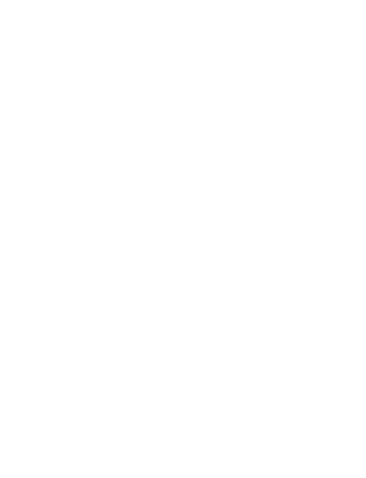
4 minute read
to Other Hazards
SAFETY FIRST How to Apply your COVID-19 Safety Plan to Other Hazards
By: Workplace Safety & Prevention Services
Akey tool in the Ontario Government’s COVID-19 Response Framework is a requirement for workplaces to develop a safety plan. The plan’s goal is to prevent transmission of the virus.
The process is straightforward: a safety plan template created by the provincial government poses six questions. Your answers to the questions form your plan.
It’s simple and effective, but the benefits don’t end there. Having developed a safety plan for controlling one workplace hazard, you can apply the same process to other hazards.
“A COVID-19 safety plan is just one element of a broader workplace safety program,” explains WSPS Consultant Alyson Smith. “The six questions it asks are based on the RACE principle for Recognizing, Assessing, Controlling, and Evaluating hazards, which is the basis of an effective safety program.”
The questions help workplaces recognize where transmission of COVID-19 could occur, assess the likelihood of transmission, implement effective controls, and review the controls to make sure they’re effective.
Ship with the experts in temperature-controlled, time-sensitive Food transportation

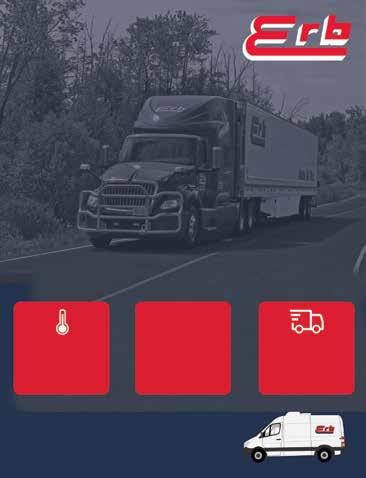
TRANSPORTATION - Temperature Controlled - Truckload - Less than Truckload
COLD STORAGE - Multiple Locations - HACCP Certified - Sorting & Labelling
cHECK OUT OUR NEW ONLINE GROCERY MARKET: ERBANMARKETPLACE.COM
EXPEDITE SERVICES
- Home Delivery - Dedicated Services - Store Door Distribution Here’s an example of how you could adapt those questions to the potential hazards of using a new chemical in your workplace.
1. How will you ensure workers know how to keep themselves safe from exposure to the chemical?
• Determine the hazards before bringing the chemical into the workplace by obtaining the Safety Data Sheet (SDS) from the supplier. “This is a fantastic resource for understanding the properties of the chemical, including physical and chemical properties, handling and storage requirements, stability and reactivity, and first aid measures,” says Alyson. • Assess the risks of exposure. How and where will workers handle and use the chemical? What is the likelihood of chemical exposure or an incident occurring? Are potential exposure levels within legislated limits? • Determine what prevention measures to put in place. (See question 3.) • Develop and document safe operating procedures that cover the hazards, use and handling, storage, controls, first aid requirements, emergency response, etc. • Communicate the procedures to all applicable personnel and document the training.
2. How will you evaluate worker understanding?
• Ensure supervisors monitor the way workers handle and store the chemical. • Ask workers questions about the chemical to confirm their understanding. Also ask if they have any concerns or suggestions for reducing the level of risk. • Consider providing a proof of comprehension test during the training to confirm understanding and demonstrate due diligence.
3. How will you control hazards associated with the chemical?
Use the hierarchy of controls to determine the best combination of measures to protect workers. For example: • elimination - can you avoid using the chemical entirely? • substitution - can you replace the chemical with something less hazardous? • engineering controls - do you need to increase ventilation in the area where the chemical will be used? • awareness controls - do you need a visual or audio system to warn workers of the hazard? • administrative controls - how you will provide information, training, safety signage and supervision?
• personal protective equipment - do workers need to wear or use anything to reduce contact? Again, check the SDS and review how the chemical is used.
4. What will you do if suspected exposure to the chemical occurs in your workplace?
• Develop first aid procedures and train responders. “If the exposed worker needs to see a medical professional, send along a copy of the SDS,” says Alyson.
5. How will you manage any new risks resulting from changes you made when introducing the chemical?
• Prioritize risks based on the likelihood and severity of exposure, determine which control(s) are most effective, and ensure they are working as intended and have not created a new hazard.
6. How will you make sure your plan is working?
• During monthly inspections, have your joint health and safety committee (JHSC) or health and safety representative observe workers as they handle and store the chemical. • If a worker reports a near miss, or an incident occurs that involves the chemical, review your program and training. • Ensure that workers’ understanding of the chemical and how to use it safely matches the training provided and is sufficient to protect them from a potential incident.
Get more information and resources
• Join the WSIB Health and Safety Excellence program to help you implement policies and procedures for a variety of hazards. • Check out the following resources: • hazard assessment resource page, where you’ll find downloadable forms, eCourses, articles and consulting services • Small Business Centre for a roadmap to controlling hazards in your workplace.
About Workplace Safety & Prevention Services (WSPS)
Workplace Safety & Prevention Services (WSPS) is a not-forprofit organization committed to protecting Ontario workers and businesses. A proud partner in Ontario’s occupational health and safety system and a trusted safety advisor since 1917, WSPS has a rich history of making Ontario workplaces safer. WSPS serves the manufacturing, agricultural and service sectors. For more information visit WSPS.ca.
Workplace Safety & Prevention Services 5110 Creekbank Road Mississauga, ON L4W 0A1 (877) 494-9777 customercare@wsps.ca wsps.ca
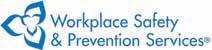
WHAT’S ON YOUR GRILL THIS SUMMER?
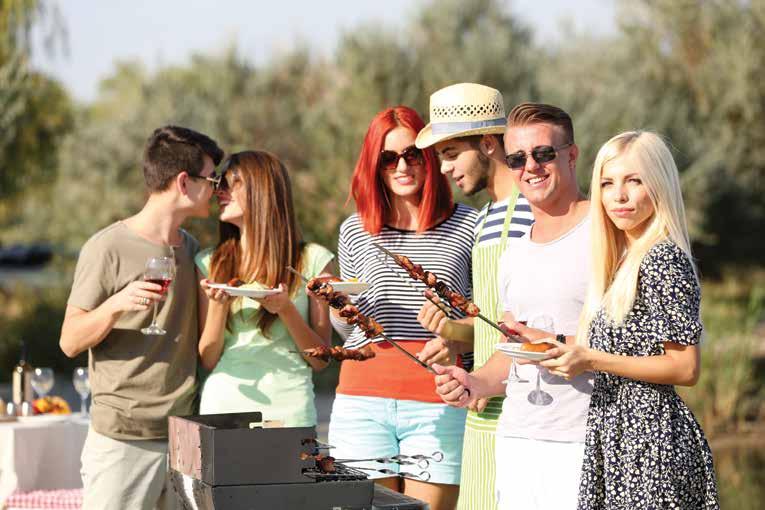
