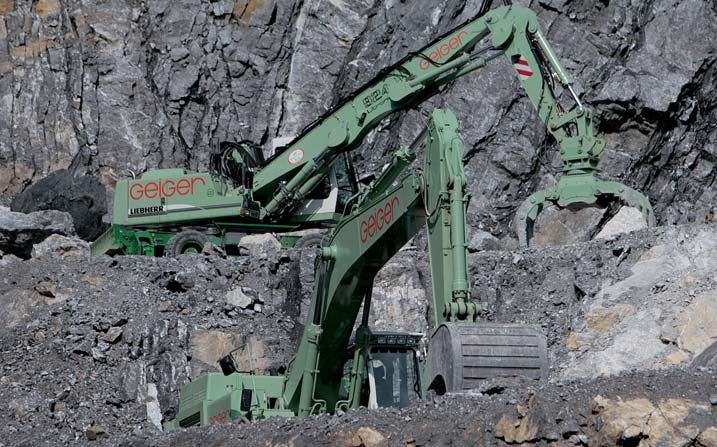
5 minute read
Geiger baut mit Erde, Steinen, Kies und bewegt Liebherr Baumaschinen mit Syntheseölen
Bregenz anfällt. Innerhalb von zwölf Monaten sind hier für den 6,7 Kilometer langen Tunnel alleine 1,8 Millionen Tonnen Material abzufahren und zu verwerten.
Um alle Herausforderungen zu meistern, setzt das Unternehmen einen entsprechenden Maschinenpark ein. Großgeräte, wie Raupenbagger und Radlader, stammen überwiegend aus dem Hause Liebherr und sind den hohen Anforderungen bei der Kiesgewinnung und in Steinbrüchen entsprechend ausgelegt. Die etwa 50 Tonnen schweren Liebherr Raupenbagger R 954 C zum Beispiel verfügen über höchste Traglastwerte und maximale Grabkräfte. Ein 6-Zylinder-Reihenmotor verleiht einem solchen Bagger das notwendige Leistungsvermögen.
Bereits 1923 in Oberstdorf gegründet, hat sich die Wilhelm Geiger GmbH & Co. KG heute zu einer mittelständischen Unternehmensgruppe mit 1.800 Mitarbeitern entwickelt. Mit Niederlassungen in Bayern, Baden-Württemberg, im Saarland, Sachsen, Österreich und Rumänien wickelt das Unternehmen Kundenaufträge aus den Geschäftsbereichen SteineErden, Bau und Umwelttechnik ab. Angefangen bei der Rohstoffgewinnung in eigenen Steinbrüchen und Kiesgruben über die Betonproduktion hin zu

Hoch,- Tief-, Straßen- und Schlüsselfertigbau bis zur umfassenden Dienstleistung im Bereich der Umwelttechnik deckt Geiger viele Facetten ab. Dazu gehören auch Großprojekte, wie beispielsweise die Belieferung der Hochwasserschutzmaßnahme am Lech bei Füssen, bei der 17.600 Tonnen Wasserbausteine mit bis zu 2.500 mm Kantenlänge verbaut wurden. Oder die Entsorgung und Verwertung des Ausbruchmaterials, das beim Bau der zweiten Röhre des Pfändertunnels bei
Motoren mit 272 PS treiben die Liebherr L 580 2plus2 Radlader an, die vor allem in der Rückverladung ihren Dienst verrichten. Mit einer Kipplast von 18.000 kg und einem Schaufelinhalt von etwa 5,5 m³ sind sie das genau passende Gerät.
Die mehr als 200 Bagger, Radlader und Raupen wartet Geiger in eigener Regie. Alleine in der Zentralwerkstatt in Sonthofen sind etwa 45 Mitarbeiter aktiv. Hinzu kommen weitere Werkstätten in Kempten und bei den Tochterunternehmen. Einmal jährlich, mindestens aber alle 1.000 bzw. 1.500 Betriebsstunden, werden die Baumaschinen einer gründlichen Inspektion unterzogen. Nach Möglichkeit erfolgen die Wartungsarbeiten in der Zentral-
Bereits seit 1995 ist OELCHECK nach DIN EN ISO 9001 und seit 2001 nach DIN EN ISO 14001 zerti fi ziert. Sämtliche Abläufe im OELCHECK Labor sind genau dokumentiert und nachverfolgbar. Immer wieder fragten allerdings einige Kunden „Ist das OELCHECK Labor auch akkreditiert?“ werkstatt in Sonthofen. Nur wenn eine Maschine ausnahmsweise nicht umgesetzt oder transportiert werden kann, sind die Experten vor Ort im Einsatz. Werden keine Unregelmäßigkeiten entdeckt, dauert so eine Inspektion zwei oder drei Tage. Eine umfangreiche Generalüberholung der Baumaschinen kann bis zur Fertigstellung aber auch bis zu zwei Wochen in Anspruch nehmen.
Im Gegensatz zur Zerti fizierung nach ISO 9001, die sich im Wesentlichen auf die Überprüfung der Prozesse bezieht, zeigt die Akkreditierung dass die jeweiligen Prüfverfahren entsprechend der gültigen Norm ausgeführt werden, dass das Managementsystem die Anforderungen der DIN EN ISO/IEC 17025 berücksichtigt und die entsprechende technische Kompetenz vorhanden ist.
Wir haben den Antrag auf Erstakkreditierung bei der DACH, der Deutschen Akkreditierungsstelle Chemie in Frankfurt, gestellt und umfangreiche Vorbereitungsarbeiten durchgeführt. In der Woche vor Ostern erfolgte die Begutachtung durch zwei Auditoren der DACH. Die Auditoren stellten keine gravierenden Mängel fest. Ein Ausstellen der Urkunde durch den Akkreditierungsrat wurde durch die Auditoren befürwortet. Spätestens im Juni dieses Jahres kann uns voraussichtlich das of fi zielle Dokument übergeben werden. Mit der Bescheinigung durch die DACH ist das OELCHECK Labor nicht nur national, sondern auch international akkreditiert.
Schmierstoffanalysen sind fest in das Überwachungsprogramm der Baumaschinen integriert. Je nach Gerät und Einsatz entnehmen die Instandhaltungs-Mitarbeiter alle 250 bis 500 Betriebsstunden, spätestens aber bei der großen Jahresinspektion Ölproben. Untersucht werden im Zusammenhang mit längerer Öleinsatzzeit vor allem die Hydrauliköle und bezüglich Verunreinigungen und Verschleiß die Öle aus den Achsgetrieben z.B. der Planierraupen. Besonders beim Einsatz der Maschinen in sensiblen Bereichen, wie der Umwelttechnik und der Flussverbauung, verwendet Geiger biologisch schneller abbaubare Hydraulik flüssigkeiten. Diese Hydrauliköle erfüllen sowohl die Anforderungen für HVLPD 46 – Mehrbereichs-Hydrauliköle nach DIN 51524 T-3, die u.a. für mineralölbasische Hydrauliköle gelten. Da sie als HEPR-Öle gemäß ISO 6743 T4 mit aschefreien Additiven formuliert sind, die als Grundöle synthetische Kohlenwasserstoffe auf der Basis von Polyalphaole finen verwenden, erfüllen sie auch einige Richtlinien wie z.B. die CEC-L-33-A-93, die für biologisch schneller abbaubare Hydraulik flüssigkeiten Gültigkeit haben. So stellen diese modernen Öle echte Alternativen zu Hydraulikmedien auf Basis von Mineralöl oder synthetischen Estern dar.
Und sie verfügen über eine ganze Reihe von Vorteilen:
Aufgrund des leichten Tieftemperatur-Fließens lassen sich die Maschinen auch im Winter noch zuverlässig bedienen und punktgenau steuern.
Bei sommerlichen Temperaturen bietet es immer noch genügend Viskositätsreserven, um interne Leckageverluste zu verhindern. So wird auch der Wirkungsgrad verbessert.
Verglichen mit konventionellen Mehrbereichs-Hydraulikölen, die ähnliche Tief- und Hochtemperatureigenschaften zeigen, lassen sich die Syntheseöle wesentlich besser filtern. Reine Öle leben länger!
Das Öl ist weniger kompressibel, weil weniger Luft im Öl gehalten wird. Deshalb ist die Kraftübertragung deutlich präziser als bei anderen Fluids.
Die Bildung von Leckagen wegen Ober flächenschaum ist bei unvermischtem Öl extrem gering.
Die Verträglichkeit in Bezug auf Schläuche, Dichtungen, Anstriche, Lacke und Elastomere ist bei PAO-Ölen besser als bei Esterölen.
Das Verhalten gegenüber Wasser und Luftfeuchtigkeit ist günstiger als bei Syntheseölen auf der Basis von ungesättigten Estern.
Die Praxis hat gezeigt, dass das Syntheseöl auch als Langzeit-Hydraulik flüssigkeit für verlängerte Ölwechselintervalle von deutlich über 5.000 Stunden Betriebszeit bestens geeignet ist.
Das Hydrauliköl der Bagger und Radlader wird bei Geiger „zustandsabhängig“ gewechselt. Die Ergebnisse der Schmierstoffanalysen übernehmen dabei die Steuerung nicht nur der notwendigen Ölwechsel, sondern liefern auch zusätzliche Hinweise zur Filterung. Je nach Typ und staubintensivem Einsatz erreichen die Hydrauliköle Standzeiten von mehreren Jahren bzw. 4.000 Stunden oder im Einzelfall auch schon von 6.000 Betriebsstunden. Bei Ölfüllmengen von bis zu 620 Liter Hydrauliköl pro Maschine stellen die Ölwechsel, besonders bei den relativ teuren Hydraulikölen, einen nicht zu unterschätzenden Kostenfaktor dar. Mit langen Ölstandzeiten sinkt der Aufwand für Schmierstoffe und Montagestunden daher ganz erheblich. Bei der Hydraulikölanalyse werden vor allem untersucht:
Verschleißmetalle: Eisen, Chrom, Zinn, Aluminium, Nickel, Kupfer, Blei, PQ-Index
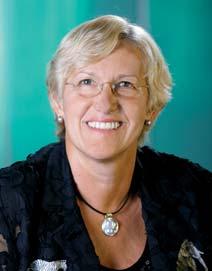
Alterungszustand des Grundöles
Abbau der Additive
Verunreinigungen, wie Staub (Silizium) oder Wasser
Ölviskosität bei 40 und 100°C und Viskositätsindex
Ölreinheit mit Reinheitsklasse nach ISO 4406, SAE 4059.
Trotz hochwertigster Dichtungen und ausgeklügelter Filtersysteme der Liebherr Baumaschinen können unter extremen Betriebsbedingungen, wie z.B. beim Meißelbetrieb oder bei Wasserverbauungen, immer wieder einmal Staub oder Wasser in das Hydrauliksystem eindringen. Sie setzen dem Öl und damit auch dem ganzen System erheblich zu. Besteht ein Verdacht auf eine solche Verschmutzung oder, z.B. nach starkem Ölverlust aufgrund eines defekten Schlauches, auch auf eine Vermischung von miteinander unverträglichen Hydraulikölen, werden sofort Ölproben außer der Reihe entnommen und untersucht. Schließlich kann eine Verschmutzung oder Vermischung ganz erhebliche Schäden hervorrufen. Wird etwa irrtümlich in eine mit biologisch abbaubarem Hydrauliköl betriebene Maschine mineralölbasisches Öl eingefüllt, kann es dadurch leichter zum Schäumen kommen, oder es bleibt ein zu hoher Anteil von gelöster Luft im Öl. Diese kann wiederum zur Kavitation führen. Bereits ab einem Anteil von mehr als 2% mineralölbasischem Hydraulik fluid besteht Gefahr für das System. Außerdem gilt das Öl nicht mehr als biologisch schneller abbaubar.
Von den OELCHECK-Schmierstoffanalysen haben die Instandhalter von Geiger auch bei der Schadensfrüherkennung bereits mehrfach profi tiert. Bei einem drohenden Pumpenschaden musste zum Beispiel nicht die komplette Pumpe, sondern nur einige Komponenten getauscht werden. Mehrmals konnten bei den eingesetzten Baumaschinen auch größere sich anbahnende Schäden an der Fahrhydraulik rechtzeitig erkannt und so teure Reparaturen bzw. der Austausch von ganzen Hydraulikaggregaten vermieden werden.
Mit Schmierstoffanalysen von OELCHECK bestimmt Geiger die optimal verlängerten Wechselintervalle der neuen vollsynthetischen Hydrauliköle und löst im Bereich der Schadensfrüherkennung die Probleme, bevor sie entstehen. Damit wird die maximale Sicherheit und Verfügbarkeit der Baumaschinen gewährleistet. Schließlich heißt es bei Geiger: „Wir bauen mit Erde, Kies und Steinen, aber nie auf Sand.“