
6 minute read
Environmentally Friendly, Sustainable & Bio-Based: Untangling Common Terms
from OOH May/June 2023
Sustainability is topic of much discussion in today’s off-highway industry. OEMs and equipment owners/operators are in continuous pursuit of new ways to decrease emissions, improve fuel economy and extend the useful lifespans of all forms of critical equipment.
Industrial fluids—be they hydraulic fluids, greases, metalworking fluids, industrial gear or other fluids—have an important role to play in this pursuit of sustainability. High-performance options can help equipment operate to its full potential, optimizing fuel consumption and overall machine efficiency, while protecting critical parts to extend lifetimes.
But for these fluids, there are other characteristics to consider. For example, biodegradability and environmental friendliness. Because considerable amounts of industrial fluids make their way into the environment every year, a fluid’s ability to safely decompose has become a highly sought-after trait. The U.S. Environmental Protection Agency (EPA) defines such fluids as environmentally acceptable lubricants (EALs). While EALs have traditionally been seen as a niche product, demand is rising due to evolving regulatory requirements.
As all industries seek to enhance their eco-conscious reputation, it is important to understand some of the subtler differences between sustainability and environmental friendliness, and how EALs differentiate from bio-based fluids.
Sustainable or Environmentally Friendly?
The preferred framework for sustainability evaluates a product’s overall effect on the environment across its entire life cycle. This accounts for the product’s impact while it is in use and in the steps leading up to its creation and those of its eventual end of life. Calculating these figures, taking into account the entire history of how the product is made, involves a methodology commonly known as life cycle analysis.
It is against this backdrop that we can better evaluate different lubricant and fluid formulations and classifications that have emerged in recently. EALs offer a good example. As noted earlier, EALs are explicitly defined by the U.S. EPA as formulations that have demonstrated acceptable levels of biodegradability, minimal aquatic toxicity and non-bioaccumulative potential. And it is worth digging into the specifics of these terms:
• Biodegradability: The capacity of lubricants to be decomposed by microorganisms over time into:
• A combination of simpler by-products (primary biodegradation)
• Carbon dioxide and water (ultimate biodegradation)
• Minimal Aquatic Toxicity: Low toxicity to aquatic organisms according to tests defined by the Organization for Economic Cooperation and Development (OECD) and EPA test guidelines.
• Bioaccumulative potential: the buildup of chemicals within the tissues of an organism over time.
These characteristics are particularly important within the realm of off-highway equipment. Because whether via machine seepage, accidental spillages or careless disposal, the final part of any industrial fluid’s life cycle may very well occur within the natural environment. Their ability to minimize harm to delicate ecosystems is critical. Traditional industrial fluid formulations do not typically account for these consequences.
Growing environmental awareness has also seen increased adoption of bio-based lubricants and fluids in off-highway applications. Frequently, bio-lubricants are made from natural oils and avoid the use of petroleum-based oils in their formulations—making them generally viewed as a more sustainable option. However, bio-lubricants need only be made from natural oils to be labeled as such, and unlike EALs, do not need to meet stringent criteria that certifies their eco-friendliness. A bio-lubricant may be biodegradable, but isn’t necessarily so by definition. For example, a bio-lubricant may still incorporate an additive component that is not bio-degradable. These are important distinctions to make as the off-highway market continues to seek to maximize its environmental protection.
Coming back to what makes a lubricant sustainable, the source of raw materials and EAL-qualifying characteristics of a lubricant only represent portions of a lubricant’s life cycle. One needs a complete life cycle analysis to honestly say that one particular formulation is more sustainable than another. That doesn’t minimize the positive impact of using EAL qualified lubricants, of course.
Included in that life cycle analysis is the in-use performance of the lubricant.
Making an Impact in Off-Highway Equipment
As mentioned at the beginning of this article, advanced fluids have the potential to optimize today’s most efficient off-highway equipment. By delivering high levels of performance across a broad range of performance characteristics, the right fluid can help machines achieve optimal fuel consumption, maximum efficiency, and extensive service life. It follows, then, that EALs—in order to best benefit the end user, and the planet—should be able to do just the same.
There are a range of performance characteristics that any reliable industrial fluid—EALs, bio-lubricants or others— should be able to provide. They include:
• Wear protection. Preventing the premature wear of metal surfaces as they contact each other is the core function of lubricants.
• Extreme-pressure protection. Industrial fluids in demanding applications require extreme-pressure additives to withstand severe conditions.
• Emulsibility. Depending on the application, many industrial fluids must properly emulsify with water. Other fluids may need to resist emulsification. The right chemistry is required.

• Antifoam performance. When air becomes entrained within an industrial fluid, foam can result, which may compromise its ability to form a protective film. A high-performance fluid will be resistant to such foaming.
• Corrosion and rust prevention. A variety of off-highway fluids come into regular contact with water and air at elevated temperatures—conditions that can lead to damaging rust and corrosion.
• Viscosity and friction performance. Some applications require specifically calibrated thickness and friction to enable proper machine performance. Many traditional chemistries deployed in most off-highway fluid formulations are not applicable in EAL products. This is because many of those ingredients, which help a completed fluid deliver each of these performance characteristics, do not meet EAL standards for biodegradability, non-toxicity, and bioaccumulation. For example, some of the most common and reliable anti-wear chemistries used today are zinc based. A nonmetallic option is required to meet biodegradability standards.
Applicable chemistries do exist, making high-performance EAL formulations are possible—and they will only become increasingly important as industries everywhere seek to minimize their environmental impact. For the off-highway equipment industry, it is worth investigating the application of these kinds of formulations today. They are only expected to gain market share as regulatory pressure grows, and as the world grows increasingly eco-conscious. Ensuring that EALs maintain the right performance characteristics—to enable off-highway machinery to achieve peak efficiency and reliability—is essential. Such formulations represent an important tool for the off-highway equipment industry to maximize environmental protection, and it can be worth opening the conversation about such options with your fluids supplier.
New PC-GO Software
Danfoss Power Solutions, a supplier of mobile and industrial hydraulics and electric powertrain systems, launched its PC-GO propel solution for single pump/motor hydrostatic transmissions. Comprising the new PC036 safety controller and PC-GO propel software, the ready-to-use platform decreases propel subsystem development time by up to 35% while simplifying compliance with environmental and safety regulations.
It is a fully developed propel system software solution that’s configurable using the Danfoss PLUS+1 service tool for quick and simple customization, and it is housed on the PC036 controller. The software is ideal for a variety of applications, including wheel loaders, telehandlers, dump trucks, street sweepers, and forestry equipment.
Battery Systems with Increased Energy Density
Yanmar Group company, ELEO Technologies B.V., a battery technology manufacturer located in Helmond, the Netherlands, displayed its next generation of battery systems at CONEXPO-CON/AGG. The new system offers increased energy density and integration flexibility following from the unique modular concept.
The new battery system is the second product generation from the Dutch manufacturer after the first generation started production in early 2020. With the new product, ELEO offers industrial original equipment manufacturers flexibility with the scalable design to meet the requirements in the off-highway industry.
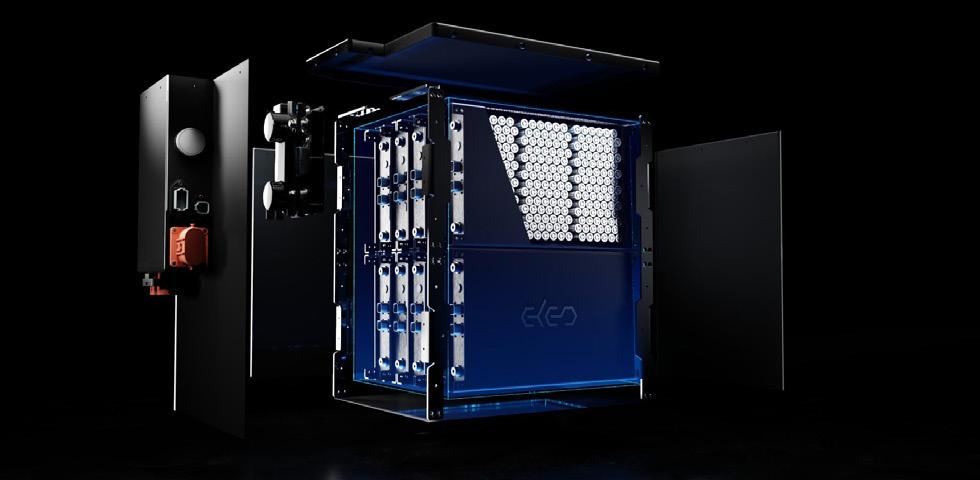
Ion Exchanger for Hydrogen Fuel Cells
To support the use of hydrogen as a climate-friendly energy carrier, Hengst developed a modular set of filtration solutions for fuel cells. During fuel cell operation, ions are introduced into the coolant. These result from the aging of the coolant itself or from components in the coolant circuit. Effective filtration is required to ensure safe operation of the fuel cell.
The Blue.iox ion exchanger from Hengst offers protection with minimum maintenance. The design of the filter cartridge—with axial filter flow and the special mixed bed resin system for cation and anion exchange—ensures high filtration efficiency across the entire service interval. The ion concentration in the coolant circuit is reduced rapidly.
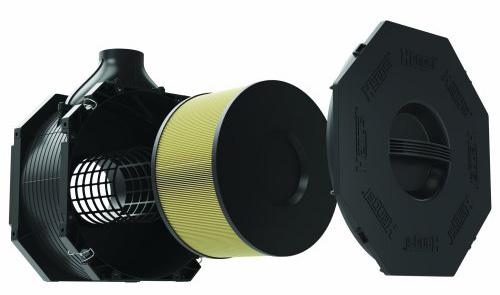
Expanded Line of DC Contactors for eMobility and Industrial Applications
Littelfuse, Inc., an industrial technology manufacturing company, announced an expansion of its portfolio of direct current (DC) contactors developed specifically for eMobility and industrial applications.
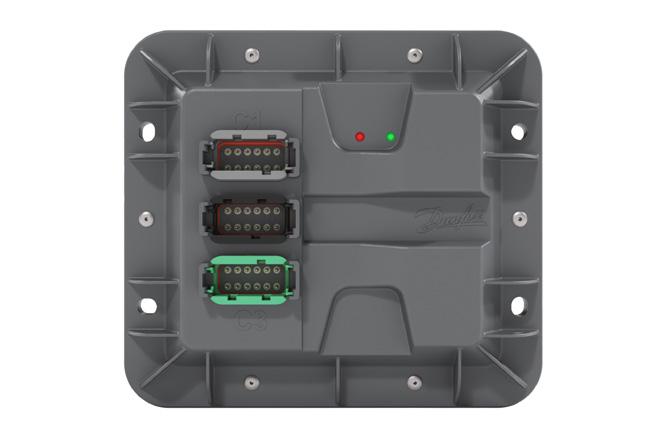
Littelfuse DC contactor relays are available with continuous current ratings up to 500 amps and maximum voltage ratings up to 1,800 volts. Multiple designs are available to meet the requirements of a range of applications. The latest additions to the portfolio include the:

• DCNLR Series: Remote-operated contactor with a spacesaving design; ideal for safely disconnecting DC energy sources in applications that require continuous run time
• DCNHR Series: High-current, high-voltage contactor with a resin body for corrosion resistance in harsh automotive environments, permanent magnet blows the magnetic field horizontally to achieve a high-voltage DC cutoff and sealed contacts for maximum safety
Quite possibly the homeliest motor scraper ever built, this is the first tandem-bowl motor scraper. Built in 1938, it consisted of the original prototype Model A Tournapull prime mover, the only 25-yard Z25 Carryall built, and a 24-yard heaped U-20 telescopic-bowl scraper.