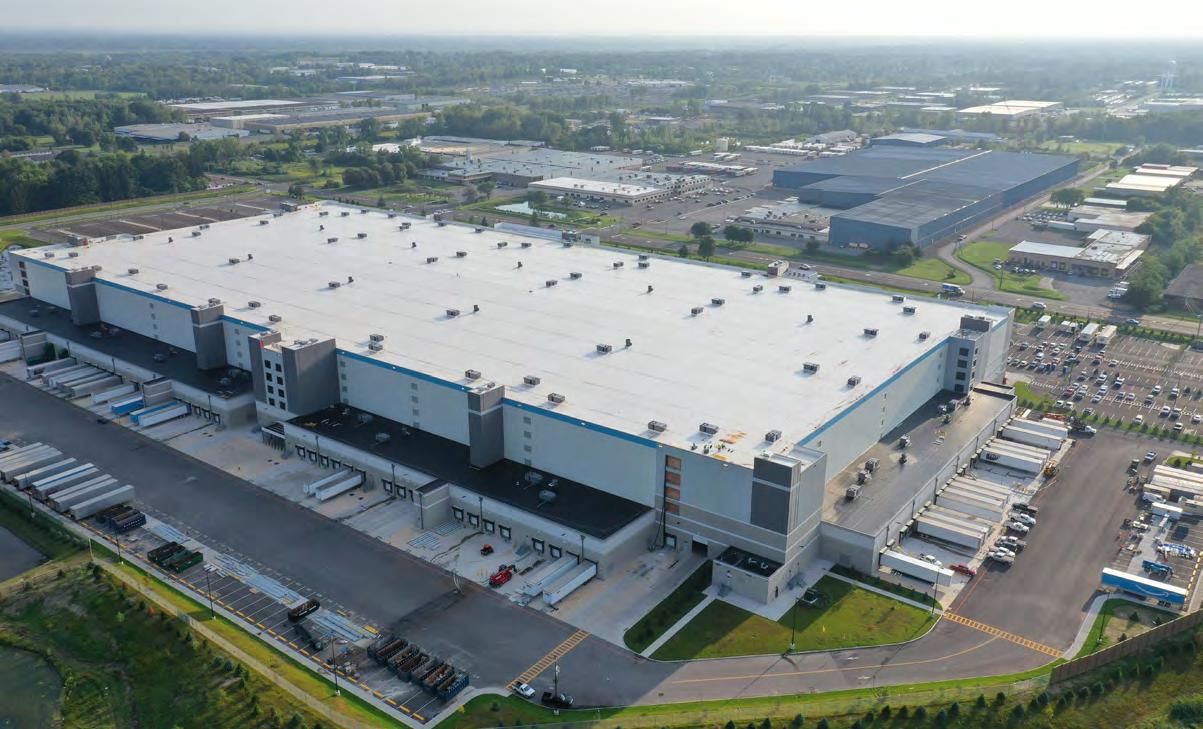
14 minute read
Amazon on a Hiring Binge
Amazon fulfillment center on Morgan Road in Clay. The 3.8-million-squarefoot space facility opened in April. It’s the largest of its type in New York state.
As Amazon Faces Setbacks, Its CNY Fulfillment Center Is Growing
While Amazon has scrapped new warehouses and delayed some projects already under construction, it’s doubling its workforce in Clay to 3,000 workers
By Ken Sturtz
The headlines for the world’s second-largest company have been decidedly negative this year.
Amazon hemorrhaged billions as e-commerce slowed coming out of the pandemic. A nationwide building spree saddled it with more space and workers than it now needs. Further headwinds may be on the way as Congress considers new antitrust legislation aimed at big technology companies like Amazon.
But those problems seem distant at its mammoth warehouse and fulfillment center on Morgan Road in Clay — known in company jargon as SYR1 — where Amazon is actually expanding.
When the 3.8-million-square-foot space opened in April the company said it planned to hire 1,000-1,500 fulltime workers. This summer company officials announced they had reached an initial hiring goal of 1,500 workers and were hiring an additional 200 people a week with the goal of having 3,000 employees when the holiday shopping season begins in October.
The news that Amazon was expanding and hiring even more workers in Central New York was made more surprising by the fact that the company is doing the opposite across its footprint.
In July Amazon reported losing $2.03 billion in the second quarter of 2022, compared to a nearly $8 billion profit last year. It was the second consecutive quarter of losses.
Several factors are at play. The spike in online shopping during the pandemic has ebbed as Americans return to in-person shopping and shift their spending from consumer goods to things they couldn’t do during the height of the pandemic, such as travel or dining out. The highest inflation in 40 years has sent costs rising, causing some to ease away from unnecessary spending.
But it was a strategy Amazon adopted during the pandemic that is causing the largest headaches.
“The big issue is they overbuilt,” said Patrick Penfield, a professor of supply chain practice at Syracuse University. “They went on just a major expansion on all their warehouses.”
Amazon nearly doubled the number of warehouses and data centers it leased and owned between 2019 and 2021.
Penfield said Amazon probably believed consumers who turned to

Marc Wulfraat, president of MWPVL International, a Montreal-based global supply chain and logistics consulting firm.
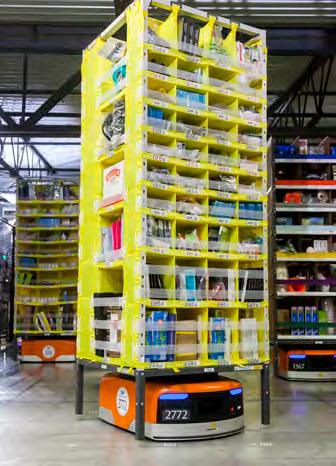
e-commerce during the pandemic would change their habits and continue buying online, and that building more warehouses would put it ahead of the curve. That bet has not paid off, however, as consumers have increasingly returned to shopping in person.
Amazon’s strategy was overly aggressive and led to losses that are unsustainable long-term, Penfield said, resulting in its move to retrench, control costs and optimize its current network.
“I think they’re realizing that they’ve got a pretty big footprint in place right now and they need to reap the rewards of that footprint and start making money off of what they already have built up,” he said.
Amazon has scrapped new warehouses and other facilities that were still in the planning phase and delayed some projects already under construction.
In the U.S. Amazon has purposely delayed opening 18 projects by leaving buildings idle and forgoing hiring employees, said Marc Wulfraat, president of MWPVL International, a Montreal-based global supply chain and logistics consulting firm. That’s the case with a fulfillment center near Rochester that was supposed to open in 2022 and another in the Buffalo market. Delayed facilities are unlikely to be operational until 2023 or 2024.
“They’re trying to reduce their operating expenses in order to be profitable again,” Wulfraat said. “And a key part of that is just a delayed opening at a number of fulfillment centers.”
Amazon is also delaying opening smaller facilities, but its giant fulfillment centers typically cost the most to run. With a thousand or more employees the annual payroll can exceed $40 million. At the end of June Amazon had 1.52 million employees company wide, down 6% from earlier in the year. The staffing reduction was achieved through attrition.
Although Amazon has closed and subleased a handful of its buildings, that’s been the exception rather than the rule.
The growth of staffing and capacity at the Clay warehouse can be explained by the fact that it’s a key piece of Amazon’s network. It is the company’s largest facility in New York state, serving much of Upstate New York and parts of Massachusetts and Connecticut. It’s slated to serve other states in the future.
About 30,000 products a day are shipped from the warehouse. Company officials said that number will grow to 150,000.
The Clay warehouse is currently the closest fulfillment center to Buffalo and Rochester and many of the packages it handles are sent there. The next closest facility to Buffalo, for example, is in Cleveland. The Buffalo, Rochester and Syracuse metro areas total about 2.9 million people in close proximity along the Thruway.
“When you combine those three cities together there’s a lot of people there that need to be served with their Amazon product,” Wulfraat said.
That could change in a couple years. Once fulfillment centers in the Buffalo and Rochester areas become operational the total volume that the Clay warehouse handles could drop off, Wulfraat said. In the long run that could lead Amazon to scale back its Central New York workforce to deal with the changes, likely through attrition.
“They just celebrated their opening
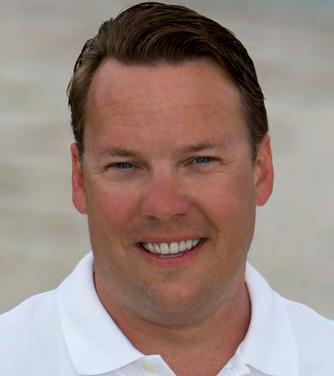
Patrick Penfield, a professor of supply chain practice at Syracuse University. and so no one’s thinking right now about anything like that,” he said. “But eventually what happens is the volume is always going to get pulled from the closest warehouse nearest the customer.”
But Amazon wouldn’t close its Clay warehouse because of the massive financial commitment involved in building the facility, Wulfraat said.
It’s also an important part of Amazon’s long-term goal to offer same-day service to most of the country.
“As soon as you place an order with them they want to be able to fill it that day,” Penfield said. “That warehouse goes a long way in really being able to accommodate that particular strategy.”
It’s easy to overstate Amazon’s recent troubles. Even with its slumping retail business, Amazon’s $121.2 billion in revenue still beat expectations and its advertising and cloud computing divisions continued to do well.
The company is also in a good position to improve its performance heading into the holiday season. Barring major transportation issues, such as with the longshoremen’s union contract negotiations, railroad staffing shortages and tight trucking industry capacity, Amazon has a big opportunity to gain back ground and make money in the second half of the year, Penfield said.
And the company’s efforts to control costs are ultimately short-term measures that haven’t affected its longterm strategy, Wulfraat said.
“They are not slamming on the brakes and going into reverse or anything like that,” he said. “This is a year when all they’re doing is taking their foot off the accelerator pedal.”
Robots moving merchandise at Amazon on Morgan Road, Clay.
Group of workers at Nucor Steel in Auburn. The company, the largest steel producer and recycler in North America, will benefit from Buy American clauses in the Infrastructure Investment and Jobs Act. Photo provided

‘BUY AMERICAN’ SEEN AS A BOON TO LOCAL MANUFACTURERS
By Steve Yablonski
The Biden Administration is working to steel the Buy American Act of 1933.
By law, American-made municipal castings must be used in many federal, state and local-level public works infrastructure projects that are funded or financed with U.S. taxpayer dollars, said Tim McKernan, facility manager at EJ USA in Schroeppel.
The Buy American Act requires the federal government to buy American-made iron, steel and manufactured goods wherever possible.
Products covered by the law include: • Manhole covers • Iron and steel inlet grating • Rings • Iron and aluminum lampposts and lamppost bases • Frames • Various miscellaneous iron products • Catch basin frames and grates
A product is defined as American–made under Buy American if at least 50% of its constituent parts or materials originated in the US.
The Biden Administration wants to increase that threshold to 60% this year, 65% in 2024 and 75% in 2029.
This will reportedly close loopholes in the current regulation while allowing businesses to onshore manufacturing and adjust their supply chains to increase the use of American-made components.
This change will create more opportunities for small- and medium-sized manufacturers and their employees, including small and disadvantaged enterprises, from all parts of the country, McKernan said.
The impact on companies like EJ and Nucor Steel of Auburn are huge.
“The Buy American clauses have revived industries that had all gone overseas to places like China and India. Not long ago, you could not find a made- in-USA bolt,” said McKernan. “The federal Buy America requirements bought this work and many other industries back to the USA.”
It started out with clauses added to Federal Highway spending. AIS was a term used that required American Iron and Steel to be incorporated in highway and bridge project. This expanded to other federal spending through recent legislation called BABA “Build America Buy America.”
One example is with EPA spending. Things like fire hydrants, valves and pipes must be made in America, McKernan said.
BABA is now tied to most if not all federal spending.
It has assured that key U.S. industries like foundries and steel mills will remain in the country.
According to the Municipal Castings Association, the federal Buy American Act and other “Buy America” laws attached to federal-aid programs provide preferences for the use of U.S.mined or domestic end products used in the United States in government procurement. Some, like the preference applied to Federal Highway Administration aid, apply to specific materials (e.g., iron and steel). Many states also have Buy America-type policies. For instance, the Pennsylvania Steel Procurement Act requires that each state contract for the construction or alteration of a public work require the use of steel products produced in the United States.
Common sense idea
Applying a domestic content requirement does much to maintain and expand manufacturing jobs in the United States. Simply giving domestic firms a preference in government contracting creates jobs. Domestic content requirements maximize the economic stimulus effects of government spending and work to create jobs here at home rather than abroad.
“Nucor has long been an advocate of the common sense idea that projects built with American tax dollars should support American jobs — and having strong Buy America laws ensure just that, “said Jason Curtis, general manager, Nucor Steel Auburn.
During the pandemic, the national security risks of over-reliance on foreign supply chains for critical materials became clear, he said.

Products for infrastructure projects made by EJ USA in Schroeppel. By law, American-made municipal castings must be used in many federal, state and local-level public works infrastructure projects that are funded or financed with U.S. taxpayer dollars.

“Sourcing materials from countries that have substandard environmental protections creates additional risks,” Curtis said. “Buy American provisions strengthen our domestic supply chain, lower costs for state and local governments through locally-sourced manufacturing, protect the environment and create strong, high-paying jobs across Central and Upstate New York.”
Nucor Corporation is the largest steel producer and recycler in North America, employing more than 31,000 workers throughout the United States and North America at its 25 steel mills and more than 300 locations.
“We make our steel by recycling scrap metal into new steel products, which makes our Nucor mills among the cleanest in the world,” according to Curtis.
In New York state, approximately 600 Nucor people work at the company’s bar steel mill in Auburn and its steel joist and deck manufacturing facility in Chemung.
However, some say there are economic risks to the buy-American mandate.
By restricting government contracts to U.S.-manufactured parts and labor, the price tag could likely climb higher — and be paid for with American tax dollars, opponents fear. The practice also may motivate other countries to retaliate.
American-made construction materials are produced in facilities with the best environmental controls available in the world — by US taxpayers paid a living wage, while working in safe conditions, according to McKernan.
“U.S. materials are certified to comply with all quality, performance and safety standards. Our infrastructure is assured of getting the highest quality products in the world, from responsible sources who support human rights and environmental sustainability,” he said. “Absent these laws, access to U.S. taxpayer-financed government spending on public works is unfettered and foreign producers, including those owned and subsidized by geopolitical adversaries such as China and Russia, reap the benefit of U.S. tax dollars and the investments in U.S. public works infrastructure.”
Domestic products are required to serve the public interest and American manufacturers are held to high standards under the program.
A federal “Made in America Office” monitors the procurement of materials (www.madeinamerica.gov).
U.S. taxpayers fund government contracts.
“Buy America laws impose preferences for domestically produced products that are permanently incorporated into taxpayer-financed public works projects. They don’t apply to contractor profit, equipment, temporary structures, overhead or labor, which account for the vast majority of costs of a public works infrastructure project,” McKernan explained.
“U.S. industrial capacities are key to our economic and national security. Every dollar spent on American-made materials supports the U.S. economy at multiple levels,” McKernan added. “Buy America laws stimulate capital investments for new manufacturing capabilities and capacity in the United States. As a result of these programs, significant reshoring of manufacturing capacity is taking place. Capital investments in new facilities and good paying manufacturing jobs are returning to the US. EJ is proud to have made significant investments in Upstate New York and throughout the United States.”
Family affair: Leading Lindsey Aggregates in Oswego are Warren Vandish and his wife, Virginia, and daughter Lindsey, for whom the company was named.
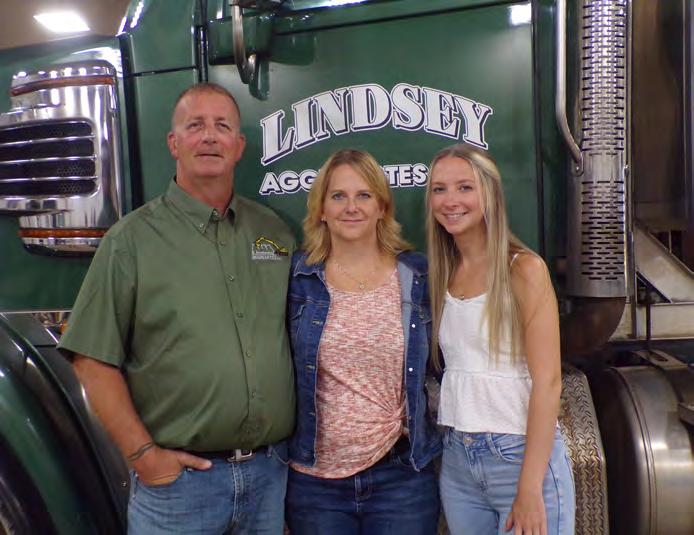
Lindsey Aggregates Poised to Grow
Thanks in part to Infrastructure Bill, company expects substantial growth
By Steve Yablonski


Lindsey Aggregates of Oswego is poised for substantial growth, thanks in part to the recently approved Infrastructure Bill.
The company, located at 5646 state Route 104, in is a major manufacturer of sand and gravel products.
Lindsey Aggregates was formed in 1999 by Warren Vandish and his wife, Virginia. She is the company president; he is the vice president.
It began as a small aggregate company which was primarily staffed by Vandish and his family.
Today, Lindsey Aggregates, Inc. has grown into a multi-faceted corporation that not only produces the aggregates in the area but also provides trucking services, both commercial and residential, according to its website.
“Even though the act has passed, we haven’t seen any direct effect yet,” said Alan Levine, the company’s CEO. “The 81 repaving project will be the first major piece. We are starting to see some activity for that future work.”
Currently, Lindsey is supplying crushed stone and sand products to a variety of projects — solar farms, water line project, gas line project and builders of homes and commercial sites, he said.
From humble beginnings, with a small investment and a dream, Warren and Virginia Vandish built a multi-million dollar company and a major supplier of sand and gravel in Central New York.
“Certainly there is a lot more work out there compared to 2020 and 2021,” Levine said. “Whether the Infrastructure Bill has had any impact I’m not sure.”
Their core customers, he added, are the concrete suppliers and the paving contractors.
“We supply them as a manufacturer and also truck the material, he said.
Lindsey’s plant produces two sands and five stone aggregate products simultaneously — open graded product (clean) as well as dense graded product (run a crush).
“Our stone and sand products are produced in Palermo, at our quarry at 1219 Red Schoolhouse Road,” Levine said. “Almost all of our raw material comes from DEC-permitted pits within a five-mile radius of our quarry.”
Their investment in state-of-the-art equipment, such as its crushing and washing equipment, enables Lindsey to “provide its customers with high quality products, consistently.”
“We currently have 25 employees and a gross between $5 million and $6 million a year,” Levine said.
Its aggregates have been supplied to virtually every market place including heavy highway, municipalities, airfields, industrial facilities as well as many residential applications.