
3 minute read
Building By Machine
Affordability is just one bonus of prefab construction
As builders search for ways to lower costs while maintaining quality, digital and fabrication advances have renewed interest in factory-built housing.
Today’s prefabricated homes have shed the stigma that regarded them as technically inferior to conventionally constructed units. In Japan, for example, one-third of all newly built homes are made in a factory.
The rising prefab trend can be attributed to their financial, environmental, structural and time-saving advantages. Further, constructing houses in a factory negates problems such as vandalism, material storage and weather delays. Factories also require fewer skilled workers, reducing labour costs.
And since the construction of an average house produces 2.5 tons of waste—25% of which is dimensional lumber, and an additional 15% being manufactured wood products—there are also the cost savings that come from improved efficiencies.
Prefabricated panel systems offer superior quality based on three interrelated characteristics: craftsmanship, technical performance and durability. The system’s craftsmanship governs its potential for consistent performance levels from one application to another.
How might such projects look?
The FAB House, designed by TDO Architecture and architect George Clarke, is a 10-unit townhouse project in North Fields, UK. It was commissioned by joint venture developers Urban Splash and Places for People in a master plan to revitalize Smith’s Dock (a former shipyard) into an urban neighbourhood to include two rows of five townhouse units.
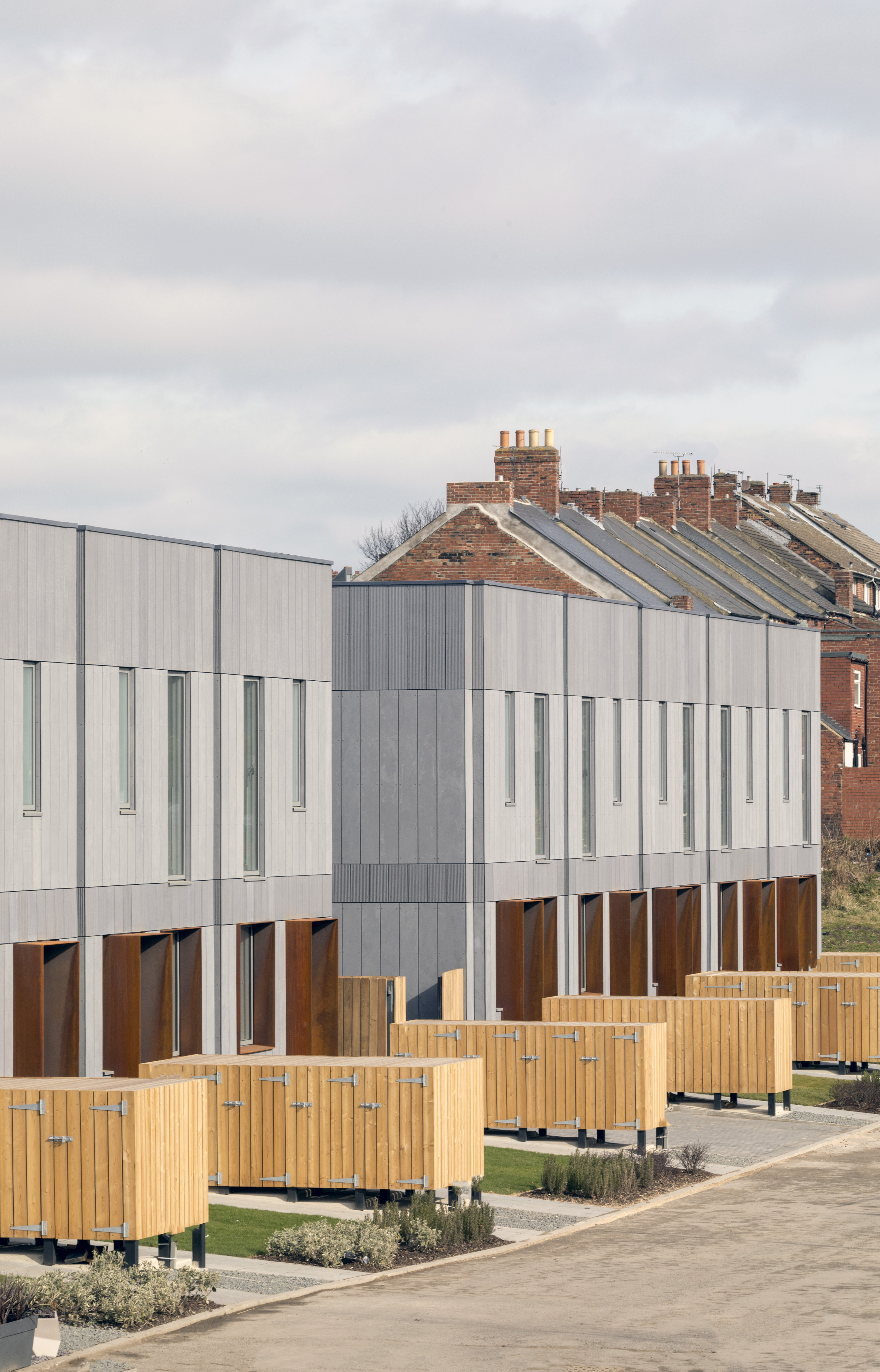
The townhouses adopt an open floor plan for the living spaces on the first floor. The entryway adjoins the kitchen, which leads to the dining area and then to a large living area at the back of the house.
Exposed ceiling joists are especially noticeable, with raised ceiling heights of 9.5 feet contributing to the home’s spacious feel. The materiality of the timber joists adds character to the space while also becoming part of a cohesive material scheme along with the birch-faced plywood staircase.
The stairwell is lit by a large skylight running lengthwise while floor-toceiling windows can be found in the reception space and the primary bedroom. The large amount of natural light makes rooms appear larger, especially on the second floor, where the space is divided into two main bedrooms and one kids’ bedroom.
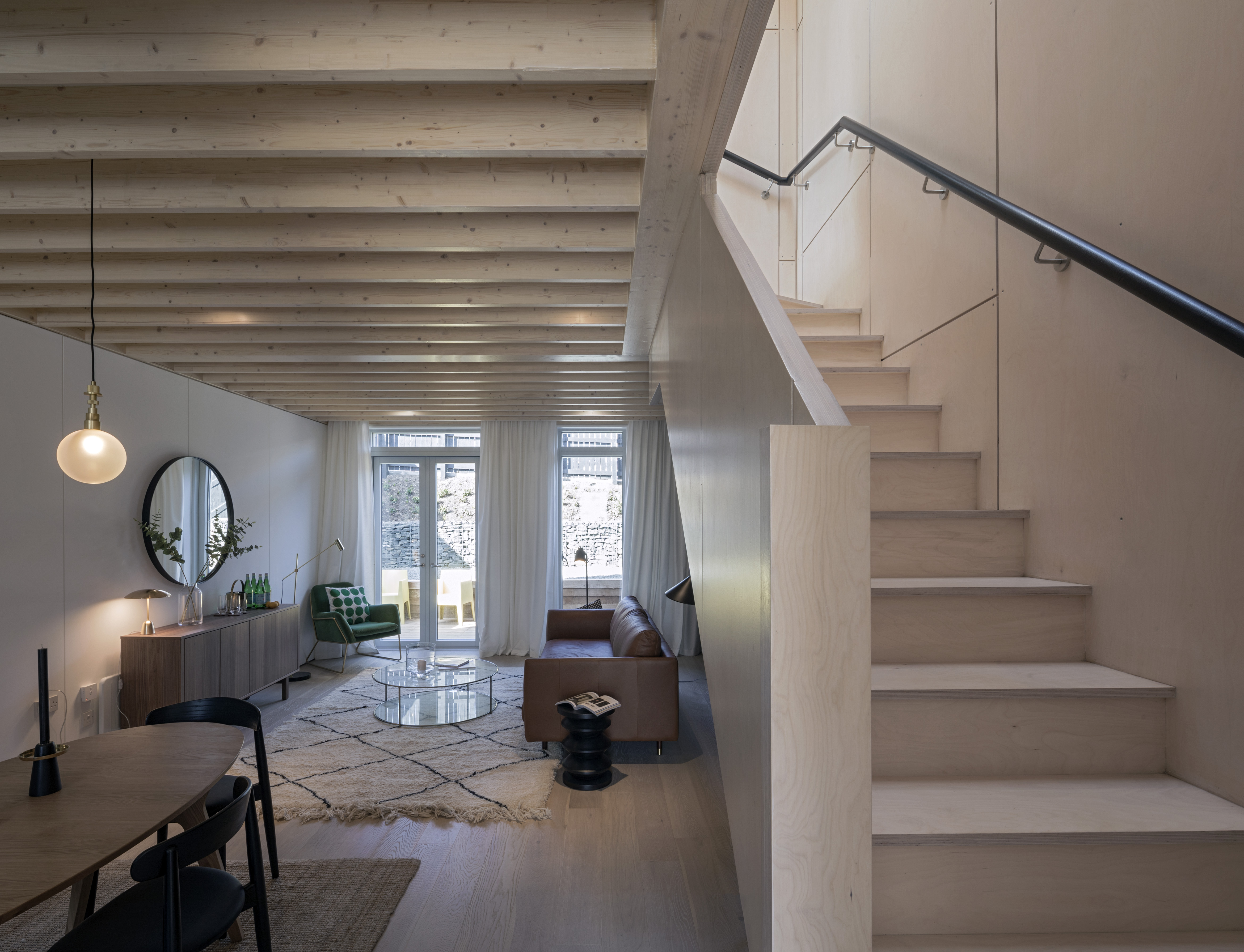
For the exterior, TDO Architecture references the site’s industrial heritage through the materiality of the facades by using a dark grey Equitone panel cladding combined with shrouds of COR-TEN steel.
The modules of the FAB House were fabricated in an off-site facility in collaboration with manufacturer SIG to minimize the effect of site conditions and maximize productivity. Each unit measures 5m wide and 11m deep, per size restrictions for transportation of the modules.
The cladding system design features a central alignment to facilitate assembly for the contractors, who would only need to align two instead of four claddings. The central alignment is also present in windows and doors. The cladding conceals a zone for services connected externally on site.
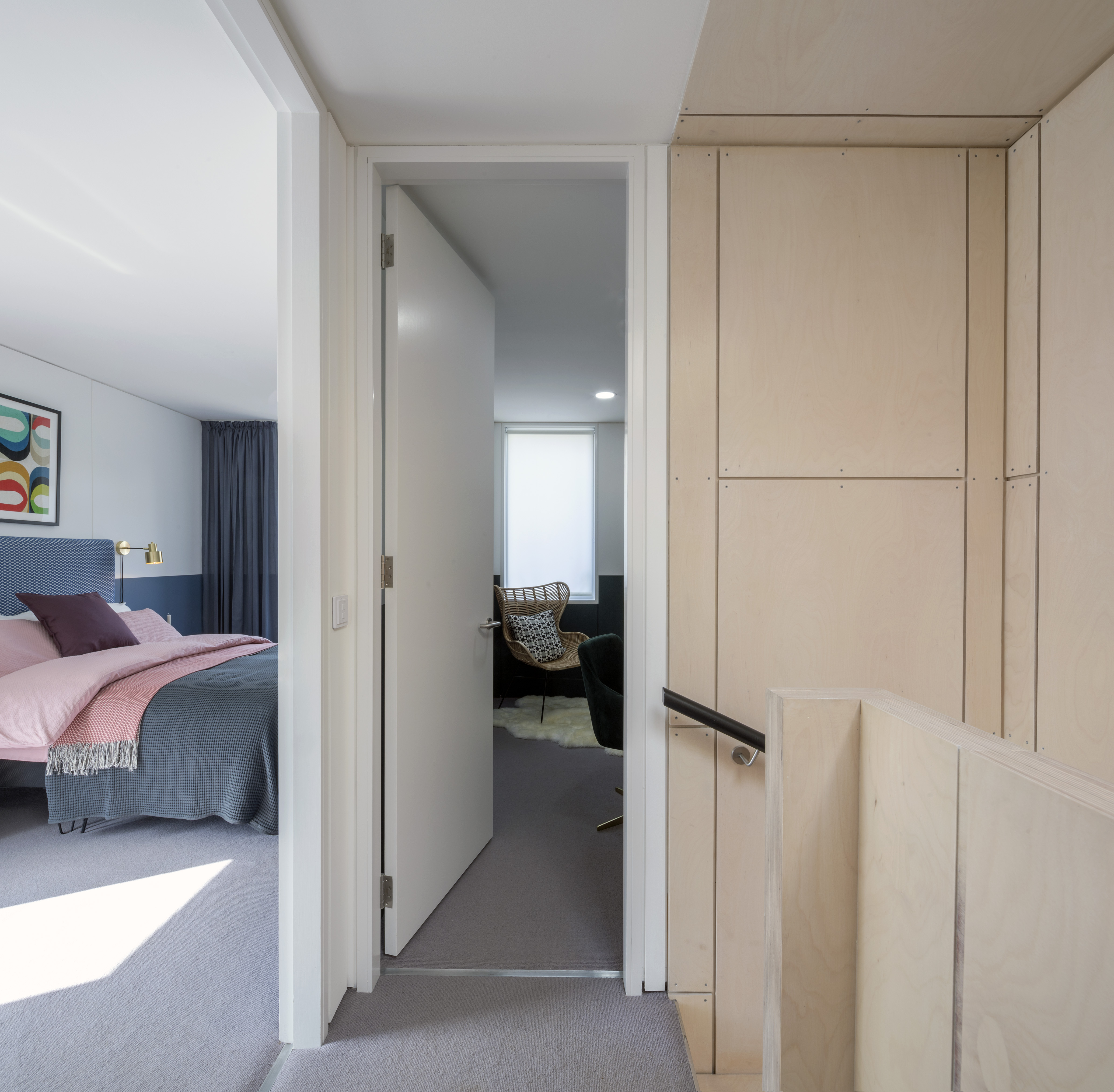
The FAB House marks an innovative development into the application of prefabrication for affordable housing on a larger scale—specifically, how it can be used to increase efficiency in production but maintain the spatial and living qualities of a more traditionally designed home.
AVI FRIEDMAN IS AN ARCHITECT, PROFESSOR, AUTHOR AND SOCIAL OBSERVER. AVI.FRIEDMAN@MCGILL.CA