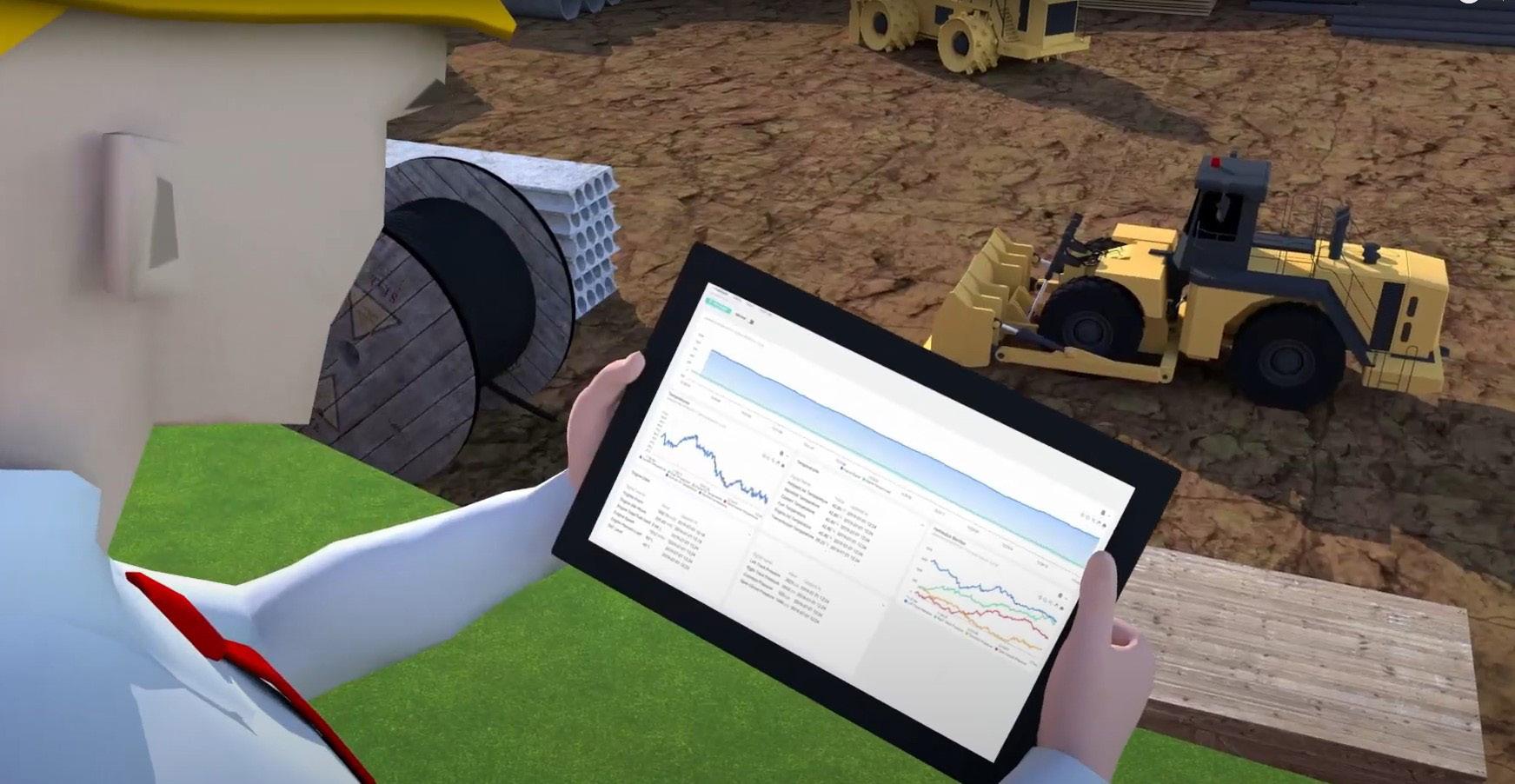
8 minute read
OEM Construction Equipment Telematics Evolves
OEM Construction Equipment Telematics Evolves by Charles Rathmann
Construction equipment users and construction executives operating mixed fleets have struggled with original equipment manufacturer (OEM) proprietary telematics systems. Executives responsible for a rental fleet or contractor fleet have had to choose between disjointed systems or try to port limited amounts of data into a solution from companies like Tenna, Fleetio or multiple multi-function software applications that also offer equipment telematics features like Assignar or HCSS.
Yet the OEM telematics category is growing at a rate of about 15.6% annually. The capabilities of OEM and independent telematics systems have expanded to include not just location and maintenance codes, but productivity, safety, cost efficiency and compliance. This data is not used just to support the asset through a defined condition-based maintenance application, but must be usable by a broad spectrum of operational and analytics systems.
ELEVAT IOT
More open APIs
Stock telematics solutions coming to market in the coming months and years will be more open as OEM vendors yield to the needs of the market. Telematics solutions that don’t play well with other technologies will put OEMs at a disadvantage as their customers want to see equipment across a mixed fleet on a single pane of glass.
According to Adam Livesay, co-founder and chief commercial officer of Seattle-based internet of things (IoT) vendor Elevāt.IoT, equipment vendors are waking up, smelling the coffee and making their technology stacks more open to external systems.
“The biggest change I have seen in the last few years is companies being comfortable using software APIs,” Livesay said, referring to the application programming interfaces that enable various software and hardware solutions to communicate with each other across all industries. “If an OEM designs a system that has a proprietary control software or algorithm, that sets up barriers. A tree trimming company using a piece of equipment may define utilization of a piece of equipment using that algorithm or telematics product differently than their competitor, or the same technology is used in a different application like street sweeping and productivity must then be captured in a different way.”
It becomes easier, according to Livesay, whose company goes to market through 20 fluid power system integrators that drive its technologies into new product development (NPD) value streams for about 300 OEMs, when this information can be exposed to external systems that can display it or use it in different ways.
“The Associated Equipment Manufacturers (AEM) standard for mixed fleets helps,” he said. “Now it is very common for them to ask us if we have a set of APIs. Yes we do. They ask how to interface with our APIs and we give them our documentation.”
This creates an open environment where the OEM can collect data per their requirements, their customer’s operator can use it to manage equipment and the data set can be exposed to other enterprise systems used across the customer environment or even across a multi-company digital construction workflow.
OEM New Product Development
This shift though will primarily be felt in the NPD process and to a certain extent among equipment users as APIs become the plug-and play approach for systems integration, equipment end users to access data for their own purposes. Specific codes thrown by a piece of construction equipment may still, however, be proprietary and incomprehensible to third party telematics systems from companies like Tenna, Fleetio and others.
“We started seeing the shift about three years ago,” Livesay said. “In the
last 18 months, we started to have this type of collaboration. Now we are getting the next tranche of companies really starting to collaborate—ecosystem partners sharing information, sharing data, making it easier to get that proprietary data out. So in the next year to four or five years, connected machines getting access to other connected machines will become a lot easier and the data system a lot richer.”
A more collaborative NPD process, cheaper sensors and controls, affordable IoT cell connectivity and cloud architectures that are likewise more easily integrated all contribute to a telematics sector that will generate a more robust data set usable in more different ways.
“We will see more machine data coming off hydraulics systems and the machine itself, including from safety sensors on seatbelts and other components,” Livesay said. “We’ll see more work information and productivity information being shared.”
According to IoTco Managing Partner and Chief Evangelist Mohamed Abuali, interoperability is becoming the watchword across multiple equipment classes and technologies.
“I think there is more openness now for all types of devices and things to interoperate and speak with a common language to the free world,” Abuali said. “You have these IoT platforms like PTC ThingWorx,
Hitachi Vantara, as well as Siemens Mindsphere. I know they have approaches that can use open source drivers and languages like OBC UA or MQTT which is a messaging broker. All these IoT platforms support these open standards and protocols. My strong recommendation for future vehicle OEMs is to incorporate these standards. Hitachi for instance created an approach for their vehicles to speak in a very common way using ZCORE, which is a data logger that performs AI on the edge as well as the ability to send data to an external IoT platform using open standards. That is a very strong move towards interoperability as well as connectivity and AI on the edge.”
Balancing cloud and edge computing
The telematics sector, as it becomes more central to how heavy equipment is operated, is coming to market with a more robust approach to communicating with the cloud. Equipment operated outside of cell phone range either still must be able to log data on the piece of equipment itself and communicate with an operator on site. Increasingly, telematics and IoT devices will include a dual-mode or even multimode communication features.
According Abuali, telematics equipment will increasingly com-
SOME THINGS ARE JUST BUILT TO LAST
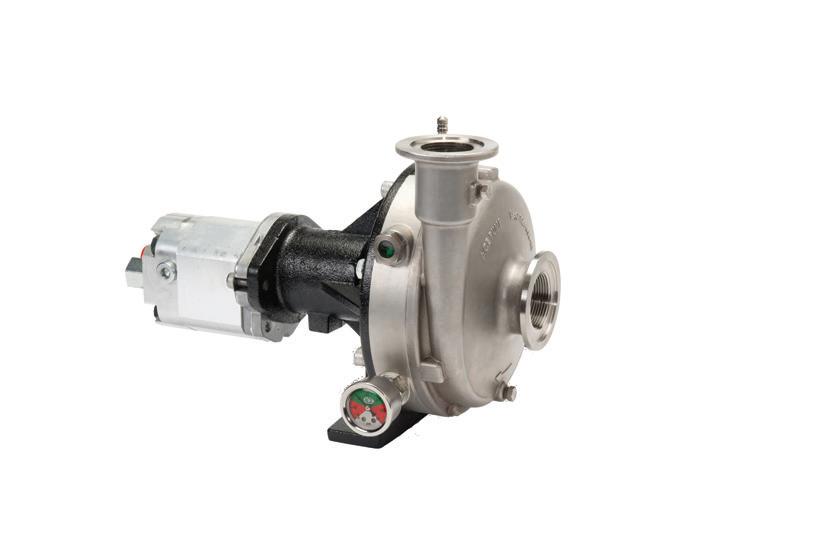
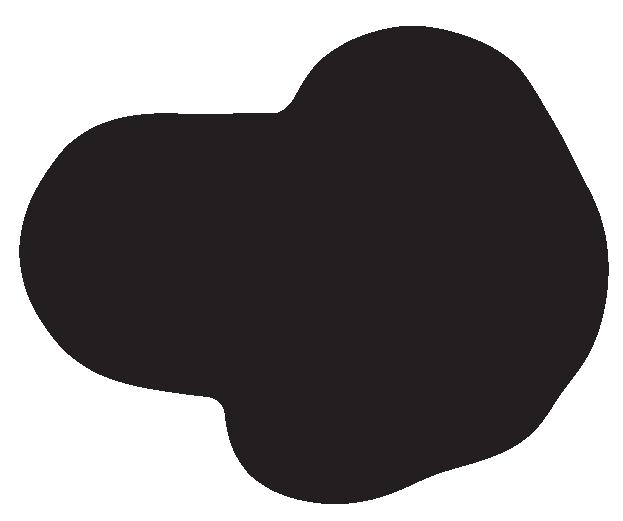
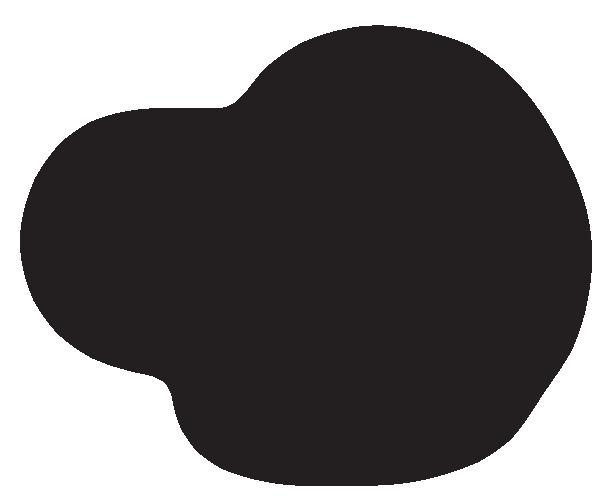
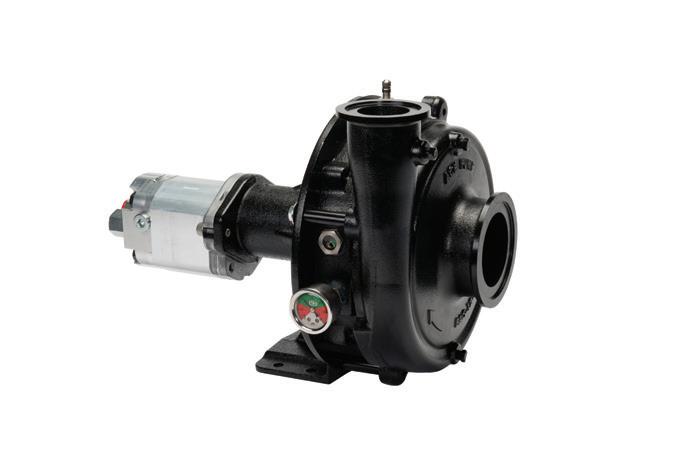
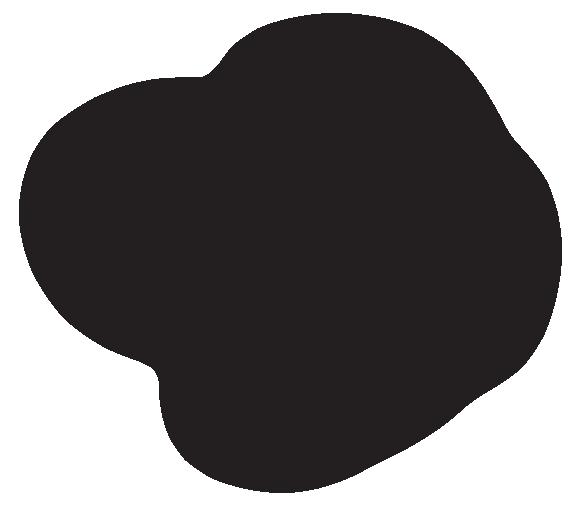
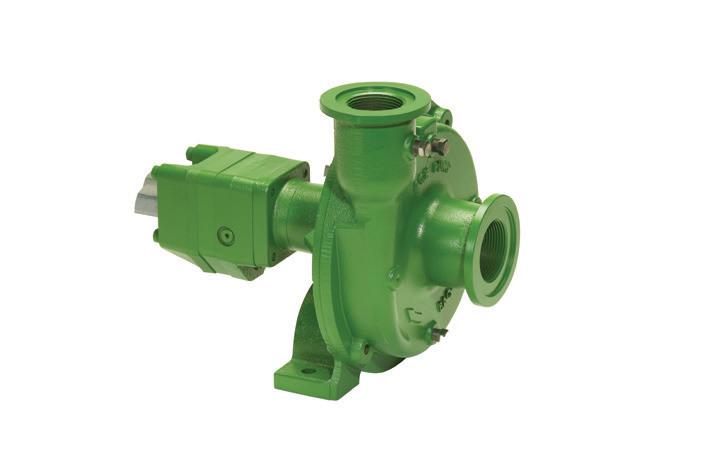
Ace pumps may not last 4,500 years like the great pyramids of Egypt, but they are designed to be the longest-lasting pumps on the market today. For more than 70 years, we’ve built our pumps with only the best components, backed by the strictest quality control standards in the industry. So, the next time you need a pump that stands the test of time, be sure to ask for an Ace pump.
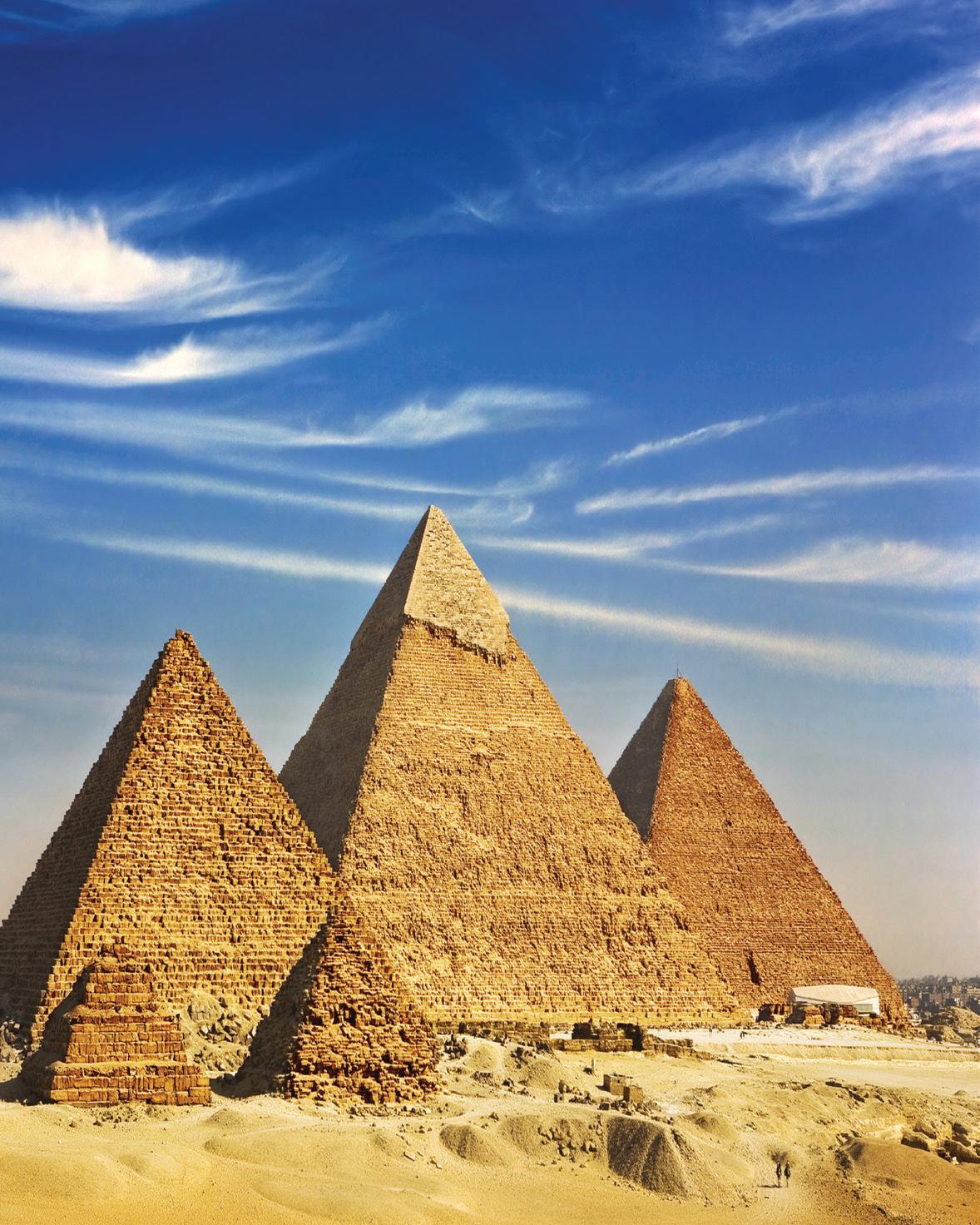
To learn more, please go to www.acepumps.com or give us a call at 800-843-2293.
plete substantial computing at the edge—local to the device rather than in a cloud-based application. Abuali and his company help OEMs embed IoT and predictive analytics software in their products and have worked on equipment product lines from Komatsu and Kion.
“The whole premise is these types of equipment are used in remote locations that are inaccessible—we find it is essential to have remote monitoring as a service,” Abuali said. “When internet connection is not available, satellite communication is needed.”
The satellite will not relay information in real time and packet loss means only so much data can make the trip. That means the equipment must make choices about what data to upload.
“We have a very special approach where data is collected on a data logger on the machine itself,” Abuali said. “If you consider a piece of equipment like a big excavator tractor, there will be some AI happening on the edge on the data. When the internet connection opens once a day, the AI has made some decisions regarding the critical components, the health of these components, and can send this information to a spare parts system.”
The edge system must perform diagnostics so it can request specific actions within the cloud-based operations and maintenance system.
“By then connecting to the service system, it can auto-generate a work order and request spare parts. The goal is to move from a reactive failure approach—AI on the edge on vehicle able to make diagnostic decisions that enable predictive and condition-based maintenance,” Abuali said.
“We definitely see blended applications where satellite is used for certain data sets,” Livesay said. “We can design into the system a protocol where for cellular, we want this type of information, generally a smaller subset of data for satellite and then all the way to wifi when we connect back to the bay at night. In situations like this, mission-critical data is communicated from the field, and deeper information after the fact. Maybe we want to collect and log data points until I connect to a local network, a service laptop, cell data or wifi.”
While Livesay says he currently sees blended connectivity applications for telematics including cell, satellite and wifi, he also sees potential for innovative Bluetooth applications similar to Amazon Sidewalk, which is a broad peer-to-peer network of connected devices. Zigbee, for instance has solid construction and mining use cases. |
Scan here to read more https://oemoffhighway.com/22080937
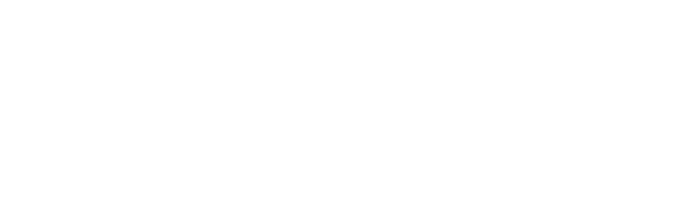
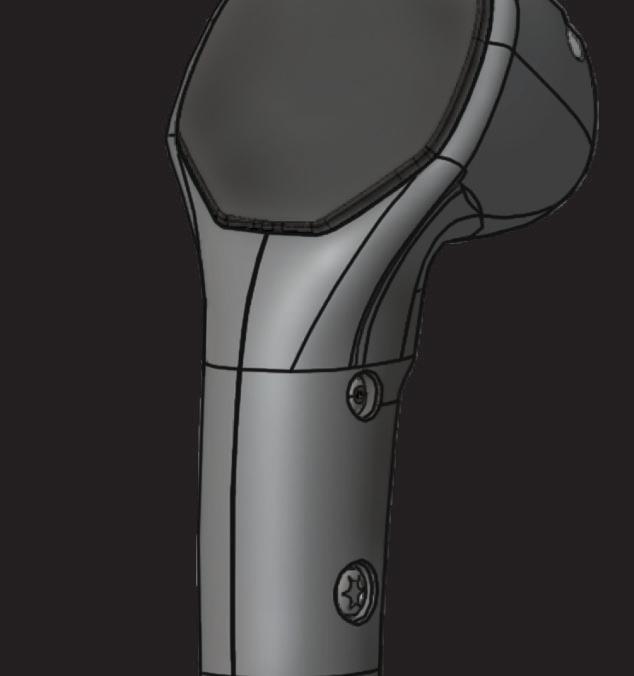
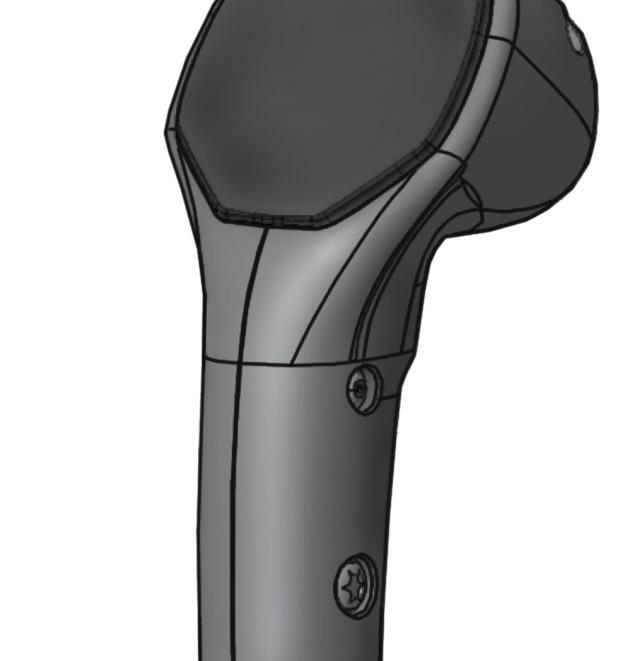
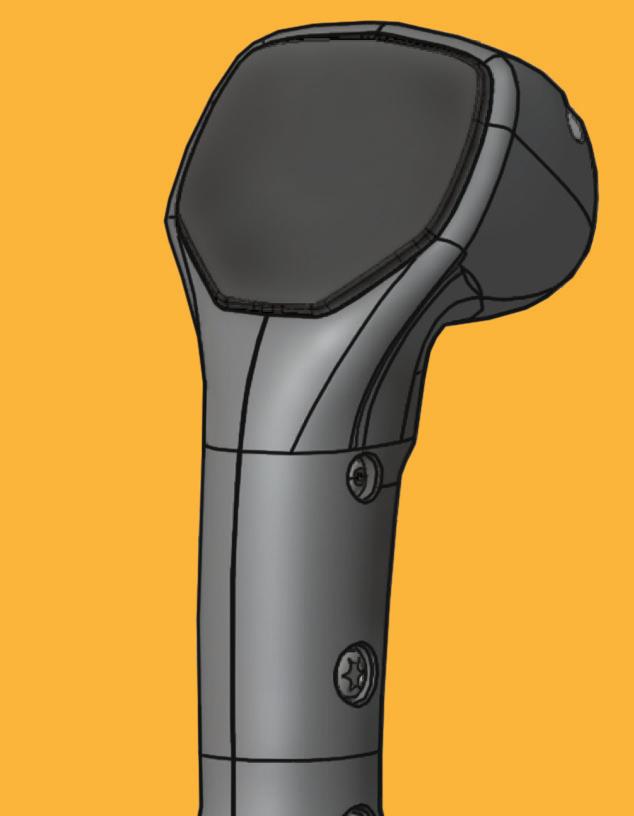
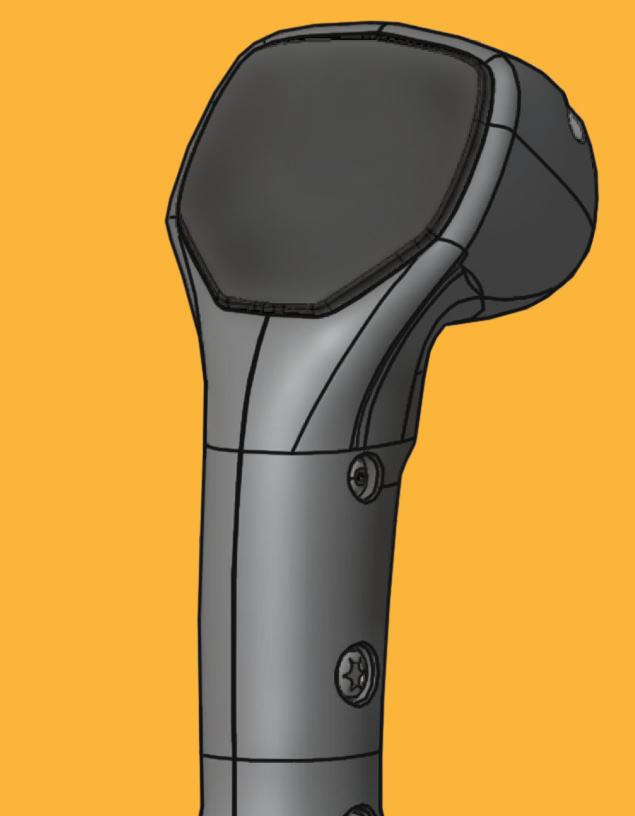
G3-C — UNIVERSAL GRIP
HIGH PERFORMANCE, HEAVY EQUIPMENT AND MATERIAL HANDLING GRIPS
Z-axis with +/- 250 rotation option
Grip Touch Switch option
Numerous standard faceplate designs
Multiple trigger options
Easily customizable
WITH Z-AXIS ROTATION ROTATION ROTATION
G3-CK G3-C
G3-C