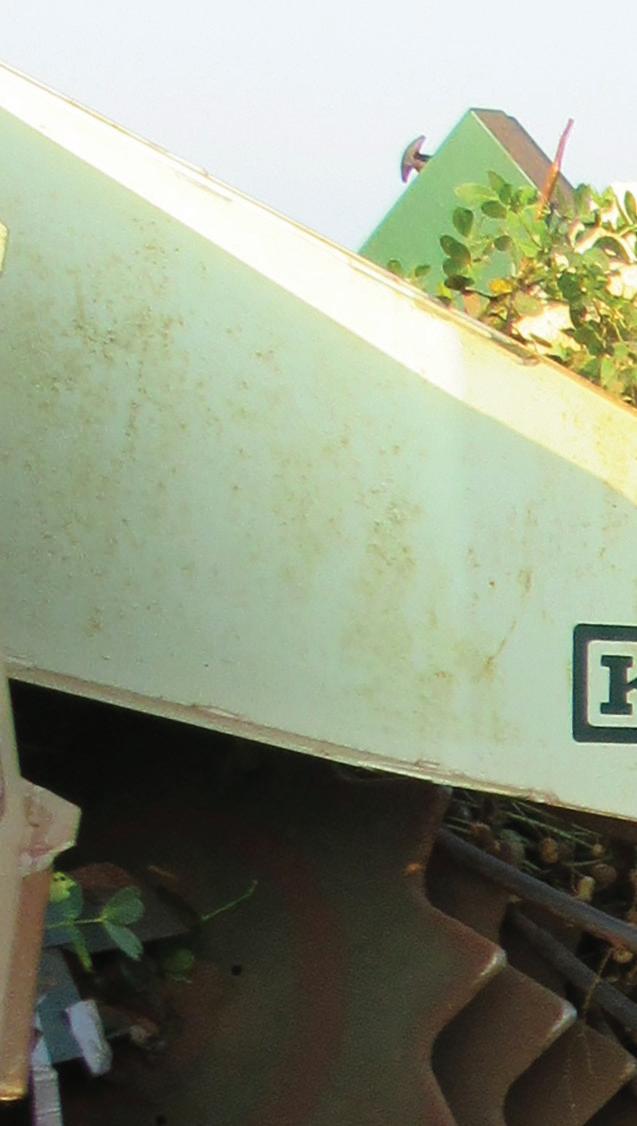
8 minute read
Harvest Preparations
Reduce yield loss at digging with proper equipment setup and maintenance.
By Amanda Huber
From before the first seed is planted until harvest, producers work diligently to provide all the inputs the crop needs and protect it from pests. Digging is carefully planned with the help of Extension and the maturity board. The same preparation should be given to digger setup and maintenance.
Prevent Mechanical Losses
Clemson University agricultural engineer Kendall Kirk says that the majority of peanut losses at digging are from weakened peg strength, disease and over maturity and mechanical actions of the digger. Reducing losses requires digging at the proper time and accurate equipment set up.
On the digger, the top link sets the angle of the digger blades. For clay soils, a more aggressive angle is needed. For sandy soils, set the blades for a less aggressive angle.
If the top link is too short, the soil will be dug too deep causing excessive soil on the blades and pushing the plants. If the top link is left too long, peanuts are dug too shallow and pods are sheared off and left in the soil.
Tractor speed is another factor in digging losses. Driving
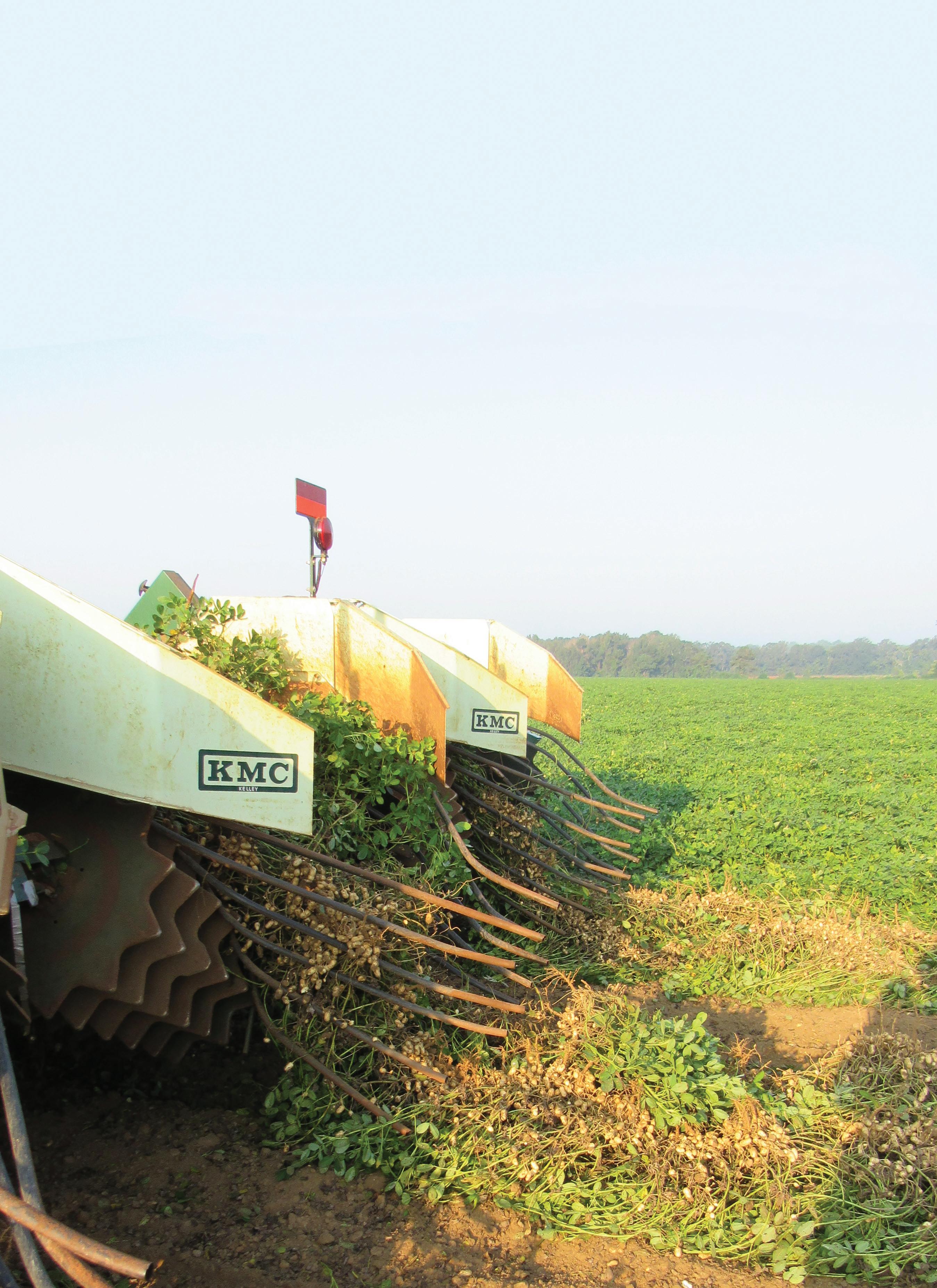
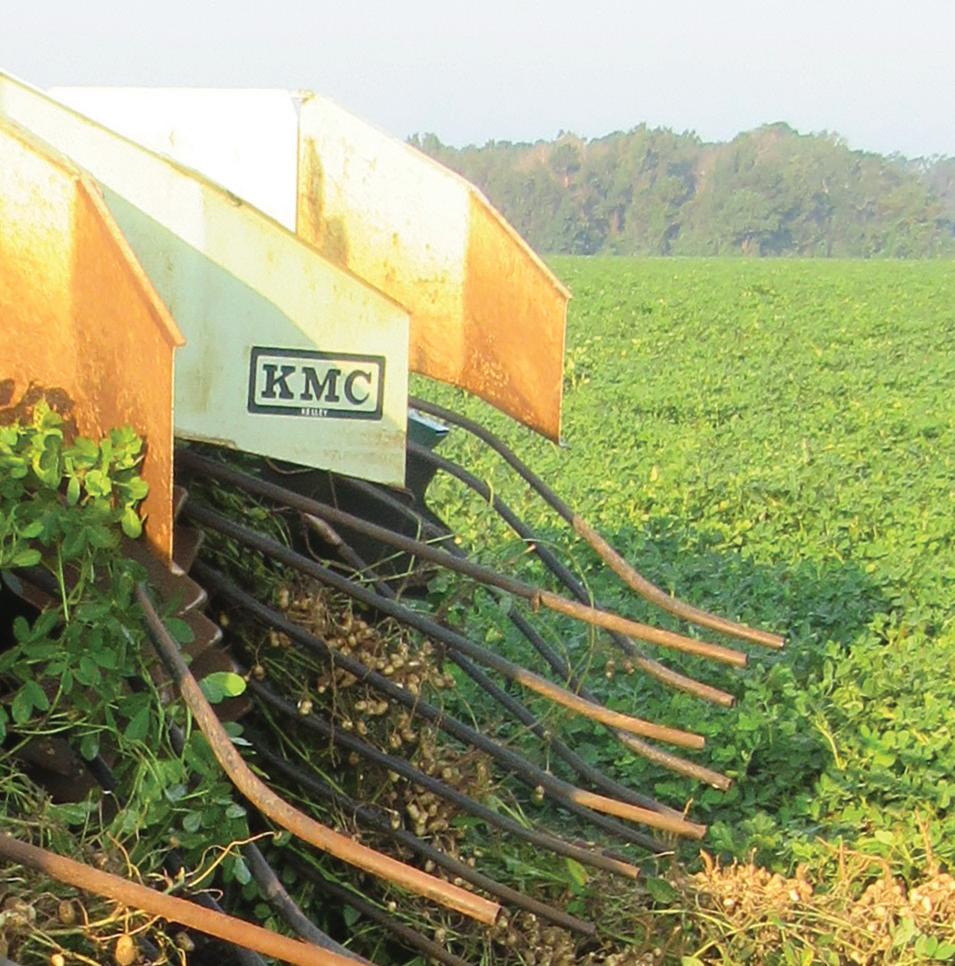
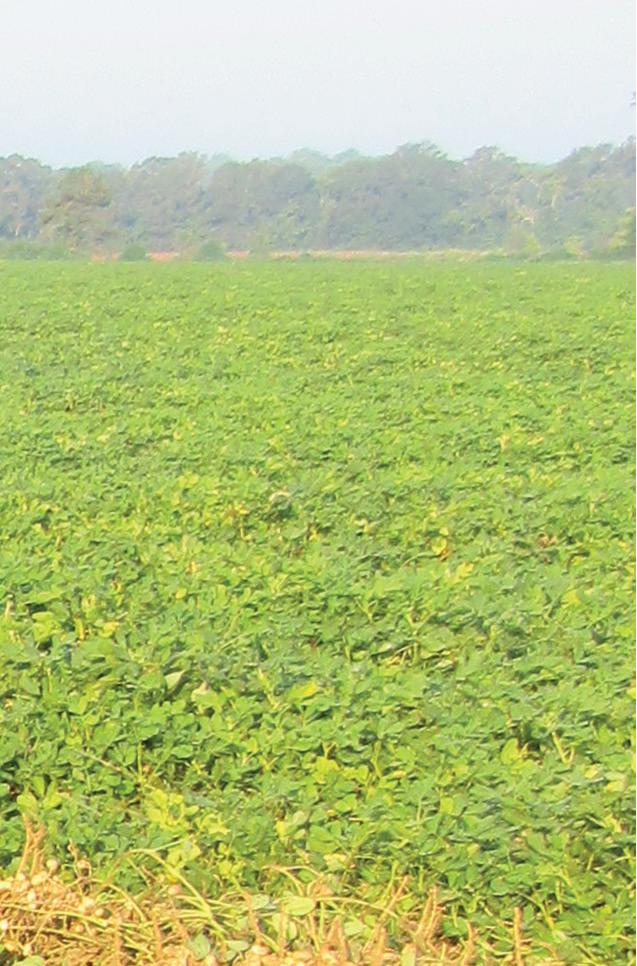
too fast causes the plants to bunch up, whereas driving too slowly leads to ripping the vines apart. According to his study, the optimal ground speed for digging Virginia peanuts is 2 to 2.5 miles per hour. For each mile per hour above that target speed, digging losses increased 200 pounds per acre.
Kirk also says growers should synchronize the speed of their digger’s shaker chain, or conveyor belt, to their ground speed. If driving 2 miles per hour, for example, the conveyor belt should be set to a speed of around 2 miles per hour. A conveyor belt running about 20% faster than ground speed can result in yield loss of 100 to 200 pounds per acre.
Look For Problems Prior To Operation
Before a speed can be selected, a thorough inspection of the equipment is a must. Inspect the digger-inverter for broken, bent or missing parts before making adjustments. Make sure the front tool bar is level with the tractor.
Stand at the rear of the machine with the implement raised and sight the top of the tool bar with the top of the rear axle. For accuracy, first be sure the rear tractor tires are inflated to the same pressure. If the tool bar is not parallel to the tractor axle, level the digger by adjusting the lift arm.
Next, inspect the blades. A well-adjusted digger will have sharp, flat-running blades set to clip taproots just below the pod zone where the taproot starts branching. Blades should run level, with a slight forward pitch to lift plants into the shaker. This adjustment can be accomplished best on a flat surface.
Excessive pitch of the digger blades may result in soil and pods being carried forward by the blade before being freed by the cutting edge. Such pods are usually lost. Dull blades cause most digging losses because they fail to cleanly cut the taproot and may drag the roots, dislodging pods from the plant.
Forming A Good Windrow
After plants pass over the digger blades, they are transferred onto the shaking conveyer. This should be set at a depth at which it picks up vines with its teeth just clearing the soil. Check the conveyer chain speed and depth. The chain speed should be set to avoid a pileup of vines ahead of the pickup point and allow a smooth flow of vines through the digger-inverter.
In the field, note the shaking action. It should be only enough to remove soil from the vines. More aggressive shaking is needed where soil clings to pods, roots and stems. The amount of shaking can be changed by adjusting knocker wheels up or down.
As vines exit the shaking conveyer, they engage the inversion wheels and rods. These rods are factory set; however, they will change position with use. Adjust the inversion rods before going to the field by placing the digger on a level surface and setting them according to the operator’s manual. Properly inverted peanut plants will form a uniform, well-aerated windrow with few pods touching the soil. PG
• Apply herbicides when weeds are small for maximum control. • Be timely with inputs, especially fungicides. • Keep up with irrigation needs, particularly during peak bloom and pod fill. • Apply gypsum for needed calcium unless lime was used at planting. • Know the insects likely for the weather conditions and scout often. • Consider using a weather advisory for leaf spot. • Maturity can be sped up or delayed depending on conditions. • Don’t dig based solely on days after planting or before a freeze or frost is forecast.
Factors Effecting Peanut Loss
1. Blade depth too shallow. 2. Dull blades that do not cut cleanly through the taproot. Pods will be lost if the plant is pushed through the soil. 3. Vine cutter springs too loose or coulters too dull. 4. Conveyor pickup running too high above the lifter rods. 5. Tractor RPM or hydraulic flow too fast. 6. Vine flow not synchronized with ground speed and conveyor speed. 7. Inverter not aligned with the row (indicated by tap roots leaning left or right).
For more information on harvesting equipment, consult your equipment owner’s manual or University of Georgia Extension publication “Peanut Digger And Combine Efficiency” at www.ugapeanuts.com.
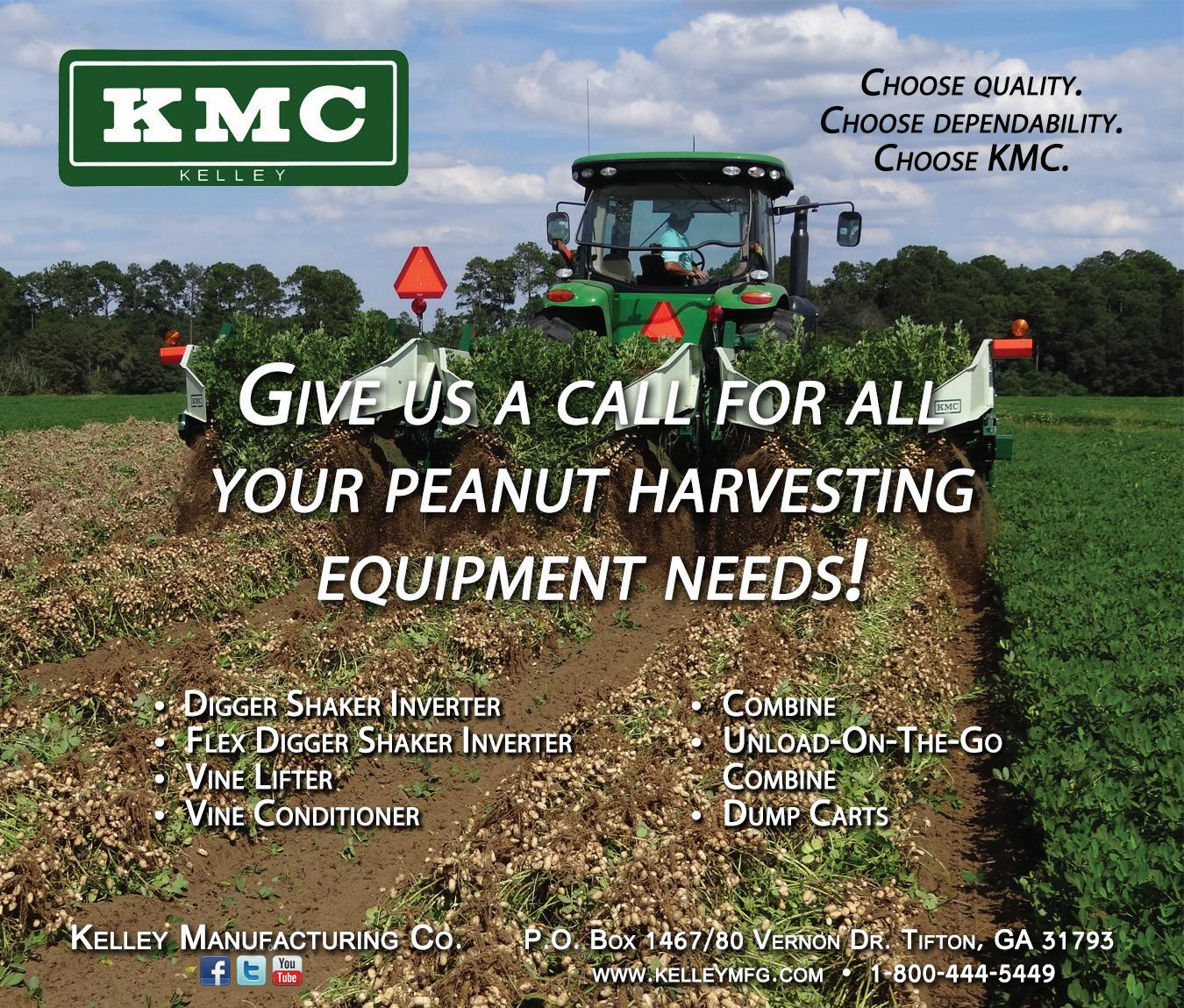
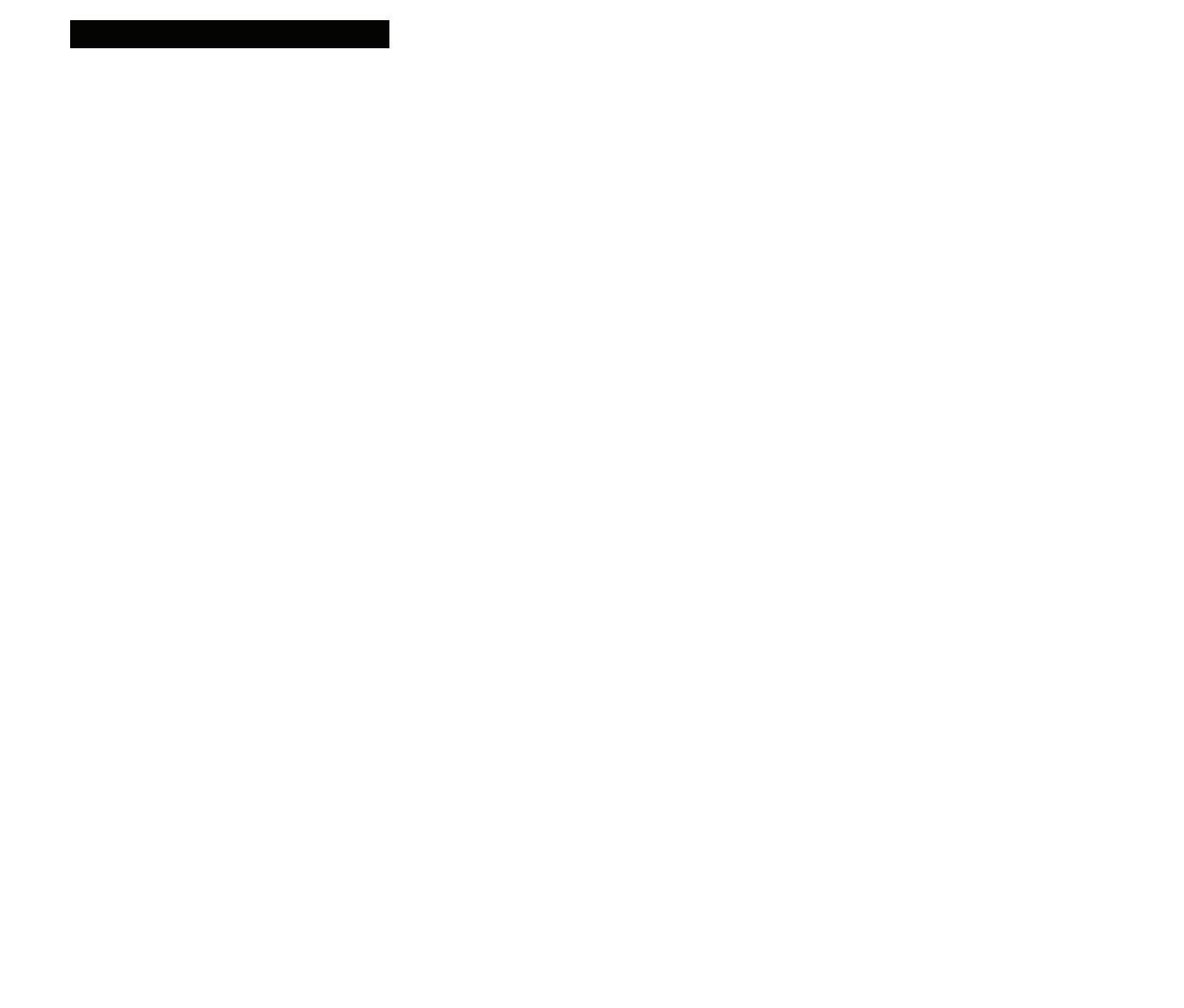
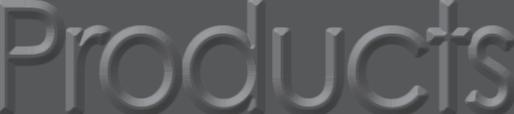
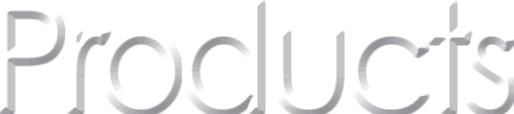

NewProducts
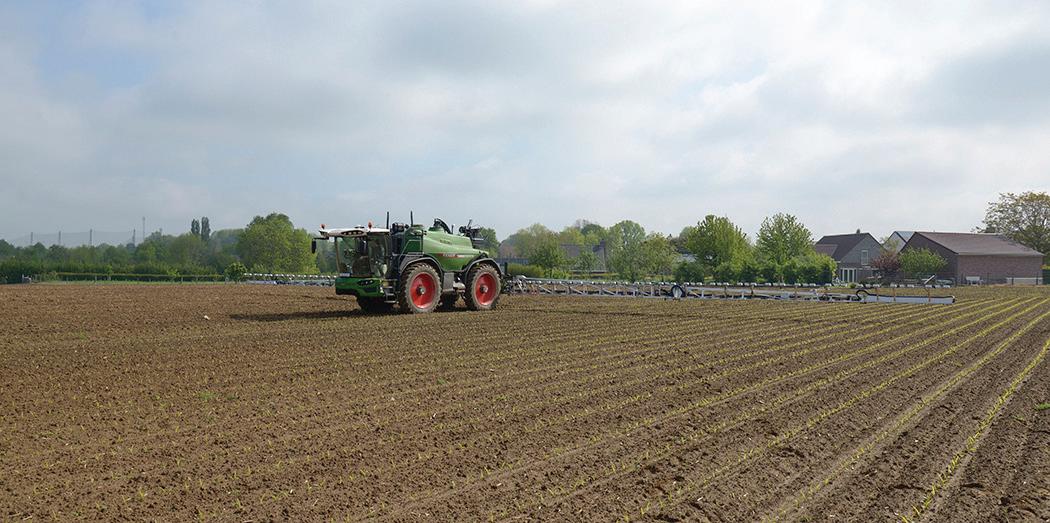
Collaboration To Evaluate Targeted Spray Technology
AGCO recently announced a collaboration with Robert Bosch GmbH, BASF Digital Farming and Raven Industries Inc. with the objective of evaluating targeted spraying technology. The goal is to make applications more effective and efficient by reducing crop input costs while driving farm and environmental sustainability.
Targeted spraying will focus on real-time sensing technology to make crop protection decisions. By detecting weeds in growing crops or fallow ground, day or night, this technology will execute precise targeted product placement to the individual plant level. Targeted spraying will also enhance farmer profitability by using herbicides only where needed. This makes the use of more efficient herbicides affordable, allowing for better weed control. Where optimal herbicides are already being used, the smart sprayer provides a volume and cost reduction.
The concept is being evaluated on a Fendt Rogator sprayer in Europe with plans to extend into North America in 2022.
“Farmers have been searching for ways to minimize chemical usage and reduce passes through the field to achieve crop protection goals. With the potential for further regulatory pressure, this effort advances our farmer-first focus and is evidence of our work to serve farmers’ needs,” says AGCO senior vice president and general manager for precision ag and digital Seth Crawford.
This collaboration will empower farmers to drive greater efficiency in their operations while helping to protect the environment through reduced chemical use.
Morton Buildings Introduces Concrete Splashboard
A new, patented concrete splashboard is now being offered by Morton Buildings to make post-frame buildings stronger and more durable by completely removing structural wood from touching the ground.
Morton Buildings President Sean Cain says the concrete splashboard offers a permanent solution compared to standard wood splashboards that have the potential to rot, decay or simply look worn over time.
The new splashboard is offered as an optional upgrade for most post-frame buildings that use the Morton Foundation System. That system consists of lower concrete columns that eliminate wood in the ground, avoiding natural decay and protecting against costly repairs. The splashboard is connected to the top of the columns, extending around the bottom of the building perimeter.
For additional information, visit mortonbuildings.com.
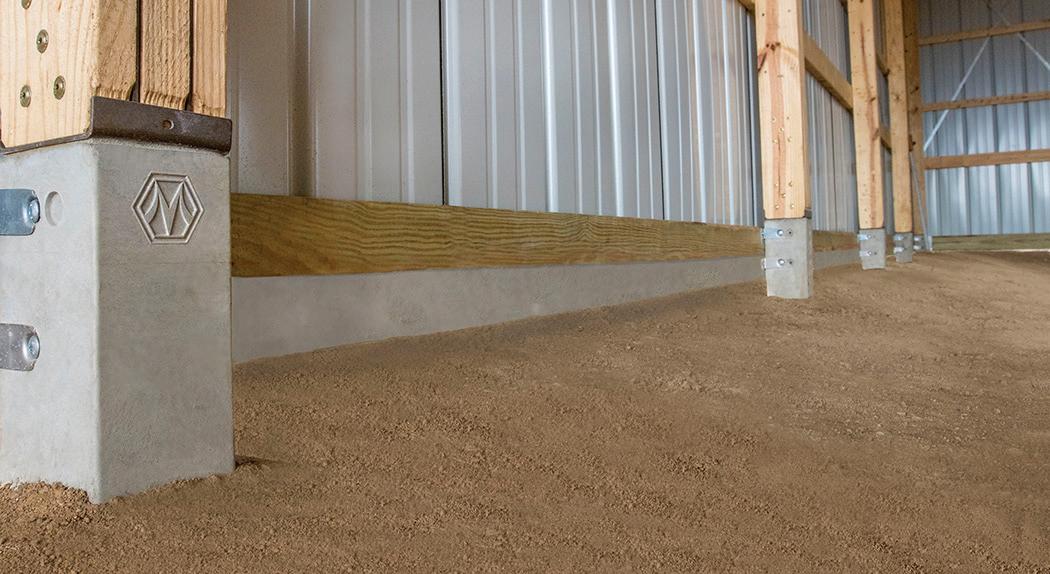
Case IH Introduces New Planter Technology, Applicator Configurations
New technology and configurations from Case IH will help producers match planting and product application to the unique needs of their fields.
Now available for 2000 series Early Riser planters, Case IH ISO Planter Control gives operators the ability to view high-resolution as-applied planting data in real time — all from one integrated display that is easy to navigate and customize. Plus, with the AFS Pro 1200 display, the technology delivers complete in-cab planter control, which can interact with multiple implements and machines, regardless of the equipment’s manufacturer.
With the ISO Planter Control and the AFS Pro 1200 display, farm managers gain important agronomic insight with the ability to view as-applied field maps down to the row level in the AFS Connect Farm platform on web and mobile. Plus, planter data can be easily shared with agronomic partners for additional analysis.
To help operators cover more ground in less time, Case IH is adding a new 90-foot boom option, the widest available, for the FA 1030 air boom applicator. The FA 1030 is also now available for either the Titan 3540 or 4540 floater models, with the choice of either three- or four-wheel configurations.
For more information about Case IH soil management, planting and application equipment lineups, contact your Case IH dealer or visit www.caseih.com.
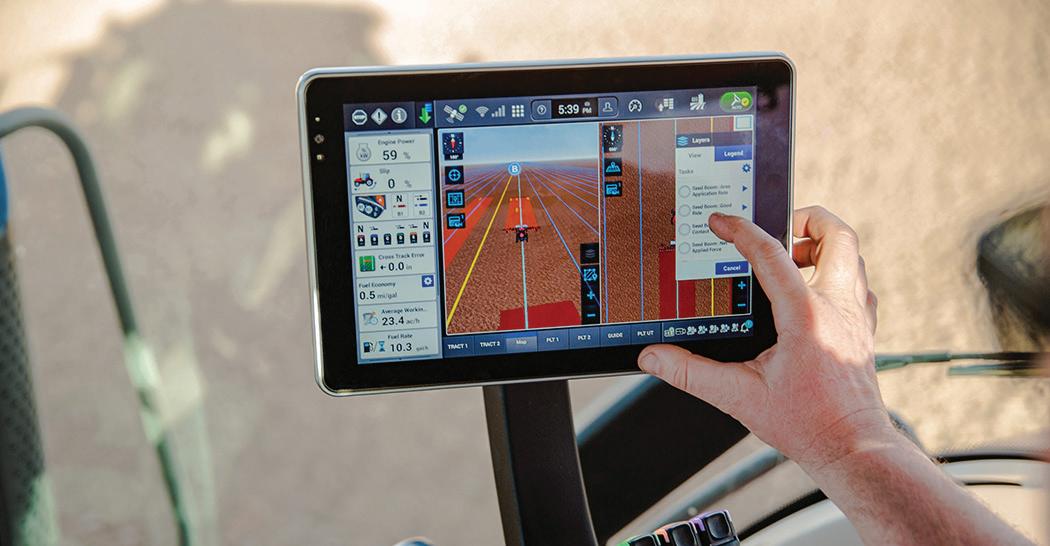
It’s not just what we do, it’s who we are.
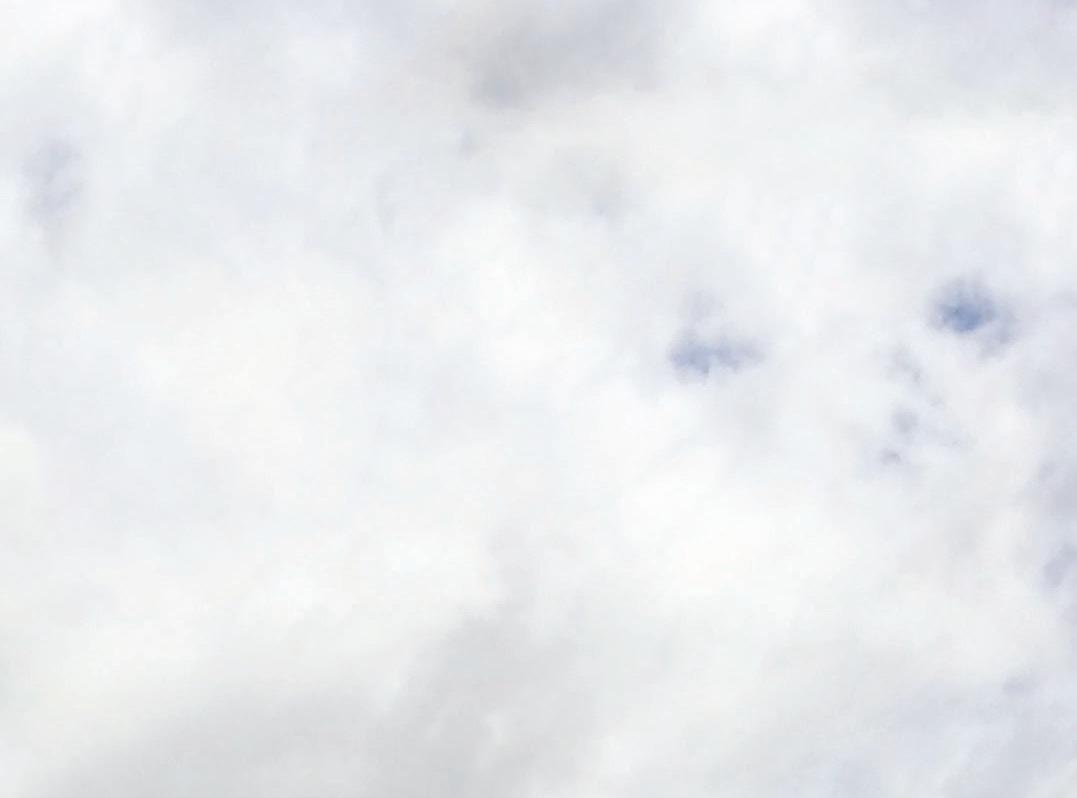

With our team’s collective 200+ years tied to agricultural production, we believe in what we do. We make it our mission to provide profitable production strategies to our farmers with information to improve their bottom lines. Our seasoned editors cover every stage of production — from land preparation, to seed selection, to crop protection through harvest.
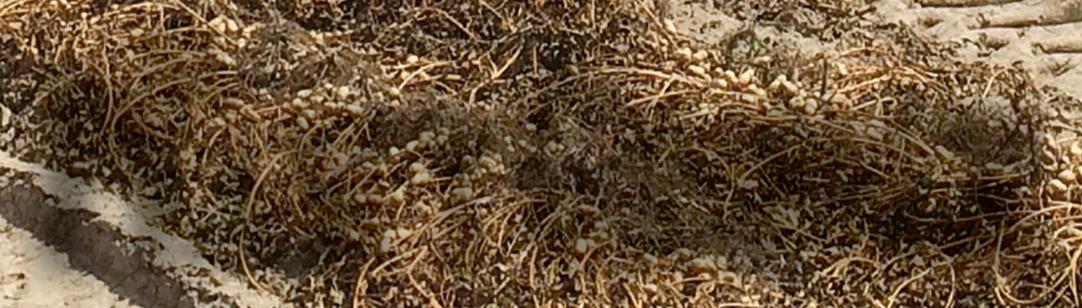

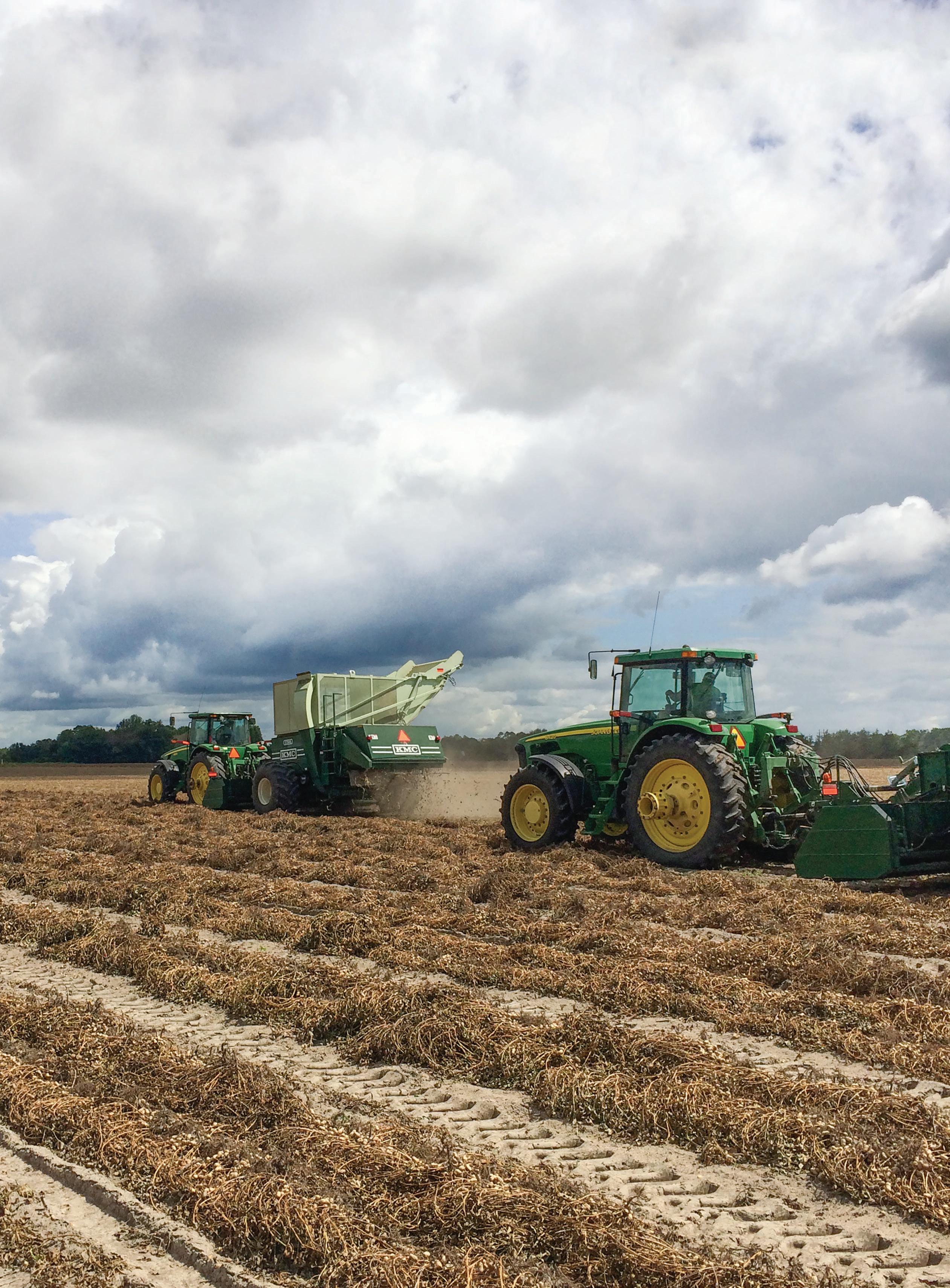