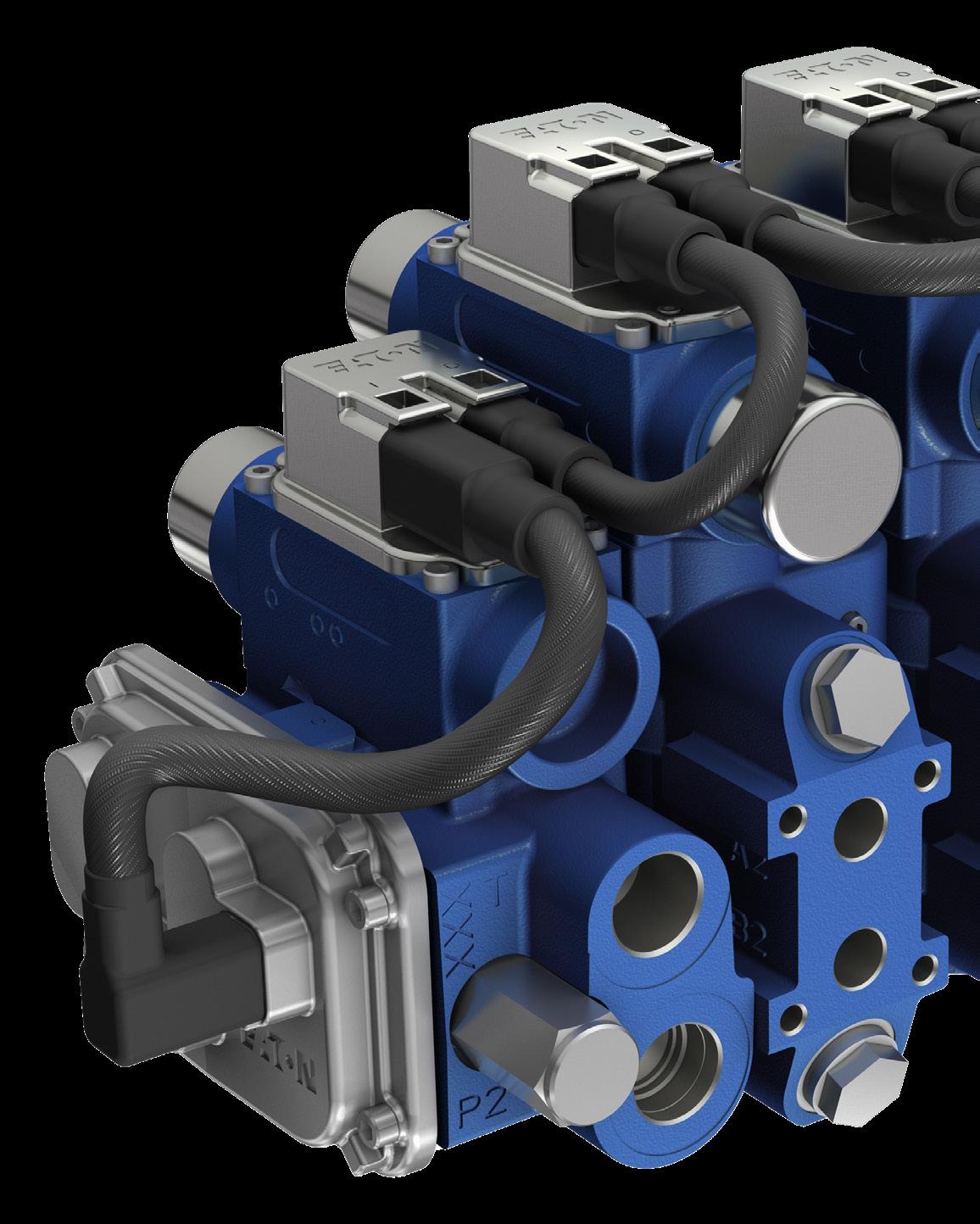
8 minute read
Considerations for Hydraulics in Electric Off-Highway Equipment
Independent metering valves, such as Eaton’s CMA valve shown here, can better control metering losses to reduce hydraulic power consumption.
As emissions standards around the world grow more stringent, non-road mobile machinery (NRMM) manufacturers are leveraging new strategies to create more efficient vehicles. Electrification is one of the most prominent. A variety of electrified machines are being brought to market, helping to dramatically reduce carbon dioxide (CO2) and nitrogen oxide (NOx) emissions compared to traditional, diesel-fueled equipment.
But electrification is a newer trend that comes with certain challenges. Consider that batteries remain expensive—and for end users, the machine’s ability to perform a full day’s work on a single charge is imperative. Original equipment manufacturers (OEMs) must balance battery cost with the power and range requirements of the machine without creating a priceprohibitive product.
Striking this balance can be tricky. Luckily, there are opportunities to achieve power savings, particularly through the deployment of efficient hydraulic components and architectures.
Electrification methodologies
While electrification methods differ, there are commonalities in the types of vehicles being electrified. Power requirements, efficiency, total cost of ownership and noise all affect electrification adoption rates. Smaller machines with less horsepower demand will transition more rapidly. So will vehicles used in low-emissions zones, particularly construction and material handling platforms. Mini excavators are primed for growth, while aerial work platforms are already heavily electrified.
Electrification affects all aspects of a machine’s power architecture, from source to conversion, transmission, consumption and management. In terms of power source, the traditional prime mover of a mobile machine is an internal combustion engine. Technology alternatives range from hybrid electric and plug-in hybrid, which maintain the diesel engine, to tethered electric and battery electric, which remove it.
As for power consumption, there are three good opportunities for electrification: The machine’s propel circuit, rotary work functions and linear work functions. • A machine’s propel circuit is how it moves around, via its wheels or tracks. Fully electric propel systems (either on the axle or wheels) are an alternative to traditional hydraulic or mechanical propel systems.
Advantages of electric propel solutions include minimized energy conversions and reduced hydraulic leaks. However, system costs are considerably higher than hydraulic propel solutions due to higher electric component costs and battery power requirements. They’re also not as rugged as hydraulic systems; which can present challenges in harsh environments. • Rotary work functions, such as
ALL IMAGES COURTESY OF EATON
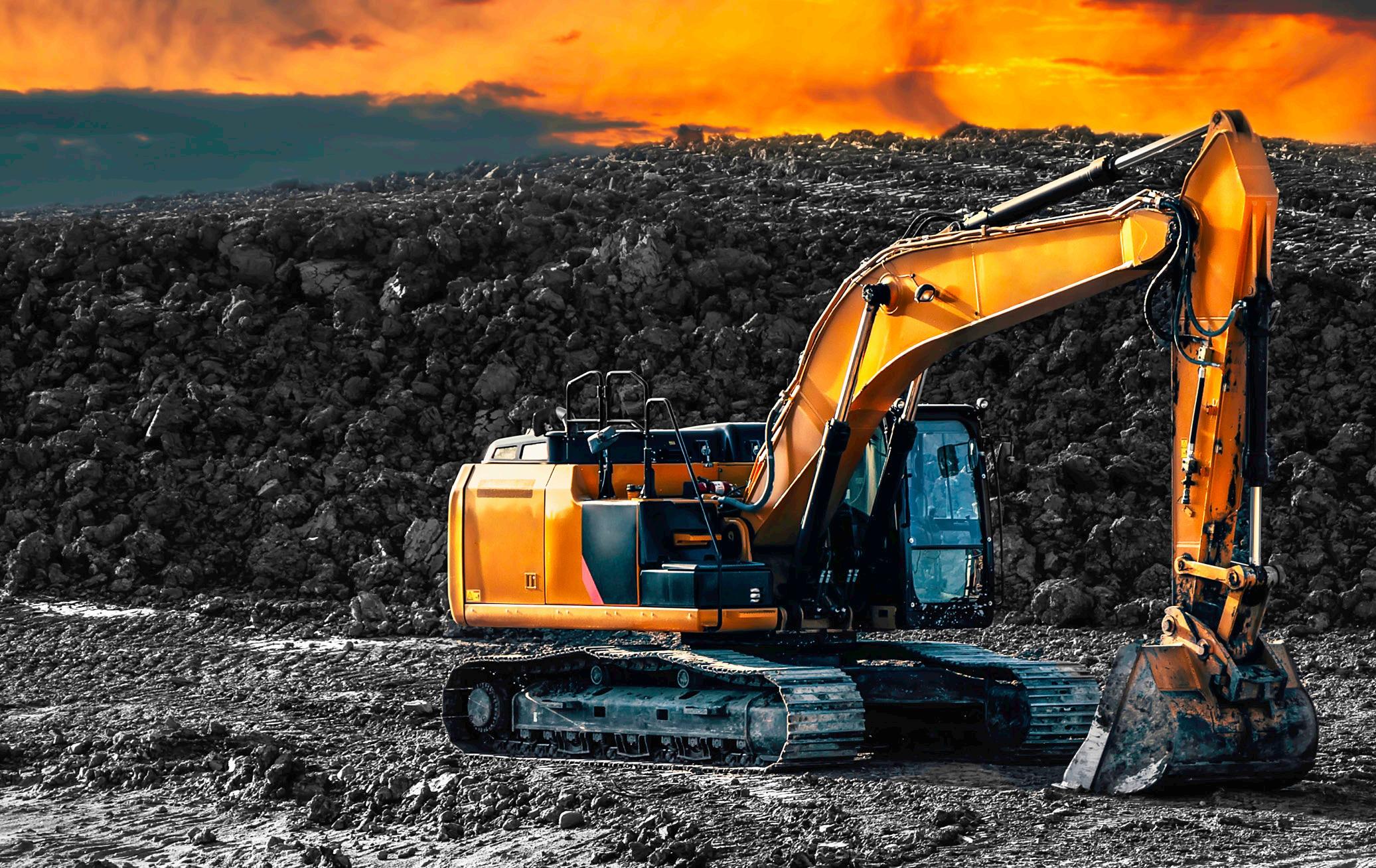
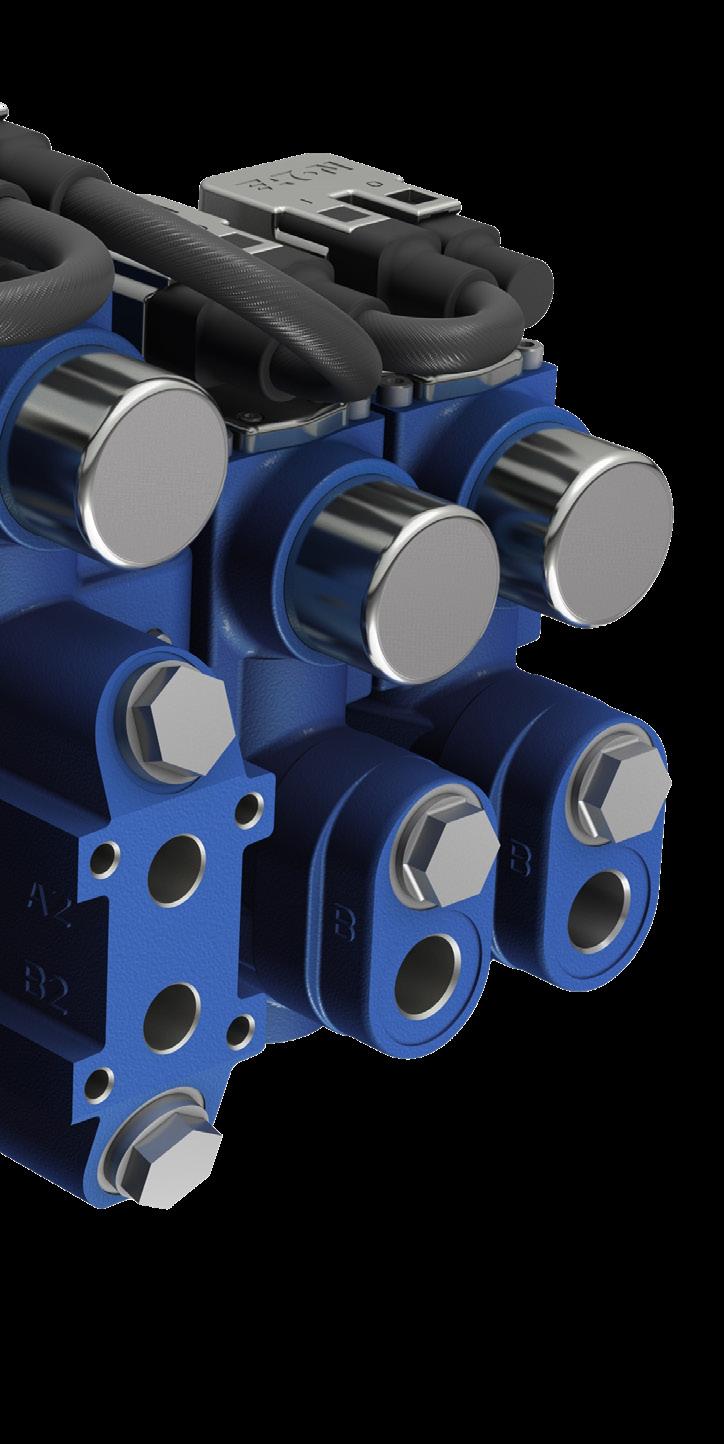
Large excavators are more likely to take a hybrid approach to electrification due to high power demands.
swing drives, fan drives, auger/ cutter services and others, have historically used hydraulic or mechanical power. These functions require precise torque control and high reliability. Electric motors have emerged as a viable alternative for low-power, high-utilization services, given their efficiency and ease of installation and maintenance. But there are limitations.
Low-voltage products have larger package sizes that are not ideal for vehicles with space constraints.
Higher-voltage products drive higher safety requirements. And, like electrified propel systems, reliability is unproven in harsh environments; water ingress and vibration present challenges. • Linear work functions include a variety of high-load services responsible for the powering of booms, lift arms and platforms, buckets and more. Requiring precise force control and high reliability, these services have traditionally been driven by centralized hydraulics.
While electromechanical alternatives are more efficient, easier to install and maintain, and offer better controllability for position and velocity, a significant limitation exists.
Electromechanical alternatives offer poor force control performance and limited force capacity. They’re also less reliable, have a shorter lifetime and more limited regeneration capabilities, and are larger than their hydraulic counterparts.
Given these advantages and disadvantages, OEMs have recognized that one size does not fit all. A different approach is required for different platforms—and even different frame sizes of the same platform.
Aerial work platforms (AWPs) are likely to shift to electric propel systems plus low-cost work circuits with electric fixed-displacement pumps. Key drivers and constraints for the electrification of AWPs include emissions reduction for safe indoor operation while keeping costs in check. AWPs are used heavily in the rental market where buyers are highly price sensitive. Other likely platforms for electrified propel circuits include turf machines, compact wheel loaders, telehandlers and compact tractors.
Mini excavators are more likely to fully electrify, with an electric motor replacing the engine. Like AWPs, electrification of mini excavators is driven by the need for zero emissions indoors. OEMs must consider the machine’s high-power propel circuit and simultaneous use of high-power work services. Precise control for high productivity must also be maintained.
Large excavators (20-ton and up) are challenged by power demands, making full electrification impractical. OEMs are more likely to look at hybrid technologies. A solution could include an electric swing motor in place of hydraulic, reducing metering losses and motor inefficiency, and enabling energy recovery and engine load leveling.
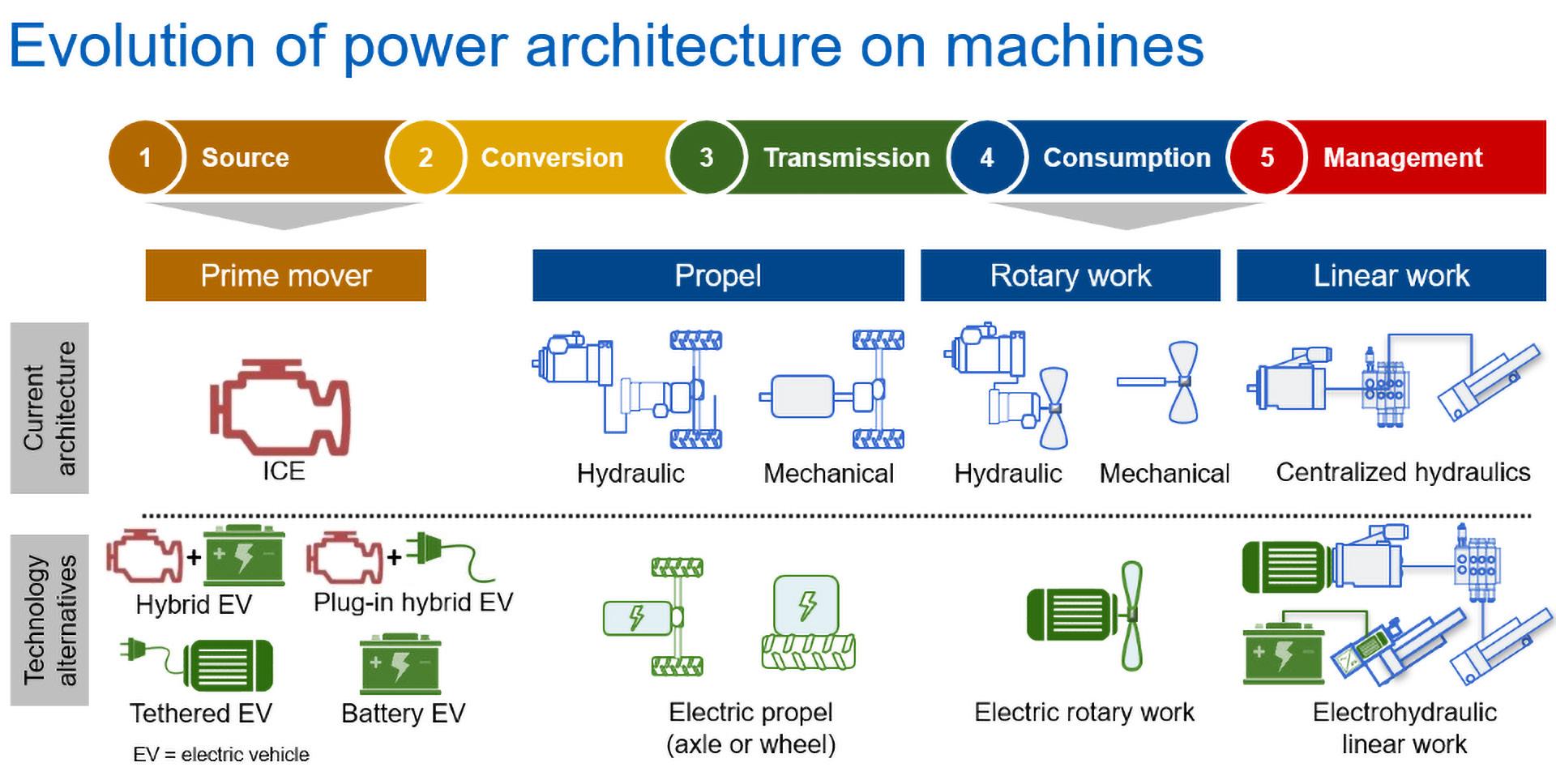
Electrification affects all aspects of a machine’s power architecture, particularly power source and consumption, as shown here.
Similar to excavators, smaller wheel loaders may fully electrify while midsized and large loaders will often take a hybrid approach.
Electrified machine challenges
Many OEMs are taking a phased approach to electrification, starting by replacing diesel engines with electric motors and batteries. They’ll put in as much battery as needed to get a decent day’s work out of the machine but keep the rest of the circuit the same. When these vehicles are taken to market, the feedback is typically: “I can’t make it through the day on one charge,” or, “This machine is too expensive.”
These challenges, common across a range of platforms, present a catch-22. Often, the runtime on a single battery charge is too short. But adding more
Several considerations must be taken into account when electrifying off-highway equipment.
battery power to enable longer runtime adds expense, and electrified machines are already more expensive than their diesel counterparts—sometimes up to twice the price. Battery costs are decreasing, but they’re still one of the most expensive components in the machine.
Elsewhere, the quieter operation of electric machines may drive demand for even longer runtimes than expected today. This is because the machines could operate earlier and later in the day when they are no longer subject to city noise ordinances.
So, how can OEMs balance extended runtime without excessive battery costs? Different architectures and components that make the machine more efficient require attention, and hydraulics are a prime target.
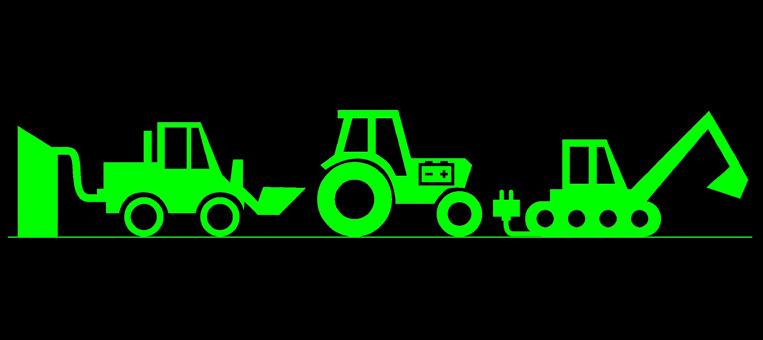
Achieving hydraulic system efficiency
Given the challenges associated with electrifying linear services, a large portion of mobile machines—particularly those performing high-power linear load movement—will likely maintain hydraulic systems. While traditional hydraulics are not the most efficient, with the right technology it’s possible to balance machine performance, cost and efficiency.
First, there is an opportunity to improve work circuit efficiencies and reduce losses on many machines. Conventional hydraulic systems often waste energy, primarily via control valve metering losses. A smarter valve can better control these losses through independent metering. For example, Eaton’s CMA advanced mobile valve enables loads to be safely lowered using gravity, rather than expending energy to push it down hydraulically. Gravity lowering and optimizing pump margins with the CMA valve has been shown to reduce hydraulic power consumption on a forestry forwarder by 7%. Furthermore, the valve’s voice coils use 66% less electrical power per section than a standard solenoid coil.
Independent metering is an advanced, often expensive technology, but the CMA valve enables cost optimization with streamlined CMT sections on services that don’t require independent metering. Expect to see additional independent metering solutions brought to market in support
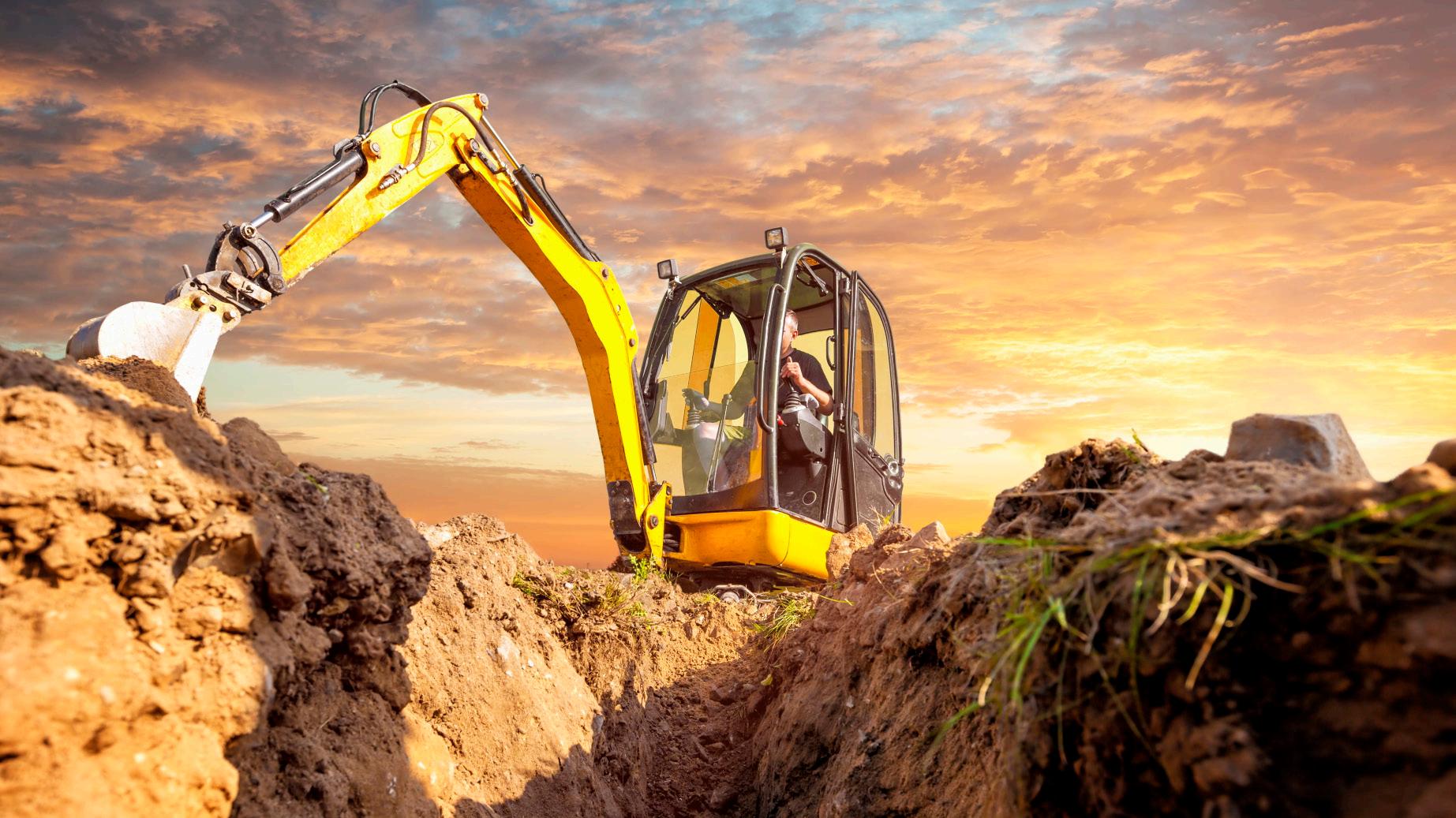

of electrification trends.
Advanced pump technology can also improve work circuit efficiency. Eaton’s X20 pump with electronic displacement control (EDC), for example, enables configurable operation modes based on power needs. For machinery that tends to run low on battery, an OEM could develop an “eco mode” to limit power and extend battery runtime. With EDC and a distributed electronic controller, it is possible to develop software solutions for better power management.
There are also opportunities to recover energy through the hydraulic system. The right technology can help store energy in a hydraulic accumulator or in the battery system through the electric motor that drives the hydraulic pump, enabling the electric motor to effectively run as a generator during gravity lowering or deceleration, for example. This process is already common in hybrid consumer vehicles where electric motors recover energy as the car brakes.
Finally, better hydraulic and electric component integration is necessary to achieve these efficiencies. Hydraulic pumps and the electric motors that power them must work together in harmony; smarter hydraulic components that can sense load requirements and opportunities for energy recovery are needed to achieve efficiency gains.
New hydraulic system architectures can significantly impact machine efficiency, but they require the right expertise to design and implement. Eaton is continuously investigating how to build more intelligence into and increase the efficiency of hydraulic components and subsystems, contributing to a holistically smarter, more efficient vehicle. There have been promising results so far—in certain applications, energy consumption has been reduced by 15-20%, resulting in potential battery savings of up to $4,000.
Investigating the opportunities available in hydraulic systems can make a difference in vehicle electrification, potentially enough to solve the runtime/cost conundrum. |
This article written and contributed by Shelley Nation, Senior Engineering Specialist, Emerging Technologies, and Aaron Jagoda, Senior Engineering Specialist, Advanced Technology at Eaton.
The demands and usage of mini excavators simplify full electrification of these machines.
LCD BATTERY INDICATOR PT33 SERIES
ENM’s PT33A1 series compact meter with various functions and alert systems is ideal for customers to get the most relevant information from their battery system. The unit has a built in hour meter and service timer, a battery level monitor, and a voltage monitor all designed to gather relevant information about your battery in an intuitive manner.
MADE IN THE USA
E-MAIL: customerservice@enmco.com TOLL FREE: 888-372-0465 www. enmco.com