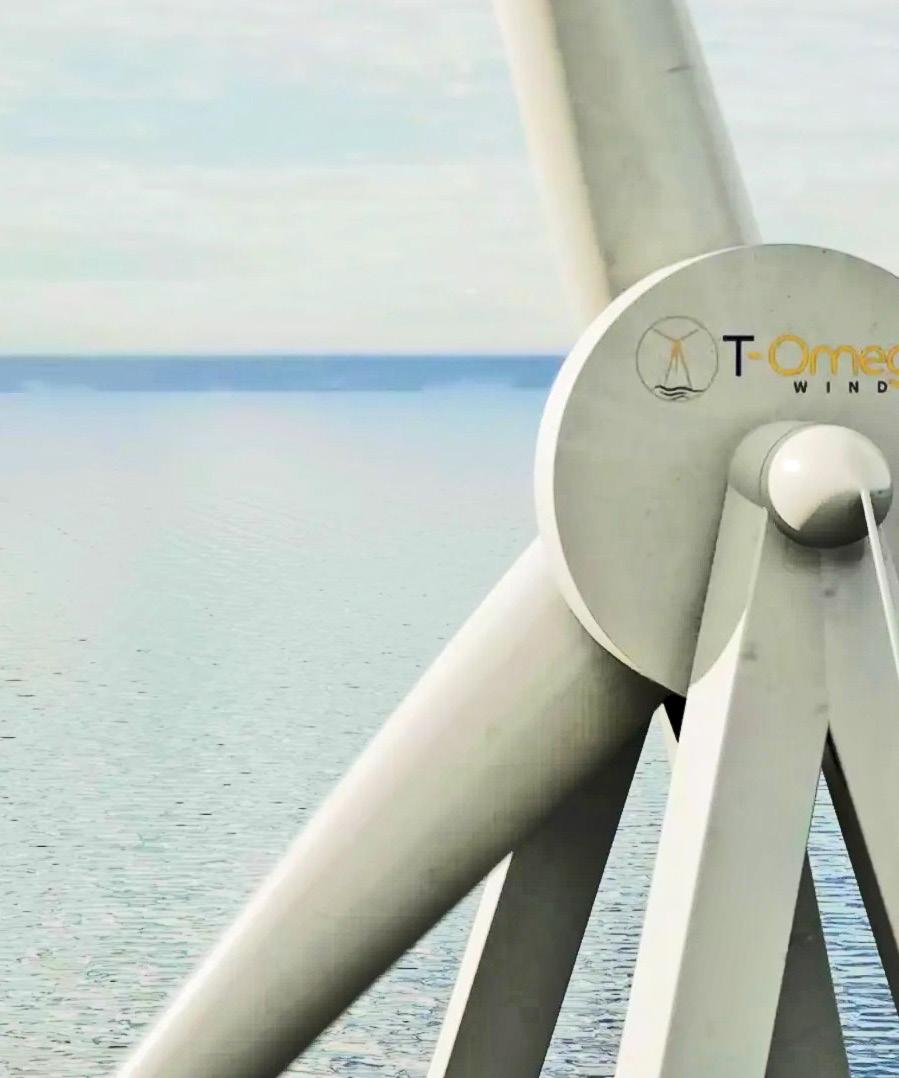
11 minute read
FLOATING WIND TURBINES
SIGNIFICANT COST SAVINGS
Advertisement
All of the world’s largest wind resources are located offshore - often far from shore, where the water is so deep that it is impractical to build typical fan-on-a-stick wind turbines with bases sunk deep into the seabed. At this stage, floating wind is so expensive to build, deploy and maintain that it ends up costing two to three times more per kilowatt-hour of energy than fixed-bottom offshore installations.
There is a huge opportunity for technological advancement here, and companies like it World Wind Norway some suggest quite radical ideas in space. Much of the cost of energy comes down to the size, weight, and materials that go into the construction of the turbine, as well as the logistics and special equipment needed to build, install, and maintain things.
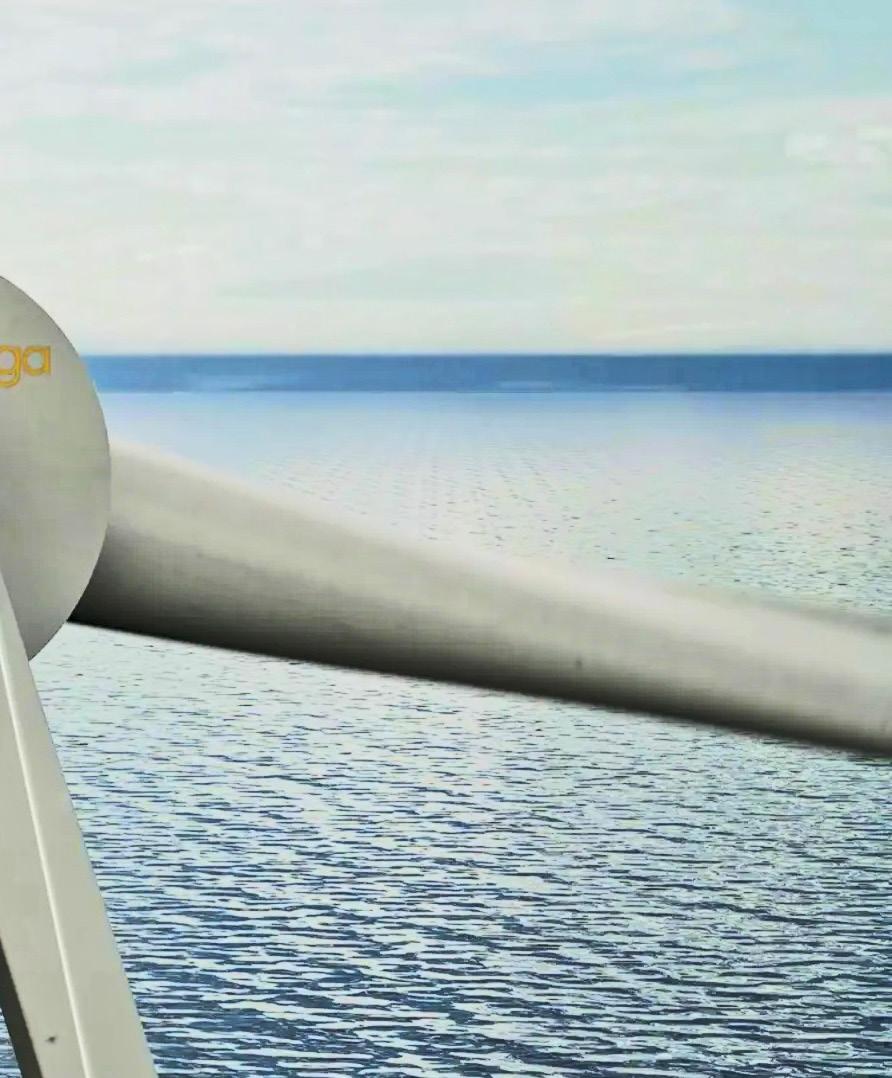
Unique
Boston-based startup T-Omega Wind says it has prototyped and tested a unique floating offshore wind turbine design that can withstand severe storms and hundred-foot waves, but is 20% lighter and about 30% cheaper than conventional designs - not to mention about super-easy deployment and installation - opening up an affordable way to use the world’s best wind resources.
Because there is so little below the waterline, the T-Omega turbines can be easily towed by a single low-cost tug, meaning that maintenance can be carried out in port rather than at sea with prohibitively expensive and specialized vessels.
“All offshore floating turbines except ours are like icebergs,” says T-Omega co-founder and chief engineer Jim Papadopoulos in a recent video chat. “Whatever is above the water, they have four times as much below. If they have 1,500 tons above water, they have 6,000 tons underwater. It’s a big expense. We put almost nothing under water. That’s one of the big differences in cost, mobility and launch.”
Conventional floating turbines, Papadopoulos says, use technology that was developed only for land. “Right now, a Vestas- or GE-style turbine, they have a stunning rotor with a shaft on one side. You can build just about anything, but with a one-way shaft, that shaft is massive and requires some pretty special bearings. And because of the forces acting on this design, there is very little margin for angle change. So they have to hold them still in an upright position – hence the heavy, expensive base. They are imbued with the philosophy of country style, and it is incredibly expensive.”
Different
T-Omega’s approach is completely different, starting with the turbine and generator itself, which are attached to a double-sided axle shaft that is rigidly supported at both ends. So, instead of a single heavyweight pole, the turbine is supported by four much thinner legs that reach up to lightweight, widely spaced floating base platforms. This is very similar to how a Ferris wheel is suspended; there’s a reason they don’t build them on the same pole.

Will it capsize?
“If you take a wooden door and put it in water, it won’t tip over,” says Papadopoulos. “It’s the width compared to the height. Yes, we have a very wide base compared to any other floating structure. To lift the floats out of the water, you’re dealing with an ungodly amount of torque - much more than the torque of the generator.’
The floating base is tethered to the seabed, and as the wind changes, the base rotates freely around its pivot point on the seabed, so that it is always facing directly into the wind – but without the need for sensors, motors or turning mechanisms to achieve this. The material savings are huge, says Papadopoulos.
This also goes for top gear. T-Omega’s bidirectionally supported design does not require the same massive generators and shaft designs that conventional turbines require, simply to handle the enormous load created by a single-sided axis. That means less metal, less weight, less specialized tools, and less cost every step of the way. It also means that a wider range of makers can create things.
Prototype
The company built a two meter high prototype - a 1:60 scale model of a 10MW commercial product and tested it for stability in a wave tank in Glasgow.
“This is the lightest 1 to 60 scale floating wind model I’ve ever tested,” said Dr. Saishuai Dai, project leader at the Kelvin Laboratory of Hydrodynamics. “The model successfully passed a stormy sea condition with an equivalent full-scale significant wave height of 18 meters. A 30-meter full-scale equivalent maximum wave height was observed in this stormy sea state, and this pushed the upper limit of our waveguides.”
Since the structure does not extend very far underwater, deployment is a simple matter. You can collect these items at the dock, put them directly in the water, and then tow them back to their place. The service is pretty much the same; unhook the turbine, tow it back to shore, do any necessary maintenance, and then when you’re done, replace it back to spin the wind farm. No need for lift ships or cranes, you just tow the turbines back to port where it’s easy.
Cheap
“We’re going for cheap, cheap, cheap,” Papadopoulos says. “And part of our game is that we’re not going to aim for 25 years without maintenance. We’ll replace parts after three years if they crack because we’ve made it easy. Conventional turbines are insanely expensive to maintain - you have to hire a tower ship for two or three million pounds a week, and even then that’s only possible in brilliant weather. They’re waiting until two or three can justify the cost of that ship – and to avoid that, they build them to last forever. This is one of the reasons why they are so expensive. They want perfection in their design. We don’t want that. Prices work much better.”
While almost every other offshore wind company aims to scale up endlessly with bigger and bigger turbines, T-Omega says its economic advantage will be about half that of today’s largest turbines. “Everybody seems to like the idea of scaling up,” Papadopoulos says, “but we hate the idea of huge size because that means you need bigger ports, bigger ships, bigger everything.”
And, he says, T-Omega’s proposition is fundamentally different.

Lowest cost
“Why do they get so big?” - he asks. “What happens is that the costs to install and maintain these turbines are so crazy that it’s better to install and maintain one giant one than two medium-sized ones. But these costs do not apply to us. And there is something called the square cube law; when you double the size of the turbine structure, you quadruple the area covered by the rotor – but the weight increases eightfold, because you double the height, width and length of each part in three dimensions. So it’s actually a losing proposition to get too big for us. We’ll probably find our sweet spot with the lowest cost somewhere around 7-8 megawatts.”
In internal calculations, the company forecasts a levelized cost of energy (LCoE) of around US$50 per megawatt hour. We are working to have this metric reviewed by an independent third party.
“According to our numbers,” says Papadopoulos, “we are in the best fixed-bottom offshore wind farm available today.”
Manufacturers
At the moment, T-Omega is a small group of people who work without pay and finance prototypes through grants and accelerators.
“We’re just starting to look seriously for investment,” says Papadopoulos, “we think this could be the most versatile, easy-to-build, cheapest floating wind turbine ever proposed. So why wouldn’t everyone want it? Maybe it’s naive!”
Indeed, there are some other massive market forces on the way.
“We went to show it to a company that makes some of the biggest turbines in the world,” says Papadopoulos. “We talked to the former CEO, a guy who really knows the business. We showed him our design. He said enthusiastically, it is really a great design. Everyone needs it. This will make maintenance easier. This will facilitate construction and make it easier to install. This is a great thing. I give you zero hance of success.’ And we looked at him with dejection and asked why. And he said, “Well, because just before I left, we had just invested three or four billion in doing things the old way. Do you think we want to throw this factory out?” So the big turbine manufacturers are not interested, they want to keep selling what they are doing now.”
Therefore, T-Omega’s challenge is to find manufacturers that are not tied to old technologies. Papadopoulos says the company has several connections with investors, but has yet to close a deal that could fund the next step: a 100-foot-tall project that could eventually become a product for small coastal communities and islands.
“We’re in the early stages of trying to prove that the ideas are good and workable,” he says. “With more evidence, you get more investment until it’s a real product.”
NORTHERN CARNARVON BASIN, WESTERN AUSTRALIA
Joint venture awarded greenhouse gas assessment permit in WA
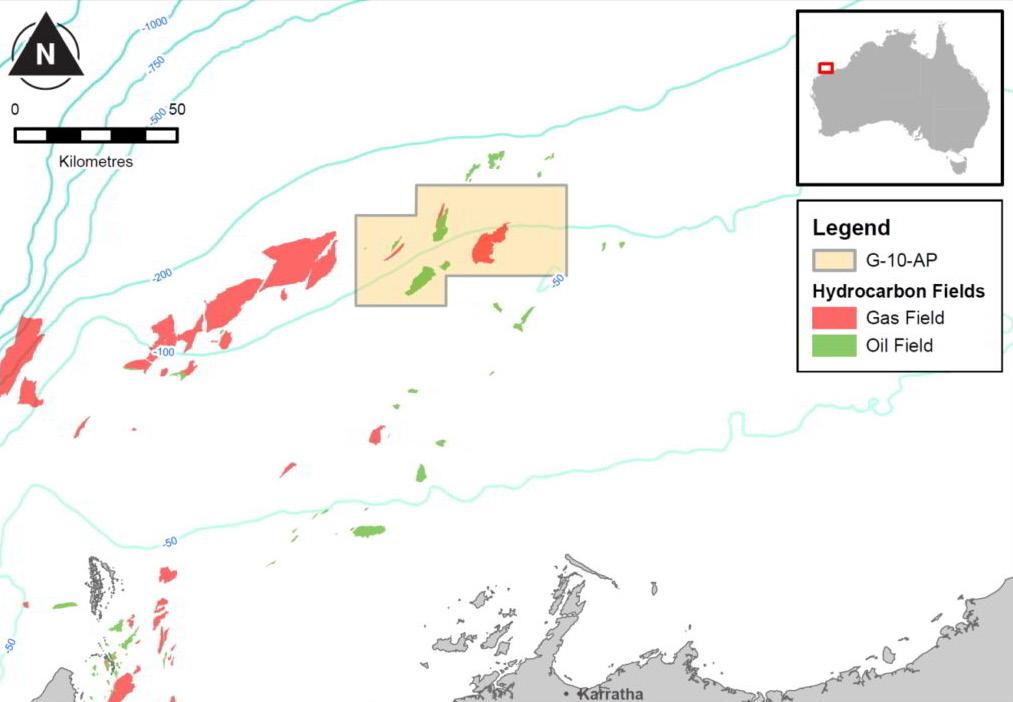
Woodside Energy (Woodside), BP Developments Australia (bp), Japan Australia LNG, which is owned equally by Mitsubishi Corporation and Mitsui & Co., Shell Australia and Chevron Australia, collectively referred to as the Joint Venture, have been awarded the greenhouse gas assessment permit (G-10-AP), located in the Northern Carnarvon Basin off the north-western coast of Western Australia.
The Permit, which is located approximately 125 km north-west of Dampier and covers an area of 1775 km2, contains the depleted Angel Gas Field. The Joint Venture has extensive existing data and knowledge of the field following decades of petroleum exploration and production.
The permit award represents an important milestone for the Joint Venture as it continues to assess the technical, regulatory and commercial feasibility of capturing carbon emitted by multiple industries located near Karratha in Western Australia. The Joint Venture will now pursue evaluation and appraisal work to investigate the potential for the geological storage of carbon dioxide in the Permit area.
A multi-user carbon capture and storage (CCS) project near Karratha would be ideally located to aggregate emissions from various existing sources. It would also have the potential to facilitate the development of new lower-carbon industries, such as the production of hydrogen and ammonia, by providing a local solution for emissions.
The size of the CCS facility is subject to the completion of additional technical, regulatory and commercial studies, but notionally it could have a processing capacity of up to 5 million tonnes of carbon dioxide per annum.
Woodside CEO Meg O’Neill welcomed the award of the permit as another key step towards the development of a pioneering, multi-user CCS project near Karratha.
“The successful deployment of CCS in Western Australia has the potential to create new jobs, protect current jobs and contribute to achieving greenhouse gas (GHG) emission reduction targets. For Woodside, it will be an important addition to our portfolio of carbon management options, as we work towards our own aspiration of net zero by 2050,” she said.
MIMI Managing Director and CEO Hiroyuki Kurahashi said: “MIMI is pleased that the Permit was awarded to the Joint Venture and we are excited to work with our partners in contributing to the environmental solution by helping to manage and reduce CO2 emissions through this multi-user CCS project.”
bp Vice President Australia Gas and Low Carbon Energy Rachael Risucci, said: “This is a fantastic opportunity for bp, working alongside our joint venture partners, to leverage our deep global expertise and explore the establishment of a large-scale, multi-user CCS hub to help decarbonise hard-to-abate sectors, and underpin Australia’s energy transition.”
Shell Australia Country Chair Tony Nunan said: “At Shell, we believe carbon capture and storage will be essential for helping society achieve net-zero emissions, particularly for sectors of the economy that are hard to decarbonise. Based off the coast of Western Australia, the project will support both the Western Australian and Australian economies as they transition to a low-carbon future, and Shell is pleased to be working in collaboration with our partners and government to play a role in that.”
Chevron Australia Manager Director Mark Hatfield said: “Chevron has a unique set of capabilities, assets, and customer relationships to support the further deployment of carbon capture and storage in Australia. Collaboration within the industry, as well as with government and customers, is going to be key in the development of this critical emissions reduction technology and we look forward to working with our joint venture partners as we investigate the potential of this permit area.”
Woodside, bp, MIMI, Shell and Chevron will each hold a twenty percent (20%) participating interest in the Permit, with Woodside as Operator.