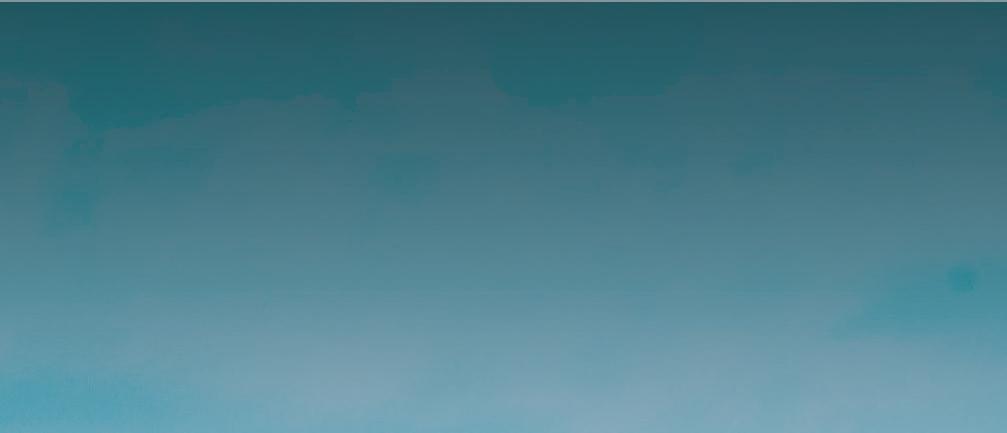
6 minute read
Editor’s Note
Carroll Smith
Goodbye To The Grinch
If I had to put a face on the pandemic, it would be a big, green, ugly Grinch with a furrowed brow and villainous eyes. Two years ago, it sneaked into the lives of people around the world and took away so many things we hold dear to our hearts — even those of the mundane everyday kind. It caught us off guard.
Our first reaction was to retreat and contemplate what had happened. As the days and months went by, we found ways to adapt in our personal and business lives. It was awkward, but it was doable.
Then we began to realize the one thing the greedy Grinch couldn’t get his hands on was the resilience of the human spirit. “Necessity is the mother of invention” moved up in status from “old cliché” to a motivating force with which to be reckoned.
It comes as no surprise that the concept aptly describes the agricultural world. This community of innovators is always up for a challenge. Examples of their creative spirit are sprinkled throughout this issue of Cotton Farming. As Missouri cotton farmer Allen Below told me during our interview, “A farmer and a ginner can always come up with some kind of contraption!”
This year, he bought a new John Deere CP770 harvester and was running it through his fields for the first time. In “Pickin’ And Ginnin’” on page 12, Below and his picker operator, Josh Morgan, discuss different aspects of the newly designed machine. But being a ginner as well as a farmer, Below has already turned his thoughts to how the bigger, denser round bales can be transported and then handled efficiently at the gin. He is formulating ideas to make sure everything goes smoothly once the cotton leaves the field.
Although Below was contemplating mechanical situations, the same holds true to developing solutions for something intangible. For example, the Grinchiness of the pandemic is still evident in agricultural supply chain issues. On page 9, Gary Adams, National Cotton Council president and CEO, talks about the organization’s efforts to find “remedies to an economically debilitating supply chain situation.” The NCC’s recommendations to the Biden administration are not just vague ramblings, they contain specific ideas to bring relief.
I challenge you as members of the agricultural community to keep fighting the good fight to overcome the hopefully temporary adversity we are facing. As we are about to embark on a new year, it’s time to say goodbye to the Grinch.
Carroll
Cotton Farming
EDITORIAL/PRODUCTION
Editor Carroll Smith csmith@onegrower.com Managing Editor Vicky Boyd vlboyd@onegrower.com Southeast Editor Amanda Huber ahuber@onegrower.com Art Director Ashley Kumpe
ADMINISTRATION
Publisher/Vice President Lia Guthrie (901) 497-3689 lguthrie@onegrower.com Associate Publisher Carroll Smith (901) 326-4443
Sales Manager Scott Emerson (386) 462-1532 semerson@onegrower.com Production Manager David Boyd dboyd@onegrower.com Audience Services Kate Thomas (847) 559-7514
For subscription changes or change of address, call (847) 559-7578 or email cottonfarming@omeda.com
EDITORIAL ADVISORY BOARD
David Burns – North Carolina David Lynch – South Carolina Bob McLendon – Georgia Larkin Martin – Alabama Mike Sturdivant Jr. – Mississippi Charles Parker – Missouri Jimmy Hargett – Tennessee Allen Helms – Arkansas Jay Hardwick – Louisiana Ronnie Hopper – Texas Ron Rayner – Arizona John Pucheu – California
ONE GROWER
PUBLISHING, LLC
Mike Lamensdorf President/treasurer
Lia Guthrie Publisher/Vice President
ACKNOWLEDGEMENT OF COOPERATION: Cooperating with COTTON FARMING are various cotton producer organizations across the Cotton Belt. Many representatives of producer organizations serve on COTTON FARMING’s editorial advisory board. Opinions expressed and conclusions reached by contributors are not necessarily those of the cooperating organizations or the editors. All statements, including product claims, are those of the person or organization making the statement or claim. The publisher does not adopt any such statement or claims as its own and any such statement or claim does not necessarily reflect the opinion of the publisher. Copyright 2021 © ASSOCIATED PUBLICATIONS – One Grower Publishing, LLC also publishes RICE FARMING, THE PEANUT GROWER, SOYBEAN SOUTH and CORN SOUTH.
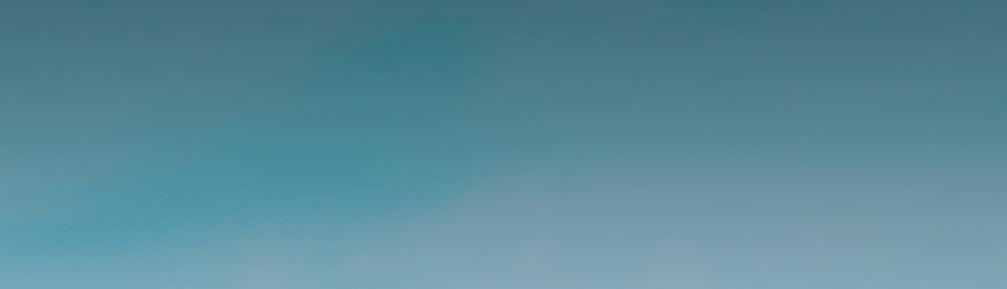
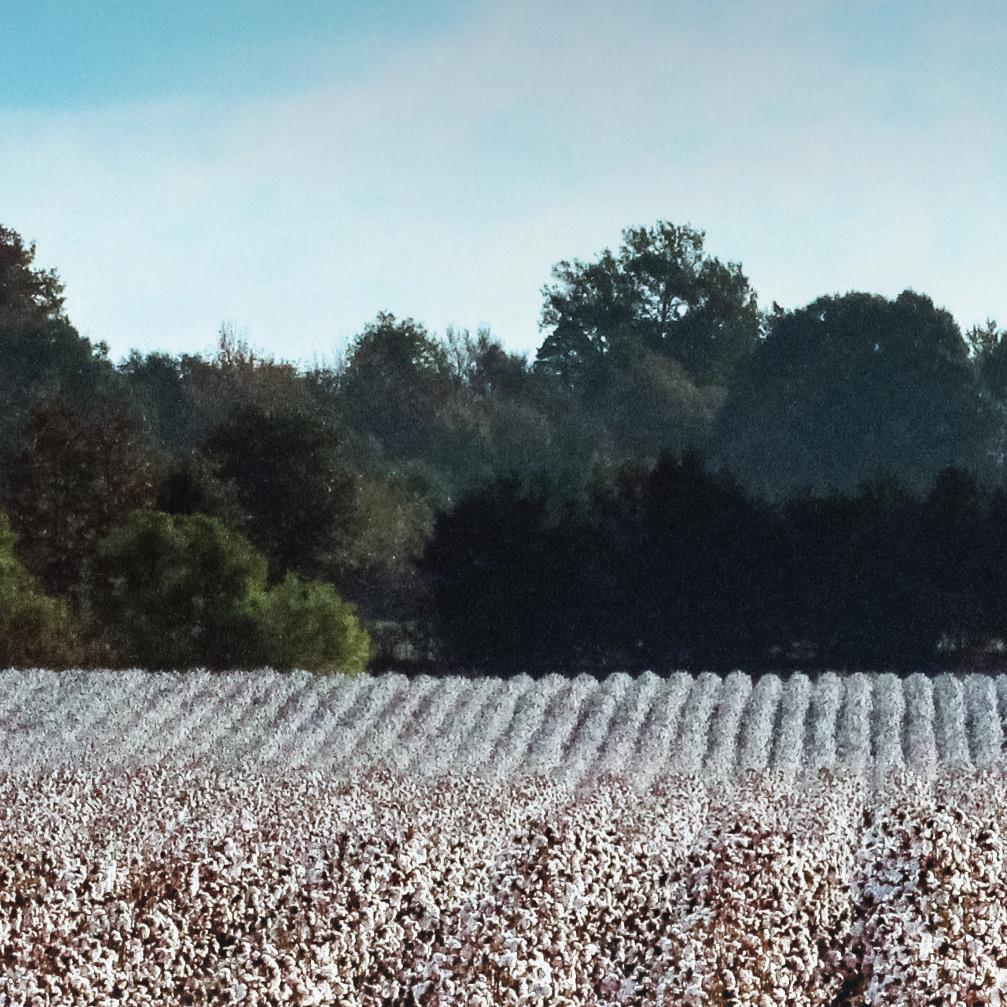


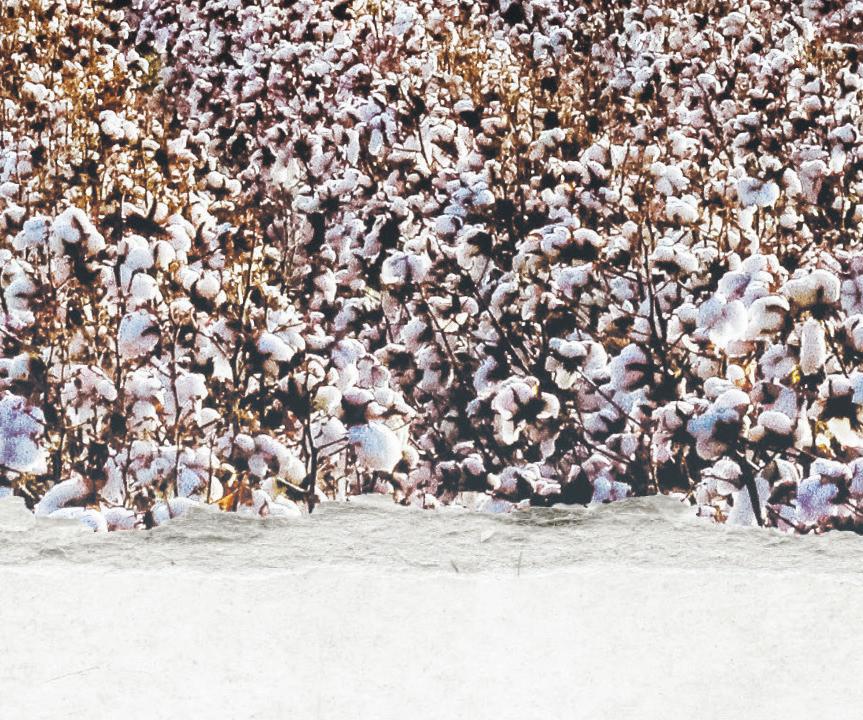
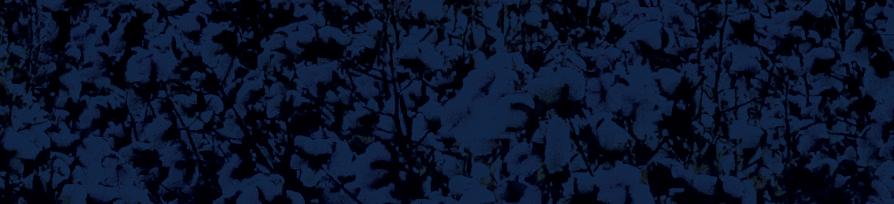

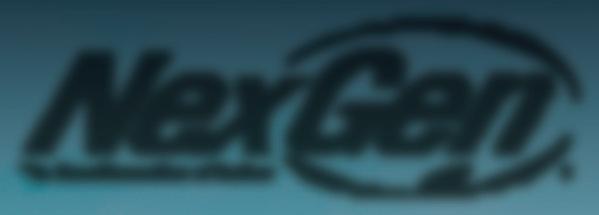

Transform Low-Quality Cotton Into A Plastic Alternative
How To Market Cotton Not Suited For Textile Processing
BY KAREN MICHAEL
TEXAS TECH UNIVERSITY
When cotton is abundant but the quality is low, farmers still need to sell the product.
Texas Tech University researchers are exploring ways to use cotton that may not be ideal for a shirt or jeans.
Noureddine Abidi is a professor in the Department of Plant and Soil Science and the director of the Fiber & Biopolymer Research Institute, or FBRI. One of the possible ways he has found to make a profit from low-quality cotton is in mimicking another product entirely. Researchers at FBRI have found a way to make a gel from low-quality cotton that can be formed into a product similar to plastic.
When handled, the smooth and pliable product looks and feels like the same plastic found in sandwich bags. It can also be made into thicker forms for other needs.
Normal plastic is a petroleum-based product. It does not decompose easily. But the benefit of using cotton for a similar purpose, such as the ubiquitous grocery bags overflowing from under the sink of almost every home, is that once the product is tossed in the trash and exposed to rain and soil bacteria, it will decompose.
“It is basically going from the soil to the soil,” Abidi says of that process.
The tricky part of using cellulose in cotton fibers to form a product is that it cannot simply be melted into the desired shape. Cotton fibers must be dissolved and molded in a gel form and film because cotton does not melt.
Discounted Cotton Market
Abidi says the new “plastic” was not developed to make a new cotton product necessarily, but as a way to make a product from low-quality, low-micronaire, cotton.
“We are not just going to tell cotton producers, don’t worry about cotton quality, just make fiber,” Abidi says.
There is plenty of demand for high- quality cotton from textile mills. However, growing cotton can be affected by Mother Nature. When cotton producers harvest cotton that is less desirable for textile processing, they need a place to sell it.
“We are still going to find a market for that,” Abidi says. “Every year, we have a good amount of cotton that is discounted. That is really what we are looking for.”
FBRI Labs
For many years, FBRI has been a leader in interdisciplinary, collaborative research with different entities within and outside Texas Tech. The FBRI labs provide valuable research and evaluation services to cotton breeders, researchers, producers and seed companies. They also provide opportunities for undergraduate and graduate students to perform their cotton research projects.
The FBRI facility, located off East Loop 289 in Lubbock, tests every aspect of the cotton fibers, from seed cotton ginning, to processing, spinning, dyeing and finishing.
“Everything is under one roof,” Abadi says. “We gin the cotton. We test for the quality. We spin, and then we form a small piece of textile product, either knitted or woven, and then we can test for the quality of that textile product. We can also do dyeing here, and we can also finish. Everything here is under one roof.
“I think we are the only one in the world going all the way from the seed to the final product. FBRI is becoming the premier institute to do this kind of work on cotton.”

Bioplastic, made from cellulose, can mimic petroleum-based plastic but will decompose when thrown away.
Karen Michael is a senior editor in the Texas Tech University Office of Research Development and Communications.