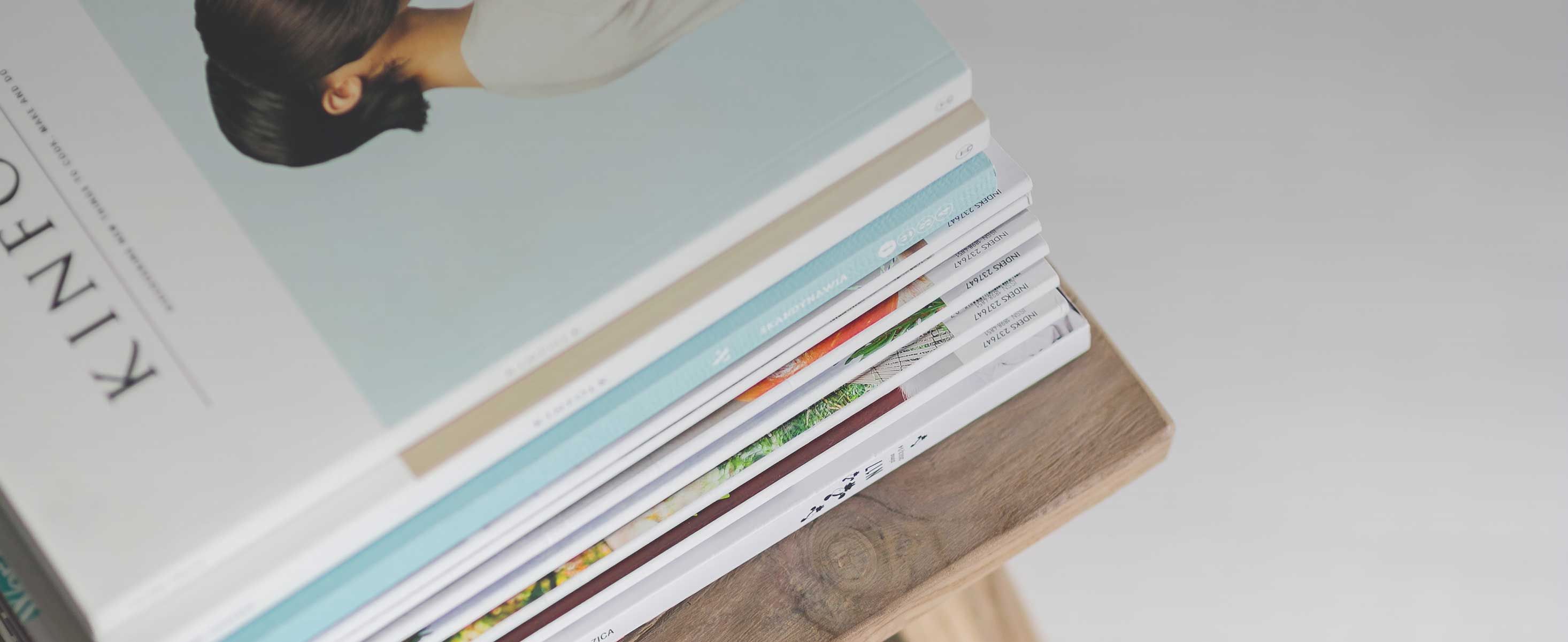
4 minute read
Guest Column: Belcan
Optimizing the Supply Chain in a Changing Environment
CEOs are refocusing efforts to improve cash flow, supply chain efficiency and employee wellbeing
Advertisement
The global situation has caused a largescale of automotive manufacturing interruptions across the globe with OEMs shutting plants temporarily to suppliers ceasing production for a few weeks. The temporary stoppage means no shipments, no transactions and staff are on either reduced income, reshuffled within the business, or laid off.
The distressed global supply base has affected the automotive industry significantly and positioned organizations under extreme pressure to increase cash flow, re-evaluate supply chains, optimize costs, and develop a safe working environment for employee welfare, along with simultaneously moving and managing staff who are working remotely.
The five-stage model outlined below can be implemented by organizations to understand the supply chain, map the critical suppliers and components, develop an action plan and timeline, mitigate risks and build a robust and resilient supply chain.
Set-up a team Understand your supply chain Create visibility at all levels Evaluate and prioritise
Deploy resources to chronic suppliers Outsource for speed and expertise Utilise global presence Employee wellbeing
Stage 5 Build a resilience supply chain
Stage 1 Critically evaluate your supply chain
Stage 2
Supplier Mapping Production volume Define critical suppliers (from all Tiers) Map Geographical location Understand inventory Border restrictions Simulate scenarios
Secure supplier capacity (at all Tiers) Advance procurement Contingency planning Communicate supply chain disruption Adjust business operations
Stage 4
Mitigate Supply Chain Risks
Stage 3
Develop an action plan and timeline Define actions Define roles & responsibilities Spread activity Create a war room
Supply chain disruption can lead to unintended damage to reputations, which can take months to recover as teams tackle multiple challenges at the same time. The five-stage model has proven to yield results by ensuring cost avoidance while mitigating supply chain risks upfront, allowing organizations that take action sooner rather than later to be better prepared with minimum impact.
Click here to read our full report
See how Belcan’s integrated and adaptive services can work for you.
Rahul Gogate | VP, Vertical Business Development | rgogate@belcan.com
By Terry Onica, Director of Automotive, QAD, Inc. and Cathy Fisher, President, Quistem, Inc.
When the US was disrupted by the COVID-19 virus in March of 2020, many believed the impact would be devastating to the Automotive industry. Fast-forward nearly six months later and we find the recovery well underway with most manufacturers returning close to pre-pandemic production levels and demand steadily increasing.
Based on the results of a recent survey conducted by the Automotive Industry Action Group, (AIAG) in partnership with Wayne State University, QAD and Quistem, it appears automotive manufacturers and suppliers were successful in leveraging their management systems along with lessons learned from past automotive industry disruptions to be well-positioned for a rapid comeback.
The restart survey was conducted in June 2020 with over 700 responses from automotive manufacturers representing OEMs, part/component manufacturers as well as service providers. Key findings from the survey included:
At the time of the survey, approximately 60% of respondents indicated they were fully prepared to prevent the virus from entering their facility, reduce the risk of virus exposure/transmission and react if/when the virus was detected in their facility. The most challenging activities for restarting operations (outside of managing the virus) were related to supply chain coordination, i.e., meeting immediate customer requirements and verifying supplier status, and labor shortages. The most common actions taken in response to disruptions involved using strategies and resources that were already immediately available, such as adapting production plans to meet new demand and/or supply and utilizing safety stocks.
The survey along with thirty insights interviews conducted with representatives across the automotive supply chain, also uncovered some valuable lessons learned from the crisis:
1.
2.
3. For those manufacturers who leveraged their existing management systems, (Safety, Quality, Supply Chain/Logistics, etc.), planning for the restart of their operations was made easier due to well-defined processes and existing communication mechanisms. Other noteworthy data points reflected how companies used pre-qualified backup suppliers, switched between different transportation modes, utilized government, industry and peer playbooks and leveraged planning systems for detecting readiness. The importance of detailed contingency/business continuity planning was recognized by senior leadership as a key restart success factor. There is no doubt that going forward, automotive manufacturers will expect more coordination and thorough risk planning. Automotive manufacturers were resilient in adapting workplaces to accommodate safe returnto-work practices while also effectively migrating many office functions to work-from-home, a trend that will likely continue well into the future for many organizations.
In closing, while the relationships between OEMs and their immediate suppliers are relatively wellunderstood, insights and communication into the lower tiers are often not as clear or well-documented. This survey provides valuable insights into this group, which may be considered in managing future disruptions.
For additional survey details and the full insights report, please contact Terry Onica at tjo@qad.com.