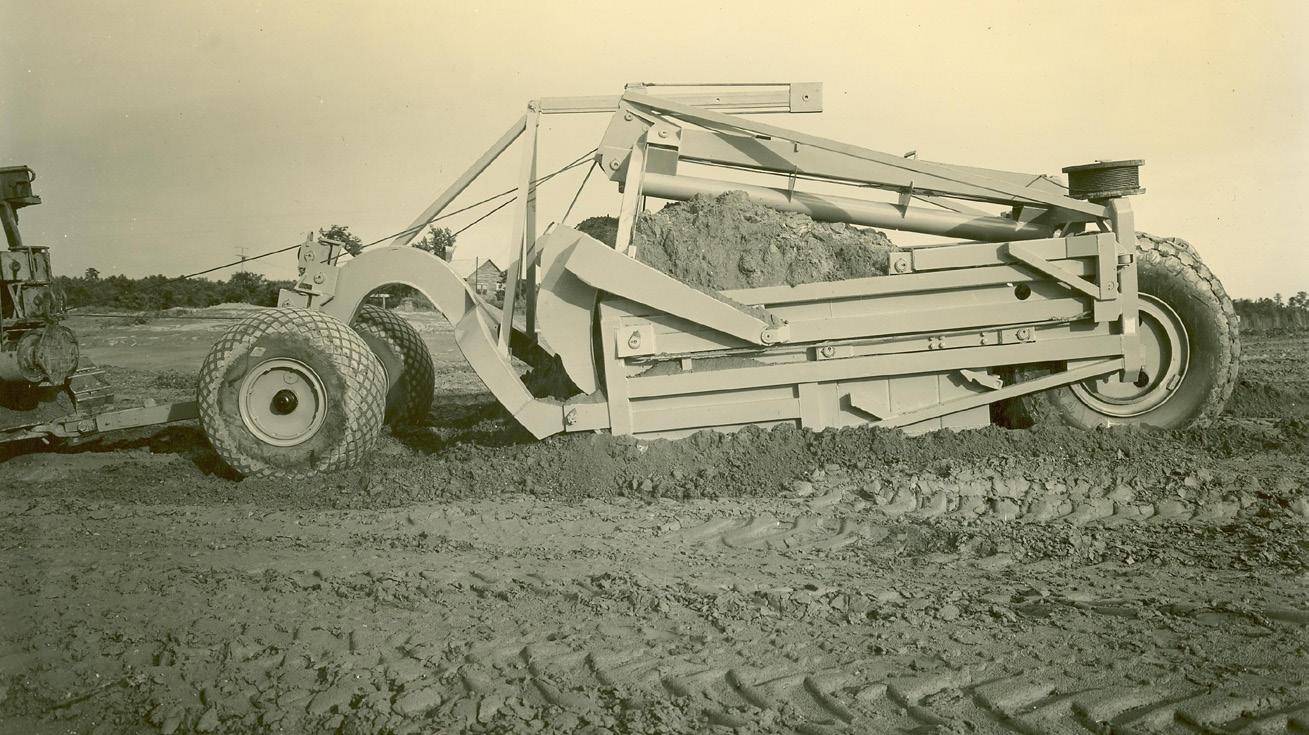
3 minute read
Telescoping Bowl Scrapers
They were developed to eliminate the high power required to force the load down the entire length of the frame.
Increased efficiency has always been a goal when designing construction machinery. Some machines lend themselves more easily to these principles than others. For instance, except for the largest models used in mining, a motor grader’s blade width is constrained by the width allowed in roadwork. However, the power and efficiency applied to the blade can be increased.
The Mechanized Scraper
One machine that could have been designed for higher capacity was the mechanized scraper. The limits of animal power kept slip, Fresno and early wheeled scrapers small. Once tractors were used, things changed.
The two simplest ways for a scraper to maximize a tractor’s pulling capacity were to design a larger bowl or hitch multiple scrapers together in train. Enlarging the bowl would have been a normal solution, but R. G. LeTourneau rarely followed norms. His concept to increase capacity was no exception.
Innovative Solution
The problem with a bigger scraper bowl was the power required to load and unload it. Width had to be kept in check for transportation and resistance on the cutting edge, so it could be deeper and/or longer. The stresses of loading and ejecting the load, especially when moving it the length of the bowl, increased the power required beyond that needed to move the load.
LeTourneau’s unusual solution was the world’s first motor scraper with a gas generator powering seven electric motors. The power system could not load and eject the 12-cubic-yard payload, so he designed and patented a telescoping bowl.
The bowl consisted of five buckets nested at the front of the scraper frame. The first bucket was loaded, and then released to move back. Each of the other bowls were loaded in sequence. Once they were loaded, they would be aligned along the frame’s length. Ejecting the load simply reversed the process, unloading the forward bowl first and then bringing another forward inside it. This kept the loading and unloading action in the front few feet instead of needing enough power to force the load down the entire length of the frame.
LeTourneau sold the patent for this design to contractor Warren Brothers Company in 1927. Then he re-acquired it in 1935. He produced a range of telescopic-bowl scrapers for crawler tractors and his largest Tournapull prime movers. When LeTourneau re-entered construction equipment manufacturing after noncompete restrictions expired following the sale of his construction interests to Westinghouse Air Brake in 1954, some of his huge electric-digger electric drive scrapers used telescopic bowls.
The Historical Construction Equipment Association (HCEA) is a 501(c )3 nonprofit organization dedicated to preserving the history of the construction, dredging and surface mining equipment industries. With over 3,500 members in a dozen countries, our activities include operation of National Construction Equipment Museum and archives in Bowling Green, Ohio; publication of a quarterly magazine, Equipment Echoes, from which this text is adapted, and hosting an annual working exhibition of restored construction equipment. Individual memberships are $35.00 within the USA and Canada, and $55.00 US elsewhere. Our next International Convention and Old Equipment Exposition will be September 22-24, 2023, in Bowling Green, Ohio. We seek to develop relationships in the equipment manufacturing industry, and we offer a college scholarship for engineering students. Information is available at www. hcea.net, or by calling 419-352-5616 or e-mailing info@hcea.net. |
MEIER-DAILEY PAPERS, HCEA ARCHIVES
Not all of LeTourneau’s telescopic scrapers were unusually large. This Model LU Carryall has only an 11-yard heaped capacity, but this image shows the significant effect of the loading of the first of two buckets. It will soon be moved back, and the second bucket will load in its place.
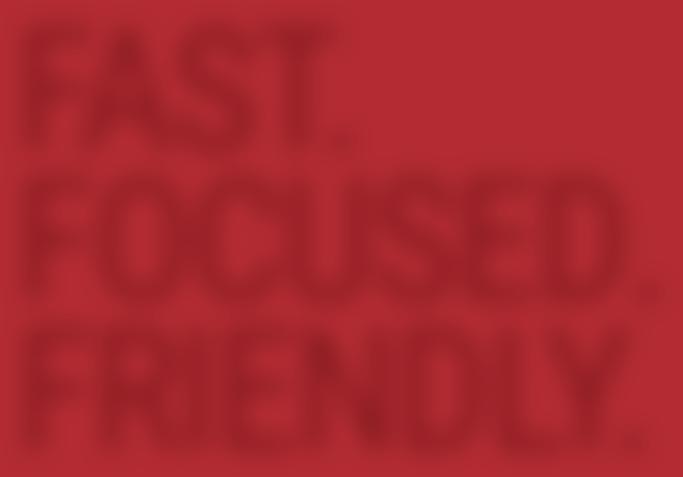
FAST. FOCUSED. FRIENDLY.
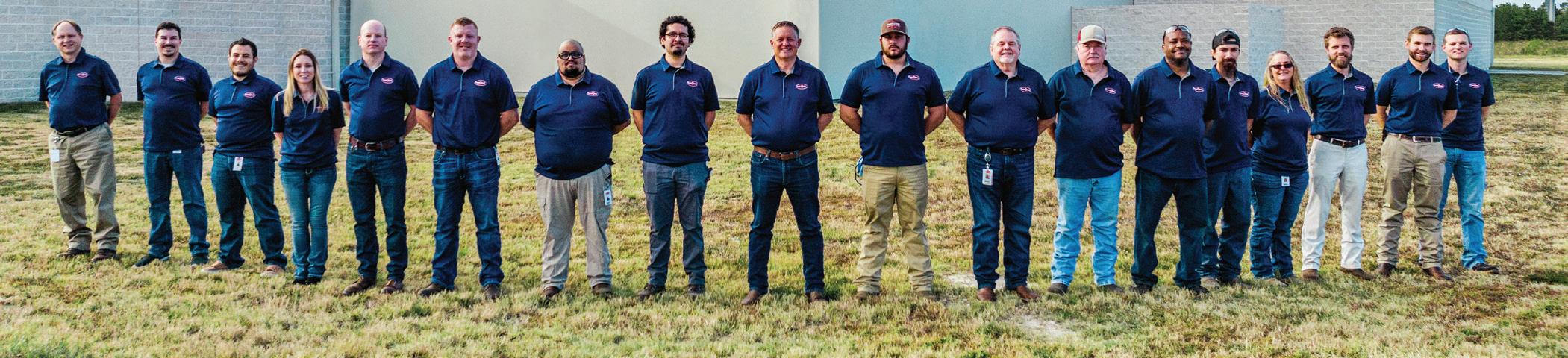
WHEN YOU NEED IT RIGHT AND YOU NEED IT NOW,
CALL SUNIE. From order entry to product shipment, Sunie and the team at Twin Disc’s Lufkin, Texas, facility care for your order to ensure you receive a product that exceeds your expectations.
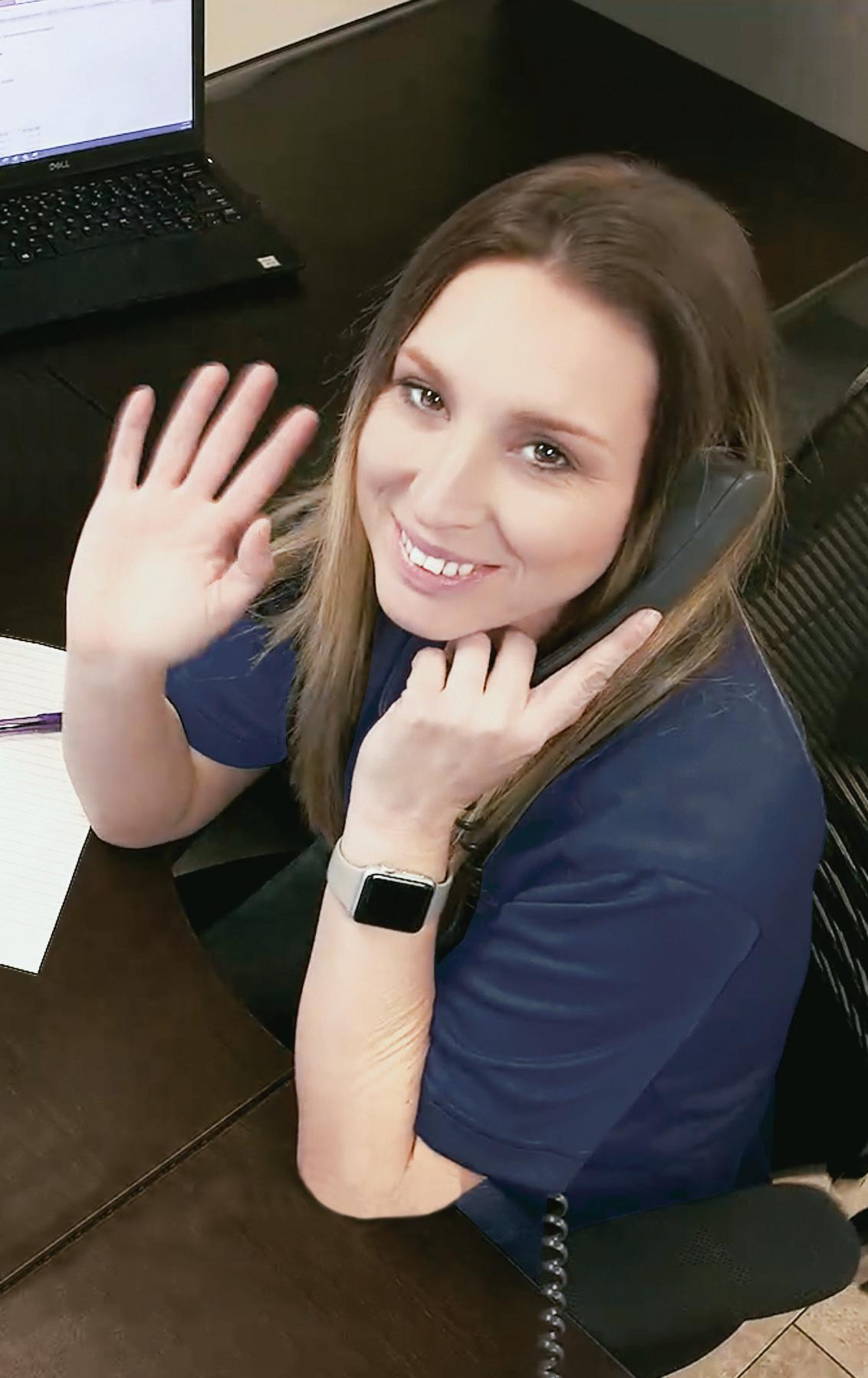

With an intense focus on land-based power transmission products, standard power take-offs, hydraulic power take-offs, mechanical clutches and pump drives are produced and shipped from Lufkin, Texas, with industry-leading delivery times. An experienced, friendly team that’s homegrown in Texas provides quick responses, fl exibility and customer service that can’t be beat.
Fast. Focused. Friendly. From deep in the heart of Texas.
Explore more at TINYURL.COM/LUFKINOEM